阀体的加工工艺.docx
《阀体的加工工艺.docx》由会员分享,可在线阅读,更多相关《阀体的加工工艺.docx(29页珍藏版)》请在冰豆网上搜索。
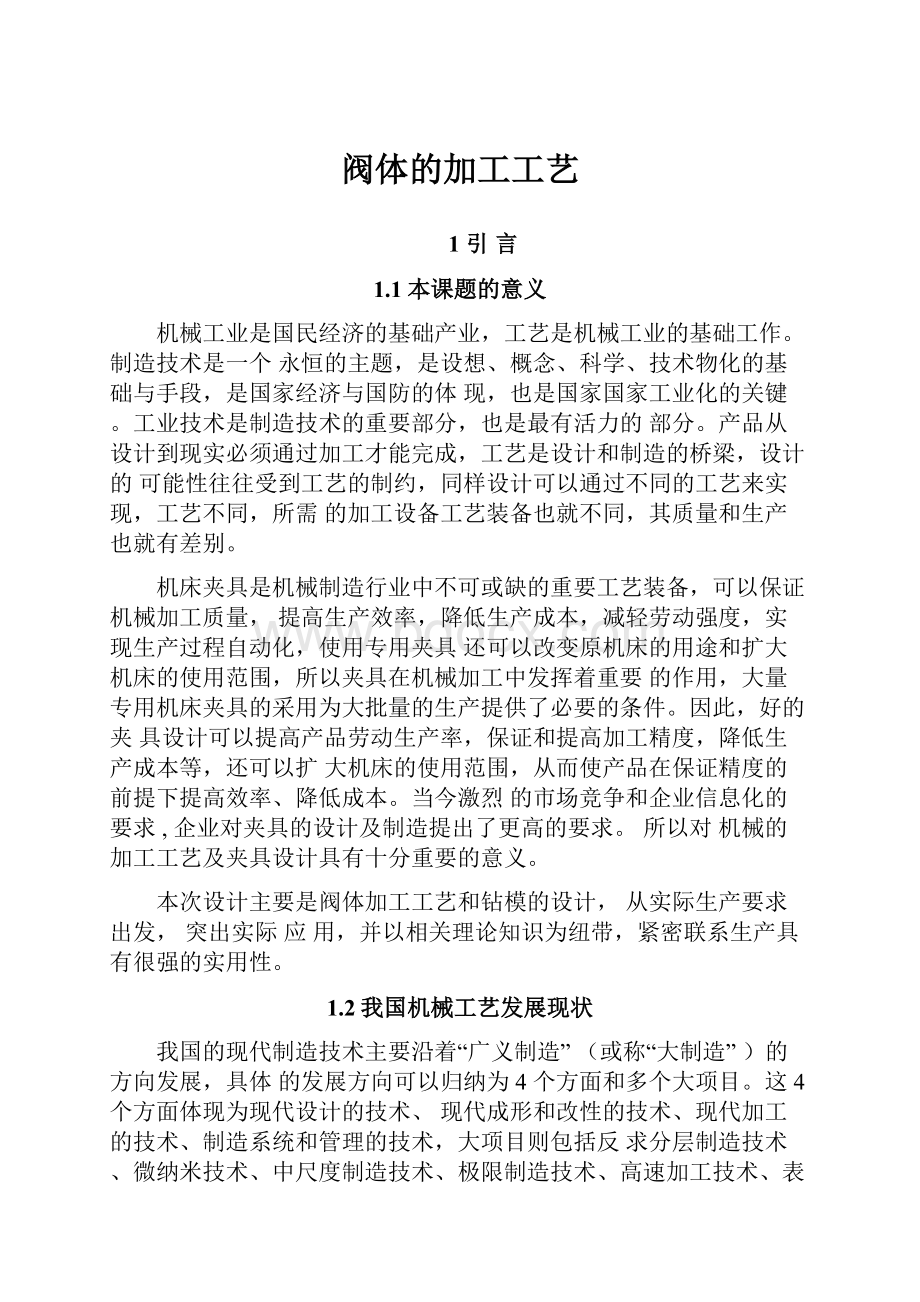
阀体的加工工艺
1引言
1.1本课题的意义
机械工业是国民经济的基础产业,工艺是机械工业的基础工作。
制造技术是一个永恒的主题,是设想、概念、科学、技术物化的基础与手段,是国家经济与国防的体现,也是国家国家工业化的关键。
工业技术是制造技术的重要部分,也是最有活力的部分。
产品从设计到现实必须通过加工才能完成,工艺是设计和制造的桥梁,设计的可能性往往受到工艺的制约,同样设计可以通过不同的工艺来实现,工艺不同,所需的加工设备工艺装备也就不同,其质量和生产也就有差别。
机床夹具是机械制造行业中不可或缺的重要工艺装备,可以保证机械加工质量,提高生产效率,降低生产成本,减轻劳动强度,实现生产过程自动化,使用专用夹具还可以改变原机床的用途和扩大机床的使用范围,所以夹具在机械加工中发挥着重要的作用,大量专用机床夹具的采用为大批量的生产提供了必要的条件。
因此,好的夹具设计可以提高产品劳动生产率,保证和提高加工精度,降低生产成本等,还可以扩大机床的使用范围,从而使产品在保证精度的前提下提高效率、降低成本。
当今激烈的市场竞争和企业信息化的要求,企业对夹具的设计及制造提出了更高的要求。
所以对机械的加工工艺及夹具设计具有十分重要的意义。
本次设计主要是阀体加工工艺和钻模的设计,从实际生产要求出发,突出实际应用,并以相关理论知识为纽带,紧密联系生产具有很强的实用性。
1.2我国机械工艺发展现状
我国的现代制造技术主要沿着“广义制造”(或称“大制造”)的方向发展,具体的发展方向可以归纳为4个方面和多个大项目。
这4个方面体现为现代设计的技术、现代成形和改性的技术、现代加工的技术、制造系统和管理的技术,大项目则包括反求分层制造技术、微纳米技术、中尺度制造技术、极限制造技术、高速加工技术、表面工程技术、质量控制工程、虚拟制造、智能制造、协同制造、绿色制造和共生制造等。
当前,我国工艺发展的重点是并行设计、创新设计、改性技术与现代成形、材料成形过程仿真和优化等。
自动化制造单元在机械制造工艺领域已经逐渐得到广泛应用,其主要特征就是利
用多台或者单台加工机器、数控机床等进行多种产品的加工,因此可以看成是一种小型化的较为
灵活的自动系统。
这是机械制造中自动化生产与成本相互配合作用下的产物,其最大的优势就是
能够提高生产效率从而降低生产成本。
机械制造中的自动化系统由多个自动化数控机床构成,在
统一的计算机体系之下接受控制,进而形成一个简单的加工性的流水线,具有很强的实用性,在我国的企业中得到广泛应用。
该系统中自动化制造和分散控制是主导,具有生产线自动化的特点,已经在很多技术领域广为使用。
1.3机械制造工艺的发展趋势
在机械制造工艺不断发展的今天,其在国内外表现出全球化、自动化、环保化、虚拟化、网络化等发展趋势,下面我们就其中几个方面作个简单探讨。
(1)全球化:
机械制造业的国内、国际市场竞争越来越激烈,不少企业,甚至包括知名企业,在无情的竞争中落败,倒闭的倒闭,被兼并的被兼并,不少暂时还得以在国内市场立足的知名企业只能另辟蹊径,拓展新市场。
网络通讯技术的快速发展进一步推动了企业间既竞争又合作的发展趋势,它与激烈的市场角逐相互作用,成为了制造业全球化的发展动力。
当然我们也需要明确,全球化机械制造的基础是技术网络化,是网络通讯技术的发展使得制造全球化得以完整实现。
(2)自动化:
自动化信息管理一直是机械制造工艺领域追求的终极目标,制造技术自动化可以提高产品的质量和生产率,同时又能降低成本,减轻工人的劳动强度。
目前,制造技术自动化的研究方向主要是制造系统中的集成和系统技术、制造单元技术、人机一体化制造系统、工业机器人、制造过程的计划和调度、柔性制造技术以及适应现代化生产模式的制造环境等。
(3)网络化:
网络通讯技术的迅速发展和普及为企业生产、经营等活动带来了新的变革,零件制造、产品设计、产品销售与市场开拓都变得可以在异地甚至异国进行网络通讯技术的快速发展同时也加快了技术信息的交流,加强了产品开发的合作与经营管理模式的学习,在一定程度上推动了企业向既竞争又合作的方向发展。
众所周知,现代机械制造技术突出表现为现代技术和工业创新的集成,它不仅是国民经济的重要组成部分,也是衡量国家科技发展水平的重要标志,是国际间科技竞争的重点。
我们要抓住机遇,了解机械制造技术工艺的发展特点,把握现代机械制造技术的发展趋势,紧跟发展先进制造技术的世界潮流,将发展现代机械制造工艺放在战略优先地位,尽快缩小与发达国家的差距,才能在全球化的激烈竞争中立于不败之地。
2阀体的加工工艺设计
机械加工工艺是实现产品设计,保证产品质量,节约能源,降低消耗的重要手段,是企业进行生产准备,计划调度,加工操作,安全生产,技术检测和健全劳动组织的重要依据,也是企业上品种,上质量,上水平,加速产品更新,提高经济效益的技术保证。
在实际生产中,由于零件的生产类型、材料、结构、形状、尺寸和技术要求等不同,针对某一零件,往往不是单独在一种机床上,用某一种加工方法就能完成的,而是要经过一定的工艺过程才能完成其加工。
因此,不仅要根据零件的具体要求,结合现场的具体条件,对零件的各组成表面选择合适的加工方法,还要合理地安排加工顺序,逐步地把零件加工出来。
2.1阀体的结构特点和技术要求
阀体是模铸件,根据要求主要是加工孔、底平面。
具体特点和技术要求如下:
①①26的孔与①30孔中心轴线是一条
2①18与①22的孔要有同轴度要求,且与①26与①30孔的轴线有垂直度要求
3左右端面的八个①7孔同轴度位置,需设计一立轴回转分度钻床夹具。
4上下端面各有的两个①7的孔有同轴度要求
2.2阀体的材料、毛坯和热处理
2.2.1毛坯材料及热处理
毛坯材料:
HT150,可热处理强化。
222毛坯的结构确定
毛坯的结构工艺要求:
毛坯的形状尺寸主要由零件组成表的形状、结构、尺寸及加工余量等因素确定,并尽量与零件相近,以达到减少机械加工的切削力,力求达到少或无切削加工,但是,由于现有的毛坯制造技术及成本的限制以及产品零件的加工精度和表面质量要求愈来愈高,所以毛坯某些表面须留一定的加工余量,以便通过机械加工达到零件的技术要求。
设计毛坯形状、尺寸还应考虑到:
1各加工面的几何形状应尽量简单。
2工艺基准以设计基准相一致。
3便于装夹、加工和检查。
在确定毛坯时,要考虑经济性。
虽然毛坯的形状尺寸与零件接近,可以减少加工余量,提高材料的利用率,降低加工成本,但这样可能导致毛坯制造困难,需要采用昂贵的毛坯制造设备,增加毛坯的制造成本。
因此,毛坯的种类形状及尺寸的确定一定要考虑零件成本的问题但要保证零件的使用性能。
在毛坯的种类形状及尺寸确定后,
必要时可据此绘出毛坯图。
2.3工艺过程设计中应考虑的主要问题
2.3.1加工方法选择的原则
1所选加工方法应考虑每种加工方法的经济、精度要求相适应。
2所选加工方法能确保加工面的几何形状精度,表面相互位置精度要求。
3所选加工方法要与零件材料的可加工性相适应。
4加工方法要与生产类型相适应。
5所选加工方法企业现有设备条件和工人技术水平相适应。
2.3.2加工阶段的划分
按照加工性质和作用的不同,工艺过程一般可划分为三个加工阶段:
1粗加工阶段
粗加工的目的是切去绝大部分多余的金属,为以后的精加工创造较好的条件,并为半精加工,精加工提供定位基准,粗加工时能及早发现毛坯的缺陷,予以报废或修补,以免浪费工时。
粗加工可采用功率大,刚性好,精度低的机床,选用大的切前用量,以提高生产率、粗加工时,切削力大,切削热量多,所需夹紧力大,使得工件产生的内应力和变形大,所以加工精度低,粗糙度值大。
一般粗加工的公差等级为IT11~IT12,粗糙度为Ra20-50um。
2半精加工阶段
半精加工阶段是完成一些次要面的加工并为主要表面的精加工做好准备,保证合适的加工余量。
半精加工的公差等级为IT9~IT10。
表面粗糙度为Ra10~1.25um。
3精加工阶段
精加工阶段切除剩余的少量加工余量,主要目的是保证零件的形状位置几精度,尺寸精度及表面粗糙度,使各主要表面达到图纸要求•另外精加工工序安排在最后,可防止或减少工件精加工表面损伤。
精加工应采用高精度的机床小的切前用量,工序变形小,有利于提高加工精度.精加工的加工精度一般为IT6~IT7,表面粗糙度为Ra1.6~0.8um
233工序的合理组合
确定加工方法以后,就按生产类型、零件的结构特点、技术要求和机床设备等具体生产条件确定工艺过程的工序数。
确定工序数的基本原则:
1工序分散原则
工序内容简单,有利选择最合理的切削用量。
便于采用通用设备。
简单的机床工艺装备。
生产准备工作量少,产品更换容易。
对工人的技术要求水平不高。
但需要设备和工人数量多,生产面积大,工艺路线长,生产管理复杂。
2工序集中原则
工序数目少,工件装,夹次数少,缩短了工艺路线,相应减少了操作工人数和生产面积,也简化了生产管理,在一次装夹中同时加工数个表面易于保证这些表面间的相互位置精度。
使用设备少,大量生产可采用高效率的专用机床,以提高生产率。
但采用复杂的专用设备和工艺装备,使成本增高,调整维修费事,生产准备工作量大。
一般情况下,单件小批生产中,为简化生产管理,多将工序适当集中。
但由于不采用专用设备,工序集中程序受到限制。
结构简单的专用机床和工夹具组织流水线生产。
234加工顺序的安排
零件的加工过程通常包括机械加工工序,热处理工序,以及辅助工序。
在安排加工顺序时常遵循以下原则:
表2.2加工工序安排原则
工序类别
工序
安排原则
机械加工
1)对于形状复杂、尺寸较大的毛坯,先安排划线工序,
为精基准加工提供找正基准
2)按“先基准后其他”的顺序,首先加工精基准
3)在重要表面加工前应对精基准进行修正
4)按“先主后次,先粗后精”的顺序
5)对于与主要表面有位置精度要求的次要表面应安排在
主要表面加工之后加工
辅助工序
中间检验
一般安排在粗加工全部结束之后,精加工之前;花费工时
较多和重要工序的前后
2.4阀体的机械加工工艺过程分析
图2-1阀体零件图
由图2-1可知:
1该零件为模铸件,材料为HT150
2要求加工同心孔,表面粗糙度Ra=12.5um
3要求粗加工上下端面,表面粗糙度Ra=12.5um
4要求粗加工左右端面,表面粗糙度Ra=12.5um
5要求加工①18孔,①20孔,①22孔,①26孔
7要求粗加工上下端面①7孔。
8要求粗加工左右端面①7孔。
9要求加工①36孔
由零件图分析知,该零件有铣削部分、钻孔部分。
在钻上加工深孔和同轴孔;铣
削部分有粗加工平面;钻孔部分为在立式钻床上加工①7通孔
金——八技术要求
1.ML帥粉祕師劈L
工冊髓、骨蘇财臥、讎、变騎醸.
izjLM
阀体的毛坯图
242阀体的工艺的路线
拟定工艺路线是制定工艺过程的关键性的一步。
在拟定时应充分调查研究,多提几个方案,加以分析比较确定一个最合理方案。
采用加工方法一般所能达到的公差等级和表面粗糙度以及需留的加工余量
表(参考参数)
表面
加工
加工
粗糙
表面
公差
公差
加工
说明
表面
方法
度
光洁
等级
等级
余量
Ra
度
粗车
12.5
1~3
IT12~IT11
11~10
1~5
指尺寸在直
外
半精车
6.3
4~5
IT10~IT9
10~8
0.50~1.60
径180以下,
精车
1.6
6~7
IT8~IT7
8~7
0.2~0.5
长度在500
细车
0.8
7~8
IT6~IT5
7~6
0.1~0.25
以下,铸件的
圆
粗磨
1.0
6~7
IT8~IT7
7
0.25~0.85
直径余量
精磨
0.4
8~9
IT6~IT5
6
0.06
研磨
0.1
10~14
IT6~IT5
4~5
0.10~0.03
钻孑L
25
1~3
IT13~IT11
12
0.3~0.5
指孔径在
扩孔
6.3
4~5
IT10~IT9
10
>1.8
180以下,铸
粗镗
6.3
2~4
IT10~IT9
9~8
1.0~1.8
件直径的余
半精镗
3.2
5~6
IT9~IT8
8
0.5~0.8
量.L/d<2
内
精镗
1.6
6~7
IT8~IT7
7
0.1~0.3
L/d=2~10时,
细镗
0.2
9~10
IT7~IT6
6
0.1~0.55
加工误差增
粗铰
3.2
5~6
IT8
8~7
0.4~0.2
加1.2~2倍
孔
精铰
1.6
6~7
IT7
7~6
0.2~0.3
粗磨
1.6
6~7
IT8
7
0.2~0.5
精磨
0.2
910
IT7~IT6
6
0.1~0.2
研磨
0.1
10~14
IT7~IT6
5~4
0.01~0.02
粗刨,粗铳
12.5
1~3
IT14~IT11
11~9
0.9~2.3
指平面最大
平
精刨,精铳
6.3
4~6
IT10
10~9
0.2~0.3
尺寸500以
粗磨
1.6
6~7
IT9
8~6
0.05
下的铸件的
面
半精磨
0.8
7~9
IT7~IT6
7~5
0.03
平面余量
精磨
0.8
7~9
IT7~IT6
7~5
0.03
研磨
0.1
10~14
IT5
5~2
0.01~0.03
243阀体加工工艺路线的确定
在保证零件尺寸公差、形位公差及表面粗糙度等技术条件下,成批量生产可以考虑采用专用机床,以便提高生产率。
但同时考虑到经济效果,降低生产成本,阀体具体加工工艺过程可以设计两个,具体如下表:
表2.4机械加工工艺过程1
•
工序内容
加工车
间
设备名
称
工艺设备名称
夹具
刀具
量具
1
备料用铸锻方法获得毛坯
铸造车
间
模铸
2
毛坯时效处理
热处理
间
自然
3
粗铳阀体左右端面
金工车
间
普通铳
床
专用夹
具
/、
端面铳
刀
专用
量具
4
粗铳阀体上下端面
金工车
间
普通铳
床
专用夹
具
/、
端面铳
刀
专用
量具
5
钻左端面①7的孔
金工车
间
普通钻
床
专用夹
具
/、
高速钢
钻头
专用
量具
6
钻左端面①20的孔
金工车
间
普通钻
床
专用夹
具
/、
高速钢
钻头
专用
量具
7
锪左端面①26的孔
金工车
间
普通钻
床
专用夹
具
/、
高速钢
钻头
专用
夹具
8
钻右端面①7的孔
金工车
间
普通钻
床
专用夹
具
/、
高速钢
钻头
专用
量具
9
绞右端面①36的孔
金工车
间
普通钻
床
专用夹
具
/、
高速钢
钻头
专用
量具
10
钻下端面①18孔
金工车
普通钻
专用夹
高速钢
专用
间
床
具
/、
钻头
量具
11
钻下端面①7的孔
金工车
间
普通钻
床
专用夹
具
/、
高速钢
钻头
专用
夹具
12
钻上端面①22的孔
金工车
间
普通钻
床
专用夹
具
/、
高速钢
钻头
专用
夹具
13
钻上端面①7的孔
金工车
间
普通钻
床
专用夹
具
/、
高速钢
钻头
专用
夹具
14
去毛刺
15
清洗
16
终检入库
表2.5机械加工工艺过程2
•
工序内容
加工车
间
设备名
称
工艺设备名称
夹具
刀具
量具
1
备料用铸锻方法获得毛坯
铸造车
间
模铸
2
毛坯时效处理
热处理
间
自然
3
粗铳阀体左右端面
金工车
间
普通铳
床
专用夹
具
/、
端面铳
刀
专用
量具
4
钻左端面①7的孔
普通钻
床
专用夹
具
/、
高速钢
钻头
5
钻左端面①20的孔
金工车
间
普通钻
床
专用夹
具
/、
高速钢
钻头
专用
量具
6
钻左端面①26的孔
金工车
间
普通钻
床
专用夹
具
/、
高速钢
钻头
专用
量具
7
钻右端面①7的孔
金工车
间
普通钻
床
专用夹
具
/、
高速钢
钻头
专用
夹具
7
钻右端面①7的孔
金工车
普通钻
专用夹
高速钢
专用
间
床
具
/、
钻头
夹具
8
绞右端面①36的孔
金工车
间
普通钻
床
专用夹
具
/、
高速钢
钻头
专用
量具
9
粗铳阀体上下端面
金工车
间
普通铳
床
专用夹
具
/、
端面铳
刀
专用
量具
10
钻下端面①18的孔
金工车
间
普通钻
床
专用夹
具
/、
高速钢
钻头
专用
量具
11
钻下端面①7的孔
金工车
间
普通钻
床
专用夹
具
/、
高速钢
钻头
专用
夹具
12
钻上端面①22的孔
金工车
间
普通钻
床
专用夹
具
/、
高速钢
钻头
专用
夹具
13
钻上端面①7的孔
金工车
间
普通钻
床
专用夹
具
/、
高速钢
钻头
专用
夹具
14
去毛刺
15
清洗
终检入库
通过对以上两个工艺过程进行比较,可以发现工艺规程2在对零件进行机加工时,
由于没有对上下底面进行粗加工,会对之前所列出的加工的定位产生很大的影响,从而使零件很难甚至不可能达到要求的精度,因此采用工艺规程1,运用工艺规程1对
阀体进行机加工。
2.5阀体的工序设计
工序设计包括工序基准的选择、工序尺寸的确定、加工余量的确定、机床的选择、工艺装备的选择、切削用量的选择和时间定额的确定。
2.5.1工序基准的选择
工序基准是在工序图上以标定被加工表面位置尺寸和位置精度的基准。
所标定的位置尺寸和位置精度分别称为工序尺寸和工序技术要求,工序尺寸和工序技术要求的内容在加工后应进行测量,测量时所用的基准称为测量基准。
通常工序基准和测量基
准重合。
工序基准的选择应注意以下几点:
1选设计基准为工序基准时,对工序尺寸的检验就是对设计尺寸的检验,有利于减少检验工作量。
2当本工序中位置精度是由夹具保证而不需要进行试切,应使工序基准与设计基准重合。
3对一次安装下所加工各个表面,各加工面之间的工序尺寸应与设计尺寸一致。
2.5.2确定各工序的加工设备和工艺装备
2.5.2.1机床的选用原则
⑴机床的加工尺寸范围应与零件的外轮廓尺寸相适应。
⑵机床的工作精度应与工序要求精度相适应。
⑶机床的生产率应与工件的生产类型相适应。
查资料可得,具体的机床选择如下:
立式钻床(Z5030A),主要用于钻孔和扩孔。
万能铣床(XW6032A,主要用于铣平面加工。
2.5.2.2刀具的选用
刀具的选择主要取决于工序采用的加工方法,加工表面的尺寸,工件材料,所要求的加工精度,表面粗糙度,生产率及经济性等,一般应尽可能采用标准刀具,必要时采用高生产率的复合刀具及其化专用刀具。
查资料可得具体刀具选择如下:
铣刀:
材料高速钢(W18Cr4V)
圆柱形铣刀:
D=63mmL=70mmZ=10(GB/T1115.1-2002)钻头:
材料高速钢(W18Cr4V)
直柄长麻花钻:
①8(GB/T1135.4-1996)
专用复合刀具:
材料高速钢
用于加工①7通孔
2.5.3阀体切削用量和工序尺寸的确定
在这只确定钻上端面©7孔的加工余量、和公差。
由表2-28可查得钻孔余量Z钻=0.2mm。
查表1-20可依次确定各工序尺寸的加工精度等级为,镗:
IT12。
根据上述结果,再查标准公差数值表可确定各工步的公差值分别为,钻:
0.15mm
综上所述,该工序各工步的工序尺寸及公差分别为,钻:
©7+0.14mm
2.5.4切削用量的计算
钻①7孔
1背吃刀量的选择
由表查得,铰削前孔的直径是6.8mm因此铰孔工位的背吃刀量
ap=7mm-6.8mm=0.15mm
2进给量的选择
由表5-31查得在铸铁上铰©7的孔,进给量f=0.30~0.50mm/r,故暂取f=0.40mm/r。
3切削速度的选择
由表5-31知在铸件上铰©7的孔,v=2~6m/min,故暂取v=4m/min。
1000v1000*4
所以王轴转速n===181.89r/min
HDn*7
取转速n=185r/min。
可求出实际切削速度v=n二d/1000=4.07m/min。
3专用夹具设计
为了提高劳动生产率,保证加工质量,降低劳动强度。
在加工曲柄板沉孔时,需要设计专用夹具。
一个优良的机床夹具必须满足下列基本要求:
(1)保证工件的加工精度保证加工精度的关键,首先在于正确地选定定位基准、定位方法和定位元件,必要时还需进行定位误差分析,还要注意夹具中其他零部件的
结构对加工精度的影响,确保夹具能满足工件的加工精度要求。
(2)提高生产效率专用夹具的复杂程度应与生产纲领相适应,应尽量采用各种快速高效的装夹机构,保证操作方便,缩短辅助时间,提高生产效率。
(3)工艺性能好专用夹具的结构应力求简单、合理,便于制造、装配、调整、检验、维修等。
专用夹具的制造属于单件生产,当最终精度由调整或修配保证时,夹具上应设置调整和修配结构。
(4)使用性能好专用夹具的操作应简便、省力、安全可靠。
在客观条件允许且又经济适用的前提下,应尽可能采用气动、液压等机械化夹紧装置,以减轻操作者的劳动强度。
专用夹具还应排屑方便。
必要时可设置排屑结构,防止切屑破坏工件的定位和损坏刀具,防止切屑的积聚带来大量的热量而引起工艺系统变形。
(5)经济性好专用夹具应尽可能采用标准元件和标准结构,力求结构简单、制造容易,以降低夹具的制造成本。
因此,设计时应根据生产纲领对夹具方案进行必要的技术经济分析,以提高夹具在生产中的经济效益。
3.1夹具的基本概念及基本原理
3.1.1夹具的3.1.1.1夹具的组成
按在夹具中的作用、地位及结构特点、组成夹具的元件可以分为以下几类
(1)