高速加工高级应用之编程策略培训纲要.docx
《高速加工高级应用之编程策略培训纲要.docx》由会员分享,可在线阅读,更多相关《高速加工高级应用之编程策略培训纲要.docx(15页珍藏版)》请在冰豆网上搜索。
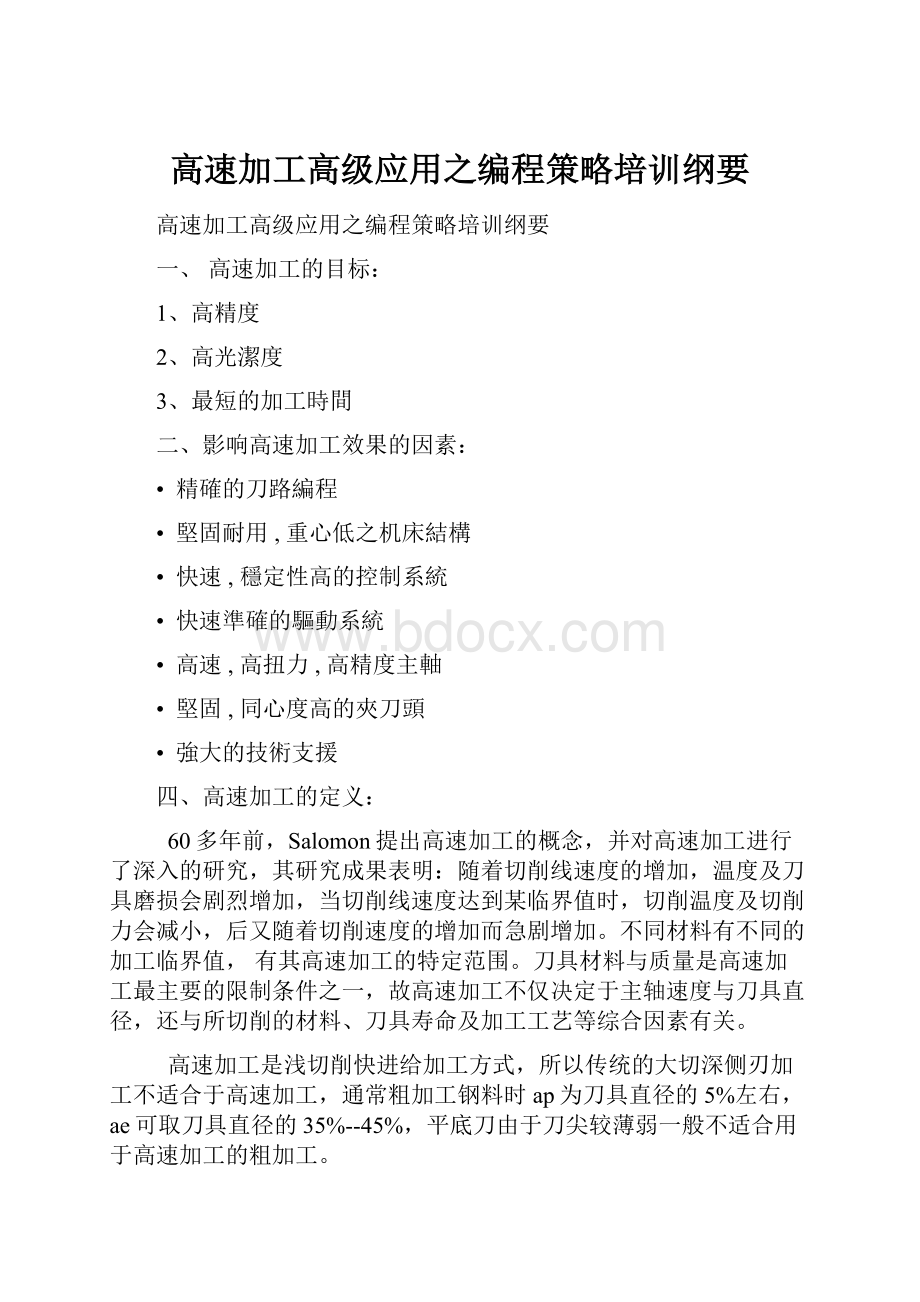
高速加工高级应用之编程策略培训纲要
高速加工高级应用之编程策略培训纲要
一、高速加工的目标:
1、高精度
2、高光潔度
3、最短的加工時間
二、影响高速加工效果的因素:
•精確的刀路編程
•堅固耐用,重心低之机床結構
•快速,穩定性高的控制系統
•快速準確的驅動系統
•高速,高扭力,高精度主軸
•堅固,同心度高的夾刀頭
•強大的技術支援
四、高速加工的定义:
60多年前,Salomon提出高速加工的概念,并对高速加工进行了深入的研究,其研究成果表明:
随着切削线速度的增加,温度及刀具磨损会剧烈增加,当切削线速度达到某临界值时,切削温度及切削力会减小,后又随着切削速度的增加而急剧增加。
不同材料有不同的加工临界值,有其高速加工的特定范围。
刀具材料与质量是高速加工最主要的限制条件之一,故高速加工不仅决定于主轴速度与刀具直径,还与所切削的材料、刀具寿命及加工工艺等综合因素有关。
高速加工是浅切削快进给加工方式,所以传统的大切深侧刃加工不适合于高速加工,通常粗加工钢料时ap为刀具直径的5%左右,ae可取刀具直径的35%--45%,平底刀由于刀尖较薄弱一般不适合用于高速加工的粗加工。
五、涂层可延长刀具的使用寿命:
涂层材料
涂层材料须具有硬度高、耐磨性好、化学性能稳定、不与工件材料发生化学反应、耐热耐氧化、摩擦因数低,以及与基体附着牢固等要求。
显然,单一的涂层材料很难满足上述各项要求。
所以硬质涂层材料已由最初只能涂单一的TiC、TiN、Al2O3,进入到开发厚膜、复合和多元涂层的新阶段。
新开发的TiCN、TiAlN、TiAlCN多元、超薄、超多层涂层与TiC、TiN、Al2O3等涂层的复合,加上新型的抗塑性变形基体,在改善涂层的韧性、涂层与基体的结合强度、提高涂层耐磨性方面有了重大进展。
目前,又突破了在硬质合金基体上涂覆金刚石薄膜技术,全面提高了刀具的性能。
工艺最成熟和应用最广泛的硬质涂层材料是TiN,但TiN与基体结合强度不及TiC涂层,涂层易剥落,且硬度也不如TiC高,在切削温度较高时膜层易氧化而被烧蚀。
TiC涂层有较高的硬度与耐磨性,抗氧化性也好,但其性脆,不耐冲击。
TiCN兼有TiC和TiN两种材料的优点,它在涂覆过程中可通过连续改变C、N的成份控制TiCN性质,并形成不同成份的多层结构,可降低涂层的内应力,提高韧性,增加涂层的厚度,阻止裂纹的扩展,减少崩刃。
TiCN基涂层适于加工普通钢、合金钢、不锈钢和耐磨铸铁等材料,用它加工工件时的材料切除率可提高2~3倍。
TiAlN、CrC、CrN、TiAlCN是近几年来开发的硬质涂层新材料。
TiAlN涂层刀片已商品化。
它的化学稳定性和抗氧化磨损性能好,用其加工高合金钢、不锈钢、钛合金和镍合金时的刀具寿命可比TiN涂层高3~4倍。
此外,TiAlN涂层中如果有合适的铝浓度,切削时在刀具前刀面和切屑的界面上还会产生一层硬质的惰性保护膜,该膜有较好的隔热性,可更有效地用于高速切削。
TiAlN涂层,是专为高速铣削合金钢、高合金钢和不锈钢等高性能材料而设计的。
CrC和CrN是一种无钛涂层,适于切削钛和钛合金、铜、铝以及其它软材料,化学稳定性好,不产生粘屑。
TiAlCN是一种梯度结构涂层,不仅具有高的韧性和硬度,而且摩擦因数也较小,适用于铣刀、滚刀、丝锥等多种刀具,切削性能明显优于TiN。
六、从切屑颜色一判别切削区域温度的高低:
切屑温度由到高的颜色是:
白色、金黄色、紫色、蓝色、黑色,紫色是较合适的温度。
七、模型精度不足是产生刀痕的主要原因:
CAD模型的精度必须高于CAM系统的精度,尤其是在高速铣时更应提高CAD模型的精度。
高速铣的优势之一就是表面精度高,但其前提条件是有一个高精度的模型。
精度的影响
加工精度高、热分布小和加工表面质量高,均是高速加工的优势;却看到一个奇怪的现象∶用於建立零件模型的公差,比最终的加工公差为大。
数据交换是影响精度问题的根本原因。
零件通常由一个CAD系统设计,然后转换至另一个CAD系统进行补充设计和加工准备。
每次进行数据传输时,都需要将几何形体由一种格式转换至另一种格式,有些转换涉及按极限公差近似。
由於这些公差属於累积,设计零件模型时必须将零件模型的公差,设定为最少比精加工公差小十倍。
八、加工策略的基本点是:
尽可能地保持刀具负荷的稳定,从而最大限度地延长刀具的使用寿命;尽可能地减少任何切削方向的突然变化,从而尽量减少切削速度的降低。
要满足上述的这些条件,则在粗加工中,必须使用环绕加工策略,而不是使用传统的平行加工策略。
粗加工中最好使用顺铣,因为使用顺序可减少刀具磨损。
高速铣削编程时需要注意的几个原则:
a.高进给,高转速,低切削量是基本原则
b.开粗时使用螺旋进刀,螺旋角度3º-5º,螺旋半径大于刀具半径,螺旋高度大于每层切深0.5-1mm
c.应尽量沿工件较长的方向走刀,减少换向次数和空刀
d.应保持刀具轨迹的平滑与平稳过渡,切削方向(顺铣/逆铣)应保持恒定,应避免切削方向突然变化,避免突然加速或减速,从而尽量减少切削速度的降低
e.尽量采用两轴联动,以减小程序量,提高数控系统的处理速度,加快加工速度
f.除非情况必须如此,否则仍应避免全力宽切削。
g.残余量加工或清根加工是提高加工效率的重要手段,一般应采用多次加工或采用系列刀具从大到小分次加工,直至达到所需尺寸,避免用小刀一次加工完成。
h.切削角落时,刀具半径应相对小于角落半径,以保持最大接触距离小于切削刀具周长的30%以下。
这样可使刀具得到足够的冷却,同时避免刀具进入角落时刀具负荷的突然增加及摩擦增加,引起弹刀等不利现象。
九、高速加工中碰到的一些问题:
1.什么是高速切削?
2.高速切削的要求?
3.什么是重切削及轻切削和有效切削?
4.高速加工的最终目的.
1.什么是高速切削?
高速切削是一种把CNC(加工中心)生产能力提至另一层次的一种新的加工方式.如精确度,加工时间,表面度及加工工件硬度等都大大提高了其生产效率,减少了很多不必要工序,如EDM(火花机),磨床..等等及工件亦能够在经过热处理(Hrc68以下)后再次加工.所以High-SpeedCNC是CNC加工的新方向!
2.高速切削的要求
CAD/CAM程式
在CAD/CAM的技巧不断提升时,我们亦要求了很多不同绘图技术及加工技术,绘图技术一般都是软件提供,然后经过人员的熟练度发挥出来的,只要对图形图纸了解就可以了,而加工技术不但需要人员对图形的了解,而且要求了解刀具,工件,机床…等等的一些问题,所以在普通CNC加工时遇不到的问题会在高速CNC加工时遇到,而且会有很严重的后果!
另外大家都会发现程式容量越来越大,因为程式的加工方式,精度要求和加工零件的复杂度亦提高了很多,自然程式容量也提高了,所以现代机床必须要有大容量的硬盘才能解决程式容量的问题.在减少程式容量,还有Nurbs,它能把程式容量减少80%以上,但它只对Spline的零件才有效,直线和圆是没有太大的效果.
3.什么是重切削及轻切削和有效切削?
重切削是一种高切削量,低切削转速及切削速度的一种加工方式.一般都应用于旧式加工中心及粗加工中.
好处:
1.一般程式上没有限制.2.大的切削量.3.刀具没有限制.
4.不需要理会程式(加工方式)
坏处:
1.低精确度.2.加工时间长.3.表面度差.4.不能加工高硬度工件.
5.对机床伤害度高.6.需要承受较大的压力.
轻切削是一种低切削量,高切削转速及切削速度的一种加工方式.一般都应用于新式加工中心及精加工.
好处:
1.高精确度.2.加工时间短.3.表面度好.4.能加工高硬度工件.
5.对机床伤害度低.
坏处:
1.程式很多的限制.2.不能大量切削.3.刀具上有限制.
有效切削是重切削和轻切削的混合体,是一种高切削量和切削速度的加工方式.一般使用于粗加工上,但要使用有效切削必须要注意刀具和程式的配合,还有机床的稳定和主轴的转速.
好处:
1.加工时间短.2.能加工高硬度工件.
坏处:
1.程式很多的限制.2.刀具上有限制.3.要求机床的稳定性较高.
4.高速加工的最终目的.
高速加工的最终目的是提高生产效率,减少不必要的工序,
降低成本..等等的加工方式.
精密切削注意事项
1.在一般的精密加工过程中,我们需要注意加工时的刀具、工件和程式,这些可以改变精度的参数。
2.刀具---刀补是调动精度的好帮手。
3.工件---它的摆动会把精度带走。
4.程式---它是灵魂,可以改变工件的精度、表面粗糙度、垂直度等,一些重要的参数。
5.铁屑----它是伤害刀具的主要原因。
夹具(Fixture)
1.夹具的设定亦是非常重要的,它是控制加工时工件的稳定性。
因为没有一个夹具是可以夹住任何的工件,所以一般我们都需要做一些专用夹具。
2.夹具的设定必须配合加工的刀路。
3.设定夹具时必须注意会否导致工件变形。
4.注意定位位置。
5.注意是否每个切削面都是平均受力。
切削金属
Aluminums(铝):
是一种容易切削的材料但亦比较软。
Copper&Brass(铜):
是一种容易切削的材料,本身亦比较脆。
Steel(钢):
耐磨性比较高,亦需要注意不同的材料成份。
HardenedSteel(超硬钢):
硬度高、较脆,60~68Hrc时是一种比较难加工的材料。
良好的刀具使用方法
1.直角刀---尽量使用在垂直面切削。
2.球头刀---一般使用在粗糙平面、精准斜面及曲面等加工面。
3.平低弧角刀---一般使用在粗削与精削中的平面、斜面及曲面等加工面。
4.刃数越多表面度越好,但转数需要减少。
5.软的金属使用刃数较少的刀具,硬的金属使用刃数较多的刀具。
6.切削一些较硬的钢材,使用有涂层的刀具。
7.使用一些少于内弧位的刀具(r<=0.7R)。
良好的切削条件
1.使用顺铣(Downcut)。
2.使用比较短的刀具。
3.减少切削量。
4.使用一些少于内弧位的刀具。
5.切削高硬度工件时,使用多刃数的刀具。
6.切削低硬度工件时,使用少刃数的刀具。
7.需要有一个平均的切削量。
8.小心全直径(Full-Diameter)切削。
如有把Feedrate调低。
机床和程式
一般编程人员认为在程式上把精度(tolerance)改小,就能提高加工零件的精度,或光洁度。
但这只能提高程式上的精度,而没有提高加工零件的精度或光洁度,因为在机床上亦提供了增加其精度(tolerance)的功能,我们亦需要相对的把机床的精度改小,才能加工出高精度,高光洁度的零件。
机床应用
一般应该具备的功能
1.巧玲珑轴(Spindle):
主轴转数的高低直接影响加工材料的光洁度及使用的刀具大小。
2.光栅尺(GlassScale):
动态加工时的进刀、出刀及其精度的控制。
3.机床结构:
加工时机床是否有摆动。
4.处理系统:
处理数据的速度、刀具数字库和模拟预试。
5.辅助工能:
Nurbs,中心运水/气,测量系统。
主轴(Spindle)
一般主轴都分为合金珠主轴,陶瓷主轴及气动主轴。
合金珠主轴
陶瓷主轴
气动主轴
转速比
低速转动
高速转动
极速转动
主轴扭力
大
小
极小
切削方式
大量切削
有效切削
近乎磨
加工方式
粗、精加工
粗、精加工
精加工
合适刀具
ø1mm以上
ø0.06mm~ø16mm
ø0.3mm~ø8mm
处理系统
每一种机床都有自己不同的操作系统,但是最基本的要求是系统处理数据后和传输到加工接收的数据速度配合,因为现时有很多机床都有传输速度太慢,导致切削刀路有间歇跳动,加工后的零件有振纹,亦会对刀具和主轴做成损伤,所以一个完善的系统是很重要的。
机床的要求
以下是旧式机床和现代机床的比较:
旧式机床
新式机床
传输方式
DNC,磁碟,手动
DNC,磁碟,手动,NETWORK
处理数据
DNC,磁碟
硬盘,DNC
座标储存
6个
255个
磁碟容量
516K(小容量)
2GMB(大容量)
模拟器
附加
基本
对刀器/仓库
附加
基本
要求精度
±0.01mm
±0.005mm
程序容量
100k(小容量)
1MB(大容量)
Nurbs
附加
基本
冷却液(水/油)
坏处:
1种类多,效果不一至。
2会把涂层刀具使用寿命缩
短。
3主轴转速高,易起雾。
4使用油性冷却液时,小心切削过热导致燃烧。
好处:
1效果佳。
2深孔加工,效果好。
3油性冷却液使用寿命
长及臭味低。
油雾
坏处:
1价格比价高。
2深孔加工,效果差。
3有臭味。
4加工完成后,需要等雾气
散。
好处:
1涂层刀具使用寿命延长。
2可以提高高速加工的效果。
主轴运水
主轴运水是一种比较合适于深孔加工,而且是冷却液不能渗透的位置。
主轴运水的过程一般都是冷却液经过主轴中心刀夹中心刀具中心,然后到达削割口发挥冷却和排削的能力。
一般主轴运水是在加工深孔,如果在加工普通的加工上,主轴运水是发挥不到应有的冷却功效。
在立式CNC,因受到地心吸力的影响,在加工太深的孔时,冷却的能力及排削都发挥不了应有的功能。
但在卧式CNC,亦同样受到地心吸力的影响,但其功能没有减少,而冷却及排削效果都能发挥到应有的水准。
在主轴运水中,刀具需要特别加工多几个孔,所以成本成了它的绊脚石。
冷却方式
冷却方式
一般问题
冷却液
(水)
冷却液
(油)
气冷
油雾
主轴运水
平面加工(平)
最好
最好
最好
较好
一般
侧面加工(平)
最好
最好
最好
较好
一般
凹位加工(平)
最好
最好
最好
较好
一般
平面加工(高)
较差
较差
较差
最好
较差
侧面加工(高)
较差
较差
较差
最好
较差
凹位加工(高)
较差
较差
一般
最好
较差
孔穴加工
较差
较差
最差
最差
最好
温度的影响
一般来说温度是分为室温和机械温度,室温一是机床所在的空间,而机械温度一是机床加工时产生的温度,很多机床的致命点(如CNC,W/C,磨床,CMM…等等的高精密机床,因为热力会使物件燃烧外,还会影响物件膨胀幅度,因此在高精密加工中,我们要求平均的温度(CNC和磨床约是20°±5°,W/C和CMM等高精密机器约是20°±2°).
结论
主轴是高速加工中心的心脏,而处理系统是高速加工中心的脑部,机身是高速加工中心的身体,在高速加工时每一部分都是很重要的,不能只是提高了主轴的转速,而没有提高处理系统和机身的稳定性,因为每一部分都需要有相应的效能,才能发挥出机床的最佳效率.
加工时会出现的情况
1.刀具断裂
2.直角刀直角位破裂.
3.刀具磨损.
4.工件变形.
5.表面度差
6.工件磨损/
1.刀具断裂
1.1减少切削量
1.2.使用比较短的刀具.
1.3.增加油雾(或冷却液)压力.
1.4.检查工装尺寸.
1.5.增加主轴速度.
1.6.注意内弧位的切削量.
1.7.刀具是否已磨损.
2.直角刀直角位破裂
2.1注意进刀方式.
2.2减少切削量.
2.3合金刀具不能转速太慢.
2.4使用比较短的刀具.
2.5进刀角度.
3.刀具磨损
3.1减少主轴速度.
3.2增加切削量.
3.3使用有涂层的刀具.
3.4合金涂层刀具请勿使用冷却液.
3.5切削铝合金时请勿使用涂层的刀具.(除加工铝合金专用涂层外)
4.工件变形
4.1增加主轴速度.
4.2减少加工速度.
4.3减少切削量.
4.4增加油雾(或冷却液)压力.
4.5使用一些少于内弧位的刀具.
5.表面度差
5.1减少切削速度.
5.2增加主轴速度.
5.3夹具的稳定性.
5.4设定机床参数有问题.
5.5使用一些比较多刃数的刀具.
5.6使用一些Twistangle比较高的刀具.
6.工件磨损
6.1使用顺铣(Downcut).
6.2减少主轴速度.
6.3减少切削量.
6.4使用一些比较少刃数的刀具.
6.5使用比较短的刀具.
6.6使用一些直身的刀具.