电弧炉冶炼操作铸钢王继朋.docx
《电弧炉冶炼操作铸钢王继朋.docx》由会员分享,可在线阅读,更多相关《电弧炉冶炼操作铸钢王继朋.docx(12页珍藏版)》请在冰豆网上搜索。
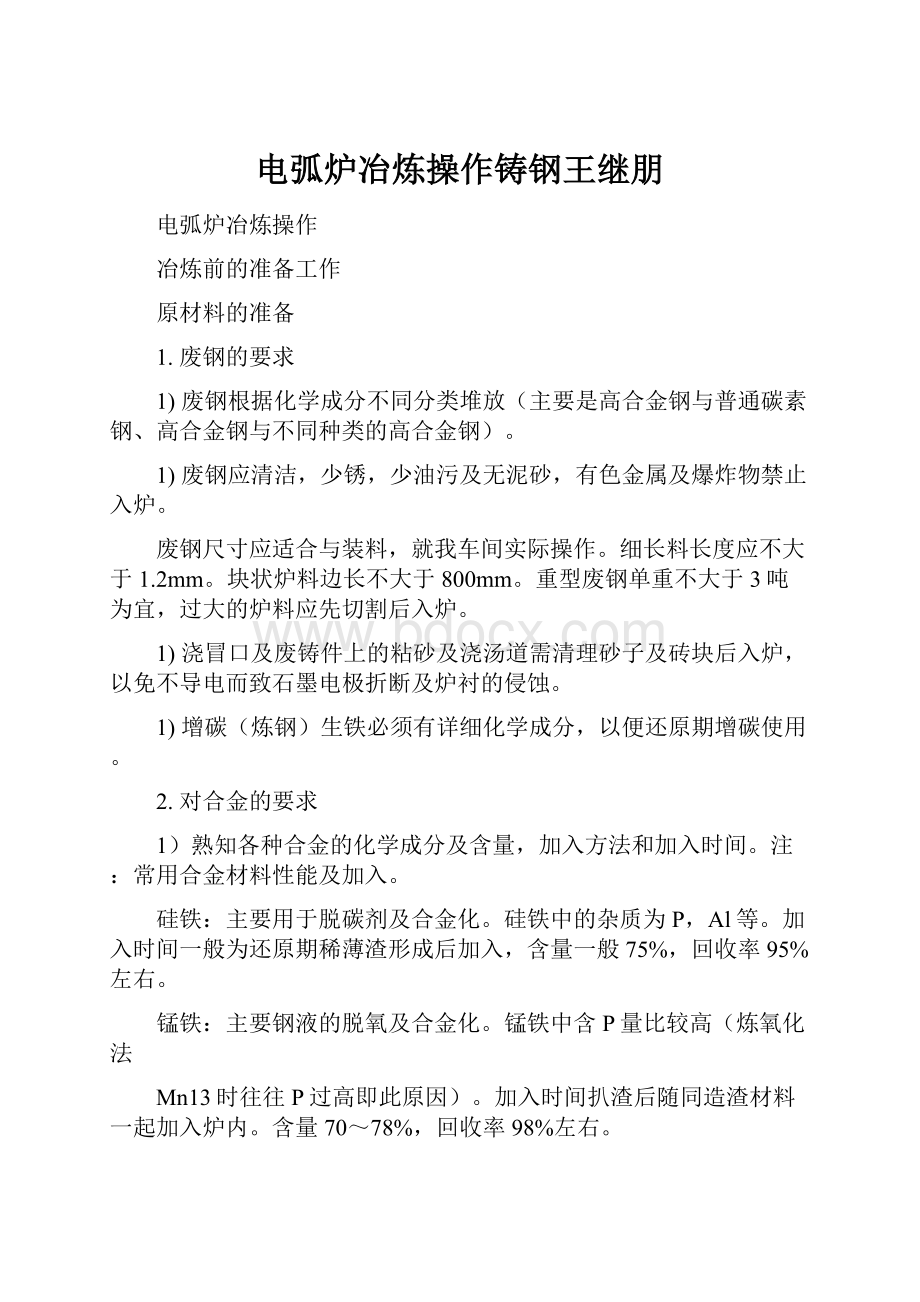
电弧炉冶炼操作铸钢王继朋
电弧炉冶炼操作
冶炼前的准备工作
原材料的准备
1.废钢的要求
1)废钢根据化学成分不同分类堆放(主要是高合金钢与普通碳素钢、高合金钢与不同种类的高合金钢)。
1)废钢应清洁,少锈,少油污及无泥砂,有色金属及爆炸物禁止入炉。
废钢尺寸应适合与装料,就我车间实际操作。
细长料长度应不大于1.2mm。
块状炉料边长不大于800mm。
重型废钢单重不大于3吨为宜,过大的炉料应先切割后入炉。
1)浇冒口及废铸件上的粘砂及浇汤道需清理砂子及砖块后入炉,以免不导电而致石墨电极折断及炉衬的侵蚀。
1)增碳(炼钢)生铁必须有详细化学成分,以便还原期增碳使用。
2.对合金的要求
1)熟知各种合金的化学成分及含量,加入方法和加入时间。
注:
常用合金材料性能及加入。
硅铁:
主要用于脱碳剂及合金化。
硅铁中的杂质为P,Al等。
加入时间一般为还原期稀薄渣形成后加入,含量一般75%,回收率95%左右。
锰铁:
主要钢液的脱氧及合金化。
锰铁中含P量比较高(炼氧化法
Mn13时往往P过高即此原因)。
加入时间扒渣后随同造渣材料一起加入炉内。
含量70~78%,回收率98%左右。
铬铁:
合金化,可分为高碳铬铁,中碳铬铁,低碳铬铁及微碳铬铁。
含量55~65%,回收率98%左右。
P、S含量不高。
钼铁:
合金化,钼铁属难熔合金,加入时间在装料时同炉料一起装入或在熔化期及氧化前期加入。
为节约用量,一般在熔毕样分析成分结果出来后按计算加入,并及时吹氧,使其完全熔化。
钼铁加入时会产生沸腾现象(称为钼沸腾)。
加料时应将炉体向后摇起,加料人员站在路门侧面。
含量50~58%,回收率98%以上(按100%计算)。
镍:
还原期(后期)加入,含量99%以上,回收率100%。
2)铁合金加入炉中以前需要烘烤(以除去水分及部分合金所含氢较高),块度适中。
3、造渣材料
1)石灰(见表)
名称
化学成分%
CaO
不小于
SiO2MgOFe2O3+Al2O3S
不大于
H2O
一级石灰
90
2
1.5
3
0.08
0.5
二级石灰
85
4
2.0
4
0.10
1.0
块度要求20~80mm。
粉末原则上不超过5%(S<0.15%)
2)萤石。
是由萤石矿直接开采而得。
改善炉渣流动性而不降低碱度,可增强渣钢面反应能力,对脱去钢液中的P、S有利。
要求CaF2含量越高越好,而SiO2含量要低。
CaF2>85%、SiO2<4%。
块度20~50mm,入炉前干燥。
补炉及装料送电
1、补炉
1)补炉采用热补方式。
车间补炉是采取铁锹投补方法。
操作要点:
对准炉衬冲蚀严重的地方快速、准确、薄补的原则。
补炉人员站在镁砂盘上时必须系好安全带,地面要有人监护。
凉补炉时注意将补过的地方补炉料踩实,大补炉后最好用薄铁皮覆盖后在装料。
2)出钢槽修补用补炉料,保证平整。
烘烤干燥。
确保在出钢过程中不散流,不翻浪。
(目的:
减少在出钢过程中钢液吸气)
2、装料
1)对配好的炉料检查核对。
并考虑上一炉所冶炼的钢种对本炉钢的化学成分影响情况。
(如上一炉为Mn13)
注:
我车间现料源熔清后几乎无碳(无配碳生铁)。
因此在装料前必须进行废电极块或蓝碳未配碳,配碳量根据所冶炼钢种高0.10~0.30%配入。
2)装料前根据炉况加入适量石灰,加入量为炉料总量的1~2%(目的:
护炉、提前造渣)。
3)装料原则,上松疏,下致密,中间高,四周低。
炉门口处无大料。
大块重料装炉底,上面轻薄小料。
3、送电
1)送电前再一次检查炉内料状况,电极下方是否有不导电材料(炉料上有大面积砂子,砖块、石棉等)。
如有时必须处理或将炉壳稍错开,保证电极导电。
2)检查电器及机械设备正常,水冷系统,电极长度等。
电极短需要早期接换,接电极操作时必须炉顶2人操作,使用电极扳手时2人配合好,用力一致,动作协调,就绪后炉长指挥送电,无关人员远离炉体。
冶炼及操作
一、熔化期:
(任务:
炉料快速熔化为均匀液体,早期脱磷,去除钢液中部分气体及杂质)
1)传统熔化期约占冶炼时间一半。
这期间电能消耗占总电耗的50%以上。
因此,快速化料是缩短冶炼周期的基本条件。
2)熔化期系用最大电流给电(变压器允许情况下)步骤:
(以我车间实际情况)。
起弧阶段,电流应小一点4000A~6000A之间。
穿井阶段及电极回升阶段,电流控制9000A~11000A之间。
低温区炉料熔化阶段电流控制应为最大。
如下图;
起弧阶段穿井阶段电极回升阶段低温区炉料熔化阶段
3)吹氧祝熔应在电极穿井完成后,炉内可见有熔池形成后进行(送电后约20分钟以后)。
专人吹氧,分人配合(一人开关氧气,一人摇炉,一人加料渣),开关氧气人员根据吹氧人习惯开氧气大小。
开关氧气时速度要慢。
4)熔化末期采用自动流渣操作。
(炉体前摇自炉门内自动向外流渣)。
目的:
提前去除钢液中的部分磷。
及时补加新渣料,保证渣液流动性良好。
如炉渣过于粘稠用萤石加以稀释。
5)炉料全熔化,搅拌取样进行全分析(具体操作,将搅拌耙杆在炉门口烘干后进入炉内渣面上蘸好渣,防止在搅拌过程中将搅拌耙熔化掉,顺时间方向推渣数下,在逆时针方向进入钢液中搅拌,然后用样勺同样蘸好渣后取样。
取样方位应基本在熔池正中央)。
全熔后的碳含量应高于所冶炼钢种的含碳量下限要求。
二、氧化期:
任务(1、继续并最终完成钢液脱磷任务,使钢液中的磷降到规格范围内;2、去除钢液中的气体及非金属夹杂物;3、加热并均匀钢液温度,一般高于出钢温度20℃以上)我车间现采取熔-氧结合法,所以氧化期不明显。
氧化期的具体操作:
1、确保渣量,渣量为炉料的2~3%,碱度R=2.0~3.5。
保持良好的流动性,且氧化铁含量要高。
脱磷的基本条件:
“三高一低”(温度相对要低1520~1550℃,高碱度,高氧化铁含量,大渣量且流动性好)。
2、氧化期最理想采用矿石-氧气综合法氧化,矿石要分批加入,控制好氧化速度。
(仅脱碳时温度应控制相对高点>1550℃)防止大沸腾。
氧气压力不得大于8个大气压。
3、氧化顺序上先磷后碳,温度控制上先慢后快;造渣上先大渣量去磷,后薄渣脱碳。
(去磷时采取自动化渣操作,并及时补加石灰、萤石、氧化铁等;最后脱碳以吹氧为主)
4、良好氧化渣应是泡沫渣,可包住弧光,有利于钢液升温和保护炉衬。
冷却后表面呈油黑色,断头致密而松脆。
这表明氧化渣FeO含量高,碱度合适。
如氧化渣表面呈黑色炉内渣显得很薄,像水面一样,电弧声刺耳。
表明FeO含量高,碱度底,这时应补加石灰(我车间此种情况最常见)。
5、氧化期几种常见典型操作:
1)碳高磷高,应在氧化初期,利用熔池湿度偏低时集中脱磷,并在脱磷的过程中逐渐升温,为后期脱碳创造条件。
2)碳高磷低,温度适当控制高一点,集中吹氧降碳,及时流渣并补充渣料。
3)碳低磷高,温度控制偏低一点,采用大渣量吹氧,加矿(氧化铁皮),自动流渣及时补充渣料,必要时扒渣重造新渣。
磷达要求范围后采取增碳操作。
4)碳低磷低(略)。
6、氧化末期搅拌取样进行全分析(操作同熔化期),使熔池进入净沸腾(也称清洁沸腾。
具体操作,按吨钢1~2Kg加入锰铁,保持熔池平静)。
并调整难熔不氧化合金元素成分至下限(比如Mo)。
具备扒渣条件时即可进行扒渣(操作要点:
迅速,平稳,彻底。
当扒渣到后期渣量少而稀薄的情况下,可视情况短时间下插2#3#电极浅入钢液,使渣液很快集中于炉门口附近,迅速扒除)。
7、增碳多是脱碳量不足或终脱碳过低所致,它是一种不正常操作。
因为增碳易使钢液中气体和夹杂物增加,既浪费原材料,又延长冶炼时间,所以尽量避免。
常见增碳方法有:
1)补加生铁增碳。
2)停电插电极增碳。
但插电极增碳消耗电极量大,一般不提倡。
3)扒渣增碳,最常用增碳方法。
操作:
必须将熔渣扒干净,增碳剂(焦粉;蓝碳末)加入后要用耙子在液面上进行充分推擀,促使钢液对碳的吸收。
三、还原期及出钢:
还原期的基本任务:
1)脱除钢液中的氧。
2)脱除钢液中的硫3)调整化学成分,使其满足规格要求。
4)调整钢液温度,为正常浇注创造条件。
脱氧操作:
1、沉淀脱氧(直接脱氧)。
扒除氧化渣后,迅速将块状脱氧剂,如硅铁,锰铁和铝饼等脱氧剂直接投入(插入)钢液中,然后造还原稀薄渣,此法速度较快,可缩短还原时间,但脱氧产物易形成钢中夹杂。
2、扩散脱氧(间接脱氧)。
还原稀薄渣形成后,将脱氧剂(一般以粉状脱氧剂为主),加在渣表面上,通过降低渣中的氧含量来达到钢液的脱氧,扩散脱氧的产物不沾污钢液,但时间长,对降低电耗和炉衬使用提高不利。
3、综合脱氧。
即是将上述二种脱氧方法的综合运用,克服了各自得缺点,集中优点来完成钢液的脱氧任务。
我们车间全采用综合脱氧方法。
4、白渣脱氧。
操作:
扒除氧化渣后,迅速加入稀薄渣料,尽量减少钢液吸气与降温,渣料比例石灰:
萤石=3~4:
1,渣量为炉料的2.5~3%。
渣料加入前加入块状脱氧剂预脱氧,薄渣形成后调入各种合金,然后分批加入扩散脱氧剂;第一批应多一些,其他各批根据炉内状况加入,每批加入前,应对渣进行推渣搅拌,适时补加石灰,保持炉渣一定的碱度,总渣量控制为炉料的4%左右
扩散脱氧剂一般指焦炭粉,硅铁粉,硅钙粉等。
我们现用的合成精炼剂。
碱度=碱性氧化物:
酸性氧化物。
即:
R=CaO/SiO2还原期碱度应保持在2.5~3。
5、脱氧效果检验。
多采用经验判断法,脱氧杯观察法和化学分析法。
经验判断法根据炉渣的颜色判断脱氧好坏。
如果渣白且保持时间长而稳定,表明渣中(FeO)含量低,这时可判断为钢液脱氧良好。
脱氧杯观察法(常用),将钢液轻轻注入清洁、干燥、圆形的高筒杯中,凝固后表面平静或有不同程度的收缩,说明脱氧良好;如凝固过程中冒出一束束火花或凝固后不但不收缩,反而上涨,突起现象,这既脱氧不好。
见图;(化学分析法取渣样化验炉渣中的FeO含量)
脱氧良好脱氧不良
6、终脱氧多采用铝在出钢前2~3min根据冶炼钢种的不同按纯钢0.7~1Kg插入钢液中,多采用出钢过程中抛投到钢包内。
低碳钢取上限,高碳及低合金废钢取下限。
钢液脱硫。
掌握好以下四方面:
1)高温,脱硫反应属吸热反应,高温有利于进行。
2)炉渣碱度要高,不小于2.5即≥2.5。
3)渣量要大且流动性要好。
4)炉渣中FeO含量要低。
钢液成分的调整
常见单一元素在钢中的作用。
碳能影响规定钢的各种物化性能及力学性能。
如强度,塑性及焊接性能,对钢的淬火,退火等热处理有直接影响。
硅常用作还原剂和脱氧剂,存在于钢中提高固溶体强度,提高钢的抗腐蚀性,屈服极限。
锰能消除和减弱钢因硫引起的热脆性,增加钢的淬透性。
◆还原期合金补加公式:
补加量=钢水量(规格控制-化验分析)%/
(合金含量%×回收率%)
例:
冶炼50Mn。
已知装料15t,炉料综合收得率为90%,还原分析锰含量为0.38%,现控制为0.75%,用含量72%锰铁,收得率95%,求锰铁补加量?
解:
锰铁补加量=15000×90%×(0.75-0.38)%/(72%×95%)=73Kg(为操作方便,一般合金加入取整数)
◆高合金钢合金用量对元素控制成分的影响合金补加(减法本身)
例:
冶炼Mn13。
已知装料(氧化法)12t,炉料综合收得率为90%,取样分析Mn含量为0.50%,控制Mn含量为11.6%,用含锰72%锰铁,收得率为95%。
求锰铁补加量?
解:
锰铁补加量=12000×90%×(11.6-0.50)%/(72%×95%-11.6%)=2110Kg(实际加入中应考虑到元素的氧化及烧损量)
◆钢液重量的校验(在冶炼过程中往往出现炉料重量不准情况,或炉料杂质多,钢液量波动较大,可惜调镍调钼元素的办法校验钢液重量)因镍、钼基本不氧化。
例:
往炉中加入钼铁15Kg。
钢液中的钼含量由0.20%增到0.25%,已知钼铁含钼量为50%。
求炉中钢液的实际重量?
解:
炉中钢液实际重量=(15×0.50%)/(0.25%-0.20%)=15000Kg
钢液成分不正常常见处理:
如果配料、装料准确及工艺合理操作正确,钢液成分极少出现不正常情况。
但有时因某个环节贻误而造成不正常情况应妥善处理。
主要指钢中元素含量高出控制规格,在冶炼过程中,为了避免元素含量超标,往往采用低控制的操作,然后在出钢前进行适量的补加和调整,做到谨慎稳妥,对于可以改钢种使用的改钢种;如不可以的只能进行钢液的重新氧化及还原。
如:
残余镍高(镍元素不氧化),残余镍超出规格不多,炉内还可以再装料时,计算后在补加不含镍元素的废钢,生铁等;残余量过多,改冶炼含镍较高钢种或倒出部分钢水后再加料冶炼。
防止措施:
1、加强料场管理。
2、提高化验分析正确性和补加合金准确性。
3、在冶炼高合金钢后下一炉适当安排含有本元素的钢种。
(因为炉内剩余钢水及炉盖,炉壁处的渣钢均匀使下一炉该元素增加)。
还原期磷高,如还原期发现磷高就得重新氧化,可加小块矿石及补加白灰,加入氧化铁皮及氧气吹渣面,切使温度不可过高(小于1550℃),采取流渣换渣操作,当磷降低后,扒除全部渣液,重新造渣还原。
出钢
出钢是炉前冶炼操作的最后一项,但必须具备条件后方可出钢。
要求:
(1)化学成分全部进入控制规格。
(2)出钢温度合乎要求(低碳钢及低碳含铬钢温度相对高点,高碳钢温度要低点)。
(3)钢液必须脱氧良好。
(4)出钢时要求白渣出钢,忌氧化性渣及电石渣出钢,除此之外,提前准备好钢包,保证设备运转正常,并使出钢口畅通,出钢槽干燥,并干净等。
出钢方式多采用大口喷吐,钢渣混冲(这种出钢方式的优点是钢液能够将熔渣较好的保护,既减少了钢液的降温,又可控制钢液的二次氧化及吸气。
有利于夹杂物上浮与去除,可进一步脱除钢液中的氧和硫)。
出钢必须停电,严禁带电出钢,并抬高电极(防止增碳),缩短出钢时间。
出钢完后,应往包内塞杆附近渣面上加上碳粉或保温剂(保温渣)。
使渣子不至于硬结而影响塞杆升降,对于高温钢液或碱度低的稀渣,应往塞杆周围加些石灰,以降低这部分的渣温或使其变稠。
电炉钢的浇注
浇注是电炉炼钢的基本组成部分,任务是将温度合适的优质钢浇注成良好的钢锭及各种规格的异型钢件,电炉冶炼的钢种都是镇静钢,均是脱氧相当完全的钢液,因此在浇注模或型腔内不再发生明显的反应,也没有气体明显逸出的现象,所以钢液的凝固过程比较平静。
钢包也叫盛钢桶,它的作用除了盛容和搬运钢液外,更主要是在出钢时,通过渣钢在包内激烈搅拌使钢液得到充分的渣洗。
钢液不能出地过满,应离包沿不少于200mm的安全空间。
浇注前钢液要在钢包内有足够的镇静时间,使的气体排出,并使各种非金属夹杂物上浮,进行清洁钢液,改善钢的质量。
出钢前钢包要进行充分烘烤,新修砌的钢包通常要烘烤8小时以上,冷却后使用前再一次烘烤。
塞杆(我车间使用塞杆水口浇注)由杆芯、袖砖、塞头砖和压紧螺母组成。
塞头砖同水口砖一起组成钢包的开闭装置,为了避免发生粘掉塞头事故,在使用时一般采取两者不同的材质。
控制浇注温度就必须控制好出钢温度。
浇注时采取低温快浇、高温慢浇的原则。
快速充型,小流补缩。
钢锭浇注过程中不得断流,断流会使钢锭产生截痕,破坏了金属的连续性,当轧制、锻造时可能会发生断裂。
举例几种常见代表性的钢的冶炼
ZG35#化学成分含量C:
0.32%-0.42%Si:
0.20%-0.45%Mn:
0.50%-0.80%P、S不大于0.040%需钢水15吨,炉料装入量应为16.8吨(炉料回收按89%)采取熔-氧结合,快白渣法快速冶炼操作。
如第二炉冶炼此钢。
当第一炉出完钢后需补炉(热补)。
操作:
将拌好的补炉料堆放于镁砂盘上并确认挂好,补炉人系好安全带后站在镁砂盘上用铁锹进行投补,地面需有人扶好镁砂盘并对补炉人监护。
补炉时不能将补炉料投到残余钢水或渣面上,对准炉体烧损部位做到准确、快速、薄补。
向炉底加入250Kg左右石灰,装入一次料。
炉料配碳至熔清0.50%左右(熔化期碳烧损量一般为40%-60%,故配碳应配至1.00%)。
生铁配碳则需生铁16800×(1.00%-0.20%)/4%=3360Kg(0.20%为废钢平均含碳量,4%为生铁平均含碳量)。
其余用废钢配足料。
若用石墨电极块或蓝碳末配碳。
则分别需要200Kg左右、300Kg左右。
将炉料压平,接、放好电极,炉体开入堵好出钢眼后便可送电。
送电熔化约40分钟后吹氧熔助5-10分钟至可装二次料。
二次料装入时由炉长指挥装料,无关人员远离炉体。
并关好配电室窗户。
迅速装完后即给电。
当炉料基本全落入钢水进行吹氧(熔-氧结合)。
炉料全熔清后,将炉投前摇,边吹氧边流渣操作,并及时补加石灰,保证一定的渣量。
至钢液温度大于1550℃停止吹氧并取样分析。
样结果出来后看C、P结果进行下一步操作。
一般分三种情况:
①碳高、磷高;②碳高、磷低;③碳低、磷低。
①操作:
采用小电流(电流不大于5000A)加入氧化铁皮,氧气吹渣面并流渣操作,及时补加石灰萤石,必要时扒除氧化渣,重造新渣。
钢液温度不可过高。
然后取样分析。
C、P合格后进入扒渣还原。
②操作:
采用大电流,迅速提升钢温,直接合格后进入扒渣还原。
③操作:
大电流迅速提升钢液温度>1600℃。
扒除氧化渣后进行钢水面上用增碳剂吹氧降碳。
吹氧管插入钢水中。
氧气压力适当高些。
然后取样分析C(焦粉、蓝碳末)增碳。
加入造渣材料(石灰及萤石,加料及加合金时,人应站在炉门两侧,防止钢液溅出烫伤),加入量为炉料的2%左右(300Kg),并加入锰铁,采用大电流给电后在渣面上均匀洒硅铁粉约50Kg、精炼剂100Kg(快白渣操作)。
渣料全溶后用扒渣耙轻推渣面,此时加入硅铁视情不断加入适量精炼剂。
稀薄白渣形成后即可进行取还原样操作。
搅拌不得少于三耙子。
取样时样勺头应垂直于钢水面入钢水,至取样点(熔池中心点部位)后翻转样勺,将盛满钢液样勺轻拿出钢面,注意不要碰到炉门及其他地方,防止钢液洒出烫伤人。
至样模前需插铝丝进行脱氧后慢慢注入样模。
样勺内剩余钢水应轻轻倒回炉内。
还原样分析结果出来后根据具体情况进行下一步操作。
如果碳低较多(>0.05%),可采取下插电极增碳方法(插电极时应注意电极不可插到炉底,以免电极折断);若碳低在0.05%内,可下插电极增碳亦可炉后出钢时钢包内增碳操作。
并调整合金元素成分(Si、Mn合金补加见前面公式)调整好钢液温度(1600℃-1630℃),在脱氧杯中观察脱氧良好后即可出钢。
在出钢过程中顺钢流抛投铝饼10Kg左右。
出钢及钢包增碳过程中一人摇炉,一人把持钢包,一人增碳。
其他人员远离。
出钢完毕后,需在钢包中取出成品样并测温,包内温度应为1570℃-1600℃。
渣面撒保温渣。
浇注前钢水应在包内镇静5-8分钟后进行浇注。
ZG35CrMo化学成分含量C:
0.30%-0.40%Si:
0.20%-0.40%Mn:
0.50%-0.80%Cr:
0.80%-1.10%Mo:
0.20%-0.30%P、S不大于0.040%需要钢水量15吨,炉料装入量为16.5吨(炉料回收按89%计,后期需补加合金约300公斤)冶炼方法采取熔-氧结合,快白渣法快速冶炼操作。
在熔-氧末期取样分析后按规格下限加入钼铁,(因钼铁合金属难熔合金且不氧化,比重较大的贵重合金),加入时需注意发生沸腾。
加入后立即用吹氧管插入炉底吹氧以确保全熔。
加入量见前面合金补加公式。
扒渣还原时碳含量应控制比要求低0.10%左右(为节约成本使用高碳铬铁,铬合金化达目标后碳含量约增加0.10%)。
以后操作均见上述ZG35#操作。
ZGMn13的冶炼
ZGMn13属高合金钢,最常见的耐磨钢。
因钢液合金含量及碳含量高,钢液流性好,易造成浇注困难。
所以要严格控制钢液出钢及浇注温度。
ZGMn13化学成分含量表
元素名称
C
Si
Mn
P
S
元素含量(%)
0.90-1.30
0.30-0.70
11.0-14.0
≤0.08
≤0.04
冶炼此钢种分为氧化法和返回法两种方法。
氧化法冶炼
钢水量10t,炉内装料应为9t(炉料回收率按89%计算)炉底加白灰200kg,炉内配碳后送电。
炉料熔至70%-80%时,吹氧助熔。
熔毕取样后,视情况是否具备扒渣条件,如此时碳含量低,可在扒除氧化渣后进行渣面碳粉增碳。
钢水液面上加入足量碳粉后迅速开出炉体,将事先天车挂好的锰铁(中碳锰铁1.6t-1.8t)加入炉内钢液中。
除炉长指挥天车以外其他人员远离炉体,并将炉体及时开回,下落好炉盖马上送电。
采取大电流并及时加入造渣材料及脱氧剂,5-10分钟后用搅拌耙子搅动炉底,锰铁熔清后加入硅铁继续还原,至渣白后取还原样样(此还原样锰含量在0.90-0.10%之间)还原样分析后补加合金并调整好钢液温度(1530℃-1550℃)。
加入萤石(高锰钢炉渣因碱度高,需多加萤石,以防渣在钢包中硬结影响浇注)后,即可出钢。
若碳含量不足,需炉后增碳,出钢过程中将适量增碳剂或碳粉加入包内钢水流之间。
返回法冶炼
返回法即装入法。
将Mn13的浇冒口及废件集中入炉后送电。
采取大电流给电,快速使炉料融化。
炉料熔清后,氧气管深插炉底,短时间吹氧(2-5min)。
随后加入锰铁(20kg/t钢)、硅铁、造渣材料、石灰(200kg)以及萤石。
使用扩散脱氧剂进行还原,至锰铁合金熔毕后取样分析。
分析样合格及温度合格(1510℃-1530℃)即可出钢。
钢包内温度1480-1510进行浇注。
西部重工铸钢车间:
王继朋(内聘技师)
2012年12月4日