年产10万吨邻苯二甲酸二辛酯工艺设计实现可行性方案.docx
《年产10万吨邻苯二甲酸二辛酯工艺设计实现可行性方案.docx》由会员分享,可在线阅读,更多相关《年产10万吨邻苯二甲酸二辛酯工艺设计实现可行性方案.docx(27页珍藏版)》请在冰豆网上搜索。
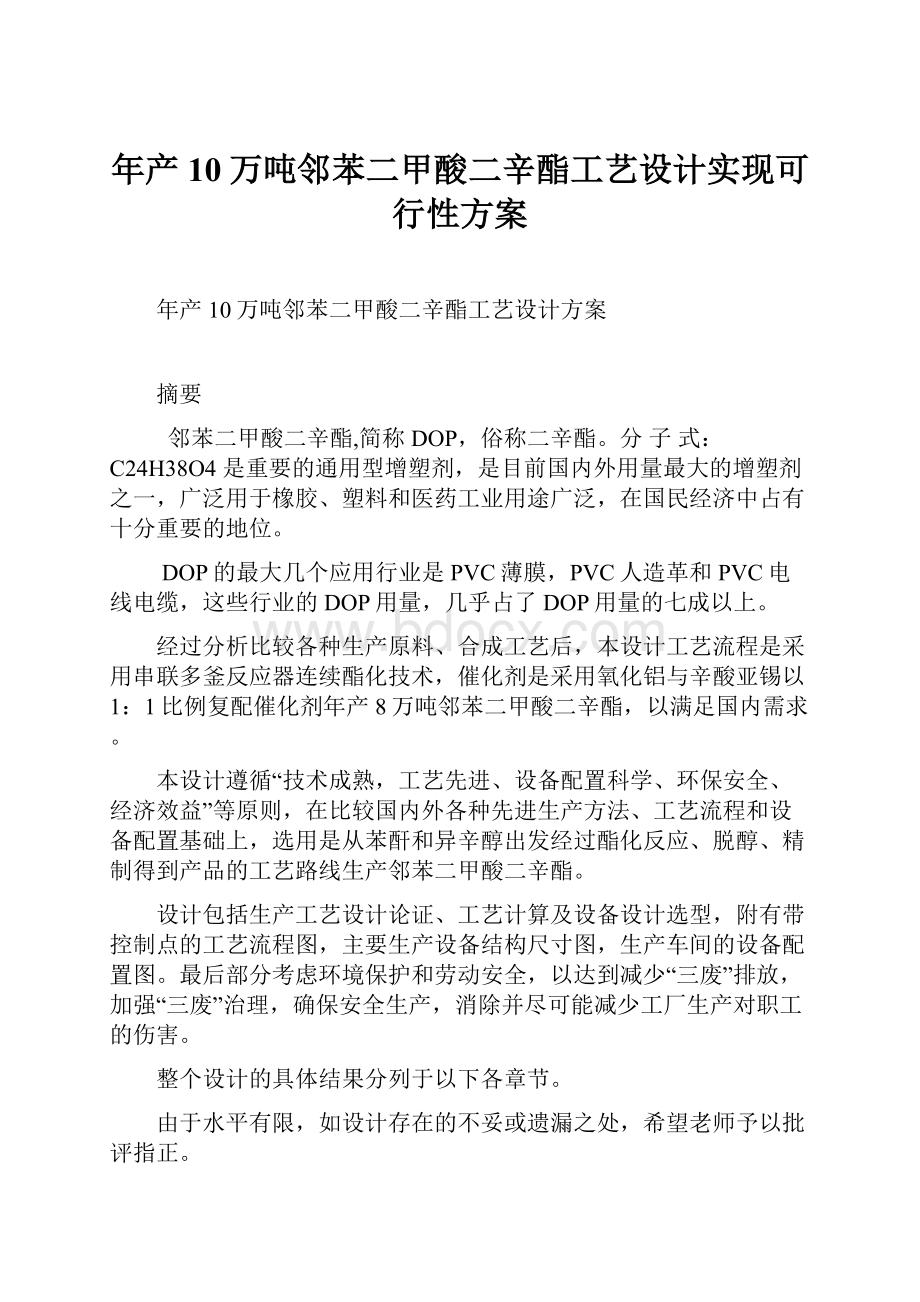
年产10万吨邻苯二甲酸二辛酯工艺设计实现可行性方案
年产10万吨邻苯二甲酸二辛酯工艺设计方案
摘要
邻苯二甲酸二辛酯,简称DOP,俗称二辛酯。
分子式:
C24H38O4是重要的通用型增塑剂,是目前国内外用量最大的增塑剂之一,广泛用于橡胶、塑料和医药工业用途广泛,在国民经济中占有十分重要的地位。
DOP的最大几个应用行业是PVC薄膜,PVC人造革和PVC电线电缆,这些行业的DOP用量,几乎占了DOP用量的七成以上。
经过分析比较各种生产原料、合成工艺后,本设计工艺流程是采用串联多釜反应器连续酯化技术,催化剂是采用氧化铝与辛酸亚锡以1:
1比例复配催化剂年产8万吨邻苯二甲酸二辛酯,以满足国内需求。
本设计遵循“技术成熟,工艺先进、设备配置科学、环保安全、经济效益”等原则,在比较国内外各种先进生产方法、工艺流程和设备配置基础上,选用是从苯酐和异辛醇出发经过酯化反应、脱醇、精制得到产品的工艺路线生产邻苯二甲酸二辛酯。
设计包括生产工艺设计论证、工艺计算及设备设计选型,附有带控制点的工艺流程图,主要生产设备结构尺寸图,生产车间的设备配置图。
最后部分考虑环境保护和劳动安全,以达到减少“三废”排放,加强“三废”治理,确保安全生产,消除并尽可能减少工厂生产对职工的伤害。
整个设计的具体结果分列于以下各章节。
由于水平有限,如设计存在的不妥或遗漏之处,希望老师予以批评指正。
1总论
1.1邻苯二甲酸二辛酯简介
2生产原料、设备选用和工艺条件
2.2项目原料
2.2工艺条件
2.2工艺反应设备
3工艺反映原理和注意事项
3.1反应原理
3.1.1主反映
3.1.2副反应
3.2反应注意事项
3.2.1脂反映
3.2.2中和反应
3.2.3分离回收
3.2.4脱色精制
3.3热力学动力学分析和催化剂
3.3.1热力学分析
3.3.2动力学分析
3.3.3催化剂
4工艺流程
4.1酯化过程
4.2脱醇过程
4.3中和水洗
4.4汽提过程
4.5过滤过程
4.6工艺流程图及其说明
5物料衡算
5.1设计生产能力
5.2一级酯化物料计算
5.3二级酯化物料计
5.4酯化工段物料衡结果
6自动控制
6.1仪表设计说明
6.2检测和控制
6.3仪表配置
6.3.1温度仪表
6.3.2压力仪表
6.3.3流量仪表
6.4仪表防护
7分析化验
7.1色度
7.2密度
7.3含量
7.4酸度
8三废处理、安全卫生防护
8.1三废治理
8.1.1废水处理
8.1.2废气处理
8.1.3废渣处理
8.2安全卫生防护
结束语
1总论
1邻苯二甲酸二辛酯简介
邻苯二甲酸二辛酯(简写为DOP,俗称二辛酯)具有以下特征:
无色粘性液体,微有气味,能溶于专款专用脂肪烃和芳香烃,微溶于甘油,不溶于水,密度是0.981g/ml,熔点是-50℃,沸点是384℃,折射率n20/D是1.485-1.487,闪点:
195℃。
邻苯二甲酸二辛酯是通用型增塑剂,主要用于聚氯乙烯酯的加工,还可用于化地树酯、醋酸树酯、ABS树酯及橡胶等高聚物的加工,也可用于造漆、染料、分散剂等。
DOP增塑的PVC可用于制造人造革、农用薄膜、包装材料、电缆,有机溶剂、气相色谱固定液。
DOP的最大几个应用行业是PVC薄膜,PVC人造革和PVC电线电缆,这些行业的DOP用量,几乎占了DOP用量的七成以上。
工业上为最广泛使用的增塑剂,除了乙酸纤维素、聚乙酸乙烯外,与绝大多数工业上使用的合成树酯和橡胶均有良好的相容性。
本品具有良好的综合性能,混合性能好,增塑效率高,挥发性较低,低温柔软性较好,耐水抽出,电气性能高,耐热性和耐候性良好。
通用级DOP:
广泛用于塑料、橡胶、油漆及乳化剂等工业中。
用其增塑的PVC可用于制造人造革、农用薄膜、包装材料、电缆等。
电气级DOP:
具有通用级DOP的全部性能外,还具有很好的电绝缘性能,主要用于生产电线和电。
食品级DOP:
主要用于生产食品包装材料。
医用级DOP:
主要用于生产医疗卫生制品,如一次性医疗器具及医用包装材料等。
目前,国内外市场需求量不断增长。
在人类日益注重环保的今天,在涂料、油墨生产中采用高档溶剂是大势所趋。
作为高档溶剂,DOP在国内外的应用在持续稳定增长,建筑、汽车等行业的迅速发展,也会带动对DOP类溶剂的需求。
随着境外的环保法规的出台,PVC电线电缆开始出现用量下降的趋势,但是在PVC薄膜和PVC人造革方面,目前受环保法规的实际影响不大。
其中工业生产的产品规格如表1所示。
2生产原料、设备选用和工艺条件
2.1生产原料
本工艺采用邻苯二甲酸酐和2-乙基己醇合成。
①原料邻苯二甲酸酐具有以下特点白色鳞片结晶,熔点130.2℃,沸点284.5℃的晶体。
它几乎不溶于水,能溶于乙醇,微溶于乙醚和热水,对皮肤有刺激性作用,空气中的浓度不宜超过2mg/L。
邻苯二甲酸酐可由萘或邻二甲苯催化氧化制得。
本项目采用邻二甲苯固定床催化氧化法制得
②2-乙基己醇(辛醇)为无色透明液体额,特俗气味,沸点181~183℃,溶于水和乙醇、乙醚等有机溶剂,
在工业上可以用乙炔、乙烯或者丙烯以及粮食为原料生产2-乙基己醇。
2.2工艺条件
①反应温度
酯化反应温度即为辛醇与水的共沸温度,通过共沸物的汽化带走反应热和水分,反应易控制。
反应温度高对化学平衡和反应速率有好多好处,但反应温度增加,产品色泽加深而影响产品质量。
一般以硫酸作为催化剂,反应温度为130~150℃;采用非酸性催化剂温度为190~230℃,大于240℃DOP则会产生裂解反应。
②原料配比
之花是可逆反应,为提高转化率,任意反应物过量,均可促使反应平衡向右移动。
由于辛醇价格较低并能与水形成共沸混合物,过量的辛醇可以将水带出反应系统,降低生成物的浓度,有利于向又进行,因此,辛醇过量,辛醇与苯酐的配比为(2.2~2.5):
1(摩尔比),若辛醇过量太多,其分离回收的负荷乙基能量小号增大。
2.3工艺反应设备
①反应器设计原则
(1)具有适宜的流体力学条件,能保证气液两相充分接触,使反应以尽可能快的速度进行,达到最大生产能力。
(2)在保证最大生产能力要求的气液流量的前提下,不能发生液泛。
(3)操作稳定,调节方便,能适应各种操作条件的变化。
②塔设备设计原则
(1)具有适宜的流体力学条件,达到气液两相的良好接触;
(2)结构简单,处理能力大,压降低;
(3)强化质量传递和能量传递。
整个生产过程中,酯化是关键,其主要设备是酯化反应器。
反应器的选用关键在于反应是采用间歇操作还是连续操作。
、
今定生产量为10万吨/年,年产量不算大,所以采用间歇操作。
其操作流程比较简单,控制也比较容易,反应其各部分的组成和温度稳定一致,无聊停留时间也一样,通常采用的间歇式反应器为带有搅拌和换热(夹套和蛇管热交换)的釜式设备,为了仿佛和保证产物纯度,可以采用衬搪玻璃的反应釜。
其中的所需的容器及其各种工艺标准如表2所示:
表2设计采用的专业标准规范
名称
标准号
《钢制压力容器》
GB150
《压力容器用钢板》
GB6654
《奥氏体不锈钢焊接钢管选用规定》
HG20537.1
《化工装置用不锈钢大口径焊接钢管技术要求》
HG20537.4
《安全阀的设置和选用》
HG/T20570.2
《爆破片的设置和选用》
HG/T20570.3
《设备进、出管口压力损失计算》
HG/T20570.9
《钢制化工容器设计基础规定》
HG20580
《钢制化工容器材料选用规定》
HG20581
《钢制化工容器强度计算规定》
HG20582
《钢制化工容器结构设计规定》
HG20583-
《钢制化工容器制造技术规定》
HG20584
《化工设备设计基础规定》
HG/T20643
《压力容器无损检测》
JB4730
《钢制压力容器焊接工艺评定》
JB4708
《钢制压力容器焊接规程》
JB/T4709
《钢制压力容器产品焊接试板的力学性能检验》
JB4744
《压力容器用钢锻件》
JB4726-472
3工艺反应原理
3.1反应原理
3.1.1主反应
邻苯二甲酸酐与2-乙基己醇酯化一般分为两步。
第一步,苯酐和辛醇合成单酯,反应速度很快,当苯酐完全溶于辛醇,单酯化基本完成。
C24H38O4+CH3CH2CH2CH2CH(C2H5)CH2OH→
第二步,邻苯二甲酸单酯与辛醇进一步酯化生成双酯,这一步反应速率较慢,一般需要使用催化剂,提高温度来加快反应速率。
3.1.2副反应
①醇分子内脱水形成烯烃。
C8H17OH醇分子内脱水形成烯烃C8H16.
C8H17OH→C8H16+H2O
②醇分子间脱水形成醚。
C8H17OH醇分子间脱水形成醚C8H1OC8H17。
2C8H17OH→C8H1OC8H17+H2O
③生成缩醛。
2C8H17OH→C8H1OC8H17+H2O
④生成异丙醇(来自催化剂本身)从而生成相应的酯。
⑤生成正丁醇(来自催化剂本身)从而生成相应的酯。
上述副反应,由于使用的选择性好高的催化剂,副反应很少,约占总质量的1%左右。
数量低,沸点较低,在酯化过程中,作为低沸物派出系统。
3.2反应注意事项
3.2.1酯化是一个比较典型的可逆反应,一般注意一下几点:
(1)将原料中的任一种过量(一般为醇类),使平衡尽量向右移动;
(2)将反应生成的酯或者水两者中任何一个即及时的从反应系统中除去,促使酯化完全,生产中常以过量的醇作为溶剂与水共沸作用,且这种共沸可以在反应中循环利用。
(3)酯化反应一般分为两步,第一步生成单酯,这步反习速率很快,但是由单酯反应生成酯的过程却很缓慢,工业上一般采用催化剂和提高反应温度来提高放映速率的。
3.2.2中和水洗
中和粗酯中的酸性杂质并除去,使粗酯酸值降低。
同时使催化剂和水失去活性并除去。
中和反应属于放热放映,为避免副反应,一般控制中和温度不超过85℃。
3.2.3醇的分离和回收
醇和酯的分离通常采用水蒸气蒸馏法,有事采用醇和水一起被蒸出,然后用蒸馏法分开。
回收醇是利用醇和酯的沸点不同,采用减压蒸馏的方法回收,回收醇中要求酯含量越低越好,否则循环使用中会使产品色泽加深,因此必须严格控制温度、压力、流量等。
3.2.4脱色精制
经醇酯分离后的粗酯采用汽提和干燥的方法,除去水分和低分子杂质很少量醇。
通过吸附剂和助滤剂的媳妇脱色作用,保证产品的色泽和体积电阻率两项指标,同时除去产品中残存的微量催化剂和其他机械杂质,最后得到高质量的邻苯二甲酸二辛酯。
3.3热力学和动力学分析
3.3.1热力学分析
邻苯二甲酸单酯与辛醇进一步酯化生成双酯的反应是可逆的吸热反应,从热力学分析,升高温度,增加反应物弄,降低生成物的浓度,都能使平衡向着生成物的方向移动。
在实际生产中,一般采用醇过量来提高苯酐的转化率,同时反应生成的水与醇形成共沸物,从系统中脱出,以降低生成物的浓度,使整个反应向着有利于生成双酯的方向移动。
3.3.2动力学分析
邻苯二甲酸单酯与辛醇进一步酯化生成双酯的反应是可逆的吸热反应,其平衡常数为
k=k1/k2=6.95
提高反应温度和使用催化剂,可缩短达到平衡的时间。
3.3.3催化剂
催化剂分为酸性催化剂和非酸性催化剂,由于采用非酸性催化剂可以免去中和和水洗两道工序,且通过过滤即可除去,跟酸性催化剂相比,优越性在于能生产出高质量的增塑剂产品和减少污染。
因此本设计采用的是非酸性催化剂。
非酸性催化剂又分为单催化剂和复配型催化剂,由于单催化剂催化反应时间长,不适合做酯化反应催化剂,相反,复配型催化剂催化反应时间短,转化率高,酸值降低幅度大,比较适合做酯化反应催化剂。
氧化铝与辛酸亚锡以1:
1比例复配非酸性催化剂合成DOP效果最佳,力求达到流程简单,设备少,热能利用合理,产品质量高。
(1)酸性催化剂以硫酸为首的酸类催化剂是传统的酯化催化剂:
常用的有:
对甲苯磺酸、十二烷基苯磺酸、磷酸、锡磷酸、亚锡磷酸、苯磺酸和氨基磺酸等。
此外硫酸氢钠等酸式盐,硫酸铝、硫酸铁、等强酸弱碱盐,以及对苯磺酰氯,也属于酸催化剂。
其中他们的催化剂活性顺序:
硫酸>对甲苯磺酸>苯磺酸>2-萘磺酸>氨基磺酸
硫酸活性高,价格便宜,是应用最普遍的酸性催化剂,用他制备DOP,在100~130℃就有很高的催化剂作用。
但是硫酸也有知名的弱点,不仅严重腐蚀设备,还会因其氧化、脱水作用与醇发生一系列的副反应,生成醛醚、硫酸单酯、硫酸双酯、不饱和物和羧基化合物,使醇的精致和回收复杂化。
为了避免这一问题,可以使用活性地狱硫酸但较为温和的其他酸作为催化剂。
比如用对甲苯磺酸。
(2)非酸性催化剂非酸性催化剂有
①铝的化合物,如氧化铝、氯酸钠,含水Al2O3+NaOH等
②ⅣB族元素化合物,如氧化钛,钛酸四丁酯,氧化锆、氧化亚锡和硅的化合物
③碱土金属氧化物,氧化锌、氧化镁,
④ⅤA族元素化合物,氧化锑、羧酸铋等。
非酸性催化剂的应用对酸性工艺来说是一项重大的技术进步,使用非酸性催化剂可缩短酯化反应时间,产品色泽优良,回收醇只需简单处理,即可循环使用。
主要的不足是酯化温度较高,一般为190~230℃,否则活性较低。
4工艺流程
在实际生产中一般有两种生产邻苯二甲酸二辛酯的方法:
酸性催化剂间歇生产邻苯二甲酸二辛酯和非酸性催化剂连续生产邻苯二甲酸二辛酯。
其中酸性催化剂间歇生产邻苯二甲酸二辛酯操作流程与控制比较简单,反应器个部分的组成和温度稳定一致,物料停留的时间也一样,容易改变品种,但是原料消耗定额高,能量消耗大,劳动生产率低,产品质量稳定。
多用于多品种、小批量生产。
非酸性催化剂连续生产邻苯二甲酸二辛酯单脂转化率高,副反应少,简化了中和、水洗工序,废水量减少,产品质量稳定,原料及能量消耗低,劳动生产率高,生产能力大,适合大吨位的生产。
由于产量不算大我们采用酸性催化剂间歇生产邻苯二甲酸二辛酯。
酸性催化剂间歇生产邻苯二甲酸二辛酯生由单酯、酯化、中和、脱醇、过滤等工艺流程组成。
4.1酯化过程
苯酐和辛醇按比例在5个串联阶梯形的酯化釜中,在氧化铝与辛酸亚锡以1:
1比例复配催化剂作用下酯化反应生成粗酯,主要工艺参数确定如下:
(1)进料温度及5釜的反应温度见表2。
(2)投料比:
PA:
2一EH=1:
2.30(wt)
(3)催化剂量:
0.03%(wt)
(4)酯化压力:
常压(带氮封)
表3进料温度及与釜反应温度
PA
2一EH
催化剂
釜1
釜2
釜3
釜4
釜5
170
175
20
190
200
210
220
230
(5)停留时间:
约7h,酯化釜体积27.4m3
(6)酯化釜搅拌器转速:
74r/min
(7)总转化率:
约99.5%
4.2脱醇过程
由于酯化反应是在过量醇的条件下进行的,必须将粗酯中的醇脱除,回收重复利用。
本设计采用真空降膜脱醇工艺,热能利用合理,脱醇效率高,可脱醇至1%左右。
脱醇工艺参数确定如下:
(1)进料粗酯温度:
230℃
(2)进料粗酯含醇量:
16%~17%
(3)降膜脱醇真空度:
30mbar
(4)加热蒸汽压力:
20ba
4.3中和、水洗过程
由于在酯化过程中会生成一些酸性杂质,如单酸酯等,本设计采用加入Na0H水溶液进行中和,生成可溶于水的钠盐与酯分离。
中和水洗工艺参数确定如下:
(1)Na0H水溶液浓度:
0.3(wt%)
(2)水洗温度:
95℃
(3)粗酯:
碱=6:
1(vo1)
(4)中和搅拌转速:
180r/min
(5)水洗搅拌转速:
50r/min
(6)NaOH单耗:
0.4kg/tDOP
(7)中和水洗后酸值:
0.01~0.02KOHmg/DOP
4.4汽提过程
汽提是通过直接蒸汽减压蒸馏,除去粗酯中的醇和有气味的低沸物,本设计采用过热蒸汽直接减压汽提工艺。
汽提干燥工艺参数确定如下:
(1)粗酯人塔温度:
140~1600C
(2)汽提塔顶部真空度:
40mbar
(3)干燥塔顶部真空度:
99mbar
(4)粗酯量:
汽提蒸汽量:
10:
1(wt)
(5)干燥塔出口酯中含水量:
0.01%~0.05%(wt)
4.5过滤过程
在粗酯中加入吸附剂和助滤剂,脱除粗酯中含色素的有机物和吸附脱除残存的催化剂和其它机械杂质,以保证DOP产品外观的透明度和纯度。
本设计采用二级过滤工艺,粗滤采用时间程控的芬达过滤器,精滤采用多层滤纸。
过滤工序工艺参数确定如下:
(1)粗酯温度:
90℃
(2)芬达过滤器粗滤周期:
48h
(3)精滤后DOP色值:
10~15(HAzEN)
4.6生产工艺流程图及其说明
DOP生产工艺流程方块图(见图1)
苯酐、异辛醇
助滤剂
无离子水
NaOH
催化剂、N2
汽提脱醇
过滤
干燥
中和水洗
二级酯化
一级酯化
产品
滤液
废水
图1DOP工艺流程方块图
工艺流程图如图2所示:
图2间歇式邻苯二甲酸二辛酯的生产工艺流程
邻苯二甲酸酐与2-乙基己醇以1:
2的质量比在总无聊质量分数为0.25%~0.3%的硫酸催化剂作用写,于150℃左右进行减压酯化反应。
操作系统的压力维持在80kPa,酯化时间一般为2~3小时,酯化时加入总物料的0.1%~0.3%的活性炭,反应混合物用5%的碱液中和,在经过80~85℃热水洗涤,分离后粗酯在130~140℃与80kPa的减压下进行脱醇,知道闪电为190℃以上为止。
脱醇后再以直接争气脱去低沸物,必要时在脱醇前可以补加一定量的活性炭,最后经过压滤而得到成品。
熔融苯酐和辛醇以一定的摩尔比[(1:
2.2~1:
2.5)在130-150先制成单酯,再经预热后进入四个串联的阶梯式酯化釜的第一级.非酸化催化剂也在此加入.第二级酯化釜温度控制不低于180,最后一级酯化温度为220~230,酯化部分用3.9MPa的蒸汽加热.邻苯二甲酸单酯的转化率为99.5%~99.9%。
为了防止反应混合物在高温下长期停留而着色,并强化酯化过程,在各级酯化釜的底部都通入高纯度的氮气(氧含量<10mg/kg中和,水洗是在一个带搅拌的容器中同时进行的。
碱的用量为反应混合物酸值的3~5倍。
使用20%的NaOH水溶液,当加入无离子水后碱液浓度仅为0.3%左右。
因此无需在进行一次单独的水洗。
非酸性催化剂也在中和、水洗工序被洗去。
然后物料经脱醇(1.32~2.67kPa,50~80℃)、干燥(1.32kPa,50~80℃)后送至过滤工序。
过滤工序不用一般的活性炭,而用特殊的吸附剂和助滤剂。
吸附剂成分为SiO2、AL2O3、Fe2O3、MgO等,助滤剂(硅藻土)成分为SiO2、AL2O3、Fe2O3、CaO、MgO等。
该工序的主要目的是通过吸附剂和助滤剂的吸附,脱色作用,保证产品DOP的色泽和体积电阻率两项指标,同时除去DOP中残存的微量催化剂和其他机械杂质。
最后得到高质量的DOP。
DOP的收率以苯酐或以辛醇为99.3%。
回收的辛醇一部分直接循环到酯化部分使用,另一部分需进行分馏和催化加氢处理。
生产废水(COD值700~1500mHg/L)用活性污泥进行生化处理后再排放。
本工艺流程特点:
原料简单,工艺流程短,物料循环使用,生产效率高。
5、物料衡算
5.1 设计生产能力
DOP年生产能力根据设计任务规定为年生产80000吨/年,取工作日为330天。
DOP 10000吨
年生产日 330天
日产DOP100000÷330=303.03吨
每小时生产 303.3÷24=12.63吨
要求达到最后产品达规格
产品规格:
一等品DOP 含量99.5%
故每小时要得纯DOP为:
12.63×99.5%=12.57吨
设整个过程之中DOP损失量为4%
则实际每小时产纯DOP为12.57÷(1-4%)=13.09吨
分子量:
苯酐148.12异辛醇130.0DOP390.3H2O18
5.2一级酯化物料计算
根据一级酯化反应式:
二级酯化反应式:
第一步酯化转化率为100%,第二步酯化转化率为99.5%.
一小时一级酯化反应釜进釜苯酐的量为:
13.09×1000÷390.3÷0.995=33.71kmol
根据投料比苯酐:
异辛醇=1:
2.2
异辛醇投入量为33.71×2.2=74.16kmol
又回流异辛醇量21.55kmol
总异辛醇量74.16+21.55=95.71kmol
出釜异辛醇量为74.16-33.71+21.55=62.00kmol
单酸酯的量33.71kmol
5.3二级酯化物料计算
进釜异辛醇62.00kmol
单酸酯的量33.71kmol
氧化铝与辛酸亚锡复配催化剂量0.32kmol
N28m3/h
出釜第一釜的转化率XA=0.523
DOP的物质的量33.71*0.523=17.63kmol/h
异辛醇量为62.00-26.96*0.523=47.90kmol/h
单酸酯的量33.71-17.63=16.08
氧化铝与辛酸亚锡复配催化剂量0.32kmol
产生的水的物质的量n水=33.71*0.523=17.63kmol/h
异辛醇一部分作为带水剂与水一起出釜,异辛醇经冷凝器冷却再回流至反应釜中,经测定nB:
n水=2.5:
1。
所以nB=17.63
2.5=44.08kmol/h
N28m3/h,转化为摩尔流量:
∴每一小时将有:
3排出反应釜。
5.4酯化工段物料衡结果
表4.一级酯化段物料衡算表
入塔
苯酐
异辛醇
单酸酯
出塔
苯酐
异辛醇
单酸酯
量(kmol/h)
33.71
95.71
0
量(kmol/h)
0
62.00
33.71
摩尔含量(%)
25.0
75.0
0
摩尔含量(%)
0
66.67
33.33
表5二级酯化段釜1物料衡算表
入釜
异辛醇
单酸酯
氧化铝与辛酸亚锡
N2
水
DOP
量(kmol/h)
62.00
33.71
0.32
0.32216
0
0
出釜
异辛醇
单酸酯
氧化铝与辛酸亚锡
N2
水
DOP
量(kmol/h)
39.80
12.86
0.32
0.32216
14.10
14.10
6自动控制
4.6.1仪表设计说明
为对生产过程中各种工艺参数进行测量、指示和记录,本厂设有大量检测仪表,代替了操作人员对工艺参数的不断人工观察与记录,节省了大量的人力与时间。
同时,在自动检测过程中,一旦发现工艺参数超过了设定允许范围,计算机自控系统自动地发出声光报警信号,告诫操作人员注意;与此同时联锁系统立即采取应急措施,打开安全阀或切断某些管道,必要时紧急停车,以防事故的发生和扩大,最大限度的保护操作人员的安全。
6.2检测和控制
根据工艺生产过程的需要,在控制上采用了集中和就地相结合的方案,即重要的工艺参数集中在控制室进行指示、报警、控制和操作,非重要的工艺参数于就地指示。
所有工艺参数的显示,打印、趋势记录以及信号越限报警均由DCS来完成,DCS留有与上位机的通讯接口,以便将来与总厂调度通讯,使厂方的管理人员时时刻刻掌握整个工厂的生产运行状况。
6.3仪表配置