混炼工艺.docx
《混炼工艺.docx》由会员分享,可在线阅读,更多相关《混炼工艺.docx(33页珍藏版)》请在冰豆网上搜索。
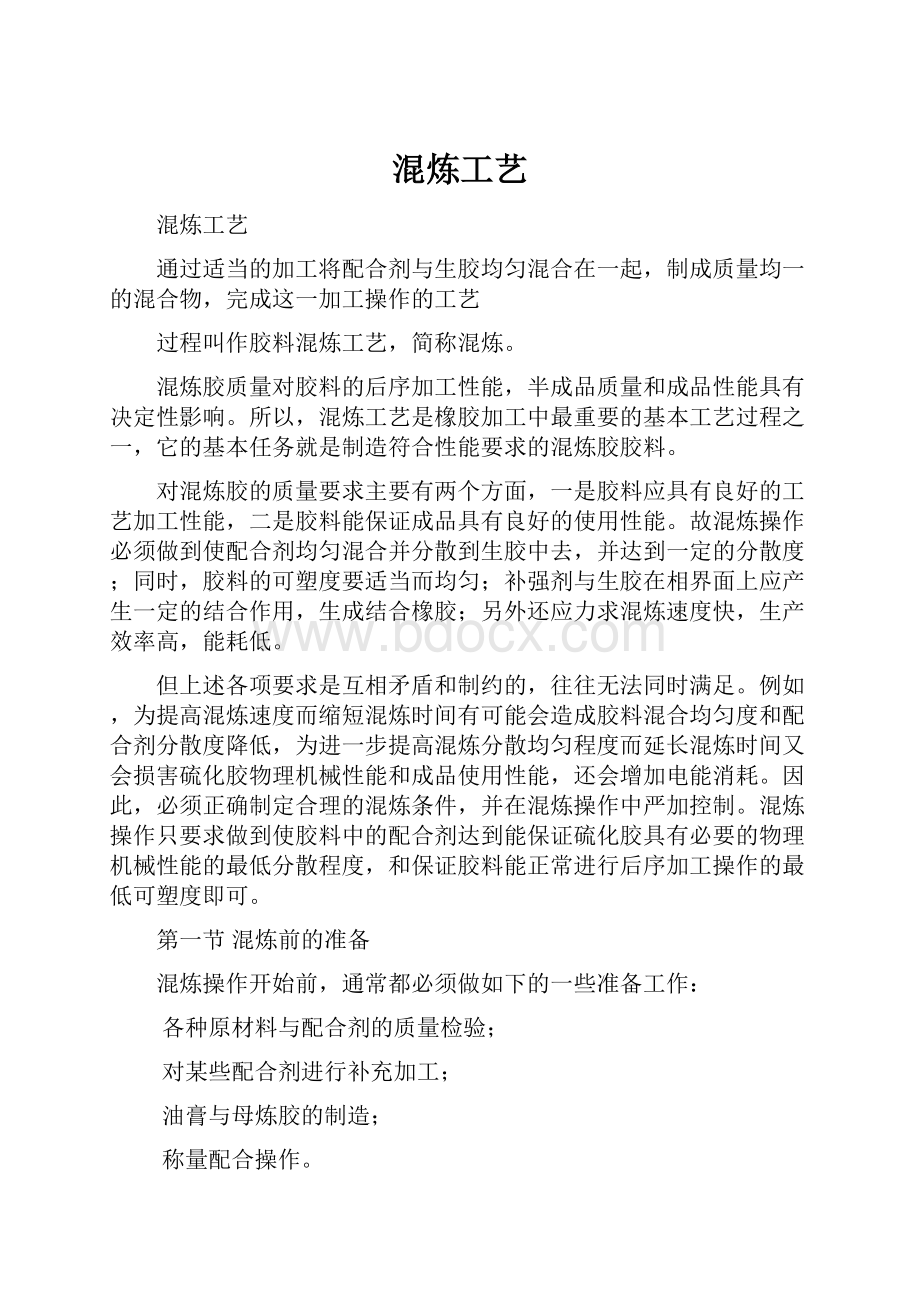
混炼工艺
混炼工艺
通过适当的加工将配合剂与生胶均匀混合在一起,制成质量均一的混合物,完成这一加工操作的工艺
过程叫作胶料混炼工艺,简称混炼。
混炼胶质量对胶料的后序加工性能,半成品质量和成品性能具有决定性影响。
所以,混炼工艺是橡胶加工中最重要的基本工艺过程之一,它的基本任务就是制造符合性能要求的混炼胶胶料。
对混炼胶的质量要求主要有两个方面,一是胶料应具有良好的工艺加工性能,二是胶料能保证成品具有良好的使用性能。
故混炼操作必须做到使配合剂均匀混合并分散到生胶中去,并达到一定的分散度;同时,胶料的可塑度要适当而均匀;补强剂与生胶在相界面上应产生一定的结合作用,生成结合橡胶;另外还应力求混炼速度快,生产效率高,能耗低。
但上述各项要求是互相矛盾和制约的,往往无法同时满足。
例如,为提高混炼速度而缩短混炼时间有可能会造成胶料混合均匀度和配合剂分散度降低,为进一步提高混炼分散均匀程度而延长混炼时间又会损害硫化胶物理机械性能和成品使用性能,还会增加电能消耗。
因此,必须正确制定合理的混炼条件,并在混炼操作中严加控制。
混炼操作只要求做到使胶料中的配合剂达到能保证硫化胶具有必要的物理机械性能的最低分散程度,和保证胶料能正常进行后序加工操作的最低可塑度即可。
第一节混炼前的准备
混炼操作开始前,通常都必须做如下的一些准备工作:
各种原材料与配合剂的质量检验;
对某些配合剂进行补充加工;
油膏与母炼胶的制造;
称量配合操作。
一、原材料与配合剂的质量检验
生胶与配合剂的质量都必须符合规定的质量等级技术指标才能使用。
各种原材料的质量虽然应当由生产供应者予以保证,但由于在长期的贮存和运输过程中,因各种原因往往会出现质量变化,造成性能不符合规定标准指标的要求。
故在使用前都必须按规定对其进行质量检验,合格者才能使用。
通常对配合剂的检验内容主要有纯度、粒度及其分布、机械杂质、灰分及挥发分含量、酸碱度等。
具体依配合剂类型不同而异。
生胶一般除了检验化学成分和门尼粘度外,还检验物理机械性能。
二、配合剂的补充加工
配合剂的加工包括固体配合剂的粉碎,干燥和筛选;低熔点固体配合剂的熔化和过滤;液体配合剂的加温和过滤;粉状配合剂的干燥和筛选。
(一)粉碎
块状和粗粒状配合剂必须经过粉碎或磨细处理才能使用。
如防老剂A、沥青和松香等脆性固体可用锤式粉碎机破碎;硬脂酸和石蜡用刨片机切片后再粉碎,以使其粒度符合标准。
通常的粒度要求为:
防老剂A、石蜡和硬脂酸≤10克/块,树脂≤20克/块,松香≤50克/块,沥青≤100克/块,矿质胶≤150克/块。
(二)干燥
干燥的目的是减少配合剂中的水分和其他挥发分含量,防止粉末状配合剂结团,便于筛选和混炼分散,避免某些配合剂遇水变质和胶料内部产生气泡和海绵。
干燥方式可采用真空干燥箱、干燥室或螺杆式连续干燥机等。
具体方法和工艺条件随配合剂性质和质量要求而定。
例如低熔点配合剂的干燥温度应低于其熔点25—40℃,促进剂、防老剂和硫黄即是。
硫黄最好铺在干燥盘中呈薄层于35~40℃下干燥,这样还可同时除去其中的亚硫酸,其他一些粉末状配合剂的干燥温度一般是:
防老剂BLE≥50℃,碳酸钙≥50℃,陶土>~50℃。
干燥后的含水率均应<0.5%。
(三)熔化与过滤及加温
低熔点固体软化剂像石蜡和松香等须先进行加热熔化,达到干燥脱水和降低粘度作用后,再经过滤去掉其中的机械杂质。
而对于粘度太高的液体软化剂如松焦油等,则应进行加温脱水并使其粘度减少,以便于进行过滤及利用管道输送和称量配合操作。
(四)筛选
粉末状固体配合剂粒度及粒度分布达不到规定标准者,或者已发生配合剂结团者及含有机械杂质者必须进行筛选加工,去掉其中的机械杂质、较大颗粒与结团。
如硫黄粉应采用规定的筛网全部过筛后才能使用。
常用的筛选设备有振动筛、鼓式筛选机和螺旋式筛选机等。
炭黑对筛网的附着力较强,故在鼓式筛网内还装有毛刷,以保证炭黑顺利通过网子L。
选用的筛网规格一般为氧化锌用40~60目,硫黄用60~80目以上。
细度达不到标准的其他配合剂采用100目的筛网。
三、称量配合
称量配合是按照配方规定的原材料品种和用量比例,选用适当的衡器进行称量搭配的操作过程。
称量配合操作对保证产品质量具有重要作用。
因为配合剂的错用或漏用,以及称量的不准确都会给胶料性能和产品质量造成损害甚至完全报废。
因此,要求称量配合操作必须做到精密、准确、不漏、不错。
根据生产规模和技术水平的不同,称量配合的操作方式分为两种:
一种是手工操作法,一种是机械化自动称量配合法。
前者,不适于机械化自动化的大规模生产。
所以现代化大生产中的称量配合操作都采用机械化自动称量配合方法。
在整个炼胶系统中配备一整套原材料贮存和输送及自动称量和向炼胶机加料的系统装置,由计算机进行远距离操纵和集中控制,使生产效率大大提高。
改善了操作条件,避免了主观误差。
只是变换配方不如手工法灵活,设备投资大,维护技术复杂,不适于小型生产使用。
目前,随着快速密炼机炼胶技术的发展和连续混炼设备的工业应用,原材料的称量配合装置已与炼胶设备形成了一套完整而又系统的装置,整个炼胶过程从原材料贮运称量到混炼胶下片,冷却和叠放均实现了自动化。
为了确保称量误差在规定范围之内,在选用衡器时必须保证每次的称量重量不少于衡器最大称量容量的10%。
这是因为低于该值的称量误差至少为0.4%,而达到衡器最大称量容量时的称量误差仅为0.1%。
即同一衡器的每次称量重量越多,其称量误差越小。
所以,在不超过衡器的称量容量的前提下,应尽可能选用容量较小的衡器。
第二节混炼工艺
橡胶工业生产中目前采用的混炼方法分两种:
一种是间歇式混炼操作,另一种为连续式混炼操作。
间歇式混炼方法应用最早,至今仍在广泛使用。
这种混炼方法的特点是胶料分批加工制造。
依据所用炼胶设备不同又分为开放式炼胶机混炼和密闭式炼胶机混炼两种方法。
从混炼生产效率和混炼胶质量上看以密炼机混炼最优越。
所以,目前凡拥有密炼机而又允许用密炼机加工的胶料,一般都是采用密炼机进行混炼。
随着橡胶工业科学技术水平的发展,正在向着机械化自动化操作的快速密炼机混炼的方向发展,使混炼效率大大提高,成为目前混炼工艺的主要发展方向。
连续混炼操作方式是60年代末到70年代初发展起来的混炼方法。
它的操作方式的主要特点是原材料连续加料,混炼胶连续排胶。
炼胶设备配有一整套自动称量配合加料装置。
混炼设备是一类专用的螺杆式连续混炼机。
目前技术上比较成熟,能够实际用于混炼加工的连续混炼机主要有三种,即转子式双螺杆型连续混炼机、传递式单螺杆型连续混炼机和隔板式单螺杆型连续混炼机。
该三种设备虽然已在混炼加工上得到实际应用,但因其本身仍然存在一定局限性而使其用途受到一定限制。
所以,目前橡胶混炼加工的主要方式仍以开放式炼胶机和密闭式炼胶机的间歇式混炼加,工为主。
本章以介绍间歇式混炼工艺为重点。
一、开炼机混炼工艺
开炼机混炼是橡胶工业应用最早的混炼方法,开炼机混炼生产效率低,劳动强度大,操作不安全;混炼时配合剂的飞扬损失大,污染环境;混炼胶的质量也不如密炼机的好。
但是,开炼机混炼后机台容易清洗,变换胶料配方比较灵活,适合于配方种类多变、生产批量小的小规模生产和实验室小型试验用胶料的混炼。
另外还有些不适于用密炼机混炼的胶料,如发泡胶料、硬质胶胶料、某些合成胶、硅橡胶和混炼型聚氨酯橡胶等,以及某些浅色和彩色胶料,适合于采用开放式炼胶机混炼。
所以开炼机混炼方法目前在橡胶工业生产中仍占有一定的位置。
(一)开炼机混炼的原理
开炼机混炼的一般操作方法是先让生胶包于前辊,并在辊距的上方留有适量的存胶(称堆积胶),再按规定的加料顺序往堆积胶上面依次加入配合剂。
当生胶夹带配合剂通过辊距时受到剪切混合作用而被混合和分散。
当配合剂完全混入生胶后立即进行切割翻炼操作,以保证混合均匀,再经薄通后下片,所以开炼机混炼过程分为三个阶段:
包辊、吃粉和翻炼。
1.胶料的包辊性胶料的包辊性与生胶本身的性质,混炼温度和机械加工切变速率都有关系。
混炼温度对胶料包辊性的影响可以分成4个区域。
混炼温度不同,胶料在辊筒上的包辊状态可能会出现下面4种不同的情况:
混炼温度低,橡胶呈弹性固体状态(1区),硬度高,弹性大,胶料难以进入辊距中,若强制压入辊距,则胶料通过辊距后呈碎块掉下。
因而胶料在这种状态下不能包辊,也无法进行混炼操作。
温度升高,胶料进入高弹性状态(2区),既有塑性流动,又有适当的高弹形变,所以胶料通过辊距后成为一弹性胶带紧紧地包在前辊表面上,不发生碎裂和脱落,不仅有利于混炼操作,也有利于配合剂在胶料中的混合分散。
继续升温胶料虽然仍为高弹性固体(3区),但其流动性进一步增加,分子之间的作用力和胶片的拉伸强度已大大减小,不能紧包前辊而呈袋囊状脱辊或破碎掉下,无法进行混炼操作。
在温度更高的时候,生胶变为粘流态(4区),通过辊距后呈粘流薄片包于前辊表面,这时胶料主要发生塑性流动和变形,弹性已几乎消失,且对辊筒发生粘附而难于切割。
所以应当控制混炼温度使生胶处于2区的温度范围内进行混炼,必须防止进入3区和1区的温度范围或包辊状态。
各种橡胶的结构特性和玻璃化温度不同,因而处于最佳包辊状态的2区的温度范围也不一样。
天然橡胶和乳聚丁苯橡胶在一般操作温度下没有明显的3区,只出现1区和2区,所以包辊和混炼性能好。
顺丁橡胶低温包辊在2区。
如果在50℃以上即转变到3区而出现脱辊现象。
另外,橡胶的粘弹性不仅受温度影响,还受外力作用速率的影响。
辊筒的转速一定时,胶料的切变速率与辊筒的直径成正比,与辊距大小成反比。
减小辊距会增大剪切速率,对胶料粘弹性的影响和降低温度的作用是一样的。
所以当温度进入包辊性能不好的3区范围而冷却方法又不能有效地使其回到2区的包辊状态时,可以通过减小辊距的方法宋实现。
只是对顺丁橡胶,若混炼温度超过50℃时,即使将辊距减至最小也不能再回到2区的包辊状态了。
橡胶的分子量大小和分布对其2区的温度范围也有重要影响。
分子量分布宽会使包辊性能良好的2区的温度范围加宽,胶料的包辊性就好。
据认为,从2区向3区的转变温度高低与生胶的断裂拉伸比λb有关。
实质上,在给定的转速和辊距下,当温度逐渐升高时,生胶在2区是处于剪切力作用下而尚未达到断裂点以前的状态。
随温度升高,生胶的强度和λb减小,到达一定温度后生胶即发生断裂而进入3区的状态;再继续升温则转入粘流态而进入4区。
橡胶的分子量增大,生胶的拉伸强度和断裂拉伸比λb增大,流动温度也提高,所以胶料从2区到3区和从3区到4区的转变温度也都随之提高,从而使包辊性能良好的2区的温度范围加宽。
同时,分子量分布宽,则橡胶的流动温度降低,使3区向4区的转变温度降低,因而使包辊性能不好的3区的温度范围缩小,故有利于混炼操作。
顺丁橡胶,乙丙橡胶等合成橡胶的包辊性能差,主要是因为其分子量分布比较窄,生胶的内聚力和拉伸强度低,胶料的最大松驰时间短,混炼时胶料的抗起始裂口能力低,使胶料出现破裂脱辊现象。
顺丁橡胶的分子量分布加宽时,胶料的抗起始裂口的能力增大,最大松驰时间加长,使裂口增加减弱,胶料的包辊性得到改善。
橡胶中加入炭黑后,因生成结合橡胶提高了胶料的强伸性能,脱辊现象就会很快扭转。
2.吃粉胶料包辊后应在辊距上方留有适当数量的堆积胶。
然后再向堆积胶的上面添加配合剂,这样有利于混炼。
如果辊距上方没有存胶,则胶料通过辊距时只发生周向的混合作用,使胶料呈周向层流状态而变形,无径向剪切变形和混合作用。
当有堆积胶存在时,在积胶处因胶料发生拥塞和绉褶将进入狭缝内部的配合剂夹带一起进入辊距,受到剪切产生径向混合,使配合剂向包辊胶片的厚度方向混合分散。
但若堆积胶数量过多反而会减慢混炼速度,并使散热困难而升温,影响混炼。
为此,通常是当胶料包辊后将堆积胶以外的多余胶料割下,再添加配合剂。
待全部粉剂混入生胶后,即吃粉完毕再将割下的余胶加入并翻炼混合均匀,这叫抽胶加药混炼法。
若配方本身填充量较大,还应在混炼过程中逐步放大辊距,以使堆积胶数量始终保持在适宜的范围内。
3.翻炼推积胶的存在虽然使胶料在辊距中产生了径向的混合作用,但仍不能使配合剂达到包辊胶片的整个厚度范围。
实际上只能达到包胶层厚度的2/3处,在贴近辊筒表面的一边仍有占胶片总厚度1/3的一层胶料无配合剂进入,这层胶料就叫呆滞层或死层,在这种情况下,开炼机辊筒上胶料的混合状态分为三种情况:
周向混合的均匀程度最高;轴向混合的均匀程度较差,两端部胶料的均匀程度比中央部位更差;径向混合均匀程度最差。
可见堆积胶的作用也是有限的。
为弥补其不足,在混炼吃粉后应立即进行切割翻炼操作,以使死层胶料进入活层。
切割翻炼方法有八把刀法,三折四扭法和打三角包法等。
切割翻炼后,必须将胶料薄通3~5遍,然后放大辊距下片,结束混炼操作。
(二)开炼机混炼的影响因素
开炼机混炼的影响因素有容量、辊距、辊速和速比、辊温、加料顺序、混炼时间及药品的一次添加量,必须根据胶料配方特性及配合剂的性质合理确定和调节。
1.容量每次混炼的胶料容积大小必须依炼胶机的规格及胶料配方特性合理确定。
容量过大会使辊距上方的堆积胶量过多而难以进入辊距,使混炼分散效果降低,而且因散热不良会使混炼温度升高,容易产生焦烧现象而影响胶料质量。
容量过大还会导致设备超负荷和劳动强度加大等一系列其他问题。
容量过小会降低生产效率。
所以容量过大过小都不利。
合理的混炼容量应按经验公式
Q=K·D·L
式中Q—塑炼容量,L;
K—经验系数,一般取值范围为0.0065~0.0085,L/cm2;
D——前辊简直径,cm;
L——辊筒工作部分长度,cm。
实际的混炼装胶容量还必须参考胶料配方和性质对计算结果加以适当修正。
例如合成胶混炼时的生热量较多,配方含胶率低填充量大,密度大的胶料,其混炼容量都应适当减小。
天然胶混炼生热量少,以及采用母炼胶混炼的胶料,其混炼容量可适当增加。
2.辊距炼胶机的辊距一般为4一8mm。
辊距减小,胶料通过辊距时的剪切效果增大,会加快混合分散速度;但同时也增加生热量和升温速度,并使堆积胶量增多,散热困难,又不利于剪切分散效果。
所以,随着混炼过程的配合剂不断加入,胶料的容积增大,辊距也应逐步调厚,以保持辊距上方的堆积胶量适当。
3.辊速与速比提高辊筒的转速和速比会加大混炼时对胶料的剪切作用与混合分散效果,但也会提高胶料混炼时的生热升温速度,又不利于提高剪切效果。
辊速过快操作危险性也大,辊速和速比过小又会降低机械剪切分散效果和生产效率。
所以开炼机混炼的辊筒转速一般控制在16—18r/min。
速比范围一般在1/1.1~1.2。
4.辊温开炼机混炼温度就是辊筒表面的温度,辊温低,胶料的流动性差,生胶对配合剂粒子表面的湿润作用下降,不利于混合吃粉过程,还会使设备负荷增加;但有利于提高机械剪切和混合分散效果。
若辊温过低,胶料硬度太大,容易损坏设备。
辊温提高有利于降低胶料的粘度,提高流动性和对配合剂粒子表面的湿润性,加快混炼的吃粉速度。
但若温度过高容易产生胶料脱辊现象和焦烧现象,难以操作,也会降低对胶料的剪切分散效果和混炼质量。
故应根据生胶种类和配方特点合理确定混炼温度,并使辊温控制在包辊性最好的温度范围以内进行混炼。
由于胶料在混炼过程中不断生热,应及时加强冷却调节辊温,使之始终保持在适宜温度范围内。
另外,为了便于操作,开炼机混炼时前后辊温度应保持5~l0℃温差。
由于天然橡胶容易包热辊,因而前辊温度应高于后辊。
多数合成胶容易包冷辊,故前辊温度应低于后辊。
同时,因合成橡胶混炼时生热量比天然橡胶多,故混炼时的两辊温度均应比天然橡胶低5~l0℃。
5.混炼时间开炼机混炼时间受开炼机转速和速比,容量和加药顺序,混炼的操作方法及混炼温度、胶种和配方的影响,混炼时间短,配合剂分散不良,胶料质量和性能差;混炼时间过长容易发生焦烧和过烧现象,也降低胶料质量和性能,生产效率也低。
适宜的混炼时间由试验确定,并应在保证混炼质量的前提下尽可能缩短混炼时间,以提高生产效率和节约能耗。
6.加药顺序配合剂的添加次序是影响开炼机混炼的最重要的因素之一。
加料顺序不当有可能造成配合剂分散不良,使混炼速度减慢,并有可能导致胶料出现焦烧和过烧现象,使混炼胶质量降低,甚至还会引起胶料发生脱辊现象而难以进行混炼操作。
所以加药顺序应根据混炼方法和工艺条件以及胶料配方特性合理确定。
加药顺序确定的一般原则是:
①用量少而在胶料中所起的作用又很大的配合剂如促进剂、活性剂、防老剂和防焦剂等应尽可能早加或先加。
生产实际中都是将这一类小药加在填料和液体软化剂的前面。
就是因为它们的用量虽少,但起的作用却很大,对其分散的均匀度要求高,故应先加,有些促进剂如胍类和噻唑类促进剂对生胶有增塑作用,先加有利于混炼;防老剂先加有利于防止胶料高温下混炼时的老化现象。
②在胶料中难以混合分散的配合剂,如氧化锌和固体软化剂,亦应适当早加,只是因软化剂容易使胶料产生脱辊,最好将其与粉料预混后再加入。
③临界温度低,化学活性大,对温度比较敏感的配合剂,如硫黄和超速促进剂应当在混炼后期降温后加入。
④硫黄与促进剂应当分开加入。
若混炼先加促进剂,则硫黄应在混炼过程最后加入;或者相反。
加药顺序是长期实践经验的积累和总结。
天然胶胶料开炼机混炼的一般加药顺序为:
①生胶、塑炼胶、母炼胶、再生胶;②固体软化剂如右马隆、松香、石蜡等;③促进剂活性剂、防焦剂和防老剂;④补强填充剂如炭黑、陶土和碳酸钙等;⑤液体软化剂如松焦油,酯类等;⑥硫黄。
当天然胶配方中的液体软化剂用量较少时,习惯上都是将液体软化剂加在填料之前。
合成胶因配方中的填料和液体软化剂用量比例较大,故液体软化剂一定要加在补强填充剂之后,或与液体软化剂交替分批加入。
其他基本相同。
对于某些特殊情况则必须对上述加药顺序作适当调整。
如硬质胶胶料混炼时硫黄必须先加才能保证其混合均匀,海绵胶混炼时则必须将液体软化剂放在最后加入,否则其他配合剂难以混合分散均匀。
丁腈橡胶混炼时亦应先加硫黄。
7.药品添加量粉状配合剂主要靠堆积胶的作用而被混入橡胶内部的。
当混炼初期堆积胶表面被粉剂完全覆盖时,混炼的吃粉速度是恒定不变的,随着堆积胶表面配合剂的不断混入,其数量逐渐减少,到不能完全覆盖推积胶表面时,配合剂的吃粉速度便开始减慢。
所以,为了加快混炼的吃粉过程,应尽可能把每次加药的数量添足一些,这样可以缩短混炼时间。
二、密炼机混炼工艺
与开炼机混炼相比,密炼机混炼工艺具有以下优点:
(1)自动化程度高,生产效率高,劳动强度低,操作安全;
(2)密闭操作,药品飞扬损失少,有利于胶料质量的保证,并改善丁操作环境条件;
(3)胶料中的炭黑分散度高,混炼胶质量均匀;
(4)同样产量所需机台数少,厂房面积减小。
故密炼机混炼特别适合于胶料配方品种变换少、生产批量大的现代化大规模生产。
密炼机混炼法的缺点是:
(1)混炼后机台不容易清洗,变换胶料配方困难;
(2)密闭条件下混炼,散热条件差,生热升温快,混炼温度高;容易发生焦烧和过烧现象;
(3)排胶不规则,需配备辅助设备进行补充加工处理,设备初投资较大,对厂房建筑要求高;
(4)不适于特殊胶料的混炼。
尽管如此,密炼机混炼方法仍然是制造炭黑混炼胶的最理想的混炼方式。
在现代橡胶工业生产中,凡是能用密炼机混炼者都已不再用开炼机混炼。
密炼机混炼已成为现代混炼工艺的主要而普遍的方式。
(一)胶料在密炼室中的流动状态和变形
以椭圆形转子的Banbury型密炼机为例。
由于密炼机转子结构的特殊几何形状,使得胶料在混炼过程中于密闭室内受到的剪切搅混作用非常剧烈,其流动状态和变形情况比开炼机复杂得多。
当密闭室内两转子相对回转时,将来自加料口的胶料夹住并通过辊缝使胶料受到挤压和剪切。
胶料穿过辊缝被挤压到密炼室底部后,碰到下顶栓的突棱时被分成两部分,分别沿前后室壁与辊筒之间再回到辊距上方。
在两转子不同速度作用下,两部分胶料以不同速度重新汇合。
由于转子表面有螺旋状突棱,使转子表面各处与转子轴心间距离不等,于是产生了不同的线速度,两转子间的速比也是变化的。
例如11号Banbury密炼机转子间的速比变化范围可达1/0.91~1.47,使胶料受到剧烈剪切和混合作用。
转子表面突棱与室壁之间的缝隙和两转子之间的缝隙也随着混炼过程而变化,其变化范围分别为2—83mm和4~166mm,因此胶料无法随转子表面等速旋转,而是随时变换速度和方向,从间隙小的地方向间隙大处湍流,从而使胶料在混炼过程中不仅绕转子表面作圆周运动,同时还沿转子的螺槽作轴向运动,从转子两端向中间捣翻,受到充分的混合。
但是,胶料在密炼室中的混合行为用形变而不是用流动来描述更为合适。
因为混炼时材料的形变很大,其形变往往超过极限应变。
材料破裂是该行为的重要组成部分。
因此,不可能用稳态的流动粘度来描述橡胶的行为,而必须考查大形变时的粘弹性能和极限性能。
在本伯里(Banbury)密炼机中的转子棱边与室壁之间,胶料经受的变形程度是最大的。
胶料在这里既有剪切变形,又有拉伸变形。
由于剪切变形可等效变换为拉伸变形,因此用拉伸变形即可描述橡胶在密炼机中混炼时的变形行为。
(二)密炼机混炼工艺操作方法密炼机混炼开始时提起上顶栓,按加药顺序规定依次将生胶和配合剂从加料口投入密闭室中,每次投料后都要放下上顶栓加压混炼一定时间后再提起上顶栓投加下一批材料。
直到混炼完毕。
放开下顶栓将胶料排至压片机加硫黄,并压成规则的一定厚度的胶片,进行冷却和停放。
密炼机混炼操作方法有三种:
一段混炼法、两段混炼法和逆混法。
1.一段混炼法一段混炼法就是将配方组分加入密炼机后整个混炼作业过程在密炼机上一次全部完成,中间没有胶料的压片、冷却和停放过程。
一段混炼法的优点是胶料管理比较方便,节省车间胶料停放面积,但所制得的混炼胶胶料的可塑度比较低,填料不易分散均匀,且混炼周期较长,排胶温度较难控制,容易发生焦烧和过炼现像,使混炼胶质量受到影响。
一般混炼法适用于胶料粘度较低,配方填充量较少的胶料混炼,如天然胶配方或以天然胶为主的并用胶配方含胶率高,适于采用一般混炼法。
一段混炼法又分为传统一段混炼法和母胶一段混炼法两种。
(1)传统一段混炼法该法的操作和工艺要点是:
按照规定的加药顺序采用分批逐步加料,对于用量较多的配合剂(如补强填充剂等)有时还得分几次投加。
每次加料之前先将上顶栓提起,加料后再放下上顶栓加压或浮动混炼一定时间。
加压程度依材料性质而定。
如投加生胶和再生胶后,就需施加较高的压力,投加粉状配合剂时则应先使上顶栓浮动后再加压,加压程度亦应适当减小,在加硬质炭黑时甚至可以不加压,以免胶料升温过高引起焦烧和防止受压过大而使粉剂结团。
一段混炼时为防止胶料升温过快,一般采用慢速密炼机。
炼胶周期一般在10~12min,个别情况如高填充配方可达14~16min。
最好采用双速或变速密炼机,混炼过程初期采用快速,在短时间内完成硫黄以外的各种配合剂的加料混炼过程,最后改用慢速使之冷却降温后再加硫黄。
采用在密炼机内直接加硫黄的关键是加炭黑之后做到有效的冷却降温,使排胶温度降到ll0℃以下。
实际生产中一般是在压片机上加硫黄,这时密炼机一段混炼的排胶温度通常控制在130℃以下,需将胶料排到开炼机上冷却到100℃以下再加硫黄翻炼和压片。
(2)母胶法一段混炼法中还可采用分批投加生胶的方法,以提高炭黑等填料的相对浓度来强化其分散效果,故此法又称母胶法。
具体操作方法又分以下两种:
第一种是先往密炼机中投加60%~80%的生胶和全部配合剂(不包括硫黄),在70~120℃下混炼至总混炼时间的70%~80%,制得母胶,然后投入其余生胶和塑炼胶,再混炼约1~2min排料。
投入的生胶和塑炼胶温度低,可使密炼室内胶料温度暂时降低15~20℃,能在混入热胶料的同时使部分炭黑从母胶中迁至后加的橡胶中。
该法制备混炼胶可提高剪切分散效果,并能有利于减小生热升温和防止发生焦烧,还可提高混炼机装填系数15%~30%和生产效率,提高混炼胶质量和硫化胶性能。
此法适用于异戊胶、氯丁胶、丁苯胶和丁腈胶混炼。
该法缺点是密炼机磨损较大。
第二种混炼过程:
将60%~80