柴油机齿轮室盖钻镗专机总体及主轴箱设计.docx
《柴油机齿轮室盖钻镗专机总体及主轴箱设计.docx》由会员分享,可在线阅读,更多相关《柴油机齿轮室盖钻镗专机总体及主轴箱设计.docx(22页珍藏版)》请在冰豆网上搜索。
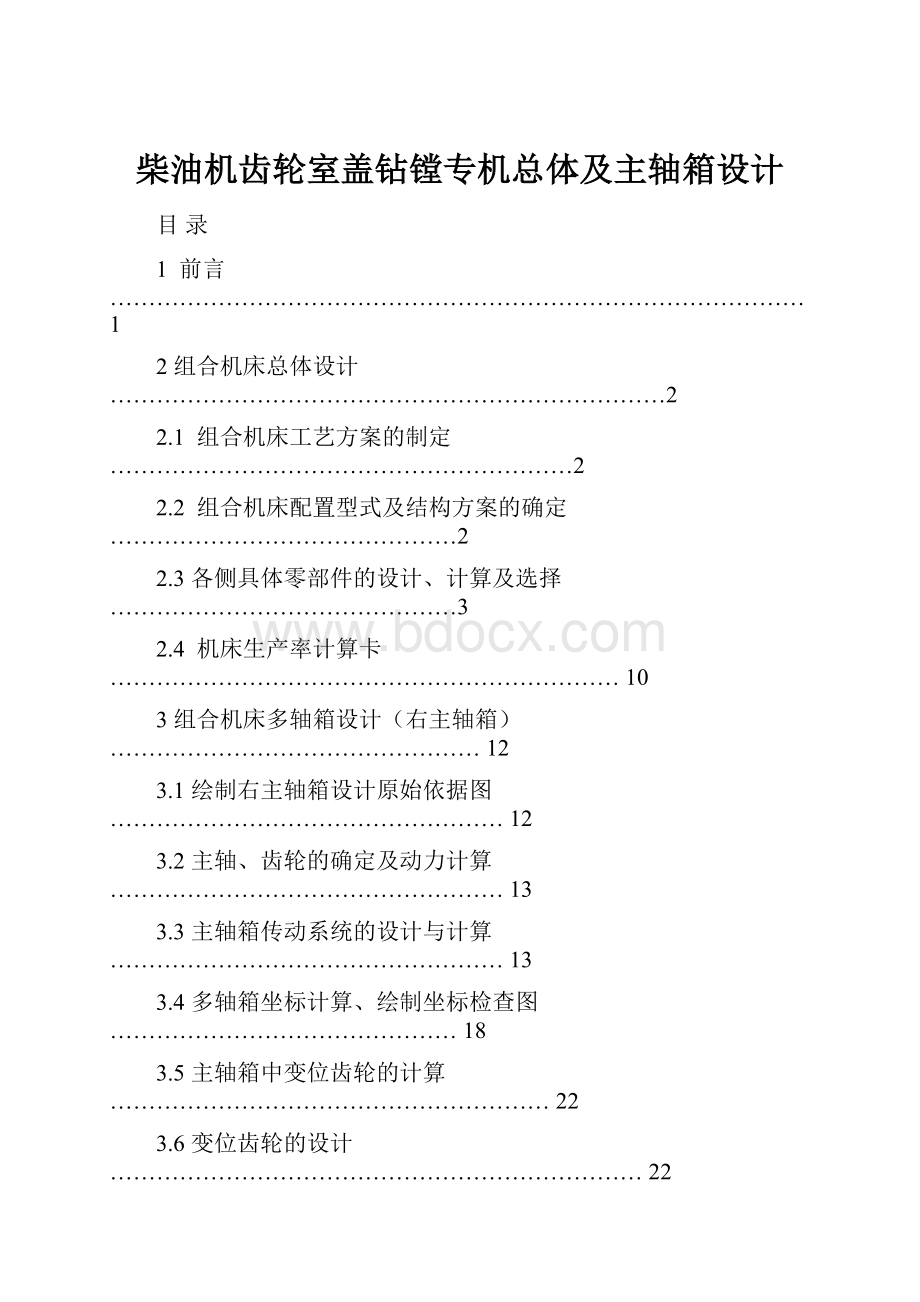
柴油机齿轮室盖钻镗专机总体及主轴箱设计
目录
1前言………………………………………………………………………………1
2组合机床总体设计………………………………………………………………2
2.1组合机床工艺方案的制定……………………………………………………2
2.2组合机床配置型式及结构方案的确定………………………………………2
2.3各侧具体零部件的设计、计算及选择………………………………………3
2.4机床生产率计算卡…………………………………………………………10
3组合机床多轴箱设计(右主轴箱)…………………………………………12
3.1绘制右主轴箱设计原始依据图……………………………………………12
3.2主轴、齿轮的确定及动力计算……………………………………………13
3.3主轴箱传动系统的设计与计算……………………………………………13
3.4多轴箱坐标计算、绘制坐标检查图………………………………………18
3.5主轴箱中变位齿轮的计算…………………………………………………22
3.6变位齿轮的设计……………………………………………………………22
3.7齿轮强度校核………………………………………………………………23
3.8传动轴直径的确定和轴的强度校核………………………………………25
3.9主轴箱体及其附件的选择设计……………………………………………28
4结论……………………………………………………………………………30
参考文献……………………………………………………………………………31
致谢…………………………………………………………………………………32
附录…………………………………………………………………………………33
1前言
组合机床是根据工件加工需要,以大量通用部件为基础,配以少量专用部件组成的一种高效率专用机床。
目前,组合机床主要用于平面加工和孔加工两类工序。
平面加工包括铣平面、锪(刮)平面、车平面;孔加工包括钻、扩、铰、镗孔以及倒角、切槽、攻螺纹、锪沉孔滚压孔等。
随着综合自动化的发展,其工艺范围正扩大到车外圆、行星铣削、拉削、推削、磨削、珩磨及抛光、冲压等工序。
此外,还可以完成焊接、热处理、自动装配和检测、清洗和零件分类及打印等非切削工作。
组合机床在汽车、拖拉机、柴油机、电机、仪器仪表、军工及缝纫机、自行车等轻工行业大批大量生产中已经获得广泛的应用;一些中小批量生产是企业,如机床、机车、工程制造业中也已推广应用。
组合机床最适宜于加工各种大中型箱体类零件,如汽缸盖、汽缸体、变速箱体、电机座及仪表壳等零件;也可用来完成轴套类、轮盘类、叉架类和盖板类零件的部分或全部工序的加工。
组合机床的设计,目前基本上有两种情况:
其一,是根据具体加工对象的具体情况进行专门设计,这是当前最普遍的做法。
其二,随着组合机床在我国机械行业的广泛使用,广大工人总结自己生产和使用组合机床的经验,发现组合机床不仅在其组成部件方面有共性,可设计成通用部件,而且一些行业在完成一定工艺范围内组合机床是极其相似的,有可能设计为通用机床,这种机床称为“专能组合机床”。
这种组合机床就不需要每次按具体加工对象进行专门设计和生产,而是可以设计成通用品种,组织成批生产,然后按被加工的零件的具体需要,配以简单的夹具及刀具,即可组成加工一定对象的高效率设备。
本次毕业设计课题来源于生产实际,具体的课题是柴油机齿轮室盖钻镗专机总体及主轴箱设计。
在设计前认真研究被加工零件的图样,研究其尺寸、形状、材料、硬度、重量、加工部位的结构及加工精度和表面粗糙度要求等内容,为设计提供大量的数据、资料,作好充分的、全面的技术准备。
在准备了充足的资料之后进行总体及零部件的设计工作,总体的设计的主要工作是完成“三图一卡”,即绘制机床的总体尺寸联系图、加工示意图、零件的工序图及编制生产率计算卡;主轴箱设计的方法是:
绘制主轴箱设计的原始依据图;确定主轴的结构、轴颈及齿轮模数;拟订传动系统;计算主轴、传动轴坐标,绘制坐标检查图;绘制多轴箱总图,零件图及编制组件明细表。
在此次的设计中采用“一面两销”定位,液压夹紧,提高了生产效率,降低了劳动强度,同时在设计中采用了大量的通用零部件,降低了产品的成本。
在设计过程中,得到了刘道标老师的大力指导和同课题组同学的热情帮助,在此谨致谢意。
限于本人水平和经验,本设计中一定有错误和不妥之处,敬请批评指正。
2组合机床总体设计
组合机床总体设计,通常是根据与用户签定的合同和技术协议书,针对具体加工零件,拟订工艺和结构方案,并进行方案图样和有关技术文件的设计。
2.1组合机床工艺方案的制定
工艺方案的拟订是组合机床设计的关键一步。
因为工艺方案在很大程度上决定了组合机床的结构配置和使用性能。
因此,应根据工件的加工要求和特点,按一定的原则、结合组合机床常用的工艺方法、充分考虑各种因素,并经技术经济分析后拟订出先进、合理、经济、可靠的工艺方案。
此次设计的组合机床是用于加工柴油机齿轮室盖的钻镗专用组合机床,其工艺方案为钻孔和镗孔,其具体的加工工艺如下:
a.钻6-M6-6H孔至Φ5,左侧面;
b.钻6-Φ9孔(深38),右侧面;
c.钻3-Φ9孔(深78),右侧面;
d.镗Φ45H8孔至Φ43.5,后侧面;
e.倒孔口角至Φ46.6,后侧面;
正确选择组合机床加工工件采用的基准定位,是确保加工精度的重要条件。
本设计的柴油机齿轮室盖是箱体类零件,箱体类零件一般都有较高精度的孔和面需要加工,又常常要在几次安装下进行。
因此,定位基准选择“一面双孔”是最常用的方法,因此该被加工零件采用“一面两销”的定位方案,定位基准和夹压点见零件的工序图。
该定位方案限制的自由度叙述如下:
以工件的右侧面为定位基准面,约束了y、z向的转动和x向的移动3个自由度。
短定位销约束了y、z向的移动2个自由度。
长定位销约束了x向的转动1个自由度。
这样工件的6个自由度被完全约束了也就得到了完全的定位。
2.2组合机床配置型式及结构方案的确定
根据选定的工艺方案确定机床的配置型式,并定出影响机床总体布局和技术性能的主要部件的结构方案。
既要考虑能实现工艺方案,以确保零件的精度、技术要求及生产率,又要考虑机床操作方便可靠,易于维修,且润滑、冷却、排屑情况良好。
对同一个零件的加工,可能会有各种不同的工艺方案和机床配置方案,在最后决定采取哪种方案时,绝不能草率,要全面地看问题,综合分析各方面的情况,进行多种方案的对比,从中选择最佳方案。
各种形式的单工位组合机床,具有固定式夹具,通常可安装一个工件,特别适用于大、中型箱体类零件的加工。
根据配置动力部件的型式和数量,这种机床可分为单面、多面复合式。
利用多轴想同时从几个方面对工件进行加工。
但其机动时间不能与辅助时间重合,因而生产率比多工位机床低。
在认真分析了被加工零件的结构特点及所选择的加工工艺方案,又由单工位组合机床的特点及适应性,确定设计的组合机床的配置型式为单工位卧式组合机床。
2.3各侧具体零部件的设计、计算及选择
2.3.1刀具的选择
考虑到工件加工尺寸精度,表面粗糙度,切削的排除及生产率要求等因素,所以加工15个孔的刀具均采用标准锥柄长麻花钻和单导向悬臂镗刀。
2.3.2右侧面钻9-Φ9
a.切削用量的选择
右侧是钻削6-Φ9(深38)及3-Φ9(深78)
根据孔径的大小和深径比,以及被加工材料的硬度查参考文献[9]表2.17知:
主轴的进给量f为0.1~0.18mm/r,切削速度vc=10~18m/min。
钻孔的切削用量还与钻孔的深度有关,当加工铸铁件孔深为钻头直径的6~8倍时,在组合机床上通常都是和其他浅孔一样采取一次走刀的办法加工出来的,不过加工这种较深孔的切削用量要适当降低些,因此选择切削速度vc=13m/min进给量f=0.13mm/r,由此主轴转速n由公式
(2-1)
计算出
r/min,将主轴转速圆整为470r/min。
实际切削速度vc、工进速度vf、工进时间tf分别由下列公式求得
(2-2)
(2-3)
(2-4)
计算出实际切削速度vc=13.282m/min,工进速度vf=61.1mm/min,工进时间tf=1.26min
b.切削功率,切削力,转矩以及刀具耐用度的选择
由参考文献[9]表6-20计算公式
切削力
(2-5)
切削转矩
(2-6)
切削功率
(2-7)
刀具耐用度
(2-8)
计算出切削力F=1144.5N,切削转矩T=3.18N·m,切削功率P=0.153kw,刀具耐用度Tn=768.799min
c.动力部件的选择
由上述计算每根轴的输出功率P=0.153kw,右侧共9根输出轴,且每一根轴都钻Φ9直径,所以总切削功率P切削=0.153×9=1.377kw。
则多轴箱的功率:
kw,其中η=0.8,所以
kw。
因电机输出经动力箱时还有功率损耗,所以选择功率为2.2kw的电机,其型号为:
Y100L1-4,由参考文献[9]表5-39选取1TD32-I型动力箱,动力箱的主轴转速715r/min。
d.确定主轴类型,尺寸,外伸长度
滚珠轴承主轴:
前支承为推力球轴承和向心球轴承,后支承为向心球轴承或圆锥滚子轴承。
因为推力轴承设置在前端,能承受单方向的轴向力,适用于钻孔主轴。
在右侧面,主轴用于钻孔,因此选用滚珠轴承主轴。
又因为浮动卡头与刀具刚性连接,所以该主轴属于长主轴。
所以主轴均为滚珠轴承长主轴。
根据主轴转矩T=3.18N·m,由参考文献[9]表3-4可知
(2-9)
其中B=7.3,则计算出d=17.335mm,选取d=20mm。
由参考文献[9]表3-6查得主轴直径d=20mm,D/d1=30/20mm,主轴外伸尺寸L=115mm,接杆莫氏圆锥号1,2。
e.导向装置的选择
组合机床钻孔时,零件上孔的位置精度主要是靠刀具的导向装置来保证的。
导向装置的作用是:
保证刀具相对工件的正确位置;保证刀具相互间的正确位置;提高刀具系统的支承刚性。
固定式导套:
刀具或刀杆本身在导套内既有相对转动又有相对移动,由于这部分表面润滑困难;工作时有粉尘侵入,当刀杆相对导套的线速度超过20m/min时就会有研着的危险,因此选用导套前计算一下导套与刀具的线速度。
由上述内容知导套与刀具的线速度vc=13.282m/min<20m/min,所以该导套选用通用短导套
由参考文献[9]表8-4查得导套的具体数值如下:
D=15mm,D1=22mm,D2=26mm,D3=M6,L取16mm,(短型导套)l=8mm,l1=3mm,l3=12mm,e=18.5mm
f.连杆的选择
在钻、扩、铰孔及倒角等加工小孔时,通常都采用接杆(刚性接杆)。
因为主轴箱各主轴的外伸长度和刀具均为定值,为保证主轴箱上各刀具能同时到达加工终了位置,须采用轴向可调整的接杆来协调各轴的轴向长度,以满足同时加工完成孔的要求。
为了获得终了时多轴箱前端面到工件端面之间所需要的最小距离,应尽量减少接杆的长度。
因为9-Φ9孔的钻削面是同一面且主轴内径是20mm,由参考文献[9]表8-1选取A型可调接杆d=16mm,d1=Tr16×1.5mm,d2=9mm,L=85mm,l4=110~135mm。
g.动力部件工作循环及行程的确定
切入长度一般为5-10mm,取L1=7mm,切出长度由参考文献[9]表3-7公式
(2-10)
通过计算L2=8mm,加工时加工部位长度L(多轴加工时按最长孔算)L=78mm.由公式
(2-11)
求出L工=93mm。
为排屑要求必须钻口套与工件之间保留一点的距离,根据麻花钻直径Φ9,由参考文献[9]表3-4得导套口至工件尺寸l2=(1+1.5d)(参考钻钢)取l2=10mm,又根据钻套用导套的长度确定钻模架的厚度为16mm。
附带得出底面定位元件的厚度l4=38mm。
快退长度的确定:
一般在固定式夹具钻孔或扩孔的机床上动力头快速退回的行程只要把所有的刀具都退回至导套内,不影响工件装卸即可。
快退距离L快退=l2+L工-L1=10+93-7=96mm
快进距离L快进=l2-L1=10-7=3mm
因快进距离太短,故将快进距离改为工进,则工进距离L工=93+3=96mm。
选择刀具:
根据钻口套至工进行程末端的距离L快退=96mm,及钻口套长度L套=8+3+16=27mm,由参考文献[5]表3-1查得选择:
矩形柄麻花钻GB1435-78Φ9×250mm(切削长度部分145mm)。
h.滑台及底座的选择
由于液压驱动,零件损失小,使用寿命长,所以选择液压滑台。
已知工进Vf=61.1mm/min,单根主轴的切削力F单=1144.5N,则9根轴总的切削力F切削=9F单=1144.5×9=10300.5N,又因为ITD32-Ⅰ型动力箱滑鞍长度L=630mm,由参考文献[9]表5-1选择1HY32-Ⅰ型滑台及配套的侧底座选择ICC321
i.多轴箱轮廓尺寸的设计
确定机床的装料高度,新颁国家标准装料高度为1060mm,实际设计时常在850~1060mm之间选取,选取装料高度为950mm。
多轴箱的宽度与高度的大小与被加工零件的加工部位有关,可按下列关系式确定:
B=b+2b1(2-12)
H=h+h1+b1(2-13)
b-工件在宽度方向相距最远两孔距离,b=340mm。
b1-最边缘主轴中心距箱体外壁的距离,推荐b1≥70~100mm,取b1=100。
h-工件在高度方向相距最远的两孔距离,h=277mm。
h1-最低主轴高度。
因为滑台与底座的型号都已经选择,所以侧底座的高度为已知值650mm,
滑台滑座总高280mm;滑座与侧底座的调整垫厚度一般取5mm,多轴箱底与滑台滑座台面间的间隙取0.5mm。
故h1=11+950-(0.5+5+280+560)=115.5mm,通常推荐h1〉85~140mm,所以h1=115.5mm符合通常推荐值。
所以B=b+2b1=340+2×100=540mm,
H=h+h1+b1=277+115.5+100=492.5mm
由此数据查参考文献[15]表8.22选取多轴箱尺寸B×H=630mm×500mm,台面宽度为320mm。
2.3.3左侧面钻6-Φ5
a.切削用量的选择
根据参考文献[9]查表6-11高速钢钻头切削用量,加工材料铸铁,孔径d=1~6mm,切削速度10~18m/min,进给量f=0.05~0.1mm/r。
取切削速度vc=16m/min,进给量f=0.08mm/r,主轴的转速、实际切削速度、工进速度、工进时间分别由公式(2-1)、(2-2)、(2-3)、(2-4)求得
转速
r/min,将其圆整为1100r/min。
实际切削速度
m/min
工进速度
mm/min
工进时间
其中h为6-Φ5的深度。
b.切削功率,切削力,转矩以及刀具耐用度的选择
刀具的切削力、切削转矩、切削功率及刀具耐用度分别由公式(2-5)、(2-6)、(2-7)、(2-8)求得
切削力
N
切削转矩
N·m
切削功率
kw
刀具耐用度
c.动力部件的选择
由上述计算每根轴的输出功率P=0.0797kw,左侧共6根输出轴,且每一根轴都钻Φ5直径,所以总切削功率P切削=0.0797×6=0.598kw。
则多轴箱的功率:
kw,其中η=0.8,所以
kw
因电机输出经动力箱时还有功率损耗,所以选择功率为1.5kw的电机,其型号为:
Y100L-6,由参考文献[9]表5-39选取1TD25-IA型动力箱,动力箱的主轴转速为520r/min。
d.确定主轴类型、尺寸、外伸长度
根据主轴转矩T=0.70593N·m,由公式(2-9)求出满足条件的最小直径
mm(B=7.3)
选取d=15mm,由参考文献[9]表3-6查得主轴直径=15mm,D/d1=25/16mm,主轴外伸尺寸L=85mm,接杆莫氏圆锥号1。
e.导向装置的选择
查参考文献[9]表8-4选用通用短型导套,具体参数的数值:
D=10mm,D1=15mm,D2=18mm,D3=M6,L取12mm,l=8mm,l1=3mm,l3=12mm,e=14.5mm选用通用导套。
f.连杆的选择
为了获得终了时多轴箱前端面到工件端面之间所需要的最小距离,应尽量减少接杆的长度。
因为6-Φ5孔的钻削面是同一面且主轴内径是15mm,查参考文献[9]表8-1选取A型可调接杆d=10mm,d1=Tr10×1.5mm,d2=6mm,L=62mm,l4=72~82mm。
g.动力部件工作循环及行程的确定
切入长度一般为5-10mm,取L1=8mm;因为该6-Φ5孔为盲孔,所以刀具没有切出长度,所以切出长度L2=0mm。
加工时加工部位长度L(多轴加工时按最长孔计算)L=16mm,由公式(2-11)求出L工=24mm
为排屑要求必须钻口套与工件之间保留一点的距离,根据麻花钻直径Φ5,由参考文献[9]表3-4知导套口至工件尺寸l2=(1+1.5d)及综合考虑装卸工件的空间要求取l2=50mm,又根据钻套用导套的长度确定钻模架的厚度为12mm。
快退长度的确定:
一般在固定式夹具钻孔或扩孔的机床上动力头快速退回的行程只要把所有的刀具都退回至导套内,不影响工件装卸即可。
快退距离L快退=l2+L工-L1=50+24-8=66mm
快进距离L快进=l2-L1=50-8=42mm
h.滑台及底座的选择
已知工进vf=88mm/min,单根主轴的切削力F单=430.879N,则6根轴总的切削力F切削=6F单=6×430.879=2585.274N,又因为1TD25-IA型动力箱滑鞍长度L=500mm,由参考文献[9]表5-1选择1HY25-Ⅱ型滑台及它的侧底座选择ICC251,其相应的数值查表5-3可得:
台面宽度250mm,台面长度500mm,行程400mm,最大进给力8000N,工进速度32~800mm/min,快速移动速度12m/min。
i.多轴箱轮廓尺寸的设计
多轴箱的宽度与高度的大小与被加工零件的加工部位有关,计算方法同确定右侧钻九孔的主轴箱轮廓的方法一致,取b1=100mm,工件在高度方向相距最远的两孔距离h=209mm。
装料高度取950mm,工件最低孔距定位基准面的距离为11mm,
因为滑台与底座的型号都已经选择,所以侧底座的高度为已知值:
650mm,
滑台滑座总高:
280mm;滑座与侧底座的调整垫厚度一般取5mm,多轴箱底与滑台滑座台面间的间隙取0.5mm。
故h1=11+950-(0.5+5+280+560)=115.5mm,通常推荐h1〉85~140mm,所以h1=115.5mm符合通常推荐值。
所以B=b+2b1=264.2+2×100=464.2mm,
H=h+h1+b1=209+115.5+100=424.5mm。
由此数据查参考文献[15]表8.22选取多轴箱尺寸B×H=500mm×500mm,,台面宽度为320mm。
2.3.4后侧镗Φ45H8孔至Φ43.5,倒孔角Φ46.6
a.切削用量的选择
由参考文献[9]表6-15查得用高速纲刀具粗镗铸铁的切削用量:
v=20~25m/min,f转=0.25~0.8mm/r,则选取v=20mm/min,f转=0.4mm/min,由此由公式(2-1)求出镗刀的转速:
n=146.35r/min,圆整为n=150r/min,则实际切削速度vc由公式(2-2)求得vc=20.5m/min,工进速度vf=nf=150×0.4=60mm/min
b.切削力,切削转矩,切削功率及刀具耐用度的计算
刀具的切削力、切削转矩、切削功率及刀具耐用度分别由以下公式求出
Fz=51.4apf0.75HB0.55(2-14)
Fx=0.51ap1.2f0.65HB1.1(2-15)
T=25.7Dapf0.75HB0.55(2-16)
(2-17)
Fz=51.4×1×0.40.75×2140.55=494.58N
Fx=0.51×11.2×0.40.65×2141.1=102.89N
T=25.7×43.5×0.40.75×2140.55=10757N·mm
kw
c.确定主轴类型、尺寸、外伸长度
滚锥轴承主轴:
前后支承均为圆锥滚子轴承。
这种轴承可承受较大的径向和轴向力,且结构简单、装配调整方便,广泛用于扩、镗、铰孔和攻螺纹等加工。
因此选用滚锥轴承主轴。
由公式(2-9)求出满足条件的最小直径
mm
再由参考文献[9]表3-6查取d=25mm,D/d1=40/28mm,主轴的外伸尺寸为75mm
d.确定镗杆直径
由镗孔直径为Φ43.5mm,参考参考文献[5]表2.5-4选取镗杆的直径为Φ35mm,镗刀方截面直径为10×10
e.浮动卡头的选择
根据轴外径Φ40mm,内径Φ28mm,由参考文献[9]图8-2选择浮动卡头D×p=Tr28×3,根据镗孔形式为单导向悬臂孔,采用较为普遍的内滚式单导向悬臂镗孔,根据卡头内径尺寸d=Φ22mm及镗孔直径为Φ43.5mm,及倒角直径Φ46.6mm确定滑套的径向尺寸d1=Φ53mm
f.导向装置的选择
由参考文献[9]表3-4查得导套的总长度:
l1=106~159mm,导套口至工件的距离20~50mm,取导套的长为150mm,选取导套口至工件的距离为50mm
g.工作循环及行程的确定
由于该动力箱只加工Φ45H8及倒角,故行程主要由镗孔Φ45H8至Φ43.5决定工作进给长度,切入长度一般为5-10mm,取L1=8mm,L2=5-10mm,取L2=8mm,切出长度由参考文献[9]表3-7查得,加工长度L根据零件图可知Φ45H8孔深13mm,算出工作进给L工=8+13+8=29mm
快退长度的确定:
一般选固定式夹具或钻孔或扩孔机床上,动力头快速退回行程只要将所有的刀具都退回至导套内,不影响工件装卸即可,故快退尺寸由以下尺寸链可知
图2-1快进、快退尺寸链图
l快退=50+13+8=71mm,l快进=50-8=42mm
h.动力部件的选择
由上文算出镗削Φ43.5mm孔的输出功率P切削=0.166kw,设多轴箱的传递效率η=0.85,则动力头输入多轴箱的功率P多=
kw
根据多轴箱功率P多=0.195kw,由参考文献[9]表5-38,选用1TD25-IA型动力箱驱动(n马达=520r/min,电机选Y100L-6型,功率为1.5kw)
已知工进Vf=60mm/min,进给力Fz=494.58N,又因1TD25-IA型动力箱的滑鞍长L=320mm,,由参考文献[9]表5-1选择1HY25型滑台及配套后底座1CC251。
i.多轴箱轮廓尺寸的设计
多轴箱的宽度和高度的确定方法同右侧钻九个孔的确定方法,由于后侧镗只有一个孔所以b=0mm,h=0,推荐b1≥70~100mm,取b1=100。
卧式组和机床上的多轴箱最低主轴高度h1等于工件最低孔距工件定位基准面的尺寸与机床装料高度之和与侧底座高度、滑座与侧底座间的调整垫厚度(一般取5mm)、滑台滑座总高、多轴箱底与滑台滑座台面间的间隙(取0.5mm)之和的差值。
分析零件图知工件最低距定位基准面的距离为68mm,选取装料高度为950mm,因为滑台与底座的型号都已经选择,所以侧底座的高度为已知值:
560mm,
滑台滑座总高:
280mm;滑座与侧底座的调整垫厚