综采放顶煤工作面超前预裂爆破方案.docx
《综采放顶煤工作面超前预裂爆破方案.docx》由会员分享,可在线阅读,更多相关《综采放顶煤工作面超前预裂爆破方案.docx(33页珍藏版)》请在冰豆网上搜索。
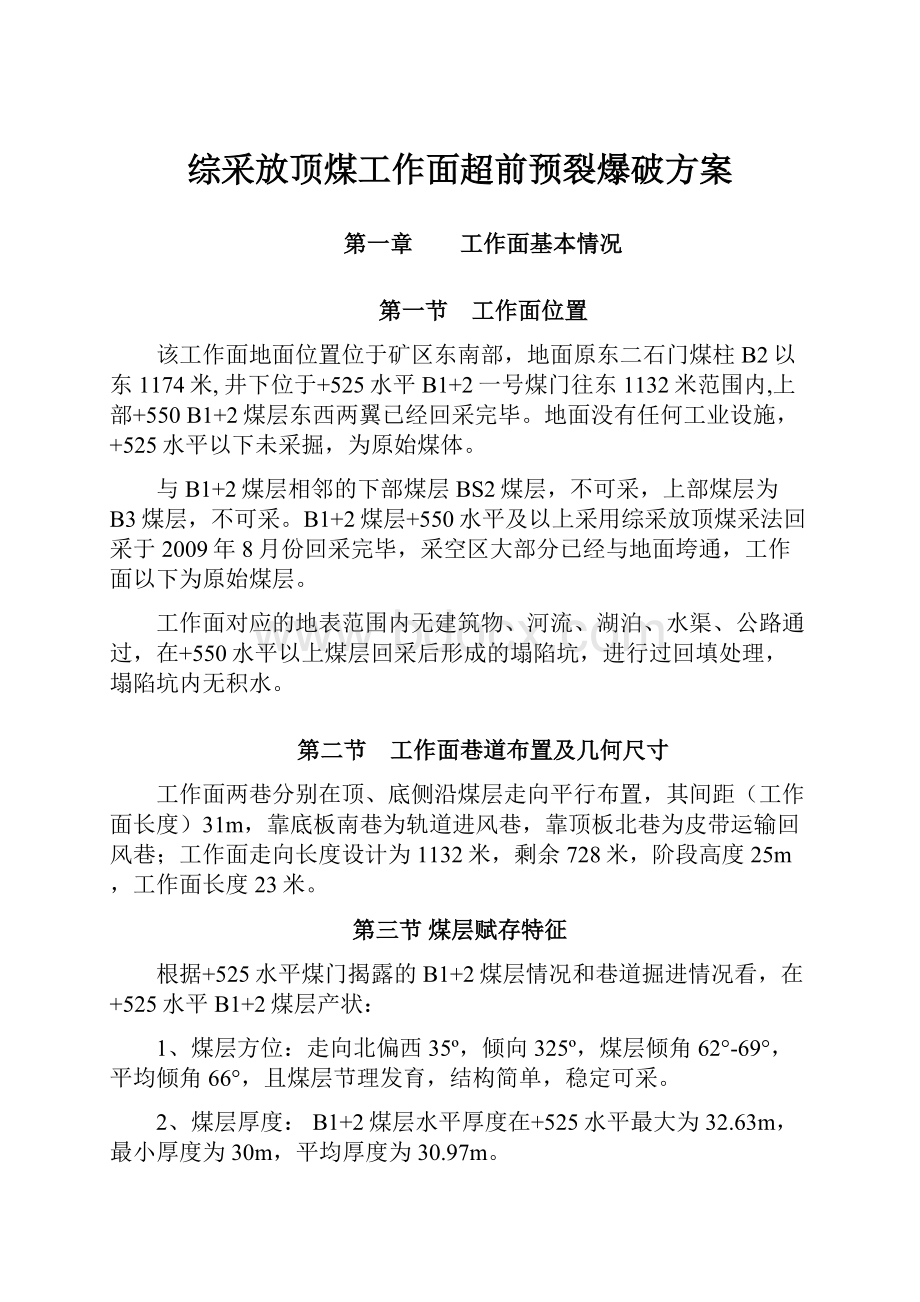
综采放顶煤工作面超前预裂爆破方案
第一章 工作面基本情况
第一节 工作面位置
该工作面地面位置位于矿区东南部,地面原东二石门煤柱B2以东1174米,井下位于+525水平B1+2一号煤门往东1132米范围内,上部+550B1+2煤层东西两翼已经回采完毕。
地面没有任何工业设施,+525水平以下未采掘,为原始煤体。
与B1+2煤层相邻的下部煤层BS2煤层,不可采,上部煤层为B3煤层,不可采。
B1+2煤层+550水平及以上采用综采放顶煤采法回采于2009年8月份回采完毕,采空区大部分已经与地面垮通,工作面以下为原始煤层。
工作面对应的地表范围内无建筑物、河流、湖泊、水渠、公路通过,在+550水平以上煤层回采后形成的塌陷坑,进行过回填处理,塌陷坑内无积水。
第二节 工作面巷道布置及几何尺寸
工作面两巷分别在顶、底侧沿煤层走向平行布置,其间距(工作面长度)31m,靠底板南巷为轨道进风巷,靠顶板北巷为皮带运输回风巷;工作面走向长度设计为1132米,剩余728米,阶段高度25m,工作面长度23米。
第三节煤层赋存特征
根据+525水平煤门揭露的B1+2煤层情况和巷道掘进情况看,在+525水平B1+2煤层产状:
1、煤层方位:
走向北偏西35º,倾向325º,煤层倾角62°-69°,平均倾角66°,且煤层节理发育,结构简单,稳定可采。
2、煤层厚度:
B1+2煤层水平厚度在+525水平最大为32.63m,最小厚度为30m,平均厚度为30.97m。
3、煤层结构:
该煤层内含夹矸3层,夹矸层单层厚度为0.18-0.53m,夹矸总厚度0.93米,该矸石硬度较小对机械化开采无影响.该煤层属巨厚煤层,煤层层理、节理发育,结构复杂,其空间形态比较稳定。
B1+2煤层之间夹矸较稳定,以灰色沙质泥岩为主,较软。
煤岩类型为半光亮型。
煤层厚度变化不大,煤层厚度自西向东稍有变厚。
煤层夹矸3层。
煤层较松散,南面较硬,北面较松散,易冒落。
煤质情况表
煤
质
情
况
Mt
Ad
Vdaf
Qnet.ay
FC
St.d
Y
工业牌号
1.89
13.87
39.84
6616
83.6
1.04
0—14
弱粘结
良好的工业用煤。
4、煤层顶底板情况
顶底夹矸较稳定,煤岩类型为半暗淡型,煤层顶、底板为灰色泥岩,松散。
煤
层
顶
底
板
情
况
顶板名称
岩石名称
厚度(m)
岩石特征
老顶
泥岩、砂质泥岩
22.55
浅质状,夹煤屑、节理发育
直接顶
泥岩
3.62
灰色、层理节理发育,含煤屑松散
伪顶
直接底
泥岩、砂质泥岩
3.98
灰色、层理节理发育,含煤屑
老底
砂质泥岩
10.00
灰色、节理发育,层理明显
第四节地质构造
为一单斜构造,井田地质条件相对较简单.根据勘探资料和我矿的开采情况,在本工作面内无断裂和褶曲构造,无岩浆侵入体、无岩溶陷落柱破坏,属于赋存稳定、构造简单型煤层。
第五节水文地质
1、煤层含水情况
该煤层为弱含水煤层,水文地质条件简单,补充水源主要来自地面雨雪洪水及灌浆水,+550水平B1+2煤层已开采,故上部采空区可能存在积水,+525B1+2煤层顶底板节理裂隙发育,煤体松散,所以局部煤层裂隙含水,在回采过程中工作面可能出现淋水,从上分层掘进及开采情况看,上部采空区无积水,水对工作面威胁不大,
2、地表河流
该工作面对应地表无河流,地表西部为水磨沟河,距工作面2077m,东部八道湾河距工作面2057m,对工作面的回采无影响。
3、地面雨雪水
该工作面对应地表为塌陷坑,已进行过回填处理,塌陷坑内无积水,少量地面雨雪水流入地表塌陷坑,但经过这几年的观测未发现地表塌陷坑大量积水的现象。
4、涌水情况
该工作面的涌水水源主要是地表大气降水,大气降水直接渗入井下或经老塘渗入井下,这部分水也是矿井涌水量的主要构成部分,其次为灌浆防尘水,从掘进巷道河工作面开采情况看,工作面无淋水滴水现象,无影响
5、其他水源的分析
工作面其他水源为工作面喷雾用水、工作面冷却用水以及乳化液泵站用水。
第六节瓦斯、煤尘、煤层自然发火情况
1、瓦斯情况:
属于低瓦斯煤层,含H2S气体。
绝对瓦斯涌出量为0.15m3/min,瓦斯相对涌出量为0.19m3/t。
二氧化碳绝对涌出量为0.81m3/min,二氧化碳相对涌出量为0.99m3/t。
2、煤尘情况:
煤尘挥发份较高,具有爆炸危险性,爆炸指数为47.7%,煤尘爆炸性试验结果见下表。
煤尘爆炸性试验结果表
煤层编号
采样编号
工业分析(%)
爆炸性试验
爆炸性
结论
备注
Mad
Aad
Vad
Vdaf
火焰长度(mm)
B1+2
200904028
9.87
23.40
38.77
58.10
≥100
有爆炸性
该工作面粉尘中游离二氧化硅的含量不详。
粉尘的职业危害有:
煤尘爆炸、矽(煤)肺病。
3、煤层自燃发火情况:
该煤层属变质程度较低,挥发份较高的弱粘结煤,燃点较低,加之煤层裂隙较发育,与空气接触面积较大,极易氧化。
属于容易自燃煤层,自然发火期一般为3~6个月,最短的发火期为45天。
工作面地温15—17℃,煤层的自然发火倾向性为Ⅱ级。
煤层自燃倾向性试验结果表
煤样编号
煤层编号
采样时间
采样地点
煤的吸氧量,cm/g.干煤
自燃倾向性分类
200904028
B1+2
09.04.17
工作面
0.68
自燃
第七节工作面设备配备
工作面主要设备:
MGD-250/300NWD采煤机一台,11付ZF5000/17/28型放顶煤液压支架支护工作面顶板;北端头采用两付ZFG5600/19/35型支撑式液压支架,SGZ-730/110前部刮板输送机一台,SGZ-730/110后部刮板输送机一台,SZZ-730/110桥式转载机一台,选用DSJ-100/75型胶带输送机一台,SJ-80N/75胶带式输送机一台,PLM-500型破碎机一台,KSGZY-800/6移动变电站一台。
WRB-200/31.5型乳化泵,KHYD75岩石钻,DZ-3.15单体液压支柱。
第八节现工作面采煤方法及生产系统简介
采用经十多年实践成功有效的正规的综采放顶煤采煤方法。
工作面两顺槽沿煤层顶底板布置,底板巷道(B1)安装轨道(兼进风巷),安有移动变电站串车等电气设备,顶板巷道(B2)安装刮板机(兼回风巷),两巷采用锚网、锚索联合支护。
工作面支护为液压支架支护,两端头采用箱型对梁迈步式支护;两巷超前支护采用一字铰接梁配单体支护。
通风方式为分区独立负压通风该工作面采用负压通风系统,新鲜风流经地面→副斜井→+550运输大巷→+550石门→轨道暗斜井→+525东B1巷→冲洗工作面,乏风经+525东B2回风巷→+525东B2通风天井→+558东B2巷→+558石门→+550—+610回风上山→+610回风石门→+610至+670回风上山→+670石门→+670底板大巷→+670回风井→地面。
运输采用机械运输,即工作面→+525东B2运输巷→+525-+500B2煤仓→+500石门→+500B5煤仓→皮带暗斜井→+558煤仓→+550底板运输巷→+550集中煤仓→皮带斜井→地面。
采煤工艺主要是进刀→打顶煤爆破孔、装药→前移液压支架→顶煤爆破→放顶煤。
综放工作面顶煤爆破主要采用架前直接用岩石电钻打孔,人工装药,架顶松动爆破落煤方式。
工作面分段高度25m,机采高度2.8m,放顶煤高度22.2m。
第二章顶煤预裂爆破实施方案
根据新《煤矿安全规程》第六十八条第三款严禁在工作面内采用炸药爆破方法处理顶煤、顶板、及卡在放煤口的大块煤的规定,按照公司的要求,停止架间放炮爆破工艺,实施工作面顺槽超前预裂爆破。
根据我矿实际情况,结合碱沟煤矿实施的经验编制顺槽超前预裂爆破方案。
详见+550水平东翼B6综采工作面超前预裂爆破设计图。
第一节工作面超前预裂爆破工艺
一、超前预裂爆破方式:
距现工作面煤壁15—30米的超前顺槽(南巷)垂直于煤层走向由南向北布置φ100mm扇形爆破孔进行顶煤超前工作面正向爆破的方式,即从工作面架顶爆破移到南巷提前爆破,
二、超前预裂爆破孔布置方式:
从东往西距工作面煤壁15—30米的超前顺槽(南巷)垂直于煤层走向由南向北布置φ100mm扇形爆破孔,每排在一个截面线上布置或错位分组布置。
三、超前预裂爆破孔施工方式:
采用ZY—650型坑道钻机施工超前预裂爆破孔,在ZY—650型坑道钻机未到货前采用ZDY—548型液压钻机和KHYD—75dIA岩石钻施工超前预裂爆破孔,大于60°的孔采用岩石钻施工,小于60°的孔采用液压钻机施工。
四、超前预裂爆破技术参数:
1、爆破孔排距:
4.2m,由东向西每隔4.2m布置一排。
2、爆破孔间距:
每排的炮孔间距为0.5m,每排8个炮孔,在一个截面线上布置或错位布置,错距为0.5—1m。
3、爆破孔长度、角度:
详见下面表。
4、爆破孔装药长度、封孔长度、空孔长度:
详见下表。
5、爆破孔炮头、雷管数:
每个炮孔2个炮头,每个炮头2发雷管。
6、护巷煤厚3.2m;顶部煤厚1.9m;爆破孔末端距顶板2.5m,距底板1.5m。
7、距工作面煤壁15—30米爆破。
炮孔技术参数表
孔号
孔
长
(m)
角度(°)
间距
m
排距
m
装药长度
(m)
封泥长度
(m)
空孔长度(m)
装药量
(Kg)
雷管
(个)
起爆
顺序
连线方式
装药结构
1
18.97
68
0.5
4.2
11.98
3
3.99
85
4
一
次
性
起
爆
雷管
并联
,孔与孔间
串联方式
连续
正向
装药
2
17.38
83
0.5
4.2
8.9
3
5.48
63.5
4
3
17.35
80
0.5
4.2
11.09
3
3.26
80
4
4
18.75
66
0.5
4.2
8.61
3
7.14
61.5
4
5
21.48
54
0.5
4.2
14.24
3
4.24
101.7
4
6
23.39
45
0.5
4.2
10.6
3
9.799
75
4
7
21.76
33
0.5
4.2
10.84
3
5.92
77.5
4
8
21.42
19
0.5
4.2
4.08
3
14.34
29
4
合计
573.2
32
五、装药方式:
采用装药车装药,在装药车未到货时,采用人工装药,为正向装药结构,炸药为乳化筒装炸药,每10节炸药装一个炮头,每孔2个炮头,每个炮头2发瞬发电雷管。
六、封孔方式:
采用封孔器封孔,在封孔器未到货时,采用人工封孔,使用不燃性黄土炮泥封孔。
封孔长度不小于3m。
七、连线方式:
孔内并联,孔外串联,即孔内每个炮头2发雷管并联,孔外炮线串联。
八、起爆方式及顺序:
1、起爆方式:
采用200型发爆器一次性起爆,每排7个爆破孔一次起爆,每次爆破原则上不多于3排。
2、起爆顺序:
从东向西(从里往外)逐排起爆。
九、工作面超前预裂爆破工艺流程:
预裂爆破工作布置→准备(准备工具、材料、设备并进行支护、设备检查)→加强预裂爆破孔段支护→施工超前预裂爆破孔→回撤工具、设备、物料→装孔→爆破。
1、预裂爆破工作布置工序:
方案交底→贯彻学习→布置工作。
⑴由矿领导和主管单位把预裂爆破方案向预裂爆破施工单位交底并布置预裂爆破实施工作。
⑵由施工单位组织学习贯彻预裂爆破方案,使作业人员了解掌握预裂爆破工艺、工序、参数、标准、措施,
⑶施工单位每班班前会必须由技术员和值班队长认真安排预裂爆破工作,讲清讲透,交待清楚。
2、准备工序:
配备工具、材料、设备→检查
⑴准备好所需的工具、材料、设备,并在超前预裂爆破打孔处按标准化要求分类码放整齐,收拾干净打孔附近的杂物、浮煤浮矸,
⑵检查支护和设备是否完好,发现问题立即处理好。
支护和设备不完好不准打孔作业。
3、加强预裂爆破孔段支护:
采用液压单体加强支护,或对原先失效单体重新补液或更换,必须先支护后作业,必须支护有效可靠。
4、施工超前预裂爆破孔工艺:
测设孔位→剪网口→稳钻→上钻头钻杆→试机→钻进→退钻杆→回撤钻机钻杆。
⑴由施工单位技术员在现场根据预裂爆破方案测设标定预裂爆破孔位置。
⑵按标定的孔位剪网,剪网口尺寸为25*25cm,并挖干净网口的活煤活矸。
⑶稳钻,按预裂爆破孔方位角度把打孔钻机稳定在打孔的位置,用测角仪实测,直到符合规定值。
钻机必须牢固可靠。
⑷上钻头上钻杆,必须停机上,严禁开机上,钻头钻杆上牢固。
⑸开机试机空转一次,发现问题立即停机处理。
⑹开机钻进,按钻机操作规程操作。
⑺退钻杆,必须停机人工退钻杆,退下的钻杆必须码放整齐,严禁乱扔乱放,不得影响行人。
⑻回撤钻机钻杆,每孔打完后,立即停电把钻机钻杆搬运到下一个孔位置施工。
5、回撤工具、设备、物料工艺:
当每排孔打完后,及时回撤工具、设备、物料,搬运到下一排爆破孔处分类放整齐。
6、装孔工艺:
检查瓦斯→验孔→制作引药→装药→封孔→收
打完一排孔即时装完一排孔,本排严禁打孔装药同时进行,目前采用乳化筒状炸药,人工装药,待装孔机到货后采用装药车装散装胶质炸药,使用煤矿许可瞬发电雷管。
⑴检查瓦斯,装孔前先由瓦斯检查员检查瓦斯,瓦斯超限不准装孔作业。
⑵验孔,装药前先验孔,检查孔内的温度、孔深、角度、方向;
计算装药量确认无误后方可进行装药;检查装药工具及作业环境,作业环境附近气体是否正常,顶板与帮是否完好,装药地点是否有障碍物,检查炮杆子是否完好,根数是否够量;装孔前先清理干净孔内的残渣;准备好装孔的工具和炸药及炮泥。
⑶制作引药,必须避开带电导体和设备,在支护完好处制作引药,
禁止在带电物体附近制作引药。
必须先将雷管脚线短路,用绝缘胶布包好,每个引药装两发电雷管,从筒状炸药雷管孔插入并用雷管脚线缠绕紧,制作完毕后应由专人看管。
⑷装药,人工装药,正向装药结构,雷管聚能穴朝孔内方向。
一
次最多10节药往孔内送,用专用炮杆子送到孔底并捣紧。
每6—10节药装一个引药,引药两发雷管并联,每孔装2两个引药,4发雷管。
严格按照设计装药量进行装药,不得随意增减装药量。
炮眼内发现异常、有显著瓦斯涌出、煤岩松散、温度骤高骤低等情况,不得装药;炮眼内煤、岩粉没有清除干净,不得装药;发现炮眼缩小、坍塌或有裂缝,不得装药。
没有合乎质量和数量要求的封泥,不得装药。
未检查瓦斯,或装药地点附近20m以内风流中瓦斯浓度达到1%时,不得装药。
⑸封孔,采用人工装黄土炮泥封孔,把黄土装入塑料袋中填满填
实,把口封好,每孔炮泥长度不得小于3米,炮泥捣紧。
封泥时要防止母线挤断或挤破线皮造成短路或拒爆。
严禁用可燃物材料做炮泥严禁用煤粉、块状材料做炮泥。
⑹收尾,母线另一端应先进行短接用绝缘胶布包缠紧,将包好母线放入孔内保存好。
填写装孔记录,记录好现场的装药量,孔深、孔径、孔数、雷管的使用量,记录装药时间、地点、封泥量、计算最小抵抗线。
打扫装药现场,清理工具及垃圾。
恢复装药现场的标准化工作。
装药各种器具归位,在工作面现场清点炸药与雷管的数量,严格按清退制度将火工品送回炸药库与库工核实。
7、爆破工艺:
检查瓦斯→加强支护→导通测试→连线→撤人设警岗→接线→起爆。
根据采区进度或采区通知进行爆破,采用正向爆破,距工作面煤壁4.2米时进行起爆爆破,装药两排孔放一排孔,每排一次性起爆爆破。
连线方式为孔内并联,孔与孔之间串联;起爆方式为发爆器起爆。
⑴检查瓦斯,起爆前必须由专职瓦斯检查员检查瓦斯,未检查瓦
斯,或装药地点附近20m以内风流中瓦斯浓度达到1%时,严禁起爆。
⑵加强支护,工作面液压支架走到位,片帮板伸出紧贴煤壁,对
端头支护和两巷超前支护单体重新补液,爆破点20米内打单体进行双排支护或三排支护。
⑶导通测试,由专职爆破员进行对雷管母线和起爆线用专用仪表或发爆器测试,发现问题立即处理。
⑷连线,采用孔内并联,孔与控串联方式连线。
⑸撤人设警岗,指定专人包区域撤人,把本工作面和影响区域的
人员全部撤出到进风巷起爆点外,起爆点距爆破点距离不得小于150米,指定专人包区域在起爆安全距离外所有进入爆破点的通道口设警岗。
⑹接线,接线前清点确认人员去向后,由爆破员接线。
⑺起爆,起爆前必须用电话向矿调度汇报请示,待接到调度室起
爆指令后,确认无问题时进行起爆。
起爆30分钟后,从进风巷进入爆破地点和工作面检查瓦斯、支护、巷道、工作面垮冒情况,并收掉起爆线,发现问题立即组织处理,无问题后恢复采面生产作业。
第二节工作面超前预裂爆破主要设备配备
第三节工作面超前预裂爆破劳动组织
一、作业方式
采用“三班四运转”作业方式,即三个班生产作业,一个班轮休,两天一倒班,每班8小时,除法定节假日外,每天连续生产作业。
打孔班“三八”工作制,每班4人,装药工根据打眼情况插班作业,打孔完成后立即装药,爆破时间根据工作面推进情况确定。
二、循环方式
综采工作面每完成一个放煤步距,工作面推进度4.2m,完成一次顶煤超前预爆破。
超前预爆破孔完成装药待放炮的孔不少于2排。
循环作业图表与原架顶爆破相同。
三、劳动组织表
早班
中班
夜班
合计
备注
打孔工
4人
4人
8人
装药工
6人
6人
合计
6人
4人
4人
14人
其它与原架顶爆破相同。
第三章 方案实施基本要求
1、施工人员必须严格按照方案所要求的各项参数进行施工。
2、发生严重冒顶的地段不得打孔或者少打眼、少装药,同时装完药的孔必须根据工作面和巷道实际情况滞后放炮。
3、在施工炮孔时,减少人为的误差,提高施工精度,保证施工质量。
必须提高装药和封孔质量。
4、方案实施过程中可根据现场实际情况进行炮孔参数调整。
5、顶煤超前预爆破周期可根据试验效果进行调整。
6、安全员负责现场打孔和装孔质量监督检查,施工单位技术人员必须即时认真如实记录打孔、装药、封孔、爆破、推进度、放煤量、回采率等实际技术参数,分析超前预裂爆破效果,提出调整技术参数意见。
第四章 危险源辨识及风险评估
根据工作面超前预裂爆破工艺工序,并参照风险管理手册结合实际工作经验分析每道工序可能出现的危害因素,具体如下:
危险源辨识及风险评估表
任务
危险源
风险类型
风险评估及后果描述
事故类型
风险评估
可能性
损失
风险值
风险等级
一、技术措施学习
全员未学习安全技术措施
人
1、人员作业前不能有效地控制危险源,作业时,发生事故。
2、发生灾害不能有效的进行自保互保工作
其他事故
I4
B5
20
重大
二、开工前的准备
1.搬运钻机时,带电进行搬运
人
搬运时,钻机误启动,造成人员伤害。
机电事故
K2
A6
12
中等
2.个人防护不到位
人
作业中,衣襟、袖口、裤口没束紧搅入钻机内造成人员伤害。
其它事故
J3
E2
6
一般
3.开钻前未进行试运行检查
人
不能及时发现钻机存在的问题造成设备损坏或人员伤害。
其它事故
K2
E2
4
一般
4.水沟不畅通
环
1、巷道内积水多,滑倒行人。
2、打到含水层时,不能及时进行排水。
其它事故
K2
A6
12
中等
5.未检查施工地点支护情况
环
支护不完好垮冒伤人。
其它事故
J3
E2
6
一般
三、钻敲帮问顶
1.未进行敲帮问顶工作
人
不能消除顶板隐患,易发生顶板事故
顶板事故
I4
C4
16
中等风险
2.敲帮问顶工具不合适
机
人员操作不便,易发生顶板事故
其他事故
K2
D3
6
一般风险
3.敲帮问顶人员站位不合理、监护不到位
人
处理过程中被块煤砸伤
顶板事故
K2
D3
6
一般风险
四、钻机的使用
1.安装、稳固钻机时人员配合不当
人
精神不集中,行走时、相互用力不协调,钻机偏倒造成人员伤害。
其它事故
J3
E2
6
一般
2.钻孔角度定位不准确
人
达不到钻孔目的,浪费人力物力。
其它事故
J3
E2
6
一般
3.开钻施工时停水
人
停水后容易埋钻,造成钻机设备损坏。
其它事故
J3
F1
3
一般
4.钻进过猛
人
机架后部脱离固定物,反倒造成人员伤害。
其它事故
J3
D3
9
中等
5.发现异常未停钻
人
记录偏差,孔深具体数据不详,使防止隐患处理计划错误。
其它事故
I4
F1
4
一般
6.操作人员正对孔口
人
有害气体喷出造成人员气体中毒。
其它事故
J3
D3
9
中等
7.钻杆不完好
机
钻杆被堵、钻杆变形、丝口损坏造成埋钻、钻眼变形、废眼,降低工作效率。
其它事故
J3
E2
6
一般
8.操作工和上钻杆工配合不当
人
钻杆甩出击伤作业人员。
其它事故
J3
D3
9
中等
9.加接钻杆误操作
人
钻杆脱落伤人
其它事故
J3
D3
9
中等
10.人员配合不好未按程序卸钻杆
人
钻杆、管钳飞出击伤人员。
其它事故
J3
E2
6
一般
11.管钳未卡在钻杆四方上
人
管钳飞出造成人员伤害
其它事故
I4
D3
12
中等
12.钻杆未及时回收、码放
机
影响行人,发生灾害时,人员不能及时撤离
其它事故
K2
D3
6
一般
五、装药及封孔
1.未验孔或验孔不认真
人
孔成型不好、孔深不符合要求或出现打穿现象,装药过程中无法装药、装药量不符合要求影响爆破效果或炸药泄漏引发放炮事故
其它事故
I4
D3
12
中等
2.制作起爆药包没有选择合适环境、装配好的引药没有按要求存放
人
造成火工品爆炸及人员伤亡
放炮事故
K2
A6
12
中等
3.没有按正确的方法制作起爆药包
人
造成火工品爆炸,造成人员伤害
放炮事故
K2
A6
12
中等
4.封泥质量不符合要求
机
封泥质量不符合要求造成放炮效果降低或发生事故
其它事故
K2
D3
6
一般
5.炮泥封孔长度不够
人
放炮坐力大,损坏设备或降低爆破质量
其它事故
K2
D3
6
一般
六、爆破管理
1.放炮前清点人数不明
人
放炮过程中造成人员伤亡
放炮事故
I4
B5
20
重大
2.未执行“一炮三检”“三人连锁”放炮制度
人
放炮时人员误入,造成人员伤亡
放炮事故
H5
E2
10
中等
3.未设置警戒或设置的警戒不醒目
人
放炮时有滞留或误入人员时致使人员受伤
放炮事故
K2
D3
6
一般
4.连线方式与连线质量不符合要求
人
连线方式与接线不符合要求发生拒爆、残爆,当处理残爆、拒爆过程中发生事故,造成人员伤害
放炮事故
H5
E2
10
中等
5.爆破后,检查的程序不对
人
造成进入工作面的人员受到伤害
其它事故
K2
D3
6
一般
6.监控设备失效
机
不能及时发现瓦斯超限造成人员伤