模具检验验证规范.docx
《模具检验验证规范.docx》由会员分享,可在线阅读,更多相关《模具检验验证规范.docx(15页珍藏版)》请在冰豆网上搜索。
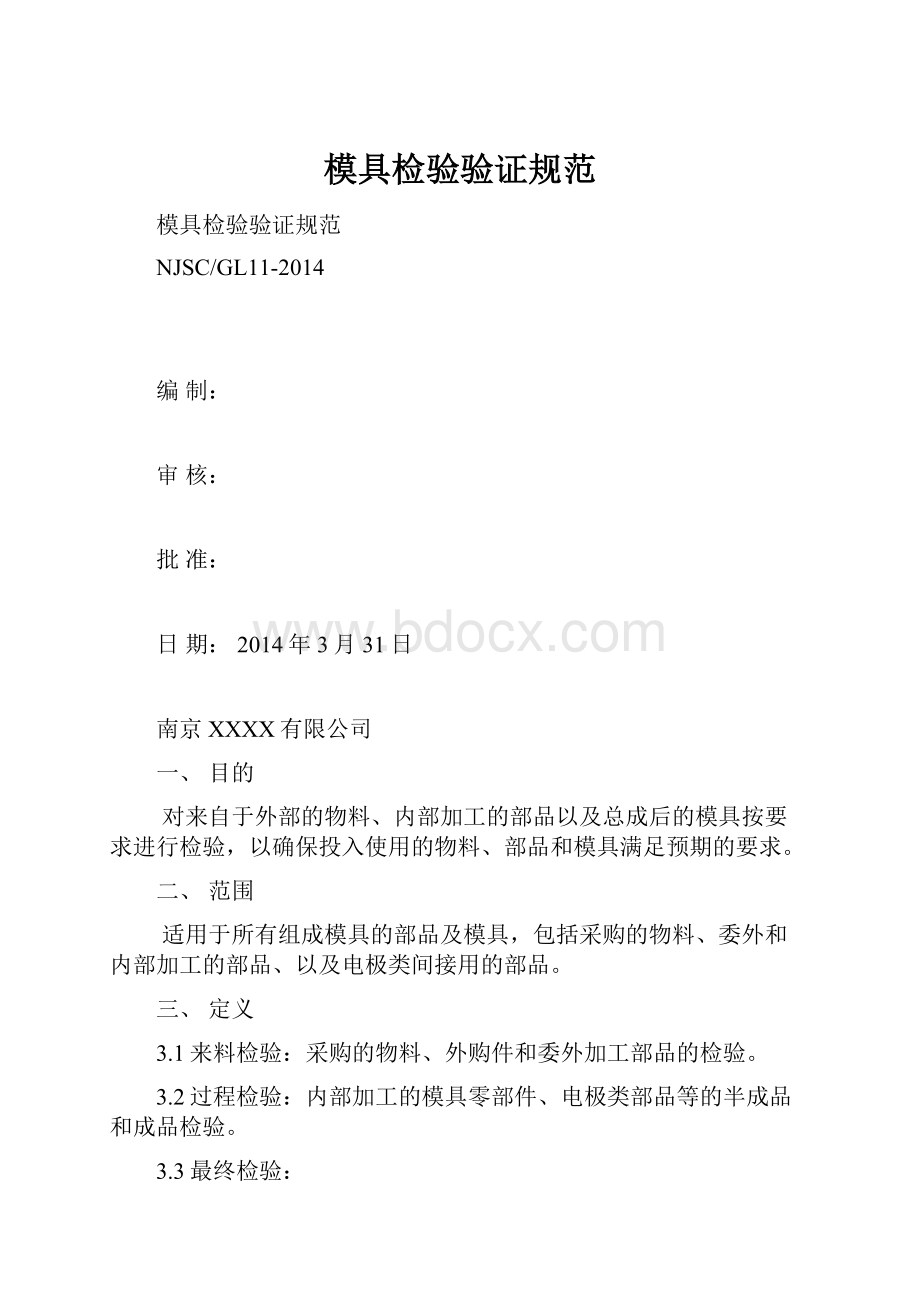
模具检验验证规范
模具检验验证规范
NJSC/GL11-2014
编制:
审核:
批准:
日期:
2014年3月31日
南京XXXX有限公司
一、目的
对来自于外部的物料、内部加工的部品以及总成后的模具按要求进行检验,以确保投入使用的物料、部品和模具满足预期的要求。
二、范围
适用于所有组成模具的部品及模具,包括采购的物料、委外和内部加工的部品、以及电极类间接用的部品。
三、定义
3.1来料检验:
采购的物料、外购件和委外加工部品的检验。
3.2过程检验:
内部加工的模具零部件、电极类部品等的半成品和成品检验。
3.3最终检验:
3.3.1模具零部件的成品最终检验,包括零部件的尺寸公差、形位公差、光洁度的检验。
3.3.2模具总成后的检验,包括模具外观、可成形性、成形产品等的检验。
四、职责
4.1技术部负责相关检验要求数据的提供。
4.2质量部负责对物料、部品以及模具实施来料检验、过程检验和最终检验。
4.3采购部对采购物资质量负责,并配合质量部做好来料检验工作。
4.4生产部协助做好过程检验,并确保未经检验或检验不合格的物资不投入使用。
五、检验验证流程
5.1来料检验
5.1.1作业流程图
5.1.2作业流程
5.1.2.1仓管员在接收到外来的物料时,对物料种类、供应商、数量等信息进行确认,确认无误后将物料存放在暂放区域,并以“待检品”予以标识同时通知质检。
5.1.2.2质量部接到报检信息后在二个工作日内对物料名称、规格、供应商、包装、标识等与相应的采购文件进行核对,无误后进行抽样或全数检查,并将检验结果填入《进货检验记录》。
如遇到特殊情况,生产急需使用物料,质量部应在半个工作日内完成检查工作。
5.1.2.3检验合格的物料贴上“合格”标签,仓管人员办理入库手续。
5.1.2.4检验不合格的物料,填写《不合格品处置单》,质量部会同技术部相关人员进行检讨,可接受的以“特别采用”进行标识,无法采用的贴上“不合格”标签并予以隔离。
5.1.2.5项目部将不合格物料的信息反馈给供应商,无法采用的物品予以退回。
5.1.2.6如特别采用的物料要修整的,修整后须检验合格方能投入使用。
5.2过程检验
5.2.1作业流程图
5.2.2作业流程
5.2.2.1各工序作业者完工后按图纸或工艺卡质量要求进行自检;若自检不合格则重新返工,本工序无法返工的按不合格处理。
5.2.2.2质量部接到报检信息后进行全数检查,并将检验结果填入《零件卡片(检验)记录》。
5.2.2.3检验合格的零/部件以“合格”进行标识,检验员签字、盖章后,移交下一道工序。
5.2.2.4检验不合格的零/部件,质量部会同技术部相关人员进行检讨,可接受的以“特别采用”进行标识,无法采用的贴上“不合格”标签并予以隔离。
5.2.2.5对于不合格项质量部开《不合格品处置单》,有重大质量事故质量部开《质量事故处理报告》。
相关部门对问题点分析、纠正和预防,同时对预防措施进行确认。
5.2.2.6特别采用的部品对其它工序有影响的,技术部需立即办理相关文件更改手续并及时通知相关方;要修整的部品,修整后须检验合格方能投入使用。
5.3最终检验
5.3.1作业流程图
5.3.1.1模具零部件的成品最终检验作业流程图
返工或返修
NG
不合格品标/识隔离
报检
最终产品
OK
记录存
入库
合格品检验报告ianyanbaogao
不合格品报告
让步接收
不合格品评审
报废
5.3.1.2模具总成后的检验作业流程图
修模联络
NG
检验并记录
产品检测、送样
零部件组装复合
NG
NG
试作
总装实配复模
试模联络
验收移交
修正
OK
5.3.2作业流程
5.3.2.1模具零部件制造完成后,质检人员对所有零部件做最终成品检验。
零部件都检验合格后,装配钳工人员担当对各部件进行组装、复合,实配合格后再进行总装实配复模,并确认各部件功能运作正常,不符合要求的及时修正。
装配钳工负责将装配过程中发现的问题及时记录于《钳工装配表》,并及时与技术部沟通。
5.3.2.2总装实配后装配钳工按《模具组装质量检查表》相关内容进行检验。
自检完成后,将《模具组装质量检查表》交质量部主管报检,由质量部主管召集技术部主管、分管工艺员、钳工组组长、装配钳工,对模具进行试模前的检查。
检查合格,检查人员在《模具组装质量检查表》上签字,质量部负责保存《模具组装质量检查表》,并通知生产部安排试模。
试模工作由分管工艺员负责、试模员参加、检验员配合。
试模过程中,试模人员须按规定及时填写《试模单》。
5.3.2.3试模后,质量部对产品进行检测并及时将试模样件的检测报告发给相关人员。
技术部负责对质量部提供的检测数据进行分析、判定,对不符合图纸要求或试作中的问题点以及要求设计更改、模具调整的内容向生产部提出修正。
5.3.2.4模具验证合格,由分管工艺员在《试模单》上填写模具验证结论,经分管工艺员、试模员、技术部主管签字,交质量部主管签批后,方可交付。
六、检验和试验
6.1取样
同一规格的外购件(五金件、标准件)按每批3~5件抽取样本或由质检担当确定,小于5件的批次进行全检,有公差标准的关键尺寸在现有资源可以测量的情况下要全部测量。
对原材料、所有自制零部件及外协制作零部件全检。
6.2检验要求
6.2.1质检人员抽取样本后,先分别对外观、尺寸进行判定。
6.2.2外观检查环境要求:
采用常态照明,待测量物品测量面与检验人员肉眼距离25~35cm,观察角度要求垂直于待测量物品被测面的±45º角,观察时间为10±5秒。
6.2.3监视和测量装置要求:
卡尺精度等级不低于0.02mm,千分尺精度等级不低于0.01mm,标准规精度等级不低于0.01mm,其它或自制的检具等装置要满足相关的工艺、检验文件或工程图纸上的测量要求。
6.2.4圆形零件的外径检查:
公差要求在±0.05以下的,测量工具为:
游标卡尺;公差要求在±0.05以上的,测量工具为千分尺或数显卡尺;
6.2.5内孔检查:
圆形内孔的检查量具为:
公差在0.05以下的用游标卡尺检查;公差在0.05以上的用内径千分尺、内径表或数显卡尺。
方孔的检查量具为:
公差在0.05以下的用游标卡尺检查;公差在0.03以上的用千分尺、数显卡尺或塞规检查。
6.2.6方形零件的外形检查:
公差要求在0.05以下的用游标卡尺检查;公差在0.05以上的用千分尺或数显卡尺检查。
6.2.7成品模具的检查:
外观无划痕、无碰伤、无癍点;上、下模合模顺畅、无干涉;落料冲孔模必须经过切纸检验后间隙均匀;符合上述要求的则视为合格;否则为不合格。
6.2.8判定:
6.2.8.1检查结果误差在允许的公差范围内,则判为合格;
6.2.8.2检查结果误差超出公差允许的范围(不含允许公差的上限或下限),则判定为不合格。
6.2.8.3客户有具体要求的按客户的要求进行检查。
6.3检验内容
6.3.1五金类(螺丝、弹簧等)
性质
检验项目
检验方法
检验要求
缺陷类别
外观
表面外观
目视
无色差、无混料、无氧化、无毛边
一般
无机械损伤、无缺损、变形等不良
重要
功能
适配性
配合产品
配合应满足图纸或规格说明书
重要
使用功能
测试
按规定测量其机械要求项目
尺寸
尺寸测量
卡尺
符合规格要求
重要
包装
包装状况
目视
包装无破损,标签字迹清楚
一般
6.3.2模具零/部件类(含毛坯和成品及委外加工的零/部件)
性质
检验项目
检验方法
检验要求
缺陷类别
外观
表面外观
目视
无机械损伤,无缺损及扭曲变形,无开裂
重要
无氧化现象,表面光洁,倒角均匀无锐边,编号正确、清晰
一般
材质
供方检测
目视
供方提供的质保书(或物性表)满足规格要求
重要
硬度
硬度计
硬度满足规格要求
重要
加工性
工艺验证
使用部门试用确认
重要
尺寸
2D尺寸
卡尺,深度尺,高度尺,
满足设计图纸要求(孔、槽可用塞规、芯棒测量)
重要
千分尺/机床
3D值
三坐标/机床
满足造型数据要求
垂直度
三坐标/机床
满足设计图纸要求
斜度
三坐标/角度尺
适配性
实配
滑动部滑动顺畅,产品面间隙≤0.03mm,其它间隙≤0.05mm
6.3.3原材料入厂
性质
检验项目
检验方法
检验要求
缺陷类别
外观
表面外观
目视
无机械损伤,无缺损及扭曲变形,无开裂
重要
无氧化现象,表面光洁,编号正确、清晰
一般
材质
供方检测
目视
供方提供的质保书(或物性表)满足规格要求
重要
硬度
硬度计
硬度满足规格要求
重要
加工性
工艺验证
使用部门试用确认
重要
尺寸
2D尺寸
卡尺,卷尺,
满足设计图纸要求
重要
6.3.4零/部件热处理后入厂
性质
检验项目
检验方法
检验要求
缺陷类别
外观
表面外观
目视
无缺损及扭曲变形,无开裂
重要
编号正确、清晰
一般
材质
供方检测
目视
供方提供的质保书(或物性表)满足规格要求
重要
硬度
硬度计
硬度满足规格要求
重要
加工性
工艺验证
使用部门试用确认
重要
尺寸
2D尺寸
卡尺,深度尺,高度尺
满足设计图纸要求
重要
3D尺寸
三坐标/机床
满足设计图纸要求
重要
6.3.5模具装配检验
6.3.5.1试装模具,修配销孔,检查零件的基本尺寸,外形是否与图纸一致,是否有干涉或不合理的结构。
6.3.5.2模板处理,表面突起部位要修平,避免磕碰,划伤模板。
6.3.5.3所有零件在安装前要进行消磁处理,检验标准,用0.02mm塞尺靠近不吸。
6.3.5.4选择螺丝。
零件的旋合长度应达到螺钉外径的1.5-2倍。
在装配时,同一个工装或项目所用的同一规格螺钉应一致,同一件上螺丝长短应一致。
6.3.5.5选择销子。
销子深入工件的长度应为销子直径的2倍左右对于淬火件,渗氮件来说,应用手压入或者用铜棒轻轻敲入即可,不可大力的砸入;对于软料来说,应用小锤敲入即可。
当两连接件的销孔都是通孔时,要控制销子松紧,防止销子脱落。
6.3.5.6弹簧装配时,应了解弹簧的压缩量,压缩量必须大于滑块的工作行程,且有安全间隙。
6.3.5.7所有应接触表面之间都无间隙,装完后检测。
6.3.5.8配合面采用红丹涂色法检测。
在检测面上涂较薄的红丹,被测面不动,转动相配合的零(部)件一圈,观察红丹研合研合情况,红丹被均匀抹去程度大于70%,则配合良好。
6.3.5.9锥面配合间隙检测。
将锥度相同的外锥与内锥按使用状态闭合,推紧上下零件使之完全结合,先轻轻推动锥度配合部,再旋转一周;推动无间隙且能较轻松转动,则锥度配合间隙符合要求。
6.3.5.10所有件按图纸装配,如有缺件,及时补做。
6.3.5.11填写记录《钳工装配表》与《模具组装质量检查表》。
6.3.6试模检验
6.3.6.1上冲床或液压机前必须确定模具已经试过安全性,无任何干涉,成型及刃口间隙无误。
对于冲孔类模具尽量安装在冲床上工作。
6.3.6.2了解模具的闭合高度,机床的闭合高度。
首先要了解所要使用机床的闭合高度。
上模具前应了解模具的闭合高度,如果超过机床的闭合高度上限就不能装在这台冲床上,否则就会损坏模具或冲床;如果模具的闭合高度低于机床的闭合高度下限,就要准备合适的垫铁,并保证垫铁等高。
6.3.6.2冲床闭合高度的调整方法。
模具上冲床前,应先走一个空行程(检验是否合适),将滑块运动到最低点(是否运动到最低点,看滑块上方的显示器)然后用米尺测量冲床的最低闭合高度是否大于模具的闭合高度。
例如如果显示器的值为260mm而模具高度为300mm,就应该将冲床上的滑块调整按钮拨到“上升”位置,将滑块高度调到大于模具的闭合高度320以上。
确定无误后在装模具。
模具上冲床后在通过几次周期运动来微调。
(不准磨具弹簧压缩状态时微调闭合高度)。
6.3.6.3模具放在冲床上,双手点动,使滑块慢慢下落,直到与模具上模板接触,然后用压板将模具固定。
6.3.6.4将模具固定好,空合模1-2次,如果零件没有干涉,在放入料进行合模。
如果料切不断,需要将--闭合高度调低一些,直到能够切断。
带限位柱的模具调整闭合高度时,在保证能正常工作的前提下,不管理论闭合高度是多少,必须以上下两限位柱不接触为准,最好先留0.5mm左右的间隙,在进行微调,注意限位柱不能承受力。
否则容易损坏模具或冲床。
如上压力机的模具,要知道其能成受的最大压力,使用大吨位压力机时一定要调整系统压力后再用,防止损坏磨具。
模具放在压力机或冲床上,要知道模具压力的中心在哪(主要取决于弹簧的分布,材料成型过程的受力情况,及限位柱的分布),要放在机床的压力中心上。
6.3.6.5调试原则
6.3.6.5.1凸凹模间隙调整方法。
透光法,塞尺法,压铅丝,精修时用压料研点法。
6.3.6.5.2每道序都应留有样件,好有对比,看看修整的位置是否有效果,也便于弄清楚是哪道工序产生的。
6.3.6.5.3每次送样件,必须留样。
6.3.6.5.3相关人员及时填写《试模单》。
6.3.7缺陷等级
6.3.7.1重要:
性能达不到预期的目标,会导致模具不能成形或最终成形品达不到要求。
6.3.7.2一般:
不满足规定的要求但不影响性能的。
6.3.8不合格品判定
6.3.8.1所有原材料、五金件、本厂加工的零部件、外协加工及热处理的零部件的存在重要缺陷的都判定为不合格品。
6.3.8.2试模出来的样品尺寸达不到要求,判定为模具不合格,需要进行调试。