7第七章高辛烷值组分生产全.docx
《7第七章高辛烷值组分生产全.docx》由会员分享,可在线阅读,更多相关《7第七章高辛烷值组分生产全.docx(45页珍藏版)》请在冰豆网上搜索。
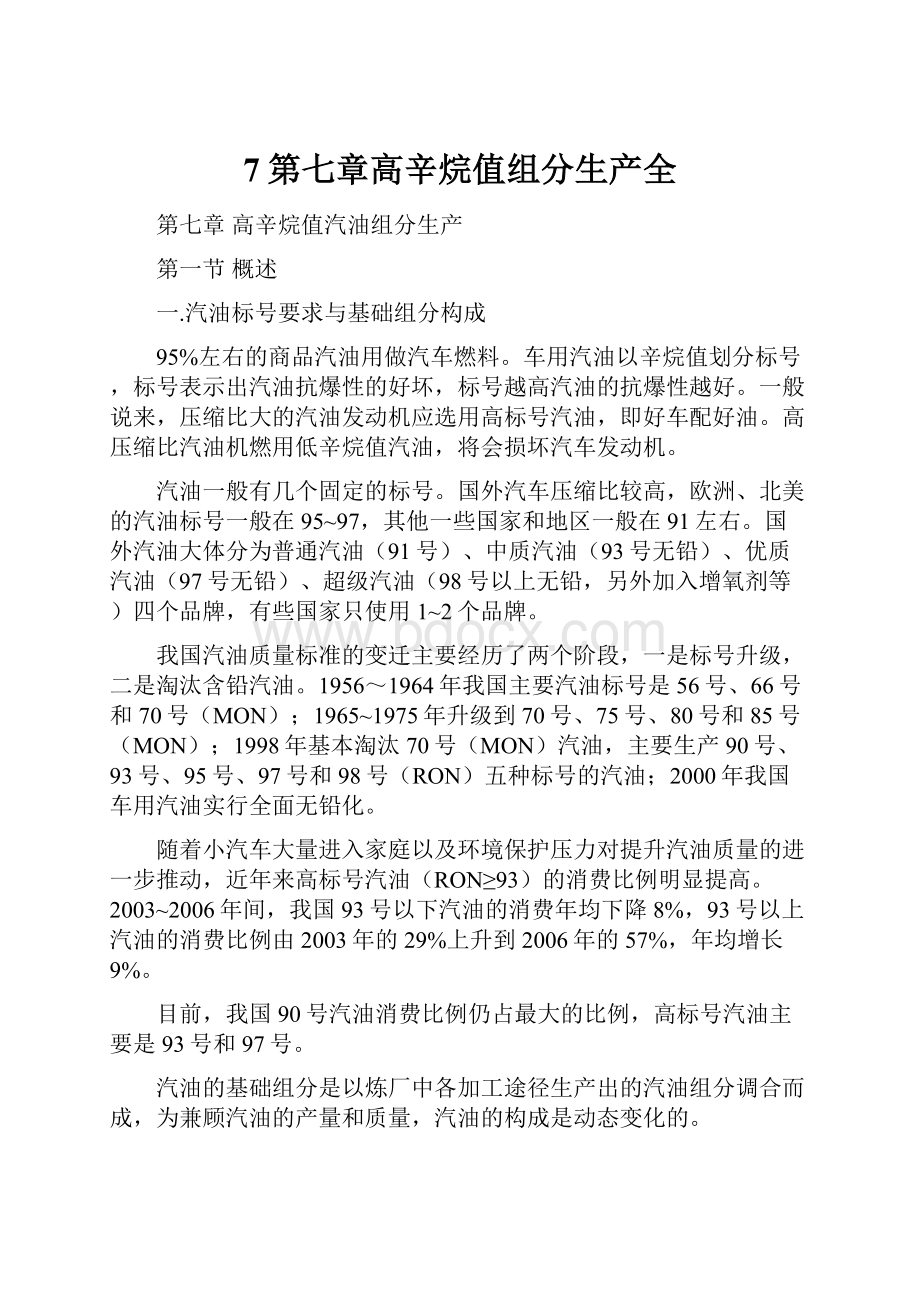
7第七章高辛烷值组分生产全
第七章高辛烷值汽油组分生产
第一节概述
一.汽油标号要求与基础组分构成
95%左右的商品汽油用做汽车燃料。
车用汽油以辛烷值划分标号,标号表示出汽油抗爆性的好坏,标号越高汽油的抗爆性越好。
一般说来,压缩比大的汽油发动机应选用高标号汽油,即好车配好油。
高压缩比汽油机燃用低辛烷值汽油,将会损坏汽车发动机。
汽油一般有几个固定的标号。
国外汽车压缩比较高,欧洲、北美的汽油标号一般在95~97,其他一些国家和地区一般在91左右。
国外汽油大体分为普通汽油(91号)、中质汽油(93号无铅)、优质汽油(97号无铅)、超级汽油(98号以上无铅,另外加入增氧剂等)四个品牌,有些国家只使用1~2个品牌。
我国汽油质量标准的变迁主要经历了两个阶段,一是标号升级,二是淘汰含铅汽油。
1956~1964年我国主要汽油标号是56号、66号和70号(MON);1965~1975年升级到70号、75号、80号和85号(MON);1998年基本淘汰70号(MON)汽油,主要生产90号、93号、95号、97号和98号(RON)五种标号的汽油;2000年我国车用汽油实行全面无铅化。
随着小汽车大量进入家庭以及环境保护压力对提升汽油质量的进一步推动,近年来高标号汽油(RON≥93)的消费比例明显提高。
2003~2006年间,我国93号以下汽油的消费年均下降8%,93号以上汽油的消费比例由2003年的29%上升到2006年的57%,年均增长9%。
目前,我国90号汽油消费比例仍占最大的比例,高标号汽油主要是93号和97号。
汽油的基础组分是以炼厂中各加工途径生产出的汽油组分调合而成,为兼顾汽油的产量和质量,汽油的构成是动态变化的。
美国汽油构成大致为催化裂化汽油占1/3,催化重整汽油占1/3,其他高辛烷值调合组分(烷基化油、异构化油、MTBE等)占1/3。
西欧催化汽油27%,催化重整汽油47%,剩余部分主要是其他高辛烷值组分。
参见第五章表5.1.1、表5.1.2及表5.1.3。
我国原油一般偏重,轻质油品含量低,为增加汽油、柴油、乙烯裂解原料等轻质油品产量,原油二次加工路线已经形成了以催化裂化为主体,延迟焦化、加氢裂化和减粘裂化等工艺为辅助的加工体系,这使得我国汽油的构成比较单一,且以催化裂化汽油占主导地位。
1998年我国汽油构成中催化裂化汽油占85%,重整汽油、烷基化油、MTBE等比例很低,2003年催化裂化汽油占74.1%,重整汽油占14.6%,其他组分所占比例很小。
从标号来看,我国90号汽油几乎全部为催化裂化汽油,93号汽油也主要由催化裂化汽油和重整汽油调和而成。
97号、98号汽油以催化裂化汽油和重整汽油为基础,再调入MTBE、烷基化油等高辛烷值组分。
汽油组成的差别使得我国汽油质量与国外有明显差距。
二.提高汽油辛烷值的途径
目前提高汽油辛烷值的技术主要有催化重整技术、烷基化技术、异构化技术、叠合技术、醚化技术和添加汽油辛烷值改进剂(抗爆剂)等。
各种添加剂虽然能显著地提高汽油抗爆性的能力,但由于它们不是汽油的组分(烃类),往往在使用过程中会带来这样那样的问题,同时添加剂的价格往往很高。
催化重整汽油的重组分的辛烷值较高,轻组分的辛烷值较低,可以弥补催化裂化汽油重组分辛烷值低,轻组分辛烷值高的不足,但其芳烃含量及苯含量高。
烷基化油辛烷值高、敏感度好、蒸气压低、沸点范围宽,是不含芳烃、硫和烯烃的饱和烃,是理想的高辛烷值清洁汽油组分。
异构化是提高整体汽油辛烷值最便宜的方法之一,可使轻直馏石脑油的辛烷值提高10%~22%。
MTBE是开发和应用最早的醚类辛烷值改进剂。
ETBE不仅使汽油的辛烷值得以提高,而且汽油的经济性及安全性都比添加MTBE的汽油要好。
催化裂化和催化重整工艺前已述及,本章重点介绍其它的生产高辛烷值汽油组分的装置。
三.汽油抗爆剂
为了弥补汽油各方面质量的不足,需添加各种汽油添加剂。
使用抗爆剂是提高汽油抗爆性最经济、最行之有效的方法之一。
汽油抗爆剂分为金属有灰类和有机无灰类两种。
金属有灰类抗爆剂主要包括烷基铅、铁基化合物、锰基化合物、稀土羧酸盐等,这类抗爆剂虽能有效提高汽油的抗爆性,但存在颗粒物的排放问题,欧美等发达国家已不再提倡使用。
近一段时期以来,汽油抗爆剂的开发研究一直朝着有机无灰类方向发展。
有机无灰类抗爆剂主要包括一些醚类、醇类、酯类等。
以上两类抗爆剂作用相同,抗爆机理各异,金属有机化合物类抗爆剂的抗爆机理与四乙基铅(TEL,Pb(C2H5)4)相似:
在燃烧条件下分解为金属氧化物颗粒,使正构烷烃氧化生成的过氧化物进一步反应为醛、酮或其他环氧化合物,将火焰前链的分支反应破坏,使反应链中断,阻止汽油过度燃烧,使汽缸的爆震减小。
苯胺及其衍生物、烯烃聚合物和含氧有机化合物(醇、酮、醚及酯)等有机化合物抗爆剂,按过氧化物减少机理抗爆:
在燃烧进入速燃期以前与汽油中的不饱和烃发生反应,生成环氧化合物,使整个燃烧过程中生成的过氧化物浓度减少,避免多火焰中心生成,使向未燃区传播活性燃烧核心的作用减弱。
1.金属有灰类抗爆剂
1)烷基铅
1970年以前,美国主要依靠添加四乙基铅提高汽油的辛烷值,由于四乙基铅毒性大,因此于1970年颁布清洁空气法,并于1975年采取了限铅和禁铅措施。
1999年12月,我国国家技术监督局发布“车用无铅汽油”国家标准GB17930-1999,2000年7月1日,全国停止销售含铅汽油。
2)锰基化合物
可作抗爆剂的锰基化合物有多种,以甲基环戊二烯三羰基锰(简称MMT)性能最好,适于应用,使用MMT主要有以下效果。
①提高无铅汽油辛烷值,与含氧调合组分具有良好的配伍性;
②减少炼油厂及汽车的NOx、CO、CO2的排放,总体上减少碳氢化合物排放;
③可配合汽车废气排放控制系统,对催化转化器有改善作用,对氧气传感器没有危害;
④减少排气阀座缩陷,对进气阀具有保洁作用。
3)铁基化合物
铁基化合物的代表物为二茂铁,分子式为(C5H5)2Fe,也叫二环戊二烯合铁,常温下为橙黄色粉末,有樟脑气味,能升华,熔点为173~174℃,沸点为249℃,不溶于水,易溶于有机溶剂中。
二茂铁在汽油中加入质量浓度为0.01~0.03g/L,同时加入质量浓度为0.05~0.10g/L的乙酸叔丁酯,辛烷值可增加4.5~6.0个单位。
此外,目前也有报道,采用二茂铁、聚异丁烯基丁二酰亚胺、聚异丁烯钡盐等可组成一种具有抗爆功能、无毒,安全、稳定性好的无铅汽油抗爆添加剂。
该添加剂用量小、成本低、使用方便。
2.有机无灰类抗爆剂
1)醚类
包括甲基叔丁基醚(MTBE)、甲基叔戊基醚(TAME)、乙基叔丁基醚(ETBE)、二异丙基醚(DIPE)等。
醚类是提高辛烷值最好的品种,它们具有高辛烷值、低蒸汽压和高燃烧热等突出优点,同时具有优异的燃料相容性和发动机性能,因而其用量不断增长。
其中MTBE性能最好,当添加质量分数为2%~7%时可将汽油研究法辛烷值提高2~3个单位。
MTBE的物理性质与汽油烃类相差不大,与汽油的混溶性好,可以以任何比例与汽油混溶而不发生相分离。
MTBE还具有改善燃烧室清洁度和减少发动机磨损等特点。
虽然MTBE有很多优点,但近年来出现了争议。
问题的根源是人们发现MTBE容易对地下水造成污染,由此可能带来的对人体健康的危害。
美国加利福尼亚州已于2003年1月l日起禁止MTBE的使用。
2)醇类
包括甲醇、乙醇、丙醇、异丙醇、丁醇、异丁醇、叔丁醇等,应用较广的是乙醇和甲醇。
车用乙醇汽油是指在不添加含氧化合物的液体烃类中加入一定量变性燃料乙醇和为改善使用性能的添加剂,用于点燃式内燃机汽车的燃料。
变性燃料乙醇是以淀粉质、糖质为原料,经发酵、蒸馏制得乙醇,脱水后再添加变性剂变性的燃料乙醇。
《变性燃料乙醇国家标准》规定燃料乙醇与变性剂的体积混合比应为100:
2~100:
5(与美国标准规定相同),水分含量不大于0.8%,标准中还规定了甲醇、实际胶质、无机氯、酸度、铜等的限量指标,目的是防止车用乙醇汽油在发动机燃烧过程中腐蚀金属部件及堵塞管路系统。
按照我国的国家标准,乙醇汽油是用90%(上下幅度不超过0.5%)的普通汽油与10%的变性燃料乙醇调和而成。
在汽油标号前加写字母“E”作为车用乙醇汽油的标号,它的标号有四种,即:
E90#、E93#、E95#、E97#,E后的数字代表辛烷值。
目前推广使用的乙醇汽油标号为E90#和E93#,E95#和E97#将逐步推广应用。
乙醇汽油作为一种新型清洁燃料,是目前世界上可再生能源的发展重点,符合我国能源替代战略和可再生能源发展方向,它可以有效改善油品的性能和质量,降低一氧化碳、碳氢化合物等主要污染物排放。
乙醇的饱和蒸汽压、闪点、燃烧热值、水溶性等与汽油之间存在一定差异,将乙醇加入汽油中,比例不当会对发动机、油品存储及消防安全等产生某些负面影响。
乙醇目前的主要生产原料为粮食,价格比汽油高,生产燃料乙醇时会排放大量废水,这些都是影响乙醇作为车用汽油调和组分的障碍。
甲醇作为汽油替代燃料在20世纪80年代已得到国际公认。
通常按汽油中的甲醇含量将甲醇汽油分为低醇(M3~5)、中醇(M15~30)和高醇(M85~100)三类,其中M后的数字代表甲醇体积分数。
低醇(M3~5)汽油:
当甲醇含量≤3%时,甲醇溶于汽油,欧洲规定可与一般汽油通用,甲醇可不标识;当甲醇含量>3%时,应标明甲醇含量。
甲醇在汽油中的溶解性与温度、含水量及基础汽油的组成有关,为保证甲醇与汽油全部混溶,要适当添加助溶剂。
使用低醇与中醇汽油时,发动机可以不做改动。
中醇(M15~30)汽油:
由于甲醇含量高,必需添加助溶剂。
高醇(M85~100)汽油:
必需对发动机进行改造,充分提高压缩比,以发挥甲醇的优点,降低甲醇消耗。
高醇汽油与汽油不能通用。
甲醇燃料与汽油相比优点是:
甲醇的辛烷值高,理论上可以提高汽油机的压缩比;甲醇的点火温度和自燃温度都比汽油高,燃烧过程比汽油更安全;甲醇燃料富含氧,这使甲醇完全燃烧时所需要的空气量较少,燃烧比汽油彻底,尾气中HC、CO及NOx含量可显著降低。
缺点是:
甲醇含有50%的氧,导致甲醇的燃烧热值较低;甲醇的气化潜热大,冷起动较汽油困难;甲醇的饱和蒸气压和沸点都较低,易形成气阻;甲醇是极性有机溶剂,易使橡胶和塑料零部件发生溶涨,提前老化,对某些有色金属具有腐蚀作用;甲醇对人体有较强的毒害作用。
要克服甲醇燃料的缺点,需对汽车发动机的点火装置和其它零部件作适当改进,同时要对燃料供给系统做严格密封处理。
3)酯类
包括碳酸二甲酯(DMC)、三甲基硅烷基乙酸叔丁酯、聚氧乙烯醚二羧酸酯等;其中碳酸二甲酯最受关注,被认为是最具发展前途的辛烷值改进剂。
研究表明,加入DMC后,对汽油的饱和蒸汽压、冰点和水溶性影响不大。
和MTBE相比,DMC的含氧量高,汽油中达到同样氧含量时,DMC的添加体积只有MTBE的40%左右。
碳酸酯类化合物制备比较容易,一般都是采用醇类与一氧化碳反应制得。
例如碳酸二甲酯可用甲醇在催化剂甲氧基氯化酮以及促进剂三乙基苯甲基季胺盐酸盐存在下,与CO共同反应而制得。
反应温度控制在90℃,氮气分压维持为0.69MPa,CO分压为3.4MPa,反应时间5h。
用过的催化剂可通入空气鼓泡给以再生。
四.高辛烷值汽油组分的生产原料
在炼油厂中,利用炼厂气或轻质石脑油通过叠合、烷基化、异构化、醚化工艺制得的叠合汽油、烷基化汽油、工业异辛烷、异戊烷、MTBE等组分都是高辛烷值汽油组分,调入汽油中,不仅增加了汽油的产量,也可大大提高汽油的辛烷值。
炼厂气是指炼油厂各加工装置所有生产气体的总和,一般约占原油加工量的5~10%。
炼油厂中产气较多的装置有:
热裂化、焦化、减粘裂化、重整、催化裂化等加工过程。
因各装置的加工任务不同,操作条件各异,故所产气体的组成和收率也不一样。
但总的来说都是C1~C4的低分子烃类,并且含有相当数量的烯烃,特别是催化裂化所产富气,其中C3、C4烃占气体总量的70%以上,而且烯烃含量很高,一般都通过吸收、稳定系统与干气分离开来,称为液态烃,它是生产高辛烷值汽油组分及石油化工产品极为宝贵的原料。
轻质石脑油的主要来源是重整预分馏所得小于C6的组分,一般为60℃以前的轻汽油,约占重整原料的5~15%,还有重整油芳烃抽提的抽余油、焦化石脑油以及天然气凝析油等。
从技术和经济角度考虑,利用炼厂气中的液态烃生产高辛烷值汽油组分较为适宜。
第二节炼厂气的精制与分馏
炼厂气在使用和加工前须根据加工过程的特点和要求,进行不同程度的脱硫和干燥,称为气体精制,之后还要根据进一步加工它们的工艺过程对气体原料纯度的要求,进行分离得到单体烃或各种气体烃馏分。
一.气体精制
加工含硫原料时,炼厂气中常含有H2S、CO2和有机硫化物。
如以这样的含硫气体作为高辛烷值组分的生产原料,就会引起设备腐蚀、催化剂中毒、污染大气,并且还会影响产品质量等。
因此,必须将这些含硫气体进行脱硫后才能使用。
由于脱H2S的同时也能脱去CO2,所以气体精制的主要目的即脱硫。
1.无机小分子酸性气体的脱除
脱H2S、CO2等无机小分子酸性气体的途径有多种,我国炼厂气绝大多数采用醇胺溶液湿法脱硫的方法。
醇氨溶液由醇胺和水组成。
所使用的醇胺有一乙醇胺(MEA)、二乙醇胺(DEA)、二异丙醇胺(DIPA)、甲基二乙醇胺(MDEA)等。
醇胺类化合物中至少含有一个羟基和一个胺基。
羟基的作用是降低化合物的蒸汽压,并增加在水中的溶解度,而胺基则为水溶液提供必要的碱度,促进对酸性组分的吸收。
醇胺可分为伯醇胺、仲醇胺和叔醇胺三类。
H2S及CO2在醇胺溶液中依靠与醇胺的反应从石油气体中脱除,以伯醇胺为例,其发生的主要反应如下:
RNH2+H2S
RNH3HS
RNH2+CO2+H2O
RNH3HCO3
这类方法是以可逆的化学反应为基础,以碱性溶剂为吸收剂的脱硫方法,溶剂与原料气中的酸性组分(主要是H2S和CO2)反应而生成某种化合物;吸收了酸气的富液在升高温度、降低压力的条件下,该化合物又能分解而放出酸气。
图7.2.1是醇胺法脱硫的工艺流程,包括吸收和解吸(即再生)两部分。
1)吸收部分
含硫气体冷却至40℃以下,并在气液分离器内分出水和杂质后,进入吸收塔的下部,与自塔上部引入的温度为40℃左右的醇胺溶液(贫液)逆向接触,吸收气体中的H2S、CO2等。
脱硫后的气体自塔顶引出,进入分离器,分出携带的醇胺液后出装置。
2)溶液解吸部分
吸收塔底出来的醇胺溶液(富液)经换热后进人解吸塔上部,在塔内与下部上升的蒸气(由塔底重沸器产生)直接接触,将溶液中吸收的气体大部分解吸出来,从塔顶排出。
再生后的醇胺溶液从塔底引出,部分进人重沸器被水蒸气加热气化后返回解吸塔,部分经换热、冷却后送到吸收塔上部循环使用。
解吸塔顶出来的酸性气体经冷凝、冷却、分液后送往硫磺回收装置。
2.硫醇的脱除
原料中硫含量不太高时,醇胺法能脱除气体中大部分的无机硫,但对有机硫化物脱出效果较差。
液化气中的硫化物主要是有机硫化物,且以硫醇为主,可用化学或吸附的方法予以除去,其中化学方法主要是催化氧化法脱硫醇,即把催化剂分散到碱液(氢氧化钠)中,将含硫醇的液化气与碱液接触,其中的硫醇与碱反应生成硫醇钠盐,然后将其分出并氧化为二硫化物。
所用的催化剂为磺化酞菁钴或聚酞菁钴。
醇胺法粗脱后的液化气引入到车间液化气脱硫醇单元,通过与含有催化剂磺化钛菁钴的碱液在静态混合器(或抽提塔)中充分接触,液化气中的硫醇与NaOH在催化剂的作用下发生反应,变成硫醇钠溶于碱液中,从而达到了脱硫醇的目的,反应式如下:
RSH+NaOH
RSNa+H2O
在再生系统中,向含有硫醇钠的催化剂碱液通入压缩空气,在催化剂的作用下,在氧化塔内发生氧化反应,生成二硫化物和碱,二硫化物不溶于碱液中,可定期排掉,从而使碱液得以再生并循环使用反应式如下:
4RSNa+O2+2H2O→2RSSR+4NaOH
图7.2.2是液化气脱硫醇的工艺流程图,包括抽提、氧化和分离三部分。
1)抽提
经碱或乙醇胺洗涤脱除硫化氢后的液化气进入抽提塔下部,在塔内与带催化剂的碱液逆流接触,在小于40℃和1.37MPa的条件下,硫醇被碱液抽提。
脱去硫醇后的液化气与新鲜水在混合器混合,洗去残存的碱液并至沉降罐与水分离后出装置。
所用碱液的浓度一般为10%~15%,催化剂在碱液中的浓度为100~200ppm。
2)氧化
从抽提塔底出来的碱液,经加热器被蒸汽加热到65℃左右,与一定比例的空气混合后,进入氧化塔的下部。
此塔为一填料塔,在0.6MPa压力下操作,将硫醇钠盐氧化为二硫化物。
3)分离
氧化后的气液混合物进入分离器的分离柱中部,气体通过上部的破沫网除去雾滴,由废气管去火炬。
液体在分离器中分为两相,上层为二硫化物,用泵定期送出,下层的再生碱液用泵抽出送往抽提塔循环使用。
液化气催化氧化脱硫醇的效果一般在95%左右,好的能达98%以上。
二.气体分馏
1.气体分馏的基本原理
炼厂液化气中的主要成分是C3、C4的烷烃和烯烃,即丙烷、丙烯、丁烷、丁烯等,这些烃的沸点很低,如丙烷的沸点是一42.07℃,丁烷为一0.5℃,异丁烯为一6.9℃,在常温常压下均为气体,但在一定的压力下(2.0MPa以上)可呈液态。
由于它们的沸点不同,可利用精馏的方法将其进行分离。
所以气体分馏是在几个精馏塔中进行的。
由于各个气体烃之间的沸点差别很小,如丙烯的沸点为一47.7℃,比丙烷低4.6℃,所以要将它们单独分出,就必须采用塔板数很多(一般几十、甚至上百)、分馏精确度较高的精馏塔。
2.气体分馏的工艺流程
气体分馏装置中的精馏塔一般为三个或四个,少数为五个,实际中可根据生产需要确定精馏塔的个数。
一般地,如要将气体分离为n个单体烃或馏分,则需要精馏塔的个数为n-1。
现以五塔为例来说明气体分馏的工艺流程见图7.2.3。
图7.2.3气体分馏装置工艺流程图
1-脱丙烷塔;2-脱乙烷塔;3-脱丙烯塔(下段);
4-脱丙烯塔(上段);5-脱异丁塔;6-脱戊烷塔
①经脱硫后的液化气用泵打入脱丙烷塔,在一定的压力下分离成乙烷一丙烷和丁烷一戊烷两个馏分。
②自脱丙烷塔顶引出的乙烷一丙烷馏分经冷凝冷却后,部分作为脱丙烷塔顶的冷回流,其余进入脱乙烷塔,在一定的压力下进行分离,塔顶分出乙烷馏分,塔底为丙烷一丙烯馏分。
③将丙烷一丙烯馏分送入脱丙烯塔,在压力下进行分离,塔顶分出丙烯馏分,塔底为丙烷。
④从脱丙烷塔底出来的丁烷一戊烷馏分进入脱异丁烷塔进行分离,塔顶分出轻C4馏分,其主要成分是异丁烷、异丁烯、1一丁烯等;塔底为脱异丁烷馏分。
⑤脱异丁烷馏分在脱戊烷塔中进行分离,塔顶为重C4馏分,主要为2一丁烯和正丁烷;塔底为戊烷馏分。
以上流程中,每个精馏塔底都有重沸器供给热量,塔顶有冷回流,所以都是完整的精馏塔。
分馏塔板一般均采用浮阀塔板。
操作温度均不高,一般在55~110℃范围内;操作压力视塔不同而异,一般地,脱丙烷塔、脱乙烷塔和脱丙烯塔的压力为2.0~2.2MPa,脱丁烷塔和脱戊烷塔的压力0.5~0.7MPa。
液化气经气体分馏装置分出的产品有以下几种:
丙烯:
纯度达99%以上,可以生产聚合级丙烯或作为叠合装置原料等;
丙烷:
纯度96%,可做丙烷脱沥青的溶剂;
轻C4馏分:
纯度99.88%,可做烷基化、甲基叔丁基醚装置原料;
重C4馏分:
纯度99.91%,可做烷基化原料;
戊烷馏分:
C5烷烃与烯烃的混合物,纯度95%,可做裂解原料或掺入车用汽油。
第三节烷基化
一.概述
异丁烷与小分子烯烃生成的烷基化油为C5~C9的异构烷烃混合物,其中以富含各种三甲基戊烷的C8为主要成分,是理想的高辛烷值清洁汽油组分。
烷基化油具有以下特点:
①辛烷值高(其RON可达96,MON可达94,在内燃机中燃烧后,排气烟雾少,不引起爆震,是清洁汽油理想的高辛烷值调合组分;②不含烯烃、芳烃,硫含量也很低,将烷基化汽油调入汽油中通过稀释作用可以降低汽油中的烯烃、芳烃、硫等有害组分的含量;③蒸气压较低。
④烷基化油几乎完全是由饱和的分支链烷烃所组成,因此还可以用烷基化油作成各种溶剂油使用。
正是由于烷基化汽油的各种优点,使得烷基化工艺蓬勃发展。
烷基化油生产的发展开始于二次世界大战期间,用于生产航空汽油,但当时数量不大。
烷基化包括直接烷基化与间接烷基化(拟烷基化)两种反应形式及工艺技术。
直接烷基化是指异丁烷和丁烯在强酸催化剂的作用下发生烷基化反应生成烷基化油的过程。
在传统液体酸烷基化工艺中,可以按所用催化剂分为硫酸烷基化和氢氟酸烷基化工艺。
由于腐蚀和环保问题,寻求一种固体酸催化剂替代硫酸和氢氟酸生产烷基化油就成了炼油工业的热门课题。
二.异丁烷与小分子烯烃的烷基化反应
乙烯烷基化所用的催化剂是氯化铝的有机络合物,硫酸和氟氢酸对异构烷和乙烯的烷基化反应没有催化作用。
丙烯在使用无水氯化铝、硫酸和氟氢酸催化剂时与异丁烷反应,主要生成2,3-二甲基戊烷,RON为91,使用这三种催化剂时的产物收率分别为92%、50%和35%。
1-丁烯与异丁烷烷基化时,如使用硫酸和氟氢酸催化剂,则1-丁烯首先异构化生成2-丁烯,然后再与异丁烷发生烷基化反应。
在无水氧化铝、硫酸或氟氢酸的催化作用下,2-丁烯与异丁烷烷基化主要生成高辛烷值的2,2,4-三甲基戊烷、2,3,4-三甲基戊烷和2,3,3-三甲基戊烷(RON100~106)。
异丁烯和异丁烷烷基化反应生成辛烷值为100的2,2,4一三甲基戊烷,即俗称的异辛烷。
实际上,除上述一次反应产物外,在过于苛刻的反应条件下,一次反应产物和原料还可以发生裂化、叠合、异构化、歧化和自身烷基化等副反应,生成低沸点和高沸点的副产物以及酯类(酸渣)和酸油等。
三.烷基化原料及要求
1.烷基化原料
以生产车用汽油、航空汽油为目的的烷基化工艺,使用两类原料,第一类原料是异构烷烃,由于烷基化反应遵循正碳离子机理,要求烷烃具有叔碳原子,所以只能在≥C4的烷烃中寻找,因为≥C5的烷烃已经是汽油组分,且它们的烷基化产物辛烷值提高不大,甚至还会下降,故烷基化原料的异构烷烃均选择异丁烷。
另一类原料是小分子烯烃,包括丙烯、丁烯和戊烯。
丁烯是最好的烷基化原料,产品质量最好,酸耗也最低,丙烯和戊烯的酸耗几乎是丁烯的几倍。
近年来由于通过丙烯二聚生产高辛烷值调合组分(叠合汽油)得到较快的发展,因此选择丙烯做烷基化原料的做法越来越少,至于戊烯其本身就可做为马达燃料组分,几乎没人把它做为烷基化原料,因此烷基化烯烃的原料最主要的是丁烯,它包括4种异构体:
异丁烯、1-丁烯、顺-2-丁烯和反-2-丁烯。
小分子烯烃更多的是以不同比例烯烃混合物的形成出现。
不同的丁烯异构体的烷基化反应结果也不尽相同。
以氢氟酸为催化剂时,2-丁烯烷基化产品的辛烷值最高,异丁烯烷基化产品的辛烷值次之,1-丁烯烷基化产品的辛烷值最低。
以硫酸为催化剂时,1-丁烯所得烷基化油的辛烷值还稍高于2-丁烯和异丁烯烷基化产品的辛烷值。
2.烷基化原料中的杂质
烷基化原料的质量不仅关系到烷基化装置的产品质量和收率,而且关系到装置的安全平稳操作。
要确保烷基化原料的质量,就要建立一个包括一系列烷基化的上游装置在内的质量保证体系。
烷基化装置的原料主要来自催化裂化装置生产的液化气。
在烷基化装置开工前,要确认催化裂化装置的操作处于平稳状态。
如果催化裂化装置操作不正常,则烷基化原料的质量将无法保证,就应当停止烷基化原料进入装置,使装置处于循环状态。
烷基化原料中的杂质有以下几种:
1)乙烯
如果催化裂化液化气中混入一定量的干气,而气体分馏装置也未能很好地除去C2组分时,乙烯就可能进人烷基化装置。
当乙烯进人烷基化反应器时,乙烯与硫酸反应生成呈弱酸性的硫酸氢乙酯,而不是发生