技术交流材料催化剂表面成膜钝化处理技术1.docx
《技术交流材料催化剂表面成膜钝化处理技术1.docx》由会员分享,可在线阅读,更多相关《技术交流材料催化剂表面成膜钝化处理技术1.docx(11页珍藏版)》请在冰豆网上搜索。
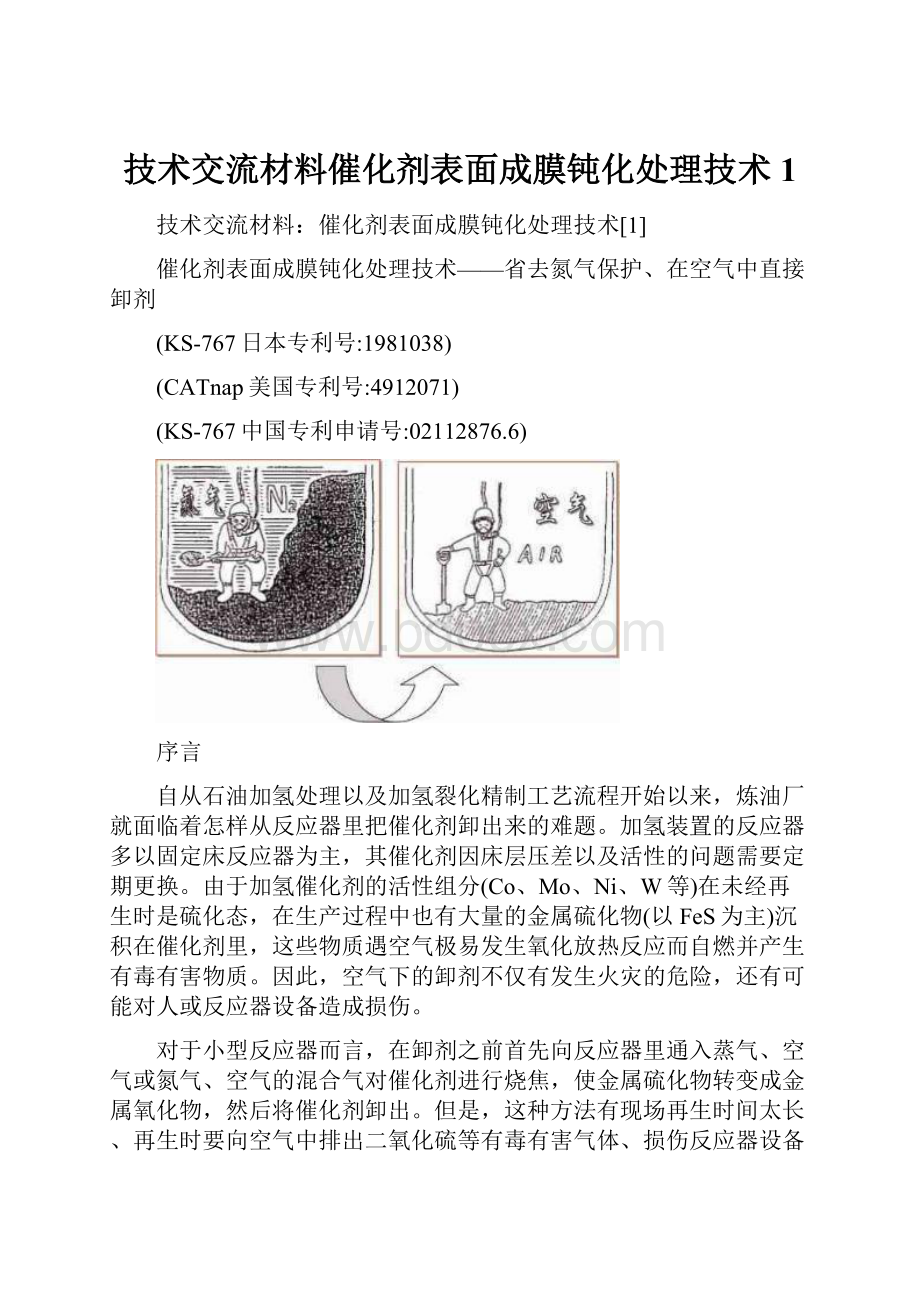
技术交流材料催化剂表面成膜钝化处理技术1
技术交流材料:
催化剂表面成膜钝化处理技术[1]
催化剂表面成膜钝化处理技术——省去氮气保护、在空气中直接卸剂
(KS-767日本专利号:
1981038)
(CATnap美国专利号:
4912071)
(KS-767中国专利申请号:
02112876.6)
序言
自从石油加氢处理以及加氢裂化精制工艺流程开始以来,炼油厂就面临着怎样从反应器里把催化剂卸出来的难题。
加氢装置的反应器多以固定床反应器为主,其催化剂因床层压差以及活性的问题需要定期更换。
由于加氢催化剂的活性组分(Co、Mo、Ni、W等)在未经再生时是硫化态,在生产过程中也有大量的金属硫化物(以FeS为主)沉积在催化剂里,这些物质遇空气极易发生氧化放热反应而自燃并产生有毒有害物质。
因此,空气下的卸剂不仅有发生火灾的危险,还有可能对人或反应器设备造成损伤。
对于小型反应器而言,在卸剂之前首先向反应器里通入蒸气、空气或氮气、空气的混合气对催化剂进行烧焦,使金属硫化物转变成金属氧化物,然后将催化剂卸出。
但是,这种方法有现场再生时间太长、再生时要向空气中排出二氧化硫等有毒有害气体、损伤反应器设备等缺点,随着二十世纪七十年代世界各国防止大气污染相关法规的实施,器内再生的卸剂方法就被淘汰。
对于大型反应器而言,卸剂操作是在氮气保护下进行。
在卸剂过程中向反应器内连续充入氮气,阻止空气进入反应器内防止催化剂自燃,卸剂人员配备救生设备进器卸剂。
卸出的催化剂要加干冰密闭保存或用水浸泡以防止其自燃,然后送去再生、金属回收或者废弃。
这种方法施工人员工作环境比较恶劣、危及生命安全、污染环境。
氮气保护下的卸剂是很危险
的,发生过多起重大的事故,而且危险程度随着催化剂装填床层的增多以及反应器塔盘构造的复杂而增高。
二十世纪八十年代初期,日本索夫塔特工业株式会社和鹿岛工程株式会社经过多年的研究,发明了无需氮气保护直接在空气环境中卸剂的技术,即KS-767催化剂表面成膜钝化处理技术。
应用这种技术卸剂的方法是在加氢装置停工过程中,向循环的反应系统内加入少量的成膜剂,在催化剂的表面形成一层特殊的膜,这层膜能阻止空气与催化剂的接触,杜绝了含硫加氢催化剂的自燃,使卸剂工作能直接在空气中进行。
膜保护后的催化剂在卸出后具有足够的稳定性,在运输、储存时不需要特殊的措施,而且容易再生。
KS-767催化剂表面成膜钝化处理技术1984年首先在日本的炼油厂应用。
1992年推广到美国,其后新加坡、南韩、中东、中国台湾等国家和地区的炼油厂也开始使用。
2001年江苏天鹏石化特种工程有限公司将此技术引进并在中国大陆推广,先后在中国石油化工股份有限公司茂名分公司渣油加氢装置、大连西太平洋石油化工有限公司重油加氢装置、中国石油化工股份有限公司齐鲁分公司胜利炼油厂重油加氢装置应用。
至2003年底,此技术已在世界各地的炼油厂成功应用202次,从716个反应器里卸出133498立方米的催化剂(详细应用装置请看表1),其中有一部分催化剂再生使用(见表2)。
二、KS-767催化剂表面成膜钝化处理技术的实施
KS-767催化剂表面成膜钝化处理技术典型的操作步骤列于表3。
详细的操作步骤将根据各炼油厂的工艺流程、装置构造、停工要求以及催化剂的种类等而定。
首先,将进料量减少到设计流量的60,80,左右。
为防止降温过程中催化剂床层压降上升过快,减少进料量是必须的。
但是,为了使催化剂床层里有较好的成膜剂分布,要保证反应器有一定的流速。
在降量的同时将反应器温度降到加氢精制反应温度以下。
当流量以及温度降到预定值后,向反应系统里引入循环油置换原料油。
循环油可以是柴油(轻柴油、重柴油、减压柴油的一种或其混合物),对这种油在粘度、沸点范围、燃点以及其他标准方面有一定的要求。
循环油引入后,利用装置开工线进行整个系统的油循环。
通常,循环油是从汽提塔或蒸馏塔的底部产品线经开工线循环回到原料罐。
当油循环建立后,在系统内低压处(比如原料泵的入口),将成膜剂注入到循环油中。
成膜剂的用量约为循环系统内存油体积的0.5,2%。
然后,油在系统内至少循环2周,对催化剂进行表面成膜钝化处理。
当循环结束系统温度也降到
o140C以下时,停止油循环。
继续气体循环,将催化剂、管道内以及装置里的油置换出去。
同
o时,把反应器的温度降到人可以进器卸剂的温度40,50C以下。
然后,泄压、对系统进行氮气置换、分析系统内气体烃最低爆炸下限(LEL)、CO、HS、SO以及Ni(CO),直至满足各炼油224厂的安全标准。
为防止系统漏窜有毒有害物质,在卸剂前应将各反应器各开口管线加盲板密封,然后通过重力自卸或用真空吸取的方式来卸剂。
如果从反应器下部卸料口利用重力来卸剂时,操作
-2-
很简单。
因为催化剂经过表面成膜钝化处理后,不会燃烧,可以直接在空气下从卸料口放出,送去再生或回收废弃。
如果是通过真空吸取的话,从反应器上部的人孔将催化剂吸取出来。
进器前,首先对反应器内作业区域进行空气置换,保证器内氧气含量在20%以上。
可是,因催化剂里有油气,进器卸剂人员须戴面罩。
但与氮气保护操作时不同的是,万一面罩脱落,操作人员不会有生命的危险。
经KS-767表面成膜钝化处理后的催化剂无粉尘,能提高真空吸取卸剂效率,解决了过去真空吸取卸剂时催化剂摩耗以及相撞的缺点,清除速度可达14,183m/Hr,这是普通真空抽吸速度的2,3倍。
三、装置检修应用KS-767技术的优点
KS,767催化剂表面成膜钝化处理技术的优点列于表4中。
1、卸剂施工安全得到保障
-767催化剂表面成膜钝化处理技术最大的优点是保障了设备和人身的安全。
首先,排KS
除了有生命危险的氮气保护工作环境,反应器里的空气至少含有19.5%氧气。
其次,抑制了催化剂的氧化发热,防止了催化剂的自燃,减少了卸剂时的事故发生。
废催化剂可以像其他废弃物一样作为非危险物处理,可以减少在包装、运输、贮藏时的费用。
第三,催化剂粉尘问题也很重要,因为此粉尘里含有致癌成分(NiS),会引起健康问题。
经热氢气提过的催化剂32
粉尘很多,卸剂时反应器内外处处粉尘飞扬,污染环境。
经KS-767处理过的催化剂无粉尘,对环境无污染,保障人身健康。
经KS-767表面成膜钝化处理过以及未加处理催化剂的自燃试验结果显示在图1里。
在空气流动下对催化剂进行加热,随着温度上升,测定催化剂的温升。
当化学反应发生时,温升会显著变大。
未加处理的试样取自普通计划检修停工工序(有热氢冲洗)反应器里的Co/Mo催化剂。
对
o此催化剂(实线)加热时,当温度上升到120C时,第1个放热反应被观测到,这是金属硫化物变
o成金属氧化物的氧化放热反应,继续升温到300C时,第2个放热反应被观测到,这是催化剂上
o堆积碳的燃烧反应。
经过KS-767表面成膜钝化处理过的催化剂(虚线)在加热到320C之前,没有放热反应被观测到,在这之后,催化剂上的可燃物开始燃烧,催化剂迅速升温。
2、装置检修总工期缩短
KS-767催化剂表面成膜钝化处理技术在许多方面具有节省检修工期的优点。
很显然,该技术的实施省去了热氢气提、恒温消氢、中和清洗等工序,可节省24小时或更长的停工时间,这就意味着炼油厂能提前开工一天以上。
另外,在催化剂冷却过程中采用了油冷却,热传导也有改善,反应器的冷却时间相应缩短。
施工人员可以在器内长时间作业,施工速度大大加快,相应缩短检修工期。
3、装置检修总费用降低
在氮气保护下卸除催化剂,必须保证反应器内氮气微正压,真空抽吸机械及气动破碎机械也要消耗大量的氮气,仅此一项就要花费数十万元人民币的开支。
采用KS-767催化剂表面成膜钝化处理技术后,可以在空气中直接卸剂,对于结块催化剂的气动破碎机械也使用空气
-3-
作为动力,节省大量氮气。
热氢气高温气提、恒温消氢的工序被省略,相应的装置运行费用(燃料费、氢气损失费以及人工费等等)被节约;中和清洗工序被省略,相应的中和材料及其运行费用被节约。
KS-767处理后的废催化剂可以作为非危险物处理,采用普通编织袋包装。
这样可以省出催化剂铁桶费、干冰费用、运送费、贮藏费以及其他相应的费用,相应的环境保护费用也大幅降低。
经过KS-767处理后的催化剂可以使用高真空系统进行抽吸,催化剂的磨损以及破碎相应减少。
催化剂回收率提高,购买新催化剂的费用相应减少。
很显然,如果催化剂卸装工序是炼油装置计划检修关健步骤的话,那么卸剂工期的缩短,使得整个检修工期缩短,相应的检维修费用减少,炼油装置可以提前投入生产,对炼油厂会产生巨大的经济效益。
另外,KS-767催化剂表面成膜钝化处理技术尚有许多有实际价值的优点。
例如,催化剂的后续再生利用对炼油厂的经济性有很大的影响。
KS-767处理过的催化剂再生后能得到与氮气保护下卸剂同样的活性。
四、使用CATnap催化剂表面成膜钝化处理技术可以防止PSCC
加氢处理、加氢裂化反应器一般由低Cr-Mo合金钢制成,这种钢材能满足高温高压的强度要求。
但是,在实际生产条件下,低合金钢易被腐蚀。
为了解决此问题,在反应器的内壁堆焊奥氏体不锈钢(TP309、TP347)作为衬里,器内部件也采用奥氏体不锈钢(321或347型)制作。
对于奥氏体不锈钢,人们担心在卸剂时会生成连多硫酸(HSO,x通常为3,4,5),导致奥2x6
氏体不锈钢的连多硫酸应力腐蚀龟裂(PSCC)。
PSCC必须在存在张力及应力、不锈钢已变成敏感性钢、存在连多硫酸等三个条件同时存在的条件下方可发生。
只要其中有一条件不成立时,就不会发生PSCC。
连多硫酸又是在水、氧气、硫化物等三个成分同时存在时才会生成。
只要排除其中一个成分,连多硫酸就不会生成。
2,,xS+3O+2HO?
HSO+2OH(x=3,4,5)222x6
防止PSCC就是要控制或消除PSCC形成的三个条件之一或连多硫酸生成的三个成分之一。
PSCC的发生源以及防止对策总结于表4中。
设备在制造时就存在着应力,在加氢处理或加氢裂化的操作过程中要承受应力,总之应力是存在的。
判断不锈钢是否具有敏感性,在日本是采用不锈钢敏感性测定仪DOS(Degreeof
oSensitization)测试不锈钢的敏感度(Cr的量)。
经验表明,反应器温度不到430C以上,采用304L低碳钢以及321、347安定型钢基本上不会发生敏感性问题。
当确认不锈钢是不敏感时,就不要考虑PSCC。
防止连多硫酸生成的最简单的方法是反应器内的空气湿度控制(防止水生成)。
也就是说,
-4-
保证塔内空气温度在露点温度以上。
实际上,器内催化剂温度比周围空气温度要高出10度以上,塔内水生成的几率很小。
在下雨天卸剂时,为防止水的生成,可以向塔内通入干燥空气。
从除去硫化物的角度,对不锈钢进行苏打液中和处理也是防止连多硫酸生成的一种有效手段。
-767催化剂表面成膜钝化处理技术后,不仅催化剂的表面能形成一层特殊的膜,采用KS
同时反应器衬里表面、塔内件的表面以及管道内表面都能形成一层膜。
这层膜能阻止空气、水与不锈钢的接触,能防止连多硫酸的生成,从而达到防止奥氏体不锈钢连多硫酸应力腐蚀开裂的目的。
表5列举了1984,2003年间应用催化剂表面成膜钝化处理技术时,世界各地炼油厂在空气下卸剂时的PSCC预防措施。
-767催化剂表面成膜钝化处理技术已在加氢处理、加氢裂化工艺等的反应设备中使用KS
202次,从716个反应器里卸出133498立方米的催化剂。
其中,有许多反应器是多次重复使用,至今没有任何PSCC事故发生的报告。
催化剂表面成膜钝化处理技术对不锈钢的保护作用渐渐被炼油厂所认识。
从表中可以看出,苏打液中和处理(浸泡以及喷洒)的方法已基本上不采用了,越来越多的厂家采用湿度控制或不采取措施。
五、总结与结论
1、KS-767催化剂表面成膜钝化处理技术是在催化剂表面形成一层特殊的膜,阻止催化剂与空气的接触、控制催化剂的氧化放热反应,使卸剂工作直接在空气下进行的一种卸剂技术。
它排除了氮气保护下非常危险的操作以及尘土飞扬的工作环境。
同时,塔内壁以及内件表面上也形成一层特殊的膜,此层膜能阻止空气、水与不锈钢的接触,能防止连多硫酸的生成,避免反应器内壁衬里奥氏体不锈钢发生连多硫酸应力腐蚀开裂事故。
2、KS-767催化剂表面成膜钝化处理技术具有抑制含硫催化剂的自燃性、无需氮气保护在空气下直接卸剂、卸剂工期缩短、节省卸剂费用、改善催化剂再生回收率、降低催化剂的危险性、节省包装及运输费用、能防止连多硫酸的生成等主要优点。
3、KS-767催化剂表面成膜钝化处理技术是加氢领域催化剂卸剂、装置检维修领域里的一种新技术,将会给石油化工企业带来巨大的经济效益。
表1KS-767在世界各地的卸剂实绩(1984,2003)
装置反应器备注3装置名称催化剂(m)数数
3常压渣油脱硫装其中中国1套8台反应器1100m催化剂8240481730置
-5-
3减压渣油脱硫装其中中国3套28台反应器3692m催化4621941342置剂
加氢裂化装置24425930
蜡油加氢装置16171050
润滑油精制装置16172470
轻柴油脱硫装置89430
汽油脱硫装置1183
其他装置97463
合计202716133498
表2KS-767实施后催化剂再使用情况总结
处理能力反应器数催化剂体催化剂备注国装置名称实施年(万吨/量积使用情家3年)(只)(m)况
蜡油加氢脱括号内19841101150硫的
数字为1986904450日渣油加氢脱
未本硫1990;199126081700部分卸
卸反应剂1991/1993/1995/加氢裂化1102500器1997/1999/2001
数量。
韩加氢裂化19951402390国
加氢裂化1992,19951604200
1992901140美全部再
蜡油加氢脱国生19921801220硫
19931802170
1996/1997160
(2),41130日渣油加氢脱部分再本硫生1992260(8)2380
-6-
1993/1996/1998/260
(2),817001999/2000/2001
1997260102080
表3KS-767催化剂表面成膜钝化处理技术的一般操作程序序号内容
1减少原料流量到设计流量的约60,80%。
o2将反应器的床层平均温度降到化学反应温度(320C)以下。
3引入循环油置换原料油。
4建立反应系统循环油的大循环
5在系统内低压处(原料泵入口等)注入成膜剂,用量约为系统内存油量的0.5,2%。
o6反应系统最少循环2周,同时将反应器降温到140C以下。
7根据操作规程或建议降低压力。
8停止油循环。
o9在气体循环下赶油,同时将反应器降温到40C以下。
10泄压,氮气置换,分析LEL、CO、HS、SO等,直至满足要求。
22
11将反应器各管线盲封,预防管道窜气。
12打开反应器头盖,取出积垢篮筐以及分配器塔盘后,对器内进行空气置换。
13卸剂开始(真空抽吸卸剂或重力自卸)
表4KS-767催化剂表面成膜钝化处理技术的优点优点内容
对设备、催化剂、人身无任何影响
消除了有生命危险的卸剂工作环境安
全处理后的催化剂在空气状况下不会氧化发热、自燃
性处理后的催化剂从危险物变为非危险物,降低了再生、运送及贮藏时的危险性
提供了无粉尘(带有致癌成分)工作环境,保护环境
省去了热氢气高温气提工序、恒温消氢工序、中和清洗工序省
时采用了液体冷却,提高了冷却速度
间在空气状况下施工速度加快
不须氮气保护、省去真空吸取及气动破碎机械用氮气,氮气费用降低经省去热氢高温气提、恒温消氢工序,装置运行费用降低费省去了中和清洗工序,材料及运行费用降低削
可作为非危险物处理,运送、包装、存放以及贮藏的费用降低减
因磨擦和破损减少,催化剂损失减少。
如果旧剂再生利用,则购买新剂的费用降低
-7-
经过成膜的催化剂能够完全再生利用,购买新剂的费用降低
检修总工期缩短,相应的人工、设备租借等等费用降低
环境保护费用降低
表5连多硫酸应力腐蚀龟裂(PSCC)的发生源及防止对策
必要因素来源对策
1张力张力,应力没有对策连多
操作温度低于430?
硫酸敏感含Cr低于2非敏感时不要对策使用低碳钢304L型应力性13,腐蚀使用化学稳定钢321、347型
龟裂a硫化物中和处理(苏打浸泡或苏打喷洒)
连多(PSCC)3b水湿度控制(KS-767处理时形成的膜将水阻止)硫酸
c氧气惰性气体吹扫(KS-767处理时形成的膜将氧气阻止)
表6采用KS-767时的连多硫酸应力腐蚀龟裂的防止对策
连多硫酸应力腐蚀龟裂的防止对策年度苏打浸泡苏打喷洒湿度控制不采取对策198410001985100019862000198712001988201019891220199020301991148219922711119930511319940811519950784199604541997037719980041119990027
-8-
200000352001003820020039200300510合计13428776
图1KS-767的自燃试验
(试验用催化剂为失活的钴,钼催化剂)
-9-
-10-