基座的数控技工零件加工工艺设计方案正式版.docx
《基座的数控技工零件加工工艺设计方案正式版.docx》由会员分享,可在线阅读,更多相关《基座的数控技工零件加工工艺设计方案正式版.docx(43页珍藏版)》请在冰豆网上搜索。
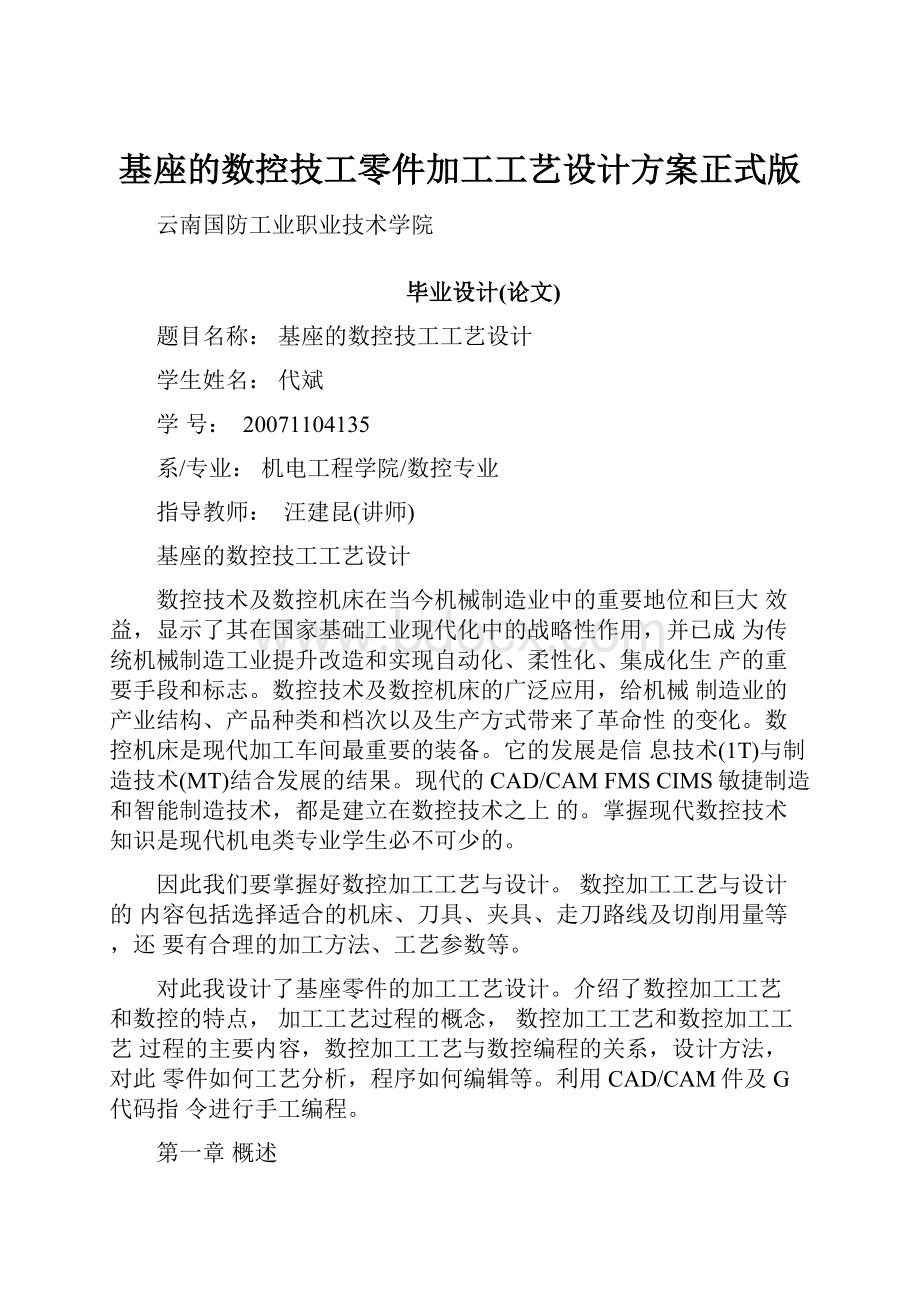
基座的数控技工零件加工工艺设计方案正式版
云南国防工业职业技术学院
毕业设计(论文)
题目名称:
基座的数控技工工艺设计
学生姓名:
代斌
学号:
20071104135
系/专业:
机电工程学院/数控专业
指导教师:
汪建昆(讲师)
基座的数控技工工艺设计
数控技术及数控机床在当今机械制造业中的重要地位和巨大效益,显示了其在国家基础工业现代化中的战略性作用,并已成为传统机械制造工业提升改造和实现自动化、柔性化、集成化生产的重要手段和标志。
数控技术及数控机床的广泛应用,给机械制造业的产业结构、产品种类和档次以及生产方式带来了革命性的变化。
数控机床是现代加工车间最重要的装备。
它的发展是信息技术(1T)与制造技术(MT)结合发展的结果。
现代的CAD/CAMFMSCIMS敏捷制造和智能制造技术,都是建立在数控技术之上的。
掌握现代数控技术知识是现代机电类专业学生必不可少的。
因此我们要掌握好数控加工工艺与设计。
数控加工工艺与设计的内容包括选择适合的机床、刀具、夹具、走刀路线及切削用量等,还要有合理的加工方法、工艺参数等。
对此我设计了基座零件的加工工艺设计。
介绍了数控加工工艺和数控的特点,加工工艺过程的概念,数控加工工艺和数控加工工艺过程的主要内容,数控加工工艺与数控编程的关系,设计方法,对此零件如何工艺分析,程序如何编辑等。
利用CAD/CAM件及G代码指令进行手工编程。
第一章概述
1.1数控技工的特点
1.2数控加工工艺的概念
1.3数控加工工艺的主要内容
1.4数控编程
1.5CAD/CAM系统
第二章基座的零件加工工艺
2.1零件图工艺分析
2.2材料分析
2.3选择数控机床
2.4设计工艺
2.5填写数控加工工序卡片
2.6加工程序
2.7参考资料
第三章
3.1数控专业毕业论文心得与体会
3.2参考资料
第一章概述
1.1数控加工的特点
数控加工,也称之为NC(NumericalControl)加工,是以数值与符号构成的信息,控制机床实现自动运转。
数控加工经历了半个世纪的发展已成为应用于当代各个制造领域的先进制造技术。
数控加工的最大特征有两点:
一是可以极大地提高精度,包括加工质量精度及加工时间误差精度;二是加工质量的重复性,可以稳定加工质量,保持加工零件质量的一致。
也就是说加工零件的质量及加工时间是由数控程序决定而不是由机床操作人员决定的。
数控加工具有如下优点:
(1)提高生产效率;
(2)不需熟练的机床操作人员;
(3)提高加工精度并且保持加工质量;
(4)可以减少工装卡具;
(5)可以减少各工序间的周转,原来需要用多道工序完成的工件,数控加工一次装夹完成加工,缩短加工周期,提高生产效率;
(6)容易进行加工过程管理;
(7)可以减少检查工作量;
(8)可以降低废、次品率;
(9)便于设计变更,加工设定柔性;
(10)容易实现操作过程的自动化,一个人可以操作多台床;
(11)操作容易,极大减轻体力劳动强度随着制造设备的数控化率不断提高,数控加工技术在我国得到日益广泛的使用,在模具行业,掌握数控技术与否及加工过程中的数控化率的高低已成为企业是否具有竞争力的象征。
数控加工技术应用的关键在于计算机辅助设计和制造(CAD/CAM)系统。
1.2数控加工工艺和数控加工工艺过程的概念
1.数控加工工艺是采用数控机床加工零件时所运用各种方法和技术手段的总和,应用于整个数控加工工艺过程。
数控加工工艺是伴随着数控机床的产生、发展而逐步完善起来的一种应用技术,它是人们大量数控加工实践的经验总结。
2.数控加工工艺过程
是利用切削工具在数控机床上直接改变加工对象的形状、尺寸、表面位置、表面状态等,使其成为成品或半成品的过程。
1.3数控加工工艺和数控加工工艺过程的主要内容
1.选择并确定进行数控加工的内容;
2.对零件图纸进行数控加工的工艺分析;
3.零件图形的数学处理及编程尺寸设定的确定;
4.数控加工工艺方案的制定;
5.工步、进给路线的确定;
6.选择数控机床的类型;
7.刀具、夹具、量具的选择和设计;
8.切削参数的确定;
9.加工程序的编写、校验与修改;
10.首件试加工与现场问题处理;
11.数控加工工艺技术文件的定型与归档。
1.4数控编程系统
1.数控程序
输入数控机床,执行一个确定的加工任务的一系列指令,称为数控程序或零件程序。
2.数控编程
即把零件的工艺过程、工艺参数及其他辅助动作,按动作顺序和数控机床规定的指令、
格式,编成加工程序,再记录于控制介质即程序载体(磁盘等),输人数控装置,从而指挥机床加工并根据加工结果加以修正的过程。
数控加工机床与编程技术两者的发展是紧密相关的。
数控加工机床的性能提升推动了编
程技术的发展,而编程手段的提高也促进了数控加工机床的发展,二者相互依赖。
现代数控
技术下在向高精度、高效率、高柔性和智能化方向发展,而编程方式也越来越丰富。
1.5CAD/CAM系统
20世纪90年代以前,市场上销售的CAD/CAM软件基本上为国外的软件系统。
90年
代以后国内在CAD/CAM技术研究和软件开发方面进行了卓有成效的工作,尤其是在以PC
机动性平台的软件系统。
其功能已能与国外同类软件相当,并在操作性、本地化服务方面具
有优势。
一个好的数控编程系统,已经不是一种仅仅是绘图,做轨迹,出加工代码,他还是一种先进的加工工艺的综合,先进加工经验的记录,继承,和发展。
第二章基座零件加工工艺
图1-1
图示为基座零件图。
已知该零件的毛柸为410mm*260mm*90mm的方形坯料,材料为
HT250。
2.1零件图工艺分析
该零件由平面、圆、孔系、U型槽、外轮廓组成。
其中有4个①8和4个①12的孔,2
个①20的孔,1个①200的圆,1个141.42*141.42的内方,4个U型槽,2个开口槽。
长度和厚度公差为土0.1,孔径公差为土0.1,表面粗糙度为3.2。
根据上述分析基座零件的外轮廓和U型槽的加工应分粗铳、半精铳、精铳三个阶段
进行;4-①8孔的加工分为钻中心孔、钻孔二个阶段进行;4-①12孔的加工分为钻中心孔、
钻孔、扩孔三个阶段进行;①20的孔的加工分为钻中心孔、钻孔、扩孔三个阶段进行。
以
保证表面粗糙度要求,同时以底面定位,提高装夹刚度以满足垂直度要求。
2.2材料分析:
灰铸铁
牌号:
HT250标准:
GB9439-88
特性及适用范围:
为珠光体类型的灰铸铁。
其强度、耐磨性、耐热性均较好,减振性良好,铸造性
能较优,需进行人工时效处理。
可用于要求高强度和一定耐蚀能力的泵壳、容器、塔
器、法兰、填料箱本体及压盖、碳化塔、硝化塔等;还可制作机床床身、立柱、气缸、齿轮以及需经表面淬火的零件
化学成分:
碳C:
3.16〜3.30硅Si:
1.79〜1.93锰Mn:
0.89〜1.04硫S:
0.094〜0.125磷P:
0.120〜0.170
力学性能:
抗拉强度db(MPa):
250硬度:
(RH=1时)209HB试样尺寸:
试棒直径:
30mm
热处理规范及金相组织:
热处理规范:
(由供方定,以下为某试样的热处理规范,供参考)铸态金相组织:
片状石墨+珠光体零件材料为HT250。
2.3选择数控机床
由于基座零件的上表面为孔、圆、外轮廓和U型槽,只需单工位加工即可完成。
故选择立式加工中心。
加工表面不多,只有粗铳、半精铳、精铳、钻孔、扩孔等工步,所需刀具不超过20把,选用华中立式加工中心即可满足上述要求,工件一次装夹后可
自动完成铳钻铰攻螺纹等工步的加工。
2.4设计工艺
(1)选择加工方法
1.表面的粗糙度要求为Ra3.2。
可选择“粗铳----精铳”方案。
2.孔加工方法的选择。
孔加工前,为了便于钻头定位,先用中心钻钻中心孔,然后再
钻孔。
内孔的加工方案在很大程度上取决于内孔本身的尺寸精度和粗糙度,对于精度较高
粗糙度较小的表面一般不能一把刀加工到图纸要求的尺寸报表表面粗糙度,而要分工步进行
加工。
该零件孔的加工方案选择如下:
(1)孔4-①8表面粗糙度为Ra3.2,选择“中心钻——钻”方案。
(2)孔4-①12表面粗糙度为3.2,选择“中心钻——钻——扩孔”方案。
3.U型槽加工方法。
槽表面的加工方案在很大程度上取决于内槽表面本身的尺寸精度
和粗糙度。
对于U型槽,表面粗糙为Ra3.2,选择,“粗铳-----精铳方案”。
(2)确定加工顺序
按照基面先行,先面后孔,先粗后精的原则确定加工顺序。
外轮加工采用顺铳方
式,内轮廓加工采用逆铳方式,刀具沿切线方向切入与切出。
1.铳六方保证400mm*250mm*80mm
2.去毛刺0.2~05*45°
3.铳圆保证①200mm
(1)粗铳轮廓。
(2)精铳轮廓。
4.铳内方
(1)粗铳圆,去除大部分余量。
(2)粗铳轮廓,留0.3mm单边余量。
(3)精铳轮廓到要求尺寸。
5.加工4-①8孔保证①8、Ra3.2
(1)钻中心孔。
(2)扩4-①8孔至要求尺寸。
6.加工4-①12孔保证①12、Ra3.2
(1)钻中心孔。
(2)钻4-①12孔。
(3)
扩4-①12孔至要求尺寸。
7.铳开
口槽
(1)
粗铳轮廓。
(2)
精铳轮廓。
&加工2-①20孔
(1)
钻中心孔。
(2)
钻2-①20孔。
(3)
扩2-①20孔至要求尺寸。
9.加工
U型槽
(1)粗铳U型槽,留0.30mm单边余量。
(2)精铳U型槽至要求尺寸。
(3)确定装夹方案和选择夹具
基座零件毛坯的外形比较规则,因此在加工上平面、圆、孔系、U型槽、外轮廓、
开口槽时。
选平口虎钳来夹紧使零件伸出8mm左右,下面用垫块垫起,夹紧用百分表找正。
(4)选择刀具
所需有中心钻、钻头、立铳刀。
其规格根据加工尺寸选择,表面粗铳铳刀直径应选大一些,
以增大切削面积,但要考虑到刀库允许装刀直径也不能太大;表面精铳铳刀直径应选小一
些,以减少误差。
刀具选择时应注意:
1.零件表面采用立铳刀加工,根据圆半径选择立铳刀直径,使铳刀工作时减少时间消耗。
2.采用立铳刀加工,铳刀半径受轮廓最小曲率半径限制,R=10mm。
3.孔加工各共步的刀具直径根据加工余量和孔径确定。
刀具卡片
产品名称
零件图号
工序号
刀具号
刀具名称
刀具型号
01
T01
立铳刀
①40
02
T02
立铳刀
①20
03
T03
钻头
①3
04
T04
钻头
①8
05
T05
钻头
①10
06
T06
钻头
①12
07
T07
钻头
①14
(五)确定进给路线
表面的粗、精铳削加工进给路线根据铳刀直径确定。
因而所选铳刀直径为①40mm。
故它沿X方向一次进给,其铳削范围见图2-1。
在原点下刀依次粗加工半径39.9,79.8,99.7mm的圆,每次下刀10mm,加工三次;精加工时加工半径100mm的圆。
斜方轮廓的粗精铳削加工由于受余量和R10的影响,因而所选立铳刀为①20mm,其铳削
范围见图2-2。
先用铳刀直径为①40mm的刀加工一个半径65的圆,每次深度为10mm,加工三次,去除多余余量;用①20mm的铳刀粗铳内方单边余量0.3mm;再用①10mm的精加工,通过修改刀补分三次加工。
所有孔加工进给路线均按最短路线确定,因为孔的位置精度要求不高,机床的定位精
度完全能保证。
图2-3所示为各孔加工工步的进给路线;打中心孔一钻孔(----扩孔).
(^点/参考平帀
C25
图2—3
U型槽的粗精加工由于受R11的影响,因而选立铳刀为①20mm,其铳削范围见图2
4,可以用同把刀完成粗精加工。
图2-4
开口槽粗精铳选用立铳刀直径为次。
①40,其铳削范围见图2-5,每次加工深度为10mm,加工六
图2-5
(六)确定切削用量
工*材科
無齿进哄血•V
feft
ftn
高追稱诜畀
1UNJ15
:
:
iu-ij.2*
乩:
二•.序
G10411S
012420
015-C1.3U
工件持料
挠削堂4人'rt--n;irt'
JS噫撬抚刀
据
<225
1也贮
66«U0
225*31$
1备扬
54*120
125-42S
沏
36-75
<190
2】・35
66-150
】g(W60
亠冷
占事釦
266*310
aS10
2L-D
■1*
if
杞
a
MM
St
5=5
5=*ao^i:
'jkP.
(ISO.20Cr)
U*ain;')
f
Qai■r
f
迪r")
IP.
n
fa«ain)
f
Gat■:
rJ
a-25
Al1
12-30
也05**^・】
Q037(IQ
匸〜。
a—2a
aZ,2
12-30
o.i.2
QF
GlOfljQl15
127
■J.2—13
1270
0.2-43
5
G.23
425
0l3七4145
12-3G
0.卄0.討
■S-*]□
O.2EML35
根据零件图知,该零件材料切削性能较好。
铳削圆平面、斜方、U型槽及两侧型腔时,留精
加工余量0.3mm。
该零件表面粗糙度要求为Ra=3.2卩m,可分粗铳、半精铳、精铳三步。
半精铳时背吃刀量或侧吃刀量取1.5〜2mm;精铳时圆周铳侧吃刀量取0.3〜0.5mm。
1.铳刀的切削参数计算(①40立铳刀)
(1)刀具转速n(单位:
r/min)
查表2-3知v=16m/min
由式v=ndn/1000知
n=1000v/nd
贝Un=1000X16/3.14X40
=127.4r/min
(2)刀具进给速度vf(单位:
mm/min)
查表2-2知f=0.18mm/z
由式v=nzf知v=127.4X2X0.18
=45.9mm/min
其它铳刀切削参数计算类同,切削参数见表2-5.
2•钻头的切削参数计算(①3中心钻)
(1)刀具转速n(单位:
r/min)
查表2-4知v=8m/min
由式v=ndn/1000得
n=1000v/nd
贝Un=1000X8/3.14X3
=849.3r/min
(2)刀具进给速度vf(单位:
mm•min)
查表2-4知f=0.05mm/z
由式v=nzf知
v=1000X2X0.05
=100mm/min
其它钻头切削参数计算类同,切削参数见表2-5。
2.5填写数控加工工序卡片
为更好地指导编程和加工操作把该零件的加工顺序、所用刀具和切削用量等参数编入表所示基座零件加工工艺卡片表2-5中.
零件号
001
零件名称
基座
编制日期
2010.10
程序号
01000
编制
赵小玉
工步号
程序段号
工步内容
刀具号
刀具补偿
半径补偿
刀具规格
背吃刀量
1
N10
钻中心孔
T03
H03
①3
2
N11
粗铳圆
T01
H01
D01
①40
1.5
3
N12
精铳圆
T01
H01
D01
①40
0.3
4
N13
斜方大余量
T01
H01
D01
①40
1.5
5
N14
粗铳斜方
T02
H02
D02
①20
1.5
6
N15
精铳斜方
T02
H02
D02
①20
1.5
7
N16
钻中心孔
T03
H03
①3
8
N17
钻4-①8孔
T04
H04
①8
9
N18
钻中心孔
T03
H03
①3
10
N19
钻①10孔
T05
H05
①10
11
N20
钻4-①12
T06
H06
①12
12
N21
铳两侧行腔
T01
H01
D01
①40
1.5
13
N22
精铳行腔
T02
H02
D02
①20
0.3
14
N23
钻中心孔
T03
H03
①3
15
N24
钻①14孔
T07
H07
①14
16
N25
2-①20孔
T02
H02
D02
①20
0.3
17
N26
粗铳U型槽
T02
H02
D02
①20
1.5
18
N27
精铳U型槽
T02
H02
D02
①20
0.3
2.6
加工程序
序号
程序内容
程序说明
1
01000
主程序号
2
N10
钻中心孔
3
T03M06
选择刀具
4
G90G54G00X0Y0S800M03
建立工件坐标系
5
G43Z50H03
安全高度
6
Z5
初始高度
7
G99G81X0Y0Z-60R5F30
钻孔
8
G00X0Y0
回到原点
9
Z50
至安全高度
10
M05
11
M30
程序结束
12
N11
粗铳圆
13
T01M06
选择道具
14
G90G54G00X0Y0S200M03
建立工件坐标系
15
G43Z50H01
建立刀具补偿,走到安全高度
16
Z5
初始高度
17
G42G01X0Y0D01(20)
加入半径补偿
18
G01Z-10F40
卜刀
19
G01X-39.9
走刀
20
G02X-39.9Y0I39.9J0
加工圆
21
G01X-79.8
走刀
22
G02X-79.8Y0I79.8J0
加工圆
23
G01X-99.7
走刀
24
G02X-99.7Y0I99.7J0
加工圆
25
G01Z5
抬刀
26
G01X0Y0
回到原点
27
GO1Z-20F40
下刀
28
G01X-39.9
走刀
29
G02X-39.9Y0I39.9J0
加工圆
30
G01X-79.8
走刀
31
G02X-79.8Y0I79.8J0
加工圆
32
G01X-99.7
走刀
33
G02X-99.7Y0I99.7J0
加工圆
34
G01Z5
抬刀
35
G01X0Y0
回到原点
36
GO1Z-30F40
下刀
37
G01X-39.9
走刀
38
G02X-39.9Y0I39.9J0
加工圆
39
G01X-79.8
走刀
40
G02X-79.8Y0I79.8J0
加工圆
41
G01X-99.7
走刀
42
G02X-99.7Y0I99.7J0
加工圆
43
G01Z5
抬刀
44
G40G00X0Y0
取消刀补
45
Z50
至安全高度
46
M05
47
M30
程序结束
48
N12
精铣圆
49
T01M06
选择刀具
50
G90G54G00X0Y0S200M03
建立工件坐标系
51
G43Z50H01
建立刀具补偿,走到安全高度
52
Z5
初始高度
53
G42G01X0Y0D01(20)
加入半径补偿
54
GO1Z-30F40
下刀
55
G01X-100
走刀
56
G02X-100Y0I100J0
加工圆
57
G01Z5
抬刀
58
G40G00X0Y0
取消刀补
59
Z50
至安全高度
60
M05
61
M30
程序结束
62
N13
内方大余量
63
T01M06
选择刀具
64
G90G54G00X0Y0S200M03
建立工件坐标系
65
G43Z50H01
建立刀具补偿,走到安全高度
66
Z5
安全高度
67
G42G01X0Y0D0(120)
加入半径补偿
68
GO1Z-40F40
下刀
69
G01X-65
走刀
70
G02X-65Y0I65J0
加工圆
71
G01Z5
抬刀
72
G01X0Y0
回到原点
73
GO1Z-50F40
下刀
74
G01X-65
走刀
75
G02X-65Y0I65J0
加工圆
76
G01Z5
抬刀
77
G01X0Y0
回到原点
78
GO1Z-60F40
下刀
79
G01X-65
走刀
80
G02X-65Y0I65J0
加工圆
81
G01Z5
抬刀
82
G40G00X0Y0
取消刀补
83
Z50
至安全高度
84
M05
85
M30
程序结束
86
N14
粗铣斜方
87
T02M06
选择刀具
88
G90G54G00X0Y0S400M03
建立工件坐标系
89
G43Z50H02
建立刀具补偿,走到安全高度
90
G68X0Y0P-45
旋转指令
91
M98P100D02(29)
子程序调用
92
M98P100D02(10.7)
子程序调用
93
G69
取消旋转指令
94
G00Z50
至安全高度
95
X0Y0
回到原点
96
M05
97
M30
程序结束
98
100%
子程序号
99
G01Z5
初始高度
100
G42G01X-70.5Y0
加入半径补偿
101
G01Z-60F60
下刀
102
G01Y60.5
走刀
103
G02X-60.5Y70.5R10
加工圆弧
104
G01X60.5
走刀
105
G02X70.5Y60.5R10
加工圆弧
106
G01Y-60.5
走刀
107
G02X60.5Y-70.5R10
加工圆弧
108
G01X-60.5
走刀
109
G02X-70.5Y-60.5R10
加工圆弧
110
G01Y0
走刀
111
G01Z5
抬刀
112
G40G00X0Y0
取消刀补
113
Z50
至安全高度
114
M99
子程序结束
115
N15
精铣斜方
116
T02M06