时效振动.docx
《时效振动.docx》由会员分享,可在线阅读,更多相关《时效振动.docx(15页珍藏版)》请在冰豆网上搜索。
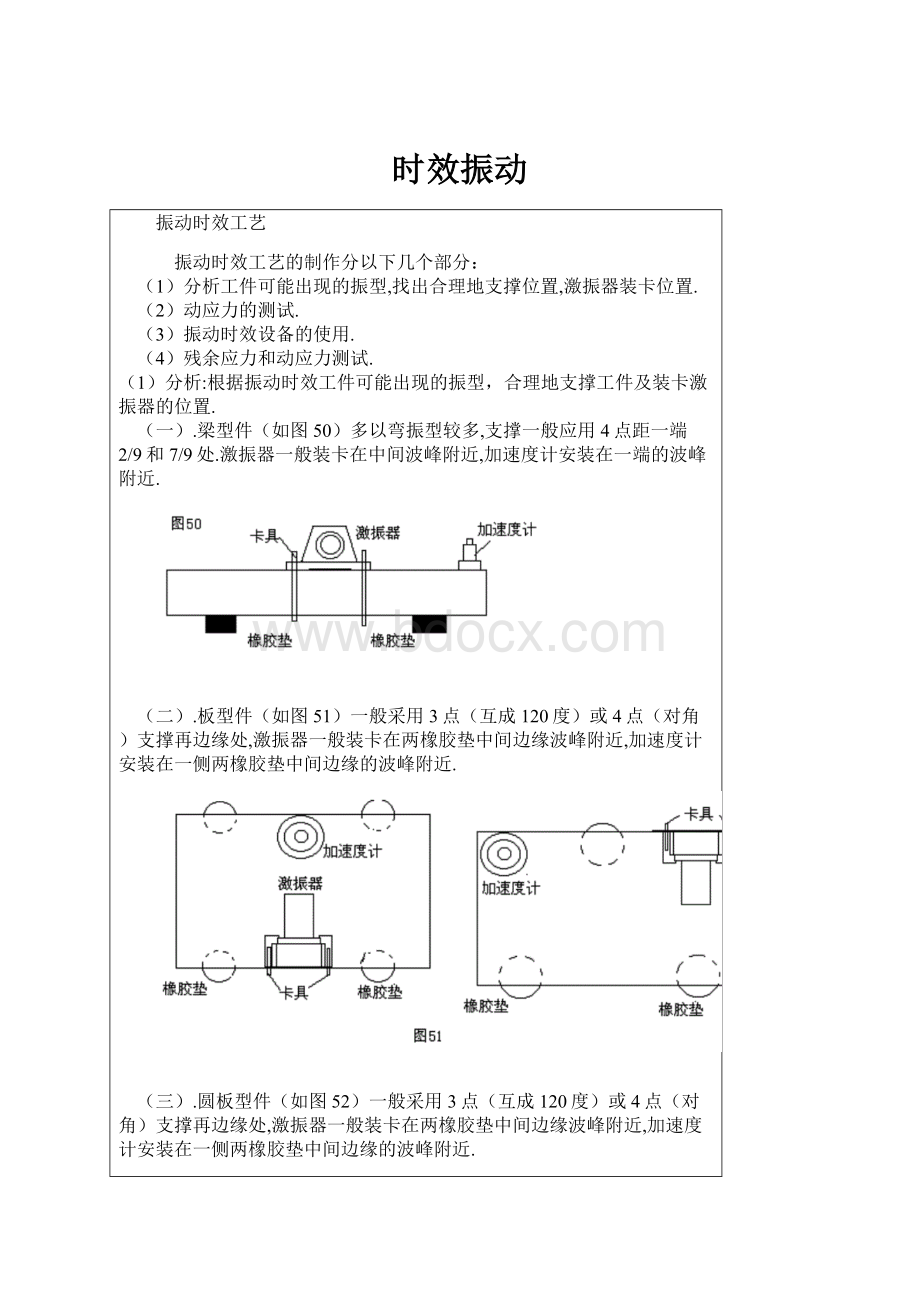
时效振动
振动时效工艺
振动时效工艺的制作分以下几个部分:
(1)分析工件可能出现的振型,找出合理地支撑位置,激振器装卡位置.
(2)动应力的测试.
(3)振动时效设备的使用.
(4)残余应力和动应力测试.
(1)分析:
根据振动时效工件可能出现的振型,合理地支撑工件及装卡激振器的位置.
(一).梁型件(如图50)多以弯振型较多,支撑一般应用4点距一端2/9和7/9处.激振器一般装卡在中间波峰附近,加速度计安装在一端的波峰附近.
(二).板型件(如图51)一般采用3点(互成120度)或4点(对角)支撑再边缘处,激振器一般装卡在两橡胶垫中间边缘波峰附近,加速度计安装在一侧两橡胶垫中间边缘的波峰附近.
(三).圆板型件(如图52)一般采用3点(互成120度)或4点(对角)支撑再边缘处,激振器一般装卡在两橡胶垫中间边缘波峰附近,加速度计安装在一侧两橡胶垫中间边缘的波峰附近.
(四).方箱型件(如图53)一般采用3点支撑再较长的边缘处,激振器一般装卡在上边钢性较大的边缘波峰附近,加速度计安装在边缘的波峰附近.
上述只是简要的介绍一般常规工件的支撑与激振器的装卡位置,具体情况还需要反复试验(利用手动工作模式)来找出合适的振动时效工艺参数.
(2)动应力的测试.
测试动应力所用的仪器设备:
1)动态电阻应变仪(如图54),
2)测试方法1.贴片,沿波峰--波节--波峰的振型方向依次贴6--10片.
2.计算:
可用虎克定律计算动应力值.
(3)振动时效设备的使用:
(一)准备工作:
1.振动时效处理前要准备好做弹性支撑的橡胶垫(或用旧轮胎代替)。
被振工件与激振器连接用的专用卡具。
2.将被振工件水平放置在橡胶垫上。
一般情况下,要根据工件的几何形状合理地选择好支撑点?
支撑点应选择在波节处(工件在自由振动时振幅最小处)。
3.激振器的安装:
将激振器安装在被振工件的被振工件的波峰处(工件在自由振动时振幅最大处)。
激振器底座与工件应刚性连接,接触面要良好。
并用专用卡具卡紧,然后将偏心调到1档。
连接大小四芯线。
4.加速度传感器的安装:
将加速度传感器固定在磁座上放置在工件的波峰处。
连接好加速度信号线。
5.绘图仪的安装:
将绘图仪水平放置与控制箱连接绘图仪信号线,插上电源。
连接控制箱电源。
(二)操作
1.智能工作:
打开控制箱电源,打开绘图仪电源,此时机器进入自检程序,控制箱各显示器显示为零,绘图仪绘制四个彩色小方框,按复位键几秒钟后按智能启动键,绘图仪绘制坐标后机器启动进入智能工作程序。
自动扫频,自动选择工艺参数,自动时效处理,并绘制工艺曲线。
2.手动工作模式:
不用绘图仪,打开控制箱电源开关,按复位键,使系统初始化。
按手动键,再按启动键机器即进入手动工作模式,调节手动旋钮即可达到你所需要的转数进行时效处理或制定工艺参数(波峰.波节及支撑位置)。
3.效果检查:
按中华人民共和国机械行业标准(jb/t5926-91)中的振动时效工艺参数选择及技术要求,即可判定振动时效工艺效果。
(三)时效处理的频率.波峰波节.支撑点的选择:
利用手动扫频到被振工件发出较大的翁翁声时,往工件上撒一些沙子,沙子会剧烈的跳动,沙子聚拢处为波节,反之为波峰,共振频率是在电流和加速度值最大时相对应的频率。
波峰.波节要反复找多次,使支撑更加合理。
(四)激振力的选择:
激振力大小的选择应根据工件的不同材质.几何形状.刚度的大小及重量等因素来确定。
实验和国内外的资料证明,工件的动应力应在20mpa-35mpa之间。
焊接件大一些(35mpa)铸件小一些(20mpa)效果较好。
动应力的大小可用动态电阻应变仪来测定,若无仪器,可根据被振工件的形态依据材料力学介绍的"理想体"来进行估算。
动应力大小的调整是通过改变激振力的大小来完成的,改变激振力是通过改变激振器的偏心距来实现。
(五)振动时间的选择:
根据国内外总结的振动时效处理时间表参考来选择。
构件重量(吨)处理时间(分钟)
小于或等于1吨15--20
在1-5吨20--25
大于5吨25--30
表中数据只作参考,实际情况应根据被振工件的几何形状.材质.重量及检查尺寸稳定性,通过实验找出最佳时间。
(六)应注意的几个问题
1.发生强迫共振:
随着振动频率的升高,电枢电流一直上升无下降趋势,这时即发生了强迫共振,这种现象一般是由被振工件的重量太小而刚性又太大所导致。
2.找不到共振区:
在扫频过程中发现随着频率的升高,电枢电流也缓慢增加,但是电流并不大,直到扫频结束加速度始终在增加并很小,这种现象一般都是由于工件的固有频率超出设备的控制频率范围。
3.发生以上情况,通过实验的方法可以解决。
方法1.可以反复改变激振力和支撑点以及激振器的装卡位置。
方法2.可以采用悬臂的方法(将工件一端固定.激振器装卡在另一端的方法)。
方法3.采用组合振动法(将多个工件刚性连接在一起可以降低工件的固有频率)。
残余应力的测试:
目前通常采用的方法有盲孔法和x射线法,
振动时效技术
一.振动能消除焊接件的残余应力
大家都知道,焊接会产生很大的残余应力,我们利用这点,制成如图一所示的六块试样,其编号为1#-6#,材质为A3,板厚30mm。
在其一面沿纵向堆焊两条8mm宽,2-3mm高的焊道(见图一)。
由于焊接应力的作用,钢板呈弧形挠曲,沿纵向中心线附近可认为产生一弹性应力场。
从材料力学可知
(1)沿纵向拉(压)应力σmax=E·Ymax/ρ其中E为杨氏模量,Ymax=I/2板厚=15mm,ρ=1/2(h+12/4H)
H为挠曲直,I为工件长。
用此式计算出其拉(压)应力在11.9-16.7kg/mm2之间。
将这六件做不同的处理:
1#.2#不做任何时效,3#.4#振动时效,5#.6#热时效。
振动时效规范:
扫描得一阶共频为52.9Hz(3172转/分),二节线距两端面340mm,沿纵向振幅分布列于表一。
在52.2Hz(3132转/分)共振30分钟。
由图二可知:
3#.4#试样纵向振幅为正弦形,最大振幅约为12个加速度。
热时效规范:
室温装炉,550oC保温3小时,随炉冷至250o出炉。
表一.3#4#试样振动加速度分布:
编号
与一端距离
50
250
450
650
850
1050
1250
1450
单位:
mm
3
振幅a
-12.0
-5.1
8.0
11.7
11.2
7.2
-4.3
-11.6
单位:
g
4
振幅a
-11.8
-4.7
7.9
10.9
11.6
7.4
-4.7
-11.2
单位:
g
为测这六块试样的残余应力,在每件距其一端400mm处划出150×160mm的方块,沿纵向中心线,在如图一所示的位置上贴两张3×5(片基距)的纸基120Ω电阻片。
用刨床或手锯,将这150Χ160mm的方块缓慢切下(以不产生残余应力为限)。
同时用YJ-5型静态电阻应变仪测出释放应变,再用公式σr=E·ε计算释放应力的大小。
其中:
E为杨氏模量,ε为测得的微应变数。
计算结果列于表二。
表二:
消除应力比较表 应力单位:
公斤/平方毫米
试样编号
1
2
3
4
5
6
工件状态
没时效
没时效
振动时效
振动时效
热时效
热时效
原挠曲(mm)
14.9
9.7
12.6
13.9
14.7
11.8
残留内应力:
16.7
11.9
14.1
15.6
16.3
13.3
释放应变:
με
617
518
159
233
74
127
释放应力
13.0
10.9
3.3
4.9
1.6
2.7
单件消除应力百分比%
76.5
67.3
90
79.6
平均消除应力百分比%
71.9
84.3
从表二可知:
没经时效的1#.2#试样释放出的应力几乎等于焊接时的残余应力,这表明我们所用的方法是可靠的。
从表二还可看出,振动消除应力71.9%,热时效消除应力84.3%,振动和热时效能消除残余应力的大部分。
振动时效消除的应力虽然比热时效略低但振动有许多优点,比如,经振动工件松弛刚度比热时效有显著体高,在动载和静载下的变形显著降低等,都表示了它可与热时效相媲美。
注:
松弛刚度是指工件产生松弛时的最小应力值小
二.振动能使中小型铸件尺寸稳定
振动也能消除中.小型铸件的残余应力吗?
为此,我们做了下述实验:
用C5116A(1米6立车)的立刀架滑枕(件号55011)七件,振动时效后长期观测其几何尺寸的变化。
按工艺规定:
55011件需二次热时效,否则因导轨面挠曲而易擦伤。
我们试验的目的是看振动时效能否使工件尺寸稳定,进而用振动时效代替热时效。
55011件如图二所示。
扫频(激振力频率从低缓慢向高调整)证明:
我们现用的激振器不能使这固有频率300Hz的工件共振,为此,采用了如下的降拼措施:
用M20的螺栓三支将工件对接(01#与03#对接,04#与05#对接).扫频得一.二.三阶共振频率为31.5Hz,62.9Hz91.9Hz。
令工件在31.5Hz振25分钟。
弹性两点支撑,支点分别在距两端700mm处,沿纵向的加速度.相角.速度列于表三,其振型如图三所示。
从列表三和图三可知:
55011件做正弦振动,每组一阶共振有两个节点,距一端约700mm.
将这七件(四件振动的.三件没振的)三点支撑,放在300mm以上陈旧水泥地面上,调水平后,测各件两导轨的平直性。
用德国蔡氏合向水平仪,每件分七段.从小头80mm处测起,仪器精度:
2μ/200mm。
室温为22℃±2o.01#-03#,04#-05#振前测量一次,振后再测一次,所得结果列于表四。
从表四看出:
振动使变形提前发生了,最大变形达24.0微米。
说明了振动使工件变形(但不大).
在同一天测量其余三件导轨的平直性,然后每隔一个月测量一次,所得结果列于表五--表八。
用统计方法对表五--八进行分析.
因为仪器的精度为2μ/200mm,若变形量低于3微米的测量段认为没变形,则振动件的变形段数占段数的10.4%,没振动件的变形段数却占段数的24.3%,比振动件的大一倍还多。
从图四可看出;振动件半高宽(.峰值0.70处)窄,而没有振动件,半高宽宽说明没振动件数据弥散,大变形量的段数占的比重大;而振动件,数据集中在在小变形段上,大变形量的段数占的比重小。
直接观查数据,可看到;振动件大变形量为4.4微米,没振动的却是8微米,比振动件的约大一倍。
所以,我们认为振动可使中.小铸件尺寸稳定。
三.振动能使大型铸件尺寸稳定
为了进一步观察振动时效对大型铸件的尺寸稳定效果,我们用CW6163/3000万能车床床身静止半年,定期测量其上母线的平直度(纵向平直度)和扭曲变形。
该床身重1.6吨,长4.5米,长条形结构(如图五所示,支点距端部2/9,激振点在中间。
动应力3.5kg/mm2。
第一共振峰71.4Hz,第二共振峰93.7Hz。
第一至第六个月纵向不止度数据列于表十---十一,纵向变形列于表十二---十三;扭曲变形数据列与表十四---十五。
床身纵向频数列于表十六,六个月累计变形频率列于表十七。
从表十六可见,每月变形量:
振动件最高为8μ,没振件最高为14μ。
我们用的合向水平仪精度为2μ/200mm,所以认为0-2μ为不变形测量段。
振动件不变形段数为250个,占总测量段数的81.7%,变形段数占18.3%,没振件不变形段数为179个占总测量段数的62%,变形段数占38%。
6μ以上的变形段数,振动件仅有8个,占总测量段数的2.6%,没振件有36个,占总测量段数笳呤乔罢叩?
倍。
9μ以上的大变形段数,振动件为零,没振件7个,占总测量段数的2.4%。
上述表明:
没振件的变形比振动件的变形高1倍以上,特别是6μ以上的大变形段数,没振件比振动件高4倍以上,半年的累计变形(见表十七),更能说明这一点。
如没振件六个月的最大变形高达27μ,振动件只有12μ;1-7μ的变形段,没振件有3段,占总测量段数的3.3%,振动件却有30段,占总测量段数的33.3%,10μ以下的变形段,没振件有16段,占总测量段数的35.6%,振动件有42段,占总测量段数的91.1%。
11μ以上的大变形段,没振动件有29段,占总测量段数的29%,振动件只有3段,占总测量段数的6.75。
由上面分析,得出结论;振动时效可使大件尺寸稳定。
从表示八可知:
振动件最大月变形量为5μ,而没振件12μ,相差1倍多,振动件不变形(0-2μ)段数位243个,占总测量段数的79.4%,没振动件不变形(0-2μ)段数位215个,占总测量段数74.4%,二者相差不大,6μ以上的变形段,振动件为0个,没振动件为10个,占测量段总数的3.5%。
表十六与表十八对比可以看出,没振件的纵向变形段数比振动件多1倍还多,而(横向变形扭曲)相差仅有5%,但无论纵向还是横向,大变形都明显降低。
结论:
纵向应力消除比横向好,这是因为纵向振动比横向充分。
所以振动时要注意横向共振,在可能条件下,要同时激起纵横向共振。
回首页
由于篇幅所限所有列表未能全部登出,如有需要可来电索取.
jb/t5926-1998
1.主题内容与适用范围
本标准规定了振动时效工艺参数的选择及技术要求和振动时效效果评定办法。
本标准适用于材质为碳素结构钢,低合金钢,焊接件的振动时效处理。
2.术语
2.1扫频曲线—将激振器的频率缓慢的由小调大的过程称扫频,随着频率的变化,工件振动响应发生变化,反映振动响应与频率之间关系的曲线,称扫频曲线,如a—f称振幅频率曲线;a—f称加速度频率曲线。
注:
a表示振幅,a表示加速度,f表示频率
2.2激振点—振动时效时,激振器在工件上的卡持点称激振点。
3.工艺参数选择及技术要求
3.1首先应分析判断出工件在激振频率范围内的振型。
3.2振动时效装置(设备)的选择。
3.2.1设备的最大激振频率应大于工件的最低固有频率。
3.2.2设备的最大激振频率小于工件的最低固有频率时,应采取倍频(或称分频),降频等措施。
3.2.3设备的激振力应能使工件内产生的最大动应力为工作应力的1/3~2/3。
3.2.4设备应具备自动扫频,自动记录扫频曲线,指示振动加速度值和电机电流值的功能,稳速精度应达到±1r/min。
3.3工件支撑,激振器的装卡和加速度计安装
3.3.1为了使工件处于自由状态,应采取三点或四点弹性支撑工件,支撑位置应在主振频率的节线处或附近。
为使工件成为两端简支或悬臂,则应采取刚性装卡。
3.3.2激振器应刚性地固定在工件的刚度较强或振幅较大处,但不准固定在工件的强度和刚度很低部位(如大的薄板平面等)。
3.3.3悬臂装卡的工件,一般应掉头进行第二次振动时效处理,特大工件,在其振动响应薄弱的部位应进行补振。
3.3.4加速度计应安装在远离激振器并且振幅较大处。
3.4工件的试振
3.4.1选择试振的工件不允许存在缩孔,夹渣,裂纹,虚焊等严重缺陷。
3.4.2选择激振器偏心档位,应满足使工件产生较大振幅和设备不过载的要求,必要时先用手动旋钮寻找合适的偏心档位。
3.4.3第一次扫频,记录工件的振幅频率(a—f)曲线,测出各阶共振频率值,节线位置,波峰位置。
3.4.4必要时通过调整支撑点,激振点和拾振点的位置来激起较多的振型。
3.4.5测定1~3个共振峰大的频率在共振时的动应力峰值的大小。
3.4.6选择动应力大,频率低的共振频率作为主振频率。
3.4.7按主振型对支撑,拾振位置进行最后调整。
(注:
主振频率的振型称为主振型。
)
3.5工件的主振
3.5.1在亚共振区内选择主振峰峰值的1/3~2/3所对应的频率主振工件。
3.5.2主振时设备的偏心档位应使工件的动应力峰值达到工作应力的1/3~2/3,并使设备的输出功率不超过额定功率锝80%。
3.5.3进行振前扫频,记录振前的振幅频率(a—f)曲线。
3.5.4主振工件,记录振幅时间(a—t)曲线。
3.5.5起振后振幅时间(a—t)曲线上的振幅上升,然后变平或上升后下降然后再变平,从变平开始稳定3—5min为振动截止时间,一般累计振动时间不超过40min。
3.5.6进行振后扫频,记录振幅频率(a—f)曲线。
3.5.7批量生产的工件可不作振前,振后扫频。
3.5.8有些工件可作多点激振处理,有些工件可用附振频率作多频共振辅助处理,是否调整支撑点,拾振点的位置视工件而定。
3.5.9工件存在夹渣,缩孔,裂纹,虚焊等缺陷,在振动时效中这类缺陷很快以裂纹扩展的形式出现时,应立即中断振动时效处理,工件排出缺陷后,允许重新进行振动时效处理。
3.6振动时效工艺卡和振动时效操作记录卡
3.6.1批量生产的工件进行振动时效处理时,必须制定“振动时效工艺卡”,操作者必须严格执行并填写“振动时效操作记录卡”,再工件上作以振标记。
3.6.2“振动时效工艺卡”应按3.1—3.5条的要求,试验三件以上,找出规律后制定。
3.6.3“振动时效工艺卡”和“振动时效操作记录卡”的内容和格式分别参照附录。
3.7铸件振动时效时应使动应力方向尽量与易变型方向一致。
3.8制订焊接件振动时效工艺时,应明确工件上承受力的主要焊缝和联系焊缝,振动处理中,其振动方向应使工件承受力的主要焊缝处的动应力最大或较大。
4:
振动时效工艺效果评定方法
4.1参数曲线评定法
4.1.1振动处理过程中从振幅时间(a—t)曲线和振前,振后振幅频率(a—f)曲线的变化来监测。
4.1.2出现下列情况之一时,即可判定为达到振动时效工艺效果。
a:
振幅时间(a—t)曲线上升后变平。
b:
振幅时间(a—t)曲线上升后下降然后变平。
c:
振幅频率(a—f)曲线振后的比振前的峰值升高。
d:
振幅频率(a—f)曲线振后的比振前的峰值点左移。
e:
振幅频率(a—f)曲线振后的比振前的带宽边窄。
4.1.3振动处理过程中,如果不出现4.1.2条中所列的任一情况时,应重新调整振动参数,按上述规定的条款再进行时效处理后重新检验。
4.2残余应力的测试
4.2.1推存使用盲孔法,x射线衍射法。
4.2.1.1被振工件振前,振后的残余应力测定点数均应大于5个点。
4.2.1.2用振前,振后的应力平均值(应力水平)来计算应力消除率,焊接件应大于30%,铸锻件应大于20%。
4.2.1.3用振前,振后的最大应力与最小应力之差值来衡量均化程度,振后的计算值应小于振前的计算值。
4.3精度稳定性检测法
4.3.1以要求精度稳定性为主的工件,振后应进行精度稳定性检验。
a.精加工后检验。
b.长期放置定期检验尺寸稳定性,再放置15天时第一次检验,以后每隔30天检验一次,总的静置时间应在半年以上。
c.在动载荷后检验。
应根据具体情况选用上述条款。
4.3.2各种检验结果均应达到设计要求。