塑料制件的设计原则1.ppt
《塑料制件的设计原则1.ppt》由会员分享,可在线阅读,更多相关《塑料制件的设计原则1.ppt(39页珍藏版)》请在冰豆网上搜索。
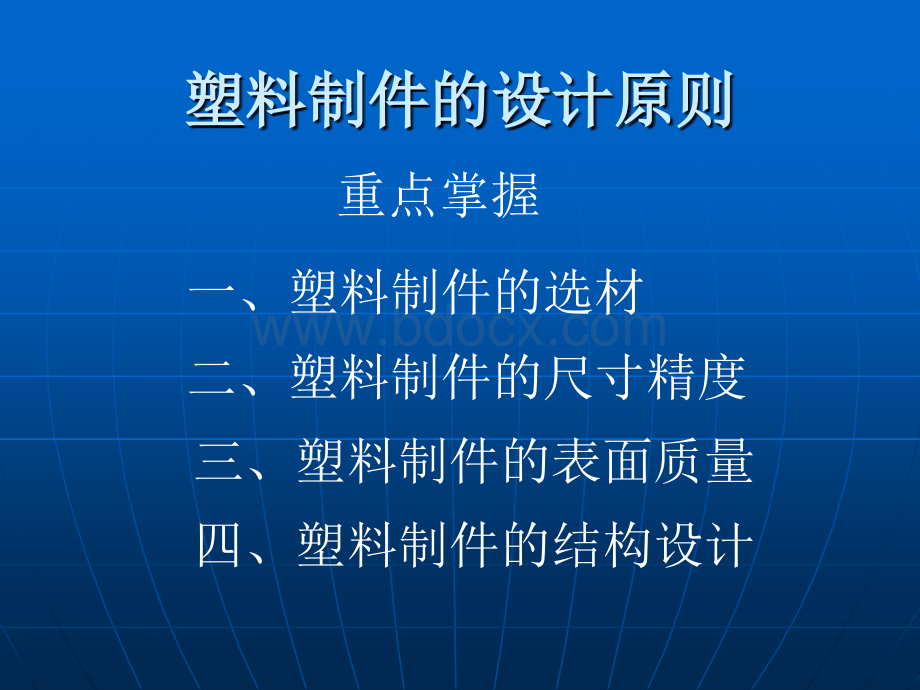
塑料制件的设计原则塑料制件的设计原则重点掌握一、塑料制件的选材二、塑料制件的尺寸精度三、塑料制件的表面质量四、塑料制件的结构设计力求结构简单、壁厚均匀、成型方便,利于模具分型、力求结构简单、壁厚均匀、成型方便,利于模具分型、排气、补缩和冷却。
排气、补缩和冷却。
塑件结构应能使其模具的总体结构尽可能简化,避免模具侧抽芯和简化脱模机构。
塑件成型以后尽量不再进行机械加工。
塑件设计原则:
在保证使用要求的前提下尽量选用价格低廉和成型性能在保证使用要求的前提下尽量选用价格低廉和成型性能较好的塑料。
较好的塑料。
塑料的力学性能。
塑料的物理性能。
塑料的化学性能。
必要的精度。
成型工艺性。
一、塑料制件的选材一、塑料制件的选材具体做法:
通过塑料的特性表进行选择和比较。
选出要求的材料后,再判断所选的材料是否满足制品的使用条件,最好是通过试样做试验。
最好是按照试验所形成的设想来制作原形模具,再通过原型模具生产的试验制品来确认目标值,这样会使塑料材料的选择更为准确。
聚丙烯(PP)和高密度聚乙烯(HDPE)的使用特性和选择原则:
PP比HDPE优越的方面:
PP收缩率比HDPE小,制件细小部位的清晰度好,表面可制成皮革图案;而HDPE收缩率较大,制品表面的细微处难以模塑成型。
PP的透明性比HDPE好。
PP的尺寸稳定性优于HDPE。
PP的热变形温度高于HDPE。
HDPE的耐冲击性能比PP强,即使在低温下韧性也好。
HDPE适应气候的能力优于PP。
HDPE比PP优越的方面:
二、塑料制件的尺寸和精度二、塑料制件的尺寸和精度1塑件的尺寸塑件的尺寸塑件可成型的总体尺寸主要取决于塑料品种的流动性。
在一定的设备和工艺条件下,流动性好的塑料可以成型较大尺寸的塑件;反之,成型出的塑件尺寸较小。
塑件外形尺寸还受成型设备的限制。
从能源、模具制造成本和成型工艺条件出发,只要能满足塑件的使用要求,应将塑件设计得尽量紧凑、尺寸小巧一些。
2塑件的尺寸精度塑件的尺寸精度影响尺寸精度的因素:
模具制造精度及其使用后的磨损,成型工艺条件的变化,塑料收缩率的波动,塑件的形状、脱模斜度及成型后塑件尺寸变化,飞边厚度的波动等。
尺寸精度选用原则尺寸精度选用原则:
为了降低模具的加工难度和模具制造成本,在满足塑件使用要求的前提下应尽量把塑件尺寸精度设计得低一些。
塑件尺寸公差标准SJ13721978(表3-2)。
此标准规定,塑件精度分为8个等级,其中l、2级属精密技术级,只有在特殊要求下使用。
对于未注公差尺寸建议8级精度。
该标准只规定标准公差值,基本尺寸的上下偏差可根据塑件的性质来分配。
对孔类、轴类尺寸可取表中数值分别冠以(+)号、()号;对于中心距尺寸取表中数值之半再冠以()号。
根据塑料收缩率的不同,各种塑料的公差等级分为高、一般、低精度三种,表3-3。
表中未被列出的塑料,可根据塑件成型后的尺寸稳定性参照上表选择精度等级。
选择精度等级时,应考虑脱模斜度对尺寸公差的影响。
工程塑件尺寸公差还可参阅标准GBT144861993。
该标准规定了热固性和热塑性工程塑料模塑塑件的尺寸公差。
三、塑料制件的表面质量三、塑料制件的表面质量表面质量包括:
表面粗糙度和表观质量表面粗糙度和表观质量。
塑件表面粗糙度的高低,主要与模具型腔表面的粗糙度有关。
目前,注射成型塑件的表面粗糙度通常为Ra0.021.25m,模腔表壁的表面粗糙度应为塑件的l2,即Ra0.0l0.63m。
塑件的表观质量:
指塑件成型后的表观缺陷状态。
造成缺陷的因素可能有塑件成型工艺条件、塑件成型原材料的选择、模具总体设计等。
四、塑料制件的结构设计四、塑料制件的结构设计1脱模斜度脱模斜度因塑料冷却后收缩,紧包在凸模或成型型芯上,或由于粘附作用,塑件紧贴在凹模型腔内。
为了防止塑件表面在脱模时划伤、擦毛等,设计时塑件表面沿脱模方向应具有合理的脱模斜度,如图3l所示。
有时,为了在开模时让塑件留在凹模内或型芯上,有意将该边斜度减小。
塑件的性质、收缩率、摩擦因数、塑件壁厚和几何形状。
硬质塑料比软质塑料脱模斜度大;形状较复杂或成型孔较多的取较大的脱模斜度;高度较大、孔较深,则取较小的脱模斜度;壁厚增加、内孔包紧型芯的力大,脱模斜度也应取大些。
影响脱模斜大小的因素:
影响脱模斜大小的因素:
说明:
说明:
脱模斜度不包括在塑件公差范围内,否则在图样上应予说明。
在塑件图上标注时,内孔以小端为基准,斜度由放大的方向取得;外形以大端为基准,斜度由缩小的方向取得。
表34列出了若干塑件的脱模斜度,可供设计时参考。
2、壁厚、壁厚壁厚应设计合理:
太薄熔料充满型腔时的流动阻力大,会出现缺料现象;太厚塑件内部会产生气泡,外部易产生凹陷等缺陷,同时增加了成本;壁厚不均将造成收缩不一致,导致塑件变形或翘曲,在可能的条件下应使壁厚尽量均匀一致。
3加强筋加强筋加强筋的作用:
尺寸:
壁厚为l4mm,大型塑件的壁可达8mm。
主要是在不增加壁厚的情况下,加强塑件的强度和刚度,避免塑件变形翘曲。
合理布置加强筋还可以改善充模流动性,减少内应力,避免气孔、缩孔和凹陷等缺陷。
加强筋的形状、尺寸:
(图32)厚度小于塑件壁厚,与壁用圆弧过渡。
壁厚为t,加强筋高度L=(13)t,筋条宽A=(141)t,筋根过渡圆角R=(1814)t,收缩角=20一50,筋端部圆角r=t8,当t2mm,取A=t。
加强筋端部不与塑件支承面平齐,缩进0.5mm以上,图33。
若一个制件上需设置许多加强筋,加强筋之间的中心距必须大于制件壁厚的两倍以上,各条加强筋的排列互相错开,以防收缩不均匀引起制品破裂。
各条加强筋的厚度应尽量相同或相近,可防止因熔体流动局部集中而引起缩孔和气泡。
图34(a)中的加强筋因排列不合理,在加厚集中的地方容易出现缩孔和气泡,可改用图34(b)所示的排列形式。
图35采用加强筋改善制品壁厚与刚度的,图35(a)为不合理,(b)为合理。
4支承面支承面设计塑件的支承面应充分保证其稳定性。
不宜以塑件的整个底面作支承面,因塑件稍有翘曲或变形就会使底面不平。
通常采用凸缘或凸台作为支承面,图36。
5圆角圆角塑件除使用要求需要采用尖角之外,其余所有内外表面转弯处应尽可能用圆角过渡,以减少应力集中。
图37(a)是不合理的,图37(b)改成了圆角过渡设计就比较合理。
这样不但使塑件强度高,塑件在型腔中流动性好,而且美观,模具型腔不易产生内应力和变形。
圆角半径的大小主要取决于塑件的壁厚,图38,其尺寸可供设计时参考。
图39表示内圆角、壁厚与应力集中系数之间的关系,图中R为内圆角半径,t为壁厚。
由图可见,将Rt控制在1/43/4的范围内较为合理。
6孔的设计孔的设计孔:
通孔、盲孔、异形孔(形状复杂的孔)。
原则上讲,这些孔均能用一定的型芯成型,但孔与孔之间、孔与壁之间应留有足够的距离。
它们的关系如表3-7所示。
塑料制件上的固定用孔和其他受力孔周围可设计凸边来加强,如图310所示。
(1)通孔通孔孔的成型方法一般有三种方法:
图311。
(a)为一端固定的型芯成型,用于较浅的孔成型。
(b)为对接型芯,用于较深的通孔成型,这种方法容易使上下孔出现偏心。
(c)为一端固定,一端导向支撑,这种方法使型芯有较好的强度和刚度,又能保证同轴度,常用,但导向部分周围由于磨损易产生圆周纵向溢料B。
不论用何种方法固定的型芯成型,孔深均不能太大,否则型芯会弯曲。
压缩成型时尤其注意通孔深度不得超过孔径的4倍。
(2)盲孔)盲孔盲孔只能用一端固定的型芯来成型,如果孔径较小深度又很大时,成型时型芯易于弯曲或折断。
根据经验,注射成型或压注成型时,孔深度应不超过孔径的4倍。
压缩成型时,孔深应不超过孔径的25倍。
当孔径较小深度太大时,孔只能用成型后再机械加工的方法获得。
(3)异形孔异形孔对于斜孔或复杂形状的孔,可参考图312所示的成型方法。
当塑件带有侧孔或侧凹时,成型模具就必须采用瓣合式结构或设置侧向分型与抽芯机构,使模具结构复杂化,因此,在不影响使用要求的情况下,塑件应尽量避免侧孔或侧凹结构。
图313为带有侧孔或侧凹塑件的改进设计示例。
(3-1)对于较浅的侧凹槽并带有圆角的制件,若制件在脱模温度下具有足够的弹性,可采用强制脱模的方法将制件脱出,图314,而不必采用组合型芯的方法。
塑件材料:
聚甲醛、聚乙烯、聚丙烯。
图中,A与B的关系应满足7螺纹设计螺纹设计塑件上的螺纹既可以直接用模具成型,也可以在成型后用机械加工获得,对于需要经常装拆和受力较大的螺纹,应采用金属螺纹嵌件。
塑件上的螺纹,一般直径要求不小于2mm,精度不超过IT7级,螺距较大。
细牙螺纹尽量不直接成型,而是采用金属螺纹嵌件。
为了增加塑件螺纹的强度,防止最外圈螺纹崩裂或变形,其始端和末端均不应突然开始和结束,应有一过渡段。
如图315所示,过渡段长度为L,其数值按表38选取。
塑料螺纹与金属螺纹的配合长度应不大于螺纹直径的15倍(一般配合长度为810牙)。
在同一螺纹型芯或螺纹型环上有前后两段螺纹时,应使两段螺纹的旋向和螺距相同,图316(a),否则无法使塑件从型芯或型环上拧下来。
当螺距不等或旋向不同时,就要采用两段型芯或型环组合在一起的成型方法,成型后分别拧下来,图(b)所示。
8、嵌件设计、嵌件设计什么是嵌件什么是嵌件?
塑件内部镶嵌有金属、玻璃、木材、纤维、纸张、橡胶或已成型的塑件等称为嵌件。
使用嵌件的目的:
使用嵌件的目的:
在于提高塑件的强度,满足塑件某些特殊要求,如导电、导磁、耐磨和装配连接等。
使用嵌件的缺点:
使用嵌件的缺点:
嵌件的设置往往使模具结构复杂化,成型周期延长,制造成本增加,难于实现自动化生产等问题。
常用的嵌件材料为金属,常见的形式图317:
(a)为圆形嵌件;(b)为带台阶圆柱形嵌件;(c)为片状嵌件;(d)为细杆状贯穿嵌件。
带有嵌件的塑件设计程序:
带有嵌件的塑件设计程序:
先设计嵌件,后设计塑件。
注意:
注意:
金属嵌件与塑料冷却时的收缩值相差较大,塑料周围存在很大的内应力,如设计不当,会造成塑件的开裂,因此应选用与塑料收缩率相近的金属作嵌件,或使嵌件周围的塑料层厚度大于许用值。
表39列出了嵌件周围塑料层的许用厚度。
嵌件的顶部也应有足够的塑料层厚度,否则会出现鼓泡或裂纹。
同时嵌件不应带有尖角,以减少应力集中。
对于大嵌件进行预热,使其温度达到接近塑料温度。
嵌件上尽量不要有穿通的孔(如螺纹孔),以免塑料挤入孔内。
图319为板片形嵌件与塑件的连接.嵌件镶嵌在塑件中的方法:
将嵌件先放在模具中固定,然后注入塑料熔体加以成型;把嵌件在塑料预压时先放在塑料中,然后模塑成型。
某些特制嵌件(如电气元件)可在塑件成型以后再压人预制的孔槽中。
图320所示为小型圆柱嵌件与塑件的连接,可供参考。
嵌件定位:
嵌件定位:
图3-2l为外螺纹嵌件固定方法。
图3-22内螺纹嵌件固定方法。
嵌件过长或细长杆状时,在模具内设支柱以免嵌件弯曲,但在塑件上留下工艺孔,图3-23。
成型时为了使嵌件在塑料内牢固地固定而不被脱出,其嵌件表面可加工成沟槽、滚花,或制成各种特殊形状。
9标记符号标记符号塑件上有时带有装潢或某些特殊要求的文字或图案标记的符号,符号应放在分型面的平行方向上,并有适当的斜度以便脱模,图3-24。
(a)为标志符号在塑件上呈凸起状,在模具上即为凹形,加工容易,但凸起的标记符号容易被磨损;(c)为在凹框内设置凸起的标记符号,它可把凹框制成镶块嵌入模具内,这样既易于加工,在使用时标记符号又不易被磨损破坏,常用。
(b)为标记符号在塑件中呈凹人状,在模具上即为凸起,用一般机械加工难以满足,需要用特殊加工工艺,但凹人标记符号可涂印各种装饰颜色,增添美观性;10、表面彩饰、表面彩饰作用:
作用:
掩盖塑件表面在成型过程中产生的疵点、银纹等缺陷,增加产品外观的美感,如收音机外壳采用皮革纹装饰。
常用:
凹槽纹、皮革纹、菱形纹、芦饰纹、木纹、水果皮纹等彩饰,方法有:
彩印、胶印、丝印、喷镀漆等。
习题与思考习题与思考1、设计塑件时,为什么既要满足塑件的使用要求,又要满足塑件的结构工艺性?
2、影响塑件尺寸精度的因素有哪些?
在确定塑件尺寸精度时,为何要将其分为四个类别?
(根据塑料收缩率变化范围,将塑件尺寸精度分为四个内别)3、试确定注塑件PC的孔类尺寸85mm、PA1010的