空气净化系统验证方案.docx
《空气净化系统验证方案.docx》由会员分享,可在线阅读,更多相关《空气净化系统验证方案.docx(44页珍藏版)》请在冰豆网上搜索。
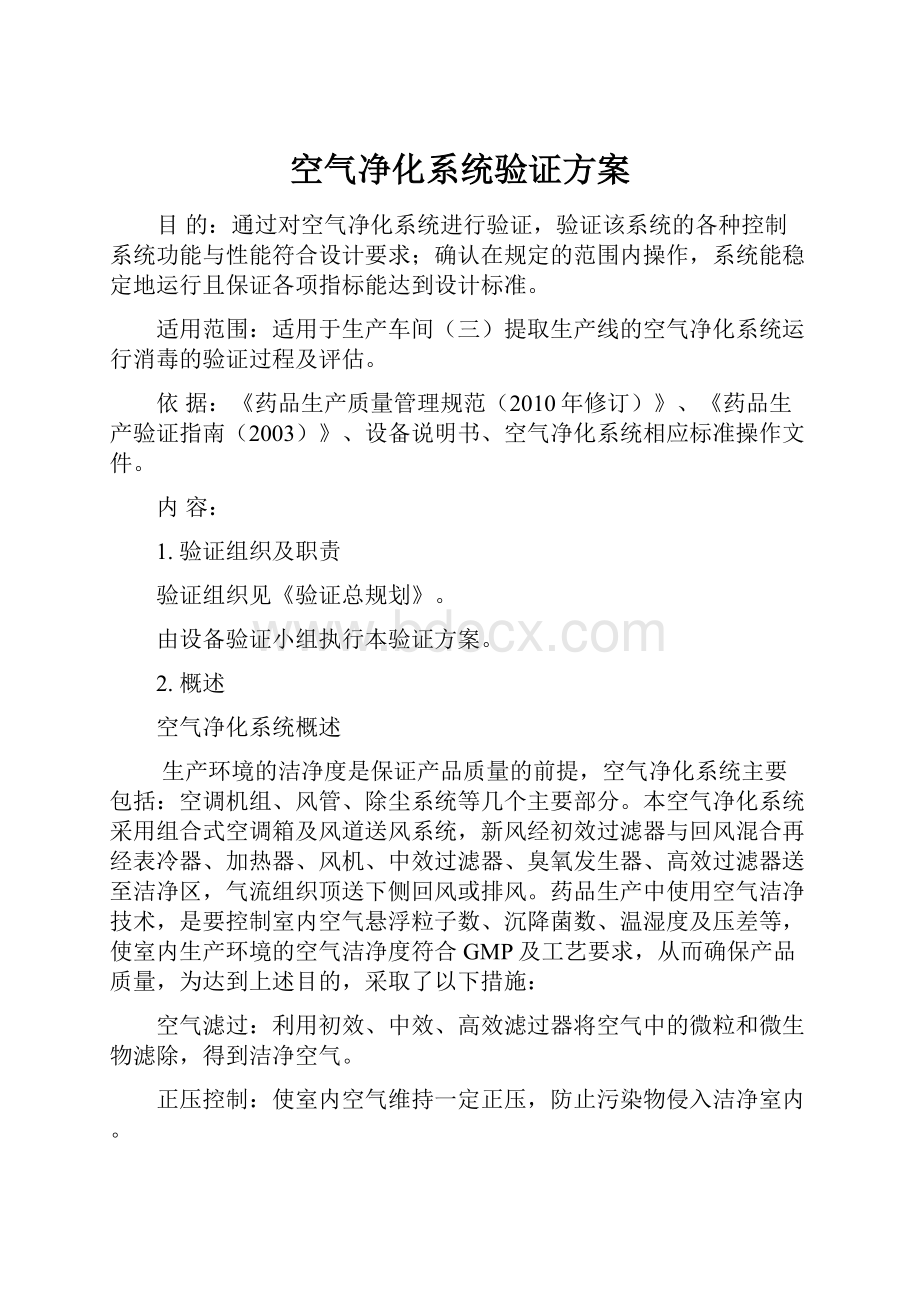
空气净化系统验证方案
目的:
通过对空气净化系统进行验证,验证该系统的各种控制系统功能与性能符合设计要求;确认在规定的范围内操作,系统能稳定地运行且保证各项指标能达到设计标准。
适用范围:
适用于生产车间(三)提取生产线的空气净化系统运行消毒的验证过程及评估。
依据:
《药品生产质量管理规范(2010年修订)》、《药品生产验证指南(2003)》、设备说明书、空气净化系统相应标准操作文件。
内容:
1.验证组织及职责
验证组织见《验证总规划》。
由设备验证小组执行本验证方案。
2.概述
空气净化系统概述
生产环境的洁净度是保证产品质量的前提,空气净化系统主要包括:
空调机组、风管、除尘系统等几个主要部分。
本空气净化系统采用组合式空调箱及风道送风系统,新风经初效过滤器与回风混合再经表冷器、加热器、风机、中效过滤器、臭氧发生器、高效过滤器送至洁净区,气流组织顶送下侧回风或排风。
药品生产中使用空气洁净技术,是要控制室内空气悬浮粒子数、沉降菌数、温湿度及压差等,使室内生产环境的空气洁净度符合GMP及工艺要求,从而确保产品质量,为达到上述目的,采取了以下措施:
空气滤过:
利用初效、中效、高效滤过器将空气中的微粒和微生物滤除,得到洁净空气。
正压控制:
使室内空气维持一定正压,防止污染物侵入洁净室内。
温度控制:
通过蒸汽加热器升温或通过表冷段降温,使洁净区温度符合要求。
相对湿度控制:
通过表冷段除湿或通过加湿器进行加湿使洁净区相对湿度符合要求。
空气净化系统示意图
空调机组简介
生产线
洁净区域面积
(m2)
洁净
级别
高效过滤器数量
设计
风量
(m3/h)
空调机组型号
生产厂家
提取生产线
290
D级
45
25708
SJ-20
苏净集团
为确保空气净化质量达到生产要求,待厂房设施安装结束,使用的仪器仪表校验合格,且在校验有效期范围内,对空气净化系统进行验证,验证项目包括空气净化系统的预确认、安装确认、运行确认和性能确认及空调系统的监控和空气净化系统的日常监测。
3.预确认
目的:
通过对空气净化系统设计资料及空调机组的设备技术指标适用性的审查,确认空气净化系统工艺布局及空调机组能否满足GMP及工艺要求。
确认的内容
空调机组技术适用性确认,结果记录于附表1。
洁净区工艺布局确认,结果记录于附表2。
空调机组风机选型确认,结果记录于附表3。
4.风险评估
风险确认、分析与评价
通过对空气净化系统进行风险评估,确定系统可能存在的危害并预估已确认危害的相关风险。
风险评价
对验证可能存在的风险进行评价,确定风险等级,针对评价中确定的风险点制定控制措施。
风险控制
验证结束后根据验证过程中针对风险分析中提出项目采取的措施进行评价。
5.安装确认
目的:
进行安装确认是对洁净区扩建部分
的风管安装、高效过滤器安装过程符合设计规范要求。
安装确认内容
空气净化系统的文件确认
确认空气净化系统的资料和正在使用的文件是否符合GMP管理要求,检查确认内容有说明书、合格证、电气原理图;洁净区工艺布局平面图;洁净区送、排、回风平面图及空气流向图;空调设备操作规程、维护保养规程、清洁规程及有关记录;设备采购合同等。
结果记录于附表4。
风管制作、清洁、气密性检查、安装的确认
风管制作、清洁、气密性检查、安装流程
风管制作→风管气密性检查→风管清洁→风管安装→风管吹扫→高效过滤器安装
风管制作、气密性及清洁确认项目、方法及标准
确认项目
检查方法及标准
风管制作
依据送风、回风、排风系统图及风管制作要求,目测风管制作应采用法兰铆接,风管的闭合咬口采用单咬口,矩形风管采用转角咬口,联合角咬口风管和配件表面应平整,圆弧均匀、纵向接缝应错开,咬缝应紧密,宽度均匀。
风管气密性检查
风管制作完成后,将风管置于暗室内,把电压不大于36V,功率在100W以上带保护罩的灯泡接通电源放在风管内,两端用遮光材料密封,目测风管应无漏光现象。
若风管外能观察到光线射出,说明有严重的漏风,应对风管进行修补后再查,直至合格。
如有漏点应附图标明漏点位置、编号并有文字说明。
风管清洁
用洗洁精擦拭风管内壁,用洁净布及纯化水擦洗干净,用75%乙醇擦洗一遍,目测应无灰尘、无污物、无颗粒物质,并用洁净PVC膜密封将风管两端封住待用。
结果记录于附表5。
风管安装确认项目、方法及标准
检查项目
标准要求
风管厚度
管道边宽度、高度在320mm(含320mm)以下的铁皮厚度为,边宽度、高度在320mm以上,630mm(含630mm)以下的铁皮厚度为,边宽度、高度在630mm以上,1000(含1000mm)以下的铁皮厚度为,1000mm以上、1250mm(含1250mm)以下的铁皮厚度为
风管制作
风管不得有横向接缝,矩型风管边长不大于900mm时不得有纵向接缝。
保温材料
应为橡塑海绵
风管材料
应为优质镀锌钢板
风管的密封
应以板材连接的密封为主,可采用密封胶嵌缝的方法密封
风管安装
应符合风管安装示意图及工艺要求,接缝及接管连接处应严密,所有咬口、翻边、铆钉处必须涂密封胶
送、回风管
总风管上要有送风阀及送风口;送、回风管道有调节阀门顶送下侧回
排风管
排风管末端应安装有过滤器及止回阀
结果记录于附表6。
高效过滤器安装确认
目的:
通过对高效过滤器安装过程的控制确认,确保高效过滤器安装符合要求。
通过检漏发现高效过滤器及其安装的缺陷所在,以便采取补救措施。
检测仪器:
尘埃粒子计数器。
确认内容及可接受标准
项目
可接受标准
出厂合格证
应有合格证
规格尺寸
规格尺寸应符合要求
安装
安装前必须对洁净室及净化空调系统全面清洁,在现场拆开包装并立即安装。
高效过滤器应有合格证,且标注的效率为%;并不得有变形、脱落、断裂破损;按高效过滤器分布图确定安装位置,安装时高效过滤器箭头正方向向下
气密性
过滤器框架的密封垫和过滤器组支撑框架之间,支撑框架和墙壁或顶棚之间测风速为0m/s
检漏
检测结果应符合B级/C级/D级净化标准,并且尘埃粒子数显示无异常,否则应判为泄漏。
一旦在线检测时发现高效过滤器泄漏,可用硅胶修补,但在一个过滤器上,全部修补点的面积总和应小于过滤器面积5%,
厂房
高效过滤器检漏检测方法
检漏时用粒子计数仪采样器放在被检部位的下面2-3cm处,对被检过滤器的整个断面,封头处和边框进行巡回扫描检查,巡回速度为20mm/s,以粒子计数仪显示器无脉冲现象为合格。
检查结果记录于附表10。
仪器、仪表的校验确认
目的:
在空气净化系统的测试调整及运行监控过程中,需要对空气的状态参数和冷、热介质的物理参数、空调设备的性能、房间的洁净度等进行大量的测定工作,将测得的数据与设计数据或标准要求数据进行比较、判断。
这些物理参数的测定需要通过比较准确的仪表及仪器来完成,因此所有仪器仪表的校准必须在设备确认及环境监控前完成,并记录在案,作为整个验证的一个重要的组成部分。
方法:
现场查看。
可接受标准
所有用于空气净化系统(空气净化系统)测试的仪器、仪表必须经过法定计量部门校准,并在校验有效期内;所有用于空气净化系统(空气净化系统)运行监控的仪器、仪表必须经过法定计量部门校准,并在校验有效期内。
检查结果记录于附表11、附表12。
6.运行确认
空气净化系统的运行确认是为证明空气净化系统能否达到设计要求及生产工艺要求而进行的实际运行试验,运行确认期间,所有的空调设备必须开动,与空调系统有关的工艺排风机、除尘机也必须开动,以利于空气平衡,调节房间的压力。
运行确认的主要内容有:
空调设备的测试、高效过滤器的风速及气流流型测定、空调调试和空气平衡、悬浮粒子和微生物的预测定。
运行确认所需文件资料
资料名称
编号
存放处
空气净化系统管理程序
高效过滤器检漏及更换操作规程
初、中效过滤器清洗规程
温湿度计操作规程
组合式空调使用维修保养规程
空调机组的运行测试
按照设备操作规程进行单机试运行,每一小时记录一次各功能段的参数,连续运行三次,每次12小时。
确认各功能段运行应正常,检查结果记录于附表13。
高效过滤器风速、风量及换气次数测试
目的:
证明空调系统能够提供符合设计要求的风速及风量,确定换气次数能否达到洁净室换气次数。
检测仪器:
风速仪。
检测方法
洁净室风速风量检测前,必须首先检查风机运行是否正常,系统中各部件安装是否正确,有无障碍(如过滤器有无被堵、挡),所有阀门应固定在一定的开启位置上,并且必须实际测量被测风口。
用风速仪贴近风口处测量,按定点测量法的要求按风口截面大小,把它划分为同样大小的若干面积相等的小块。
由于送风口为矩形风口,尺寸较小,故在风口处取5个测试点,用风速仪贴近各测量点,测得各点风速,求出5个测试点的平均风速。
用风速仪贴近风口处测量,按定点测量法的要求按风口截面大小,把它划分为同样大小的若干面积相等的小块。
测试点布置如图所示:
计算方法
风口平均风速(V)计算公式:
(m/s)
式中:
V1,V2…Vn为各测点的风速(m/s);n为测点总数(个)。
风口风量(L)的计算:
L=3600×F×V(m3/s)
式中:
F为风口通风面积(m2);V为测得的风口平均风速(m/s)。
换气次数(n)的计算:
(次/h)
式中:
L1,L2…Ln为房间各送风口的风量;
A为房间面积;H为房间高度。
可接受标准
洁净级别
风速
风量
换气次数
D级
出口处的面风速应≥s
风口实测风量与设计风量之差在±15%以内
≥15次/h
检测结果记录于附表14。
房间静压差测定
检查洁净室和邻室之间是否保持必须的正压或负压,从而知道空气的流向,这一项测定应在风量测定之后进行。
检测仪器:
测试仪器用微压计。
测定方法:
测试仪器用微压计安装在墙壁上,可随时观察压力变化情况,并读数记录。
测定前应将所有的门都关闭并开启房间中的排风机或除尘器,不允许有人穿越房间。
为避免压力出现不必要的变化,测试状态应固定,在空气净化系统稳定后,以平面上最里面的房间依次向外测定。
监测频率:
每日检测两次,每5±小时读数记录1次,连续检测三天。
可接受标准
洁净室与室外的压差应≥10Pa;
相邻不同级别房间的静压差绝对值应≥5Pa,洁净级别要求高的区域对相邻的洁净级别要求低的区域呈相对正压;
相同级别洁净室,产尘大的房间应形成相对负压,压差应≥5Pa。
检测结果记录于附表15。
自净时间测试
目的
确定设施清除悬浮微粒的能力。
产生粒子后在一定时间内恢复到特定洁净级别的自净能力是空气净化系统最重要功能之一。
仪器
气溶胶生成器、粒子计数器。
测定的房间
洁净度级别
D级
测定房间
总混间
测定程序
将初始粒子浓度提高到目标洁净程度的100倍或更高。
本次检测使用的粒径为μm。
洁净度级别
D级
初始粒子浓度
2900000
目标洁净程度
29000
将粒子计数器的采样探头置于检测点,计数器的采样探头不应直接位于送风口下。
将单次采样体量调整到测定洁净度级别时用的同一量值。
计数器每次开始计数到输出计数结果的延时应调整到不超过10s。
检测时,空气净化系统正常运行,洁净室被测区域充斥气溶胶污染物。
将气溶胶初始浓度提高到目标洁净程度的100倍或更高。
每隔1min进行一次测量,直到离子浓度达到100×目标浓度阈值,记录当时的时间(t100n)。
记录粒子浓度降至目标洁净度的时间(tn)。
自净时间计算
100:
1自净时间为=(tn-t100n)
将测定结果记录于附表17。
房间温湿度测定
确认空气净化系统系统具有将洁净厂房温度、相对湿度控制在设计要求范围内的能力。
温、湿度测定应在风量风压调整后进行。
测试仪器:
温、湿度计。
测定方法
测试应在空气平衡结束后进行。
测试前,空调系统连续运行24小时以上,所有照明设施也应在测试前24小时全部打开。
测量和记录温度、湿度应按不同的房间、测点不同的要求进行。
监测频率:
每日检测两次,每5±小时读数记录1次,连续检测三天。
测点分布:
测点应放在洁净室的中心点。
所有测点宜在同一高度,离地面,距外墙表面应大于。
可接受标准
洁净度级别
温度
相对湿度
D级
18-26℃
45-65%
将测定结果记录于附表18。
7.性能确认
目的
确认空调净化系统能够连续、稳定地使洁净区的洁净度符合设计标准及生产工艺的要求,也就是对空气净化系统是否能达到规定的洁净度做出判断。
性能确认周期
性能确认分为三个阶段,第一阶段为静态测试,第二阶段为动态测试,第三阶段为日常监测。
第一阶段:
空调净化系统连续运行3个周期,每个周期1天。
第二阶段:
与同时进行,连续3个批次。
第三阶段:
日常监测,测试从第一阶段开始持续一年,从而证明空气净化系统长期的稳定性。
温湿度的性能确认结果应以全年为一个周期。
只有经历了季节变化,才能全面评价空调净化系统对洁净区内温度与相对湿度的控制能力。
检测项目及检测频率
检测项目
检测频率
第一阶段
第二阶段
悬浮粒子数
每个周期监测监测一次
——
浮游菌数
每个周期监测监测一次
每天生产操作时监测一次
沉降菌数
每个周期监测监测一次
每天生产操作时监测一次
表面微生物
——
每天生产操作时监测一次
温度、相对湿度
每日监测,每天上下午各读数记录1次
静压差
每日监测,每天上下午各读数记录1次
悬浮粒子等级计数与测量
目的
悬浮粒子等级计数是对粒径分布在μm至μm之间的悬浮粒子进行计数,为了验证或定期测量设施的洁净度等级。
测试方法
采用计数浓度法,通过测试洁净环境内单位体积空气中含大于或等于某粒径的悬浮粒子数,来评定洁净室(区)的悬浮粒子洁净度级别。
仪器
激光尘埃粒子计数器。
测试状态
静态测试,测试时宜在空气净化正常运行时间不少于30min后开始,或在生产操作人员撤离现场并经过30min自净自净后开始。
动态测试,测试时需记录生产开始时间以及测试时间。
检测频率:
静态、动态连续检测三天。
采样点数目及其布置
悬浮粒子洁净度监测的采样点数目及其布置要根据房间面积和功能设置。
最少的采样点数目
面积
m2
洁净度级别
D级
<10
2
≥10≤~<20
2
≥20≤~<40
2
≥40≤~<100
2
采样点的位置
采样点一般离地面米高度的水平面上均匀布置。
采样点大于5点时,也可以在离地面~米高度的区域内分层布置,但每层不少于5点。
平面采样点布置图
采样次数的限定
对任何小洁净室(区)或局部空气净化区域,采样点的数目不得少于2个,总采样次数不得少于5次。
最小采样量
最小采样量
L/次
洁净度级别
D级
≥μm
≥5μm
结果计算
采样点的平均悬浮粒子浓度(A)
式中:
A某一采样点的平均粒子浓度,粒/m3;
Ci为某一采样点粒子浓度(i=1,2,……,n),粒/m3;
n为某一采样点上的采样次数。
95%置信上限(UCL)
式中:
UCL为平均值均值的95%置信上限,粒/m3;
t为95%置信上限的t分布系数。
95%置信上限的t分布系数
采样点数
2
3
4
5
t
结果评定
每个采样点的平均悬浮粒子浓度必须低于或等于规定的级别界限。
全部采样点的悬浮粒子浓度平均值均值的95%置信上限必须低于或等于规定的级别界限,即UCL≤级别界限。
可接受标准
洁净度级别
悬浮粒子最大允许数/立方米
静态
动态
≥μm
≥5μm
≥μm
≥5μm
D级
3520000
29000
不作规定
不作规定
检测结果记录于附表20。
微生物测定
目的
确定浮游的生物微粒浓度和生物微粒沉降密度,以此来判断洁净室是否达到规定的洁净度。
概述
测定的方法
浮游菌、沉降菌和表面微生物。
浮游菌用计数浓度表示:
CFU/L或CFU/m3;沉降菌用沉降浓度表示:
CFU/(皿·min);表面微生物用菌落数表示。
测试时间
阳性菌检查室和微生物限度检查室在臭氧消毒5天后开始检测。
无菌检查室在臭氧消毒5天后开始检测,每次检验结束后,使用杀孢子剂和酸酚消毒。
测试状态
动态测试,测试时需记录生产开始时间以及测试时间。
检测频率
连续检测三天。
浮游菌的测定
测试方法:
本方法采用计数浓度法,即通过收集悬游在空气中的生物性粒子于专门的培养基,经若干时间,在适宜的生长条件下让其繁殖到可见的菌落进行计数。
所用的仪器、设备和培养基
浮游菌采样器;培养皿;培养基;恒温培养箱;高压蒸汽灭菌器。
最少的采样点数目
最少的采样点数目同“。
采样点的位置
采样点位置可以同悬浮粒子测试点。
①工作区测点位置离地~左右(略高于工作面)。
②送风口测点位置离开送风面30cm左右。
③可在关键设备或关键工作活动范围处增加测点。
最小采样量
洁净度级别
采样量(L/次)
D级
100
采样次数
每个采样点一般采样一次。
结果计算
用计数方法得出各个培养皿的菌落数。
每个测点的浮游菌平均浓度的计算:
结果评定
每个测点的浮游菌平均浓度必须低于所选定评定标准的界限。
可接受标准
洁净度级别
cfu/m3
D级
200
检测结果记录于附表21。
沉降菌的测定
测试方法
采用沉降法,即通过自然沉降原理收集在空气中的生物粒子于培养基平皿,经若干时间,在适宜的条件下让其繁殖到可见的菌落进行计数,以平板培养皿中的菌落数来判定洁净环境内的活微生物数,并以此来评定洁净室(区)的洁净度。
仪器和设备
培养皿;培养基;恒温培养箱;高压灭菌器。
最少的采样点数目
最少的采样点数目同“。
采样点的位置
采样点位置可以同悬浮粒子测试点。
①工作区测点位置离地~左右(略高于工作面)。
②送可在关键设备或关键工作活动范围处增加采样点。
③可在关键设备或关键工作活动范围处增加测点。
最少培养皿数
在满足最少采样点数目的同时,还宜满足最少培养皿数。
洁净度级别
最少培养皿数
D级
2
采样次数
每个采样点一般采样一次。
结果计算
用计数方法得出各个培养皿的菌落数。
每个测点的沉降菌平均浓度的计算:
式中:
—M为平均菌落数;M1为1号培养皿菌落数;
M2为2号培养皿菌落数;Mn为n号培养皿菌落数;
n为培养皿总数。
结果评定
每个测点的沉降菌平均菌落数必须低于所选定评定标准的界限。
可接受标准
洁净度级别
cfu/m3
D级
100
检测结果记录于附表21。
表面微生物的测定
测试方法
触碟法和擦拭法。
仪器和设备
φ55mm培养皿(凸碟);培养基;恒温培养箱;高压灭菌器。
人员表面菌检测
操作人员出洁净区前,在更洁净衣间进行取样。
先分别取2只手套五指样,手套取样时应包括双手的手指和手掌;打开接触碟盖子,将五指轻轻按于接触碟培养基上10秒钟后,盖回上盖,做上标识。
洁净服表面取样主要是前胸、手肘和膝盖样;用接触碟分别轻压洁净服前胸部、手肘部(任一边)、膝盖部(任一边)10秒钟后,盖回上盖,做上标识,标明操作人员代号、取样位置及取样时间。
设备环境表面菌检测
在清场前用接触碟对主要检验操作设备表面、地面和墙面进行取样,取样后,立即对取样位置用消毒液擦拭。
设备表面擦拭样为操作时人员易接触位置。
结果评定
每个测点的平均菌落数必须低于所选定评定标准的界限。
可接受标准
洁净度级别
接触碟(cfu/皿)
5指手套(cfu/t手套)
D级
50
——
检测结果记录于附表21。
悬浮粒子及微生物监测采样点位置
见悬浮粒子及微生物监测采样点位置平面图。
悬浮粒子及微生物监测采样计划
房间名称
洁净度
级别
房间面积
(m2)
采样点数
悬浮粒子
沉降菌
浮游菌
采样量L/次
最少
培养皿数
采样
时间
采样量
≥μm
≥5μm
女更洁净服
D
2
2
30min
100L
静压差确认
目的:
检查洁净室和邻室之间是否保持必须的正压或负压,从而知道空气的流向,这一项测定应在风量测定之后进行。
检测仪器:
测试仪器用微压计。
检测方法:
测量前应将所有门都关闭,测量时不允许有人穿越房间,并开启房间中的排风机或除尘器,通过墙壁上安装的微压表,读出房间这间的压差。
从平面上最里面的房间依次向外测定。
检测频率:
每5±小时读数记录1次。
可接受标准
相邻不同级别房间的静压差绝对值应≥5Pa,洁净室与室外的压差应≥10Pa。
监测结果记录于附表15。
温湿度确认
目的:
确认取样间空气净化系统具有将洁净厂房温度、相对湿度控制在设计要求范围内的能力。
检测仪器:
温、湿度计。
检测方法:
通过温、湿度表对各房间进行检测。
检测频率:
每日检测两次,每5±小时读数记录1次。
可接受标准
洁净度级别
温度
相对湿度
D级
18-26℃
45-65%
监测结果记录于附表18。
8.偏差处理程序
空气净化系统性能确认过程中,应严格按照系统标准操作规程,维护保养规程,检测规程和质量标准进行操作和判定。
出现个别项目不符合标准的结果时,应按下列程序进行处理:
待系统稳定后,重新检测。
必要时,分区分段进行对照检测,分析检测结果以确定不合格原因。
若属系统运行方面的原因,必要时报验证工作组,调整系统运行参数或对系统进行处理。
若属系统运行方面的原因,需报验证小组,调整运行参数或对系统进行处理后再进行性能确认。
在验证过程中应严格按照本方案规定的内容进行,在执行本方案的过程中发生任何偏差均应有文件记录,并将所有偏差情况描述清楚,并列出偏差纠正结果,说明引起偏差的原因。
实施责任人应保证结论正确无误。
验证工作组应对本系统中所有偏差与纠正予以审核、认可。
9.验证的结果评价及建议
设备验证小组负责收集各项验证、试验结果记录,根据验证、试验结果起草验证报告,报验证工作组。
验证工作组对验证结果进行综合评估,做出验证结论,发放验证证书,确认空气净化系统日常监测程序及验证周期。
对验证结果的评审应包括:
验证测试是否有遗漏;
验证实施过程中对验证方案有无修改,修改原因、依据以及是否经过批准;
验证记录是否完整;
验证试验结果是否符合标准要求,偏差及对偏差的说明是否合理,是否需要进一步补充试验。
10.再验证周期确定
根据验证评审结果及验证后风险评估分析,提出该系统正常运行条件下的再验证周期,确认是否仍处于受控状态,若确认为非受控状态,则需立即重新进行验证。
11.验证文件归档
验证工作结束后10天内,验证小组将整套验证文件交质量管理部QM验证管理员处存档。
厂家检测报告作为验证文件的附件附在验证记录中。
12.附表
附表1:
空调机组技术适用性检查表
附表2:
洁净区工艺布局检查表
附表3:
空调机组风机选型检查表
附表4:
空气净化系统资料检查记录
附表5:
风管制作、气密性及清洁确认