论薄片零件的加工特点及其质量控制措施讲解.docx
《论薄片零件的加工特点及其质量控制措施讲解.docx》由会员分享,可在线阅读,更多相关《论薄片零件的加工特点及其质量控制措施讲解.docx(14页珍藏版)》请在冰豆网上搜索。
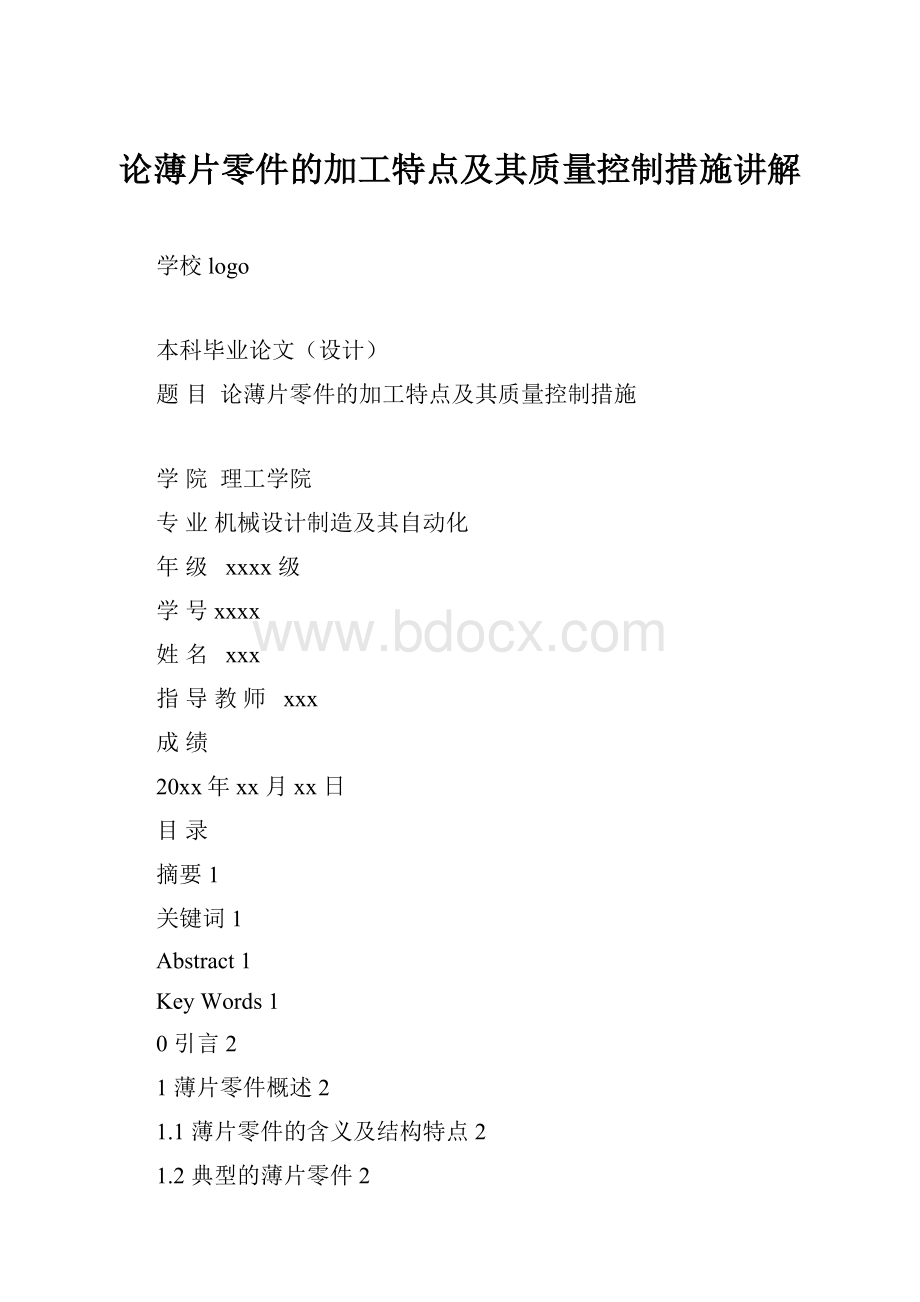
论薄片零件的加工特点及其质量控制措施讲解
学校logo
本科毕业论文(设计)
题目论薄片零件的加工特点及其质量控制措施
学院理工学院
专业机械设计制造及其自动化
年级xxxx级
学号xxxx
姓名xxx
指导教师xxx
成绩
20xx年xx月xx日
目录
摘要1
关键词1
Abstract1
KeyWords1
0引言2
1薄片零件概述2
1.1薄片零件的含义及结构特点2
1.2典型的薄片零件2
1.3薄片零件分类3
2影响薄片零件加工精度的因素3
2.1装夹变形的影响3
2.2加工热变形的影响3
2.3热变形的影响5
3保证和提高薄片零件加工精度的措施5
3.1正确装夹薄片零件5
3.2减小加工热变形的措施6
3.3减小热处理变形的措施7
4钳板零件加工实例7
4.1钳板零件图7
4.2加工钳板零件时存在的问题8
4.3钳板零件的加工过程及工艺流程图8
4.4磨削钳板时采取的工艺措施9
5结束语11
参考文献12
致谢13
论薄片零件的加工特点及质量控制措施
摘要:
本文首先提出了薄片零件的含义及结构特点。
然后文章介绍了生活中的几种典型的薄片零件。
其次介绍了影响薄片零件加工精度的因素,然后通过这些影响原因,具体说明了如何来保证和提高薄片零件的加工精度的一些方法、措施,具体介绍了钳板薄片零件的加工实例,对其加工方法做了论述。
然后针对钳板薄片零件的加工特点,分析了加工过程中容易出现的一些零件质量问题,提出了如何提高薄片零件的加工质量方法和质量控制措施。
关键词:
薄片零件工艺分析磨削方法热变形机理加工精度
Abstract:
Firstly,themeaningofthethinsectionpartsandstructuralcharacteristics.Thearticledescribesseveraltypicalthinsectionpartslife.Second,itdescribesthefactorsaffectingthemachiningaccuracyofthethinsectionparts,andthenreasonthroughtheseeffects,specifyhowtoensureandimprovetheaccuracyoftheflakespartsprocessingmethods,measuresthespecificintroductionofathenipperthinpartsoftheprocessinstance,itsprocessingthemethodsdiscussed.Thenfornipperthinpartsoftheprocesscharacteristics,theanalysisofsomepartsoftheprocesspronetoqualityproblems,howtoimprovetheprocessingqualityofthethinsectionpartsandqualitycontrolmeasures.
KeyWords:
Thinsectionparts,ProcessAnalysis,Grindingmethod,Thermaldeformationmechanism;Machiningaccuracy;
0引言
随着现代科学技术的不断发展,在机械加工行业中,对工件的加工要求越来越严格,技术手段也在不停的向着高精度、高质量要求发展。
尤其是对薄片这种刚性较差、易变形,装夹比较困难的零件的加工是有很高的技术要求的。
在机械装置中我们常常会遇见许多薄片零件,如常见的垫圈、摩擦片、薄板、飞片等,它们的刚性差、散热困难、装夹时容易引起装夹变形,加工时会出现翘曲,严重影响了零件的加工精度。
在生产中,对大部分薄片零件在位检测时,发现其加工精度完全能满足设计要求,但取下来后发现其尺寸及形位误差发生了很大的变化,其原因是:
易变形的薄片零件的刚度较弱,再加上工件基准面精度不高,平面度较差,工件因被吸住受大气压力或被压住受压紧力等装夹力的作用而导致工件发生变形。
在变形状态下加工,尽管在位检测发现工件尺寸和形位误差均满足设计要求,但取下后工件变形恢复,其尺寸及形位误差发生了很大变化,以至于超出了设计范围要求。
在本文里,我主要是针对这些薄片零件的加工,分析了其加工特点,通过对这类零件的热处理及其加工时的装夹技术的讨论,总结减少工件的热处理变形及装夹变形,减少变形工件对零件最终精度的影响,减小切削力,从而保证薄片零件质量的规律和若干工艺措施。
1薄片零件概述
1.1薄片零件的含义及结构特点
薄片零件是各种机械装置中常见的一种结构零件,薄片零件的面积比较大,而厚度尺寸比较小的片状零件。
这类零件的加工难点主要是加工过程中易变形且装夹比较困难。
这类零件主要是用于电子仪器,模具制造,精密机械中的五金零件、机械零件、冲压件等。
1.2典型的薄片零件
在各种机械装置中我们常见的薄片零件有:
垫圈、摩擦片、曲线样板、叶片泵的叶片、钳板等。
模具维修,模具测量间隙和因机器老化时出现晃动,摇摆及不稳定现象时,也可采用薄片零件作为工具检查,调整机器存在的质量问题进而正确的维修,恢复机器的精度。
1.3薄片零件分类
薄片零件大致可以分为两种类型:
一种是一般的弹性薄片零件,它是我们生活中最常能用到的零件,例如常见的垫圈、摩擦片、碟形弹簧、薄板、飞片等,它们的刚性较差、散热困难、装夹时易引起装夹变形,加工时会出现翘曲,严重影响零件的加工精度。
对于高精度的薄片零件主要是用磨削的方法进行最终加工。
还有一种是异形类薄片零件,它是在模具制造中经常会遇到的一种零件,对于这类薄片零件主要是用线切割的方法进行加工的。
2影响薄片零件加工精度的因素
2.1装夹变形的影响
薄片零件在装夹时容易引起装夹变形,加工时会出现翘曲,严重影响了零件的加工精度。
在生产中,对大部分薄片零件在位检测时,发现其加工精度完全能满足设计要求,但取下来后发现其尺寸及形位误差发生了很大的变化。
2.2加工热变形的影响
工件在加工中所受的热源,主要是切削热,对于大型或精密工件,外部热源也不容忽视。
对于不同的加工方式,切削热传入工件的比例是不同的,对于车削、铣削、刨削、立式镗削、外拉削等切削流畅、切屑和刀具的摩擦较小的情况,大部分切削热被切屑带走,传入工件的热量为约l0%左右,对于钻孔,由于钻头横刃的挤压作用,切屑与排屑沟的摩擦以及散热条件不好等原因,钻孔产生的热量约50%进入工件,磨削时,约有84%的磨削热传入工件。
即使是同一加工方式,同样的热量,由于工件受热体积不同,热变形也不一样。
工件的装夹方式对工件热变形也有影响。
如内圆磨床磨短薄壁套内孔时,虽可看作均匀受热,但由于在夹压点处的散热条件好,该处的温升较其他部分低,故加工完毕冷却后工件出现棱圆形的圆度误差,又如在两死顶尖间加工轴件,因顶尖不能轴向移动,则工件的热伸长受阻导致两顶尖间产生轴向力,使工件弯曲变形,中间部分被多磨了一些材料,加工后呈鞍形误差。
工件的热变形对粗加工的精度影响不大,但在工序集中的场合,粗、精工步连续进行时,粗加工的热变形会影响加工精度。
如钻孔完毕后接着铰孔,工件冷却后孔径收缩,尺寸超差,所以安排工艺路线时尽可能粗、精分开,精加工应在工件冷却后进行。
(1)金属在热变形时,在变形体中同时存在着各种不同的区域组织,即是当前的材料组织状态,这些组织具有不同的硬化程度和晶粒尺寸,体积各占整个变形体的一些份额。
因此,金属热变形时的组织变化是这些区域组织变化累积所表现出来的平均结果,变形体的变形抗力是这些区域组织的变形抗力和它们所占体积份额之积的总和。
机械零件在从高温冷却下来的过程中,由于零件相连部分体积变化不均匀,互相牵制,会产生内应力。
当内应力超过零件材料的强度极限时,零件将发生断裂;当内应力超过零件材料的屈服极限而没达到强度极限时,零件将发生变形。
当应力小于弹性极限时,将以残余内应力的形式存在于零件之中。
虽然在零件外表看不见有什么异样,但在切削加工时,当零件部分被切去后,会破坏原来内应力的平衡状态,零件也会发生变形。
当零件送去热处理或被投入使用时,由于热处理应力或外载荷与内应力的叠加,零件可能产生变形,甚至断裂,将严重影响机械设备的正常运转。
(2)在磨削或铣削薄片状零件时,变形主要是由于工件不均匀热变形而导致的。
铣、刨、磨平面时,除在沿进给方向有温度差外,由于工件只在单面受到切削热作用,上下表面间的温度差会导致工件拱起。
中间被多切除材料,加工完毕冷却后,加工表面就产生中凹的误差如图1所示。
板类零件一般分薄板零件如摩擦离合器和大型平板零件如机床导轨等。
两类零件受热后产生热变形大致相同。
磨削长度为L,厚度为H的薄板上下两面温差t=
—
,由于中心角很小,故中性层的弦长可近似为原长L。
近似计算热变形挠度:
f=mo-ko=mo-mo×cos(/2)
=mo(1-cos(/2))
又因为L=mo
所以f=L/×1-cos(/2)
推出f=L×L×(
—
)/(8H)
图1中凹误差
由此可知工件越长,热变形越大。
上面所推出的薄片状零件的热变形公式也可推广到矩形零件切削时的热变形。
2.3热变形的影响
对于力学性能要求较高的工件,一般都需要进行热处理,以提高工件的综合力学性能。
但由于淬火时奥氏体转变为马氏体时体积要膨胀,产生很大的组织应力,再加上快冷引起的热应力形成很大的内应力,致使工件淬火时产生变形,甚至开裂。
对于易变形弹性薄片零件来说,由于刚度较弱,其变形更大。
而要提高零件加工精度,则必须减少热处理变形。
3保证和提高薄片零件加工精度的措施
3.1正确装夹薄片零件
(1)垫弹性垫片装夹方式
在平面磨床上磨削上述薄片工件时,采用弹性夹紧机构,使薄片工件在自由状态下实现定位与夹紧。
在工件与磁性工作台之间垫一层0.5mm厚的橡胶,当工件受磁性吸引力作用时,橡胶被压缩,弹性变形小,从而可磨削出工件的平直平面。
反复磨削几次,可满足加工精度要求。
(2)用临时性加强薄片工件刚性装夹方式
采用环氧树脂脂结合剂,将薄片工件在自由状态下粘到一块平板上。
平板连同薄片一起放到磁力吸盘上。
磨平薄片工件的一个平面后,再将薄片工件从平板上取下来,以磨平的一面放到磁力吸盘上,再磨削薄片工件的另一个平面。
由于环氧树脂在未硬化之前具有一定的流动性,它可以填平薄片工件与平板之间的间隙。
当环氧树脂硬化后,工件与平板粘结在一起,成为一个整体,从而大大增加了工件的刚性。
在磁力吸引下,薄片工件不会产生夹紧变形,为磨削出平直平面创造了条件。
也可用厚油脂代替环氧树脂填充薄片工件与磁力吸盘之间的间隙,增强工件的刚性,同样可以收到良好的效果。
(3)机械装夹方式
利用平面磨床附件中的平口钳将薄片工件借助磁性工作台把小型平口钳吸住。
由于平口钳有一定的高度,因此,钳口受到的磁力较小。
采用吃刀量逐渐减少的办法磨平薄片工件的一个平面后取下,这时把已磨好的平面放到磁性工作台上,在进行磨削薄片工件的另一个平面,反复磨削几次,两平面的平面度能达到要求。
(4)真空装夹方式
利用大气的压力装夹薄片工件来进行磨削加工。
其工作原理为:
夹具体上设有橡胶密封圈,把薄片工件放在橡胶密封圈上,从而使工件与夹具体之间形成密封腔。
用真空泵将密封腔内的空气从抽气孔那里抽出,这时工件被夹紧。
由于夹紧力较小,可采用圆周磨削方法进行磨削加工。
当磨削好薄片工件一端平面后,磨削薄片工件的另一端平面时,可采用上述方法进行,同样可以得到满意的结果。
3.2减小加工热变形的措施
(1)使机床的热变形方向尽量不要位于误差敏感方向,如车床主轴的热变形方向最好不要在水平面方向。
(2)进行热变形补偿。
对于数控机床的热变形,补偿方法主要有两种:
①在精度要求不高的情况下,可利用预置补偿的方法来进行,通过直接测量出的热变形数值或通过其他方法(如离线建模等),找出热变形与工艺参数、时间参数的关系模型,得到其变形的变化规律,然后编程并按此规律进行误差补偿;②精度要求较高时,可采用实时测量补偿系统进行补偿,该方法通过一定的实时测量系统和误差模型快速实时地得到补偿值,实现实时误差补偿。
(3)隔离热源和强制冷却。
隔离热源可以从根本上减小机床的热变形,凡是可能从机床分离出去的热源如电动机、变速箱、液压系统、冷却系统等均应移出,使之成为独立单元。
对于不能分离的热源可从结构和润滑方面改善其性能、减少发热。
同时可用防热材料将发热部件和机床大件隔离开来。
(4)合理安排工艺路线,粗、精加工分开。
(5)正确选择刀具。
减少直接作用于工件上的外力,是减少工件变形,提高加工精度的有效措施。
增加刀具的主偏角和副偏角,可以减少切削力对工件表面法向方向的作用,从而可以有效地减少工件的变形。
实验表明,刀刃锋锐度不同,切削力有明显差别。
切削深度较小时,差别更明显。
当切削深度小到一定值时,单位切削力急剧增加。
这是因为超精密切削时,切削深度和进给量都很小,刃口半径r的不同将明显影响变形。
r值增大将使切削变形明显加大。
在切削深度很小时,刃口半径造成的切削变形占总变形的很大比例,r值微小变化将使切削变形产生很大的变化。
所以在切削深度很小的精切时,更应采用r值较小的切削刀具。
(6)正确选择砂轮。
砂轮的选择好坏直接会影响到零件的加工精度,所以在选择砂轮时要综合考虑各个方面的因素。
(7)合理选择切削液。
在磨削过程中,由于切削热会引起零件的热变形,所以要充分利用切削液,降低切削区的温度减少传入工件的热量,从而减小工件加工后产生的热变形。
同时切削液有润滑作用,也能降低零件的表面粗糙度Ra值,提高零件的表面质量。
根据实践经验,选择适用于不锈钢、合金钢等难加工材料的极压切削油,它具有良好的极压润滑效果,可有效地降低零件表面粗糙度值和延长刀具寿命。
(8)控制环境温度。
精密机床应安装在恒温室内,恒温精度一般控制在1℃以内,精密级为±0.5℃。
恒温基数按季节调节,春秋季取20℃,冬季取17℃。
3.3减小热处理变形的措施
(1)合理设计零件结构。
设计零件时应与工艺密切结合,注意工艺条件的限制,尽可能从零件结构上减少热处理变形。
设计零件时选择材料应尽可能选用含碳量高或含合金元素高的钢,因为一般含碳量越高、合金元素含量越高的钢,奥氏体转变为马氏体的终了温度越低,淬火后残余奥氏体越多,淬火时组织应力越小,因而变形也越小。
且合金钢的淬透性好,一般采用油淬,工件在油中冷却,冷却速度较慢,热应力相对较小,故变形开裂倾向小。
设计工件时,如果没有其它影响,应尽可能增加端面凸缘,以增加零件的刚度。
(2)回火时使用校型工装。
工件淬火后必须立即回火,即将淬火后的零件再加热到低于奥氏体转变的临界温度,经保温一段时间后,冷却到室温。
设计校型工装,将刚淬火的工件放入校型工装内固定校型,再放入炉中与工件一起回火并定型,这样可以很好地纠正工件淬火后的变形。
经实验证实,外径为φ350mm,厚度为3mm的弹性型面零件在热处理时采用校型工装,其变形量为0.20mm。
如不采用校型工装,变形量将大于1mm。
4钳板零件加工实例
4.1钳板零件图
图2钳板零件示意图
4.2加工钳板零件时存在的问题
由于该零件较薄,材料为1Cr13,铣削时粘刀不利于加工,磨削时散热性差,零件特容易变形,很难达到技术要求。
对于此类薄片零件的加工,通常是用磨削方式进行加工处理的,磨削薄片时存在以下问题。
(1)由于此类零件薄、刚性差,经过铣削后,零件有较大的平面度误差。
(2)零件须进行磨削加工,要将它吸在平面磨床的电磁吸盘上,因零件刚性差,吸紧时零件变平,放松时它又恢复原状,很难达到平面度小于0.02mm要求。
(3)磨削时热量集中,散热困难,也会产生较大的热变形。
有时还会烧伤零件表面。
4.3钳板零件的加工过程及工艺流程图
(1)零件的加工过程
首先,进行铣削粗加工,去除大余量。
铣削过程中,因零件内产生铣削应力,且零件薄和刚性差,引起了较大的弯曲变形(变形量约0.25~0.45mm)。
因此,磨削前须对零件进行校直、并去除应力。
校直采用手压床人工校直,平面度校为0.15mm,然后采用热处理去应力,由于材料为1Cr13属于马氏体不锈钢,热处理采用淬火1050~1100℃,高温回火660~790℃,使其硬度在HB150以上,去除应力后平面度恢复为0.25mm;然后再次校直,平面度校为0.1mm进行磨削。
先粗磨两大平面,平面度小于0.07mm,再去除应力,并校直,使平面度小于0.04mm,再精磨两大平面,留余量0.01mm,最后超精磨达到尺寸及精度要求。
由于零件校直时会产生应力,去除应力后零件又会变形,产生新的平面度误差,所以零件粗加工时要反复进行校直、去应力、磨削加工,逐步去除零件的残余应力。
(2)钳板零件加工工艺流程图,见下图(3)
图3钳板零件工艺流程图
4.4磨削钳板时采取的工艺措施
(1)合理选择磨削砂轮。
1)磨削磨料的选择。
因微晶刚玉具有强度高、韧性好、自锐性好的特性,磨削力和磨削热较少,适宜磨削不锈钢,所以选用微晶刚玉砂轮(MA)。
2)粒度的选择。
磨削表面粗糙度低的零件时,应选择粒度较细的砂轮,磨削薄片零件、导热性差的材料时,为减少磨削热引起的变形和烧伤,应选择粒度较粗的砂轮,综合考虑零件散热差和表面粗糙度低等情况,选择砂轮的粒度为46号。
3)砂轮硬度的选择。
磨削薄片零件,为了防止烧伤,应选用硬度低的砂轮,但砂轮硬度太低,脱落的磨粒会划伤零件表面;经全面考虑选择砂轮的硬度代号为K。
4)砂轮结合剂的选择。
考虑零件易变形,散热困难,表面粗糙度数值Ra0.8um等情况,结合剂选用陶瓷结合剂(V)。
5)砂轮的最终选择。
经过对砂轮磨料、粒度、硬度、结合剂多方面的分析,磨削砂轮选择为MA46KV。
(2)合理选择磨削参数。
经过实践确定如下:
砂轮规格为360×127×40;砂轮速度为20~30m/s;工件速度15m/min;粗磨进给速度为12~15mm/str;精磨进给速度为20mm/str;粗磨磨削深度为0.015mm/str,精磨磨削深度为0.006mm/str。
(3)精细修整砂轮。
修整砂轮时,采用较小的横向进给量和纵向进给量,选用0.15g单颗粒金刚玉,用其尖角精细修整砂轮,以获得等高性较好的微刃。
(4)正确选用冷却液。
选用69-1乳化液,浓度要较高,磨削时要充分浇注,冷却液一定要清洁,以免磨屑和碎粒划伤、拉毛工件表面。
(5)正确安装零件。
零件加工时,将其吸在平面磨床的电磁吸盘上,只允许单件加工,以便散热、减少热变形。
5结束语
通过对薄片零件的加工特点分析,使我更加理解了磨削加工工艺的特点和应用范围,特别是对这种容易变形、装夹比较困难的薄片工件的加工是很难保证其加工精度要求的,但是通过这次的毕业论文使我懂得了是如何来保证其精度要求的,这些方面涉及到很多学科的知识,比如说磨削加工薄片零件,要先考虑到磨削时温度较高,热变形对工件的影响,其次是装夹定位的正确性,然后是加工刀具的选择等等,这些问题都不是孤立存在的,是相互联系的。
随着各种先进技术的应用,低温干切削技术应用于薄片零件的加工也可以收到令人满意的效果。
参考文献
[1]王洪运.金属加工:
冷加工[M].北京:
机械工业出版社,2010年:
45
[2]程焰.磨削加工精度影响:
自然科学版[N].齐齐哈尔:
齐齐哈尔大学出版社,2008年:
23
[3]刘索明,赵强.煤矿机械[M].北京:
机械工业出版社,2008年:
35-37
[4]刘俊成.现代零部件[J].北京:
机械工业出版社,2006年:
70
[5]史文娟.机械制造文摘:
焊接分册[J].哈尔滨:
机械科学研究院哈尔滨焊接研究所出版社,2005年:
25-27
[6]刘俊成.工具技术[J].北京:
机械工业出版社,2005年:
60
[7]羊绍政.机械技术[N].北京:
中国工程物理研究院科学年报中国工程物理研究院出版社,2003年:
7
[8]张文玉,刘先兰.现代机械[M].北京:
机械工业出版社,2002年:
113-114
[9]刘先兰.机械制造[M].北京:
机械工业出版社,2002年:
86
[10]邹济林.精密制造与自动化[M].北京:
机械工业出版社,2001年:
24-25
[11]陆剑中,孙家宁.金属切削原理与刀具[M].北京:
机械工业出版社,2005年(4):
226-231
致谢
本文是在指导教师周国玉老师的精心指导和其他老师、同学的帮助下完成的。
在写作的过程中,周国玉老师从论文的选题到文章的结构和内容方面都给予我精心的指导。
周国玉老师不辞辛苦的指导我如何搜集资料并对论文内容进行细致的指导。
从周国玉老师的指导中,我学到了周国玉老师严谨的治学态度、平易谦和的为人态度和博学创新的思维,也学会了研究问题的思路和方法。
衷心的感谢周国玉老师这段时间对我论文细心、认真的指导!
同时,我还要感谢在大学的班主任宋健文老师的精心栽培,所有任课教师的谆谆教诲,以及院里和校里老师在各方面给予我的帮助。
我要感谢西南大学育才学院四年来所给予我润物细无声的教育,感谢老师和同学在四年中给予我的帮助,感谢父母多年来给予我的培养和鼓励,使我能顺利完成所有学业!
谨向所有关心和帮助过我的老师、同学、朋友和家人表示我最诚挚的谢意!
谢谢你们!