课题一数控机床基础.docx
《课题一数控机床基础.docx》由会员分享,可在线阅读,更多相关《课题一数控机床基础.docx(37页珍藏版)》请在冰豆网上搜索。
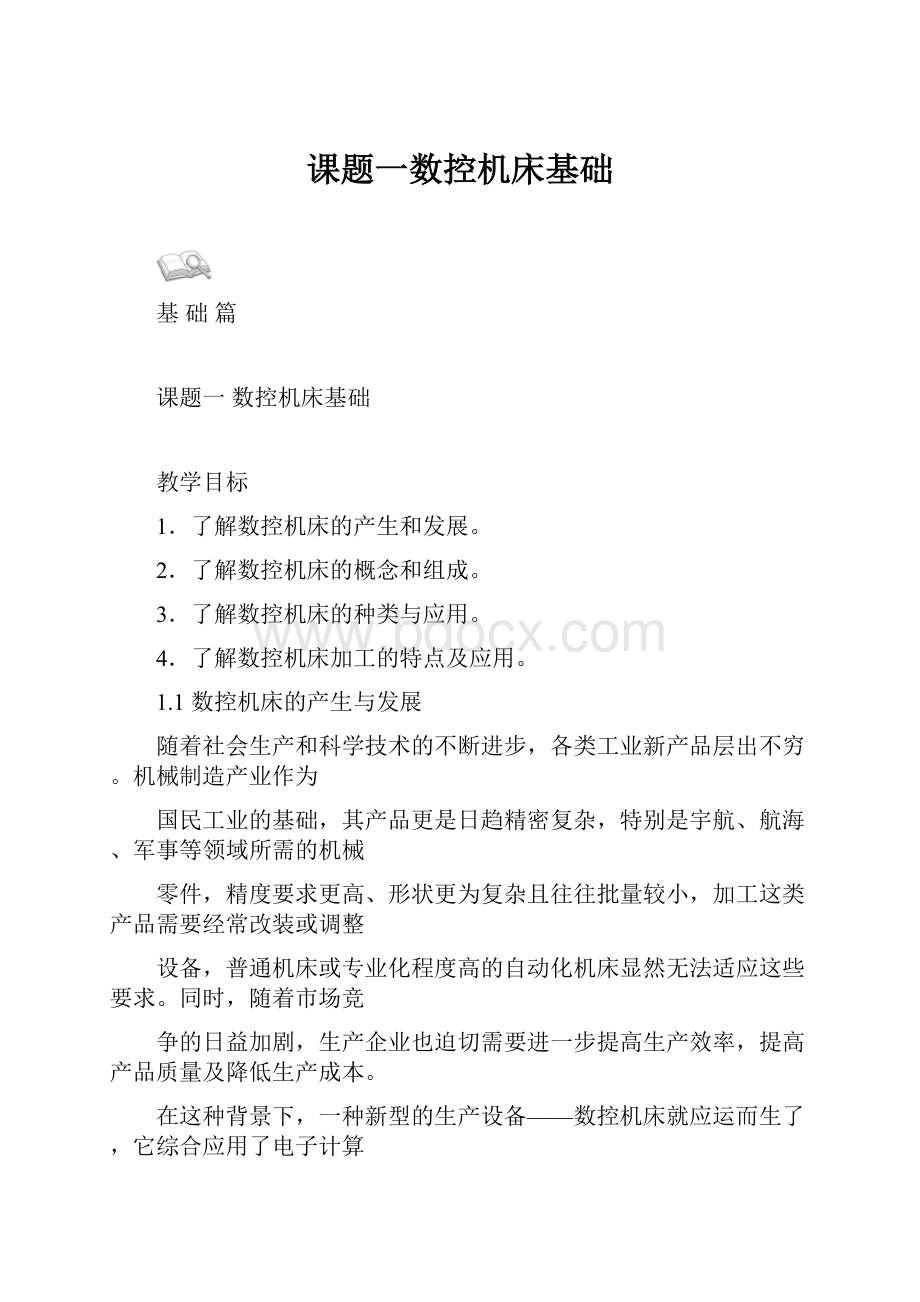
课题一数控机床基础
基础篇
课题一数控机床基础
教学目标
1.了解数控机床的产生和发展。
2.了解数控机床的概念和组成。
3.了解数控机床的种类与应用。
4.了解数控机床加工的特点及应用。
1.1数控机床的产生与发展
随着社会生产和科学技术的不断进步,各类工业新产品层出不穷。
机械制造产业作为
国民工业的基础,其产品更是日趋精密复杂,特别是宇航、航海、军事等领域所需的机械
零件,精度要求更高、形状更为复杂且往往批量较小,加工这类产品需要经常改装或调整
设备,普通机床或专业化程度高的自动化机床显然无法适应这些要求。
同时,随着市场竞
争的日益加剧,生产企业也迫切需要进一步提高生产效率,提高产品质量及降低生产成本。
在这种背景下,一种新型的生产设备——数控机床就应运而生了,它综合应用了电子计算
机、自动控制、伺服驱动、精密测量及新型机械结构等多方面的技术成果,形成了今后机
械工业的基础并指明了机械制造工业设备的发展方向。
1.数控机床的产生
数控机床的研制最早是从美国开始的。
1948 年,美国帕森斯公司(Parsons Co.)在完
成研制加工直升机浆叶轮廓用检查样板的加工机床任务时,提出了研制数控机床的初步设
想。
1949 年,在美国空军后勤部的支持下,帕森斯公司正式接受委托,与麻省理工学院
伺服机构实验室(ServoMechanismLaboratoryoftheMassachusettsInstituteof
Technology)合作,开始数控机床的研制工作。
经过 3 年的研究,世界上第一台数控机床
试验样机于 1952 年试制成功。
这是一台采用脉冲乘法器原理的直线插补三坐标连续控制
系统铣床,其数控系统全部采用电子管元件,其数控装置体积比机床本体还要大。
后来经
过 3 年的改进和自动编程研究,该机床于 1955 年进入试用阶段。
此后,其他一些国家
(如德国、英国、日本、前苏联和瑞典等)也相继开展数控机床的研制开发和生产。
1959
年,美国克耐·杜列克公司(Keaney&Trecker)首次成功开发了加工中心(Machining
数控编程与加工一体化教程
Center),这是一种有自动换刀装置和回转工作台的数控机床,可以在一次装夹中对工件
的多个平面进行多工序的加工。
但是,直到 20 世纪 50 年代末,由于价格和其他因素的影
响,数控机床仅限于航空、军事工业应用,品种也多为连续控制系统。
直到 20 世纪 60 年
代,由于晶体管的应用,数控系统进一步提高了可靠性且价格下降,一些民用工业开始发
展数控机床,其中多数为钻床、冲床等点定位控制的机床。
数控技术不仅在机床上得到实
际应用,而且逐步推广到焊接机、火焰切割机等,使数控技术应用范围不断地得到扩展。
2.数控机床的发展概况
自 1952 年美国研制成功第一台数控机床以来,随着电子技术、计算机技术、自动控
制和精密测量等技术的发展,数控机床也在迅速地发展和不断地更新换代,先后经历了 5
个发展阶段。
第 1 代数控机床:
1952—1959 年采用电子管元件构成的专用数控装置( Numerical
Control,NC)。
第 2 代数控机床:
从 1959 年开始采用晶体管电路的 NC 系统。
第 3 代数控机床:
从 1965 年开始采用小、中规模集成电路的 NC 系统。
第 4 代数控机床:
从 1970 年开始采用大规模集成电路的小型通用电子计算机控制的
系统(Computer Numerical Control,CNC)。
第 5 代数控机床:
从 1974 年开始采用微型计算机控制的系统(Microcomputer Numerical
Control,MNC)。
近年来,微电子和计算机技术日益成熟,其成果正不断渗透到机械制造的各个领域中,
先后出现了计算机直接数控(DNC)系统、柔性制造系统(FMS)和计算机集成制造系统
(CIMS)。
这些高级的自动化生产系统均以数控机床为基础,它们代表着数控机床今后的
发展趋势。
(1)计算机直接数控系统
所谓计算机直接数控(Direct Numerical Control,DNC)系统,即使用一台计算机为
数台数控机床进行自动编程,编程结果直接通过数据线输送到各台数控机床的控制箱。
中
央计算机具有足够的内存容量,因此可统一存储、管理与控制大量的零件程序。
利用分时
操作系统,中央计算机可以同时完成一群数控机床的管理与控制,因此也称它为计算机群
控系统。
目前 DNC 系统中的各台数控机床都有各自独立的数控系统,并与中央计算机连成网
络,实现分级控制,而不再考虑让一台计算机去分时完成所有数控装置的功能。
随着 DNC 技术的发展,中央计算机不仅用于编制零件的程序以控制数控机床的加工
过程,而且进一步控制工件与刀具的输送,形成了一条由计算机控制的数控机床自动生产
线,它为柔性制造系统的发展提供了有利条件。
(2)柔性制造系统
柔性制造系统(Flexible Manufacturing System,FMS)也叫做计算机群控自动线,它
是将一群数控机床用自动传送系统连接起来,并置于一台计算机的统一控制之下,形成一
个用于制造的整体。
其特点是由一台主计算机对全系统的硬、软件进行管理,采用 DNC
2
课题一 数控机床基础
方式控制两台或两台以上的数控加工中心机床,对各台机床之间的工件进行调度和自动传
送;利用交换工作台或工业机器人等装置实现零件的自动上料和下料,使机床每天 24 小
时均能在无人或极少人的监督控制下进行生产。
如日本 FANUC 公司有一条 FMS 由 60 台
数控机床、52 个工业机器人、两台无人自动搬运车、一个自动化仓库组成,这个系统每
月能加工 10000 台伺服电机。
(3)计算机集成制造系统
计算机集成制造系统(Computer Integrated Manufacturing System,CIMS),是指用最
先进的计算机技术,控制从定货、设计、工艺、制造到销售的全过程,以实现信息系统一
体化的高效率的柔性集成制造系统。
它是在生产过程自动化(例如计算机辅助设计、计算
机辅助工艺规程设计、计算机辅助制造、柔性制造系统等)的基础上,结合其他管理信息
系统的发展逐步完善的,有各种类型计算机及其软件系统的分析、控制能力,可把全厂的
生产活动联系起来,最终实现全厂性的综合自动化。
3.我国数控机床发展概况
我国从 1958 年开始由北京机床研究所和清华大学等单位首先研制数控机床,并试制
成功第一台电子管数控机床。
从 1965 年开始研制晶体管数控系统,直到 20 世纪 60 年代
末至 70 年代初,研制的劈锥数控铣床、非圆插齿机等获得成功。
与此同时,还开展了数
控铣床加工平面零件自动编程的研究。
1972—1979 年是数控机床的生产和使用阶段,例
如清华大学成功研制了集成电路数控系统;在车、铣、镗、磨、齿轮加工、电加工等领域
开始研究和应用数控技术;数控加工中心机床研制成功;数控升降台铣床和数控齿轮加工
机床开始小批生产供应市场。
从 20 世纪 80 年代开始,随着改革开放政策的实施,我国先
后从日本、美国、德国等国家引进先进的数控技术。
如北京机床研究所从日本 FANUC 公
司引进 FANUC3、FANUC5、FANUC6、FANUC7 系列产品的制造技术;上海机床研究所
引进美国 GE 公司的 MTC-1 数控系统等。
在引进、消化、吸收国外先进技术的基础上,
北京机床研究所又开发出 BSO3 经济型数控系统和 BSO4 全功能数控系统,航空航天部
706 所研制出 MNC864 数控系统等。
到“八五”末期,我国数控机床的品种已有 200 多个,
产量已经达到年产 10000 台的水平,是 1980 年的 500 倍。
我国数控机床在品种、性能以
及控制水平上都有了新的飞跃,数控技术已经进入了一个继往开来的发展阶段。
4.数控机床的发展趋势
从数控机床的技术水平看,高精度、高速度、高柔性、多功能和高自动化是数控机床
的重要发展趋势。
对单台主机不仅要求提高其柔性和自动化程度,还要求具有更高层次的
柔性制造系统和计算机集成系统的适应能力。
我国国产数控设备的主轴转速已达
10000~40000r/min,进给速度达到 30~60m/min,换刀时间 t<2.0s,表面粗糙度
Ra<0.008μm。
在数控系统方面,目前世界上几个著名的数控装置生产厂家,诸如日本的 FANUC 公
司、德国的 SIEMENS 公司和美国的 A-B 公司,其产品都在向系列化、模块化、高性能和
成套性方向发展。
它们的数控系统都采用了 16 位和 32 位微处理器,标准总线及软件模块
和硬件模块结构,内存容量扩大到了 1MB 以上,机床分辨率可达 0.1μm,高速进给速度
3
数控编程与加工一体化教程
可达 100m/min,控制轴数可达 16 个,并采用先进的电装工艺。
在驱动系统方面,交流驱动系统发展迅速。
交流驱动已由模拟式向数字式方向发展,
以运算放大器等模拟器件为主的控制器正被以微处理器为主的数字集成元件所取代,从而
克服了零点漂移、温度漂移等弱点。
1.2数控机床的概念及组成
1.数控机床的概念
数控技术是 20 世纪中期发展起来的机床控制技术。
数字控制(Numerical Control,简
称 NC)是一种自动控制技术,是用数字化信号对机床的运动及其加工过程进行控制的一
种方法。
数控机床(NC Machine)就是采用了数控技术的机床,或者说是装备了数控系统的机
床。
它是一种综合应用计算机技术、自动控制技术、精密测量技术、通信技术和精密机械
技术等先进技术的典型的机电一体化产品。
国家信息处理联盟(International Federation of Information Processing,简称 IFIP)第
五技术委员会对数控机床作了如下定义:
数控机床是一种装有程序控制系统的机床,该系
统能逻辑地处理具有特定代码和其他符号编码指令规定的程序。
2.数控机床的组成
数控机床的种类很多,但任何一种数控机床都是由控制介质、数控系统、伺服系统、
辅助控制系统和机床本体等若干基本部分组成,如图 1-1 所示。
控制介质 数控系统 伺服系统 机床本体
辅助控制系统
图 1-1数控机床的组成
(1)控制介质
数控系统工作时,不需要操作工人直接操纵机床,但机床又必须执行人的意图,这就
需要在人与机床之间建立某种联系,这种联系的中间媒介物即称为控制介质。
在控制介质
上存储着加工零件所需要的全部操作信息和刀具相对工件位移信息,因此,控制介质就是
将零件加工信息传送到数控装置去的信息载体。
控制介质有多种形式,它随着数控装置类
型的不同而不同,常用的有穿孔纸带、穿孔卡、磁带、磁盘和 USB 接口介质等。
控制介
质上记载的加工信息要经过输入装置传送给数控装置,常用的输入装置有光电纸带输入机、
磁带录音机、磁盘驱动器和 USB 接口等。
除了上述几种控制介质外,还有一部分数控机床采用数码拨盘、数码插销或利用键盘
直接输入程序和数据。
另外,随着 CAD/CAM 技术的发展,有些数控设备利用 CAD/CAM
4
阅读机
输入装置
运算器
课题一 数控机床基础
软件在其他计算机上编程,然后通过计算机与数控系统通信(如局域网),将程序和数据
直接传送给数控装置。
(2)数控系统
数控装置是一种控制系统,是数控机床的中心环节。
它能自动阅读输入载体上事先给
定的数字,并将其译码,从而使机床进给并加工零件。
数控系统通常由输入装置、控制器、
运算器和输出装置 4 部分组成,如图 1-2 所示。
穿孔带
控制器
输出装置
伺服机构
图 1-2数控装置结构
输入装置接受由穿孔带阅读机输出的代码,经识别与译码之后分别输入到各个相应的
寄存器,这些指令与数据将作为控制与运算的原始数据。
控制器接受输入装置的指令,根
据指令控制运算器与输入装置,以实现对机床的各种操作(如控制工作台沿某一坐标轴的
运动、主轴变速和冷却液的开关等)以及控制整机的工作循环(如控制阅读机的启动或停
止、控制运算器的运算和控制输出信号等)。
运算器接受控制器的指令,将输入装置送来的数据进行某种运算,并不断向输出装置
送出运算结果,使伺服系统执行所要求的运动。
对于加工复杂零件的轮廓控制系统,运算
器的重要功能是进行插补运算。
所谓插补运算就是将每个程序段输入的工件轮廓上的某起
始点和终点的坐标数据送入运算器,经过运算之后在起点和终点之间进行“数据密化”,
并按控制器的指令向输出装置送出计算结果。
输出装置根据控制器的指令将运算器送来的计算结果输送到伺服系统,经过功率放大
驱动相应的坐标轴,使机床完成刀具相对工件的运动。
目前均采用微型计算机作为数控装置。
微型计算机的中央处理单元(CPU)又称微处
理器,是一种大规模集成电路。
它将运算器、控制器集成在一块集成电路芯片中。
在微型
计算机中,输入与输出电路采用大规模集成电路,即所谓的 I/O 接口。
微型计算机拥有较
大容量的寄存器,并采用高密度的存储介质,如半导体存储器和磁盘存储器等。
存储器可
分为只读存储器(ROM)和随机存取存储器(RAM)两种类型,前者用于存放系统的控
5
数控编程与加工一体化教程
制程序,后者存放系统运行时的工作参数或用户的零件加工程序。
微型计算机数控装置的
工作原理与上述硬件数控装置的工作原理相同,只是前者采用通用的硬件,不同的功能通
过改变软件来实现,因此更为灵活与经济。
(3)伺服系统
伺服系统由伺服驱动电动机和伺服驱动装置组成,它是数控系统的执行部分。
伺服系
统接受数控系统的指令信息,并按照指令信息的要求带动机床本体的移动部件运动或使执
行部分动作,以加工出符合要求的工件。
指令信息是脉冲信息的体现,每个脉冲使机床移
动部件产生的位移量叫做脉冲当量。
机械加工中一般常用的脉冲当量为 0.01mm/脉冲、
0.005mm/脉冲、0.001mm/脉冲,目前所使用的数控系统脉冲当量一般为 0.001mm/脉冲。
伺服系统是数控机床的关键部件,它的好坏直接影响着数控加工的速度、位置、精度
等。
伺服机构中常用的驱动装置,随数控系统的不同而不同。
开环系统的伺服机构常用步
进电机和电液脉冲马达;闭环系统常用宽调速直流电机和电液伺服驱动装置等。
(4)辅助控制系统
辅助控制系统是介于数控装置和机床机械、液压部件之间的强电控制装置。
它接受数
控装置输出的主运动变速、刀具选择交换、辅助装置动作等指令信号,经过必要的编译、
逻辑判断、功率放大后直接驱动相应的电器、液压、气动和机械部件,以完成各种规定的
动作。
此外,有些开关信号经过辅助控制系统传输给数控装置进行处理。
(5)机床本体
机床本体是数控机床的主体,由机床的基础大件(如床身、底座)和各种运动部件
(如工作台、床鞍、主轴等)所组成。
它是完成各种切削加工的机械部分,是在普通机床
的基础上改进而成的。
其具有以下特点:
●数控机床采用了高性能的主轴与伺服传动系统、机械传动装置。
●数控机床机械结构具有较高的刚度、阻尼精度和耐磨性。
●更多采用了高效传动部件,如滚珠丝杠副、直线滚动导轨。
与传统的手动机床相比,数控机床的外部造型、整体布局,传动系统与刀具系统的部
件结构及操作机构等方面都发生了很多变化。
这些变化的目的是为了满足数控机床的要求
和充分发挥数控机床的特点,因此,必须建立数控机床设计的新概念。
1.3数控机床的种类与应用
当前数控机床的品种很多,结构、功能各不相同,通常可以按下述方法进行分类。
1.按机床运动轨迹进行分类
按机床运动轨迹不同,可分为点位控制数控机床、直线控制数控机床和轮廓控制数控
机床。
(1)点位控制数控机床
点位控制(Positioning Control)又称为点到点控制(Point to Point Control)。
刀具从
某一位置向另一位置移动时,不管中间的移动轨迹如何,只要刀具最后能正确到达目标位
6
课题一 数控机床基础
置,就称为点位控制。
点位控制机床的特点是只控制移动部件由一个位置到另一个位置的精确定位,而对它
们的运动过程中的轨迹没有严格要求,在移动和定位过程中不进行任何加工。
因此,为了
尽可能地减少移动部件的运动时间和定位时间,两相关点之间的移动先以快速移动到接近
新点位的位置,然后进行连续降速或分级降速,使之慢速趋近定位点,以保证其定位精度。
点位控制加工示意图如图 1-3 所示。
这类机床主要有数控坐标镗床、数控钻床、数控点焊机和数控折弯机等,其相应的数
控装置称为点位控制数控装置。
(2)直线控制数控机床
直线控制(Straight Cut Control)又称平行切削控制(Parallet Cut Control)。
这类控制
除了控制点到点的准确位置之外,还要保证两点之间移动的轨迹是一条直线,而且对移动
的速度也有控制,因为这一类机床在两点之间移动时要进行切削加工。
直线控制数控机床的特点是刀具相对于工件的运动不仅要控制两相关点的准确位置
(距离),还要控制两相关点之间移动的速度和轨迹,其轨迹一般由与各轴线平行的直线
段组成。
它和点位控制数控机床的区别在于当机床移动部件移动时,可以沿一个坐标轴的
方向进行切削加工,而且其辅助功能比点位控制的数控机床多。
直线控制加工示意图如图
1-4 所示。
图 1-3 点位控制加工示意图图 1-4 直线控制加工示意图
这类机床主要有数控坐标车床、数控磨床和数控镗铣床等,其相应的数控装置称为直
线控制数控装置。
(3)轮廓控制数控机床
轮廓控制又称连续控制,大多数数控机床具有轮廓控制功能。
轮廓控制数控机床的特
点是能同时控制两个以上的轴联动,具有插补功能。
它不仅要控制加工过程中的每一点的
位置和刀具移动速度,还要加工出任意形状的曲线或曲面。
轮廓控制加工示意图如图 1-5
所示。
属于轮廓控制机床的有数控坐标车床、数控铣床、加工中心等。
其相应的数控装置称
为轮廓控制装置。
轮廓控制装置比点位、直线控制装置结构复杂得多,功能齐全得多。
2.按伺服系统类型进行分类
7
数控编程与加工一体化教程
按伺服系统类型不同,可分为开环控制数控机床、闭环控制数控机床和半闭环控制数
控机床。
图 1-5轮廓控制加工示意图
(1)开环控制数控机床
开环控制(Open loop Control)数控机床通常不带位置检测元件,伺服驱动元件一般
为步进电动机。
数控装置每发出一个进给脉冲后,脉冲便经过放大,并驱动步进电动机转
动一个固定角度,再通过机械传动驱动工作台运动。
开环伺服系统如图 1-6 所示。
这种系
统没有被控对象的反馈值,系统的精度完全取决于步进电动机的步距精度和机械传动的精
度,其控制线路简单,调节方便,精度较低(一般可达 ± 0.02mm),通常应用于小型或经
济型数控机床。
图 1-6开环伺服系统
(2)闭环控制数控机床
闭环控制(Closed loop Control)数控机床通常带位置检测元件,随时可以检测出工作
台的实际位移并反馈给数控装置,与设定的指令值进行比较后,利用其差值控制伺服电动
机,直至差值为零。
这类机床一般采用直流伺服电动机或交流伺服电动机驱动。
位置检测
元件常有直线光栅、磁栅、同步感应器等。
闭环伺服系统如图 1-7 所示。
由闭环伺服系统的工作原理可以看出,系统精度主要取决于位置检测装置的精度,从
理论上讲,它完全可以消除由于传动部件制造中存在的误差给工件加工带来的影响,所以
这种系统可以得到很高的加工精度。
闭环伺服系统的设计和调整都有很大的难度,直线位
移检测元件的价格比较昂贵,主要用于一些精度要求较高的镗铣床、超精车床和加工中心。
(3)半闭环控制数控机床
半闭环控制(Semi-Closed loop Control)数控机床通常将位置检测元件安装在伺服
8
课题一 数控机床基础
电动机的轴上或滚珠丝杠的端部,不直接反馈机床的位移量,而是检测伺服系统的转角,
将此信号反馈给数控装置进行指令比较,用差值控制伺服电动机。
半闭环伺服系统如图 1-
8 所示。
图 1-7闭环伺服系统
图 1-8半闭环伺服系统
因为半闭环伺服系统的反馈信号取自电动机轴的回转,因此系统中的机械传动装置处
于反馈回路之外,其刚度、间歇等非线性因素对系统稳定性没有影响,调试方便。
同样,
机床的定位精度主要取决于机械传动装置的精度,但是现在的数控装置均有螺距误差补偿
和间歇补偿功能,不需要将传动装置各种零件的精度提得很高,通过补偿就能将精度提高
到绝大多数用户都能接受的程度。
再加上直线位移检测装置比角位移检测装置昂贵得多,
因此,除了对定位精度要求特别高或行程特别长,不能采用滚珠丝杠的大型机床外,绝大
多数数控机床均采用半闭环伺服系统。
3.按工艺用途进行分类
按工艺用途不同,可分为金属切削类数控机床、金属成型类数控机床、数控特种加工
机床和其他类型的数控机床。
(1)金属切削类数控机床
金属切削类数控机床包括数控车床、数控钻床、数控铣床、数控磨床、数控镗床以及
加工中心。
切削类机床发展最早,目前种类繁多,功能差异也较大,加工中心能实现自动
换刀。
这类机床都有一个岛库,可容纳 10~100 把刀具。
其特点是:
工件一次装夹可完成
多道工序。
为了进一步提高生产效率,有的加工中心使用双工作台,一面加工,一面装卸,
工作台可以自动交换。
(2)金属成型类数控机床
金属成型类数控机床包括数控折弯机、数控组合冲床和数控回转头压力机等。
这类机
床起步晚,但目前发展很快。
9
数控编程与加工一体化教程
(3)数控特种加工机床
数控特种加工机床有线切割机床、数控电火花加工机床、火焰切割机和数控激光机切
割机床等。
(4)其他类型的数控机床
其他类型的数控机床有数控三坐标测量机床等。
4.按数控系统功能水平进行分类
按数控系统的主要技术参数、功能指标和关键部件的功能水平不同,数控机床可分为
低、中、高 3 个档次。
国内还分为全功能数控机床、普及型数控机床和经济型数控机床。
这些分类方法划分的界线是相对的,不同时期的划分标准有所不同,大体有以下几个方面。
(1)控制系统 CPU 的档次
低档数控系统一般采用 8 位 CPU,中、高档数控系统采用 16 位或 64 位的 CPU,现
在有些 CNC 装置已采用 64 位的 CPU。
(2)分辨率和进给速度
分辨率为位移检测装置所能检测到的最小位移单位,分辨率越小,则检测精度越高。
它取决于检测装置的类型和制造精度。
一般认为,分辨率为 10μm,进给速度为
8~10m/min 是低档数控机床;分辨率为 1μm,进给速度为 10~20m/min 是中档数控机床;
分辨率为 0.1μm,进给速度为 15~20m/min 是高档数控机床。
通常分辨率应比机床所要求
的加工精度高一个数量级。
(3)伺服系统类型
一般采用开环、步进电动机进给系统的为低档数控机床;中、高档数控机床则采用半
闭环或闭环的直流伺服或交流伺服系统。
(4)坐标联