锥齿轮轴加工工艺及及夹具设计.docx
《锥齿轮轴加工工艺及及夹具设计.docx》由会员分享,可在线阅读,更多相关《锥齿轮轴加工工艺及及夹具设计.docx(22页珍藏版)》请在冰豆网上搜索。
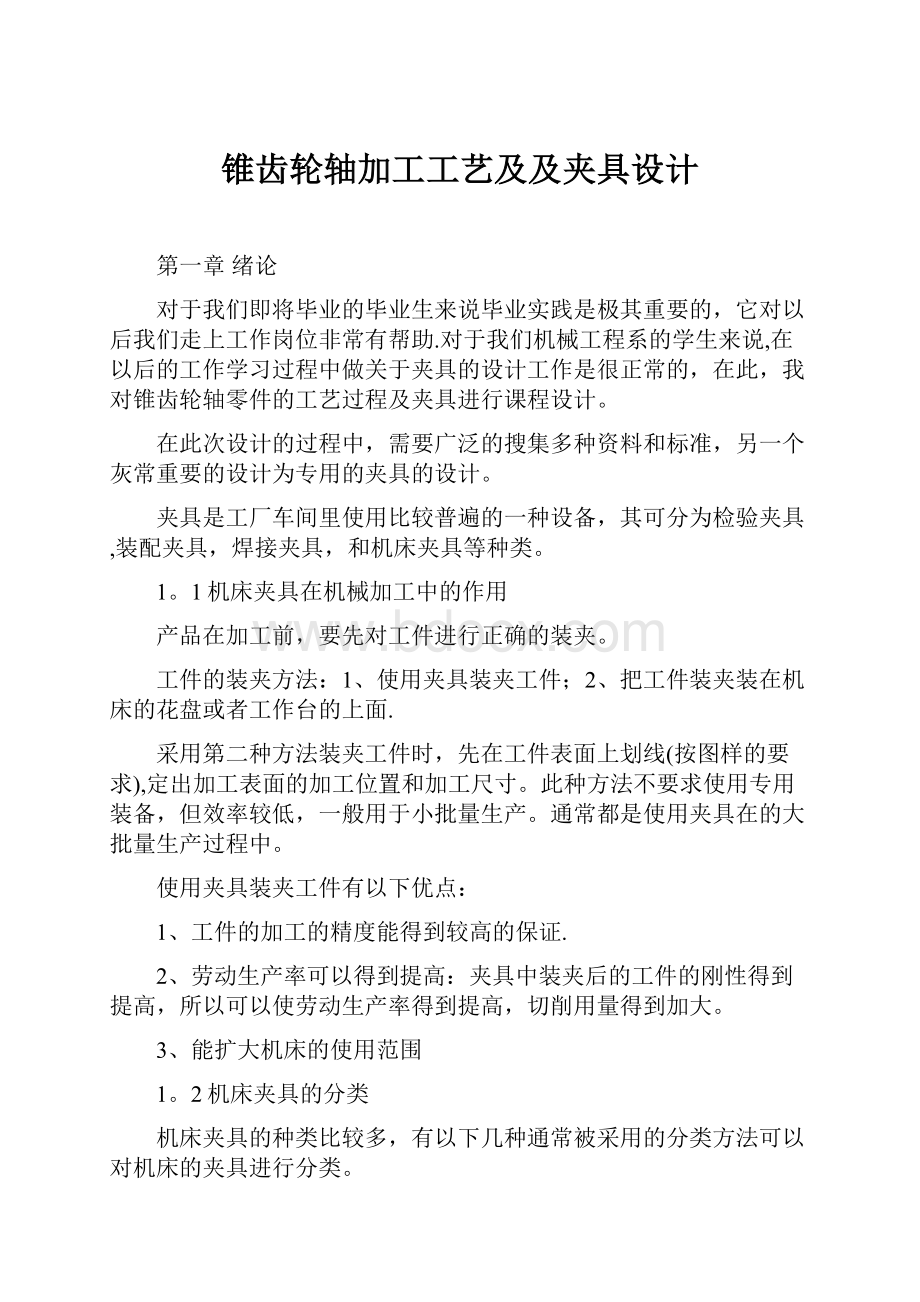
锥齿轮轴加工工艺及及夹具设计
第一章绪论
对于我们即将毕业的毕业生来说毕业实践是极其重要的,它对以后我们走上工作岗位非常有帮助.对于我们机械工程系的学生来说,在以后的工作学习过程中做关于夹具的设计工作是很正常的,在此,我对锥齿轮轴零件的工艺过程及夹具进行课程设计。
在此次设计的过程中,需要广泛的搜集多种资料和标准,另一个灰常重要的设计为专用的夹具的设计。
夹具是工厂车间里使用比较普遍的一种设备,其可分为检验夹具,装配夹具,焊接夹具,和机床夹具等种类。
1。
1机床夹具在机械加工中的作用
产品在加工前,要先对工件进行正确的装夹。
工件的装夹方法:
1、使用夹具装夹工件;2、把工件装夹装在机床的花盘或者工作台的上面.
采用第二种方法装夹工件时,先在工件表面上划线(按图样的要求),定出加工表面的加工位置和加工尺寸。
此种方法不要求使用专用装备,但效率较低,一般用于小批量生产。
通常都是使用夹具在的大批量生产过程中。
使用夹具装夹工件有以下优点:
1、工件的加工的精度能得到较高的保证.
2、劳动生产率可以得到提高:
夹具中装夹后的工件的刚性得到提高,所以可以使劳动生产率得到提高,切削用量得到加大。
3、能扩大机床的使用范围
1。
2机床夹具的分类
机床夹具的种类比较多,有以下几种通常被采用的分类方法可以对机床的夹具进行分类。
1通用夹具
通用夹具是指已经进行过标准化的,能够加工特定范围内的不同的种类工件的夹具。
2专用夹具
专用夹具是指专门为了特定的工件的某道指定的工序而进行设计制造出的夹具。
通常在批量生产过程中使用专用夹具。
3可调夹具
可调夹具是指夹具的某些元件可以更换或者可以调整,从而可以适应多种工件加工的夹具。
对其可以分作成组夹具和通用可调夹具两类。
4组合夹具
组合夹具是指采用标准化的组合而成夹具部件和元件。
5拼装夹具
拼装夹具是指专门运用的系列化和标准化的拼装夹具组合而成的夹具。
它的夹紧部件和基础板中通常装备着小型液压缸。
1.3机床夹具的组成
机床夹具的主要组成部分:
1定位装置作用是使工件在夹具中间占据正确的位置的设置被称作定位装置。
2夹紧装置作用是将对工件进行夹牢压紧,从而确保工件在加工过程不会因为受到外力的作用而离开开始占据的正确的定位的设置被称作夹紧装置.
3对刀或导向装置作用是确保被加工元件相对刀具的正确的加工位置的设置被称为向导或对刀装置。
4.连接元件连接元件是用来元件在机床上的正确位置的部件。
5。
夹具体夹具体是机床加工中的夹具的基本组成部件。
6.辅助装置和元件辅助装置和元件是指夹具中因不同的要求而安装的装置或元件。
1。
3本设计的任务
该设计的主要任务是:
对典型的夹具进行精度分析和结构的分析并且对工件的工艺规程进行设计。
第二章锥齿轮轴加工工艺规程的编制
2。
1计算生产纲领,确定生产类型
按下式计算零件生产纲领。
N=Qn(1+a%)(1+b%)2-1
确定生产类型。
如图,为某产品上的一个零件.假设该产品年产量为10000台。
机械加工的废品率是0。
1%,一台产品中零件的生产数量是2件,它的备品率为20%,下面制定该零件的机械加工的工艺规程进行。
N=Qn(1+a%)(1+b%)
=10000×2×(1+20%)(1+0.1%)
=24048件/年
该零件每年的产量为24048件,该产品属于轻型的机械,确定其生产类型是大量的生产
图2—1锥齿轮轴零件图
大量生产的工艺特征:
1零件的互换性,具备比较广泛的互换性,少数装配精度要求比较高的地方,通常可以采用调整法以及分组装配法等方法。
2毛坯的加工余及制造方法:
较广泛地使用模锻,金属模机器造型或者别的比较高效的方法.毛坯的加工余量较小并且精度比较高。
3机床设备和它的布置形式:
广泛应用自动机床和商效专用机床,按照自动排列和流水线进行装备。
4工艺装备:
使用某种量具,从而根据调整法来达到对精度的要求。
5工艺文件:
有工序卡或者工艺过程卡.
6成本较低。
7生产率高。
8工人劳动条件较好.
2。
2零件的分析
2.2。
1零件图样的分析
1齿轮轮齿外表面对轴心线的圆跳动的公差是0.030mm。
2φ40右端面对轴心线圆的跳动公差是0.015mm。
3渗碳淬火硬度55~62HRC。
4齿轮精度等级8GK。
5零件材料为22CrMnTi。
2。
2。
2工艺分析
1此齿轮的精度相对比较低,因此在刨齿渗碳淬火工序之后,不再对工序进行磨齿,假如齿轮精度的要求大于了7级,就要添加磨齿的工序。
2没标注轴径各处R3,在加工时磨削。
φ45轴径右端面,靠磨后(工厂俗称“一刀下")可保证右端面圆跳动公差.
3齿轮的轮齿的外表面相对于轴心线的圆跳动;检查φ45右端面相对于轴心线的圆跳动,可以应用装夹在偏摆仪上进行检测两中心孔定位。
4可以应用专用样板进行或游标万能角度尺检查锥齿轮的锥角。
2。
2。
3选择毛坯及毛坯制造方法
1依据零件用途确定毛坯类型。
2毛坯的制造方法依据批量确定.
3依据手册查定余量公差及表面加工余量。
4依据技术的要求,零件材料为20CrMnTi。
20CrMnTi化学成分:
碳C:
0.16~0.24
硅Si:
0.16~0。
38
锰Mn:
0。
81~1。
12
硫S:
允许残余含量≤0.038
磷P:
允许残余含量≤0。
038
铬Cr:
1。
01~1.32
铜Cu:
允许残余含量≤0。
032
镍Ni:
允许残余含量≤0.032
钛Ti:
0。
03~0.11
20CrMnTi力学性能:
抗拉强度σb(MPa):
≥1090(110)
屈服强度σs(MPa):
≥836(85)
伸长率δ5(%):
≥10
断面收缩率ψ(%):
≥48
冲击功Akv(J):
≥56
冲击韧性值αkv(J/cm2):
≥69(8)
硬度:
≤217HB
试样尺寸:
试样毛坯尺寸为17mm
20CrMnTi热处理:
在加热钢材870℃保温速冷670℃后保温等温正火渗碳温度在1010——1050℃,强渗保温时间大约2.0小时,碳势控制在0.6%,扩散时间大概为2。
5小时,控制碳势为1。
08%,降温保温在870℃,碳势。
为80%,时间为50分钟。
降低渗碳温度-—马氏体超差,增加降温保温时间,减低淬火的温度.产品变形—先正火处理然后再进行渗碳,减小淬火温度。
20CrMnTi表示бs≥845MPa,бB≥1090MPa的低碳合金钢.低碳合金钢碳质量分数通常为0.18%—0.25%,其铸造性能没铸造铁高,力学性能却比铸造铁好些,主要用于制造力学性能的要求比较高,形状比较复杂等相对重要的机械零件,比如机车车辆的车销和联轴器,锥齿轮轴等。
制造毛坯的方法:
由于零件并不是复很杂,所以毛坯基本可以和零件的形状保持接近。
键槽可以不用锻出,而直接进行加工.
查看相关加工余量表,可以得出两端面总加工余量是2mm,通过加工余量可以确定毛坯尺寸的大小。
主要依据采用毛坯模锻:
形状复杂的毛坯可以通过模锻锻造出,毛坯钎维组织比较好,强度也比较高,生产的率比较高,但是需要使用锻锤设备和专用锻模。
大批量生产,适用于锻造合金钢,碳素钢.
锻件可以加工平面度的公差和表面的直线度。
模锻件的长度是279mm,进行热处理调质的时候,精密度是0.8mm,平面度公差和直线度的普通级是1。
2mm。
图2-2毛坯图
2.3工艺规程设计
2。
3.1定位基面的选择
选择定位基面是确定加工方案.定位基面选择的合理、正确与否,将会使直接的影响到工件的生产率和加工的质量。
通过对下面3个问题同时进行考虑来选择定位基面。
1加工时选用哪一表面作为统一基准或精基面,方能使加工的精度得到保证,使机械加工工艺的过程可以进行地顺利?
2应当使用哪个表面作为粗基面加工上述统一基准或者精基面?
3是否有个别工序因为特殊的加工要求需要使用统一基准以外的精基面?
选择精基面:
依据选择精基面的原则,当精基面选择时,要首先对基准重合问题进行考虑,若情况允许,定位基准应当尽可能地选择加工表面的设计基准。
2。
3.2锥齿轮轴零件表面加工方法的选择
选择零件各表面的加工方案和方法,要使得加工表面的表面粗糙度和加工精度的要求得到保证。
本零件的加工面有:
两头端面(其中一头须刨成齿面),φ35的外圆面,两个φ45的外圆面,两个φ42的外圆面,磨得圆面,刨的齿面.铣键槽.
φ35外圆面:
公差为
Ra3。
3um需要精车和精粗。
两个φ42的外圆面:
两个面未注公差。
其中一个的粗糙度为Ra1.7
另一个为Ra6。
3需要粗车,精车
两个φ46的外圆面:
公差为
。
粗糙度为.需要粗车,精车
刨的齿面:
大端面公差等级为
铣键槽:
未注公差等级,采用铣床加工即可
磨得圆面:
采用砂轮打磨即可。
零件各表面加工顺序的确定
1机械加工顺序安排
依据机械加工工顺序安排时应当遵循的原则,由于该工件的具体特点,首先安排锻材料至φ55×230mm+φ85×52mm。
车端面,粗车右端,见平即可。
长46mm,车外圆φ78mm,钻中心孔A5/10.8
倒头,粗车,车断面,车左端,车外圆至φ46mm与φ78mm接刀,保总长267mm,钻中心孔A5/10。
7
精车,定位装夹工件时用两中心孔,大端外圆,21°06。
倒头,用中心孔点位来装夹工件,外圆留余量。
精车左端φ35的一段.
精车φ45两处,并外圆留余量。
精车齿部左端面,保证尺寸34.411mm(或33mm)。
车圆角R5(φ53mm,14。
尺寸留打磨量0。
3mm)。
划10mm键槽线。
两处φ45定位,装夹工件,按线找正,铣键槽11mm到图样尺寸,和轴线保证对称。
磨,定位装夹工件靠两中心孔,两处φ46mm,磨φ38mm,至图样尺寸.并且靠磨14mm端面到图样尺寸。
靠磨圆R5。
2热处理工序的安排
在加工之前,首先要金信通正火处理安排,从而使锻造应力消除,改善切削性能。
刨齿过后,要进行齿部渗氮淬火,按图样要求渗氮深度0。
7~1。
1mm,渗氮淬火硬度为58~63HRC
3辅助工序的安排.
检验工序:
在磨工序之后进行终结检验安排。
最后入库。
2。
3.3制定工艺路线
制定工艺的路线主要是对加工阶段及确定加工方法进行确定。
1.选择加工方法时依据零件加工表面的技术条件,主要为加工面的形状精度,表面粗糙度,尺寸精度.
2。
各表面加工方法选定之后,就需要对加工方法的大致顺序作进一步考虑。
3。
排加工路线图表。
下面列出大量生产轴类零件时的工艺路线.
工序10:
锻造来料尺寸(φ55×230mm+φ85×52mm)。
工序20:
车端面,粗车右端,见平即可。
车外圆φ76mm,钻中心孔A5/10.6,长48m
工序30:
倒头,粗车,车左端,车断面,车外圆至φ78mm与φ46mm接刀,钻中心孔A5/10。
7保总长267mm.
工序40:
精车,大端外圆。
工序50:
倒头,用精车右端齿轮部分的锥面,中心孔点位装夹工件,精车左端φ36的一段。
外圆留余量.
精车φ45两处,并外圆留余量。
精车齿部左端面,保证尺寸34.411mm(或33mm).
车圆角R5(φ53mm,14.尺寸留打磨量0.3mm)。
工序60:
划10mm键槽线。
工序70:
以两处φ46来定位,装夹工件,按线找正,铣键槽11mm到图样尺寸,与轴线确保对称。
工序80:
刨齿,定位来装夹工件用φ46轴径,精刨齿z=20,m=3.7到图样尺寸要求
工序90:
刨齿过后,要进行齿部渗氮淬火,按图样要求渗氮深度0.8~1。
4mm,渗氮淬火硬度为56~64HRC
工序100:
磨,用两中心孔定位来装夹工件,两处φ45mm,磨φ35mm到图样尺寸。
并靠磨14mm端面至图样尺寸.靠磨圆R5。
2。
3。
4选择加工设备及工艺装备
1确定机床规格和种类时应根据零件轮廓尺寸,加工精度和批量等因素,.
2根据经济性、效率及质量选择夹具数量及其种类等。
3根据工件生产率的要求,材料以及切削用量,选择刀具,应当尽可能选择标准刀具。
4选择量具根据加工精度及批量.
因为是大批量生产,所以以通用机床为主,并且可以少量地运用专用机床的流水生产线。
1.选择机床
A工序20,30,40,50:
是粗车和精车,本零件的精度较高,选用C620(C6140)
B工序70:
为半精铣及粗铣,应用X56K。
C工序80:
刨齿选用Y236.
D工序100:
用磨床M1342.
2选择夹具
除本轴类零件铣键槽要求设计专用夹具以外,其他的工序可使用通用夹具。
3.选择刀具
A铣键槽选错齿两面铣刀(YT15)直径为10。
B车刀YT15弯头刀.
C刨刀。
D砂轮。
4。
选择量具
大批量生产本零件,通常都使用量具,有两种方法选择量具:
一为不确定度选择(按计量器具);二为极限误差选择。
检查φ46的右端面对轴心线的圆跳动时,使用装夹在偏摆仪上的两中心孔定位进行检测。
2.3.5加工工序设计、及切削用量的计算
1。
用查表法确定工序余量.
2.当无基准转换时,工序尺寸及其公差的确定应首先明确工序的加工精度。
3.当有基准转换时的工序尺寸及其公差应由解算工艺尺寸链获得。
4。
工序尺寸确定常用的方法:
若无基准转换,多次加工同一表面的工序尺寸只与工步(或工序)的相关加工余量。
若有基准转换,应当使用工艺尺寸链解算工序尺寸。
切削用量的选择
小批量生产单件时,通常操作工可自定,大批量生产时,工艺规程一定要给定详细数值的切削用量,选择的原则是要具有比较高的经济性和生产率(确保质量的前提下),可根据情况具体选用。
工序10:
锻造来料尺寸(φ55×230mm+φ85×52mm)。
查看相关手册,得到半精加工的余量Z是2mm,因为已知端面的总余量Z总是4mm,故得出粗加工余量Z粗是2mm.
工序20:
车端面粗车右端,,见平即可。
外圆直径为78mm,依据选择切削用量的原则,在加工质量得到保证的条件下,使f,ap,vc相乘最大.粗车时,应尽量一刀走完,在中等功率的车床上可达8~10mm,本工序用的是C6140,故取背吃刀量为9mm,可满足一次走完余量。
粗车时,一般是靠经验选择进给量,查表得到也可,根据切削手册选的进给量f=0。
71mm/r.vc根据公式
2—2
可得出
为235mm/min。
为磨刀费用,
为刀具使用寿命。
(这里的刀具为转为车刀,大约是15~30min)
工序30:
倒头,粗车,车断面,车左端,总长267mm,车外圆至φ78mm和φ46mm接刀,钻中心孔为A5/10.7,这里进给量为f=0.72mm/r.被吃刀量是8mm.同理可以计算出
工序40:
精车,大端外圆.
精车被吃刀量的要求比较高,可取0。
1~0.4mm此处取0。
2mm.进给量为f=0.71mm/r。
工序50:
倒头,装夹工件时使用中心孔点位,精车左端是φ36的一段。
外圆留余量。
精车φ45两处,并外圆留余量。
精车齿部左端面,保证尺寸34.411mm(或33mm).
车圆角R5(φ53mm,14.尺寸留打磨量0.3mm)。
端部倒角为2×46,车φ43两处到图样要求的尺寸.
因为这里的车各个面都是精车取背吃刀量0.2mm,进给量0.71mm/r.vc=175mm/min
工序60:
划10mm键槽线。
工序70:
用两处φ46定位,装夹工件,按线找正,铣键槽11mm至图样尺寸,确保对称于轴线。
1.切削速度为Vc,切削速度Vc是铣刀最外点的线速度,计算公式如下:
2—3
式中:
铣刀切削速度是vc,单位(m/min)
d为铣刀直径(mm);
n为铣刀转数(r/min).
2。
铣刀的进给量为ƒ,因为是多刃刀具,有下列3种度量的方法(计算时根据单位时间的不同)
(1)每分钟的进给量f,单位(mm/min);
(2)每转进给量ƒ,单位(mm/r);(3)每齿进给量ƒ,单位Z(mm/z)。
3.铣削深度ap(又称背吃刀量),单位是mm。
经过计算分析,本设计中铣削深度为10mm,取ap=2mm,f=0.08mm/z,vc计算可得为0.157m/min.
2.3。
6填写机械加工工艺过程卡和机械加工工序卡
1。
工艺过程综合卡片
简明写出各道工序,以便生产管理时使用。
2.工艺卡片
对整个工艺过程进行详细地说明。
3.工序卡片
用作较为详细的工艺文件指导工人的生产过程,使用于大量生产的关键零件的关键工序中。
1.可按比例缩小简图。
2.被加工表面用粗实线(或红线)表示,其余均用细实线.
要求标明该工序的粗糙度和公差等要求.
3.应使用规定的符号对夹紧、定位表面进行标明。
由于本设计已将各个工序给出
故工艺文件只有机械加工工艺过程卡.
工艺文件详见表
第三章锥齿轮轴零件的夹具设计
3。
1机床夹具设计的基本要求和一般步骤
3。
1。
1对专用夹具的基本要求
1。
保证工件的加工精度
2.提高生产效率
3。
工艺性好
应保证专用夹具的结构:
夹具的结构合理、简单.
4.使用性好
专用夹具应当便于使用、省力、安全可靠,排屑应方便.
5.经济性好
3。
1.2专用夹具设计步骤
1明确设计任务与收集设计资料
为了更好地了解工件的材料、结构特点;确定该工序的加工余量、加工要求、加工表面、夹紧表面和定位基准及所用的刀具、机床、量具等.
2。
拟订夹具结构方案与绘制夹具草图
1依据工件定位方案对定位装置进行设计。
2依据工件夹紧方案对夹紧装置进行设计。
3依据导向或对刀方案对对刀或导向装置进行设计。
设计和确定其它元件及装置的结构形式。
4绘制出夹具的草图,并且标注公差、尺寸和技术要求等.
3。
进行必要的分析计算
若工件的加工精度比较高,就应当对工件加工进行精度分析。
4。
审查方案与改进设计
夹具草图画出后需要进一步修改夹具方案作.
3.2锥齿轮轴零件的铣床夹具设计
所示为锥齿轮轴零件
图3—1锥齿轮轴工件图
3.2.1零件本工序的加工要求分析
本工序前已加工的表面如下:
1粗车端面(右面).
2粗车端面(左面).
3精车(以中心孔定位),精车右端齿轮部分锥面.
4精车左端各外圆面,并至规定的尺寸.
5划100—0.043键槽线。
本工序使用机床为X52k立式铣床;刀具是错齿两面刃铣刀。
3。
2。
2拟订定位与夹紧方案
1。
定位方案根据工件结构特点,其定位方案和夹紧方案如下图所示:
根据加工的相关要求,应当限制5个自由度在铣键槽时。
方案:
工件以直径42的两个外圆在四个互相垂直的平面上定位.即可对它的5个自由度进行基本限制。
3.2。
3对刀方案
键槽铣刀只需在一个方向上对刀,可采用直角对刀块,因为至要加工一个键槽,故只需一个对刀块即可满足要求。
图3—2夹紧与定位图
3.2。
4夹具体与定位键
为了保证安装稳定夹具在工作台上,应该根据夹具体的高度比小于等于1.26的原则来对其宽度确定,并设置耳座在它的两端。
以便固定。
为使槽的对称度的要求得到保证,应该设置定位键在夹具体的底面。
为了使夹具的安装误差减小,B型定位键通常会被采用。
3。
2。
5夹具总图上的尺寸,公差和技术要求
1。
夹具的最大轮廓尺寸为长400mm,宽200mm,高140mm。
。
2.刀块表面对刀块的位置尺寸h限位基准的距离。
最小位移量使加工尺寸增大的时候
h=H±s—imin
当最小位移量使加工尺寸缩小时
h=H±s+imin
试中h对刀块的位置尺寸
H定位基准至加工表面的距离
s塞尺厚度。
计算塞尺厚度为imin=Xmin/2
Xmin是圆孔和圆柱面之间的最小的配合间隙。
但本设计中是以V型板定位,故imin=0。
将各环准换为平均尺寸,分别算出h1,h2的平均尺寸.
h1=(9。
9785+4。
91)mm=14.8885mm(基本尺寸)
h2=(35。
042÷2—4.91)mm=12。
6111mm(基本尺寸)
4.影响对刀精度的尺寸:
塞尺的厚度尺寸5h8=50—0。
018mm。
3。
2.6加工精度分析
由于零件是两V型板定位,由于面与轴面接触时即使摩擦力很大,也无法保证轴在轴向的横向移动。
所以在铣槽时可以产生直线位移误差。
由于误差对铣键槽的影响很小,可忽略不计。
具体见下分析.
3.2。
6。
1铣键槽侧面对轴线的平行度的加工精度。
1.定位误差ΔD因为定位基准是该工件的轴线,对称度的工序基准亦是该轴线,所以得出ΔB=0.
因为V形块的对中性,ΔY=0.所以,对称度的定位误差为0.
2。
安装误差ΔA如下图a所示,可以得出ΔA=X=0。
027mm。
如果在两定位键外,就可按照下图b计算出ΔA为
+X
图a图b
图3-3定位误差
3。
对刀误差ΔT因为塞尺厚度和对称度的对刀误差的公差相等,所以ΔT=0.018mm.
4.夹具误差ΔJΔJ=0。
03+0。
03=0.06mm。
3。
6.2.2键槽侧面对轴线的平行度的加工误差
1。
定位误差ΔD因为V形块之间相互位置的误差极小,可看作一个长的V形块,故ΔD=0。
2.安装误差ΔA定位键的位置如图a中所示时,工作台导轨相对于工件的轴线是平行的,故ΔA=0。
如图b所示定位键,由于工件的轴线和工作台导轨之间有转角误差,使键槽侧面和轴线产生了平行度误差,所以
ΔA=
3。
对刀误差ΔT由于平行度不受塞尺厚度的影响,ΔT=0。
4。
夹具误差ΔJ因为是定位键侧面B的平行度0。
03mm和工位V型板设计心轴轴线影响平行度的制造误差的,因此
ΔJ=0。
03mm.
3。
3确定夹具方案
参考夹具资料,利用v型板定位,夹紧。
如图所示。
图3-4夹具总装图
总结
时光飞逝,为期半年的毕业设计即将结束.回首这近半年的设计过程,感触颇多。
使我加深了对机械的认识。
受益匪浅!
在这次设计过程中,我真正的意识到自己的不足之处,以前学习过程中从未涉及到的知识,在这次设计当中也涉及到了。
使我真正感受到了机械的博大精深.
在这次毕业设计中,第一件事是对工件机械加工的工艺规程进行制定,如此就可以知道在加工工件时用什么机床加,如何操作,加工工艺设备及装备等,因此,对工件机械加工的工艺规程制定就是极其重要的.
在毕业设计过程中还用到了一些计算机软件和CAD制图,毕竟学过时间已经很长了,在开始画图的时候出现了诸多的问题,而且没曾经那么熟练。
但很快就能熟练运用了。
相信CAD制图不管是现在,还是对以后的工作都会有很大帮助的。
所以,这次毕业设计真正地把曾经所学的知识和实际应用联系起来了。
在此次毕业设计中,还有一个非常重要的就是关于夹具的设计,在开始设计的过程中,存在着很多的问题,在老师的细心指导和自己坚持不懈的努力下,我一步一个脚印的设计,画图,查阅各种关于专用夹具的资料,最终将它成功地设计了出来,我感到很有成就感,因为在此过程中我掌握了很多曾经没有掌握的的知识.这次设计使我懂得了很多东西,真正地将理论和实际联系了起来
在此次毕业设计中,我掌握了很多知识,更为重要的是,我能以设计人员的身份,设计出一个零件,也因此,我懂得了设计人员的精神,任何零件,所有产品都是要先设计出来,再进行加工的,所以,作为设计人员,在设计的过程中一丝一毫都不能大意,每个步骤都要有理根据,绝对不能凭空捏造。
亲自操作后我才明白,任何事情都不是简简单单的就能完成的,是要付出大量努力的。
所以,我们也要用心去感悟每个设计者的思想,这样方能像他们一样设计出满意的作品。
此次毕业设计,对我来说有