盐雾试验标准已打印.docx
《盐雾试验标准已打印.docx》由会员分享,可在线阅读,更多相关《盐雾试验标准已打印.docx(18页珍藏版)》请在冰豆网上搜索。
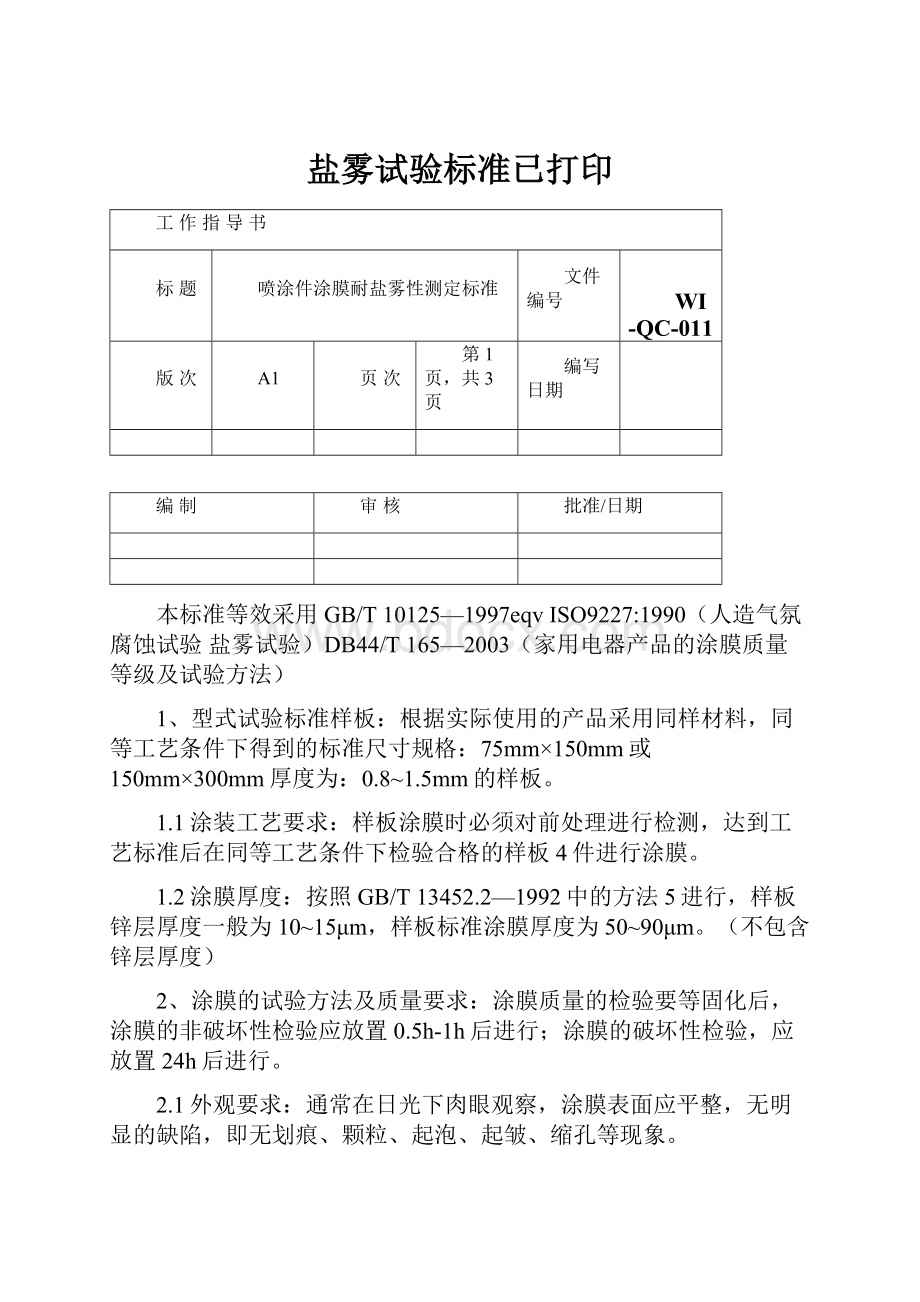
盐雾试验标准已打印
工作指导书
标题
喷涂件涂膜耐盐雾性测定标准
文件编号
WI-QC-011
版次
A1
页次
第1页,共3页
编写日期
编制
审核
批准/日期
本标准等效采用GB/T10125—1997eqvISO9227:
1990(人造气氛腐蚀试验盐雾试验)DB44/T165—2003(家用电器产品的涂膜质量等级及试验方法)
1、型式试验标准样板:
根据实际使用的产品采用同样材料,同等工艺条件下得到的标准尺寸规格:
75mm×150mm或150mm×300mm厚度为:
0.8~1.5mm的样板。
1.1涂装工艺要求:
样板涂膜时必须对前处理进行检测,达到工艺标准后在同等工艺条件下检验合格的样板4件进行涂膜。
1.2涂膜厚度:
按照GB/T13452.2—1992中的方法5进行,样板锌层厚度一般为10~15μm,样板标准涂膜厚度为50~90μm。
(不包含锌层厚度)
2、涂膜的试验方法及质量要求:
涂膜质量的检验要等固化后,涂膜的非破坏性检验应放置0.5h-1h后进行;涂膜的破坏性检验,应放置24h后进行。
2.1外观要求:
通常在日光下肉眼观察,涂膜表面应平整,无明显的缺陷,即无划痕、颗粒、起泡、起皱、缩孔等现象。
2.2光泽度;按照GB/T9754—1988测量涂膜的光泽检验85±5。
2.3色差:
按照GB/T9761—1988及GB/T11186.2—1989、GB/T11186.3—1989进行综合评定,色差:
(△E)△E≤0.8BS。
2.4硬度:
按照GB/T6739—1996测量涂膜的硬度,我司按2级标准评定采用铅笔
硬度≥2H测试。
2.5耐冲击性:
按照GB/T1732—1993,用4倍放大镜正/反面观察受冲击的涂层有无
裂痕、皱纹及剥落等现象,无上述现象既为合格,冲击强度≥50(cm)。
2.6附着力:
按照GB/T9286—1998进行试验和评定,涂膜百格检验应放置0.5h-1h
工作指导书
标题
喷涂件涂膜耐盐雾性测定标准
文件编号
WI-QC-011
版次
A1
页次
第2页,共3页
编写日期
2010/10/08
后进行,标准尺寸规格:
1mm×1mm45~90角,我司按0级标准评定,划格后无脱落。
2.7柔韧性:
按照GB/T6742—1986进行试验和评定,将样板折弯圆弧为φ8mm
之后看样板折弯圆弧处有无裂纹现象,无上述现象既为合格。
3、耐盐雾试验;按照GB/T10125--1997进行试验和评定
3.1GB1266分析纯氯化钠标准溶液。
3.2GB6682三级水(蒸镏水)。
3.3经过PH计测定校正的精密试纸。
3.4喷嘴式盐雾箱;喷雾流量控制在1.5~2.0mL/80cm2/H,压缩空气压力控制在1.0±0.1kga/cm2。
3.5划痕刀和四倍放大镜。
4、测试方法:
4.1用蒸馏水配制氯化钠溶液浓度为50±5g/L,在250C时测定试验溶液的PH值6.5~7.2之间。
超出范围时,可加入盐酸和氢氧化钠溶液进行调整。
4.2样板投入前需对样板进行清洗将表面尘埃、油污清洗干净待自然干燥。
4.3在样板表面必须划一处“X”痕,长度约为50~70mm,夹角为600,划“X”时使用力度要求划到基材为标准。
4.4取样板3件投入试验盐雾试验箱内,一件作为标准样板保存,投试前记录样板的原始状态、生产日期、试验日期。
4.5将试件纵向排放与盐雾沉降方向成300角在喷雾室内,相邻两件试板保持一定的空隙,行间距不少于7.5cm。
工作指导书
标题
喷涂件涂膜耐盐雾性测定标准
文件编号
WI-QC-011
版次
A1
页次
第3页,共3页
编写日期
2010/10/08
4.6开启设备,20分钟后开始试验、喷雾室内温度为35±20C,每隔45分钟喷雾15分钟,连续试验48小时检查一次,看设备是否正常,如正常隔240,360、480小时检查一次,本公司规定500小时为标准试验时间,每次检查后,样板应变换位置,在连续试验过程中,必须经常检查喷嘴,保证喷雾正常,氯化钠溶液不能循环使用。
(注;除在规定时间内检查,其余时间禁止打开盐雾试验箱查看)
5、试验后样板的处理:
5.1试验结束后取出样板,为减少腐蚀产物的脱落,样板在清洗前放在室内自然干燥0.5~1h,然后用温度不高于400C的清洁自来水轻轻清洗以除去样板表面残留的盐雾溶液,再立即吹干。
6、试验结果评定:
6.1划痕“X”处起端及尾端各5mm不纳入检项。
6.2观察涂膜的划痕处腐蚀的蔓延情况,以沿划痕线单边锈蚀、起泡直径≤2mm为合格。
6.3样板锈蚀、起泡局部一点直径≥2mm为合格,3块样板其中2块样板单边锈蚀、起泡均匀直径≥2mm(且去除划痕“X”处起端及尾端各5mm)超过2/3为不合格。
7、试验结果的判定及复试要求:
7.1同样材料,同等工艺条件下打样板4件或抽样三件,按以上标准操作检验。
7.2若三件样板试验后为同一个级别,其中2块样板单边锈蚀、起泡均匀直径≥2mm(且去除划痕“X”处起端及尾端各5mm)超过2/3为不合格。
8、盐雾试验结束后需对盐雾试验机进行清洗,严格按照标准添加溶液。
9、每月对喷粉生产线抽样2批次进行盐雾试验,分别为5号25号对喷涂件进行盐雾试验。
工作指导书
标题
喷涂钣金件磷化膜质量检测标准
文件编号
WI-QC-013
版次
A0
页次
第1页,共2页
编写日期
2010/04/08
编制
审核
批准/日期
1、引用标准:
GB/6807-2001《钢铁工件涂装前磷化处理技术条件》
2、磷化膜外观检测:
2.1磷化后工件的颜色应为(锌系)浅灰色到灰黑色或(铁系)彩色;膜层应结晶致密,连续和均匀。
2.2磷化后的工件具有下列情形或其中之一时,均为允许缺陷:
2.2.1轻微的水迹、钝化痕迹、擦白及挂灰现象。
2.2.2由于局部热处理、焊接以及表面加工状态的不同而造成颜色和结晶不均匀。
2.2.3在焊缝处无磷化膜层。
2.3磷化后工件具有下列情形或其中之一时,均匀不允许缺陷:
2.3.1、疏松的磷化膜层。
2.3.2、有锈蚀或绿斑。
2.3.3、局部无磷化膜(焊接处除外)。
2.3.4、表面严重挂灰。
3.磷化膜重、膜厚:
3.1、用作涂装底层磷化膜膜重为1.1~4.5g/m2,为轻重量级磷化膜。
3.2、磷化膜厚度与膜重换算关系图;
厚度(微米)
膜重g/m2
1
1~2
3
3~6
5
5~15
工作指导书
标题
喷涂钣金件磷化膜质量检测标准
文件编号
WI-QC-013
版次
A0
页次
第2页,共2页
编写日期
2010/04/08
4.外观检验时要根据磷化膜的外观颜色、不允许缺陷及膜重进行验收。
测试膜重采取备制与工件同材料的试板同时前处理的计量方式。
5.磷化膜的耐蚀性:
磷化样件(室温)立即浸入3%的氯化钠(NaCI)水溶液中,在15~250c下,保持1小时后,取出,洗净,吹干,目测磷化表面是否出现锈蚀。
6.检测频数:
6.1自动生产线;外观:
第30分钟抽检一次。
6.2手工生产线;外观:
每框抽检一次。
6.3耐蚀性、膜重,不定时抽检。
工作指导书
标题
喷涂前处理药剂来料检验指导书
文件编号
WI-QC-012
版次
A0
页次
第1页,共6页
编写日期
2010/08/04
编制
审核
批准/日期
1.检验对象、项目和指标
1.1浓流酸
1.1.1供应商每送一批硫酸,品管部均应抽一至三桶作为样件进行测试检验。
1.1.2检验项目和指标:
1)比重:
≥1.83
2)质量百分比浓度:
≥98%
1.1.3比重的测定(比重计法,用1.5-2.0的比重计测):
先将抽样的桶装硫酸振荡混匀,取500ml左右浓硫酸于1000ml烧杯中,将比重计缓缓浸入盛有硫酸的烧杯中,轻轻地松开手,使比重计自立于液面上,静止10分钟,取出比重计,读取液面对应的刻度值,即为比重值。
1.1.4硫酸质量百分比浓度的测定:
在抽样桶中取10ml浓酸于装有一半水的100ml容量瓶中,用水稀释至刻度,摇匀。
用吸量管吸稀释液10ml于250ml锥形瓶中,加水50ml,加酚酞指示剂2-3滴,用0.1mo1.L-1氢氧化钠标准溶液滴定至溶液变为浅红色,即为终点,记下消耗氢氧化钠溶液的体积。
计算:
硫酸(g/l)=CV×0.049×1000
式中,C—氢氧化钠标准溶液的浓度,单位:
mo1.L-1
V—消耗氢氧化钠标准溶液的体积,单位:
ml
工作指导书
标题
喷涂前处理药剂来料检验指导书
文件编号
WI-QC-012
版次
A0
页次
第2页,共6页
编写日期
2010/08/04
查表:
硫酸浓度和比重的关系表
质量百分比溶度(%)
比重
质量浓度(g/l)
90
1.814
1633
92
1.824
1678
94
1.8312
1721
96
1.8335
1762
98
1.8365
1799
备注:
工业硫酸的标准浓度为98%,如检验的硫酸浓度低于94%判不合格。
1.2浓盐酸
1.2.1抽样方法同硫酸。
1.2.2检验项目和指标:
1)比重:
≥1.15.
2)浓度:
≥36%.
1.2.3比重的测定(比重计法,用1-1.5比重计测,方法同硫酸)
1.2.4百分浓度的测定
吸10ml浓盐酸于盛有一半水的100ml的容量瓶中,用水稀至100ml刻度,摇匀。
用移液管吸10ml稀释液于250ml锥形瓶中,加水50ml,加酚酞指示剂2-3滴,用0.1mo1.L-1氢氧化钠标准溶液滴定至溶液变为浅红色,即为终点,记下消耗氢氧化钠标准溶液的体积。
计算:
盐酸(g/l)=CV×0.0365×1000
式中,C—氢氧化钠标准溶液的浓度,单位mo1.L-1
V—消耗氢氧化钠标准溶液的体积,单位ml
工作指导书
标题
喷涂前处理药剂来料检验指导书
文件编号
WI-QC-012
版次
A0
页次
第3页,共6页
编写日期
2010/08/04
查表:
盐酸浓度和比重的关系
质量百分比浓度(%)
比重
质量浓度(g/l)
28
1.139
319.0
30
1.149
344.8
32
1.159
371.0
34
1.169
397.5
36
1.179
424.4
备注:
工业盐酸的标准浓度为36%,如检验的盐酸浓度低于32%判不合格。
1.3除油粉
1.3.1检验项目及指标
项目
C—4A(二线用)
C—16A(手动线用)
C—23(铝材除油用)
外观
白色粉末,不结块
白色稍带黄色粉末,不结块
白色粉末,不结块
5%水溶液的碱度
35±(点)
40±5(点)
15—18(点)
5%水溶液的PH值
12±1
11±1
11±1
1.3.2检验溶液的配制
称取50克除油粉,加800ml水溶解,再加水稀释至1000ml,搅拌均匀,备用。
1.3.3PH值的测定
取一条PH试纸于检验溶液中,取出于空气中静止30秒后,与标准色版对比,读出相应的值。
1.3.4碱度的测定
吸10ml检验溶液于250ml锥形瓶中,加水50ml,加2-3滴酚酞指示剂,用0.1mol.L-1.硫酸标准溶液滴定至红色消失,即为终点,消耗硫酸标准溶液的体积,即为碱度值。
工作指导书
标题
喷涂前处理药剂来料检验指导书
文件编号
WI-QC-012
版次
A0
页次
第4页,共6页
编写日期
2010/08/04
1.4磷化剂
1.4.1检验项目及指标:
1)外观:
浅绿色透明液体,无杂质及沉淀物。
2)比重:
1.35±0.05
3)浓磷化液的总酸度:
700±100(点)
4)浓磷化液的游离酸度:
90±10(点)
1.4.2比重的测定(方法:
用1-1.8比重计测定)
1.4.3磷化剂检验溶液的配制
取10mL磷化液于100ml容量瓶中,用水稀至100ml刻度,摇匀,备用。
1.4.4总酸度的测定
吸10ml检验溶液,加水50ml,加2-3滴酚酞指示剂,用0.1mol.L-1氢氧化钠标准溶液滴定至粉红色,即为终点,所消耗氢氧化钠标准深液的体积V1(mL),则总酸度=10×V1(点)。
1.4.5游离酸度的测定
吸10ml检验溶液,加水50ml,加溴酚蓝指示剂2-3滴,用0.1mol.L-1氢氧化钠标准溶液滴定至蓝紫色,即为终点,所消耗氢氧化钠标准深液的体积V2(ml),则游离酸度=10×V2(点)
1.5铝脱氧剂A1—6
1.5.1检验项目及指标:
1)外观:
乳白色液体,无杂质及沉淀。
2)5%水溶液PH=1
3)游离酸:
1000±100(点)。
工作指导书
标题
喷涂前处理药剂来料检验指导书
文件编号
WI-QC-012
版次
A0
页次
第5页,共6页
编写日期
2010/08/04
1.5.2检验溶液的配制
吸10mlA1-6于100m1容量瓶中,用纯水稀释至100ml刻度,摇匀,备用。
1.5.3游离酸的测定
吸10ml检验溶液于100m1锥形瓶中,加水50m1,加溴酚蓝指示剂2-3滴,用0.1mol.L-1氢氧化钠标准溶液滴定至溶液由黄色变为兰绿色为终点,消耗氢氧化钠标准溶液的体积V为(m1),则游离酸=10×V(点)。
1.6铝黄色铬化剂A1-1
1.6.1检验项目及指标:
1)外观:
棕红色液体。
2)Cr6+含量:
80±20(点)。
3)总酸度:
90±10(点)。
4)游离酸度:
(参考)
1.6.2检验溶液的配制
吸10mlA1—1于100ml容量瓶中,用水稀释至100ml刻度,摇匀备用。
1.6.3Cr6+的测定
吸检验溶液10ml于150ml锥形瓶中,加50ml水,25ml50%的硫酸溶液,加P.A指示剂3-4滴,用0.1mol.L-1硫酸亚铁铵标准溶液滴定至溶液呈亮绿色为终点,消耗硫酸亚铁铵溶液的体积为V(ml),则Cr6+含量为10×V(点)。
1.6.4总酸度的测定
吸10ml检验溶液于150ml锥形瓶中,加50ml水,加酚酞指示剂2-3滴,用0.1mol.L-1氢氧化钠标准溶液滴定至粉红色为终点,消耗氢氧化钠溶液的体积为V,
工作指导书
标题
喷涂前处理药剂来料检验指导书
文件编号
WI-QC-012
版次
A0
页次
第6页,共6页
编写日期
2010/08/04
则总酸度=10×V(点)。
1.6.5游离酸的测定
吸检验溶液10ml于150ml锥形瓶中,加20-30滴溴甲酚绿指示剂,用0.1mol.L-1氢氧化钠标准溶液滴定至黄色变为绿色为终点,消耗氢氧化钠的体积为V,则游离酸度=10×V(点)。
1.7表调剂
1.7.1检验项目及指标:
1%水溶液PH=8-9。
1.7.2称50克表调剂溶于500ml水中,摇匀,静止10分钟。
用一条广泛PH试纸浸于溶液中,取出30秒后与标准色版比较,得出溶液PH。
工作指导书
标题
喷涂产品喷涂操作工艺标准
文件编号
WI-QC-014
版次
A0
页次
第1页,共5页
编写日期
2010/04/08
编制
审核
批准/日期
一、蒂森喷涂工艺;
1、喷涂件以冷轧板为主,在前处理前必须用煤油擦拭(槽钢类除外)。
2、梯级为轧铸铝材料,采取手工擦拭表面油污的方式。
即布或细丝铜刷粘除油液对梯级表面进行擦拭。
要求对喷涂面全部擦拭到位(包括两端弯边)。
然后进行高压清水冲洗后经过炖化处理。
梯级属铝制齿形零件,容易断裂和齿尖变形。
所以在操作时应注意轻搬轻放。
3、蒂森公司梯级,确定7310粉末为合格使用粉末,其他型号银色粉末或另外其他公司粉末不得混合使用。
喷涂时必须对两边扣脚加防粉套,避免上粉。
4、对有折弯边零件:
如门板、立柱、门楣组件、门框、轿顶、地板等零件。
喷涂时为避免固化后折弯边角处出现流挂现象,对喷手的操作要求:
喷内表面折弯边角处时,降低输送空气的气压值,使粉末吐出雾量的大小适当。
把握好喷涂时喷枪与工件的距离和走枪遍数。
为避免粉量太大或走枪遍数太多而沉淀过多粉末一般情况下对折弯边死角位走枪三遍适宜。
在此零件喷涂完毕后,喷手应自检折弯边、死角部位沉淀粉末是否过多,应轻轻吹净后再补喷适量粉末。
补粉部位表面应光滑、平整、洁净。
固化冷却后的零件内表面挂钩处有露底现象,应用天那水调同类型号的粉末进行补粉。
注:
适应手工、流水三线喷涂。
二、KT系列产品喷涂工艺要求;
1、本产品需两面喷涂,正面厚度应保持在50um以上,背面(即贴海棉面)不允许露青,涂膜厚度在35um以上。
工作指导书
标题
喷涂产品喷涂操作工艺标准
文件编号
WI-QC-014
版次
A0
页次
第2页,共5页
编写日期
2010/04/08
2、允许喷回收粉末,但不允许使用潮湿结块,有明显杂粉点的粉末。
3、钣金件有折边夹缝,注意烘烧温度必须在1400CC—1600C,保温时间在15—50分钟以上。
KT系列脱塑件,前处理注意对夹缝重点冲水。
注:
适应手工一线、自动二线和三线喷涂。
三、亚拓公司喷涂产品《放大器》喷涂操作工艺指导;
1、前处理:
铝合金材料。
工序;除油—(15-20分钟)—水洗—铝脱氧(5-10分钟)—水洗—铝皮膜(5-10分钟)—冲水—烘烤(温度140度)。
2、喷涂;适应手工、流水三线喷涂。
2.1备制规范的小铁钩、胶塞、螺杆、夹具等。
2.2上紧螺杆,上严密胶塞,上木塞。
2.3喷盒体时用备制的专用夹具,扣实平稳。
注意木塞与胶塞部位的上粉状态(该部位容易露表)。
2.4喷盖面时摆放在喷台上喷涂。
2.5下胶塞、木塞,挂炉时间不准超过1.5小时。
2.6固化温度:
1900C。
四、KY20底盘如果是脱塑件,前处理前对三个螺杆检查是否松动,松动零件必须重新点焊。
喷粉时按要求喷好零件,后取下螺杆上胶管,用喷枪雾化的外端余粉轻快地喷一层薄粉,厚度不超15um。
注:
适应手工一线、自动二线和三线喷涂。
五、格力产品喷涂工艺指导;
1、28、60等系列焊接打磨零件及格力其他产品,必须在前处理前进行打磨校正,
工作指导书
标题
喷涂产品喷涂操作工艺标准
文件编号
WI-QC-014
版次
A0
页次
第3页,共5页
编写日期
2010/04/08
前处理后不允许用抛光机打磨。
该系列产品根据零件规格、氧化程度分为电泳、酸洗与不酸洗。
前处理操作时按相应类别的《电泳、酸洗工作指导书》进行操作。
2、60上盖、底座、左右侧框内表面焊接、角等处允许补粉。
其他新型号框式类允许补粉零件临时确定。
注:
适应手工一线喷涂。
六、金鹰产品喷涂工艺指导:
金鹰箱体喷涂银白色粉末,外表面必须按30%的新粉与回收粉末配比喷涂,保障涂膜颜色一致。
箱体内部结构复杂,控制好喷枪的出粉量与气量及挂钩的导电性能,挂钩的钩头必须朝内底板,注意回收粉末的沉淀量。
箱体内折弯、角处允许补粉。
注:
只适应于手工一线喷涂。
七、克劳迪喷涂产品操作工艺标准;
1.平型、弧型面板零件存在毛边与压铸锌屑。
前处理时毛边用抛光机打磨平滑,刮净中间四孔多除锌屑及内表面压铸锌屑。
中山市健威五金电器有限公司
2、喷涂时上螺杆四个,吹尘干净,挂上部螺杆上,调小粉量,先喷内后喷表面槽位,之后喷两边。
固化温充1650C,保温时间15分钟。
注:
适应于手工、流水三线喷涂。
八、积家产品属于小面积产品,喷涂时必须注意小铁钩具备良好的导电性能。
注:
适应于手工一线、自动二线和三线喷涂。
九、所有喷涂产品要求在前处理之前打磨校件,冷轧材料在磷化后喷涂前存放时间
工作指导书
标题
喷涂产品喷涂操作工艺标准
文件编号
WI-QC-014
版次
A0
页次
第4页,共5页
编写日期
2010/04/08
十、不准超过10小时磷化膜表面不允许存在锈蚀氧化现象。
注:
磷化后允许校件打磨的物殊产品,磷化后打磨面积每一处不准超过0.02m2。
十一、所有喷涂产品固化温度根据其粉末性能进行调试达到客户色样一致并有经相关部门检验合格的喷涂样板方可批量生产。
十二、所有铝质材料钣金件前处理方案;除油(15-20分钟)水洗—铝脱氧(5-10分钟)—水洗耳恭听—铝皮膜(5-10分钟)—冲水。
注意水压不能太高,以免冲坏铝皮膜。
铝质材料钣金件烘烤只允许1500C。
十三、喷涂钣材厚度与固化温度控制的规定;
1、涂固化保温时间统一为15分钟。
2、对于浅色哑光粉末根据客户提供色板深浅程度调节165-1800C。
其它型号粉末最低固化温度为1800C。
3、1.5mm以下厚度钣材,固化温度1800C。
4、1.5mm-2mm厚度钣材,固化温度1850C。
5、2mm-2.5mm厚度钣材,固化温度2000C。
6、2.5mm-3mm厚度钣材,固化温度2000C。
7、3mm-3.5mm厚度钣材,固化温度2100C。
8、3.5mm以上厚度钣材,固化温度2200C。
以上固化温度允许正负公差50C。
十三、针对有螺孔的产品且客户要求孔内不能有粉时,在喷涂前必须对其孔装适当规格大小的螺丝杆后进行喷涂,如不慎孔内粘了粉在包装前需攻丝后再包装。
凡是有螺丝杆要求不喷涂的零件,在喷涂前必须用胶纸完全覆盖信后再喷涂,在包装前将烤硬的胶纸撕下。
凡是接地符号处不需喷涂的零件,在喷涂前必须用可以
工作指导书
标题
喷涂产品喷涂操作工艺标准
文件编号
WI-QC-014
版次
A0
页次
第5页,共5页
编写日期
2010/04/08
盖住接地符号规格的纸胶纸在喷涂前贴牢,在包装去掉。
十四、格力内销机除底盘和阀门支架外,(25*2、120、75、50侧板类)内表面整体喷涂层厚度不作考核,喷涂时可停止喷内表面的喷枪,让其自由吸附上粉。
但考虑到积水问题,所以内表面距离底下部边缘100mm以上要求喷涂,并喷涂层不低于40um。
但周围折边一定要求喷涂合格。
十五、所有喷涂的产品在上线喷、地喷台都必须挂试验件,以便做划格、撞击力试验和验证是否够温。
附:
以上喷涂产品操作工艺从即日起执行,如有增加、更改另行通知。
以前喷涂产品操作工艺同时作废。