最新大米加工生产线集中控制系统设计.docx
《最新大米加工生产线集中控制系统设计.docx》由会员分享,可在线阅读,更多相关《最新大米加工生产线集中控制系统设计.docx(37页珍藏版)》请在冰豆网上搜索。
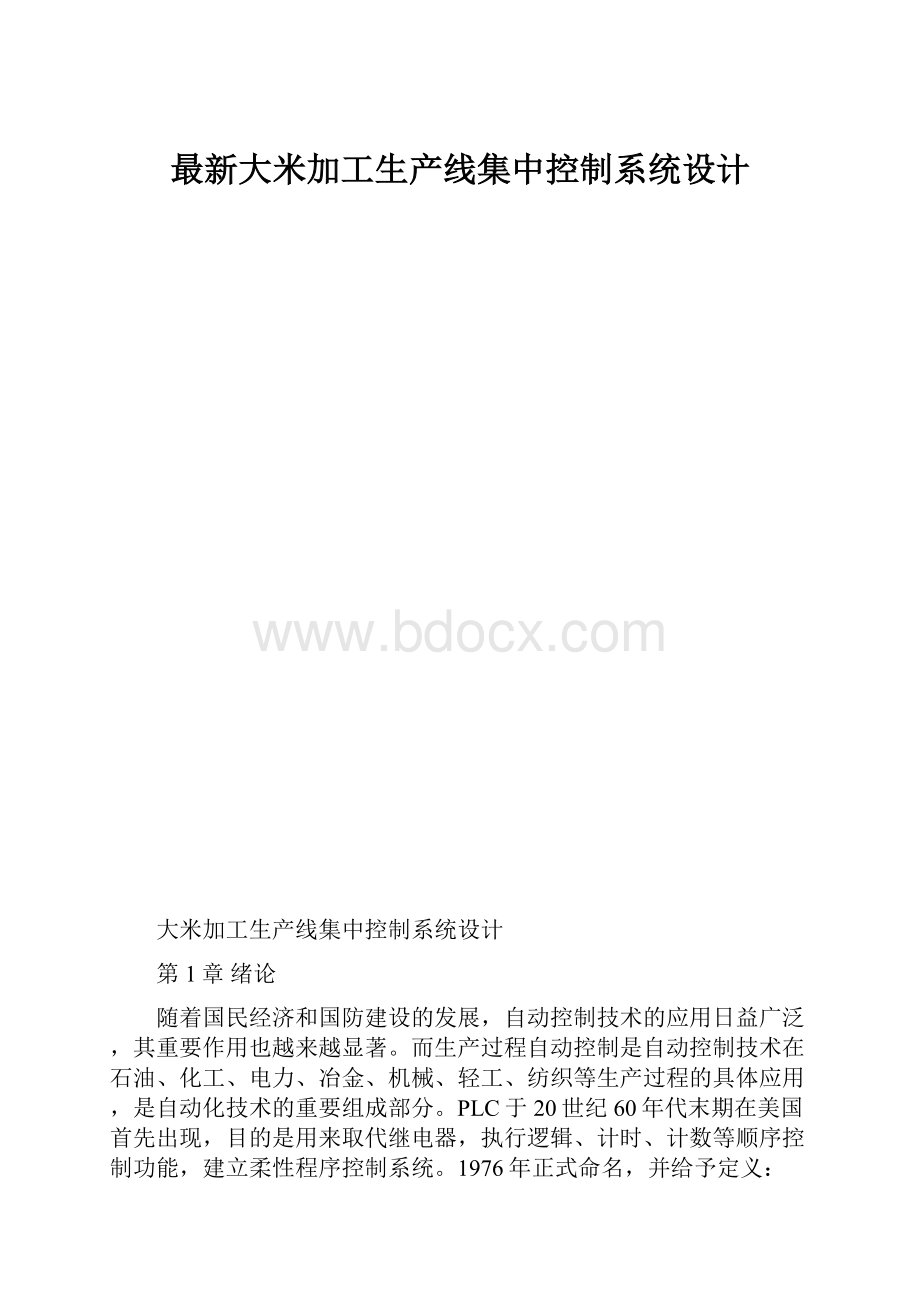
最新大米加工生产线集中控制系统设计
大米加工生产线集中控制系统设计
第1章绪论
随着国民经济和国防建设的发展,自动控制技术的应用日益广泛,其重要作用也越来越显著。
而生产过程自动控制是自动控制技术在石油、化工、电力、冶金、机械、轻工、纺织等生产过程的具体应用,是自动化技术的重要组成部分。
PLC于20世纪60年代末期在美国首先出现,目的是用来取代继电器,执行逻辑、计时、计数等顺序控制功能,建立柔性程序控制系统。
1976年正式命名,并给予定义:
PLC(ProgrammablelogicController)是一种数字控制专用电子计算机,它使用了可编程序存储器储存指令,执行诸如逻辑、顺序、计时、计数与演算等功能,并通过模拟和数字输入、输出等组件,控制各种机械或工作程序。
随着工业自动化水平的迅速提高,计算机在工业领域的广泛应用,人们对工业自动化的要求越来越高,种类繁多的控制设备和过程监控装置在工业领域的应用,使得传统的工业控制软件已无法满足用户的各种需求。
本次设计的大米加工生产线控制系统是以PLC为核心控制器,并结合昆仑组态软件MCGS,辅以光电传感器,继电器等实现的可远程控制的集成系统。
它能够很好地解决传统工业控制软件存在的种种问题,使用户能根据自己的控制对象和控制目的任意组态,完成最终的自动化控制工程。
1.1本课题研究的目的、意义
现代自动控制越来越朝着智能化发展,在很多自动控制系统中都用到了工控机,小型机、甚至是巨型机处理机等,当然这些处理机有一个很大的特点,那就是很高的运行速度,很大的内存,大量的数据存储器。
但随之而来的是巨额的成本。
在很多的小型系统中,处理机的成本占系统成本的比例高达20%,而对于这些小型的系统来说,配置一个如此高速的处理机没有任何必要,因为这些小系统追求经济效益,而不是最在乎系统的快速性,所以用可编程序逻辑控制器(PLC)[1]控制小型的,而又不是很复杂,不需要大量复杂运算的系统中是非常适合的。
本论文是对现在大量使用的大米生产线控制系统进行自动化设计改造。
现有的控制系统很大部分是采用老式的继电器触点控制,系统故障率高,工人劳动强度大,系统设备升级困难。
大米生产过程中,如果系统控制不当,则会出现杂质、碎米率大、加工精度不易控制等问题。
为了提高系统的自动化水平,解决大米生产中产生的这些问题,利用现代化的PLC与MCGS组态结合的集中控制技术,在一定程度上能够提高劳动生产率,改善劳动条件,克服人为的不稳定因素,为现代化的生产管理提供强有力的物质条件,以达到系统自动化控制和系统升级的目的。
1.2PLC的简介
可编程序控制器(ProgrammableLogicController)简称PLC,是一种以微处理器为核心的用于工程自动控制的工业控制机,其本质是一台工业控制专用计算机[2]。
PLC是一种专为在工业环境应用而设计的数字运算电子系统,它是以微处理机为基础,综合了计算机技术、自动控制技术和通信技术等现代科技而发展起来的一种新型工业自动控制装置,是当今工业发达国家自动控制的标准设备之一。
1.2.1PLC的特点及应用
可编程序控制器(PLC)得以迅速发展和广泛使用的原因是由于它具有继电接触器控制装置和通用计算机以及其他控制系统所不具备的特点:
1.运行稳定、可靠性高、抗干扰能力强
2.设计、使用和维护方便
3.编程语言直观易学
4.与网络技术相结合
5.体积小、质量轻、能耗低[3]
可编程控制器所具有的功能,使它既可用于开关量控制,又可用于模拟量控制;既可用于单机控制,又可用于组成多级控制系统;既可控制简单系统,又可控制复杂系统。
它的应用可大致归纳为如下几类:
逻辑控制、运动控制、过程控制、数据处理、多级控制。
1.3论文主要研究内容
本篇论文主要论述了如何用三菱FX-2N系列PLC设计大米加工生产线集中控制系统。
从而实现系统所需要的各项功能,满足设计要求。
本文研究内容主要是以PLC控制整个生产过程,其内容有以下几个方面:
1.接通电源开关后,将设备模式旋转到自动定量输送物料模式,将所有阀门旋转到关闭位置;
2.按下启动按钮,利用真空泵把原料吸进吸料漏斗内。
由吸料漏斗落入预量漏斗,再由预量漏斗落入称量漏斗。
通过称重传感器实现自动称量控制;
3.原料由称量漏斗进入砻谷缸,当原料达到砻谷缸设定的位置时,关闭进料阀门开始砻谷,砻谷后,启动鼓风机,进行谷糙分离,分离时,糙米预存缸的进料阀门打开;
4.谷糙分离完毕后,糙米预存缸内开始进行碾米,碾米结束后,起动振动电机筛选碾好的大米,利用鼓风机与高压空气推出大米,通过高压输管送入料笼。
1.4论文组成
对大米加工生产线集中控制系统的设计论文主要从机械和电气两方面进行设计和说明。
第一章讲述的是课题研究意义和目的以及简单地介绍了以下PLC的有关内容如:
PLC特点、PLC的应用和发展趋势、PLC的结构、PLC的工作方式等等。
第二章讲述系统概述及控制方案设计,包括制系统设计目标控制系统设计内容,大米加工生产线集中控制系统方案选择论证。
第三章是本次论文设计的核心部分之一:
控制系统的硬件设计。
它包括了控制系统分析及元件选择,PLC控制系统I/O点数的估算,PLC及主要模块的选型
控制系统的I/O地址分配,控制系统电路设计。
第四章讲述的是软件设计。
包括PLC控制系统梯形图,PLC控制系统程序的编制方法选择,主要模块程序设计和模拟量输入的算法设计。
第五章讲述的是监控界面的设计。
包括系统操作界面,系统参数界面,报表界面,也是本设计的核心控制部分。
第2章控制系统方案设计
随着我国工业自动化水平的不断提高,对大米加工生产线集中控制系统的自动化程度也提出了更高的要求。
传统的大米加工生产线多采用继电器[8]控制电路实现控制要求,机械触点多,可靠性差,控制设备体积大。
近年来,随着计算机技术的发展,机械和电气化程度的提高,新技术产品PLC由于其特有的优点,已广泛地用于粮食加工行业。
2.1大米加工生产线集中控制系统设计要求
2.1.1控制系统设计目标控制系统设计内容
根据大米加工生产线集中控制系统设计的要求,要求达到以下目标:
1.设备具有全自动模式。
2.可远程监控大米加工情况,并对加工量进行历史记录。
3.保证出糙率和大米加工精度。
根据课题要求,该控制系统的设计主要有以下内容:
1.真空吸料:
用一台真空泵将待发原料吸入吸料漏斗,保证原料的称料供应;
2.称量设定:
面板人工设置一次加工需要量,通过称重传感器实现自动称量控制;
3.砻谷控制:
检测垄谷缸内的原料位置,到达设定值时实现自动砻谷控制;
4.大米接收:
砻谷完毕,启动鼓风机进行谷糙分离,分离出的糙米进入碾米缸继续加工,加工后,自动打开缸门,利用鼓风机和高压空气将经过筛选的大米送入料仓。
2.1.2控制系统的主要工艺流程
如图2.1所示大米加工生产线集中控制系统的工艺流程图,可知该集中控制系统的工作过程大概如下:
原料先置于缸内或传送袋内,通过真空泵吸入吸料漏斗,由吸料漏斗再自动落入预量漏斗,由于吸料漏斗为真空,预量漏斗在此起缓冲作用。
原料由预量漏斗落入称量漏斗,待光电开关检测到原料达到设定位置时,关闭放料阀门,进行称量,取得数据后,再打开放料阀门,让称好的稻谷进入砻谷缸进行砻谷,砻谷完毕后,启动鼓风机,让糙米和谷壳经过振动电机进行谷糙分离,糙米进入碾米缸进行碾米,碾米结束后起动振动筛,让合格的大米颗粒进入填料器,鼓风机和高压空气将经过筛选的大米送入料仓。
2.2大米加工生产线集中控制系统方案选择论证
由基于PLC的大米加工生产线集中控制系统的工艺过程可知,整条生产线三个单元功能相对独立且分散,但又需要相互连锁协调。
这需要一个控制系统进行指挥控制。
这些都给控制系统提出了较高要求,需要采用先进的控制技术和控制方法,以提高工程质量并简化控制线路的复杂性,兼顾降低项目成本。
故本课题控制系统选型的基本原则如下:
1.采用先进、可靠、成熟的控制技术以提高系统可靠性;
2.采用模块化设计,提高通用性及设备效率,易于维护;
3.适应今后的技术发展、要求,系统有较高的可扩展性[7]。
控制系统一般采用PLC控制或继电器-接触器控制系统。
PLC的控制与继电器的控制差别有以下几个方面。
1.控制逻辑
继电器控制逻辑采用硬接线逻辑,利用继电器触点的串联或并联,及延时继电器的滞后动作等组合成控制逻辑,其接线多而复杂,体积大、功耗大、故障率高,一旦系统构成后,想再改变或增加功能都很困难。
另外,继电器触点数目有限,每只只有4~8对触电,因此灵活性和扩充性很差。
而PLC采用存储逻辑,其控制逻辑以程序方式存储在内存内,要改变控制逻辑,只需改变程序即可,故成为“软接线”。
其接线少,体积小,因此灵活性和扩展性都很好。
PLC中大规模集成电路组成,功耗小。
2.工作方式
电源接通时,继电器控制线路中各继电器同时都处于受控状态,即该吸合的都应吸合,不该吸合的都应受到某种条件限制不能吸合,它属于并联工作方式。
而PLC的控制逻辑中,各内部器件都处于周期性循环扫描中,属于串联工作方式。
3.可靠性和可维护性
继电器控制逻辑使用了大量的机械触点,连线也多。
触点开闭会受到电弧的损坏,并有机械磨损,寿命短,因此可靠性和可维护性差。
而PLC采用微电子技术,大量的开关动作由无触点的半导体电路完成,体积小,寿命长,可靠性高。
PLC还配有自检和监控功能。
能检查出自身的故障。
并随时显示给操作人员。
还能动态地监视控制程序的执行情况。
为现场调试和维护提供了方便。
4.控制速度
继电器控制逻辑依靠触点的机械动作实现控制,工作频率低,触点的开闭动作一般在几十ms数量级。
另外,机械触点还会出现抖动问题。
而PLC是由程序指令控制半导体电路来实现控制。
属于无触点控制,速度极快,一般一条用户指令的执行时间在μm数量级,而不会出现抖动。
5.定时控制
继电器逻辑利用时间继电器进行时间控制。
一般来说,时间继电器存在定时精确度的不高,定时范围窄,且易受环境湿度和温度变化的影响,调整时间困难等问题。
PLC使用半导体集成电路做定时器,时基脉冲由晶体振荡器产生,精度相当高。
且定时时间不受环境的影响,定时范围一般从0.001s到若干天或更长。
用户可以根据需要在程序中设置定时值,然后由软件来控制定时时间[8]。
从以上几个方面的比较可知,PLC在性能上比控制逻辑优异,特别是可靠性高,设计施工周期短,调试修改方便,而且体积小,功耗低,使用维护方便,但在很小的系统中使用时,价格要高于继电器控制系统。
可编程序逻辑控制器(PLC)采用微处理器作为控制系统的核心,内含存储器、运算器、控制器,根据工业控制过程的特点,进行专门的电路设计,是一种通用的标准的工业控制计算机。
PLC的输入、输出模块与主模块组装在一起,不需要另外的接口,可以直接与行程开关等传感器及驱动执行机构的电磁线圈连接在一起,使控制系统比较简单。
PLC根据类似于继电器控制系统的梯形图进行程序设计,简单明了。
与继电器控制相比较,PLC性能好价格低,功率价格适中[9]。
根据上述分析,PLC是现阶段基于PLC的泡沫发泡机控制系统最理想的控制机。
所以本设计选用PLC作为系统控制机。
下面是对选定方案的分析:
1.可行性分析
A.功能可行性分析:
由于系统各主要部分所需要满足的功能步骤及要求大多是开关量信号,所以选择可编程序逻辑控制器是完全能够满足其功能要求的。
B.系统可靠性分析:
系统设置了光电检测开关,对整条生产线进行监控,使系统可靠性得到了进一步的保证。
C.系统扩展性分析:
系统采用PLC作为控制器,其本身就具有极强的功能扩展性,加之PLC产品的完整性,使得系统功能扩展极其方便。
D.系统可维护性分析:
系统采用先进控制方式,大大降低了工程成本,并由于系统组态及结构简单,这使得可维护性增强。
2.技术性能
A.吸料漏斗物位的控制;
B.欲量漏斗物位的控制;
C.垄米,碾米时间限制;
D.阀门受阻时进行故障报警;
E.整个工作流程的自动化。
本课题所设计的基于PLC的大米加工生产线集中控制系统,利用可编程序控制器和传感器,克服了人为的不稳定因素,充分利用了现代先进技术,提高了劳动生产率,为现代化的生产管理提供了强有力的物质条件。
第3章系统硬件设计
整个系统由软件系统和硬件系统两部分组成。
本章详细介绍了系统的硬件设计,并对硬件的每一个部分进行了分析。
硬件设计的每一个环节完成相应的功能,并组成一个统一的整体。
在对控制系统分析的基础上,对所用的元器件进行选型,PLC地址分配,最后对系统硬件进行总体设计。
3.1控制系统分析及元件选择
本设计的加工集中控制系统是可编程控制器(PLC)为主要控制其,需要进行控制的是整个工艺流程的实现。
通过可编程控制器(PLC)与电机(包括砻谷机、振荡电机、碾米机、真空泵及鼓风机)以及其他外部硬件(电磁阀,传感器)相连实现了整个大米加工生产线集中控制系统的设计。
本次设计的控制系统的结构示意图,如图3.1所示:
光电开关
图3.1系统结构示意图
其主要工作原理如下:
接通电源后,将设备模式旋转到自动定量输送物料模式,将所有阀门旋转到关闭位置;按下启动按钮,利用真空泵把原料吸进吸料漏斗内,等光电开关1检测到原料到位后,关闭真空泵,打开吸料漏斗开关门电磁阀KV1吸料漏斗空气阀KV16,使原料由吸料漏斗落入预量漏斗;
重复该步骤直至光电开关2检测原料到位后,关闭KV1,打开预量漏斗开关门电磁阀KV3,KV2及预量漏斗开关门电磁阀KV4,KV5,让原料快速落入称量漏斗内,达到设定时间后,关闭所打开的KV3,KV2及KV4,KV5,,进行称量,称量结束后,把所测量的数值传送给MCGS触摸屏;
完成称量步骤后,打开称量漏斗高压空气电磁阀KV6,KV7,让待加工的原料由称量漏斗落入砻谷缸内。
启动砻谷电机,进行砻谷,待到砻谷结束后启动鼓风机,让脱出的稻谷壳与糙米分离开来;
分离后,打开砻谷缸高压空气电磁阀KV8,KV9,垄谷缸开关门电磁阀KV10,让糙米快速落入碾米缸内,达到设定时间后,关闭KV8,KV9,KV10,启动碾米电机,碾米结束后,启动振动电机,利用振动筛选取合格大米,最后打开空气电磁阀KV14,碾米缸高压空气阀KV11,KV12,电动阀KV15,把加工好的大米送入料仓。
3.1.1控制系统分析
根据课题设计要求及大米加工生产线集中控制系统的特点,对系统的控制分析如下:
1.打开电源开关后,设定加工方式:
自动或手动,并设定原料重量。
2.按下启动按钮,利用真空泵把原料吸进吸料漏斗内。
由吸料漏斗落入预量漏斗,再由预量漏斗落入称量漏斗。
通过称重传感器实现自动称量控制。
3.原料由称量漏斗进入砻谷缸,通入空气,由压力传感器测量缸内压力,光电传感器检测原料位置,实现自动砻谷控制。
4.砻谷完毕,启动鼓风机进行谷糙分离,分离出的糙米进入碾米缸继续加工,加工后,自动打开缸门,利用高压空气将经过筛选的大米送入料仓。
3.1.2元器件选择及依据
根据控制系统的各项分析以及对元器件的要求,为满足系统功能,系统需要的主要元器件有PLC控制器、压力传感器、称重传感器、光电传感器、砻谷机、碾米机、电磁阀等,下面对几个主要的器件功能进行介绍:
1.三菱FX-2NPLC介绍
三菱FX-2N运行速度快、功能强,适用于要求较高的中小型控制系统。
所以本设计应用此系列的PLC。
FX-2N基本单元由中央处理器(CPU)、电源以及数字量输入输出单元组成。
这些都被紧凑地安装在一个独立的装置中。
在基本单元上连接扩展单元或扩展模块,可进行16-256点的灵活输入输出组合。
可选用16/32/48/64/80/128点的主机,可以采用最小8点的扩展模块进行扩展。
可根据电源及输出形式,自由选择。
程序容量:
内置800步RAM(可输入注释)可使用存储盒,最大可扩充至16K步。
丰富的软元件应用指令中有多个可使用的简单指令、高速处理指令、输入过滤常数可变,中断输入处理,直接输出等。
便利指令数字开关的数据读取,16位数据的读取,矩阵输入的读取,7段显示器输出等。
数据处理、数据检索、数据排列、三角函数运算、平方根、浮点小数运算等。
特殊用途、脉冲输出(20KHZ/DC5V,KHZ/DC12V-24V),脉宽调制,PID控制指令等。
外部设备相互通信,串行数据传送,ASCIIcode印刷,HEXASCII变换,校验码等。
时计控制内置时钟的数据比较、加法、减法、读出、写入等。
2.称重传感器的介绍
智能化称重传感器是近些年来的开发热点。
智能传感器的定义在各国传感器杂志上讨论多年,直到90年代初才有了比较一致的看法:
把凡具有一种或多种敏感功能,能够完成信号探测和处理、逻辑判断、双向通讯、自检、自校、自补偿、自诊断和计算等全部或部分功能的器件叫做智能传感器。
智能传感器可以是集成的,也可以是分离件组装的。
数字式智能称重传感器正是按此思路发展和应用的,同样有两种结构形式,即整体型和分离型[11]。
整体型是在称重传感器内部安装有放大、滤波、A/D转换、微处理器芯片和温度敏感元件等组成数字处理电路,利用微处理器已存入的软件,实施各项数字补偿工艺进行各项性能调整和测试,最后采用电子束焊或激光焊进行密封。
数字式智能称重传感器的制造工艺完全不同于模拟式称重传感器,主要是两个环节:
其一弹性体贴片组成惠斯登电桥电路后,通过试验测试建立数字补偿工艺要求的各项数学模型,形成便于程序化计算的公式。
其二是根据数学模型编制出简单实用的补偿计算软件,存储在微处理器芯片中进行各项误差修正和补偿。
软件技术主要有数字滤波技术,标度变换技术,数字调零技术,温度补偿技术和线性补偿技术等。
同时还应解决抗射频干扰(RFI)、电磁干扰(EMI)和闪电引起的电瞬变等过压保护问题。
分离型是将放置在称重传感器内部的A/D转换等数字处理电路移至一个外部接线盒内,将普通的模拟式称重传感器接入数字接线盒后,其输出便以数字信号传输给与其配套的称重显示控制仪表。
通常把模拟式称重传感器加数字接线盒模式称为模块化数字称重传感器系统。
模拟式称重传感器基本上是手工化生产,人为的因素对产品质量影响较大,数字式智能称重传感器基本上是自动化生产,排除了人为因素对产品质量的影响。
数字式智能称重传感器具有输出信号大,抗干扰能力强,信号传输距离远,易实现智能化控制等特点,较广泛的应用于大型电子平台秤、电子汽车衡,结构复杂的电子料斗秤、电子容器秤和大死载、小活载的特殊电子秤。
NS-TH16系列智能(数字)称重传感器结构简单、坚固、安装方便、抗振动冲击力强,采用先进的微处理技术和数字通讯技术,全密封结构,防水、防腐。
被广泛应用在自动化控制系统中,作为称量、测力等自动控制元件。
所以本设计采用此类型的称重传感器。
3砻谷机的介绍
本次设计所选用的HR10C是佐竹(苏州)机械有限公司的最新研制的砻谷机,它具有以下特点:
1.脱壳率高且保持稳定,本机采用自动控制操作,脱壳率在90%左右,能在生产过程中保持稳定的脱壳率;
2.操作调节方便,本机通过气动控制辊间压力,有料位器与之连接,断料可立即松辊,来料自动延时紧辊;
3.运转平稳,机器主要回转件都经动平衡检验,所以运转平稳,振动小;
表3.1砻谷机主要参数
型号
HR10C
加工能力
长粒稻3-5t/h
短粒稻4-6t/h
所需功率
7.5kw-4p,52W+3.7kw-4p,0.1kw
主轴转速
HU10FT1150转/分
HA10W
(2)1400转/分
橡胶辊尺寸
直径:
10英寸,宽:
10英寸
橡胶辊硬度
87°±5°
净重
HU10FT410kg
HA10W
(2)890kg
4碾米机的介绍
新型立式碾米机的设计思想是近百年来立式碾米经验的积累。
该机汇集了许多立式碾磨的最新技术,它广泛使用在美国、欧洲和亚洲国家的许多主要加工厂中。
用于加工不同等级白米的VTA系列是现代大米加工工业的理想设备,其具有以下特点:
1.加工产量高、破碎低,在碾磨过程中,由于采用了新研制的最佳碾磨室,因此大米产量提高,破碎减少,水分损失小;
2.操作调节方便,通过卸料门压力调整即可容易地获得所需的研白精度;
3.部件易于更换,砂辊能很容易从机器顶部抽出。
筛片设计从机器旁边取出,在不拆除机器框架情况下,筛片更换迅速、容易。
全部其它部件易于操作、易于更换;
4.部件使用寿命长,由于碾白室进行了特殊的热处理以及它受到均匀一致的较小压力,从而该磨损部件的使用寿命延长;
5.机器内部的米糠残留量最少,碾白室的下部有回转式排出器,有助于米糠顺利排出机外;
6.结构设计紧凑,特殊设计的碾白室几乎是传统设备碾白面积的两倍,而且该机占地小,产量高;
表3.2砻谷机主要参数
型号
VTA7C
糙米处理量
4-6(t/h)
电机
37kw-6p
主轴转速
700r.P.m
风量
40m3/min
静压
-100--150mmAq
外形尺寸
1,447×850×1,989(mm)
5触摸屏的介绍
本次设计采用MCGS触摸屏,MCGS即"监视与控制通用系统",英文全称为MonitorandControlGeneratedSystem。
作为工业过程控制和实时监测领域服务的通用计算机系统软件MCGS,它的功能十分完善,不仅操作简便、可视性好,而且具有可维护性强等突出特点。
MCGS为解决工程监控问题提供了丰富多样的手段,从设备驱动(数据采集)到数据处理、报警处理、流程控制、动画显示、报表输出、曲线显示等各环节,均有丰富的功能组件和常用图形库可供选用,用户只需根据工程作业的需要和特点,进行方案设计和组态配置,即可生成用户应用软件系统。
在这次大米加工生产线集中控制系统的设计中,触摸屏的使用加深了自动化的程度,我们不仅可以通过PLC的在上位机的线上监控功能查询加工情况,更能直接通过MCGS直观图像获取我们大米加工所进行的流程,大米实时加工量,及历史加工量的记录,也能直观的找到报警记录,同时我们可以直接在触摸屏上对加工物料量进行调整设置等,极大地便利了加工生产线的操作。
系统所需主要元器件及功能要求表如下所示。
表3.3系统所需主要元器件及功能要求
序号
器件名称
规格
数量
性能
1
PLC控制器
三菱FX-2N系列
1
控制大米加工工作流程
2
昆仑通态触摸屏
TPC7062KS
1
监控生产流程
3
光电开关
SA3M-1K
2
用于检测称量漏斗和预量漏斗的原料到位情况
4
称重传感器
NS-TH16
1
用来测稻谷的重量
输出0~10V
量程:
0~500Kg
5
真空泵
1.5Kw
1
通过真空管把原料颗粒吸入吸料缸内
6
振动电机
0.5Kw
1
电机振动使碎米粒筛选出去
7
鼓风机
3.7Kw
1
通过鼓风将谷糙分离
8
砻谷机
HR10C
1
给稻谷脱壳
9
碾米机
VTA7C
1
糙米
3.2控制系统的硬件设计
对系统进行硬件设计,主要包括I/O点数的估算、模块选型、I/O地址分配和电路设计。
3.2.1PLC控制系统I/O点数的估算
由大米加工生产线集中控制系统的PLC自动控制结构示意图以及工艺流程图可得:
大米加工生产线集中控制系统需要两个模拟量输入通道:
1个称重传感器检测原料重量,1个压力传感器用来检测砻缸内的压力。
系统还要求6台电机运行,所以需接接触器线圈。
还应用到大量的电磁阀及少量的开关和按钮等器件。
所需各元器件功能及所占PLC输入输出点数见表3.2,表3.3,表3.4。
由表可知,本次设计的泡沫发泡机控制系统的输入模拟量是2个通道,输入开关量点