筛板式精馏塔的设计论文.doc
《筛板式精馏塔的设计论文.doc》由会员分享,可在线阅读,更多相关《筛板式精馏塔的设计论文.doc(45页珍藏版)》请在冰豆网上搜索。
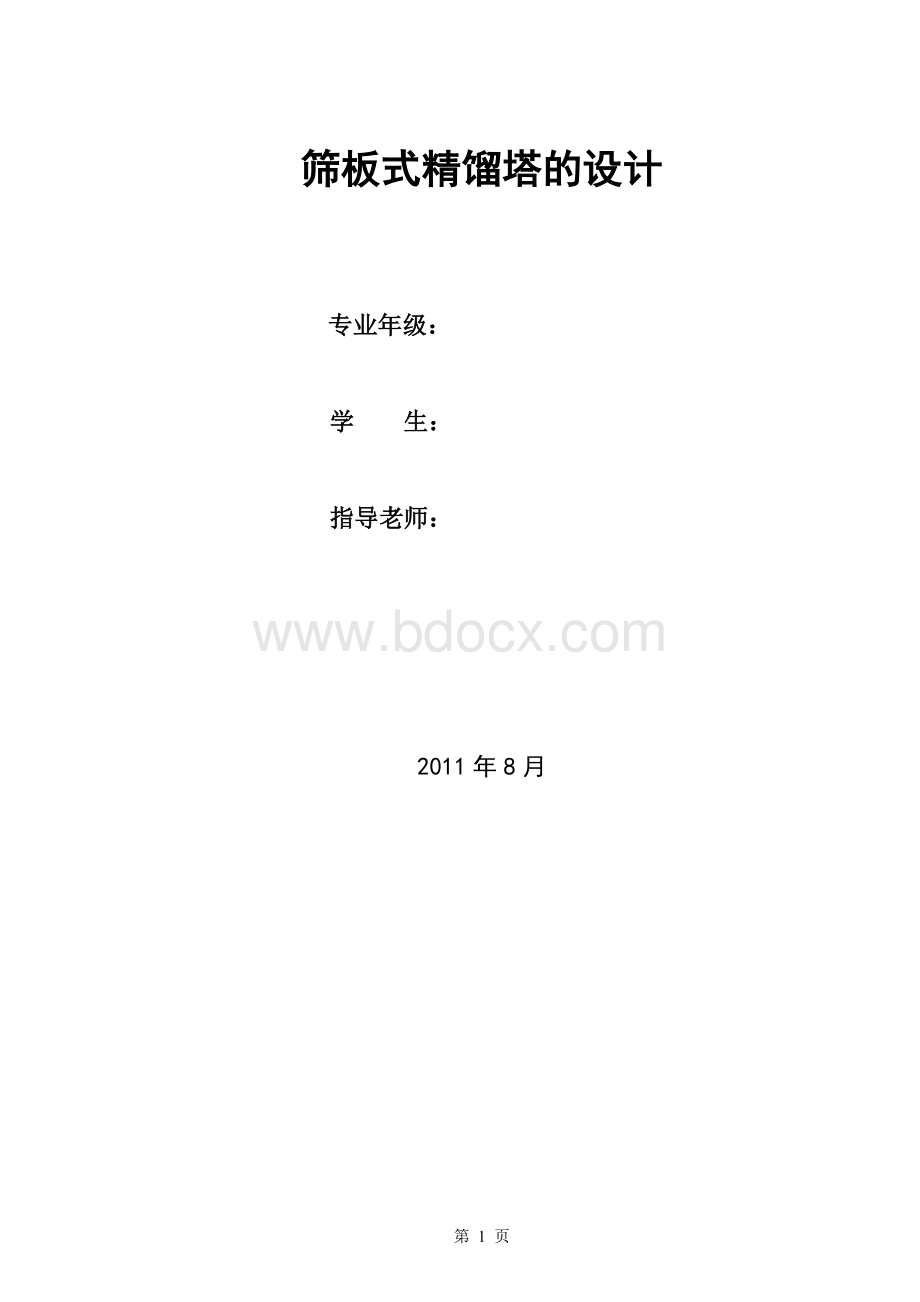
筛板式精馏塔的设计
专业年级:
学生:
指导老师:
2011年8月
目录
目录 2
摘要 5
1概述 5
2精馏工艺流程确定 6
2.1进料热状况 6
2.2进料方式 6
2.3冷凝方式 7
2.4加热形式 7
3、精馏塔的物料衡算 7
3.1、原料液、馏出液、釜液组成 7
3.1.1、原料液组成 7
3.1.2、馏出液组成 7
3.1.3、釜液组成 8
3.2、物料衡算 8
3.2.1、质量流量 8
3.2.2、摩尔流量 8
3.2.3、体积流量及体积分率 9
3.3、结果汇总表 10
4、塔板数的确定 11
4.1、理论塔板数的确定 11
4.1.1、最小回流比Rmin 11
4.1.2、最小理论塔板数Nmin的确定 12
4.1.3、最佳回流比的确定 12
4.2操作线方程 13
4.2.1精馏段操作线方程 14
4.2.2提溜段操作线方程 14
4.2.3q线方程 14
4.2.4用逐板计算出理论塔板数 14
4.3、总板效率η的估计 16
4.3.1、平均挥发度 16
4.3.2、加料摩尔组成的液体平均摩尔粘度μav 17
4.3.3、估计总板效率η 17
4.3.4实际板数的确定 17
5、塔板结构的工艺设计 18
5.1、初选塔板间距HT 18
5.2、塔径初算 18
5.2.1液泛气速uF 18
5.2.2、塔径的核算 20
5.3、塔板上溢流型式的确定 20
5.4、塔板布置 21
5.4.1、筛孔孔径 21
5.4.2、筛孔中心距t0和开孔率φ0 21
5.4.3、筛板厚度tp 22
5.4.4、溢流堰长lw 22
5.4.5、堰板高度hw 22
5.4.6、降液管下沿与塔板板间距ta 23
5.4.7、安定区宽度Ws和边缘区宽度Wc 23
5.5、塔板各部分面积和对应气速计算 24
5.5.1降液管面积Ad 24
5.5.2塔板工作面积Aa 24
5.5.3塔有效截面积An 25
5.5.4筛孔总面积 25
6.塔板流体力学校核 26
6.1、板上溢流强度检查 26
6.2、气体通过塔板的压力降ΔHt 26
6.3、液面落差校核 27
6.4、漏液点气速校核 27
6.5、降液管内液面高度Hd和液体停留时间t校核 27
6.5.1、降液管内液面高度Hd 27
6.5.2、停留时间t 28
7.塔板负荷性能图 29
7.1负荷性能图的绘制 29
7.1.1液体流量下限线 29
7.1.2液体流量上限线 29
7.1.3漏液线 29
7.1.4液泛线 30
7.1.5雾沫夹带上限线 31
7.2、塔板结构设计评述 32
8.、塔总体结构 32
8.1、塔体与裙座结构及封头的选用 32
8.2、塔盘结构 32
8.3、除沫装置 33
8.4、塔附件 33
8.5、塔高的计算 33
8.5.1、塔的顶部空间高度 33
8.5.2、塔的底部空间高度 33
8.5.3、加料板的空间高度 34
8.5.4、支座高度 34
8.5.5、人孔 34
8.5.6塔高 34
8.6、接管 34
8.6.1、回流管和液体进料管 34
8.6.2、釜液出口管 36
8.6.3、气体进口管 36
8.6.4、气体出口管 37
9、精馏塔附属设备选型计算 38
9.1、釜底再沸器 38
9.2、馏出蒸汽冷凝器(余热利用) 38
9.3、产品冷却器 39
9.4、泵的选用 40
10.数据汇总 42
参考文献 45
摘要
本实验设计采用筛板式精馏塔对乙醇~水溶液进行分离。
以9200kg·h-1,24.8%的溶液进料,塔顶馏出液的质量分率为89.3%,塔釜馏出液的质量分率为0.95%。
该筛板式精馏塔塔高12m,塔板数为15块,其中,精馏段12块,提馏段3块,且第13块板为进料板。
塔板间距选用450mm,塔径为1200mm,塔板筛孔孔径为5mm,筛孔中心距为17.5mm,开孔率7.4%,筛板厚度为3mm,溢流堰长864mm,堰板高度为40.93mm,安定区宽度80mm,边缘区宽度30mm。
塔板降液管截面积为0.109m2,工作面积为0.719m2,有效截面积为1.021m2,筛孔总面积为0.0532m2。
本塔选用IS65-50-160型号的进料泵冷液进料,塔顶采用冷却水用量为22795.2kg·h-1的A900-240-0.6-280型号的冷凝器及冷却水用量为2865.6kg·h-1的A600V-120-6-50型号的产品冷却器,塔釜采用蒸汽用量为6802.343kg·h-1的A400-60-1-10型号的再沸器。
关键词:
乙醇~水溶液精馏分离
1概述
均相物系的分离方法有吸收、萃取、干燥、精馏等操作,其中工业上分离均相液体混合物最常用的过程是蒸馏。
利用液体混合物中组分挥发性能的差异,以热能为媒介使其部分汽化,从而在气相富集易挥发组分,液相富集难挥发组分,使混合物得以分离的方法称为蒸馏。
根据操作方式,蒸馏分为简单蒸馏、平衡蒸馏和精馏。
前两种只能实现初步分离,而精馏能实现混合物的高纯度分离,无需与外界进行热量交换,采用多次平衡级的蒸馏过程来实现混合液的高纯度分离,这种多级蒸馏过程的组合就是精馏。
塔设备是实现精馏、吸收、解吸和萃取等化工单元操作的主要设备,它可以使气(或汽)液或液液两相之间进行紧密接触,达到相际传质及传热的目的。
因此,塔设备在化工过程中有时也用来实现气体的冷却、除尘、增湿或减湿等。
最常用的塔设备可分为两大类:
板式塔和填料塔。
此外,还有多种内部装有机械运动构件的塔,例如脉动塔河转盘塔等,则主要用于萃取操作。
板式塔按其塔盘结构,填料塔按所用填料的不同,又各细分为多种塔型。
不管是对何种塔型,除了首先要能使气(汽)液两相充分接触,获得较高的传质效率,还希望能综合满足下列要求:
(1)生产能力大。
在较大的气液流速下,仍不致发生大量的雾沫夹带及液泛等破坏正常操作的现象。
(2)操作稳定,操作弹性大。
当塔设备的气液负荷量有较大的波动时,仍能在较高的传质效率下进行稳定的操作。
(3)流体流动阻力小,即流体通过塔设备的压力降小。
以节省动力消耗,降低操作费用。
对于减压蒸馏,较大的压力降还将使系统无法维持必要的真空度。
(4)结构简单,材料耗用量小,制造和安装容易。
(5)耐腐蚀,不易堵塞,方便操作、调节和检修。
事实上,任何一种塔形都难以全面满足上述要求,而只能在某些方面具有独特之处。
但是,对于高效率、大生产能力、稳定可靠的操作和低压降的追求,则推动着塔设备新结构型式的不断出现和发展。
筛板塔是板式塔中较早出现的塔型之一,它综合具有结构简单,制造维修方便,生产能力大(可比浮阀塔大),塔板效率较高,压降小等优点,不足之处是操作弹性较小。
筛孔也易堵塞,使用曾一度受到限制,但是近几十年来,经过大量工业规模的研究,逐步掌握了筛板塔的性能,并形成了较完善的设计方法,还开发了大孔径筛板,导向筛板等形式,使筛板塔的不足得到补救,即合理的设计可以保证较高的操作弹性。
现在,筛板塔已经成为生产上最广泛采用的塔型之一。
二元物系精馏用筛板塔的工艺设计,主要包括精馏系统工艺流程的确定、物料衡算、塔板数的计算、塔结构工艺设计、热量衡算和附属设备的选型计算等项。
2精馏工艺流程确定
2.1进料热状况
选择20℃冷液进料。
2.2进料方式
选择进料泵进料。
泵的主要目的是迫使液体通过过程的固定阻力和克服过程中可能有的静压头。
2.3冷凝方式
塔顶蒸汽采用全凝器冷凝,冷凝液在泡点下一部分回流至塔内,剩余部分经产品冷却器后送至储罐。
由于调节回流比时分凝器不如全凝器便利准确,故采用全凝器。
2.4加热形式
塔釜采用分离式间接蒸汽加热。
所需工艺流程见附图一。
3、精馏塔的物料衡算
3.1、原料液、馏出液、釜液组成
3.1.1、原料液组成
已知水的摩尔质量:
MA=46.07kg·mol-1
乙醇摩尔质量:
MB=18.02kg·mol-1
质量分率:
ωF=24.80%
摩尔分率:
注:
所有下标A代表乙醇,所有下标B代表水。
3.1.2、馏出液组成
质量分率:
ωD=89.30%
摩尔分率:
3.1.3、釜液组成
质量分率:
ωW=1.04%
摩尔分率:
3.2、物料衡算
3.2.1、质量流量
全塔物料横算式:
mF=mD+mW
mFωF=mDωD+mwωw
已知mF=9200kg·h-1,代入数据得
9200=mD+mW
92000.248=mD0.893+mw0.0095
联立,解方程得
mD=2383.531kg·h-1
mw=6716.469kg·h-1
3.2.2、摩尔流量
原料液的摩尔流量
全塔物料衡算式:
F=D+W
FxF=DxD+Wxw
代入数据:
433.45=D+W
433.450.114=D0.766+W0.00374
解方程得
D=62.699kmol·h-1
W=370.755kmol·h-1
3.2.3、体积流量及体积分率
(1)、进料体积流量及分率
由于采用冷液进料,查表【1】,进料组成F=24.80%时,20℃时,进料液的密度=959.781kg·m-3
查表【2】,当tF=20℃时,乙醇的的密度=795kg·m-3
进料体积流量
进料体积流率
xF′==0.299
(2)、馏出液体积流量
由于采用泡点回流,查表【3】,D=89.3%时,气液混合物的泡点为78.731℃。
查表【1】,当tD=78.731℃时馏出液的密度=758.408kg·m-3
查表【2】,当tD=78.731℃时,乙醇的的密度=730.350kg·m-3
馏出液体积流量
VD=
=3.275m3·h-1
馏出液体积分率
xD′==0.927
(3)、釜液体积流量
查表【3】,w=0.95%时,气液混合物的泡点为98.98℃。
查表【4】,当tW=98.98℃时,水的密度=959.104kg·m-3
查表【2】,当tW=98.98℃时,乙醇的密度=717.428kg·m-3
进料时混合物的密度
=958.200kg·m-3
釜液体积流量
VW=
=7.009m3·h-1
釜液体积流率
xW′=
3.3、结果汇总表
表1
质量分率/%
摩尔分率∕℅
体积分率/%
进料液
24.8
11.4
29.9
溜出液
89.3
76.6
92.7
釜液
0.95
0.374
1.27
表2
质量流量/㎏•h-1
摩尔流量/mol•h-1
体积流量/m3•h-1
进料液
9200
433.454
9.586
馏出液
2483.531
62.699
3.275
釜液
6716.496
370.755
7.009
4、塔板数的确定
4.1、理论塔板数的确定
4.1.1、最小回流比Rmin
查表【5】,质量分率为24.8℅的乙醇~水溶液的泡点温度为85.75℃,露点温度为96.97℃。
将料液由20℃升温至85.75℃,
查图【6】,
20℃时,CPA=2.345kJ·kg-1·K-1,CPB=4.179kJ·kg-1·K-1
CP1=CPAxF+CPB(1