轧钢机下压机构设计 正文教材.docx
《轧钢机下压机构设计 正文教材.docx》由会员分享,可在线阅读,更多相关《轧钢机下压机构设计 正文教材.docx(16页珍藏版)》请在冰豆网上搜索。
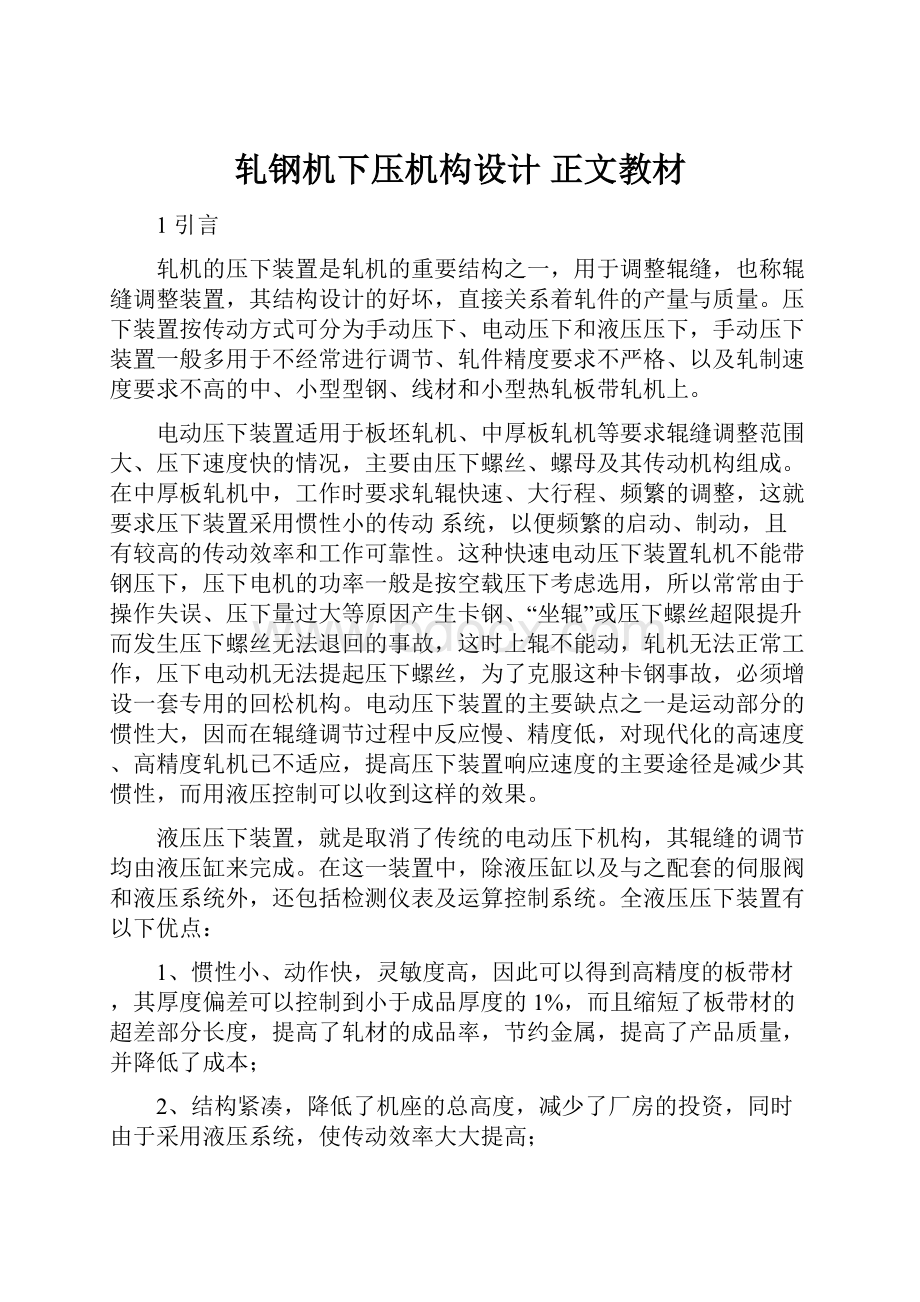
轧钢机下压机构设计正文教材
1引言
轧机的压下装置是轧机的重要结构之一,用于调整辊缝,也称辊缝调整装置,其结构设计的好坏,直接关系着轧件的产量与质量。
压下装置按传动方式可分为手动压下、电动压下和液压压下,手动压下装置一般多用于不经常进行调节、轧件精度要求不严格、以及轧制速度要求不高的中、小型型钢、线材和小型热轧板带轧机上。
电动压下装置适用于板坯轧机、中厚板轧机等要求辊缝调整范围大、压下速度快的情况,主要由压下螺丝、螺母及其传动机构组成。
在中厚板轧机中,工作时要求轧辊快速、大行程、频繁的调整,这就要求压下装置采用惯性小的传动系统,以便频繁的启动、制动,且有较高的传动效率和工作可靠性。
这种快速电动压下装置轧机不能带钢压下,压下电机的功率一般是按空载压下考虑选用,所以常常由于操作失误、压下量过大等原因产生卡钢、“坐辊”或压下螺丝超限提升而发生压下螺丝无法退回的事故,这时上辊不能动,轧机无法正常工作,压下电动机无法提起压下螺丝,为了克服这种卡钢事故,必须增设一套专用的回松机构。
电动压下装置的主要缺点之一是运动部分的惯性大,因而在辊缝调节过程中反应慢、精度低,对现代化的高速度、高精度轧机已不适应,提高压下装置响应速度的主要途径是减少其惯性,而用液压控制可以收到这样的效果。
液压压下装置,就是取消了传统的电动压下机构,其辊缝的调节均由液压缸来完成。
在这一装置中,除液压缸以及与之配套的伺服阀和液压系统外,还包括检测仪表及运算控制系统。
全液压压下装置有以下优点:
1、惯性小、动作快,灵敏度高,因此可以得到高精度的板带材,其厚度偏差可以控制到小于成品厚度的1%,而且缩短了板带材的超差部分长度,提高了轧材的成品率,节约金属,提高了产品质量,并降低了成本;
2、结构紧凑,降低了机座的总高度,减少了厂房的投资,同时由于采用液压系统,使传动效率大大提高;
3、采用液压系统可以使卡钢迅速脱开,这样有利于处理卡钢事故,避免了轧件对轧辊的刮伤、烧伤,再启动时为空载启动,降低了主电机启动电流,并有利于油膜轴承工作;
4、可以实现轧辊迅速提升,便于快速换辊,提高了轧机的有效作业率,增加了轧机的产量。
全液压压下也存在一些缺点:
压下系统复杂,工作条件要求高,有些元件(如压力传感器、位移传感器及测厚仪等测量元件)和伺服阀等制造精度要求很高,并要求在高温、高压及有振动条件下,工作不应失灵或下降测量精度和控制灵敏度,因此制造困难、成本高,维护保养要求很严格,以保证控制精度。
虽然液压压下相对于电动压下还存在着一些缺点,但是由于电动压下无法满足目前正在发展的高生产率、高产品质量的现代化带轧机的工作要求,因而,采用液压压下的板厚自动控制系统来代替电动压下的板厚自动控制系统已是必然趋势,因而随着科学技术的发展,液压压下板厚自动控制系统将会愈来愈完善。
2轧机简介
2.1轧延原理
轧机是实现金属轧制过程的设备。
泛指完成轧材生产全过程的装备﹐包括有主要设备﹑辅助设备﹑起重运输设备和附属设备等。
实现金属轧制过程的设备。
泛指完成轧材生产全过程的装备,包括有主要设备、辅助设备、起重运输设备和附属设备等。
但一般所说的轧机往往仅指主要设备。
据说在14世纪欧洲就有轧机,但有记载的是1480年意大利人达·芬奇(LeonardodaVinci)设计出轧机的草图。
1553年法国人布律列尔(Brulier)轧制出金和银板材,用以制造钱币。
此后在西班牙、比利时和英国相继出现轧机。
图1为1728年英国设计的生产圆棒材用的轧机。
英国于1766年有了串列式小型轧机,19世纪中叶,第一台可逆式板材轧机在英国投产,并轧出了船用铁板。
1848年德国发明了万能式轧机,1853年美国开始用三辊式的型材轧机(图2),并用蒸汽机传动的升降台实现机械化。
接着美国出现了劳特式轧机。
1859年建造了第一台连轧机。
万能式型材轧机是在1872年出现的;20世纪初制成半连续式带钢轧机,由两架三辊粗轧机和五架四辊精轧机组成。
以轧机为主体,将金属坯料轧延成材的成套设备。
轧机是直接轧延金属的主机,它利用旋转的轧辊辗压坯料,使金属按规定的要求产生塑性变形,如图1。
轧延是生产率最高、成本最低的金属成形方法,适用于轧延横断面相同或有周期性变化的条状或板状材料;特殊轧机可轧制机械零件或其毛坯以及某些非金属材料。
轧延主要有热轧和冷轧两种方式。
热轧是在轧件加热的条件下进行轧延,以降低轧延压力;冷轧是在室温下进行,可使轧件得到很高的形状尺寸精度和表面光洁度,并可改善轧件的机械性能。
轧机原理的表面现象很简单,就是通过轧辊的轧制把较厚的板带或坯料轧成较薄的板带(箔),目前我国钢铁行业有热轧,有冷轧等,有色行业有铸轧机、冷轧机、铝箔轧机(又分为粗轧机、精轧机),最近又开始兴起热轧机等等,相关的辅助设备就更多了:
横切机、纵切机、分卷机、合卷机,拉弯矫直机。
但轧机的控制系统相当复杂,总体上分为机械、液压和电气控制三部分,轧机精度的高低除与机械制造的水平有关外,液压与电气控制也是必要的。
2.2轧机的分类
轧延机械可按所轧延的材料分为轧延钢材的和轧延铝、铜等有色金属的两类。
各类轧机的工作原理和主要结构基本相同,只是轧延的温度、压力和速度有所差异。
轧机中使用最多的是轧钢机。
轧机又可分为半成品轧机和成品轧机。
半成品轧机主要是开坯机,包括初轧机、板坯轧机和钢坯轧机。
随着连铸机的逐步推广,某些装有连铸机的钢厂已不再使用开坯机开坯。
成品轧机有型材轧机、轨梁轧机、线材轧机、厚板轧机、薄板轧机、带材轧机、箔带轧机、无缝管轧机、铜板轧机、铝板轧机和某些特殊轧机。
它们的主要区别是轧辊的布置和辊的形状不同,并且在精度、刚度、强度和外形尺寸上也有很大的差别。
辅机是成套的辅助设备,可分为加工用辅助设备和储运包装等辅助设备。
加工辅助设备包括:
切成一定尺寸用的各种锯床、剪断机和圆盘剪;精整轧材用的矫正机和平整机;热处理用的各种工业炉(包括推料出料机)和可控气氛装置;表面加工和清理用的除鳞(清氧化皮)、抛丸(铁丸喷射钢材表面)、酸洗、清洗、镀层、涂塑、涂油和打印等机组。
储运包装辅助设备有运锭车、各种辊道、推床(横移轧件)、升降台、翻转机、回转台,以及带材卷取机、开卷机、堆垛机和打捆机等。
此外,轧延机械还包括复杂的机械传动系统和相应的电力拖动系统,以及先进的电气控制系统。
2.3轧机的组成
轧机主要由主电机、主传动和主机座(工作机座)组成,如图2。
主电机在需要调速时使用直流电机,不需要调速时使用同步或异步(带飞轮)交流电机。
主机座由机架、轧辊、轴承座、压下装置和平衡装置等组成,如图3。
机架是承受轧延力的部件,闭式机架有较好的刚度,但开式机架换辊较方便,如图4。
轧辊是轧延金属的部件,辊身为工作部分,轴头用于传动,如图5。
板材轧辊的辊身形状称为辊型,型材轧辊的轧槽称为孔型。
压下装置用来调节轧辊的压下量。
高速带材轧机的厚度自控常由液压压下装置来完成。
平衡装置用于消除压下螺丝等处游隙的影响,以免受载时产生冲击。
板带轧机的主机座中还设有液压弯辊装置,在辊颈施加附加弯矩而使辊身产生附加挠度,以此来控制带材的横向厚度而获得最佳的板型。
主要设备有:
1、工作机座:
由轧辊、轧辊轴承、机架、轨座、轧辊调整装置、上轧辊平衡装置和换辊装置等组成。
2、轧辊:
是使金属塑性变形的部件。
3、轧辊轴承:
支承轧辊并保持轧辊在机架中的固定位置。
轧辊轴承工作负荷重而变化大,因此要求轴承摩擦系数小,具有足够的强度和刚度,而且要便于更换轧辊。
不同的轧机选用不同类型的轧辊轴承。
滚动轴承的刚性大,摩擦系数较小,但承压能力较小,且外形尺寸较大,多用于板带轧机工作辊。
滑动轴承有半干摩擦与液体摩擦两种。
半干摩擦轧辊轴承主要是胶木、铜瓦、尼龙瓦轴承,比较便宜,多用于型材轧机和开坯机。
液体摩擦轴承有动压﹑静压和静—动压三种。
优点是摩擦系数比较小,承压能力较大,使用工作速度高,刚性好,缺点是油膜厚度随速度而变化。
液体摩擦轴承多用于板带轧机支承辊和其它高速轧机。
4、轧机机架:
由两片“牌坊”组成以安装轧辊轴承座和轧辊调整装置,需有足够的强度和钢度承受轧制力。
机架形式主要有闭式和开式两种。
闭式机架是一个整体框架,具有较高强度和刚度,主要用于轧制力较大的初轧机和板带轧机等。
开式机架由机架本体和上盖两部分组成,便于换辊,主要用于横列式型材轧机。
此外,还有无牌坊轧机。
5、轧机轨座:
用于安装机架,并固定在地基上,又称地脚板。
承受工作机座的重力和倾翻力矩,同时确保工作机座安装尺寸的精度。
6、轧辊调整装置:
用于调整辊缝,使轧件达到所要求的断面尺寸。
上辊调整装置也称“压下装置”,有手动、电动和液压三种。
手动压下装置多用在型材轧机和小的轧机上。
电动压下装置包括电动机、减速机、制动器、压下螺丝、压下螺母、压下位置指示器、球面垫块和测压仪等部件;它的传动效率低,运动部分的转动惯性大,反应速度慢,调整精度低。
70年代以来,板带轧机采用AGC(厚度自动控制)系统后,在新的带材冷、热轧机和厚板轧机上已采用液压压下装置,具有板材厚度偏差小和产品合格率高等优点。
7、上轧辊平衡装置:
用于抬升上辊和防止轧件进出轧辊时受冲击的装置。
形式有弹簧式,多用在型材轧机上;重锤式,常用在轧辊移动量大的初轧机上;液压式,多用在四辊板带轧机上。
为提高作业率,要求轧机换辊迅速、方便。
换辊方式有C形钩式、套筒式、小车式和整机架换辊式四种。
用前两种方式换辊靠吊车辅助操作,而整机架换辊需有两套机架,此法多用于小的轧机。
小车换辊适合于大的轧机,有利于自动化。
目前,轧机上均采用快速自动换辊装置,换一次轧辊只需5~8分钟。
8、传动装置:
由电动机、减速机、齿轮座和连接轴等组成。
齿轮座将传动力矩分送到两个或几个轧辊上。
9、辅助设备包括轧制过程中一系列辅助工序的设备。
如原料准备﹑加热﹑翻钢﹑剪切﹑矫直﹑冷却﹑探伤﹑热处理﹑酸洗等设备。
10、起重运输设备:
吊车、运输车、辊道和移送机等。
11、附属设备:
有供、配电、轧辊车磨,润滑,供﹑排水,供燃料,压缩空气,液压,清除氧化铁皮,机修,电修,排酸,油、水、酸的回收,以及环境保护等设备。
2.4轧机的结构形式
轧机的结构形式和性能主要决定于轧辊的布置形式和主机座的布置形式,如图6。
①二辊轧机:
结构简单、用途广泛。
它分为可逆式和不可逆式。
前者有初轧机、轨梁轧机、中厚板轧机等。
不可逆式有钢坯连轧机、叠轧薄板轧机、薄板或带钢冷轧机、平整机等。
80年代初最大的二辊轧机的辊径为1500毫米,辊身长3500毫米,轧制速度3~7米/秒。
②三辊轧机:
轧件交替地从上下辊缝向左或向右轧制,一般用作型钢轧机和轨梁轧机。
这种轧机已被高效二辊轧机所取代。
③劳特式三辊轧机:
上下辊传动,中间辊浮动,轧件从中辊的上面或下面交替通过。
因中辊的直径小,可减少轧延力。
常用于轧制轨梁、型钢、中厚板,也可用于小钢锭开坯。
这种轧机渐为四辊轧机所取代。
④四辊轧机:
工作辊直径较小,传递轧制力矩,轧延压力由直径较大的支承辊承受。
这种轧机的优点是相对刚度高、压下量大、轧延力小,可轧制较薄的板材。
有可逆和连轧两种,广泛用作中厚板轧机、板带热轧或冷轧机以及平整机等。
⑤五辊轧机:
有两种,一种是C-B-S(接触-弯曲-拉直)轧机,它是一种带有使轧件弯曲的小直径(为工作辊的1/20)空转辊的四辊轧机,其压下量比通常的四辊轧机大许多倍。
轧件围绕小空转辊发生塑性弯曲变形,可轧制难变形的金属和合金带材。
另一种是泰勒轧机,中间小辊的位置可沿轧机入口或出口方向调节,以保持轧件正确的厚度,用来轧制厚度公差很小的不锈钢、碳钢和有色金属带材。
⑥HC轧机:
高性能的、可控制辊型凸度的轧机。
相当于在四辊轧机的工作辊与支承辊之间增设一对可轴向移动的中间辊,并将两中间辊辊身的相应端部分别调整到与带钢两边缘对应的位置,以提高压力分布和工作辊弹性压扁的均匀性,保证带钢的尺寸精度并可减少其边缘的超薄量和开裂等缺陷。
HC轧机宜用作冷轧宽带钢。
⑦偏八辊轧机:
它是四辊轧机的变型。
工作辊直径为支承辊的1/6,且作相对的偏移,以防止工作辊的水平弯曲,轧制力比四辊轧机小一半。
工作辊的稳定性好、水平刚度高,可用以轧制须用二十辊轧机轧制的部分产品。
它的结构及其调整却比二十辊轧机简单得多。
这种轧机可改装为二、四、八、十六辊几种型式,适宜多品种的需要,因而又称多用途轧机。
它有可逆和连轧两种,用于冷轧难变形钢、硅钢和有色金属带材。
⑧六辊轧机:
由一对工作辊和两对支承辊组成,有较稳定的辊系。
但它的刚性与四辊轧机相仿,且操作不便,因而应用不广,一般用于轧制高精度海底电缆的铜带。
⑨多辊轧机:
有十二辊、二十辊和三十六辊3种型式。
轧机中部一对直径最小的轧辊是工作辊,其余均为支承辊。
它具有相对刚度高、压下量大、轧延力小、可轧极薄的带材等优点。
初期的多辊轧机由工作辊传动,后来用中间支承辊传动。
可轧制宽200~1000毫米,厚0.02~0.0015毫米的箔材。
⑩行星轧机:
两个大直径支承辊带动两组行星辊系,板坯或扁锭一次通过即可热轧成薄带,压下率达90~95%。
若在前道工序配以连铸机,后道工序配以平整机则可简化热轧带钢的生产工艺。
大型行星轧机的辊身长度可达1450毫米。
2.5现状和发展趋势
80年代以来,大容量、高参数、连续化和自动化的成套轧延设备成为发展的重点。
如2050热连轧机,年产量400万吨,粗轧区有轧机5台,精轧区有轧机7台和地下卷取机3套,最大轧制速度为25米/秒,总重量63231吨,总装机容量211022千瓦,其中主电机为93100千瓦。
又如新型45°或Y型无扭线材轧机,轧制速度为65~80米/秒,盘重超过4吨,尺寸精度为±0.1毫米,四线轧制年产量达100万吨。
现代化轧机的主机已广泛采用计算机控制。
在使用多级计算机的全自动化生产过程中,计算机控制已扩展到储运、加热、精整、热处理、表面清理、镀层和剪切等辅助工序。
随着微处理机的发展,它已被用于分别控制冷轧机的各部分功能。
这种控制方式可简化程序的编制,具有灵活可靠、投产时间短和经济效益好等优点。
轧延机械的发展注重节能、成材率、质量、品种等综合经济指标的提高。
发达国家致力于现有轧机的更新和改造,新建的大型轧机有减少的趋势,生产新型材料的中小型轧机将得到进一步的发展。
连铸机将取代初轧机,并进行直接轧制。
线材和棒材的无头轧制技术的发展,使小方坯连铸机与连轧机组成一体。
带钢冷轧机的发展方向是无头全连续轧制。
3传动方案拟定
整个轧延装置由电机带动,固定在底座上。
轧延系统和压下系统分别由两部不同的电机提供动力,如图7。
上下轧辊的转动来自主电机,压下丝杠的转动来自机架上的副电机。
主电机连接着主联轴节,主联轴节连接着主齿轮座(即主减速箱),主减速箱连接着两个连接轴,两个连接轴成上下布置,分别连接轧机的上下两个轧辊。
上下两个轧辊通过轴承座分别固定在上下两个夹具当中,夹具镶嵌在机架里。
下夹具固定,上夹具可上下移动移动一定的距离,即下轧辊固定不动,辊缝的调节是通过调整上轧辊来实现的。
而固定上轧辊的上夹具的上下移动又是通过压下丝杠的转动来实现的。
副电机连接着副联轴节,副联轴节连接着副减速器,副减速器通过齿轮传动将动力传给蜗杆,再通过蜗轮—蜗杆部件将动力传给压下丝杠,压下丝杠的转动再转化为压下板的上下移动,压下板的上下移动转化为上夹具的上下移动,上夹具的上下移动最终转化为了上轧辊的上下移动,以此来调节辊缝。
图7二辊可逆式初轧机工作图
4电机的选择
根据设计要求,主电机选用一部三相交流异步电动机,输出功率P0=1000W,转速n0=1440r/min。
副电机选用一部直流电动机,输出功率P0’=200W,转速n0’=360r/min。
5主传动系统参数计算
5.1主减速箱的设计
设计轧辊的转速为n=20r/min
主电机的转速为n0=1440r/min
则,总传动比i=n0/n=72
设计主减速箱为五级齿轮减速
且,五级传动比分别为i1=2,i2=2,i3=2,i4=3,i5=3
即总传动比i=i1*i2*i3*i4*i5=72
五级效率分别为η1=0.96,η2=0.96,η3=0.92,η4=0.98,η5=0.95
减速箱的总传动效率η=η1*η2*η3*η4*η5=0.79。
5.2轧辊功率的确定
设计联轴器的传动效率η0=0.98
且由5.1得知,η=0.79
由4得知,P0=1000W
则,轧辊的转动功率P=P*η*η0=774.2W。
图8主减速箱示意图
6压下系统参数计算
6.1副减速箱的设计
设计蜗杆的转速为n’=60r/min
副电机的转速为n0’=360r/min
则,总传动比i=n0’/n’=6
设计副减速箱为二级齿轮减速
且,二级传动比分别为i1’=2,i2’=3
即总传动比i’=i1’*i2’=6
二级效率分别为η1’=0.94,η2’=0.98
减速箱的总传动效率η’=η1’*η2’=0.92
则,蜗杆的功率P1=P0’*η’=184W
图9副减速箱示意图
6.2蜗杆传动参数计算
设计压下丝杠的转速为n’’’=2r/min
由设计图知,蜗轮的转速n’’=n’’’=2r/min
由6.1得知,蜗杆的转速为n’=60r/min
则,总传动比i’’=n’/n’’=30
又,模数m=m1=m2=2
压力角a=a1=a2=20°
蜗杆的分度圆直径d1=20
蜗杆的头数z1=1
则,直径系数q=d1/m=10
导程角r=arctan(z1/q)=5.71°
由i’’=u(齿数比)=z2/z1得,蜗轮的齿数z2=i’’*z1=30
蜗杆传动的标准中心距ɑ=(d1+d2)/2=[(q+z2)m]/2=40
蜗轮的分度圆直径d2=m*z2=60
又,蜗轮—蜗杆的传动效率为η’’=0.72,蜗轮的功率P1=184W
蜗轮的功率P2=P1*η’’=135W
6.3压下丝杠参数计算
由设计知,丝杠螺纹大径d=16,小径d1=10,螺纹线数n=1
要求丝杠每转一圈,上轧辊上升或下降h=5mm
则,压下丝杠的螺纹螺距P=h/n’’’=2.5mm
螺纹导程S=nP=P=2.5mm
6.4强度校核
由要求知,压下力F=2000N
则许用应力[σ]=最大应力σmin
=F/(πd1*d1/4)=25.5MPa
材料要求,应力小于或等于25.5Mpa为合格。
7润滑
7.1润滑方法
轧辊轴承的润滑原则上与其他滚动轴承的润滑基本一致,只是轧辊轴承的工作条件比较恶劣,其工作性能能否获得有效发挥在很大程度上取决于轴承的润滑情况。
轧辊轴承采用的润滑方法主要有脂润滑和油润滑。
1、脂润滑的润滑脂兼有密封作用,密封结构和润滑设施简单,补充润滑脂方便,因此只要工作条件答应,轧辊轴承一般都采用脂润滑。
2、油润滑的冷却效果强,并能从轴承内带走污物和水分。
轧辊轴承采用油润滑的润滑方法有压力供油润滑、喷油润滑、油雾润滑和油气润滑。
3、压力供油润滑是常规转速下轧辊轴承最有效的润滑方式。
4、喷油润滑是将润滑油以一定的压力通过装在轴承一侧的喷油嘴喷入轴承内部进行进行润滑,一般应用在高速轧辊轴承,或者压力供油润滑不能满足冷却要求的场合。
5、喷雾润滑是将含有油雾的干燥压缩空气喷到轴承内部进行润滑,使用油量少,由于空气的作用,冷却效果极强,主要用于轧制速度高和轧制精度高的大型轧辊轴承,或者用于在轴承箱中不经常拆卸的轧辊轴承。
6、压力供油润滑和喷油润滑都需要装设进、出油管、润滑泵、储油器,有时还需润滑油冷却器,因此,费用较高,一般轧辊轴承较少采用。
7.2润滑的分类
1、根据润滑剂的不同,润滑可分为:
1流体润滑。
指使用的润滑剂为流体,又包括气体润滑(采用气体润滑剂,如空气、氢气、氦气、氮气、一氧化碳和水蒸气等)和液体润滑(采用液体润滑剂,如矿物润滑油、合成润滑油、水基液体等)两种。
2固体润滑。
指使用的润滑剂为固体,如石墨、二硫化钼、氮化硼、尼龙、聚四氟乙烯、氟化石墨等。
3半固体润滑。
指使用的润滑剂为半固体,是由基础油和稠化剂组成的塑性润滑脂,有时根据需要还加入各种添加剂。
2、根据摩擦副之间摩擦状态的不同,润滑分为:
①流体摩擦润滑。
用流体(厚度在1.5~2微米以上)将摩擦表面隔开的润滑方式。
根据润滑膜压力的产生方式不同又可分为流体动压润滑(靠摩擦表面的几何形状和相对运动由粘性流体的动力作用产生压力平衡外载荷)和流体静压润滑(由外部将一定压力的流体送入摩擦表面间,靠流体的静压平衡外载荷)两种。
②边界摩擦润滑。
摩擦表面间存在一层薄膜(边界膜)时的润滑状态;它可分为吸附膜(润滑剂中的极性分子吸附在摩擦表面所形成的膜,包括物理吸附膜和化学吸附膜)和化学反应膜(润滑油中的添加剂与金属表面起化学作用生成能承受较大载荷的表面膜)两类。
润滑可以延长机器设备的寿命,提高精度、节约能源。
7.3确定润滑方法
根据设计要求,轧辊轴承采用半固体脂润滑;顶盖上的压力轴承采用液体油润滑;上夹具与机架之间采用半固体脂润滑;压下丝杠与压下板之间采用液体油润滑;蜗轮—蜗杆之间采用半固体之润滑。
8设计小结
这次毕业设计当中,即便我的理论知识比较扎实,可是平时就几次设计经验,一开始的时候有些手忙脚乱,不知从何入手。
在老师的谆谆教导,和同学们的热情帮助下,使我找到了信心。
现在想想其实毕业设计当中的每一天都是很累的。
正向老师说得那样,机械专业的毕业设计没有那么简单,你想copy或者你想自己胡乱蒙两个数据上去来骗骗老师都不行,因为你的每一个数据都要从机械设计书上或者机械设计手册上找到出处。
虽然种种困难我都已经克服,但是还是难免我有些疏忽和遗漏的地方。
完美总是可望而不可求的,不在同一个地方跌倒两次才是最重要的。
抱着这个心理我一步步走了过来,最终完成了我的任务。
三个半月的毕业设计结束了。
在这次实践的过程中我学到了一些除技能以外的其他东西,领略到了别人在处理专业技能问题时显示出的优秀品质,更深切的体会到人与人之间的那种相互协调合作的机制,最重要的还是自己对一些问题的看法产生了良性的变化。
经过这段时间的奋战,我的我设计终于完成了。
在没有做毕业设计以前觉得毕业设计只是对大学四年来所学知识的单纯总结,但是通过这次做毕业设计,我发现自己的看法有点太片面。
毕业设计不仅是对前面所学知识的一种检验,而且也是对自己能力的一种提高。
通过这次毕业设计使我明白了自己原来知识还比较欠缺。
通过这次毕业设计,我才明白学习是一个长期积累的过程,在以后的工作、生活中都应该不断的学习,努力提高自己知识和综合素质。
参考文献
[1]黄清华:
《轧钢机械》,冶金工业出版社,北京,1980。
[2]蒋维兴:
《轧钢机械设备》,冶金工业出版社,北京,1981。
[3]王海文:
《轧钢机械设计》,机械工业出版社,北京,1983。
[4]丁修肇:
《轧制过程自动化》,冶金工业出版社,北京,1986
[5]胡玉兴:
《液压传动》,中国铁道出版社,北京,1980。
[6]胡师金:
《机械可靠性设计》,河南科学技术出版社,郑州,1968。
[7]成大先:
《机械设计手册》,化学工业出版社,北京,2002。
[8]边金生:
《轧钢机械设备》,冶金工业出版社,北京,1998。
[9]蒋庄德:
《机械精度设计》,西安交通大学出版社,西安,2000。
[10]邱宣怀:
《机械设计》,高等教育出版社,北京,1985。
[11]施东成:
《轧钢机械设计方法》,冶金工业出版社,北京,1990。
[12]赵毅德:
《中厚板轧机液压AGC的工作原理》,甘肃冶金出版社,甘肃,1997。
致谢
在此要感谢我的指导老师马老师对我的悉心指导,感谢马老师给我们的帮助。
在设计过程中,我通过查阅大量有关资料,与同学交流经验和自学,并向老师请教等方式,使自己学到了不少知识,也经