ZCSⅡ液体动压轴承实验台指导书.docx
《ZCSⅡ液体动压轴承实验台指导书.docx》由会员分享,可在线阅读,更多相关《ZCSⅡ液体动压轴承实验台指导书.docx(27页珍藏版)》请在冰豆网上搜索。
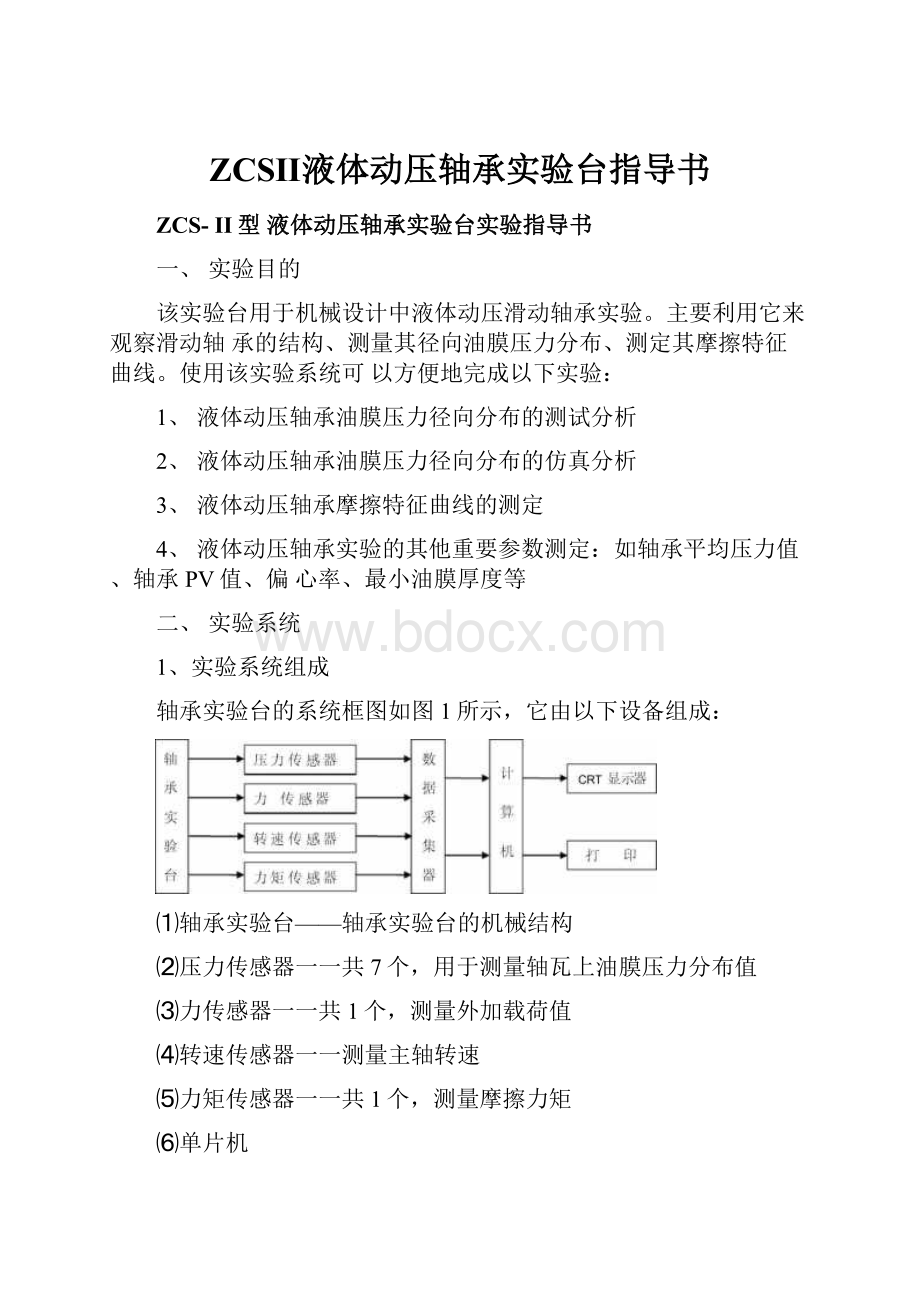
ZCSⅡ液体动压轴承实验台指导书
ZCS-II型液体动压轴承实验台实验指导书
一、实验目的
该实验台用于机械设计中液体动压滑动轴承实验。
主要利用它来观察滑动轴承的结构、测量其径向油膜压力分布、测定其摩擦特征曲线。
使用该实验系统可以方便地完成以下实验:
1、液体动压轴承油膜压力径向分布的测试分析
2、液体动压轴承油膜压力径向分布的仿真分析
3、液体动压轴承摩擦特征曲线的测定
4、液体动压轴承实验的其他重要参数测定:
如轴承平均压力值、轴承PV值、偏心率、最小油膜厚度等
二、实验系统
1、实验系统组成
轴承实验台的系统框图如图1所示,它由以下设备组成:
⑴轴承实验台——轴承实验台的机械结构
⑵压力传感器一一共7个,用于测量轴瓦上油膜压力分布值
⑶力传感器一一共1个,测量外加载荷值
⑷转速传感器一一测量主轴转速
⑸力矩传感器一一共1个,测量摩擦力矩
⑹单片机
⑺PC机
⑻打印机
2、实验系统结构
该实验机构中滑动轴承部分的结构简图如图2
F6
『跖滑劝轴乐部分直罔
1、电机
2、皮带
3、摩擦力传感器
4、压力传感器:
测量轴承表面油膜压力,共7个F1~F7,
5、轴瓦
6、加载传感器:
测量外加载荷值
7、主轴
9、油槽
10、底座
11、面板
12、调速旋钮:
控制电机转速
试验台启动后,由电机1通过皮带带动主轴7在油槽9中转动,在油膜粘力作用下通过摩擦力传感器3测出主轴旋转时受到的摩擦力矩;当润滑油充满整个轴瓦内壁后轴瓦上的7个压力传感器可分别测出分布在其上的油膜压力值;待稳
定工作后由温度传感器t1测出入油口的油温,t2测出出油口的油温。
3、实验系统主要技术参数
(1)实验轴瓦:
内径d=70mm长度L=125mm
(2)加载范围:
0〜1800N
(3)摩擦力传感器量程:
50N
⑷压力传感器量程:
0〜1.0MPa
⑸加载传感器量程:
0〜2000N
(6)直流电机功率:
355W
(7)主轴调速范围:
2〜500rpm
三、实验原理及测试内容
1、实验原理
滑动轴承形成动压润滑油膜的过程如图3(a)所示。
当轴静止时,轴承孔与轴颈直接接触,如图3(a)所示。
径向间隙△使轴颈与轴承的配合面之间形成楔形间隙,其间充满润滑油。
由于润滑油具有粘性而附着于零件表面的特性,因而当轴颈回转时,依靠附着在轴颈上的油层带动润滑油挤入楔形间隙。
因为通
过楔形间隙的润滑油质量不变(流体连续运动原理),而楔形中的间隙截面逐渐变小,润滑油分子间相互挤压,从而油层中必然产生流体动压力,它力图挤开配合面,达到支承外载荷的目的。
当各种参数协调时,液体动压力能保证轴的中心与轴瓦中心有一偏心距e。
最小油膜厚度nmin存在于轴颈与轴承孔的中心连线上。
液体动压力的分布如图3(c)所示。
图3液体动压润滑膜形成的过程
液体动压润滑能否建立,通常用f-入曲线来判别。
图4中f为轴颈与轴承之间的摩擦系数,入为轴承特性系数,它与轴的转速n,润滑油动力粘度n、润滑油压强p之间的关系为:
入为=nn/p
式中,n为轴颈转速;n为润滑油动力粘度;P为单位面积载荷。
Fr
即式中,p=lid;Nmm。
Fr是轴承承受的径向载荷;d是轴承的孔径,本实验中,d=70mm;11是轴承有效工作长度,对本实验轴承,取Ii=125mm
如图4,当轴颈开始转动时,速度极低,这时轴颈和轴承主要是金属相接触,产生的摩擦为金属间的直接摩擦,摩擦阻力最大。
随着转速的增大,轴颈表面的圆周速度增大,带入油楔内的油量也逐渐加多,则金属接触面被润滑油分隔
开的面积也逐渐加大,因而摩擦阻力也就逐渐减小。
当速度增加到一定大小之后,已能带入足够把金属接触面分开的油量,油层内的压力已建立到能支承轴颈上外载荷程度,轴承就开始按照液体摩擦状态工作。
此时,由于轴承内的摩擦阻力仅为液体的内阻力,故摩擦系数达到最小值,如图4摩擦特性曲线上A点。
当轴颈转速进一步加大时,轴颈表面的速度亦进一步增大,使油层间的相对速度增大,故液体的内摩擦也就增大,轴承的摩擦系数也随之上升。
图4摩擦特性曲线(Stribeck曲线)
特性曲线上的A点是轴承由混合润滑向流体润滑转变的临界点。
此点的摩擦系数最小,此点相对应的轴承特性系数称为临界特性系数,以入。
表示。
A点之右,即入〉入。
区域为流体润滑状态;A点之左,即入v入。
区域称为边界润滑状态。
根据不同条件所测得的f和入之值,我们就可以作出f-入曲线,用以判别轴承的润滑状态,能否实现在流体润滑状态下工作。
2、油膜压力测试实验
(1)理论计算压力图5为轴承工作时轴颈的位置。
根据流体动力润滑的雷诺方程,从油膜起始角i到任意角「的压力为:
式中:
P:
――任意位置的压力单位:
Pa
其中D为轴承孔直径,d为轴径直径
油压任意角单位:
度
0――最大压力处极角单位:
度
'i油膜起始角单位:
度
其中e为偏心距
在雷诺公式中,油膜起始角「、最大压力处极角''o由实验台实验测试得到
另一变化参数:
偏心率的变化情况,它由查表得到。
具体方法如下:
对有限宽轴承,油膜的总承载能力为:
式中:
F――承载能力,即外加载荷单位:
N
B轴承宽度单位:
mm
Cp承载量系数,见表1
I
Jf
图5径向滑动轴承的油压分布
由公式(1-2)可推出:
由公式(1-3)计算得承载量系数Cp后再查表可得到在不同转速、不同外加载荷下的偏心率情况。
注:
若所查的参数系数超出了表中所列的,可用插入值法进行推算。
(2)实际测量压力
如图2所示,启动电机,控制主轴转速,并施加一定工作载荷运转一定时间轴承中形成压力油膜后图中代号2,3,4,5,7,8,9七个压力传感器用于测量轴瓦表面每隔22度角处的七点油膜压力值,并经A/D转换器送往PC微机中显示压力值。
在实验台配套软件中可以分别作出油膜实际压力分布曲线和理论分布曲线,比较两者间的差异。
3、摩擦特性实验
(1)理论摩擦系数
理论摩擦系数公式:
+0.55'-*;
(1-4)
摩擦系数
轴承平均压力,
单位:
Pa
£随轴承宽径比而变化的系数,对于
当B/d>1时,£=1;
■-__相对间隙'=D-
d
B/d<1的轴承,£=(d/B)1.5;
由公式(1-4)可知理论摩擦系数f的大小与油膜粘度n、转速①和平均压力p(也即外加载荷F)有关。
在使用同一种润滑油的前提下,粘度n的变化与油膜温度有关,由于不是在长时间工作的情况下,油膜温度变化不大,因此在本实验系统中暂时不考虑粘度因素。
(2)测量摩擦系数
如图2所示,在轴瓦中心引出一压力传感器10,用以测量轴承工作时的摩擦力矩,进而换算得摩擦系数值。
对它们分析如图6:
刀F*r=N*L
(1)
刀F=f*F
N
式中:
刀F――圆周上各切点摩擦力之和刀F=F1+F2+F3+F4,+r――圆周半径
N――压力传感器测得的力
L――力臂
F――外加载荷力
f摩擦系数
所以实测摩擦系数公式:
£N*Lf=
F*r
(1-5)
4、轴承实验中其他重要参数
在轴承实验实验中还有一些比较重要的参数概念,以下分别作一一介绍⑴轴承的平均压力p(单位:
MPa
p=d
(1-6)
F――外加载荷,N
B轴承宽度,mm
d轴径直径,mm
[p]――轴瓦材料许用压力,MPa,其值可查
(2)轴承pv值(单位:
MPa*m/S
轴承的发热量与其单位面积上的摩擦功耗fpv成正比(f是摩擦系数),限制pv值就是限制轴承的温升。
F+■:
*d*nF*n
Pv=*=<[pv](1-7)
B*d60*100019100*B
式中:
v――轴颈圆周速度,m/s
[pv]轴承材料pv许用值,MPa*m/s其值可查
⑶最小油膜厚度
hmin=r*'-*(1一)(1-8)
式中各参数说明见前。
四、实验操作步骤
〈一〉系统联接及启动
1、连接RS232通讯线
在实验台及计算机电源关闭状态下,将标准RS232通讯线分别接入计算机及ZCS-II型液体动压轴承实验台RS232串行接口。
2、启动机械教学综合实验系统
确认RS232串行通讯线正确联接,开启电脑,点击“轴承实验台
进入ZCS-II型液体动压轴承实验台系统“油膜压力分布实验”主界面如图7
〈二〉油膜压力测试实验
滑动轴承实验系统“油膜压力分布实验”主界面如图7:
图7油膜压力分析实验主界面
1、系统复位
放松加载螺杆,确认载荷为空载,将电机调速电位器旋钮逆时针旋到底即零转速。
顺时针旋动轴瓦前上端的螺钉,将轴瓦顶起将油膜放净,然后放松该螺钉,使轴瓦和轴充分接触。
点击“复位”键,计算机采集7路油膜压力传感器初始值,并将此值作为“零点”储存。
2、油膜压力测试
点击“自动采集键”系统进入自动采集状态,计算机实时采集7路压力传感器、实验台主轴转速传感器及工作载荷传感器输出电压信号,进行“采样-处理-显示”o慢慢转动电机调速电位器旋钮启动电机,使主轴转速达到实验预定值(一般nW300vpm。
旋动加载螺杆,观察主界面中轴承载荷显示值,当达到预定值(一般为1800N后即可停止调整。
观察7路油膜压力显示值,待压力值基本稳定后点击“提取数据键”,自动采集结束。
主界面上即保存了相关实验数据。
3、自动绘制滑动轴承油膜压力分布曲线
点击“实测曲线”键计算机自动绘制滑动轴承实测油膜压力分布曲线。
点击“理论曲线”键计算机显示理论计算油膜压力分布曲线。
4、手工绘制滑动轴承油膜压力分布曲线
根据测出的油压大小按一定比例手动绘制油压分布曲线,如图8所示。
具体画法是沿着圆周表面从左向右画出角度分别为:
24°,46°,68°,90°,112°,134°,156°等分,得出压力传感器1,2,3,4,5,6,7的位置,通过这些点与圆心连线,在它们的延长线上,将压力传感器测出的压力值,按0.1MPa:
5mm的比例画出压力向量1-12-27-7'。
实验台压力传感器显示数值的单位是大气压
(1大气压=1kgf/mm2),换算成国际单位值的压力值(1kgf/mm2=0.1MPa。
经1',2',7'各点连成平滑曲线,这就是位于轴承宽度中部的油膜压力在圆周方向的分布曲线。
图8径向压力分布与承载量曲线
为了确定轴承的承载量,用pisin©i(1,2,,7)求出压力分布向量1-1',2-2',,7-7'在载荷方向上(y轴)的投影值。
然后,将pisin©i这些平行与y轴的向量移到直径0-8上,为清楚起见,将直径0-8平移到图4的下面部分,在直径0-8〃上先画出圆周表面上压力传感器油孔位置的投影点1',2',,
7'。
然后通过这些点画出上述相应的各点压力在载荷方向上的分布量,即T,
2〃,,7〃点位置,将各点平滑地连接起来,所形成的曲线即为在载荷方向上的压力分布。
在直径0'-8'上作一矩形,采用方格坐标纸,使其面积与曲线包围的面积相等,则该矩形的边长Pav即为轴承中该截面上的油膜中平均径向压力。
滑动轴承处于流体摩擦(液体摩擦)状态工作时,其油膜承载量与外载荷相平衡,轴承内油膜的承载量可用下式求出:
Fr=W=©书PavBd
(3-6-9)
W
书=PavBd(3-6-10)
式中,W轴承内油膜承载能力;
Fr――外加径向载荷;
书一一轴承端泄对其承载能力的影响系数;
Pav——轴承的径向平均单位压力;
B――轴瓦长度;
D——轴瓦内径。
润滑油的端泄对轴承内的压力分布及轴承的承载能力影响较大,通过实验可
以观察其影响,具体方法如下。
将由实验测得的每只压力传感器的压力值代入下式,可求出在轴瓦中心截面
上的平均单位压力:
i=7
刀Pisin$i
Pav=i=1=Pisin也+P2Sin2+…P7sin$
77(3-6-11)
轴承端泄对轴承承载能力的影响系数,由公式(3-6-11)求得
〈三〉摩擦特性测试实验
滑动轴承的摩擦特性曲线见图4。
参数n为润滑油的动力粘度,润滑油的粘
度受到压力与温度的影响,由于实验过程时间短,润滑油的温度变化不大;润滑
油的压力一般低于20MPa因此可以认为润滑油的动力粘度是一个近似常数。
根据查表可得N46号机械油在20°C时的动力粘度为0.34Pa•s。
n为轴的转速,是一个实验中可调节的参数。
轴承中的平均比压可用下式计算:
Fr_
P=Bd(3-6-12)
在实验中,通过调节轴的转速n或外加轴承径向载荷Fr,从而改变nn/p,将各种转速n及载荷Fr所对应的摩擦力矩测出由1-5求得出摩擦系数f并画出f-n及f-Fr曲线。
1、载荷固定,改变转速
(1)确定实验模式
打开轴承实验主界面,点击“摩擦特性实验”进入摩擦特性实验主界面如图9所示。
买测曲线亚億曲线摩捺特性买验压力分和宴验帮助打印追岀
图9滑动轴承摩擦特性实验主界面
点击图9中“实测实验”及“载荷固定”模式设定键,进入“载荷固定”实验模式。
(2)系统复位
放松加载螺杆,确认载荷为空载,将电机调速电位器旋钮逆时针旋到底即零转速。
顺时针旋动轴瓦前上端的螺钉,将轴瓦顶起将油膜放净,然后放松该螺钉,使轴瓦和轴充分接触。
点击“复位”键,计算机采集摩擦力矩传感器当前输出值,并将此值作为“零点”保存。
(3)数据采集
系统复位后,在转速为零状态下点击“数据采集”键,慢慢旋转实验台加载螺杆,观察数据采集显示窗口,设定载荷为100-200N。
慢慢转动电机调速电
位器旋钮并观察数据采集窗口,此时轴瓦与轴处于边界润滑状态,摩擦力矩会出现较大增加值,由于边界润滑状态不会非常稳定,应及时点击“数据保存”键将这些数据保存(一般2〜3个点即可)。
随着主轴转速增加机油将进入轴与轴瓦之间进入混合摩擦。
此时nn/p的
改变引起摩擦系数f的急剧变化,在刚形成液体摩擦时,摩擦系数f达到最小值。
继续增加主轴转速进入液体摩擦阶段,随着nn/p的增大即n增加,油膜厚度及摩擦系数f也成线形增加,保存8个左右采样点即完成数据采集。
点击“结束米集”键完成数据米集。
(4)绘制测试曲线
点击“实测曲线”计算机根据所测数据自动显示f-n曲线。
也可由学生抄录测试数据手工描绘实验曲线。
点击“理论曲线”计算机按理论计算公式计算并显示f-n曲线。
按“打印”功能链,可将所测试数据及曲线自动打印输出。
2、转速固定改变载荷
(1)确定实验模式
操作同载荷固定改变转速模式确定一节,并在图9中设定为“转速固定”实验模式。
(2)系统复位
同上节操作
(3)数据采集点击“数据采集”键,在轴承径向载荷为零状态下,慢慢转动调速电位器
旋钮,观察数据采集显示窗口,设定转速为某一确定值,例如200rpm,点击“数据保存”键得到第一组数据。
点击“数据采集”键,慢慢旋转加载螺杆并观察采集显示窗口。
当载荷达到预定值时点击“数据保存”得到第二组数据。
反复进行上述操作,直至采集8组左右数据,点击“结束采集”键,完成数据采集。
(4)绘制测试曲线
方法同上节,可显示或打印输出实测f-F曲线及理论f-F曲线。
同样也可由学生手工绘制。
〈四〉注意事项
在开机做实验之前必须首先完成以下几点操作,否则容易影响设备的使用寿命和精度。
(1)在启动电机转动之前请确认载荷为空,即要求先启动电机再加载。
(2)在一次实验结束后马上又要重新开始实验时请顺时针旋动轴瓦上端的螺钉,顶起轴瓦将油膜先放干净,同时在软件中要重新复位(这很重要!
),这样确保下次实验数据准确。
(3)由于油膜形成需要一小段时间,所以在开机实验或在变化载荷或转速后请
待其稳定后(一般等待5〜10s即可)再采集数据。
(4)在长期使用过程中请确保实验油的足量、清洁;油量不足或不干净都会影响实验数据的精度,并会造成油压传感器堵塞等问题。
五、附录
附录1、轴承实验台软件说明本软件界面有两个主窗体:
主窗体1:
油膜压力仿真与测试(见附图1)
主窗体2:
摩擦特性仿真与测试(见附图2)
注:
图中数据仅为参考值,不代表实验数据
邇斥力吋实验-一杭州皐辰科屈谡备右配绘市
标定®串口选释劝实輕项目迪实验说覗②复拉有效②退出蝕©
-滑动軸承压力实际测试曲钱
实际油胆压力伯
3OD,DM
田200^00
1W.CW
500pM
-lOO.OOO
5010D150
角度简
握奉嘰崛的灰屢为I:
.区]因叵]牺音姑图]I養除馭舍
鬲胡軸耳压力分布遅论曲线
理億油馬庄力伯
900,000
400.000^3CO.OM£出200.000
100,000
50100150
甬.度©
X(£
領膜压力采
第一点
0.12
第二点
0.24
第三点
0.45
第四点
0.5
第五点
0.53
匏六点
0.4
第七点
0,1
•松歎惜魂.
串口苗择
①卑口1
O串口2
夹眇数一一:
轴承转壷n[缈|审
轴孚戟荷F[1^~|.进口油逞II|_度
出口油君龙匚二|度
倉果显示
轴垂贯度
0.0TO
迈爭讦冃.土刁3
轴承PV值io.15
轴承pV讦用僧15
IPa.m/s
⑥鬆屢验尙
实測曲钱理论曲钱.詰栗蛊示圧力少布其验辱援特性实捡
帮阳打印
目前正在使用审口]
油腥励仿真与测试
杭卅星辰科戦设番有限公可
牖障擦特性实瞬一-抗州早辰科裁设帝有眼瓷司
(附图
EW
在平均转速230rpm下LF)实测摩擦系数曲統
0.02S
0.026
0.024-
0.022
0.02
0018
SQCl1,M0f,»Q1,4001冏口
F㈣
-
0.02
0.035
003
在平均转违330咁“下卄屮[诧论匪捋条数曲渥
-相关操论——
序溜就_
^理论棍扌II
O实测实脸
掾作棣式
◎速度固定
rrtr口-
懐)串疔口1
C*串行口2
•尋号载荷呗1转速沁mF
1'£55;23C
2830230
\3963230
41115230
5I40D230
61656230
摩擦力矩肚ml
0.702
0.723
0.790
0.B3)
0.8S2
0.S7D
-浜测实脸
至少需釆集昶数
术果
「理论根按转速女
戟荷
rpm
展存
预存数毎
4+算箱杲
实际摩攥黑数
理论摩攧甭救1:
平沟压力MPa
实验机构瑟墩
轴承直径!
70二|棚
轴瓦宽度|125iran相刑间晾oopi-
润滑油粘度0审
复宜
其測曲线
淫论曲皴|摩捺特性溟验
压力分布实验
打即
追岀
册勝
计茸
(附图2)
附录2、有限宽轴承的承载量系数CP表
0.30.4
0.5
0.G
0.65
0.7
0.750,8①西0.9
695
0.9?
祇載量帘截即
Q.3
07fli522C.082&
0.S28
1L
C.S590.347
3,4750.659L122
J?
M4
E,73
0,4
0.0893Cl14:
0,21f.
0.339
C.4^l0.ST3
17751.0791.775
3.195
S.3^3
65.联
D.1330.2C9
0.Sl^
0.強3
0.S22p,819;
1.M81.5722.428
4,216
10.TO«
75.se
0.6.
a诫o.its
中
0.tit
.C.SJ192.0?
1.41J2.001工窓
S.214
12,64
-3.21
L.7
0l2340*361
匕538
:
■:
;a
1.014LSlg
L722.3993.72
6.029
214
819
還
0,28?
0.43&
0.tr
0.彗2
1.1991.533
17^52.诚4.0=3
6.721
15.37
找託
0.9
C.3390.515
a754
1.113
1.3711.745
Z2483.0674.459
L294
16.37
96.35
1.0
a3910,589
Q.S&3
1.253
1.528基磁
2.4«93,3724,808
L7T2
IL13
93.9E
1,1
0.440.&bB
o.yrf
1.377
1.6692.097
'L56^3.5B5.106
y.3i6
17.BS
101.15
1>2
C.4370.723
1.033
1.48?
1.796£2好
Z.333二TSTN冀4
8.533
IS.C3
LO工?
1.3
C.5290・吒4
1,111
1.59
1.9L22.3TD
缶舗3.^685.&:
6
8.831
13.&1104.42
1.5
0.610.851
1.248
1.7&3
2.2.6
3.2424.26&5.947
9”驱
i9.es
1佩嗣
2・Q
17631+O9l
L483
2.t)7
二4誌2.931
3.67:
4.T78&闊£
inT09i
iia#9
六、思考题
1为什么油膜压力曲线会随转速的改变而改变?
2、为什么摩擦系数会随转速的改变而改变?
3、哪些因素会引起滑动轴承摩擦系数测定的误差?
七、实验报告
专业班级姓名
指导老师日期
〈一〉实验目的
〈二〉实验机构及测试原理图
〈三〉实验步骤
〈四〉数据和曲线
1实验数据记录
滑动轴承压力分舟
—
载荷
转速
斥力表号|
1
2
3
4
5
6
Ll>
8
Frl
nl
n2
Fr2
nl
n2
滑功丹虞悴瘵系敌(转速网运.我荷变化)
转速tr/min)
摩擦
烽莖乐数i
nii/p
I
3
J
"3"
6
~