关于紫铜熔铸中吸气的思考.docx
《关于紫铜熔铸中吸气的思考.docx》由会员分享,可在线阅读,更多相关《关于紫铜熔铸中吸气的思考.docx(12页珍藏版)》请在冰豆网上搜索。
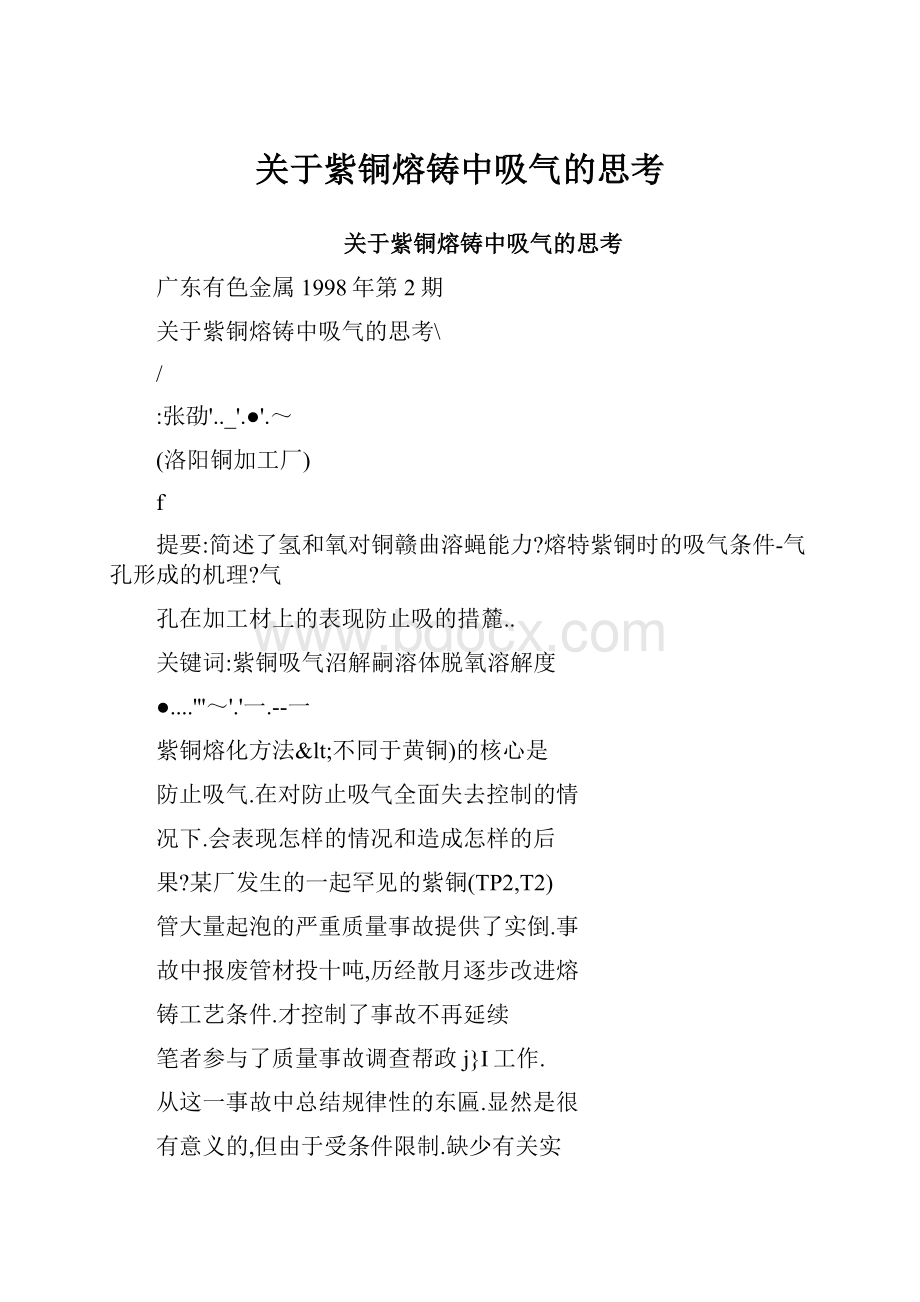
关于紫铜熔铸中吸气的思考
关于紫铜熔铸中吸气的思考
广东有色金属1998年第2期
关于紫铜熔铸中吸气的思考\
/
:
张劭'.._'.●'.~
(洛阳铜加工厂)
f
提要:
简述了氢和氧对铜赣曲溶蝇能力?
熔特紫铜时的吸气条件-气孔形成的机理?
气
孔在加工材上的表现防止吸的措麓..
关键词:
紫铜吸气沼解嗣溶体脱氧溶解度
●....'''~'.'一.--一
紫铜熔化方法<不同于黄铜)的核心是
防止吸气.在对防止吸气全面失去控制的情
况下.会表现怎样的情况和造成怎样的后
果?
某厂发生的一起罕见的紫铜(TP2,T2)
管大量起泡的严重质量事故提供了实倒.事
故中报废管材投十吨,历经散月逐步改进熔
铸工艺条件.才控制了事故不再延续
笔者参与了质量事故调查帮政j}I工作.
从这一事故中总结规律性的东匾.显然是很
有意义的,但由于受条件限制.缺少有关实
证资料,姑作分析思考抛砖引玉,』Z供同行
企业借鉴参考.文中存在错误疏漏之处.盼
专家,读者不吝赐教指正.,
1铜中的氯和氧
解溶解于铜中的气体.主要是氢和氧.
双原子的分子气体都不能直接溶解于金属
熔体中.气体的溶解过程是;吸附在金属表
面——离解成单质气体的原子——扩散进
入金属品格内,形成固溶休或化合物.
氢和氧在铜中部是有害的元素,它降低
铜的性能,并可能导致氢气病"的产生.
实际表明,钢锭中部有一定的含氧量,
陈旧
但溶人过量的氧或氢是导致俦锭质量事故
的主要原因.因此,在焙炼紫铜量.必须采取
措谴尽力堵住气体的来源.避免或尽量减少
空气,水分油以及各种l污染物和熔体接触.
从气体的溶解过程而言.也就是消除"吸附"
这一条件,使得溶解过程不能建立.
在一定的吸附条件下.气体在金属中的
溶解程度主要取决于:
1.1气体与金属的结台力
气体单质的氢原子半径最小t是概活泼
的元素,它几乎可以溶人所有金厩液体和固
体中.在许多金属中氢占全部气体含量的
60~90,所以金属吸气往往称为"吸
氧".
氧和液态下的铜也有银强的亲和率,存
在暇氧或氧化,以cuO形式溶于铜液中.
1.2温度和时间
金属的温度愈高,气体与金属接触时问
愈长.则溶解的气体愈多.只当继续提高温
度时,熔体金属本身具有相当高的蒸汽压
下,才导致溶解度逐渐降低.
1.3气体在铜液中的扩散建度
工频感应炉由于电磁力的自动搅拌作
用.极大地增强了扩散速度.
1998年第2期
以上条件决定了防止吸气成为紫铜熔
炼方法的核心.
2紫铜电炉熔炼和半连续铸锭条件
紫铜电炉熔炼采用电解铜作原料.电解
铜材质本身含有气体.其表面状态优劣对熔
池吸气有重要影响.
熔炼紫铜时常用木炭作覆盖和脱氧剂,
其脱氧作用仅在与液体金属接触的表面进
行,因此称为表面税氧剂.对脱氧铜如
(TP2).使用木炭脱氧的同时.在出炉前还
用磷铜进行最终脱氧,磷铜可沉于熔池.溶
解于整个熔池内与焙融金属中的氧化物相
互作用.脱氧效果显着.但事实上TP2既古
微量P,同时仍有残氧存在,j塞是由于熔体
的结掬和其中微量杂质的分布部是属于不
均匀体系的缘故.
以上两种脱氧的还原反应中,都有气『奉
产生,即一为CO或COz.一为PzO;(可能还
有磷酸铜),在这些气体产物由熔体中上升
途中可将氢带上一起逸出液面,但是和脱氧
作用比较而言.这种脱氧作用是次要的或是
有限的.
但是,实际上木炭都含有气俸和水分,
特别是未经煅烧良好的木炭含量尤多.因
此.木炭覆盖条件下很难避免氧化和吸氢.
熔炼时多是氧化和脱氧,吸氢和脱氧过程同
时存在的.问题是哪个为主.是有利的一面
还是有害的一面?
这需要控制工艺条件趋利
避害..
以上是发生在熔池的反应.加工铜的气
体成分在标准上一般仅规定氧古量不大于
某个微量值,对氢则不作规定.生产现场依
靠观察炉前"铸样"的表面凸起与否凭经验
来判断铜水中含气量的多少,这种有沽简单
易行,作为辅助检查手段也是有效的.
半连续铸造结晶器是二次吸气源.作为
熔体液面保护的煤气如果含水分(未经脱水
或脱水不彻底),成分不合格或者保护不好.
同样会造成熔体吸氢和氧化而|直接进入凝
固
无论是熔池还是结晶器内的熔体.在吸
气失控的情况下,铜水中的含气量势必增
加.如不能发现问题及时采取措施予以纠
正.吸人l过量的气体必定会导致铜锭质量恶
化.
某厂铜管质量事故中,吸气的主要环节
有:
2.1:
熔池(一次吸气)
①电铜过薄(8=3ram).表面锈蚀严
重;
②装料操作方法不合理(少装,多次);
⑤敞炉熔炼.不及时关闭炉盏和炉盖关
闭不严,
④术炭质量不好,未经煅烧,覆盖不及
时,覆盖厚度过薄,不匀.
:
.2结晶器液面(二次吸气)
①煤气(保护性气体)未经脱水,含水汽
量高I
@保护罩内没有用煤气充分驱尽空气
再放流而是通煤气即放流;
③保护罩放置不好,局部液面有煤气吹
拂"波浪".
2.3引锭托座
①调节水套冷水急冲后,托座温度低.
潮湿;
②用锯屑打底,锯屑未烘烤或烘烤不彻J
底.
f●
熔炼年反应造渣多.处理堵管中发现铜
捧脆.
氢和氧在液态铜中的含量关系见图l.
由图可见[氧]少[氢]多,[氧]多[氢]少这种
关系,这可以解释事故中脱氧彻底的TP2
比T2对氢害略为敏感的原因.
广东有色垒属1998年第2期
譬
地
图l铜液中的氢,氧含量关系
3气孔的形成
铜锭中气孔内的气体主要成分是氢.铜
水在凝固温度时氢的溶解度急剧变化是气
孔形成的主要原因.
氢在金属中溶解度的典型曲线为图2
所示.
同;龟;蔽裘1^意
一一—.-,,,,
——.一~?
_
图2氢在金属中溶解度示意图
由图可见,氢在铜水中的溶解度随温度
升高而增大.当结晶器中的铜水从液态冷却
至凝固温度时.氢在铜中的溶解度陡然降
低,此时生长着的晶粒内古氢量较低.如果
铜水吸氢过量,过饱和的氢则在结晶前拊的
边界屡上析出,吸附于技品和夹杂物嫩粒上
并聚集成泡.或者进入枝晶间的缩孔或缩松
中,不能上浮溢出面成为铸锭中的气孔或针
孔.
在有溶解于铜漓中的cu:
O存在时,
cuO与析出的氢产生还原反应并形成水蒸
汽.由于水蒸汽不溶解,多进入技晶间鲴松
内或晶界内形成气孔.并为氢的析出提供了
条件.这也是产生气孔的重要原因之一.
资料指出,由于氢在液态和固态铜中
溶解度的巨大差异.当溶液中存在氧时,甚
至低的含氧量就可产生气孔.
一
般情况下.氢在铜液中的溶解量小于
固体铜中的饱和溶解度.溶液中的cuzO分
解压极低.单独的cu,O也不会分解出氧气
使铸件产生气孔.但是.在严重吸气的情
况下,以上两种形成气孔的条件都存在,都
会是产生大量气孔的原因.
浇铸时中注管埋得深,液流速度快.会
促使锭内气孔的出现.
由于引锭托座潮湿和垫底锯屑所产生
的水蒸气等形成的气孔,多分布在锭底起始
的某一长度锭段上.这样的锭段和锭顶含气
量及气体成分有所不同.
由于结晶器内温度场的不同,铜锭中的
气孔大多分布在皮下.而越往里越少,中心
附近一般没有.
因此.铸锭全长以及横断面上气孔的分
布是不同的.在作分析取样时?
必须严格区
别取样部位.才能得到正确的结论.
4气孔在加工材上的表现
常规生产中,铜材上产生起泡可由于挤
压方面的原因也可由于铸锭的原因所产生?
属允许技术废辩中的儡见缺陷.长期的,异
常的大量起泡的质量责任在前工序——熔
铸.铜锭中的气孔所造成的.
铜锭中的气孔内是气体.较小的气孔经
过加工后可以被压合,在其后加工工序中可
能会暴露为表现缺陷——起皮.铜锭中气孔
很多时,同时会存在较大的气孔?
此时在挤
压营坯的中后段会表现起泡(前段上是由铸
1998年第2期
锭中心部分金属形成的),起泡多沿挤压方
向连续分布,越到后端(压余端)越严重,而
在圆周方向上起泡分布并无规律.此类起泡
严重者无法修理而只能切废.较轻微者经修
理后进入拉伸工序,但拉仲中暴露起皮,杂
质较多,对成品率有较大影响.水封挤压尺
寸较小的管坯时,由于冷却强度大起泡较小
(气体来不及聚集膨胀),但在其后冷轧——
盘拉生产过程中暴嚣起皮,夹杂等缺陷多,
管材打头中发生部分劈裂.拉制管材退火后
则表现为大量的"疹状"起泡,其和挤坯起泡
所不同的是;泡多不连续,较小,泡大者如米
粒,小者如针尖,甚至肉跟不易发现,需话手
感方可发觉.曾试验使用氨分解,氮气和石
油气燃烧的保护性气体退火.都不能消除起
泡.
气泡的形成是气孔压合后在温度——
时间作用下气体重新聚集和膨胀的结果.
成品管(无起泡)耐压,扩口,压扁性能
较差,反映材料的塑性有损失.
和铜管起泡同时存在的另一形成原因
是:
铸锭为过饱和铜圃溶体,使品格歪扭造
成第三类应力,降低塑性.在挤压或退火中,
固温度变化,氢从沿挤压方向仲长的品界或
夹杂等界面析出形成气泡.
紫铜吸氢引起挤坯起泡,退火管材起泡
的特点是基本上每根管子都有起泡,导致
成品率锐减或成批报班,这是和其它起泡原
因极大的不同.
5防止吸气的措施
铜锭中台气过高是由于生产操作不符
合紫铜熔铸工艺要求以及原料,覆盖剂,保
护气体不佳等多种不利固素综合造成的.所
有不利因素均应尽力予以排除才艟确保生
产建立在安全,优质的基础之上.完善和改
进过程表明:
熔池(--次吸气)吸气影响最
大,在这个环节基本解决之后铜管起泡即明
显减轻(泡较少亦较小).只当二次吸气和引
锭座,垫料间题同时解决之后.铜管起泡才
得以彻底消除.
防止吸氢的关键在于堵住"气源".主要
措旎有l
(1)电铜必须符合《标准';起泡管的回
炉料不用于生产紫铜,只作黄铜生产用.
(2)装料(料应.无油,无水,无混杂")必
须一次多装,装满,以充分驱除炉料吸附的
水汽.集中2~3次装完一炉,不得多次少
投.
(3)木炭必须干燥(以般烧木炭为佳).
首次装料后必须立即加入木炭,覆盖厚度
l.0~15O毫米,l:
{j菏足防止吸气,脱氧和保
温的要求
(4)装料熔化后必须及时关上炉门.
(5)煤气发生系统的干燥器内装入氯化
钙(脱水荆),井及时更新,以便吸收煤气中
的水分.煤气罩要罩好,放流前5~10分钟
提前通上煤气,充分驱除罩内原有空气.
(6)引锭座要用煤气烘千,预热.用干燥
的铜块(试样块)垫底,不得使用锯屑垫底.
本文初稿承蒙中南工业大学陈存中教
授审阅并提供宝贵意见,进志谢意.
主要参考文献
1.[苏]切尔涅茄等.有色金属及其
台金中的气体.冶金工业出版社,1989..
2.[美]J.M斯浮博选等,缔造金属中
的气体.机摇口;业出傲社t1984.9O一92页.
3.袁鹃成等.上引铸造无氧铜杆的气孔
特征及其形成机理.特种铸造及有色台金,
1997(5),13--15页.