生产和物料流管理程序.docx
《生产和物料流管理程序.docx》由会员分享,可在线阅读,更多相关《生产和物料流管理程序.docx(15页珍藏版)》请在冰豆网上搜索。
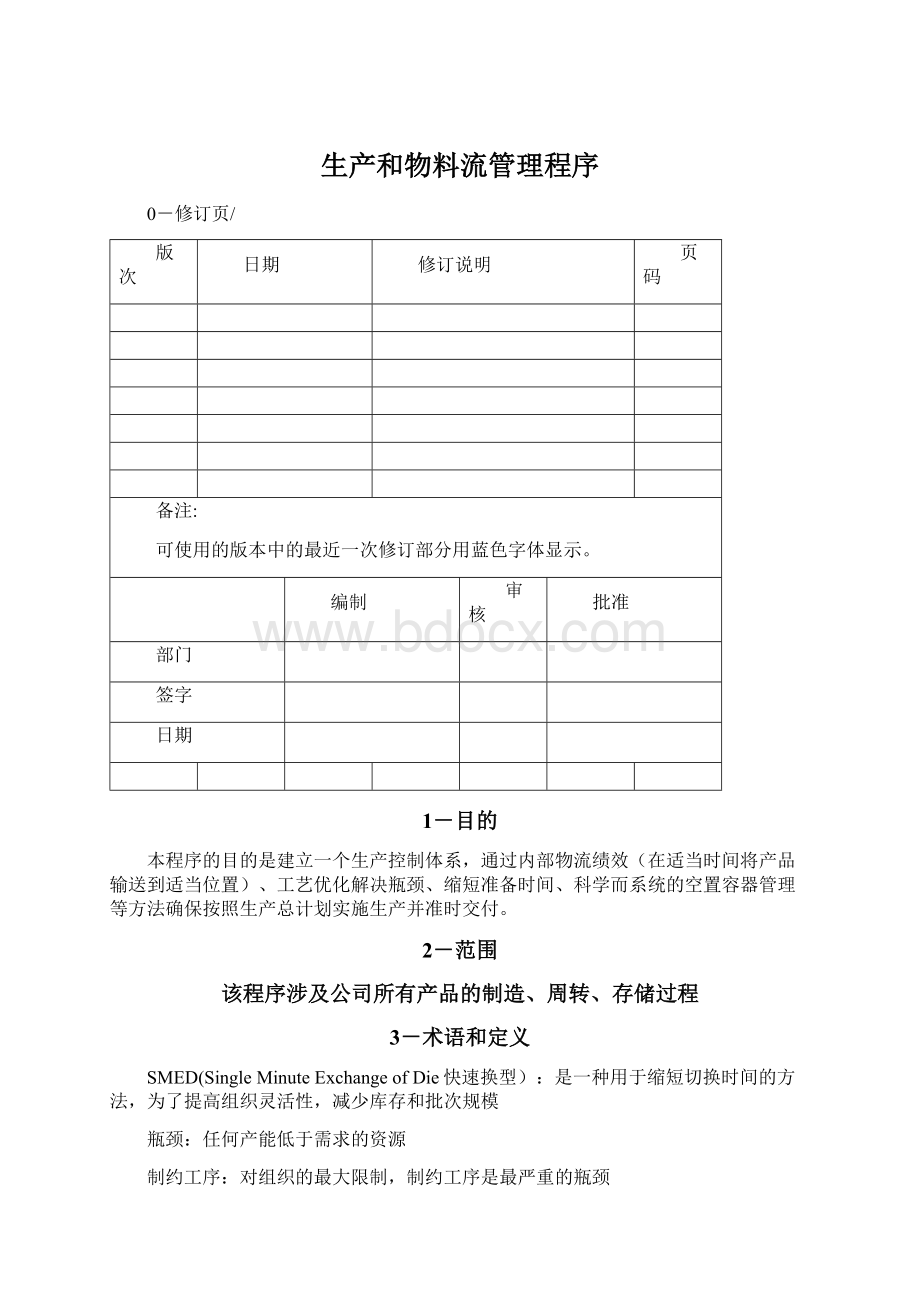
生产和物料流管理程序
0-修订页/
版次
日期
修订说明
页码
备注:
可使用的版本中的最近一次修订部分用蓝色字体显示。
编制
审核
批准
部门
签字
日期
1-目的
本程序的目的是建立一个生产控制体系,通过内部物流绩效(在适当时间将产品输送到适当位置)、工艺优化解决瓶颈、缩短准备时间、科学而系统的空置容器管理等方法确保按照生产总计划实施生产并准时交付。
2-范围
该程序涉及公司所有产品的制造、周转、存储过程
3-术语和定义
SMED(SingleMinuteExchangeofDie快速换型):
是一种用于缩短切换时间的方法,为了提高组织灵活性,减少库存和批次规模
瓶颈:
任何产能低于需求的资源
制约工序:
对组织的最大限制,制约工序是最严重的瓶颈
生产率:
系统生产产品的速率
4-职责
4.1总经理:
负责为本程序的实施提供必要的管理支持
4.2制造部:
负责生产计划的编制和实时跟踪、空置容器的规范管理
4.3工艺装备部:
负责按照精益的生产理念,全面的优化工艺过程,达到缩短准备时间和解决制约工位的目标
4.4物流部:
负责仓储原料、零部件和成品的存储防护以及物料的及时配送
5-管理内容与办法
5.1生产计划及评审
流程
权责
主要活动描述
支持文件/相关记录
商务部
5.1.1制定年度运营计划(S&OP)
商务部基于以下因素为每一种产品制定年度的预测销售计划,经评审后报管理层审核批复。
■客户需求调查及预测
■历史绩效水平
■市场调查
■生产产能(资源遏制)
■库存水平
■公司战略目标
《年度运营计划》
商务部
5.1.2运营计划评审
5.1.2.1商务部每月初组织生产、物流、工艺、采购、财务进行评审,根据以上信息的波动适时进行更新,目的是以保证其对公司产能规划、库存水平以及投资计划保持指导意义;
5.1.2.2通过评审会提出中远期的需求计划、过去达成绩效的评审、未来产能分析以及达成共识调整方向。
调整的方向包括:
更改销售计划、更改生产计划、更改库存水平等。
会议评审纪要
PMC
5.1.3确定月度生产总计划(MPS)
5.1.3.1制造部PMC根据销售计划(客户已明确的当月需求)和年度运营计划,结合实际库存、生产情况编制《月度生产计划表》,经总经理核准后下发各个部门。
月度生产总计划必须包含所有客户的当月实际需求。
5.1.3.2如遇销售计划变更或设备故障停机、批量生产质量问题等需要变更生产计划的,制造部以邮件形式将变更后生产计划发布各个部门;重大计划变更组织会议通知。
《月度生产总计划》
流程
权责
主要活动描述
支持文件/相关记录
PMC
5.1.4月生产总计划评审
5.1.4.1PMC每周六组织制造、工艺、物流、项目、采购进行评审月生产总计划以确定周生产总计划。
评审的内容主要包括原料的供给情况、交付缺口、临时性的插单(客户审核及交样)、设备的运行情况等。
评审达成一致后PMC在ERP里编制产品预测单,进行物料需求计算,仓库根据生产任务单做好备料工作。
5.1.4.2当周生产任务完成后,因计划变更出现的剩余物料,车间需退回仓库,仓库在ERP里进行调拨。
会议评审纪要、《月度生产总计划》
PMC
5.1.5制定日计划
PMC根据周生产计划制定详细的日生产计划,计划的信息填写在《日生产计划表》上并通过ERP下达,车间中间周转库存不得超过3天生产量,并发布在生产看板栏。
PMC在编制日生产计划时需要综合以下因素:
●设备和资源可用性
●当前可动率/OEE
●计划的预防维护、试模
●可用工时
●计划的换型
●交付的周期
《日生产计划表》
制造部
5.1.6每日生产计划实施
5.1.6.1生产班组根据当日生产计划安排生产,班组长按《每小时产能偏差统计表》对生产过程进行跟踪记录,统计偏差的趋势并进行原因分析和采取措施。
5.1.6.2如出现设备异常停机、生产异常等现象,制造部应立即按《快速响应管理程序》进行响应,以促进生产尽早恢复。
5.1.6.3生产车间特殊物料存储按《产品防护控制程序》的要求实施。
做到定置、定容、状态明确且符合产品的存储环境要求。
《每小时产能偏差统计表》、《快速响应管理程序》、《产品防护控制程序》
制造部
5.1.7记录保持
PMC保持整个活动运行的记录(运营计划、月度生产计划、评审纪要、升级响应的记录等),包括因偏差而采取的措施记录。
记录的保持按《记录控制程序》的要求实施存储期限、存储环境、检索力的控制,建议按照月度进行存储。
《记录控制程序》
附录:
生产计划评审流程
6-引用文件
文件编号
文件名称
QP-27
《快速响应管理程序》
QP-17
《记录控制程序》
QP-11
《产品防护控制程序》
6-相关表单
文件编号
文件名称
QR-32-08
《年度运营计划》
QR-32-07
《月度生产总计划》
QR-32-06
《日生产总计划》
/
会议评审纪要
QR-32-01
《每小时产能偏差统计表》
7-过程指标
5.2提高生产效率
为最大限度的提高生产效率,应用精益的生产理念,从提高设备利用率和解决瓶颈工位2个角度出发提高设备利用率的途径:
-----最大限度地缩短设置(准备)时间:
•组建工装变更小组
•分析换型
•分析当前工装变更
•应用快速换模(SMED)
-----最大限度地减少故障(参考“设备维护管理程序”)
•组建设备改进小组
•分析并改进机器可靠性
•实施/改进TPM(全员设备管理)
•分析/改进现有PM(设备管理)系统
•拓展预测性维护
5.2.1SMDE
注:
内部操作---设备停止运行时,操作人员可从事的其它操作;
外部操作---设备正常运行时,操作人员可从事的其它操作。
换型过程指令
文件编号:
QR-32-09版本号:
A/0
设备型号:
日期/时间:
序号
开始时间
换型活动
用时
内部
外部
1
拆解工装
10min
√
2
转移拆解工装
2min
√
3
装配新工装
15min
√
4
产品清线
√
5
不合格品清线
√
6
更换SOP文件
√
步骤1-识别
工艺装备部负责对每条需要换型的生产线建立换型过程活动表,识别出换型的每一步细节
步骤2-分离
将识别的过程进行“内、外”的分离识别
步骤3-转换
尽量通过培训等方式让产线员工提前做好准备的工作,比如被切换工装集成组装、参数预设存储
步骤4-设法提高内部效率
通过改进工艺方案、并行操作等方式
5.2.2制约瓶颈解决
瓶颈制约工位客户需求
OP010OP020OP030OP040OP050
制约分为2种情况
A.产能制约产能<需求
表现在:
设备超负荷、无预防性维护、高溢出成本、超时、高次品率、低绩效(周期时间>任务时间)
B.市场制约产能>需求
表现在:
设备闲置、成本增加、低效率
解决制约的5个步骤:
5.2.2.1步骤0–定义系统(及范围)
PMC组织产能分析,填写产能分析工作表,以识别:
−识别任何遏制的合理流程
−估算每个操作工位的产能
−注意其他瓶颈/制约(周转、物流、人员效率等)
−产能;市场;政策
5.2.2.2步骤1–识别系统制约的因素
识别哪些要素或资源的产能最低,对系统生产率的影响最为严重,识别的信息填写在产能分析工作表上。
5.2.2.3步骤2–决定减少系统制约
减少制约的因素包括以下:
•以保证基本产能的方式将制约工位从生产系统中隔离出来
•尽可能始终运行
•杜绝阻塞/缺料-零件和空间缓存区
•有效地安排操作
•减少浪费产出
将制约工位从系统中分离出来解耦操作工位
有足够的货架、容器、空间来确保零件的运输,以避免操作停止
如果下游工位停机,制约工位不停机利用缓存区管理机制准备缓存区库存,确保始终有零件运行,亦包括物料的提前准备
5.2.2.4步骤3–以制约工位正常运行为优先,再安排其他操作工位
•以运行制约工位为先安排(优化)资源
•保证制约工位的人力资源,并视情况多配
•减少瓶颈工位的工作负荷
•将工作转移至替代性工作中心或改用其他生产方法
•重新设计一些产品以减少瓶颈工位的工作负荷
•分包瓶颈工位的工作
•确定反应的优先级并先于其他操作工位对制约操作工位进行维护
•优化工装变更规范
•识别能够暂时弥补产能的替代性来源
•运行所有其他机器以消除缺件/堵塞
5.2.2.5步骤4–提高系统效率
•改进工装变更方法以缩短切换时间:
•每次切换后进行试产并核准首个制件
•通过成批处理需要类似设置的作业来减少设置次数
•缩短设置时间
•改进预防性维护以减少瓶颈工位停线时间
•增加制约操作工位的产能
•改进周期时间(是否可以加快?
)
•添加机器/人员
•提高每个周期的零件产量
5.2.2.5步骤5–持续改进
制约得到解除后重复以上动作,以更进一步的优化工艺过程,提高产能。
5.3空置容器管理
5.3..1识别空置容器
制造部应识别出产品实现过程中有关的所有的存储容器,并进行分类,相关的信息填写在《空置容器管理表》上。
空置容器包括标准的存储塑料盒、周转期、吸塑盒、货架等。
5.3.2定义储存区域数量和位置
为每类存储容器建立固定的储存位置,并提供标签或标志等视觉标识;制定并维持最小/最大数量,并建立例外情况管理制度。
5.3.4建立质量检查规范
对于空包装质量的检查,包括清洁的标准、堆放的要求,其中考虑到客户需要和包装规范要求。
所有相关工作纳入标准化作业(标准化作业指导书、工位标准化...)悬挂在控制容器存储区。
•包括图片或样品,解释验收标准
•提示客户要求和批准的替代性包装
•包装不合格时的对策
5.3.5建立空置容器安全库存
根据生产计划为每种控制容器建立安全库存标准。
其中明确了包装的使用,以及出现偏差时的反应机制和纠正措施(如,替代包装方案、包装清洗、维护、以及空包装快运等…)
5.3.6落实检查
制造部至少每周对空置容器区进行一次分层审核,以核查安全库存的标准、存储的状态、清洁的满足程度等。
相关文件:
空置器具标准化指导书
LPA
QR-32-02包装和空置容器存储动态表
附录:
空置容器管理表
文件编号:
版本号:
A/0
容器类型/名称
规格
安全库存标准
日期
收进
移出
库存
反应计划
吸塑盒
标准容器
415*270*15蓝色
周转车
纸箱
托盘
5.4原料存储及配送
5.4.1原材料存储