汽轮机结构原理与运行培训.docx
《汽轮机结构原理与运行培训.docx》由会员分享,可在线阅读,更多相关《汽轮机结构原理与运行培训.docx(26页珍藏版)》请在冰豆网上搜索。
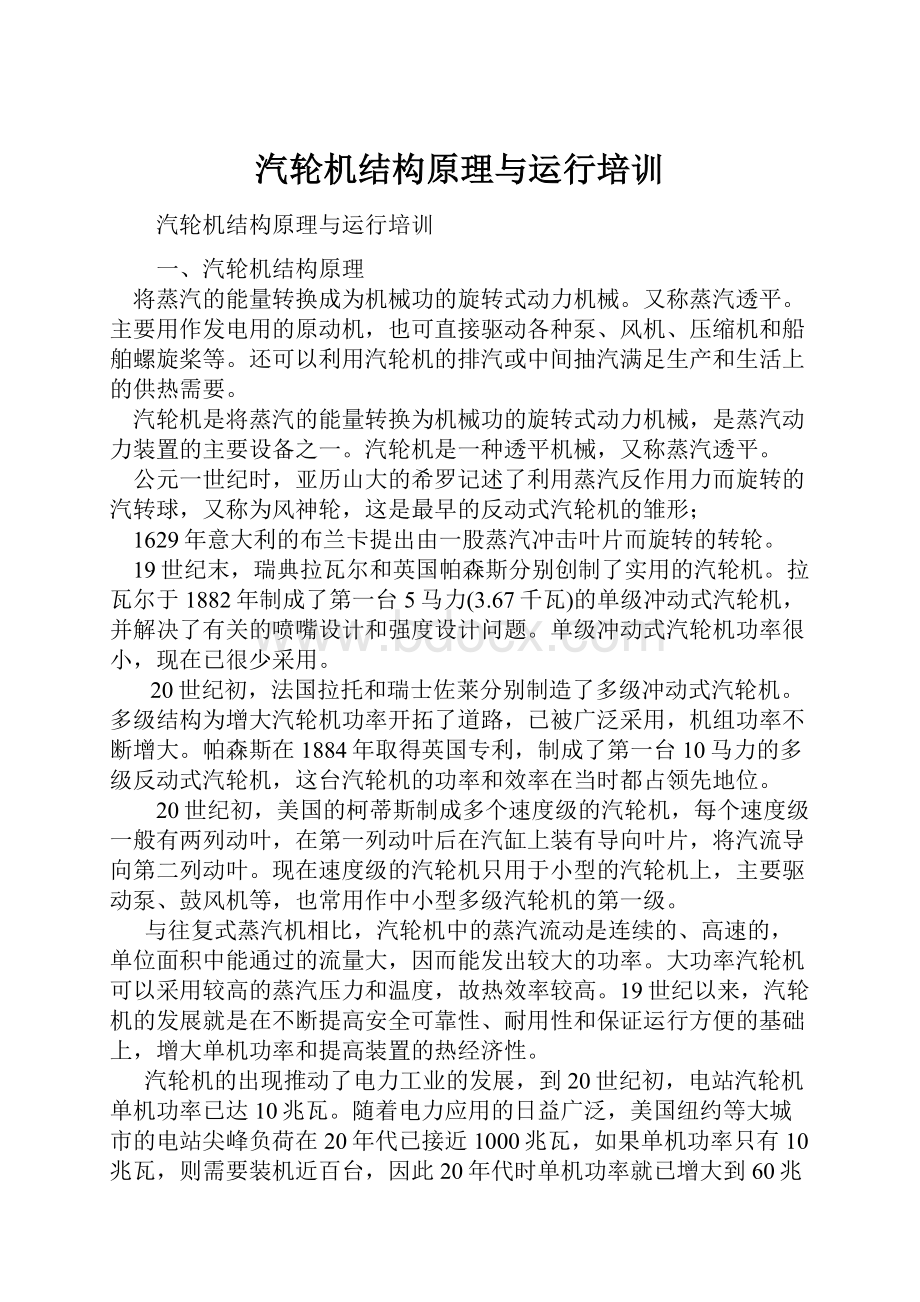
汽轮机结构原理与运行培训
汽轮机结构原理与运行培训
一、汽轮机结构原理
将蒸汽的能量转换成为机械功的旋转式动力机械。
又称蒸汽透平。
主要用作发电用的原动机,也可直接驱动各种泵、风机、压缩机和船舶螺旋桨等。
还可以利用汽轮机的排汽或中间抽汽满足生产和生活上的供热需要。
汽轮机是将蒸汽的能量转换为机械功的旋转式动力机械,是蒸汽动力装置的主要设备之一。
汽轮机是一种透平机械,又称蒸汽透平。
公元一世纪时,亚历山大的希罗记述了利用蒸汽反作用力而旋转的汽转球,又称为风神轮,这是最早的反动式汽轮机的雏形;
1629年意大利的布兰卡提出由一股蒸汽冲击叶片而旋转的转轮。
19世纪末,瑞典拉瓦尔和英国帕森斯分别创制了实用的汽轮机。
拉瓦尔于1882年制成了第一台5马力(3.67千瓦)的单级冲动式汽轮机,并解决了有关的喷嘴设计和强度设计问题。
单级冲动式汽轮机功率很小,现在已很少采用。
20世纪初,法国拉托和瑞士佐莱分别制造了多级冲动式汽轮机。
多级结构为增大汽轮机功率开拓了道路,已被广泛采用,机组功率不断增大。
帕森斯在1884年取得英国专利,制成了第一台10马力的多级反动式汽轮机,这台汽轮机的功率和效率在当时都占领先地位。
20世纪初,美国的柯蒂斯制成多个速度级的汽轮机,每个速度级一般有两列动叶,在第一列动叶后在汽缸上装有导向叶片,将汽流导向第二列动叶。
现在速度级的汽轮机只用于小型的汽轮机上,主要驱动泵、鼓风机等,也常用作中小型多级汽轮机的第一级。
与往复式蒸汽机相比,汽轮机中的蒸汽流动是连续的、高速的,单位面积中能通过的流量大,因而能发出较大的功率。
大功率汽轮机可以采用较高的蒸汽压力和温度,故热效率较高。
19世纪以来,汽轮机的发展就是在不断提高安全可靠性、耐用性和保证运行方便的基础上,增大单机功率和提高装置的热经济性。
汽轮机的出现推动了电力工业的发展,到20世纪初,电站汽轮机单机功率已达10兆瓦。
随着电力应用的日益广泛,美国纽约等大城市的电站尖峰负荷在20年代已接近1000兆瓦,如果单机功率只有10兆瓦,则需要装机近百台,因此20年代时单机功率就已增大到60兆瓦,30年代初又出现了165兆瓦和208兆瓦的汽轮机。
此后的经济衰退和第二次世界大战期间爆发,使汽轮机单机功率的增大处于停顿状态。
50年代,随着战后经济发展,电力需求突飞猛进,单机功率又开始不断增大,陆续出现了325~600兆瓦的大型汽轮机;
60年代制成了1000兆瓦汽轮机;
70年代,制成了1300兆瓦汽轮机。
现在许多国家常用的单机功率为300~600兆瓦。
汽轮机在社会经济的各部门中都有广泛的应用。
汽轮机种类很多,并有不同的分类方法。
按结构分,有单级汽轮机和多级汽轮机;各级装在一个汽缸内的单缸汽轮机,和各级分装在几个汽缸内的多缸汽轮机;各级装在一根轴上的单轴汽轮机,和各级装在两根平行轴上的双轴汽轮机等。
按工作原理分,有蒸汽主要在各级喷嘴(或静叶)中膨胀的冲动式汽轮机;蒸汽在静叶和动叶中都膨胀的反动式汽轮机;以及蒸汽在喷嘴中膨胀后的动能在几列动叶上加以利用的速度级汽轮机。
按热力特性分,有为凝汽式、供热式、背压式、抽汽式和饱和蒸汽汽轮机等类型。
凝汽式汽轮机排出的蒸汽流入凝汽器,排汽压力低于大气压力,因此具有良好的热力性能,是最为常用的一种汽轮机;供热式汽轮机既提供动力驱动发电机或其他机械,又提供生产或生活用热,具有较高的热能利用率;背压式汽轮机的排汽压力大于大气压力的汽轮机;抽汽式汽轮机是能从中间级抽出蒸汽供热的汽轮机;饱和蒸汽轮机是以饱和状态的蒸汽作为新蒸汽的汽轮机。
汽轮机的蒸汽从进口膨胀到出口,单位质量蒸汽的容积增大几百倍,甚至上千倍,因此各级叶片高度必须逐级加长。
大功率凝汽式汽轮机所需的排汽面积很大,末级叶片须做得很长。
汽轮机装置的热经济性用汽轮机热耗率或热效率表示。
汽轮机热耗率是每输出单位机械功所消耗的蒸汽热量,热效率是输出机械功与所耗蒸汽热量之比。
对于整个电站,还需考虑锅炉效率和厂内用电。
因此,电站热耗率比单独汽轮机的热耗率高,电站热效率比单独汽轮机的热效率低。
一座汽轮发电机总功率为1000兆瓦的电站,每年约需耗用标准煤230万吨。
如果热效率绝对值能提高1%,每年可节约标准煤6万吨。
因此,汽轮机装置的热效率一直受到重视。
为了提高汽轮机热效率,除了不断改进汽轮机本身的效率,包括改进各级叶片的叶型设计(以减少流动损失)和降低阀门及进排汽管损失以外,还可从热力学观点出发采取措施。
根据热力学原理,新蒸汽参数越高,热力循环的热效率也越高。
早期汽轮机所用新蒸汽压力和温度都较低,热效率低于20%。
随着单机功率的提高,30年代初新蒸汽压力已提高到3~4兆帕,温度为400~450℃。
随着高温材料的不断改进,蒸汽温度逐步提高到535℃,压力也提高到6~12.5兆帕,个别的已达16兆帕,热效率达30%以上。
50年代初,已有采用新蒸汽温度为600℃的汽轮机。
以后又有新蒸汽温度为650℃的汽轮机。
现代大型汽轮机按照其输出功率的不同,采用的新蒸汽压力又可以分为各个压力等级,通常采用新蒸汽压力24.5~26兆帕,新蒸汽温度和再热温度为535~578℃的超临界参数,或新汽压力为16.5兆帕、新汽温度和再热温度为535℃的亚临界参数。
使用这些汽轮机的电站热效率约为40%。
另外,汽轮机的排汽压力越低,蒸汽循环的热效率就越高。
不过排汽压力主要取决凝汽器的真空度,真空度又取决于冷却水的温度和抽真空的设备(通常称为真空泵),如果采用过低的排汽压力,就需要增大冷却水流量、增大凝汽器冷却水和冷却介质的换热面、降低被使用的冷却水的温度和抽真空的设备,较长的末级叶片,但同时真空太低又会导致汽轮机汽缸(低压缸)的蒸汽流速加快,使汽轮机汽缸(低压缸)差胀加剧,危及汽轮机安全运转。
凝汽式汽轮机常用的排汽压力为5~10千帕(一个标准大气压是101325帕斯卡)。
船用汽轮机组为了减轻重量,减小尺寸,常用0.006~0.01兆帕的排汽压力。
此外,提高汽轮机热效率的措施还有,采用回热循环、采用再热循环、采用供热式汽轮机等。
提高汽轮机的热效率,对节约能源有着重大的意义。
大型汽轮机组的研制是汽轮机未来发展的一个重要方向,这其中研制更长的末级叶片,是进一步发展大型汽轮机的一个关键;研究提高热效率是汽轮机发展的另一方向,采用更高蒸汽参数和二次再热,研制调峰机组,推广供热汽轮机的应用则是这方面发展的重要趋势。
现代核电站汽轮机的数量正在快速增加,因此研究适用于不同反应堆型的、性能良好的汽轮机具有特别重要的意义。
全世界利用地热的汽轮机的装机容量,1983年已有3190兆瓦,不过对熔岩等深层更高温度地热资源的利用尚待探索;利用太阳能的汽轮机电站已在建造,海洋温差发电也在研究之中。
所有这些新能源方面的汽轮机尚待继续进行试验研究。
另外,在汽轮机设计、制造和运行过程中,采用新的理论和技术,以改善汽轮机的性能,也是未来汽轮机研究的一个重要内容。
例如:
气体动力学方面的三维流动理论,湿蒸汽双相流动理论;强度方面的有限元法和断裂力学分析;振动方面的快速傅里叶转换、模态分析和激光技术;设计、制造工艺、试验测量和运行监测等方面的电子计算机技术;寿命监控方面的超声检查和耗损计算。
此外,还将研制氟利昂等新工质的应用,以及新结构、新工艺和新材料等。
目前发展瓶颈主要在材料上,材料问题解决了,单片的功率就可以更大。
凝汽式汽轮机
火电厂中普遍采用的专为发电用的汽轮机。
凝汽设备主要由凝汽器、循环水泵、凝结水泵和抽气器组成。
汽轮机排汽进入凝汽器,被循环水冷却凝结为水,由凝结水泵抽出,经过各级加热器加热后作为给水送往锅炉。
汽轮机的排汽在凝汽器内受冷凝结为水的过程中,体积骤然缩小,因而原来充满蒸汽的密闭空间形成真空,这降低了汽轮机的排汽压力,使蒸汽的理想焓降增大,从而提高了装置的热效率。
汽轮机排汽中的非凝结气体(主要是空气)则由抽气器抽出,以维持必要的真空度。
汽轮机最常用的凝汽器为表面式。
冷却水排入冷却水池或冷却水塔降温后再循环使用。
靠近江、河、湖泊的电厂,如水量充足,可将由凝汽器排出的冷却水直接排入江、河、湖泊,称为径流冷却方式。
但这种方式可能对河流湖泊造成热污染。
严重缺水地区的电厂,可采用空冷式凝汽器。
但它结构庞大,金属材料消耗多,除列车电站外,一般电厂较少采用。
老式电厂中,有的采用混合式凝汽器,汽轮机排汽与冷却水直接混合接触冷却。
但因排汽凝结水被冷却水污染,需要处理后才能作为锅炉给水,已很少采用。
运行特性 凝汽式汽轮机的排汽压力对运行经济性有明显影响。
影响凝汽器真空度的主要因素是冷却水进口温度和冷却倍率。
前者与电厂所在地区、季节及供水方式有关;后者表示冷却水设计流量与汽轮机排汽量之比。
冷却倍率大,可获得较高真空度。
但冷却倍率增大的同时增加了循环水泵的功耗和设备投资。
一般表面式凝汽器的冷却倍率设计为60~120。
由于凝汽式汽轮机循环水的需要量很大,水源条件成为电厂选址的重要条件之一。
理想情况下表面式凝汽器的凝水温度应与排汽温度相同,被冷却水带走的热量仅为排汽的汽化潜热。
但实际运行中,由于排汽流动阻力及非凝结气体的存在,导致凝结水温度低于排汽温度,两者的温差称为过冷却度。
冷却水管布置不当,运行中凝结水位过高而浸泡冷却水管,均会加大过冷却度。
正常情况过冷却度应不大于1~2℃。
排汽压力与机组功率 降低凝汽式汽轮机的排汽压力,虽可提高热效率,但因排汽比容增大,汽轮机末级通流面积和叶片需要相应增大,这加大了制造成本,使加工困难。
因此,最佳排汽压力需通过技术经济综合分析确定。
目前一般凝汽式汽轮机排汽压力取为0.004~0.006兆帕。
汽轮机功率决定于蒸汽流量。
凝汽式汽轮机可通过的最大流量决定于末级叶片长度。
由于叶片越大,离心力越大,这使它受到材料强度的限制。
目前,末级叶片最大长度可达1000~1200毫米,叶片顶端最大允许圆周速度为550~650米/秒,单排汽口极限功率约为100~120兆瓦。
低压缸采用分流式结构可提高单机功率。
到80年代末,常规火电厂最大凝汽式单机功率,双轴机组为1300兆瓦,单轴机组为800兆瓦。
凝汽式机组设计为低转速(1500或1800转/分)时,可提高极限功率,但这又使汽轮机尺寸及材料消耗增加,因为汽轮机总重量与转速的三次方成反比。
因此,除核电站为适应低参数、大流量特点,常采用低速汽轮机外,中国火力发电厂均采用3000转/分汽轮机。
汽轮机工作原理
汽轮机是将蒸汽的热能转换成机械能的蜗轮式机械。
在汽轮机中,蒸汽在喷嘴中发生膨胀,压力降低,速度增加,热能转变为动能。
如图1所示。
高速汽流流经动叶片3时,由于汽流方向改变,产生了对叶片的冲动力,推动叶轮2旋转做功,将蒸汽的动能变成轴旋转的机械能。
图1冲动式汽轮机工作原理图
1-轴;2-叶轮;3-动叶片;4-喷嘴
2汽轮机结构
汽轮机主要由转动部分(转子)和固定部分(静体或静子)组成。
转动部分包括叶栅、叶轮或转子、主轴和联轴器及紧固件等旋转部件。
固定部件包括气缸、蒸汽室、喷嘴室、隔板、隔板套(或静叶持环)、汽封、轴承、轴承座、机座、滑销系统以及有关紧固零件等。
套装转子的结构如图2所示。
套装转子的叶轮、轴封套、联轴器等部件和主轴是分别制造的,然后将它们热套(过盈配合)在主轴上,并用键传递力矩。
图2套装转子结构
1-油封环2-油封套3-轴4-动叶槽5-叶轮6-平衡槽
汽轮机主要用途是在热力发电厂中做带动发电机的原动机。
为了保证汽轮机正常工作,需配置必要的附属设备,如管道、阀门、凝汽器等,汽轮机及其附属设备的组合称为汽轮机设备。
图3为汽轮机设备组成图。
来自蒸汽发生器的高温高压蒸汽经主汽阀、调节阀进入汽轮机。
由于汽轮机排汽口的压力大大低于进汽压力,蒸汽在这个压差作用下向排汽口流动,其压力和温度逐渐降低,部分热能转换为汽轮机转子旋转的机械能。
做完功的蒸汽称为乏汽,从排汽口排入凝汽器,在较低的温度下凝结成水,此凝结水由凝结水泵抽出送经蒸汽发生器构成封闭的热力循环。
为了吸收乏汽在凝汽器放出的凝结热,并保护较低的凝结温度,必须用循环水泵不断地向凝汽器供应冷却水。
由于汽轮机的尾部和凝汽器不能绝对密封,其内部压力又低于外界大气压,因而会有空气漏入,最终进入凝汽器的壳侧。
若任空气在凝汽器内积累,凝汽器内压力必然会升高,导致乏汽压力升高,减少蒸汽对汽轮机做的有用功,同时积累的空气还会带来乏汽凝结放热的恶化,这两者都会导致热循环效率的下降,因而必须将凝汽器壳侧的空气抽出。
凝汽设备由凝汽器、凝结水泵、循环水泵和抽气器组成,它的作用是建立并保持凝汽器的真空,以使汽轮机保持较低的排汽压力,同时回收凝结水循环使用,以减少热损失,提高汽轮机设备运行的经济性。
图3汽轮机设备组成图
1-主汽阀2-调节阀3-汽轮机4-凝汽器5-抽汽器6-循环水泵
7-凝结水泵8-低压加热器9-除氧器10-除水泵11-高压加热器
为了调节汽轮机的功率和转速,每台汽轮机有一套由调节装置组成的调节系统。
另外,汽轮机是高速旋转设备,它的转子和定子间隙很小,是既庞大又精密的设备。
为保证汽轮机安全运行,配有一套自动保护装置,以便在异常情况下发出警报,在危急情况下自动关闭主汽阀,使之停运。
调节系统和保护装置常用压力油来传递信号和操纵有关部件。
汽轮机的各个轴承也需要油润滑和冷却,因而每台汽轮机都配有一套润滑油系统。
总之,汽轮机设备是以汽轮机为核心,包括凝汽设备、回热加热设备、调节和保护装置及供油系统等附属设备在内的一系列动力设备组合。
正是靠它们协调有序地工作,才得以完成能量转换的任务。
火力发电原理:
火力发电一般是指利用煤炭、石油和天然气等燃料燃烧时产生的热能来加热水,使水变成高温、高压水蒸气,然后再由水蒸气推动发电机来发电的方式的总称。
我国的火电厂以燃煤为主。
优越性:
投资相对较少,适合我国现阶段国情;烧煤比较便宜。
传统的火力发电站的燃烧能量大约有近70%要消耗在锅炉和汽轮发电机这些庞大的设备上。
弊端及对环境的影响:
烟气污染:
煤炭直接燃烧排放的SO2、NOX等酸性气体不断增长,使我国很多地区酸雨量增加。
全国每年产生140万吨SO2。
粉尘污染:
对电站附近环境造成粉煤灰污染,对人们的生活及植物的生长造成不良影响。
全国每年产生1500万吨烟尘。
资源消耗:
发电的汽轮机通常选用水作为冷却介质,一座1000MW火力发电厂每日的耗水量约为十万吨。
全国每年消耗5000万吨标准煤。
火力发电污染严重,电力工业已经成为我国最大的污染排放产业之一
改进:
利用各种技术提高发电效率;对烟尘采用脱硫除尘处理或改烧天然气;气轮机改用空气冷却。
二、汽轮机运行培训
1、轴封冷却器的作用?
答;汽轮机采用内泄式轴封系统时,一般设轴封加热器(轴封冷却器)用一加热凝结水,回收轴封漏汽,从而减少轴封漏汽及热量损失,并改善车间的环境条件。
随轴封漏汽进入的空气,常用连通管引到射水抽汽器扩压管处,靠后者的负压来抽除,从而确保轴封加热器的微真空状态。
这样,各轴封的第一腔室也保持微真空,轴封汽不外泄。
作用:
用来抽出汽轮机汽封系统的汽气混合物,防止蒸汽从端部汽封漏到汽机房和油系统中去而污染环境和破坏油质。
这些汽气混合物进入轴封冷却器被冷却成水,将凝结水加热,剩余的没有凝结的气体被排往大气。
2、轴封冷却器的运行。
轴封冷却器的投入与停止应与主机轴封供汽同步进行,即投入主机轴封供汽时就应立即投入轴封冷却器,停止轴封供汽时亦应停止轴封冷却器工作。
轴封冷却器运行时,必须有足够的冷却水通过,即保证凝结水泵的良好运行,主要室在机组启动低负荷前,对凝结水流量进行调整。
水侧投入后,投入轴抽风机。
正常运行时监视轴封冷却器的负压和水位,保证其在规定范围内运行,达到最佳效果。
3、什么是回热加热器?
答;是指从汽轮机某些中间级抽出部分做过功的蒸汽,用来加热锅炉给水或凝结水的设备。
4、采用回热加热器为什么能提高机组循环热效率?
答;回热加热系统:
汽轮机设备中,采用抽汽加热给水的回热系统的目的是减少冷源损失,以提高机组的热经济性。
因为这样能使利用汽轮机中做工部分的蒸汽,从一些中间级抽出来导入回热加热,加热炉给水和主凝结水,不再进入凝汽器。
这部分的抽汽的热焓就被充分利用了,而不被冷却带走。
采用回热加热器后,汽轮机总的汽耗量增大,而汽轮机的热耗率和煤耗率是下降的。
汽耗率增大是因为进入汽轮机的每千克新蒸汽所做的功减少了,而汽耗率和煤耗率的下降是由于冷源损失减少使给水温度提高之故,所以采用回热加热系统后,热经济性便提高了。
另外采用回热加热系统,由于提高了给水温度,可以减少锅炉受热面因传热温差过大而产生的热应力,从而提高了设备的可靠性。
5、冷油器作用?
答;作用:
汽轮机发电机组正常运行,由于轴承摩擦而消耗了一部分功,它将转化为热量使轴承的润滑油温度升高,如果油温太高轴承有可能发生软化、变形或烧损事故。
为使轴承正常运行,润滑油温必须保持一定范围内,一般要求进入轴承油温在35-45℃,轴承的排油温升一般为10~15℃,因而必须将轴承排出来的油冷却以后才能再循环进入轴承润滑。
冷油器就是冷却主机润滑油的。
温度较高的润滑油和低温的冷却水在冷油器中进行热交换,通过调节冷却水流量来达到控制润滑油温度的目的(同时由于转子温度较高,尤为高压缸进汽侧,其轴颈也向外进行热量传递,所以润滑油也具有冷却轴颈的作用。
6、冷油器工作过程。
工作过程;
润滑油从壳体下部进入,经中间带孔的大隔板和不带孔的小隔板交替流向中心或四周,油在管外呈曲折运动,最后由壳体的上部油出口流出。
冷却水由水室进入,经四个流程仍由下水室排出。
冷油器充油时,出入口油门及放空气门开启,用低压油泵出口门限制油压进行充油,注意充油速度不可过快,油侧空气排净关闭,充油结束。
充油时,注意防止油侧超压,设备损坏。
冷油器充满油后方可通冷却水。
出口水门保持全开,用入口冷却水进行油温调整。
三台冷油器采用并联运行,一台备用。
机组运行中进行冷油器的切换操作时,应遵守先投入后切除的原则。
操作时要由有经验的人员进行,同时还应有专人进行监护。
监视润滑油温、油压及轴瓦温度,防止发生误操作,造成机组跳闸、设备损坏事故。
操作要缓慢进行,投入冷油器时缓慢开启入口油门,防止油压波动,同时排净空气。
停止时关闭出口油门,关闭冷却水入口门。
7、冷油器的维护。
1;注意冷油器出口温度,及时调整,保持其在38~42℃之间,坚持少调整看原则,门开多少,相应油温变化多大,要心中有数,不能出现调整冷却水后长时间不检查,造成油温大幅度变化现象。
同时要根据经验来确证油温,防止表计故障时发生误判断、误操作现象。
2;注意油压情况(入、出口油压),能准确判断内漏。
3;注意任何情况下必须油压大于水压,防止冷却水泄漏到油中。
4;加强检查,找差漏点加以消除,防止发生火灾事故。
8、低压加热器的起动和停机
答;加热器启动前的准备工作以及启动运行都应按电厂运行规程进行。
启动顺序;
(1) 检查有关阀门,主要装置仪表等,应工作正常并处于正确位置。
(2) 排净管内空气。
(3) 缓慢开启进汽阀,按限定值控制给水温升速度,然后投入疏水调节装置。
(4) 检查壳侧抽空气系统,应工作正常。
低加的投入与停止原则;
投入:
低加启动是在汽轮机带一定负荷后投入运行的,即在机组启动并网后根据汽缸金属温度情况带相应负荷后投入低压加热器的,按压力由低向高即按其工作温度由低向高的顺序投入。
一般情况下,在机组带初始负荷(5~10%额定负荷)暖机时投入。
投入时先投水侧,将水侧出口门全开,旁路门关闭,注意充分排出空气。
抽汽管道逆止门前后疏水处于开启状态,低加疏水、空气逐级导通,缓慢开启低加进汽阀,向低加送汽。
低加疏水量达到一定量时,约15MW负荷,启动疏水泵,并调整水位,同时检查疏水调整门、水位信号、逆止门等工作情况,加热器投入后,根据机组情况关小或关闭疏水。
停止时与启动相反:
适当减负荷后按其压力由高向低先后顺序停止运行,注意其冷却情况,开启响应放空气阀。
9、汽温过高过低对机组有什么影响?
答;制造厂设计汽轮机时,汽缸、隔板、转子等部件根据蒸汽参数的高低选用钢材,对于某一种钢材有它一定的最高允许工作温度,在这个温度以下,它有一定的机械性能,如果运行温度高于设计值很多时,势必造成金属机械性能的恶化,强度降低,脆性增加,导致汽缸蠕胀变形、叶轮在轴上的套装松弛,汽轮机运行中发生振动或动静摩擦,严重使设备损坏,故汽轮机在运行中不允许超温运行。
当新蒸汽压力及其他参数不变时,新蒸汽温度降低,循环热效率下降,如果保持负荷不变,则蒸汽流量增加,且增大了汽轮机的湿汽损失,降低了机内效率。
新蒸汽温度降低还会使除末级以外的各级焓降都减少,反动度都要增加,转子的轴向力增加,对汽轮机安全不利。
新蒸汽温度急剧下降,可能引起汽轮机水冲击,对汽轮机安全运行更是严重的威胁。
10、新蒸汽压力升高时,对机组运行有何影响?
答;主蒸汽压力升高后,总的有用焓降增加了,蒸汽的做功能力增加了,因此如果保持原来的负荷不变,蒸汽流量可以减少,对机组经济运行是有利的。
但最后几级的蒸汽湿度将增加,特别是对末级叶片的工作不利。
对于调节级,最危险工况是在第一调节气门全开时,此时初压升高,调节级的焓降及流量均增加,对调节级是不利的,但在额定负荷下工作时,调节级焓降不是在最大,一般危险性不大。
主蒸汽压力升高而没有超限,机组在额定负荷下运行,只要末级排汽湿度没有超过允许范围,调节级可以认为是没有危险,但主蒸汽压力不是可以随意升高的。
主蒸汽压力过高,调节级焓降过大,时间长了会损坏喷嘴和叶片,另外主蒸汽压力升高超限,最末几级叶片处的蒸汽湿度大大增加,叶片遭受冲蚀。
新蒸汽压力升高过多,还会导致导汽管、汽室、汽门等承压部件应力的增加,给机组的安全运行带来一定的威胁。
11、新整齐压力降低时,对汽轮机运行有何影响?
假如新蒸汽温度及其他运行条件不变,新蒸汽压力下降,则负荷下降。
如果维持负荷不变,则蒸汽流量增加。
新汽压力降低时,调节级焓降减少,反动度增加,而末级的焓降增加,反动度降低,对机组的总的轴向推力没有对大的变化,或者变化不明显,新蒸汽压力降低,机组汽耗增加,经济性降低,当新蒸汽压力降低较多时,要保持额定负荷,使流量超过末级通流能力,使叶片英里及轴向推力增大,故应限制负荷。
12、排汽压力的高低对机组有什么影响?
(真空高低)
答;排汽压力的变化对汽轮机的经济性、安全性能影响很大,真空的提高,可以使汽轮机汽耗减少而获得较多的经济性、凝汽器真空越高,即排汽压力越低,蒸汽中的热能转变为机械能就愈多,被循环水带走的热量愈少,凝汽器压力每降低1Kpa,会使汽轮机负荷大约增加额定负荷的2%。
真空也不是越高越好,真空越高,循环水泵消耗的能量越多。
真空越高末级湿度越大,轴向推力增加。
如果凝汽器真空恶化,排汽压力升高,蒸汽中的热能被循环水带走的热量就越多,热能损失越多,则同样的蒸汽流量,同样的初参数,负荷就不能带到额定值。
如保持额定负荷蒸汽流量增加,叶片将要过负荷,轴向推力增加,因此机组在运行中应尽量维持经济真空,以获得较好的经济性。
13、为什么机组启动时候先送轴封后抽空?
答;热态启动时,转子和汽缸金属温度较高,如果先抽真空,冷空气将沿轴封进入汽缸,而冷空气是流向下缸的,因此下缸温度急剧下降,使上下缸温差增大,汽缸变形,动静产生摩擦,严重时使盘车不能正常投入,造成大轴弯曲,所以热态启动时应先送轴封后抽真空。
14、为什么转子静止时严禁向轴封