承压设备焊接质量控制.docx
《承压设备焊接质量控制.docx》由会员分享,可在线阅读,更多相关《承压设备焊接质量控制.docx(34页珍藏版)》请在冰豆网上搜索。
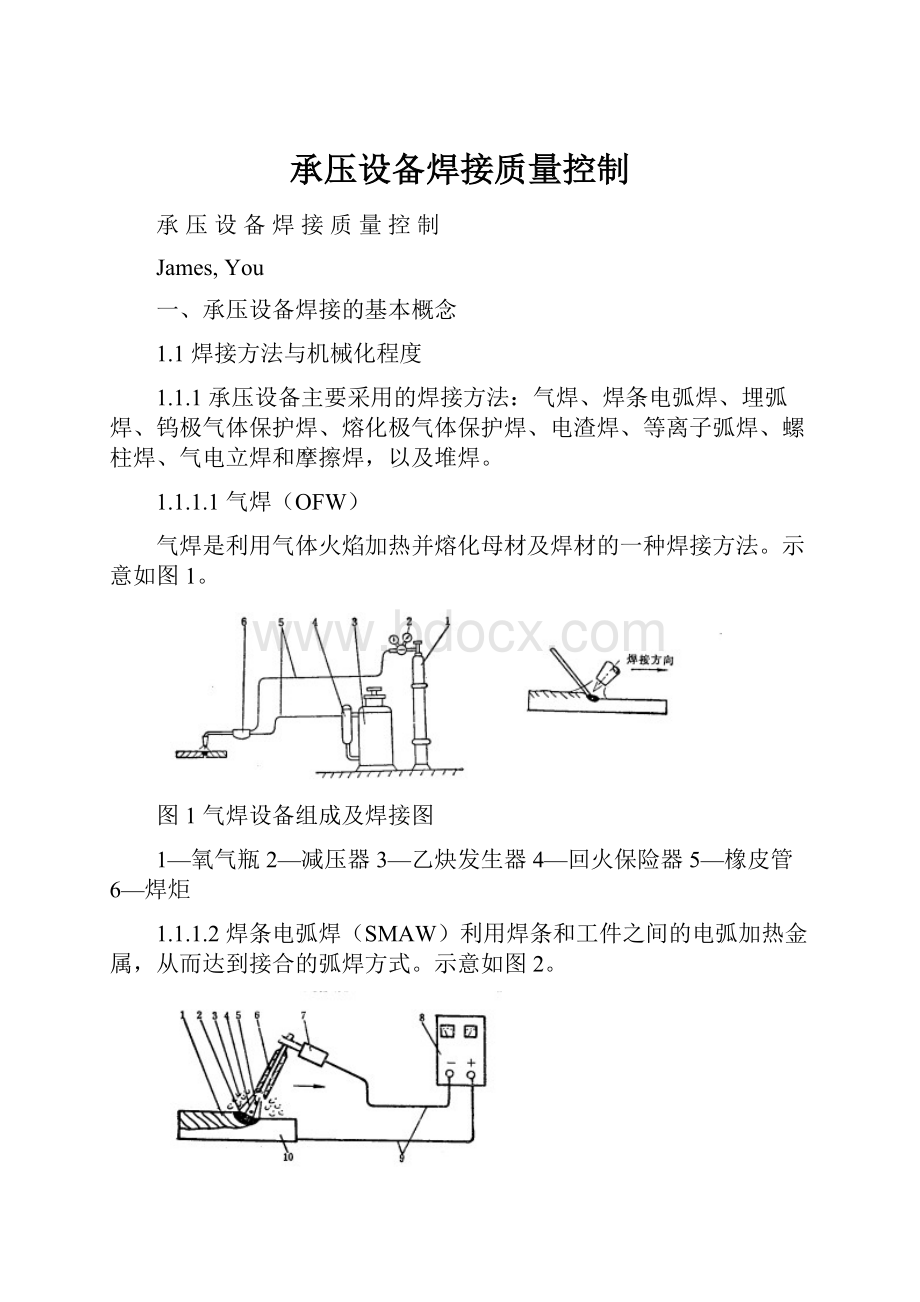
承压设备焊接质量控制
承压设备焊接质量控制
James,You
一、承压设备焊接的基本概念
1.1焊接方法与机械化程度
1.1.1承压设备主要采用的焊接方法:
气焊、焊条电弧焊、埋弧焊、钨极气体保护焊、熔化极气体保护焊、电渣焊、等离子弧焊、螺柱焊、气电立焊和摩擦焊,以及堆焊。
1.1.1.1气焊(OFW)
气焊是利用气体火焰加热并熔化母材及焊材的一种焊接方法。
示意如图1。
图1气焊设备组成及焊接图
1—氧气瓶2—减压器3—乙炔发生器4—回火保险器5—橡皮管6—焊炬
1.1.1.2焊条电弧焊(SMAW)利用焊条和工件之间的电弧加热金属,从而达到接合的弧焊方式。
示意如图2。
图2手弧焊过程
1—焊缝2—熔池3—保护性气体4—电弧5—熔滴6—焊条7—焊钳
8—电焊机9—焊接电缆10—工件
1.1.1.3钨极气体保护焊(GTAW):
在惰性气体保护下,利用钨极与工件间产生的电弧热熔化母材和填充丝的焊接方法。
示意如图3。
图3-1钨极气体保护焊示意图
1—喷嘴2—钨极3—电弧4—焊缝5—工件图3-2热丝钨极氩弧焊示意图
6—熔池7—填充焊丝8—惰性气体
1.1.1.4溶化极气体保护焊(GMAW)在气体保护下采用可熔化的焊丝与被焊工件之间的电弧作为热源溶化母材与焊材。
保护气体有:
惰性气体、氧化性混合气体(惰性气体中加入氧气、CO2气等)、全CO2气。
示意如图4。
图4-2管状焊丝气体保护电弧示意图[5]
1—导电嘴2—喷嘴3—管状焊丝
4—CO2气体5—电弧6—熔渣
7—焊缝8—熔池
8—熔池9—焊缝金属
图4-1熔化极气体保护电弧焊示意图
1—母材2—电弧3—导电嘴4—焊丝
5—送丝轮6—喷嘴7—保护气体
8—熔池9—焊缝金属
图4-3摆动电弧法窄间隙
1—气体保护罩2—冷却水3—导电嘴
4—焊丝成圈盘5—电弧摆动电机6—支撑轮7—弯曲轮8—送丝软管9—送丝电机
10—保护气11–焊枪。
12–焊丝
11—焊枪12—焊丝
8—熔池9—焊缝金属
1.1.1.5埋弧焊(SAW):
电弧在一层颗粒状的可熔化焊剂覆盖下燃烧,熔化母材与焊材(焊丝与焊剂)一种焊接方法,由于电弧光不暴露故该焊接方法称之为埋弧焊。
示意如图5,埋弧焊的主要设备自动焊焊车示意如图6。
图5埋弧焊示意图
图6-1典型半自动埋弧焊机[4]
1—送丝机构2—焊丝盘3—送丝软管(电缆)4—焊炬5—控制箱6—焊接电源
图6-2常见的自动埋弧焊机型式[5]
a)焊车式b)悬挂式c)车床式d)门架式e)悬臂式
1.1.1.6电渣焊(ESW)
电渣焊是利用电流通过溶渣产生的电阻热作为热源,将工件和填充金属熔合成焊缝的垂直位置的焊接方法。
示意见图7。
图7电渣焊过程示意图
1—水冷成形滑块2—金属熔池3—渣池4—焊接电源5—焊丝6—送丝轮7—导电杆8—引出板
9—出水管10—金属熔滴11—进水管12—焊缝13—起焊槽
1.1.1.7气电立焊(EGW)
通过连续送进的填充金属极和焊缝熔池之间的电弧使之产生接合的弧焊焊方法。
可看成由普通熔化极气体保护焊与电渣焊发展而形成的一种熔化极气体保护焊。
示意如图8。
图8气电立焊原理示意图[1]
1—水冷挡块2—水3—焊枪4—气体5—导丝管6—送丝轮7—焊丝矫直机构8—摆动器9—水冷滑块
1.1.1.8等离子弧焊(PAW)
以电极与工件间的压缩电弧(转移弧)或电板—压缩喷咀间的压缩电弧(非转移弧)加热金属,从而获取接合的弧焊方法。
示意如图9。
保护气体是从嘴孔喷出的热离子化气体,也可以再辅之以另一种气体。
图9-2微束等离子弧焊接系统示意图[3]
1—焊接电源2—维弧电源3—钨极4—离子气5—冷却水6—保护气7—喷嘴8—保护气罩9—等离子弧10—工件KM—接触器触头
图9-1大电流等离子弧焊接系统示意图[3]
1—焊接电源2—高频振荡器3—离子气4—冷却水5—保护气6—保护气罩7—钨极8—等离子弧
9—工件10—喷嘴KM1、KM2—接触器触头
1.1.1.9螺柱焊
将金属螺柱(或类似零件)与工件相连接的通用术语,示意如图10。
焊接方法可采用电弧焊、电阻焊、摩擦焊或其它适当的方法,外部保护气体可用可不用。
图10电弧螺柱焊操作顺序(箭头表示螺柱运动方向)
1.1.1.10摩擦焊(FRW)
摩擦焊是利用工件接触端面相对旋转运动中相互摩擦所产的热,使端部达到热塑性状态,然后迅速顶锻,完成焊接的一种压焊方法。
示意如图11。
图11普通摩擦焊方法示意图[1]
a)焊接准备b)摩擦加热开始c)摩擦加热终了d)顶锻焊接
1.1.1.11堆焊
是用焊接的方法把填充金属熔敷在金属表面,以便得到所要求的性能与尺寸。
1.2机械化程度
1.2.1任何一种焊接方法都可以划分为:
手工、机械化与自动化:
a)手工:
用手进行操作与控制;
b)机械化:
需要人来观察与调节;
c)自动化:
无需用人调节与控制。
举例:
①图12、图13。
图12躺条焊图13重力焊
②半自动焊也是手工焊(见图6-1)。
1.1.2.2焊工考试:
当改变焊接方法或焊接方法机械化程度改变时要重新进行考试。
1.1.2.3焊接工艺评定:
当改变焊接方法要重新评定焊接工艺;当不改变焊接方法,改变机械化程度时,只要重要因素,补加因素不变,无需重新评定焊接工艺。
1.1.3注意
焊接方法与使用电源种类、气体种类、坡口形式无关。
1.2坡口、焊缝、接头
1.2.1坡口:
根据设计或工艺需要,在焊件的待焊部位加工并装配成的一定几何形状的沟槽。
见图14。
坡口各部分的名称见图15。
1.2.1.1坡口作用
1.2.1.2坡口形式与各厂实际情况有非常密切的关系。
1.2.2焊缝:
焊件经焊接后所形成的结合部分(见图14)。
1.2.2.1焊缝只有五种形式
1.2.2.2焊接工艺评定试件分类对象:
是焊缝。
图14
续图14
续图14
续图14
续图14
图15-1
余高:
超出母材表面连线上面的那部份焊缝金属的最大高度。
a)
焊根:
焊缝背面与母材的交界处。
b)
图15-2
焊工考试试件分类对象也是焊缝,见图16。
图16
1.2.2.3焊缝各部分的名称见图17。
图17-1图17-2
图17-3
1.2.3焊接接头:
由二个或二个以上零件要用焊接组合或已经焊合的接点。
检验接头性能应考虑焊缝、熔合区、热影区甚至母材等不同部位的相互影响(见图14)。
11.2.3.1焊接接头形式:
共12种。
21.2.3.2焊接接头中最薄弱环节:
例:
JB/T4744中加强热影响区冲击试验要求。
31.2.3.3焊接接头条数,单面焊双面成形争议。
41.3焊接材料、填充材料
51.3.1焊接材料:
焊接时所消耗材料包括焊条、焊丝、气体、钨极、衬垫等。
63.2填充材料:
增加焊缝金属合金成分的材料如焊条、焊丝、焊剂。
而气体、钨极却增加不了合金成分,而不作为填充材料。
71.4焊材的型号与牌号
81.4.1型号:
符合焊接材料国家标准代号。
如:
焊条E5015,焊剂:
F4A2-H08A;
9牌号:
符合焊接材料生产厂厂标要求的代号。
如焊条J507,焊剂HJ431。
101.4.2型号与牌号之间关系:
11a符合
12b相当
13c没有关系,如W707
141.4.3焊材型号中“–G”特点。
1.4.4统一牌号:
J507、大西洋CHE507、天泰TL-507。
151.5焊缝金属与溶敷金属
161.5.1焊缝金属:
构成焊缝的金属,一般指熔化的母材和填充金属凝固后形成的那部分金属。
熔敷金属:
完全由填充金属熔化后所形成的金属。
171.5.2焊接材料性能是对熔敷金属试验结果。
181.5.3焊接材料性能在十分理想情况收到的,与实际工程中焊接不同,如:
热处理制度。
191.6焊层与焊道
201.6.1焊层:
多层焊时的每一个分层。
每个焊层可由一条焊道或几条并排相搭的焊道所组成(见图18)。
21焊道:
每一次熔敷所形成的一条单道焊缝(见图18)。
22
23图18
241.6.2层间温度已改为道间温度
25线能量是以每道焊道的线能量来判断。
261.6.3a)单层单道焊时,焊缝中心存在杂质偏折。
27b)两层为多,如“考规”。
281.7焊后热处理、消除应力热处理,中间热处理
291.7.1焊后热处理(PWHT)
30定义:
焊后,为改善焊接接头的组织与性能或消除残余应力而进行的热处理。
311.7.1.2定义:
能改变焊接接头的组织和性能或残余应力的热过程。
321.7.1.3定义:
焊后所有热处理。
331.7.1.4焊后热处理类别。
341.7.1.4.1奥氏体不锈钢
35a)不进行焊后热处理;
36b)进行焊后固溶或稳定化热处理。
371.7.1.4.2除奥氏体不锈钢外的材料
a)不进行焊后热处理;
b)低于下转变温度进行焊后热处理;
c)高于上转变温度进行热处理(如正水);
d)先在高于上转变温度,继之在低于下转变温度进行焊后热处理(即正火或淬火后继之回火);
e)在上下转变温度之间进行焊后热处理。
1.7.2消除应力热处理(ISR):
为改善焊接区域的性能,消除焊接残余应力等有害影响,将焊接区域或其中部分在金属相变点以下加热到足够高温度,并保持一定的时间,而后均匀冷却的热过程。
1.7.3中间焊后热处理
焊接过程中,对于受到反复热处理的焊接区及焊件,为了确保焊接质量而在每次焊接后紧接着进行的热处理,但无论哪一处焊接区最后都必须接受正规的焊接热处理。
1.7.4焊后热处理规定:
母材厚度还是焊缝金属厚度。
1.7.5焊后热处理温度界限
碳钢、低合金钢:
482℃(490℃)
高合金钢:
316℃(315℃)
1.7.6焊后热处理是我国承压设备制造(安装)工艺过程中最薄弱环节。
1.7.6.1缺少焊后热处理工艺规程标准。
1.7.6.2焊后热处理单位没有许可论证制度。
1.7.6.3焊后热处理中难点:
热变形及控制。
1.8预热、后热、道间温度
1.8.1定义
①预热:
焊接开始前,对焊件的全部(或局部)进行加热的工艺措施。
②后热:
焊接后立即对焊件的全部(或局部)进行加热或保温,使其缓冷的工艺措施。
它不等于焊后热处理。
③道间温度:
多层多道焊时,在施焊后继焊道之前,其相邻焊道应保持的温度。
1.8.2目的
①预热:
减低了焊缝金属和母材热影响区的冷却速度,同时也降低了收缩应力,减少裂缝发生机会。
②后热:
有利于焊缝中扩散氢加速逸出,减少焊接残余变形与残余应力,是防止焊接冷裂纹的有效措施之一。
③道间温度。
1.8.3注意问题
1.8.3.1降低预热温度会改变焊接接头的抗拉强度,所以焊接工艺评定时要规定允许最低预热温度。
1.8.3.2提高道间温度会改变接头冲击韧性。
所以焊接工艺评定时,要规定允许最高道间温度。
1.8.3.3后热温度范围及时间
1.9焊缝位置(焊接位置)与试件位置
1.9.1定义
1.9.1.1焊缝位置:
熔焊时,焊缝所处的空间位置(见图19)。
横焊缝
仰焊缝
立焊缝
平焊缝
图19
1.9.1.2试件位置:
施焊时,试件所处空间位置(见图20)。
图21
1.9.2焊缝位置与试件位置关系
1.9.2.1焊缝位置是一个范围,有平焊缝、立焊缝、横焊缝、仰焊缝。
范围详见图21、表1。
表1对接焊缝位置范围
位置
参考图
焊缝倾角,(°)
焊缝面转角,(°)
平焊缝
A
0~15
150~120
横焊缝
B
0~15
80~150
210~280
仰焊缝
C
0~80
0~80
280~360
立焊缝
D
E
15~80
80~90
80~280
0~360
1.9.2.2焊缝离开不了试件,试件位置在“考规”中是有限的几种,同一试件上焊缝有一种或多种位置。
详见图20。
图20
1.9.2.3下向焊不是标准术语,含义不明确。
二、焊接标准规范
2.1承压设备常用焊接标准规范:
①《锅炉压力容器压力管道焊工考试与管理规则》
②JB4708钢制压力容器焊接工艺评定。
③JB4709钢制压力容器焊接规程。
④JB4744钢制压力容器产品焊接试板的力学性能检验。
⑤JB/T4747压力容器用钢焊条订货技术条件。
已修订为:
《特种设备焊工考核细则》
NB/T×××承压设备焊接工艺评定
NB/T×××压力容器焊接规程
NB/T×××承压设备产品焊接试件的力学性能检验。
NB/T×××承压设备用焊接材料交货技术条件。
2.2各标准、规范特点
2.2.1《锅炉压力容器压力管道焊工考试与管理规则》。
①参照采用ASMEIX,但检验要求比ASMEIX要严得多。
适用于锅炉、压力容器、气甁和压力管道。
②只对钢质材料规定了考试方法。
钛按JB/T4734,铝按JB/T4734、铜、镍按GB50236。
③ASMEIX为企业行为、《考规》为政府行为。
④ASMEIX认为焊工考试与母材无关,《考规》规定了与母材类别有关。
2.2.2NB/T47014
①参照采用ASMEIX,母材与焊材按中国要求,只适用于压力容器。
②焊接工艺评定是重要的,但不是保证产品质量的唯一方法。
③焊接工艺评定标准的专业性与实践性都非常强。
国内同行业中认识趋于统一,但还有分歧。
2.2.3NB/T47015
①本标准只适用于压力容器,不适用于气甁、锅炉、压力管道。
②压力容器制造发展过程中,积累了不少经验上升为“规定”“规程”,以标准形式体现出来,但都是实践总结,要结合具体情况才能实施,NB/T47015只是推荐性标准,先要遵守图样的设计规定,然后才是遵守NB/T47015规定。
2.2.4NB/T47016
①适用于压力容器,不适用于气甁,参照采用了ASMEⅧ篇中相应规定。
②产品焊接试板力求能代表产品焊接接头的实际情况,因而作了多项规定。
③冲击试验时规定“常温”下进行冲击,常温没有标准。
2.2.5JB/T4747
①我国焊材国家标准大多采用美国国家标准,唯独没有采用美国焊材标准中的采购导则。
②焊材国家标准并不能完全符合承压设备的使用要求。
③从我国资源条件及承压设备法规出发编制了承压设备用焊接材料技术条件。
三、焊接工艺评定
3.1定义
3.1.1焊接工艺评定定义:
为使焊件的焊接接头性能符合指定的技术要求,对按所拟定的焊接工艺指导书进行验证性试验及结果评价。
3.1.2焊接工艺指导书[(WPS)WeldingProcedureSpecification]为验证性试验所拟定的、经评定合格的、用于指导产品施焊的焊接工艺文件。
3.1.3焊接工艺评定报告[(PQR)procedurequalificationrecord]记载验证性试验及其检验结果,对拟定焊接工艺指导书进行评价的报告。
3.1.4焊接工艺规程(GB/T3375英文及定义)[weldingprocedurespecification]制造焊件所有关的加工和实践要求的细则文件,可保证熟练焊工或操作工操作时质量的再现性。
3.1.5焊接性(weldability)材料在限定施工条件下,焊接成按规定设计要求的构件,并满足预定服役要求的能力。
焊接性受材料,焊接方法,构件类型及使用要求四个因素的影响。
3.2基本原则
3.2.1焊接工艺评定的目的是确保焊接接头的使用性能符合规定。
3.2.2焊接工艺评定的实质是验证性试验,验证所拟定焊接工艺的正确性。
3.2.3焊接工艺评定试件的分类对象是焊缝而不是焊接接头。
3.2.4对接焊缝与角焊缝—确保焊接接头力学性能
堆焊工艺评定—确保堆焊层化学成分
型式试验件—确保接头焊透
重新评足焊接工艺的判断准则:
力学性能
化学成分
焊透
3.3几个值得注意问题。
3.3.1焊接工艺评定是焊接质量管理休系中重要环节之一。
3.3.2焊接工艺评定不是模拟件、见证件。
3.3.3评定合格的焊接工艺指导书是编制焊接工艺规程基础,而拟定焊接工艺指导书的基础是金属材料的焊接性。
焊接性分为工艺焊接性与使用焊接性,焊接性试验主要解决如何焊接这个问题,而不能回答当焊接工艺因素改变后,焊接接头的性能还能不能满足标准规定,这个问题正是焊接工艺评定的任务。
3.3.4不能将焊接工艺评定规则当作焊接工艺规程使用。
焊接工艺指导书不能代替焊接工艺规程,它与焊接工艺指导书有原则区别。
3.3.5NB/T47014不适用超出标准范围,增加检验要求时的焊接工艺评定。
3.3.6不要将焊工考试范畴内的要求硬拉到焊接工艺评定中解决。
3.4有关焊接工艺评定标准
3.4.1《NB/T47014承压设备焊接工艺评定》特点
①参照采用ASME1X
②适用范围
③有关冲击试验
3.4.2编制石墨粘接工艺评定标准尚不成熟
3.4.3编制玻璃钢粘接工艺评定、塑料焊接工艺评定标准更不成熟,目前只是见证件试验阶段。
3.4.4正确执行《钢制压力容器焊接工艺评定》标准
3.4.4.1对焊接工艺评定项目的监督检查,首先要掌握金属材料的焊接性能、图样的设计要求和制造工艺过程。
a)检查厂方掌握金属材料焊接性能的最好方法是查阅厂方提供的金属材料焊接性能报告。
B)图样设计要求包括:
材料牌号及厚度、焊材牌号,设计温度、焊接接头性能及制造工艺要求。
c)同样产品,但各厂制造工艺千差万别,焊接工艺应与焊件在制造过程中相同。
3.4.4.2沿着设计图样上压力容器外壳及特殊接点,找出:
a) 不同类别的焊缝形式;
b) 各焊缝两侧母材牌号及厚度;
c) 不同焊接接头焊接工艺特点(焊接方法、焊接材料、焊接位置、焊后热处理等);
d) 分别列出所需要评定的焊接工艺项目与厂方提供的焊接工艺评定项目对照检查。
3.4.4.3NB/T47014适用范围
a)适用于钢制压力容器的温度范围是常温而不是低温。
当GB150附录C“低温压力容器”焊接工艺评定引用NB/T47014时,变更了冲击试验温度和合格指标。
b)某厂制造09MnNiDR钢质低温压力容器(设计温度-50℃),所提供审查的焊接工艺评定报告中有一份试件:
09MnNiDR+16MnR冲击试验温度-20℃,那么这份焊接工艺评定只能用于设计温度≥-20℃场合。
3.4.4.4母材
a)国外钢材及评定规则
b)对于没有列入GB150内的钢材如何进行焊接工艺评定。
举例:
GS建设两台07MnCrMoVR球罐。
3.4.4.5试件厚度与焊件厚度
①当规定进行冲击韧性试验时的厚度覆盖关系:
a) 当T≥8mm时,最小值一律为0.75T;
b) 经高于上转变温度焊后热处理,或奥氏体母材经固溶处理时的规定。
②不等厚试件经评定合格的焊接工艺适用于不等厚焊件母材厚度范围。
③不同焊接方法组合评定时厚度覆盖范围。
④焊接返修时的厚度计算。
3.4.4.6预热和层间温度:
a) 预热温度与层间温度客观存在,一定要填写。
b) 预热温度填写允许最低值,层间温度填写允许最高值。
3.4.4.7焊接线能量
①焊接工艺评定中焊接线能量作为补加因素,电流值、电压值、焊接速度单个变化不作为评定因素。
②焊接工艺指导书与焊接工艺规程中线能量的填写。
③焊接工艺规程中电流、电压与焊接速度不必与焊接工艺评定报告相同。
④如何控制焊接线能量。
3.4.4.8焊后热处理
①焊后热处理定义。
在焊接工艺中热冲压封头也是焊后热处理。
②15CrMoR拼接钢板热冲压封头的焊接工艺评定。
③焊接工艺评定温度与产品焊后热处理温度。
3.4.4.9焊接返修的焊接工艺评定
①焊接工艺评定不是模拟件也不是见证件。
②焊接返修次数不是焊接工艺评定因素。
3.4.4.10试件检验
①试件外观检查与无损检验只要求没有裂纹。
②拉伸试验
a) 试样加工错误:
如有棱角;
b) 拉伸试验报告上出现延伸率、屈服强度;
c) 拉伸试样断裂位置;
d) 拉伸试验合格指标按JB4708中规定而不是原始材料的σb。
③弯曲试验
a) 试样加工错误:
如试样无棱角;
b) 弯曲试验目的:
测定塑性与致密性;
c) 当材料延伸率小于20%时的弯曲试验;
d) 横向弯曲与纵向弯曲。
④冲击试验
a) 冲击试样加工:
光洁度达不到;
b) 16MnR冲击试验合格指标;
c) 非标试样合格指标;
d) 奥氏体焊缝合格指标;
e) JB4708中冲击试验温度。
3.4.4.11焊接工艺评定文件
①焊接工艺评定文件资料中时间的逻辑关系。
②焊接工艺评定文件资料中焊接电流、电弧电压与焊接速度数值的逻辑关系。
③扩大焊接工艺评定适用范围。
四、焊工考试规则
4.1手工焊焊工、焊机操作工
手工焊焊工:
用手操作焊钳、焊矩或焊枪,使焊条或焊丝运行以形成焊缝的焊工。
焊机操作工:
从事机械化焊接或自动化焊接的操作工人。
4.2焊工考试目的:
要求焊工焊出没有超标缺陷的焊缝
错误观点例:
①新钢种焊工考试要检验力学性能。
②薄板焊接变形大,要重新考试。
③长输管道焊接效率。
④SH/T4103中考试。
4.3影响焊工技能的九大因素。
4.3.1焊接方法;
4.3.2焊接方法的机动化程度;
4.3.3材料类别;
4.3.4焊接位置;
4.3.5焊接衬垫;
4.3..6焊缝金属厚度;
4.3.7管子外径;
4.3.8焊条药皮类型;
4.3.9焊接工艺要素。
4.4焊工考试规则性质,是资格考试不是能力考试;
4.5焊接缺陷
4.5.1未焊透,见图22。
4.5.2未熔合,见图23。
4.5.3咬边,见图24。
4.5.4焊瘤,见图25。
4.5.5凹坑,见图26。
4.5.6下塌,见图27。
未焊透:
焊接时接头根部未完全熔透的现象,见图22,对接焊缝也指焊缝深度未达到设计要求的现象。
图22
未熔合:
熔焊时,焊道与母材之间或焊道与焊道之间,未完成熔化结合的部分,电阻点焊指母材与母材之间未完全熔化结合的部分,见图23。
图23
咬边:
由于焊接参数选择不当,或操作方法不正确,沿焊趾的母材部位产生的沟槽或凹陷,见图24。
图24
焊瘤:
焊接过程中,熔化金属流淌到焊缝之外未熔化的母材上所形成的金属瘤,见图25。
图25
凹坑:
焊后在焊缝表面或焊缝背面形成的低于母材表面的局部低洼部分,见图26。
图26
下塌:
单面熔化焊时,由于焊接工艺不当,造成焊缝金属过量透过背面,而使焊缝正面塌陷,背面凸起的现象,见图27。
图27
五、焊接质量管理
5.1钢材
5.1.1要掌握钢材的焊接性能,订货前可以要求钢厂提供钢材的焊接性能试验报告。
举例08MnNiVR。