MPSMRP实验报告.docx
《MPSMRP实验报告.docx》由会员分享,可在线阅读,更多相关《MPSMRP实验报告.docx(33页珍藏版)》请在冰豆网上搜索。
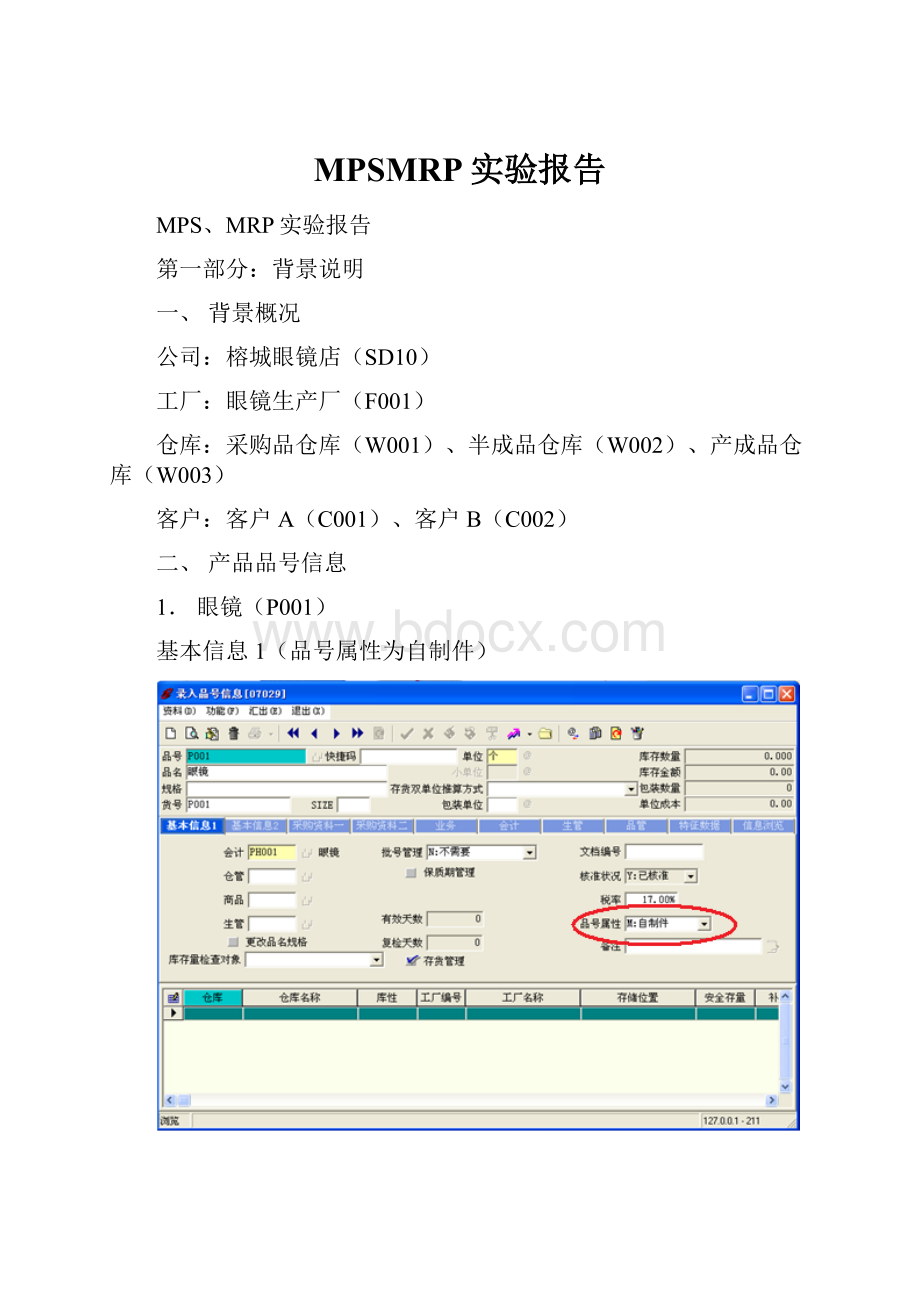
MPSMRP实验报告
MPS、MRP实验报告
第一部分:
背景说明
一、背景概况
公司:
榕城眼镜店(SD10)
工厂:
眼镜生产厂(F001)
仓库:
采购品仓库(W001)、半成品仓库(W002)、产成品仓库(W003)
客户:
客户A(C001)、客户B(C002)
二、产品品号信息
1.眼镜(P001)
基本信息1(品号属性为自制件)
基本信息2:
(请将低阶码初始值设置为00,否则计算低阶码会不正确)
采购资料一:
(
),在进行MRP时,补货政策应选择“M:
按MRP需求”)
生管:
(每日排程量是“排程批量”的整倍数,最后一个排程日除外,在进行MPS时,应勾选MPS件,“排程批量”应小于MPS系统品号资源信息模块中的产能限制)
品管:
(检验方式及检验天数将会对主生产排程结果产生影响)
2.框架(P002)
基本信息1:
自制品;
基本信息2:
低阶码初始值为00;
采购资料一:
固定前置天数和变动前置天数为1,批量为100;
生管:
MPS件,排程批量为100;
品管:
检验方式为免检,检验天数为0
注:
截图与“眼镜”相似,略
3.托架(P003)
基本信息1(品号属性为采购件)
基本信息2:
(请将低阶码初始值设置为00,否则计算低阶码会不正确)
采购资料一:
(
)
品管:
(检验方式及检验天数将会对主生产排程结果产生影响)
4.螺丝(P004)
基本信息1:
采购品;
基本信息2:
低阶码初始值为00;
采购资料一:
固定前置天数和变动前置天数为1,批量为1000;
品管:
检验方式为免检,检验天数为0
注:
截图与“托架”相似,略
5.镜片(P005)
基本信息1:
采购品;
基本信息2:
低阶码初始值为00;
采购资料一:
固定前置天数和变动前置天数为1,批量为100;
品管:
检验方式为免检,检验天数为0
注:
截图与“托架”相似,略
三、产品结构信息
说明:
1个眼镜由1个框架和2个镜片组成;其中1个框架由1个托架和6个螺丝组成。
四、订单信息
1.订单1
说明:
“订单日期”为2009-04-02,“订单数量”为500个,“预交货日”为2009-05-06,注意审核。
2.订单2
说明:
“订单日期”为2009-04-22,“订单数量”为1000个,“预交货日”为2009-05-20,注意审核。
五、工单信息
说明:
这个“工单”的数量是300个,预计开工为2009-04-16,预计完工为2009-04-22,实际开工为2009-04-16.因为这个是“框架”的工单,所以根据产品结构,“托架”和“螺丝”的需求量为300与1800个。
六、采购单信息
说明:
这个采购单的日期是2009-04-01,采购的“镜片”是1000个,预交货日为2009-04-15日。
第二部分:
主生产排程计划MPS
一、设置MPS参数
说明:
设置为有限产能,批量分摊
二、录入资源信息
说明:
“每日产能”规定了每日最大生产能力。
三、录入品号资源信息
1.眼镜耗用人力信息
说明:
“MPS件”和“排程批量”在“品号信息-生管”中设置;“每日标准产能”和“每日最大产能”在“资源信息”中设置;耗用批量:
变动耗用为1:
1,表明生产1单位眼镜耗用1单位人力。
具体结果如下:
2.框架耗用人力信息
说明:
“MPS件”和“排程批量”在“品号信息-生管”中设置;“每日标准产能”和“每日最大产能”在“资源信息”中设置;耗用批量:
变动耗用为0.5:
1,表明生产1单位框架耗用0.5单位人力。
具体结果如下:
四、生成每日资源信息
说明:
生成每日资源,起始日期必须早于订单日期,截止日期必须晚于预交货日。
具体结果如下:
五、录入每日资源
说明:
查看或修改每日资源信息。
具体结果如下:
六、录入排程来源
说明:
“来源单别”用于选择排程所依据的订单,这里选择订单20090402001,即2009-04-02产生的订单。
具体结果如下:
七、生成排程计划
说明:
“排程起始日期”将决定主排程计划MPS的开始日期。
注意将“计算损耗率”“需求日期后的供给纳入计算”“需求日期后其他需求纳入计算”勾掉,以免影响排程结果。
具体结果如下:
八、维护排程计划
分析:
由上面的排程结果可以看出,因为“框架”的低阶码(01)比“眼镜”的低阶码(00)大,所以它要先进行排程。
框架生产结束时间为2009-04-03,眼镜生产开始时间为2009-04-06,中间两天为周末。
其中,我们的这个排程由2009-04-01开始,这是因为我们在“生产排程计划”中将“排程起始日期”设置为2009-04-01。
排程所依据的订单的需求量为500个眼镜,再根据BOM表中眼镜与框架的比例关系,知道框架的需求量也是500个。
。
在“品号资源信息”中,框架的耗用批量:
变动耗用=1:
0.5,因此框架的每日最大产量为200(即100*1/0.5=200);在“品号资源信息”中,眼镜的耗用批量:
变动耗用=1:
1,因此框架的每日最大产量为100(即100*1/1=100)。
注:
每日最大产量是排程批量的整数倍,最后一个排程日除外。
第三部分:
物料需求计划MRP(依MPS与不依MPS)
一、设置MRP参数
说明:
设置“采购计划发放目的”为“采购单”,设置“补货政策”为“按MRP需求”。
具体结果如下:
二、设置计划条件
说明:
设置“使用间距方式”为“1:
日”。
具体结果如下:
生成物料需求计划(不依MPS)
说明:
按照上面的设置完成后,进入“生成物料需求计划”页面,不要对“依MPS计划生成”打勾。
然后接着选择主件品号;合理选择计划日期,以便观测所有数据变化。
例如:
选择计划日期起始为2009-04-01,而有一个产品的计划采购日为2008-12-31,那么将无法在最后的采购计划中看到结果;将“十三类数量为零且采购/生产数为零者清除”勾选掉。
具体结果如下:
1、维护生产计划
说明:
维护生产计划,查看结果,分析如下。
参考公式:
预计销货量=未结束订单的未销数量
计划销售量=未达成的销售预测量
预计生产量=未完工工单单头的未生产量
计划生产量=生产计划内的预计生量
预计可用=期初存量+预计生产+计划生产-预计领用-计划领用-预计销售-计划销售
生产数量=安全存量-预计可用(安全存量-预计可用<0,则生产数量=0)
Ø对于“眼镜”的生产计划,描述、分析以及图表如下:
描述:
“间距日期”2009-05-06时“生产数量”为500,“预计可用”为-500,“开工日”为2009-04-27,“实际供需日期”为2009-05-05,“期初库存”为0,“预计生产”为0,“计划生产”为0,“预计销售”为500,“计划销售”为0。
分析:
由于在2009-04-01下了一张眼镜订单,预交货日为2009-05-06,因此“实际供需日期”为2009-05-05(应在订单交货日期前一天完工);又因为生产提前期为6天(即:
生产量500*变动前置天数1/批量100+固定前置天数1=6),所以“开工日”为2009-04-27(其中,包含1个周末);订单数量为500,因此“预计销售”为500;没有进行销售预测,所以“计划销售”为0;没有眼镜工单,所以“预计生产”为0,“计划生产”为0;由于眼镜是产成品,因此不需要被领用,所以“预计领用”和“计划领用”为0;由于当前没有眼镜库存,因此“期初存量”为0;我们在仓库中设定“安全库存”为0;综上,“预计可用”为-500(即:
期初存量0+预计生产0+计划生产0-预计领用0-计划领用0-预计销售500-计划销售0=-500);“生产数量”为500(即:
安全存量0-预计可用-500=500)。
同理:
对于“间距日期”2009-05-20时的情形同上。
Ø对于“框架”的生产计划,描述、分析以及图表如下:
描述1:
“间距日期”2009-04-23时“生产数量”为0,“预计可用”为300,“开工日”为2009-04-17,“实际供需日期”为2009-04-22,“期初库存”为0,“预计生产”为300,“计划生产”为0,“预计领用”为0,“计划领用”为0。
分析1:
由于在2009-04-15下了一张框架工单,预计完工日为2009-04-22,因此“实际供需日期”为2009-04-22;又因为生产提前期为4天(即:
生产量300*变动前置天数1/批量100+固定前置天数1=4),所以“开工日”为2009-04-16(其中,包含1个周末);工单数量为300,因此“预计生产”为300,“计划生产”为0;无眼镜工单,因此“预计领用”为0;这一间距日期内,还没开始眼镜的生产,因此“计划领用”为0;由于框架是半成品,因此不需要被销售,所以“预计销售”为0,“计划销售”为0;由于当前没有框架库存,因此“期初存量”为0;我们在仓库中设定“安全库存”为0;综上,“预计可用”为300(即:
期初存量0+预计生产300+计划生产0-预计领用0-计划领用0-预计销售0-计划销售0=300);“生产数量”为0(安全存量0-预计可用300<0)。
此后一段时间内的期初存量变为300,直到下一次领用。
描述2:
“间距日期”2009-04-27时“生产数量”为200,“预计可用”为-200,“开工日”为2009-04-21,“实际供需日期”为2009-04-24,“期初库存”为300,“预计生产”为0,“计划生产”为0,“预计领用”为0,“计划领用”为500。
分析2:
为满足2009-04-01的眼镜订单,眼镜应在2009-04-27开工,因此框架应在2009-04-24完成(其中,包含1个周末),因此“实际供需日期”为2009-04-24;订单数量为500,因此要生产500个眼镜,由BOM表知需要500个框架,因此“计划领用”为500;这一阶段没有需要领用框架的工单,因此“预计领用”为0,“计划生产”为0,“预计生产”为0;由于框架是半成品,因此不需要被销售,所以“预计销售”为0,“计划销售”为0;此时的“期初存量”为300;我们在仓库中设定“安全库存”为0;综上,“预计可用”为-200(即:
期初存量300+预计生产0+计划生产0-预计领用0-计划领用500-预计销售0-计划销售0=-200);“生产数量”为200(即:
安全存量0-预计可用-200=200)。
同理:
对于“间距日期”2009-05-04时的情形同上。
2、维护采购计划
说明:
维护采购计划,查看结果,分析如下。
参考公式:
预计进货量=未结束采购单的未进货量
计划采购量=采购计划内的预计采购量
预计领料量=未完工工单单身的应领未领料量
计划领料量=相依需求的需求量
预计可用=期初存量+预计进货+计划采购-预计领用-计划领用
采购数量=安全存量-预计可用
Ø对于“托架”的采购计划,描述、分析以及图表如下:
描述1:
“间距日期”2009-04-01时“采购数量”为300,“预计可用”为-300,“采购日”为2009-03-25,“实际供需日期”为2009-03-31,“期初库存”为-300,“预计进货”为0,“计划采购”为0,“预计领用”为0,“计划领用”为0。
分析1:
采购日为3月25日,实际供需为3月31,因为采购的提前期为4天,(300*1/100+1=4),中间有个周末。
这是由300个数量的框架工单所产生的,显示“期初库存”为-300。
因为这个时候没有订单,所以“计划领用”为0,因为这一阶段没有需要领用托架的工单,所以“预计领用”为0。
因为这时没有未结束的采购单,所以“预计进货”为0;而且没有对采购量做出预计,所以“计划采购”为0;结合上面的数据可以知道,“预计可用”为-300(即:
期初存量-300+预计进货0+计划采购0-预计领用0-计划领用0=-300);“采购数量”为300(安全存量0-预计可用-300=300).
描述2:
“间距日期”2009-04-16时“采购数量”为1000,“预计可用”为-1000,“采购日”为2009-03-31,“实际供需日期”为2009-04-15,“期初库存”为0,“预计进货”为0,“计划采购”为0,“预计领用”为0,“计划领用”为1000。
分析2:
由上面对框架的“生产计划”的分析,可以推出为了满足订单2(即5月20日交货),托架的采购完工日(实际供需日期)应该是2009-04-15(因为“框架”要在5月1日生产完成,它的生产提前天数为11天,所以“框架”要在4月16日开始生产,也就是说在4月15日时,生产“框架”的原料—托架和螺丝要采购完成)。
因为“托架”的采购提前期为11天(1000*1/100+1=11)。
所以采购日为3月31日。
生产计划为1000个,所以“计划领用”为1000,因为这一阶段没有需要领用托架的工单,所以“预计领用”为0。
因为这时没有未结束的采购单,所以“预计进货”为0;而且没有对采购量做出预计,所以“计划采购”为0;因为上一阶段已经把库存中的量都用来完成工单的生产了,所以这阶段的“期初存量”为0;结合上面的数据可以知道,“预计可用”为-1000(即:
期初存量0+预计进货0+计划采购0-预计领用0-计划领用1000=-1000);“采购数量”为1000(安全存量0-预计可用-1000=1000).
描述3:
“间距日期”2009-04-21时“采购数量”为200,“预计可用”为-200,“采购日”为2009-04-15,“实际供需日期”为2009-04-20,“期初库存”为0,“预计进货”为0,“计划采购”为0,“预计领用”为0,“计划领用”为200。
分析3:
由上面对框架的“生产计划”的分析,可以推出为了满足订单1(即5月6日交货),托架的采购完工日(实际供需日期)应该是2009-04-20(根据上面的框架的“间距日期”为2009-04-27的生产计划),生产数量为200,所以“计划领用”为200,采购提前期为3天,则采购日为4月15日(包含一个周末)。
因为这一阶段没有需要领用托架的工单,所以“预计领用”为0。
因为这时没有未结束的采购单,所以“预计进货”为0;而且没有对采购量做出预计,所以“计划采购”为0;因为上一阶段以及把库存中的量都用来完成工单的生产了,所以这阶段的“期初存量”为0;结合上面的数据可以知道,“预计可用”为-200(即:
期初存量0+预计进货0+计划采购0-预计领用0-计划领用200=-200);“采购数量”为200(安全存量0-预计可用-200=200).
Ø对于“螺丝”的采购计划,描述、分析以及图表如下:
说明:
“螺丝”的分析过程和“托架”的分析结果类似,这里就不再赘述。
(因为在BOM表中“螺丝”和“托架”是同等地位的,唯一的不同就是数量比为1:
1).
Ø对于“镜片”的采购计划,描述、分析以及图表如下:
描述1:
“间距日期”2009-04-16时“采购数量”为0,“预计可用”为1000,“采购日”为2009-04-15,“实际供需日期”为2009-04-15,“期初库存”为0,“预计进货”为1000,“计划采购”为0,“预计领用”为0,“计划领用”为0。
分析1:
因为有张“预交货日”为4-15的“镜片”的采购单,数量为1000个镜片,所以“预计进货”为1000;但是没有对采购量做出预计,所以“计划采购”为0;这时没有工单或者订单需求“镜片”的,所以“计划领用”为0;因为这一阶段没有需要领用镜片的工单,所以“预计领用”为0;“预计可用”为1000(即:
期初存量0+预计进货1000+计划采购0-预计领用0-计划领用0=1000);“采购数量”为0(安全存量0-预计可用1000=-1000<0,所以为0).根据采购单的“预交货日”,可以知道“实际供需日”为2009-04-15。
因为采购量为0,所以“采购日”和“实际供需日”是同一天。
描述2:
“间距日期”2009-04-27时“采购数量”为0,“预计可用”为0,“采购日”为2009-04-24,“实际供需日期”为2009-04-24,“期初库存”为1000,“预计进货”为0,“计划采购”为0,“预计领用”为0,“计划领用”为1000。
分析2:
因此,到了2009-04-24的时候为了满足订单1,(即“眼镜”数量为500的那张订单),根据BOM表,知道“镜片”需要500*2=1000个。
根据上面的“框架”的实际供需日分析,可以知道“镜片”的“实际供需时期”也为2009-04-24,由于这时库存中已经有了1000个镜片(采购单采购回来的),所以“期初存量”为1000,因此库存量满足需求量,所以就不要再进行采购了,所以系统显示“采购日”为当天。
因为没有未完成的采购单,所以“预计进货”为0;同时没有对采购量做出预计,所以“计划采购”为0;这时有订单需求“镜片”1000个,所以“计划领用”为1000;因为这一阶段没有需要领用镜片的工单,所以“预计领用”为0;“预计可用”为0(即:
期初存量1000+预计进货0+计划采购0-预计领用0-计划领用1000=0);“采购数量”为0(安全存量0-预计可用0=0). 因为采购量为0,所以“采购日”和“实际供需日”是同一天。
同理:
对于“间距日期”2009-05-04时的情形同上。
采购提前期为21天
生成物料需求计划(依MPS)
说明:
在做“依MPS”的MRP计划时,要先把之前做的MRP计划清除掉(到“期末处理”里面清除)。
直接回到“生成物料需求计划”,把“依MPS计划生成”勾起来。
接着选择主件品号;合理选择计划日期,以便观测所有数据变化。
将“十三类数量为零且采购/生产数为零者清除”勾选掉。
具体结果如下:
1、维护生产计划
说明:
查看后发现“生产计划”为空。
因为这个是“依MPS计划”的MRP,在MPS中已经对生产进行排程了,所以这里就没有“生产计划”了。
2、维护采购计划
参考公式:
预计进货量=未结束采购单的未进货量
计划采购量=采购计划内的预计采购量
预计领料量=未完工工单单身的应领未领料量
计划领料量=相依需求的需求量
预计可用=期初存量+预计进货+计划采购-预计领用-计划领用
采购数量=安全存量-预计可用
说明:
因为我们前面在做MPS的时候,只选择了一张订单,所以“依MPS计划”的MRP采购计划中只考虑MPS生产计划的需求,和已有的工单和采购单的需求、供应。
下面是根据MPS产生的MRP采购计划:
Ø对于“镜片”的采购计划,描述、分析以及图表如下:
分析:
在依MPS生产计划生成的MRP采购计划,“采购日”和“实际供需日期”都应该依据MPS“排程起始日期”来计算(跟不依MPS的MRP计算方式不同)。
由上面的“维护排程计划”的结果可以知道,排程从2009-04-01开始,在2009-04-06的时候开始生产眼镜,所以要在2009-04-03时完成镜片的采购(其中有个周末),即“实际供需日期”为2009-04-03。
由于镜片的采购提前期为11天(1000*1/100+1=11),所以“采购日”为2009-03-19(其中有2个周末),又“计划领用”为1000,因此在它之后的“期初存量”为0。
因为有一张“预交货日”为2009-04-15的采购单。
所以在“实际供需日期”为2009-04-15时的“预计进货”为1000个。
因此下一阶段的期初存量为1000。
Ø关于“螺丝”
分析:
因为有300个框架的工单,因此在螺丝和托架的采购计划中,期初库存为满足工单后的库存,-300*6=-1800,为满足MPS计划中的生产,排程从2009-04-01开始,即框架是4月1号开始生产,螺丝的“实际供需日期”为3月31日,计划领用为3000,则预计可用=期初存量+预计进货+计划采购-预计领用-计划领用=-4800,采购数量=安全存量-预计可用=4800,采购提前期为1+4800/1000(取整上限)=5天。
之后的时间里,数量都是0。
Ø关于“托架”
分析:
过程与上面的“螺丝”的采购计划类似。
第四部分:
时间分析
一、MRP物料需求计划(不依MPS)
二、MRP物料需求计划(依MPS)