工序检验规程1.docx
《工序检验规程1.docx》由会员分享,可在线阅读,更多相关《工序检验规程1.docx(13页珍藏版)》请在冰豆网上搜索。
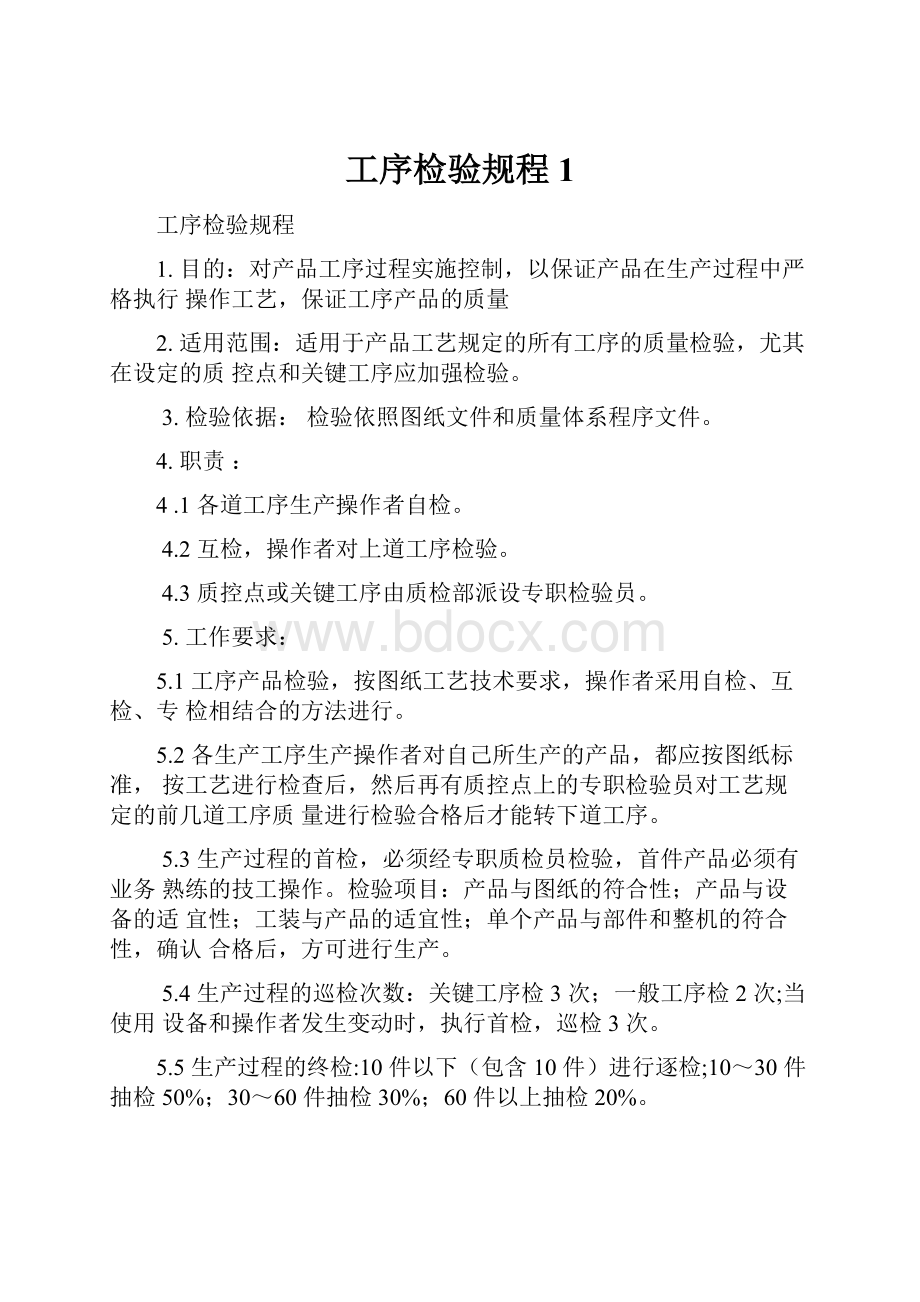
工序检验规程1
工序检验规程
1.目的:
对产品工序过程实施控制,以保证产品在生产过程中严格执行操作工艺,保证工序产品的质量
2.适用范围:
适用于产品工艺规定的所有工序的质量检验,尤其在设定的质控点和关键工序应加强检验。
3.检验依据:
检验依照图纸文件和质量体系程序文件。
4.职责:
4.1各道工序生产操作者自检。
4.2互检,操作者对上道工序检验。
4.3质控点或关键工序由质检部派设专职检验员。
5.工作要求:
5.1工序产品检验,按图纸工艺技术要求,操作者采用自检、互检、专检相结合的方法进行。
5.2各生产工序生产操作者对自己所生产的产品,都应按图纸标准,按工艺进行检查后,然后再有质控点上的专职检验员对工艺规定的前几道工序质量进行检验合格后才能转下道工序。
5.3生产过程的首检,必须经专职质检员检验,首件产品必须有业务熟练的技工操作。
检验项目:
产品与图纸的符合性;产品与设备的适宜性;工装与产品的适宜性;单个产品与部件和整机的符合性,确认合格后,方可进行生产。
5.4生产过程的巡检次数:
关键工序检3次;一般工序检2次;当使用设备和操作者发生变动时,执行首检,巡检3次。
5.5生产过程的终检:
10件以下(包含10件)进行逐检;10~30件抽检50%;30~60件抽检30%;60件以上抽检20%。
5.6质检员在生产过程中对每件产品作好首件检查、巡检、完工检,对每道工序所出现的问题及时处理,并作好记录。
记录应详实清楚。
5.7当发现严重不合格品时用红色油漆笔点圆点,做检验状态标识,检查员可直接开具《废品单》作好隔离。
对返修产品开具《返工返修单》做绿色油漆笔点圆点,不能决定时,应通知责任单位填写《不合格品评审处置单》进行评审。
评审结论确定为返工、返修的产品,由责任单位及时进行返工、返修。
5.8返工、返修的产品由操作者自检后进行交检。
检查员根据《不合格品评审处置单》复检后,确认为合格品的,由检查员用黄色油漆覆盖原检验标识。
并填写《不合格品评审处置单》和《检验记录》,注明合格数量。
5.9根据《不合格品评审处置单》要求,执行让步接收/降级使用的产品复查合格的,质检员用蓝色油漆覆盖原检验标识,并在《不合格品处置单》注明让步接收/降级使用数量。
复检结论不符合处理要求的,由检查员再次出具《返修/返工单》,用绿色油漆笔点圆点,作好检验状态标识,并签字盖章执行《不合格品控制程序》。
5.10上道工序的不合格品不允许转下道工序,如需转工序待处理完后,由质检员复查后合格,方可转工序。
5.11生产完的产品在检查员检验后,填写《生产过程检验记录》做好产品标记和状态标识,对废品隔离存放,合格品入库。
6.公司规定的关键工序为:
6.1主轴、卷筒、齿轮架的精车工序
6.2齿轮架、箱体的镗、铣工序
6.3底座的焊接工序
6.4制动装置及提升绞车的主轴装置、调度绞车、运输绞车、回柱绞车、双速绞车、慢速绞车的卷筒装置和回柱、慢速、双速绞车的减速箱装置组装工序
6.5整机试车工序
7.关键工序的检验
7.1主轴、卷筒、齿轮架的精车工序和齿轮架、箱体的镗、铣工序的检验
7.1.1检验依据和检验工具
7.1.1.1检验依据:
图纸和相关技术标准;图纸未标注公差范围而标注公差等级的按照标准GB/T1804-2000执行,我公司执行m级见表1所示。
表1线性尺寸的极限偏差数值mm
公差等级
基本尺寸分段
0.5-3
>3-6
>6-30
>30-120
>120-400
>400-1000-
>1000-2000
>2000-4000
精密f
±0.05
±0.05
±0.1
±0.15
±0.2
±0.3
±0.5
--
中等m
±0.1
±0.1
±0.2
±0.3
±0.5
±0.8
±1.2
±2
粗糙c
±0.2
±0.3
±0.5
±0.8
±1.2
±2
±3
±4
最粗v
--
±0.5
±1
±1.5
±2.5
±4
±6
±8
7.1.1.2检验工具:
千分尺、游标卡尺、卡尺、深度尺、百分表、检验台、仪器等。
7.1.2检验规程及判定准则
7.1.2.1关键工序的零件工序完工后由专职检验员实行全检
7.1.2.2将图号与实物核实,认真阅读图纸及相关技术要求。
7.1.2.3外观检验:
检验加工件表面应无毛刺、尖角、飞边、裂纹、加工表面无黑皮、表面无锈迹。
铁屑应清理干净。
否则判为不合格品.
7.1.2.4尺寸及形位公差和表面粗糙度检验:
按图纸及相关技术标准标注的公差范围进行检验,在公差范围内的判定合格,超出公差范围的判定不合格。
每种规格工序产品每道每次检验测量尺寸不得少于三次,同批次、图号的产品要求公差范围控制的一致性。
7.2底座的焊接工序的检验
7.2.1检验依据和检验工具
7.2.1.1检验依据:
图纸和相关技术标准;图纸未注尺寸公差与形位公差应符合表2-表4的规定:
焊接件尺寸偏差应符合表2的规定
表2mm
基本尺寸
用于切削加工
用于不需要切削加工
极限偏差
≦500
±1.5
±2.5
>500—1000
±2.0
±3.0
>1000—1600
±2.5
±3.5
>1600—2500
±3.0
±4.5
>2500—4000
±4.0
±6.0
>4000—6300
±5.0
±7.5
>6300
±6.0
±9.0
焊接件尺寸偏差应符合表3的规定
表3
尺寸范围(短边长度)/mm
极限偏差
≦315
±60′
>315—1000
±45′
>1000
±30′
焊接件的的平面度公差,以及有关部位的同轴度、垂直度、对称度和平行度的公差应符合4的规定
表4
基本尺寸
平面度
同轴度、垂直度、对称度
平行度
≦500
2.0
2.5
5.0
>500—1000
3.0
3.0
6.0
>1000—1600
4.0
3.5
7.0
>1600—2500
5.0
4.5
9.0
>2500—4000
6.0
6.0
12.0
>4000—6300
7.0
7.5
15.0
>6300
8.0
9.0
18.0
7.2.1.2焊接件焊后消除应力处理按图样及工艺文件的规定
7.2.1.3检验工具:
钢卷尺、万能量规、游标卡尺、低倍放大镜、检验台等。
7.2.2检验规程及判定准则
7.2.2.1关键工序的零件工序完工后由专职检验员实行全检
7.2.2.2将图号与实物核实,认真阅读图纸及相关技术要求。
7.2.3焊接检验分为如下三种
a)焊前检验;
b)焊接过程检验;
c)焊后成品检验。
7.2.3.1焊前检验的项目、检测内容与检测方法如下表:
项目
检验内容
检验方法
焊条
外观质量
用目测药皮是否牢固,紧贴在焊芯上并有一定强度。
药皮应无裂纹、气孔肿涨和未调匀的药团。
外观检查后核实焊条型号、规格。
焊丝
焊丝直径、外观质量
用目测焊丝应无氧化皮、锈、油污。
用卡尺检查焊丝直径
施焊
焊件
a待焊件焊接部位不许有锈、油漆、氧化物、毛刺和影响焊接的镀层;
b焊接坡口处边缘应均匀一致,坡口开头和尺寸应符合图样要求;
c暂焊点分布合理,不能分布在应力集中处;
d暂焊点不允许有烧穿、裂纹、未焊透和气孔等缺陷,如发现这些缺陷应在焊接前排除
a目测
b对坡口尺寸、形状按图样要求用标准样板或焊接检验尺测量。
c目测
d目测
7.2.3.2焊接过程检验的项目、检测内容与检测方法:
焊件的首件应进行首检,在焊接过程中还应对焊接设备运行情况、焊接规范进行检验。
焊接多层焊时,每焊完一道焊缝要进行质量检查和清渣检验。
同时对已焊的零件进行全检,及时发现问题,及时解决。
项目
检验内容
检验方法
外观检查
1.焊缝尺寸是否符合图样要求,焊缝表面有无裂纹等不允许的缺陷;
2外观质量
1.严格按图纸制作,加工件需预留加工量。
2.角焊高要达到6mm。
平焊宽7mm,焊高3mm,直线宽1mm以内。
3.工件外表打磨光滑、平整、锐边倒角。
4.气割渣、焊渣必须清理干净。
5.气割直线度,垂直度在1mm内。
6.属于重型工件,必须开坡口焊接。
7.工件不能有裂纹、气孔、夹渣等缺陷。
8.焊缝成型美观正常,不允许有弧坑、焊缝间断、烧穿和裂纹存在。
9.补焊件在补焊前,必须先把缺陷处彻底铲除干净,再进行补焊。
10.所有焊接件的尺寸变形量不得大于加工余量的1/3—1/2
1.万能量规,检测焊缝尺寸;低倍放大镜检验外观缺陷;
2.目测凡一项不符合要求即判为不合格品
7.2.3.3焊后成品检验的项目、检测内容与检测方法如下表
项目
检验内容
检验方法
外观检查
1.严格按图纸制作,加工件需预留加工量。
2.角焊高要达到6mm。
平焊宽7mm,焊高3mm,直线宽1mm以内。
3.工件外表打磨光滑、平整、锐边倒角。
4.气割渣、焊渣必须清理干净。
5.气割直线度,垂直度在1mm内。
6.属于重型工件,必须开坡口焊接。
7.工件不能有裂纹、气孔、夹渣等缺陷。
8.焊缝成型美观正常,不允许有弧坑、焊缝间断、烧穿和裂纹存在。
9.补焊件在补焊前,必须先把缺陷处彻底铲除干净,再进行补焊。
10.所有焊接件的尺寸变形量不得大于加工余量的1/3—1/2
目测凡一项不符合要求即判为不合格品
焊缝质量
1.焊缝不允许出现烧穿、裂纹、间断、凹坑等缺陷;
2.重要的承载焊缝在任意100mm长度上直径不大于2mm的气孔不得多于1个;
3.重要的承载焊缝未焊透深度不得大于较薄母材壁厚的15%;
4.重要的承载焊缝其咬边长度不得超过焊缝全长的10%,咬边深度应不大于如下的规定:
较薄母材壁厚≦10mm,咬边深度≦0.5mm
较薄母材壁厚>10-40mm,咬边深度≦1mm
5.对接焊缝的错边量不得大于板厚的四分之一,且最大不得超过2mm.
目测及游标卡尺测量
凡一项不符合要求即判为不合格品
7.3制动装置及提升绞车的主轴装置、调度绞车、运输绞车的卷筒装置和回柱、慢速、双速绞车的减速箱装置组装工序
7.3.1制动装置组装工序的检验
7.3.1.1检验依据和检验工具
7.3.1.1.1检验依据:
图纸和相关技术标准
7.3.1.1.2检验工具:
塞尺、游标卡尺、深度尺、钢卷尺、检验台
7.3.1.2检验规程及判定准则
7.3.1.2.1关键工序的零部件工序完工后由专职检验员实行全检
7.3.1.2.2将图号与实物核实,认真阅读图纸及相关技术要求。
7.3.1.2.3刹车块无缺损,无断裂,表面无油迹
7.3.1.2.4铆钉头端面距离石棉带表面距离不小于2.5mm
7.3.1.2.5销轴润滑良好,不松旷,操作机构和传动杆件动作灵活
7.3.1.2.6制动器在放松状态时,制动衬面与制动轮之最小间隙为0.5-1毫米
7.3.1.2.7施闸手柄、以及重锤等的施闸工作行程都不得超过各自容许全行程的3/4
7.3.1.2.8摩擦接触面积应符合如下规定:
提升绞车不小于总摩擦面积的70%
调度绞车、双速绞车、回柱绞车、慢速绞车不小于总摩擦面积的80%
运输绞车不小于总摩擦面积的75%
以上检验项目如有一条不合格即判为制动装置不合格
7.3.2提升绞车主轴装置组装工序的检验
7.3.2.1检验依据和检验工具
7.3.2.1.1检验依据:
图纸和相关技术标准
7.3.2.1.2检验工具:
塞尺、游标卡尺、百分表、检验台
7.3.2.2检验规程及判定准则
7.3.2.2.1关键工序的零部件工序完工后由专职检验员实行全检
7.3.2.2.2将图号与实物核实,认真阅读图纸及相关技术要求。
7.3.2.2.3制动盘的摩擦面不能有锈蚀、裂纹及碰伤
7.3.2.2.4卷筒与与卷筒盘、卷筒制动盘必须贴合紧密无间隙
7.3.2.2.5闸轮的圆跳动应不大于0.1mm,制动盘轮缘的端面跳动量应不大于0.2mm
以上检验项目如有一条不合格即判为主轴装置不合格
7.3.3调度绞车、运输绞车、回柱绞车、双速绞车、慢速绞车卷筒装置组装工序的检验
7.3.3.1检验依据和检验工具
7.3.3.1.1检验依据:
图纸和相关技术标准
7.3.3.1.2检验工具:
塞尺、游标卡尺、百分表、深度尺、检验台
7.3.3.2检验规程及判定准则
7.3.3.2.1关键工序的零部件工序完工后由专职检验员实行全检
7.3.3.2.2将图号与实物核实,认真阅读图纸及相关技术要求。
7.3.3.2.3绞车挡绳板轮缘高出最外一层钢丝绳的高度,至少应为钢丝绳直径的2.5倍
7.3.3.2.4绞车钢丝绳头固定在卷筒上,应有特备的卡绳装置,不能系在卷筒轴上,穿绳孔槽的方向应与卷筒绕绳方向一致,绳孔不得有锐利边缘钢丝绳的弯曲不能形成锐角
7.3.3.2.5卷筒上的螺钉不得高出卷筒圆周表面
7.3.3.2.6绞车卷筒两端挡绳板轮缘的表面粗早读应不大于50μm
7.3.3.2.7卷筒装配前必须将卷筒内部非加工表面的粘沙、氧化皮、铁锈等清除干净并涂以耐油防锈漆
7.3.3.2.8卷筒装配后应转动灵活不得有卡阻现象
7.3.3.2.9轴承内应注入适量的锂基润滑脂
以上检验项目如有一条不合格即判为卷筒装置不合格
7.3.4回柱、慢速、双速绞车的减速箱装置组装工序
7.3.4.1检验依据和检验工具
7.3.4.1.1检验依据:
图纸和相关技术标准
7.3.4.1.2检验工具:
塞尺、游标卡尺、百分表、深度尺、红丹粉、检验台
7.3.4.2检验规程及判定准则
7.3.4.2.1关键工序的零部件工序完工后由专职检验员实行全检
7.3.4.2.2装配前的要求:
a.滚动轴承用汽油清洗其他零件用煤油清洗
b.箱底用煤油侵蚀法检查有无渗漏现象,如有渗漏现象禁止使用做不合格品处理
c.所有零件和箱体内不许有任何杂质存在,箱体内壁和齿轮(蜗轮)等未加工表面先涂两遍耐油防锈漆,箱体外表面应打磨平整干净,无粘沙,飞边,毛刺等
e.零件配合面洗净后涂以润滑油
7.3.4.2.3安装和调整要求
a.滚动轴承的安装,滚动轴承安装时轴承内圈应贴紧轴肩,之间的间隙不大于0.05毫米
b.轴承间的游隙应在0.06到0.20毫米之间
c.齿轮接触斑点,用红丹粉检查锥齿轮沿齿面和齿长都不小于60%,圆柱齿轮沿齿高不小于45%,沿齿长不小于50%
d.闭式圆柱齿轮侧隙为0.25毫米,开式圆柱齿轮侧隙为0.30毫米
e.蜗轮接触斑点沿齿高不小于70%,沿齿宽不小于25%
f.蜗轮副的侧隙在0.42-0.55毫米
g.蜗轮副组合后,蜗杆螺牙接触斑点的长度为整个螺牙长度的40%-70%,且蜗杆螺纹接触斑点不应达到接近螺纹长度的10%的螺纹入口端(即在上述规定的范围内入口处不允许有螺纹接触斑点)
h.各滚动轴承内加入锂基脂,加入量不得超过容量的2/3,减速箱内加入CKC150号工业齿轮油
7.3.4.2.4密封要求
a.箱体剖分面之间不允许填任何垫片,但可以涂密封胶以保证密封
b.装配时再拧紧螺栓前应检查箱盖和箱底之间的密封性,应小于0.05毫米
c.轴伸密封处应涂以润滑油,各密封装置应严格按照要求安装
7.3.4.2.5组装完成后:
a.空负荷运转应灵活,无卡滞现象,带变速的绞车变速手把应扳动灵活闭锁可靠
b.空负荷试车应运转平稳无异常声响和振动,噪声应符合相关标准的规定
c.各密封处应无渗漏现象
d.各紧固件应连接可靠无松动现象
以上检验项目如有一条不符合要求即判为减速箱装置不合格
7.4整机试车工序
7.4.1按照出厂检验规程的要求对组装好的整机进行逐台试车检验
成品检验员必须经本岗位培训,考试合格后方可上岗。
7.4.2最终检验前,必须将所有规定的检验(包括进货和过程)均已完成,且结果满足规定要求时,才能进行最终检验。
7.4.3成品检验以产品技术条件、产品检验细则和有关国家标准为依据,所用的检测器具、检测设备必须是经检定合格的且在周检期内。
产品执行零缺陷的规定。
7.4.4检验与记录
7.4.4.1检验人员按《成品检验规程》检验项目和方法逐项检验,不得漏项漏检。
7.4.4.2成品检验记录书写要清晰、工整,填写内容完整、齐全。
检验记录作为该批次产品的质量技术档案要长期保存,以保持其可追溯性。
一般保留期为二年,顾客有要求的或特殊使用的产品检验记录,要长期保留或按顾客要求保留