Ankowrap碳纤维补强施工验收规范 07060304修改.docx
《Ankowrap碳纤维补强施工验收规范 07060304修改.docx》由会员分享,可在线阅读,更多相关《Ankowrap碳纤维补强施工验收规范 07060304修改.docx(15页珍藏版)》请在冰豆网上搜索。
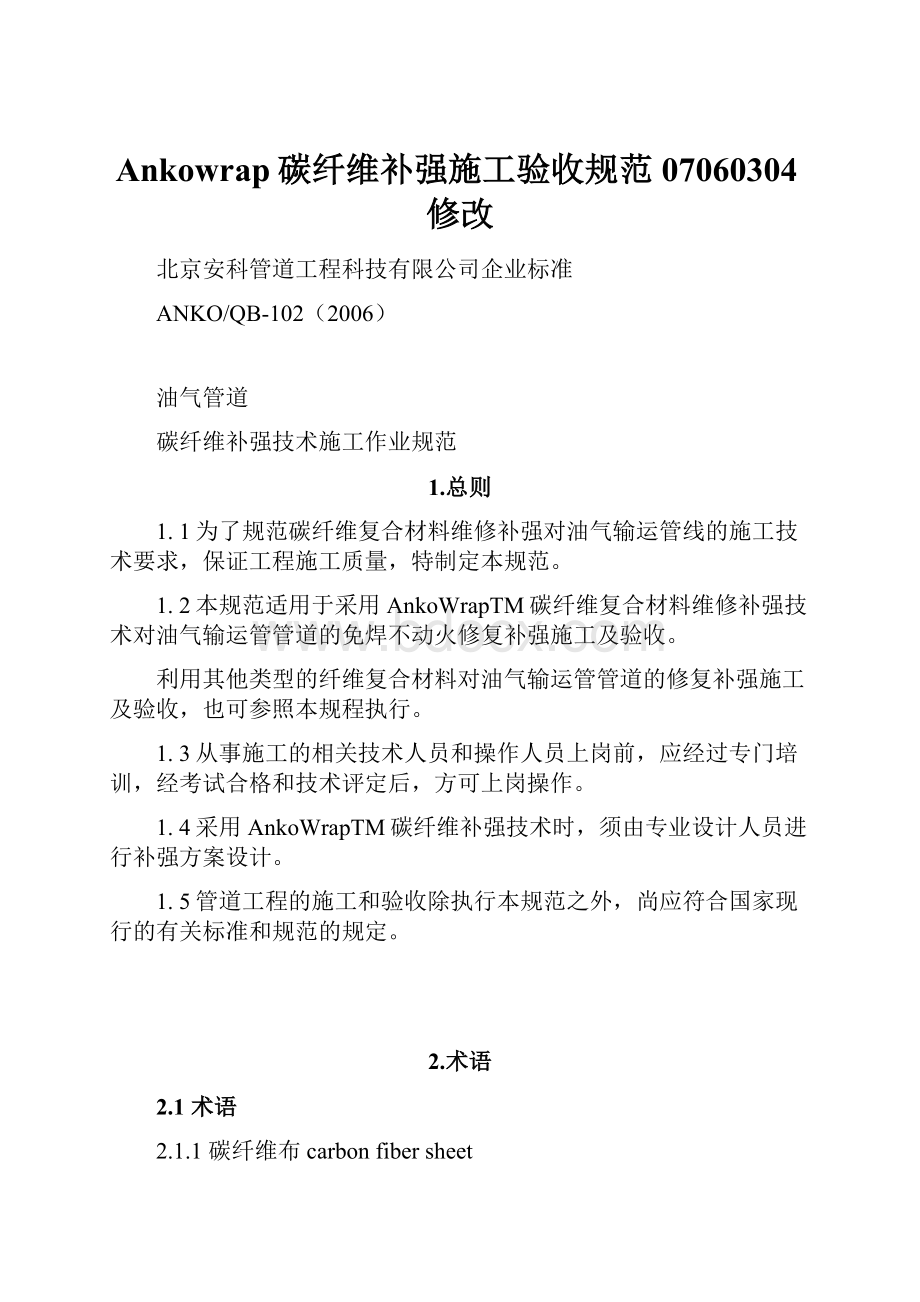
Ankowrap碳纤维补强施工验收规范07060304修改
北京安科管道工程科技有限公司企业标准
ANKO/QB-102(2006)
油气管道
碳纤维补强技术施工作业规范
1.总则
1.1为了规范碳纤维复合材料维修补强对油气输运管线的施工技术要求,保证工程施工质量,特制定本规范。
1.2本规范适用于采用AnkoWrapTM碳纤维复合材料维修补强技术对油气输运管管道的免焊不动火修复补强施工及验收。
利用其他类型的纤维复合材料对油气输运管管道的修复补强施工及验收,也可参照本规程执行。
1.3从事施工的相关技术人员和操作人员上岗前,应经过专门培训,经考试合格和技术评定后,方可上岗操作。
1.4采用AnkoWrapTM碳纤维补强技术时,须由专业设计人员进行补强方案设计。
1.5管道工程的施工和验收除执行本规范之外,尚应符合国家现行的有关标准和规范的规定。
2.术语
2.1术语
2.1.1碳纤维布carbonfibersheet
连续碳纤维单向或多向排列,未经树脂浸渍的布状制品。
2.1.2填平材料putty
用于对管道表面缺陷或不规则几何形状进行找平处理的材料。
2.1.3粘接树脂adhesives
用于粘贴碳纤维布的树脂
3.补强施工
3.1一般规定
3.1.1碳纤维复合材料维修补强技术适用于内部介质为煤气、天然气、原油、成品油、水等输送管道的维修补强。
3.1.2碳纤维复合材料维修补强技术适用于钢管、铸铁管、PE管以及水泥等材质的管道的维修补强。
3.1.3.碳纤维复合材料维修补强技术的应用不受被补强管道管径以及管道内部压力的限制。
3.1.4碳纤维复合材料维修补强技术可以修复的缺陷类型包括:
外腐蚀缺陷、裂纹、机械损伤(凹陷、沟槽等)、焊缝缺陷、材质缺陷;碳纤维复合材料维修补强技术可用于对内腐蚀管道的临时增强,也可用于对管道的提压增强处理。
3.1.5经碳纤维复合材料维修补强技术施工后的管道,需要采取适当的外防腐措施。
3.1.6施工方应对碳纤维复合材料维修补强技术的适用温度范围进行说明。
3.2材料
施工用补强材料为ANKO碳纤维、填平树脂和粘结树脂。
补强材料及其各种性能示于表1至表3。
表1ANKO碳纤维布的规格性能
品名
纤维种类
碳纤维面积重量(g/m2)
设计厚度
(mm)
抗拉强度
(MPa)
弹性模量
(MPa)
延伸率
(%)
ANKO-C-30
高强度碳纤维
300
0.167
3500
2.35×105
1.5
表2ANKO缺陷填平树脂的规格性能
内容
填平树脂
ANKO-200W(冬用)
ANKO-200S(夏用)
主剂与固化剂配比
2∶1
2∶1
环境温度℃
-15~15
15~60
可使用时间(分钟)
30~160
50~210
指触干燥时间(小时)
1.5~10
1.5~10
形状
腻子状
性能指标
钢钢粘结抗剪强度
(MPa)
钢钢粘结抗拉强度(MPa)
胶体抗压强度
(MPa)
≥10
/
≥50
主要用途
修补钢管表面缺陷
表3ANKO碳纤维复合材料性能
项目名称
指标
性能指标
抗拉强度(MPa)
≥3400
弹性模量(MPa)
≥2.4×105
伸长率(%)
≥1.7
弯曲强度(MPa)
≥700
层间剪切强度(MPa)
≥45
3.3管道资料调查及补强方案制定
3.3.1管道原始资料调查
3.3.1.1管道材质、管径、壁厚及使用年限
3.3.1.2管道运行记录
管道输送介质,压力,温度,流速等
3.3.1.3管道维修或改造资料
管道维修记录和竣工资料
3.3.2补强方案制定
3.3.2.1在甲方对需要补强点进行定点、挖坑和缺陷尺寸测试的基础上,核实缺陷的大小和类型,包括缺陷的长度、宽度和深度。
3.3.2.2根据缺陷的大小和类型,利用剩余强度评价软件及其有限元数值分析等相关方法,评价含该缺陷管道的强度损失。
3.3.2.3根据碳纤维复合材料的力学性能,在3.3.2.2对强度损失评价的基础上,针对各个缺陷,分别制定出复合材料补强方案,使其达到管道腐蚀损伤前的强度水平。
3.3.3施工现场环境调查
3.3.3.1现场环境相对湿度:
<85%,可以直接施工;>85%时需要对管体采取干燥措施或者对环境进行改善处理。
3.3.3.2现场环境温度:
-15℃~60℃,在该温度范围内,可以使用安科管道不同型号的粘结树脂直接施工;当环境温度超过该范围时,可以对施工地点采用环境改善措施进行改造后便可施工。
3.3.3.3管道输送压力:
不停输、不降压
3.3.4施工所需车辆、机械、器具及工具检查
表4施工所需机械、器具、工具一览表
种类
名称
车辆
工具车、越野车
管道开挖复查
十字镐、铁锹、超声波测厚仪
管道表面处理用具
刀、砂布、钢丝刷、刨刃、电刷、砂轮、丙酮
纤维裁切工具
卷尺、钢直尺、壁纸刀、剪刀
调和及涂刷树脂用具
台秤、搅拌容器、橡胶抹子、滚筒刷子、油漆刷、搅拌器、抹灰板
粘贴及脱泡用工具
脱泡罗拉、毛罗拉、橡胶刮板、塑料刮板
安全用具
工作服、橡胶手套、线手套
其他
可燃气体报警仪、发电机、电源线、插座、养护材料、棉纱、帆布帐篷
3.4补强施工作业规程
3.4.1施工程序
(1)现场开挖
(2)剥离防腐层
(3)管道表面清理
(4)基层处理
(5)缺陷修补
(6)涂刷粘浸剂
(7)粘贴碳纤维片
(8)补口及补强层防护
(9)作业区域固化
(9)土壤回填复原
3.4.2施工步骤说明
3.4.2.1缺陷定位及现场开挖
对内检测提供的缺陷进行定位,然后在现场监护人员的监护下进行人工开挖。
开挖过程中注意测量埋深,防止铁器损坏防腐层及钢管。
图1是挖坑所需尺寸剖面图。
管沟开挖长度为缺陷修复点里程前后各加2m。
图1现场补强施工开挖剖面示意图
3.4.2.2管道防腐层剥离与表面清理
在现场开挖复查工作完成后,对有缺陷的钢管表面防腐层进行清除。
具体操作方法是:
用砂布、钢丝刷、刨刃、电刷等工具清除防腐层,直至清除到钢管裸露部位。
必要时用专用试剂进行清除。
如果管道腐蚀情况较严重,在进行表面清理时,应考虑降压操作。
若遇有阴极保护测试桩,应取下测试桩连接线,补强施工完毕后,应对阴极保护测试桩进行原样恢复。
3.4.2.3基层处理
管材的表面基层处理一般应在补强之前的4个小时内进行完毕,以避免表面再氧化的发生。
在确保钢管表面原有防腐涂层及氧化物清除后,用清洗剂清洗钢管表面,并使其充分干燥。
基层预处理质量应达到GB/T8923—1988中规定的St3级。
施工前在需补强部位放线、定位。
3.4.2.4缺陷尺寸测量及照相
缺陷点开挖剥离防腐层后,应先对其进行确认,利用直尺、超声波测厚仪查对缺陷长度、宽度及壁厚,并照相存档,然后再进行补强修复。
对于外腐蚀缺陷点,在剥离防腐层后,使用卡尺、测深尺等工具测量确认;对于内腐蚀缺陷点,利用超声波测厚仪器进行确认。
3.4.2.5钢管表面的缺陷修补
(1)根据施工部位的温度、湿度,选择适当的ANKO填平树脂。
(2)将调配好的填平树脂计量、搅拌均匀,根据实际气温决定用量并控制使用时间。
(3)将填平树脂涂刷于钢管表面凹陷部位(蜂窝、麻面、小孔等),修补至缺陷部位表面平整。
(4)对于焊缝根部两边,应使用填平树脂进行填充,以使焊缝附近表面平滑过渡,避免由于焊缝过高而引起碳纤维粘贴时空鼓。
3.4.2.6碳纤维布粘贴
(1)碳纤维布裁剪。
碳纤维片材在裁剪过程中容易受损,因此,裁剪时应使用钢直尺、壁纸刀或者剪刀。
严格按设计要求的尺寸及层数裁剪碳纤维布。
为防止片材在保管、运输过程中损坏,片材的裁切数量应以当天的用量为准。
(2)此技术采用的碳纤维布为单向布,如果施工具有环向接头,则碳纤维片的环向接头必须搭接100mm以上。
环向缠绕时,如果具有轴向接头,则接头在轴向方向不需要搭接。
(3)配胶。
将环氧粘浸胶的主剂与固化剂按规定比例称量准确后放入容器内,用搅拌器搅拌均匀。
一次配胶量应以在可使用时间内用完为准。
建议配胶量以每次小于2.5公斤为宜。
(4)涂胶。
贴片前用滚筒刷(或油漆刷)将调配好的粘浸树脂均匀涂抹于待粘贴的部位,有搭接的部位应多涂刷一些。
(5)粘贴绝缘纤维片。
贴片时,在纤维片和树脂之间不应残留有空气。
(6)粘贴碳纤维片。
贴片时,在碳纤维片和树脂之间不应残留有空气。
确保没有空鼓现象出现。
(7)需要粘贴两层以上碳纤维时,重复(4)、(6)步骤。
3.4.2.7补口及补强层防护
(1)在碳纤维片粘贴完成后,对已剥除防腐层但未粘贴碳纤维片的区域,涂刷环氧粘浸胶。
如原防腐层厚度过大或原防腐层与补强层厚度差距较大,应采用ANKO填平树脂进行填平过渡;填平树脂初步固化后,再进行防腐处理。
(2)根据现场情况采用聚乙烯胶粘带、热收缩带或其他防腐措施对这一区域进行防护。
缠绕层与原防腐层的搭接宽度应不少于100mm。
缠绕时胶粘带边缝应平行,不得扭曲皱折。
缠绕过程中搭接宽度不小于25mm为宜。
3.4.2.8作业区域固化
(1)补强作业区域的防护修复施工完成后,使作业区域的树脂进一步固化,并应保证固化期间不受干扰。
(2)在作业区固化期间,宜用塑料薄膜等遮挡以防风沙或雨水侵袭。
(3)当树脂固化期间存在气温降低到5℃以下的可能时,可采用冬用低温固化树脂,或采取有效的加温措施。
(4)碳纤维片粘贴后可以回填的时间为1-3天,具体时间取决于环境温度以及管道内部输送介质的温度,只要达到固化就可以回填。
(5)如果在修复前管道进行了降压操作,则须在补强材料固化后再恢复管道的运行压力。
3.4.2.9安装智能检测提示装置
为了保证在下一次进行管道智能检测时,能够对补强修复的缺陷和其它未被修复缺陷点进行区分,在补强施工完成后应加装智能检测提示装置。
此步骤为可选择项,根据业主的需求实施。
智能检测提示金属条安装在复合材料的边缘两端,安装完毕后需进行防腐处理。
3.4.2.10回填
当补强层固化后,采用电火花检漏仪在确认开挖管段无漏点的情况下,采用细沙或素土进行分层夯实回填,并对现场进行清理恢复地形原貌,保证管线埋深达到设计要求。
3.5注意事项
(1)与碳纤维片配套使用的粘结树脂对充分发挥碳纤维片的拉伸强度具有明显的作用,因而在实际工程中,应保证两者选用的配套性。
(2)碳纤维片在使用过程中应远离电源,尤其是高压电线及输电线路。
(3)配套使用的树脂要远离火源,避免阳光直射,施工人员严禁在现场吸烟。
(4)开挖前对施工人员进行现场教育,注意人身安全,防止开挖时损坏管道及防腐层。
(5)负责施工的工长应每天进行班前安全教育和安全检查,督促工人戴好防护眼镜、手套、口罩、安全帽等。
4.竣工验收
鉴于油气压力管道的特殊性,在复合材料维修补强的验收中,应尽量采用非破坏性方法进行验收。
4.1非破坏性验收方法
4.1.1补强过程控制以及补强层外观验收
4.1.1.1验收内容
非破坏性验收方法在施工过程中以及施工结束后,对如下三个方面进行检查:
1、复合材料补强层检测
2、复合材料补强层与基体钢管的粘接性能
3、基体钢管检测
验收检查的对象以及要求见下表:
表5复合材料补强验收检查项目
验收项目分类
验收检查对象
验收要求/允许极限
修复前的基体管
基体管材料
确认基体管材可被复合材料修复
几何形状
修复区域不应有尖锐的几何形状改变,所有的倒角半径应大于5mm。
不满足此要求的倒角,应进行填平处理。
表面处理
表面处理要求应符合设计要求。
表面处理的轴向范围应与设计相符。
表面温度
应与设计要求相符合
管道缺陷
管道缺陷尺寸与类型不得超过补强材料应用范围
修复位置
修复区域的位置和轴向范围与设计要求一致
界面
分层、空鼓
敲击补强层测试是否有分层与空鼓。
在补强材料边缘不得有空鼓。
涂抹树脂
裂纹
无
异物、气泡、坑
最大尺寸宽10mm,高2.5mm
褶皱
厚度差别不得超过2.5mm
树脂颜色
一致
未被涂抹树脂区域
无
针孔
不得超过补强层厚度
复合材料补强层
纤维铺设方向
与设计一致
补强层数
与设计一致
未被树脂浸润纤维
无
暴露、未封边纤维
无
异物
无
轴向尺寸和修复区域
符合设计要求;不得超出表面处理区域。
4.1.1.2不符合验收要求的补强层的处理方法
上表中要求的验收项目如果没有达到验收要求,可以考虑把整个补强层剥离,重新安装新的补强层;也可以对补强层进行局部切除,再进行局部修复。
局部修复时,重新搭接贴上等量的ANKO碳纤维片材,搭接长度不应小于100mm。
补强层表面的无树脂区域可以通过打磨的方式进行切除,然后再重新涂抹树脂。
补强层空鼓面积不大于100cm2时,可采用针管注胶的方法进行修补。
4.1.2静水压试验
如果条件允许,可以通过在役静水压试验的方法对补强效果进行验证,即对补强管道进行加压试验。
在静水压试验前,补强材料应该达到完全固化。
静水压试验的压力不应低于管道正常操作压力的1.0倍,保压时间最少为60分钟。
在试验期间,应详细记录压力和温度的变化。
试验过程中如果出现了压力降低和泄漏,如无特殊原因,则补强应被认定为无效。
4.2破坏性验收方法
根据管道业主需要,可以把补强修复后的管道切割下来,通过静水压爆破试验的方法对补强效果进行验证。
爆破试验的目的是令管道发生破裂失效。
爆破试验参照《输送钢管静水压爆破试验方法》(SY/T5992-94)执行。
在静水压试验前,补强材料应该达到完全固化。
静水压试验期间,应详细记录压力和温度的变化。
试验过程中如果出现了补强缺陷处泄漏或补强层断裂失效,则补强应被认定为无效。
5.复合材料修复后管道的维护
补强层的维护应该根据原始管道缺陷的类型而定。
5.1地上管线
5.1.1对于地上管线,应该依据上表定期进行目测检查。
如果发现补强层缺陷,则应该进行相应的评价。
目测检测的频率取决于风险评估。
5.1.2如果评价决定要对补强层进行替换,则有如下替换的方法可供选择:
1、清除整个补强层(比如使用高压水喷射)并替换;
2、对补强层进行修复。
这种情况下,新的补强层应该按照管道原始的缺陷情况进行设计;
3、对补强层进行局部修复。
5.2外缺陷管道
5.2.1对于外缺陷管道,在施加补强修复材料后,可以认定管道外缺陷将停止继续发展。
所以补强材料维护的策略是确认补强材料是完好无缺的,如补强层没有被损伤、没有补强材料与管道之间的脱层现象等。
5.2.2如果复合材料补强层不再符合管道补强要求,应重新制定维护、修复方案。
这种情况下,复合材料修复仍是最佳的修复方法。
5.3内缺陷管道
5.3.1对于管道内缺陷,尽管已经施加了补强材料,但是内缺陷仍可能继续发展。
所以,除了上述外缺陷的维护措施,还应确认内缺陷的增长没有超过补强设计允许的范围以及修复层没有与基体脱层。
5.3.2内缺陷管道复合材料补强层的检测频率取决于风险评估的结果。
6.竣工资料
施工完毕,向甲方提供一下竣工资料:
1)管道缺陷资料:
缺陷部位、面积、缺陷类型;
2)补强施工资料:
补强设计方案、补强层数、补强宽度;
3)外防腐修复的施工记录;
4)补强防腐材料合格证,检测报告;
5)施工总结。
附录A施工记录表格
工程名称
施工单位
日期
管道信息
管道名称
管道材质
管道外径
管道壁厚
输送介质
管道温度
运行压力
补强信息
缺陷类型
缺陷尺寸
缺陷位置(钟点方向)
补强时管道温度
补强时湿度
补强层数
补强宽度
补强材料名称
材料出厂批号
补强施工人员
制表:
审核:
日期: