粉体成型基本工艺实验.docx
《粉体成型基本工艺实验.docx》由会员分享,可在线阅读,更多相关《粉体成型基本工艺实验.docx(14页珍藏版)》请在冰豆网上搜索。
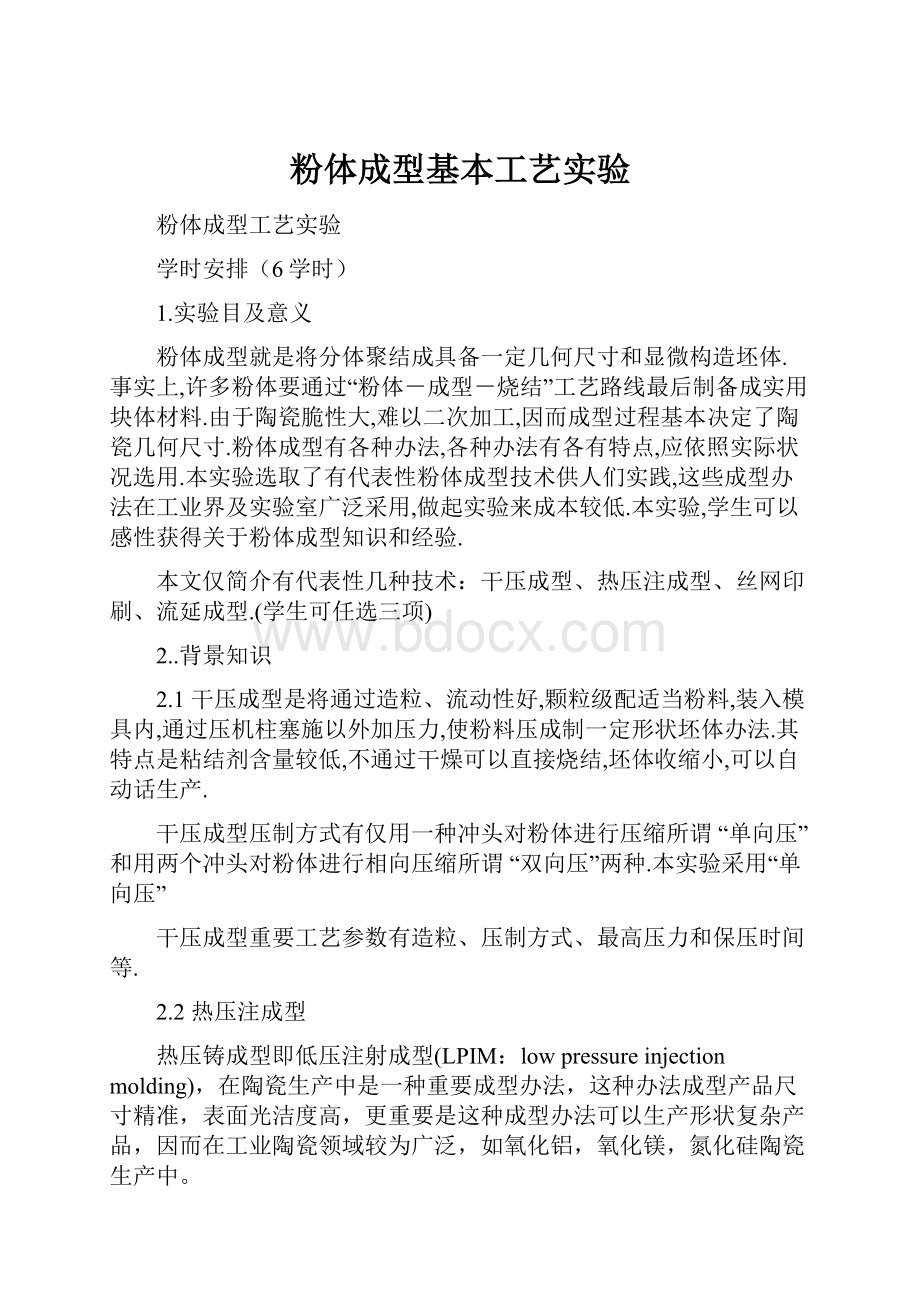
粉体成型基本工艺实验
粉体成型工艺实验
学时安排(6学时)
1.实验目及意义
粉体成型就是将分体聚结成具备一定几何尺寸和显微构造坯体.事实上,许多粉体要通过“粉体-成型-烧结”工艺路线最后制备成实用块体材料.由于陶瓷脆性大,难以二次加工,因而成型过程基本决定了陶瓷几何尺寸.粉体成型有各种办法,各种办法有各有特点,应依照实际状况选用.本实验选取了有代表性粉体成型技术供人们实践,这些成型办法在工业界及实验室广泛采用,做起实验来成本较低.本实验,学生可以感性获得关于粉体成型知识和经验.
本文仅简介有代表性几种技术:
干压成型、热压注成型、丝网印刷、流延成型.(学生可任选三项)
2..背景知识
2.1干压成型是将通过造粒、流动性好,颗粒级配适当粉料,装入模具内,通过压机柱塞施以外加压力,使粉料压成制一定形状坯体办法.其特点是粘结剂含量较低,不通过干燥可以直接烧结,坯体收缩小,可以自动话生产.
干压成型压制方式有仅用一种冲头对粉体进行压缩所谓“单向压”和用两个冲头对粉体进行相向压缩所谓“双向压”两种.本实验采用“单向压”
干压成型重要工艺参数有造粒、压制方式、最高压力和保压时间等.
2.2热压注成型
热压铸成型即低压注射成型(LPIM:
lowpressureinjectionmolding),在陶瓷生产中是一种重要成型办法,这种办法成型产品尺寸精准,表面光洁度高,更重要是这种成型办法可以生产形状复杂产品,因而在工业陶瓷领域较为广泛,如氧化铝,氧化镁,氮化硅陶瓷生产中。
热压铸成型具备设备简朴,模具磨损小,操作以便,生产效率高长处。
其成型坯体尺寸较精确,光洁度较高,构造紧密[38]。
这种办法可以成型形状复杂中小型瓷件。
热压铸成型是在热压铸机上进行。
它基本原理是:
在压力下将具备较好流动性热浆料压入金属模内,并在压力持续作用下布满整个金属模具同步凝固,然后除去压力,拆开模具,形成含蜡半成品,再通过脱脂(除去粘结剂)和烧成即得到制品。
热压铸所用浆料普通选取石蜡作为粘结剂,同步加入少量表面活性剂。
表面活性剂作用:
一方面以改进粉料与石蜡之间吸附,保证料浆长期加热后稳定性;另一方面减少粉料与石蜡界面上表面能,减少分子间作用力,提高料浆流动性,并减少石蜡用量。
惯用表面活性剂有油酸、硬脂酸、蜂蜡等。
制备浆料时石蜡加入量普通为粉料质量12.5wt%-13.5wt%,表面活性剂加入量,使用油酸时普通为粉料质量0.4%-0.8%,使用蜂蜡或硬脂酸时则为石蜡质量5%左右。
将石蜡加热熔化,然后将粉料加入,一边加热一边搅拌,也可以将粉料加热后加入石蜡溶液。
当粉料与石蜡充分混合均匀后,经凝固制成蜡板,以备成型之用。
本实验采用图1所示热压铸机成型.
图1热压注成型机
要保证热压铸正常进行,蜡浆所要满足重要性能指标涉及:
1稳定性:
长时间加热并且不搅拌时,蜡浆保持均匀不分层性能。
2可注性:
蜡浆布满型腔得到精确外形能力。
普通粘度低、凝固速度小、粉料干燥、颗粒大小适当蜡浆可注性好。
3装填密度:
单位体积坯体中所含粉料数量,装填系数大则烧成收缩变形小,构造稳定致密。
4收缩率:
熔化蜡浆凝固为固体时体积收缩率。
收缩率与粉料、石蜡膨胀系数关于,与石蜡含量成正比,也和热压铸温度关于。
将配制好蜡板放置在热压铸机盛浆桶内,加热至一定温度,熔化蜡浆在压缩空气驱动下,通过供料管进入模腔,依照产品详细状况,保持一定期间后卸压,模型中蜡浆冷却,脱模得到坯体。
热压铸成型办法生产产品具备外形规整、尺寸精准、表面光洁度高等特点。
热压铸成型工艺不但可以成型精准尺寸复杂形状制品,并且操作以便,生产效率高[38]。
因而热压铸成型办法使用十分广泛。
热压铸在成型过程中如果控制不合理容易产生各种不同缺陷,如表1:
缺陷
因素
欠铸
蜡浆流动性差;注浆口温度过高或过低;压力和注浆时间不够;
模具中气体未完全排除。
凹坑
浆料和模具温度过高,坯体冷却时收缩增大;脱模过早;
进浆口大小和位置不合理。
变形
模具温度过高或脱模过早,坯体未完全凝固。
开裂
模具温度过低,坯体冷却速度过快,模具型芯制止坯体收缩而产生开裂。
起泡
蜡浆中具有空气;浆料流动性过大或压力过大;模具设计不合理。
皱纹
浆料性能不好,粘度大,流动性差;模具内空气未排尽;
成型时温度过低影响浆料流动性。
表1热压铸成型过程易产生缺陷及其因素
可见产生缺陷重要是由蜡浆流动性,粘度,浆体和模具温度控制,成型压力等因素导致。
各种缺陷有着不同改进办法减少缺陷,如凹坑改进办法是掌握好浆料和模具温度及脱模时间,选取适当进浆口尺寸和位置;气泡改进办法是拌蜡时充分排除浆料中空气,控制好石蜡及表面活性物质加入量,防止加入过多引起浆料流动性过大,选取适当成形压力,设计合理模具。
变形与开裂解决办法是掌握好模具温度和脱模时间,模具注浆口要有一定斜度。
注意以上因素则可以有效地提高成型质量。
2.3丝网印刷
丝网印刷将流延生坯平放在承印台上,通过真空负压将丝网吸附固定,将浆料印在流延生坯上.基本原理是:
在丝网制造一种可以漏过浆料图形(网模),在压力作用下,让浆料漏过丝网在基板表面上形成该图形厚膜层.本实验所用丝网印刷如图二所示.
图2丝网印刷机一台
丝网印刷特点归纳起来重要有如下几种方面:
①丝网印刷可以使用各种类型油墨.即:
油性、水性、合成树脂乳剂型、粉体等各类型油墨.
②版面柔软.丝网印刷版面柔软且具备一定弹性不但适合于在纸张和布料等软质物品上印刷,并且也适合于在硬质物品上印刷,例如:
玻璃、陶瓷等.
③丝网印刷压印力小.由于在印刷时所用压力小,因此也适于在易破碎购物体上印刷.
④墨层厚实,覆盖力强.
⑤不受承印物表面形状限制及面积大小限制.由前述可知,丝网印刷不但可在平面上印刷,并且可在曲面或球面上印刷;它不但适合在小物体上印刷,并且也适合在较大物体上印刷.这种印刷方式有着很大灵活性和广泛合用性.
丝网印刷普通有两种,即手工印刷和机械印刷.
手工印刷是指从续纸到收纸,印版上、下移动,刮扳刮印均为手工操作.
机械印刷是指印刷过程由机械动作完毕.其中又分为半自动和全自动印刷,半自动指承印物放入和取出由人工操作,印刷由机械完毕;全自动是指整个印刷过程均由机械完毕.
本实验中采用手工印刷,印刷图案如图3所示.
图3丝网印刷印制图样
印刷后图形常用异常有:
图案有毛边、电路断断续续、涂覆层厚薄不均、线宽不均匀等:
.导致这些问题因素涉及到丝网印版,刮板,浆料,操作技术等.有是单一方面因素所引起,有是错综复杂各种因素交叉成果,产生这些缺陷因素分析如下:
(1)图案有毛边最重要因素是浆料粘度太小,穿过网框,在基板上形成电路后,发生了二次流动.也有也许是印刷完取下时,操作不当导致.
(2)电路断断续续因素也许是印刷时料浆不够,或是料浆粘度过大,不易通过网框;也有也许是刮板时用力不均.
(3)涂覆层厚薄不均最也许因素是印刷时,用力不均,导致不同地方浆料透过多少不同所致.
(4)线宽不均匀也许是浆料局限性或是网板上空隙在先前印刷中被堵住了,导致浆料无法通过.
在印刷工艺中应当注意选取浆料粉体粒度不易过大,调节浆料粘度,印刷过程中刮板用力均匀,在印刷结束前尽量避免生坯移动,防止二次印刷产生重印,印刷完毕后对丝网进行清洗,保证下次印刷时不会发生丝网堵塞等现象.
2.4流延成型
流延成型基本含义是将浆料在一平面上自由铺展,使其固化后获得一薄片状型坯.起设备并不复杂,并且工艺稳定,可持续操作,便于生产自动化,生产效率高.
流延成型基本工艺流程为:
制备浆料→流延→固化→剪裁
流延成型要用特殊浆料,其构成有点类似丝网印刷,只是少了无机粘结剂,由于流延成型坯并不需要最后依附在一种基底上.
流延时,浆料从储料斗中流出,铺展在塑料或不锈钢衬带上,其厚度由一刮刀高低额位置来控制,衬带由一转轮带动向前运动,通过固化区时,浆料固化成坯,然后从衬带上剥离下来.
图4图流延成型原理图
图5流延成型机
在本实验中,流延生坯常浮现如下缺陷,见图6.
(a) (b)
(c)(d)
图6流延成型生坯中常浮现缺陷类型
(a)中生坯表面有裂纹及团聚颗粒等;
(b)生坯有严重皱纹及开裂;
(c)生坯表面有气泡及凹坑;
(d)生坯一边有鱼鳞状纹路.
产生以上缺陷因素详细分析如下:
(1)裂纹:
产生裂纹因素有各种,除了粘结剂局限性因素,还也许是由于流延胶带不平或胶带上有杂质划痕而使流延后浆料在干燥过程中受到外界应力作用而浮现不持续状态,继而导致裂纹等缺陷;
(2)团聚颗粒:
分体分散不均匀,PVB未完全溶于溶剂时就进行秋磨或者在球磨完毕后有大颗粒杂质混入等都也许产生团聚颗粒;
(3)皱纹:
重要是由于溶剂添加量过多,生坯干燥过快时,由于表层收缩过快,而生坯里面尚未开始发生收缩,则会浮现皱纹,当生坯厚度较大时更加明显;
(4)凹坑或气泡:
球磨后浆料中混有诸多气体,如果未通过真空除泡解决则极容易产气愤泡缺陷,在流延后,气泡如果自动破裂则形成凹坑;
(5)单边鱼鳞状纹路:
重要是由于流延机表面不平使浆料发生了流动导致.
为避免以上容易产生缺陷在成型过程中应当注意如下问题:
(1)注意控制添加剂含量.当粉体松装密度小,比表面积大,一次球磨时添加溶剂和分散剂需要较多,否则将浮现一次球磨后粉体分散不均匀现象;同样在二次球磨时加入粘结剂及塑化剂含量也要相应增长,否则会产生与以上未煅烧粉体成型生坯相似塑性,强度不够及裂纹等缺陷;
(2)流延成型之前对使用除尘布胶带进行清理,避免由尖锐东西划伤胶带,定期调节流延机水平度;
(3)成型之前先对浆料进行真空搅拌除泡解决,直至浆料中无气泡溢出为止,然后过滤浆料以除去粘结剂团聚体或其她杂质颗粒;
(4)
成型后立虽然用玻璃罩将浆料罩住,防止浆料挥发干燥过快以及空气中尘埃对生坯导致污染.
生坯柔度测量:
生坯不开裂最小卷曲半径来衡量生坯柔度.流延生坯柔度测量办法如图7,不产生裂纹时最小卷曲半径,表白其柔度较好.能满足后续素坯组装工艺规定.
图7生坯柔度测量办法
3.实验内容
3.1干压成型(两学时)
重要原料、设备有:
陶瓷粉体70g、盘式电阻炉一种、瓷盘一种、刮板一种、5%聚乙烯醇水溶液10ml、烧杯一种、40目筛一种、成型模具一套、压力机一台、天平一台、游标卡尺一种
粉体成型前要进行塑化,其要领是加进塑化剂,进行造粒解决.塑化剂建议采用含5%聚乙烯醇水溶液,塑化剂与粉体重量比例大概为5:
100,视详细状况而定.将粉体盛装在瓷盘里,逐渐倒入塑化剂,同步不断用刮板手工拌和,使塑化剂与粉体充分混合,最后将拌匀粉体过40目筛.
成型前要熟悉模具装模和脱模办法以及压机操作办法,然后才干进行成型.将粉倒如模具腔内.注意粉不要太多.然后将整体放到万能材料实验机上.运用模具将经造粒粉体压制成5个重量相等、φ25圆片,但采用压力不同,压力分别为5、10、15、20、25、30Mpa.保压6-10S.坯体重量控制以控制模具装粉量来实现.取出样品,以便烧结.
采用控制用游标卡尺测量它们高度,绘出成型压力与型坯高度关系曲线.将压力为5Mpa和30Mpa坯体用手折断,感觉它们强度差别,试分析其因素.
3.2热压注成型(两学时)
本实验需用重要原料、设备有:
热压注成型用喂料50g、热压注成型机一台,空气压缩机一台、成型模具一套、天平一种、差热及热失重分析仪一套、陶瓷坩锅一种、高温烘箱一台、游标卡尺一种.
本实验规定用热压注办法制备一种管状陶瓷型坯,其重要工艺流程为:
喂料制备→成型
A)喂料制备
喂料已经由实验室实现做好,可以直接使用.喂料配方为:
氧化铝粉、石蜡、硬脂酸间质量比为77:
20:
3.
在氧化铝粉加入1%~3wt%SA作为表面活化剂球磨48小时.球磨后粉体在真空干燥箱中80℃下恒温干燥12h,注意干燥温度不适当过高,以避免SA挥发.粉体干燥后进行和蜡,将石蜡在80℃下加热溶化后,将干燥后粉体缓缓倒入溶化石蜡中,并使用玻璃棒不断搅拌,直至粉体与石蜡基本混合均匀,搅拌过程中注意保持蜡浆温度在80℃左右,将初混后浆料陈腐48小时
解决后浆料进行热压铸成型,热压铸成型压力控制在0.4~0.8MPa之间,浆料温度控制在100℃左右,模具温度约50℃,保压时间为6~10s.样品为圆片状.尺寸为φ25X2mm.
3.3丝网印刷(两学时)
重要原料、设备有:
平均粒径在1微米左右氯化铁粉末20g、由松油醇10g、乙基纤维素2g、司班801g、天平一台、球磨罐一种,氧化铝研磨体球磨150g、行星球磨一套、.真空除气装置一套、锥板粘度计一台、丝网印刷机一台(图2)、聚氨酯橡胶刮板一种、
制备好氧化铝流延成型片两块、金相显微镜一台、万用表一种.
本实验要用丝网印刷办法在氧化铝流延基片上制备一组氯化铁厚膜电路.
A)浆料制备
钨质丝网印刷浆料配方为:
氯化铁粉与有机载体质量比为75:
25,其中钨粉平均粒径在1微米左右,有机载体由松油醇、乙基纤维素、司班80构成,质量比为94:
5:
1.用天平将这些原料分别称取后装入球磨罐中后,加进5倍质量氧化铝研磨体球磨24小时,制备成浆料.将该浆料在不不大于95%真空度下进行除气解决30分钟后,即可使用.
B)丝网印刷
丝网印刷在专用丝网印刷机上进行.将流延生坯平放在承印台上,通过真空负压将丝网吸附固定,将浆料印在流延生坯上.
以此前制备氧化铝流延成型片作基板,将其固定在丝网印刷机上,压上网板,在丝网上倒上浆料,刮板加压与网框呈约60度角刮动浆料,将浆料印刷到陶瓷基片上.为了研究印刷工艺,分一次、两次印刷,观测印刷效果.印制膜至少在室温下干燥24小时后,固化.
3.4流延成型(两学时)
重要原料、设备有:
陶瓷粉体50g、三乙醇胺1.25g、无水乙醇和丁酮(质量比3:
2)混合液25g、聚乙烯醇缩丁醛PVB4.8g、聚乙二醇(PEG)邻苯二甲酸二丁酯(PHT)各3g、氧化铝研磨体200g,、球磨罐一种、瓷盘一种、100ml烧杯一种、40目筛一种、流延成型机一套、天平一台、锥板粘度计一台、行星球磨机一台.
用天平称取陶瓷粉体50g、无水乙醇和丁酮混合液25g、三醇乙胺1.25g、氧化铝研磨体200g,装入球磨罐中后,球磨24小时.再用天平称取加入邻苯二甲酸二乙酯各3g、聚乙烯醇缩丁醛(PVB)4.8g,加入球磨罐中,继续球磨24小时.将球磨好料浆过40目筛,除去粘结剂结块及研磨体.
将上述料浆倒入流延机中进行流延,流延速度为12cm/min,流延温度为22℃到24℃,刮刀高度依照成型薄片厚度进行调节.流延浆料在室温下需24小时逐渐挥发溶剂而固化,在此期间不要触动它.放置1~2天后,可将流延型坯从流延基带上剥下.再用剪刀将它裁剪成20x40mm条状.
4.实验数据解决与思考题
4.1干压成型
4.1.1纪录实验中有关参数.测量在不同成型压力下样品厚度,并计算样品密度.成果填在下表:
样品
成型压力
型坯高度
型坯密度
备注
1
2
3
4
5
依照以上数据,绘出成型压力与型坯密度关系曲线.
4.1.2思考题目
型坯密度是均匀吗?
如果不是,有那些改进办法?
4.2热压铸成型
4.2.1纪录实验中有关参数和样品缺陷.测量在不同成型温度下样品密度.成果填在下表:
样品
成型温度
型坯质量
型坯密度
备注
1
2
3
4
5
依照以上数据,绘出成型温度与型坯密度关系曲线.
4.1.2思考题目
成型后会浮现难以脱模问题,请问是什么因素?
有那些改进办法?
4.3丝网印刷
测量不同浆料粘度,观测相应样品缺陷.试分析因素.
4.4流延成型
4.4.1纪录实验中有关参数和样品缺陷.测量在不同干燥时间下样品柔度.成果填在下表:
样品
刮刀高度
干燥时间
样品柔度
备注
1
2
3
4
5
依照以上数据,绘出干燥时间与样品柔度关系曲线.
4.4.2思考题目
试分析流延速度、干燥温度对流延型坯质量影响