锌电解工业实践中电流效率下降的原因分析及对策.docx
《锌电解工业实践中电流效率下降的原因分析及对策.docx》由会员分享,可在线阅读,更多相关《锌电解工业实践中电流效率下降的原因分析及对策.docx(17页珍藏版)》请在冰豆网上搜索。
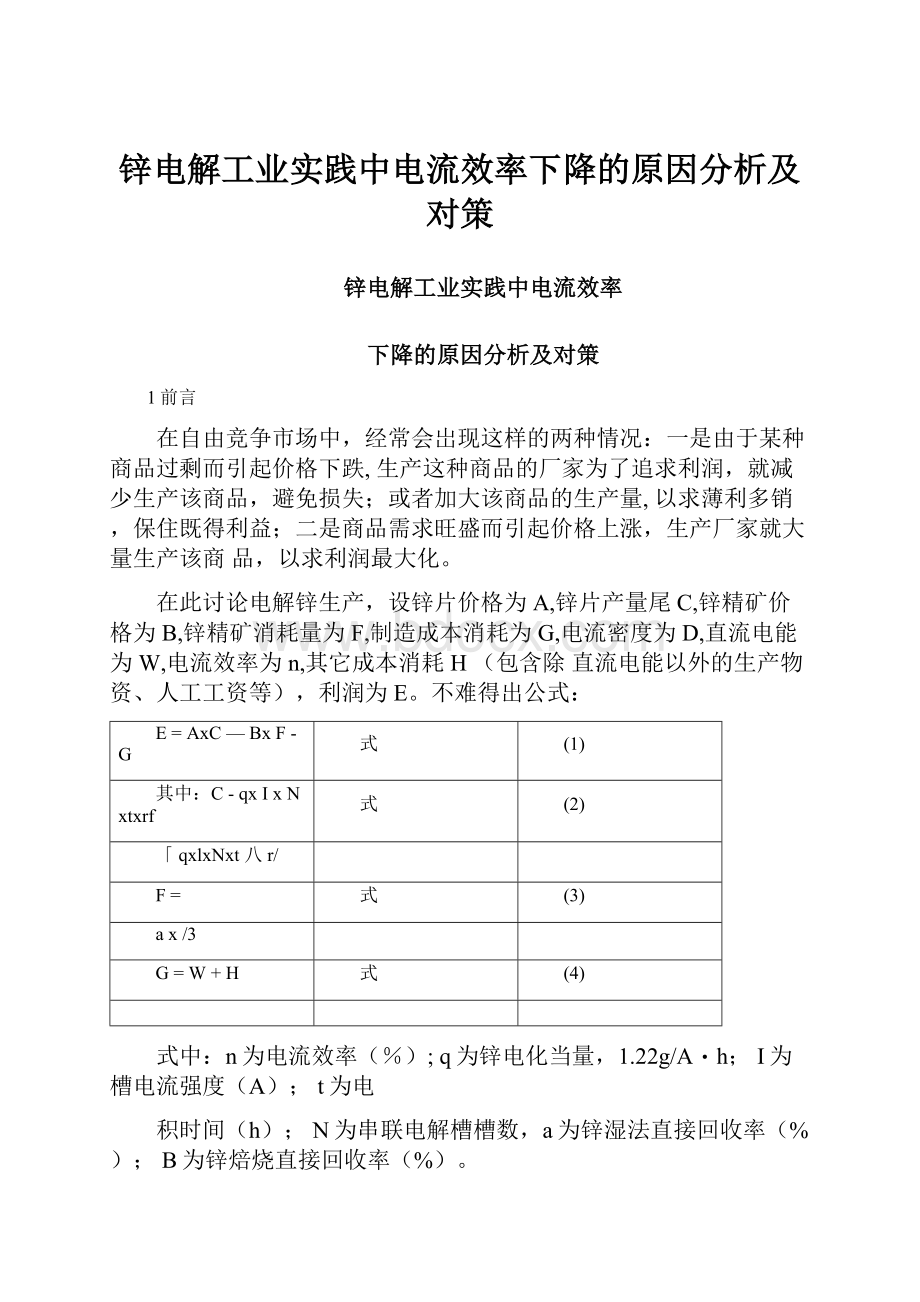
锌电解工业实践中电流效率下降的原因分析及对策
锌电解工业实践中电流效率
下降的原因分析及对策
1前言
在自由竞争市场中,经常会岀现这样的两种情况:
一是由于某种商品过剩而引起价格下跌,生产这种商品的厂家为了追求利润,就减少生产该商品,避免损失;或者加大该商品的生产量,以求薄利多销,保住既得利益;二是商品需求旺盛而引起价格上涨,生产厂家就大量生产该商品,以求利润最大化。
在此讨论电解锌生产,设锌片价格为A,锌片产量尾C,锌精矿价格为B,锌精矿消耗量为F,制造成本消耗为G,电流密度为D,直流电能为W,电流效率为n,其它成本消耗H(包含除直流电能以外的生产物资、人工工资等),利润为E。
不难得出公式:
E=AxC—BxF-G
式
(1)
其中:
C-qxIxNxtxrf
式
(2)
「qxlxNxt八r/
F=
式
(3)
ax/3
G=W+H
式
(4)
式中:
n为电流效率(%);q为锌电化当量,1.22g/A・h;I为槽电流强度(A);t为电
积时间(h);N为串联电解槽槽数,a为锌湿法直接回收率(%);B为锌焙烧直接回收率(%)。
将式
(2)和式(3)代入式
(1)后可得:
E=qxIxNxtxr/x(A-Bx—-—)-W'—H式(5)
ax
从式(5)中科看出:
决定利润E的变量有电流效率q、锌片价格为A、锌精矿价格为B、锌湿法直接回收率a、锌焙烧直接回收率B、直流电能为W和其它成本消耗H。
其中通过锌湿法直接回收率计算公式、锌焙烧直接回收率计算公式和直流电能计算公式我们不难得出:
a和B是关于n的增函数f(n),w是关于n的反函数f"(n),代入式(5)后有:
E=qXIXNXtXf(H)X[A~BXf1(q)Xf_l(n)]一尸(n)—H式(6)通过式(6)可看出:
电流效率对锌电积工厂的利润至关重要,无论产品与原料成本如何波动,提高电流效率总是增加工厂利润的关键因素之一。
2电流效率下降的原因分析
一个炼锌厂当面积电流确定后,通过电解槽的电流强度,便可根据电极面积和数目计算出。
通电一定时间后,也就可以按锌的电化当量计算岀锌的析出量,这就是锌电解车间理论上应该产岀的锌量。
但是在实际生产中产出的锌量与通过同等电量理论上计算析出锌量之比,以百分数表示便称为电流效率,其计算式为
式中:
n为电流效率(%);。
为在时间t内阴极实际析出锌量(g);q为锌电化当量,1.22g/A-h;I为槽电流强度(A);t为电积时间(h);N为串联电解槽槽数。
电流效率是湿法炼锌工业生产重要的技术经济指标之一。
1995年的调査统计平均电流是89.2%,根据2000年世界各国炼锌厂的调查统计,波动在89%〜92%之间。
2000年各炼锌厂的平均电流效率上升到90.3%o
2.1电解液中锌、酸含量
在电解液中一定的锌离子浓度是正常进行电解沉积的基本条件之一。
若电解液的含锌过低,则硫酸浓度相对增大,使阴极附近的锌离子浓度发生贫化现象,造成阴极上析出锌的“反溶”。
此外,氢的析出电位也随溶液中锌离子浓度的降低而降低,使得氢可能在阴极上放电析岀。
电流效率n
W(膈0,)%
(a)
65
A.'2
HO406080100120140
9085807570
电流效率n/%
小2
A/m2
W(HaS口4)Z
伝)
图1在不同电流密度时电积液酸度与电流效率的关系
(a)电积液含锌150g/L;(b)电积液含锌80g/L;
图1表示在不同电流密度时电积液酸度与电流效率的关系。
由图1可看出:
在不同的电流密度下,增加电解液酸度,电流效率呈下降趋势。
在锌电解生产过程中,电解液成份由硫酸、锌盐、水及少量其它元素的盐组成,由于电解槽的体积已经固定,如果电解过程中酸度增加,必将造成槽内锌浓度降低,当锌离子浓度低于阴极表面的锌离子浓度时,由于'‘浓差极化”的原因,将导致阴极附近的锌离子向电解液方向移动,降低电流效率。
但是,值得关注的是:
并不是在电解液中锌离子浓度越高就越好,从图1中可看出:
当硫酸浓度低于6%的时候,电流效率开始呈现平稳下降趋势。
从拉乌尔定律可知,对浓溶液有:
aB=Pb/Pb*=Pb/(kXC%)式(8)
其中:
a.为溶液活度;R为常温下标准蒸汽压;k为系数;C%为溶液浓度。
因此,当锌离子浓度过大时,其活度将下降,导致电流效率下降。
2.2电解液的成分与温度
电解液的主要成分是Zn"、HzSO,、HQ和少量其它杂质元素的盐。
稳定电解液中适当的Zr?
和H2SO4浓度,对提高电流效率是有益的。
实验结果表明,在一定范围内,随着电解液中锌浓度的增加和酸浓度的下降,锌电积过程的电流效率也随之升高(见图1)。
凡是电解液中存在的能降低氢超电压和能以锌为阳极形成微电池反应的较正电性的金属杂质,都会使锌电积的电流效率降低。
如铁、镣、钻、铜、珅、锐及错的存在,大都会引起烧板、析出锌返溶等阴极沉积锌的表面状态变化,使电流效率大大降低。
但由于各个工厂的生产条件或各研究者的实验条件的差别,各种杂质对电流效率影响程度也就不尽相同,所以各厂规定的
中性净液中杂质含量也有差异。
10
20
30
10
0
-1.15
效率下降
60<>禄
根据晋森罔等人的研究,各种杂质对锌电积的电流效率等影响特征总结见图2。
12各种杂质对锌电积的影响
根据文献资料对杂质的分类法,对锌电流效率影响较大的杂质有As、Sb、Ge、Co、Ni、Se„3035404550
电解液的温度对锌电积电流效率的影响如图3所示。
图中曲线表明,在35〜40°C的范围内
温度/°C
可以得到满意的电流效率,这是目前几乎所有冶炼厂控制的电解液温度范围。
图10.13电解液的温度
对锌电积电流效率的影响
图3电解液的温度对锌电积电流效率的影响
根据锌电解槽的热平衡状态,随着电积过程的进行,槽内电解液的温度会升高,超过所控制的范围。
所以目前电锌厂大都釆用大容积电解液循环冷却制度来维持所控制电解液的温度。
2.3阴极电流密度和表面状态
Qiiz=a+blnDk式(9)
式中nH2——电流密度为仇时氢的超电位,V:
成——阴极电流密度,A-m-2;
a——常数,即阴极上通过一安培电流密度时的氢的超电位,随阴极材料、表面状态、溶液组成和温度而变;
b——2X2.3RT/F,即随电解温度而变的数据。
从塔费尔方程式方程式可看出:
增大电流密度对提高电流效率是有利的。
如图4所示,在30〜40°C范围内,电流密度从OA/m,升至600A/m2之间,电流效率呈增长趋势,大于600A/m2后,电流效率趋于稳定。
但是,在实际生产中常常发现:
增大电流密度,电流效率却下降,与塔费尔方程式方程式的结果完全相反。
这是因为:
塔菲尔方程考虑的是几个理想状态:
①电流密度升高,但是电解液温度不变;②阴极始终获得结晶致密、平整的阴极锌;③电解液含硫酸锌纯度达到电积要求;④电解阳极正常进行析氧反应;⑤阴阳极导电状况良好。
在实际生产中,首先,增大电流密度,电解过程中放热反应更加剧烈,电解过程产生的热量大量增加,导致电解液温度升高。
由于工厂中的冷却设备是按照产能比例设计的,冷却效率不可能无限提高,这时容易出现电解液温度过高,但无法在有效时间内降低的局面,造成电流效率下降。
其次,在实际电锌生产中,由于存在阴阳极极间距偏差、边缘电力线、阴阳极电场中极化作用偏差等问题,本身就较难得到结晶致密、平整的阴极锌。
当增大电流密度时,在极间距较短、电力线部分和阴阳极电场中电离条件较好的地方,就比较容易发生较强的极化作用,优先析出阴极锌,最终造成阴极实际电流密度降低,并改变阴极表面状态,降低氢的超电压,最终降低电流效率。
第三,升高电流密度,由于阴阳极极化作用增强,除了造成锌离子的电积反应更加活跃外,也会导致杂质元素的电积反应更加活跃。
特别是伴随电解液温度升高的情况后,杂质离子在电解液中的浓度会同时升高。
这是因为,温度降低,会造成Ca、Mg、Zn盐的溶解度降低,进而将部分杂质元素包裹、吸附后结晶析出。
而温度升高,则Ca、Mg、Zn盐将部分溶解后,将析出的杂质元素带入溶液中。
有实验数据表明,一杯30°C的硫酸锌溶液与一杯55°C的硫酸锌溶液,其杂质Ge离子的浓度可相差3倍以上。
第四,在阳极板镀膜过程未进行完毕期间,升高电流密度,危害极其严重。
这是因为阳极的反应过程主要有三步:
Pb-2e=Pb"式(10)
Pb2++202=Pb0z式(11)
2HMnO4+3MnSO4+2H20=5Mn02+3H2S04式(12)
当电流密度升高的时候,可能造成式(10)剧烈反应,造成阳极表面迟迟不能生成PbOz和MnOz保护膜,增大阳极析氧超电压,浪费电能,电流效率下降。
第五,由电能公式P=U2t/R可知,当阴阳极导电接触状况不好时,在阴阳极板上,电流升高则电能消耗越高,电流效率降低。
因此,随着电流密度的增加,氢的超电势增大,一般来说,能够获得结晶致密的阴极锌,但一定要有相应的电解液成分、良好的阴阳极电积条件和较低的温度条件配合。
电流密度的增加也会增大电解液的电阻电压降和温度,加剧杂质的析出。
我国各锌厂的面积电流波动在300〜600A/m2之间。
根据统计资料,世界上一些工厂的平均面积电流波动在500-530A/m2之间。
100
30~40*CZn:
80g/LH2SO4:
120g/L
90
80
70
20040060080010001200
面积电流(A/m2)
图4面积电流对电流效率的影响
2.4电解液的循环制度
传统的电解液的循环制度是指:
随着电锌过程的进行,锌在阴极析出,阴极附近的锌离子浓度不断降低,酸度不断升高,电流效率随之降低。
为了维持阴极附近一定的锌、酸浓度,需电解液不断循环,即不断往槽内供给按一定比例混合有中性硫酸锌溶液的废电解液,同时从槽内排除相应的废电解液。
加大电解液的循环速度,可以消除浓差极化现象,及时补充锌以维持一定的浓度,保持较低的电解液温度,获得较高的电流效率。
为了维持稳定的锌、酸含量,必须保持均匀的电解液流量。
供给电解槽的中性硫酸锌溶液(新液)流量可用下式计算:
式(12)
I•qF•N
1000(Pi-P2
式中:
Q为中性硫酸锌溶液流量(m'/h);I为电流强度(A);n为电流效率(%);N为串联电解槽数;q为锌电化当量,为1.22[g/(A・h)];Pi为新液含锌(g/L);&为废电解液含锌(g/L)o
生产中多采用新液与废电解液按一定体积混合,再经冷却后加进电解槽内的方法进行循环。
良好的电解液循环制度,是保证电解液温度和酸锌含量稳定控制的重要环节。
良好的循环除了依靠泵、冷却塔、厂房高差等硬件设施外,还必须保证电解槽、分配槽和管道的通畅,因此及时清理阳极泥和管道结晶是十分重要的。
随着工艺的不断进步,目前工厂中所提到的循环制度还有另外一个含义,主要是指:
流程杂质的循环富集。
由于伴生锌精矿中通常伴生Ca、Mg、Ge等对电积有害的杂质元素,而这部分有害元素的浸出和净化工序中较难除去,一部分就进入的电解液。
在常规湿法锌冶炼工艺中,电积废液一部分需返回浸岀工序做溶剂用,大部分则配一部分锌液后在电解循环使用,这就造成了杂质的循环富集,长期积累后,到一定的浓度对锌电积产生严重危害,降低电流效率。
2.5电积周期
电流效率随电流时间的增加而降低。
表1说明了电积时间与电流效率密切相关。
可见,电积周期越短,电流效率越高;但电积周期短则出装槽频繁,工人劳动量大,阴极铝板消耗增加。
若电积周期过长,析出锌表面变得粗糙,电流效率随之降低。
一般电积周期采用24h作业(人工剥锌情况下),机械化和自动化剥锌要求析出锌要达到一定的厚度,通常釆用电积周期为48〜72ho目前我国已有多家铅锌冶炼厂采用48h电积周期。
电积时间/'h
电流效率/%
析出锌表面状况
19
91.317
平整
24
90.635
呈鸡皮疙瘩状
37
80.804
呈树枝状、灰黑色
表1锌电积时间对电流效率的影响
2.6添加剂使用情况
在电解使用的添加剂主要有:
明胶、碳酸锯。
其中明胶的作用主要是通过其粘附和电阻大的作用,粘附在阴极锌上,降低阴极锌表面的极化作用,使析岀锌表面平整、光滑、致密。
碳酸锯的作用主要是加入电解液后发生:
SrC03+PbS04=SrS04I+PbCO3I式(13)
形成SrSO,与PbCOa共沉淀后,减少电解液含铅,进而降低锌片含铅。
但是,明胶添加过量后,可能造成电解液和阴极表面电阻过大,降低电流效率。
其次,明胶本身属于有机物,添加过量可能降低电流效率。
碳酸總添加过量后,可能造成阳极泥量大量增加,影响电解循环效果,降低电流效率。
其次,部分碳酸镌会附着沉积在阳极板表面,长期沉积后,增大阳极电阻,影响阳极导电效率,降低电流效率。
2.7下槽阴极的表面状态
在第3点中已经提到阴极表面不平整可降低电流效率。
在实际生产中,可导致阴极表面不平整的原因主要有三点:
阴极表面有残渣、残锌、残酸;阴极变形不平整;阴极有腐蚀点、物理创伤点;阴极粘边条胶条不整齐等。
3实际生产中电流效率下降原因分析
3.1阴极附近锌离子贫化,导致阴极出现“返溶”,降低电流效率
当电流通过电极时,由于发生电极反应,将引起电极表面离子的浓度与体相溶液浓度不同而产生浓差极化,阻碍阴极的还原反应。
当ZnSO,溶液液进入电解槽后,首先是靠分子的扩散运动进行传质,混合液进入电解槽内,首先是在槽头电解液势能变为动能,因此在槽头部分分子扩散运动较剧烈,这时电极表面的Zn2+的浓度小于或等于电解液主体相的Z"的浓度,几乎不发生浓差极化的现象。
随着电解液向电解槽底部及其它方向传播,随着动能的消耗,再加上极板带来的阻力,到达槽尾和槽底时ZnSO,分子的扩散速度逐渐减慢,这就导致了阴极板下半部分以及靠电解槽尾部的阴极板附近电极表面的Zr?
的浓度大于溶液主题相的Zn»的浓度,出现在锌离子贫化的现象,从而导致了浓差极化的发生,阻碍阴极还原析出锌。
釆用大极板电解,由于分子扩散面积增大,且板面带来的阻力也增大,溶液主题相的Zn"的浓度分布更不均与,在电解槽底部和尾部的“浓差极化”现象将更为严重。
其次,开高电流密度差“分时电流”,由于电流密度升高过程中,电极的不可逆程度增大,“浓差极化”现象得到了加强。
在电解观察生产中到周期的阴极锌片也完全可以解释这一现象:
大量的阴极锌出现下半部分变薄,锌片绵软、不致密,部分锌片下半部分出现明显“返溶”迹象;插在电解槽头端的阴极锌比尾端的致密;产量大幅下降,电流效率急剧下滑等。
此时大家往往会误解为电解槽内阳极泥过多或阴极板刷板不良好,其实不然。
表2电解槽内不同点的锌浓度抽查表
位置
电解槽尾上部
电解槽尾下部
电解槽中上部
电解槽中下部
电解槽前上部
电解槽前下部
1#槽锌浓度(g/L)
65
64
61
60
60
58.5
25#槽锌浓度(g/L)
65
65
63
62
61
59
50#槽锌浓度(g/L)
63
62
62
61
59
57
100#槽锌浓度(g/L)
64
63
61
60
60.5
59
从表2可看出,在一个电解槽中的锌离子浓度并不是完全均匀、相同的。
图5下部较薄的锌片
3.2电解槽内实际电流密度分布不均匀,导致电流效率下降
我们平常所计算的电流密度是指所有阴阳极板上的平均理论电流密度,而实际生产中分布在阴阳极板上的实际电流密度却与理论值存在差距,并且当电流越高时,差距越大。
因为在搭接式电解生产过程中,不可避免的存在系统漏电、导电头与导电板接触不良、导电头或导电板的导电性能差,阳极板上阳极泥厚薄不均匀、操作不认真导致阴阳极碰电短路等现象。
这些现象就导致了阴阳极板上的实际电流密度分布不均匀,从而造成锌片不致密,产量下降,电流效率降低。
3.2.1系统漏电对电流密度和电流效率的影响
由电能公式P=fRt可知,当系统存在漏电时,在相同的漏电线路上,电流升高则漏损越严重,这就导致了供给电解槽的实际电流下降,电流效率降低。
3.2.2导电头与导电板接触不良对电流效率的影响
在搭接式锌电解过程中,由于处于强酸性且潮湿的环境中,导电头与导电板容易被腐蚀,因此在实际生产中其表面已经不再平整,再加上操作中如果导电头与导电板上残留有阳极泥等污物,就会造成导电头与导电板接触不良。
图6生产中被污染和腐蚀的导电头和导电板
当电解槽内出现部分导电头与导电板接触不良的时候,由于接触面积减小,因此电阻增大。
首先是这块板本身的导电性能变差,大量电能消耗在导电头发热上,而分布于这块板上的实际电流密度则降低,从而造成锌片产量下降,影响电流效率。
而电解槽内其它阴阳极板上的实际
图7导电铜条被氧化的阳极梁
与导电铜梁间形成间隙,导致铅板内部的导电铜梁表面均被氧化后,影响整块阳极板的导电性
图8铅板与导电铜梁间形成间隙的阳极板
3.2.4阳极板上的阳极泥厚薄不均匀对电流密度和电流效率的影响
在电解操作过程中由于阳极错牙,极距不均等现象常常造成阳极板上的阳极泥厚薄不均匀O当出现这种情况时,就会导致分布在阳极板上的电流密度不均匀,并且阳极板下部的导电性能变差,造成锌片上锌不致密,对电流效率造成长期的影响。
特别是开高电流密度时,将使板面上电流密度的差距更大,造成锌片厚薄不均、“苞钉”增多、串酸、甚至局部“返溶”等现象,降低电流效率。
图9阳极板上厚薄不均匀的阳极泥
3.2.5碰电短路对电流密度和电流效率的影响
当出现阴阳极碰电短路时,除了短路板本身消耗大量电能外,还会让电流大量从短路板上通过,降低电解槽内其它阴阳极板上的实际电流密度,使其他阴极板附近的锌离子浓度相对增大,活度降低,影响锌片产量,降低电流效率并增大槽电压。
同时,还会破坏短路阳极板表面的性状,结构,对今后的电解带来后患。
因此,在开高电流密度差“分时电流”期间应尽量避免碰电短路,因为通过式P=fRt可知,它的危害将更加严重。
3.2.6电解周期长对电流效率的影响
在第一部分已经谈到,随着电解时间的增长,首先是阴极上的锌片增厚,阴极电阻将增大,近而消耗在克服阴极电阻上的电能也将增大,发热也会更加严重。
其次是由于阴极锌片表面不平整,导致整个阴极表面各点与阳极的极化值实际上是不同的,随着电解时间的增加,锌片表面将越来越不平整,导致分布在阴极的实际电流密度降低,降低电流效率。
第三、我厂同极极间距为75mm,阴极板厚6irm,阳极板厚8mm,电解48小时候普遍锌片厚度在3〜5mm之间,因此阴阳极板间有效距离为:
(75-8-6)/2-3=27.5mm。
随着电解时间的增长,阴极锌片越厚,对槽面操作的要求就越高,否则卜分容易发生短路。
3.3阳极反复镀膜,导致电流效率降低
在电解生产过程中,热能的主要来源有:
电流通过产生的热量和新液带入的热量。
一般的电解车间新液带入的热量可以通过冷却设备控制,而直流电通过产生的热量如果较高时,设备对其就有局限性,也就是说正常情况下,当电流低时必然槽温低,当电流高时,必然槽温高。
因此,当进行“分时电流”生产时,容易出现一天当中槽温由低到高或由高到低的转变。
此时的阳极由于受热胀冷缩的影响,其表面的保护膜就会出现不同程度的脱落,脱落部分由于露出了新鲜表面,将进行再次镀膜:
Pb-2e=Pb"式(14)
Pb+S0Z-2e=PbS0,式(15)
未被硫酸铅覆盖的阳极表面上,铅可直接氧化成PbOz,即
Pb+2H2O-4e=PbO2+4H*式(16)
随着金属自由表面的完全消失,会发生如下反应。
Pb+2H2O-2e=PbO2+4H4式(17)
待露出的新鲜阳极表面基本被PbO?
完全覆盖后,将进行正常的阳极反应:
20H「-2e=H20+1/202式(18)[1]
由式(14)〜(18)可知,正常的阳极反应发生阳极镀膜之后,①部分电能浪费在镀膜上,导致电流效率下降。
②由于阳极泥脱落和镀膜的原因,造成了电解液中铅离子浓度升高,溶液变混浊,降低锌离子的活度,导致电流效率下降,槽电压升高,片铅质量降低。
③有相关文献指岀[1],阳极形成良好的PbO,和MnOz之前,氧气在阳极析出的超电压较高,因此电流效率下降。
3.4电解液循环差,导致电流效率下降
我厂使用的电解槽出液端结构为"下进上出”式,以保障电解液在电解槽内进行良好的循环。
槽内电解液的流通模式为"后进前岀”,由于电解液从尾部进入,因此大部分的阳极泥会顺电解液流向大部分在电解槽前端富集。
表4电解槽内阳极泥厚度抽查表
阳极泥厚度(cm)
槽尾
槽中
槽头
抽查1
5
8
16
抽查2
5
10
22
抽查3
7
15
24
抽査4
5
5
10
抽查5
8
15
32
抽査6
24
32
43
抽查7
7
12
14
由表4可看岀:
电解槽内的阳极泥富集点均集中在电解槽槽头。
如果不及时清理阳极泥,可能造成出液部分流量小,严重可造成出液方式变为“上进上出”,破坏电解液循环,降低电流效率。
3.5下槽阴极板板面淸理不干净,造成电流效率较低
在式(9)中,就大多数金属的纯净表面而言,式中经验常数b具有几乎相同的数值(100〜140mv),这说明表面电场对氢析出反应的活化效应大致相同。
有时也有较高的1)值(>140mv),原因之一可能是电极表面状态发生了变化,如氧化现象的出现。
式中常数a对不同材料的电极,其值是很不相同的,表示不同的电极表面对氢析岀过程有着很不相同的催化能力。
按a值的大
小,可将常用的电极材料大致分为三类:
(3)低超电位金属,其a值在0.l~0.3V,
其中最主要的是Pt和Pa等钳族金属;
电锌生产的阴极是采用铝板。
铝是化学性质十分活泼的金属,遇空气后可迅速氧化,特别在带酸的工作环境下,还可生成硫酸铝等盐类。
因此阴极必须经过清刷后迅速下槽,以保证铝板表面尽量多的纯铝表面。
如果操作不当,将残渣、残锌、残酸板下槽,将大大降低电流效率。
在实际生产中还有一个值得重视的问题,阴极铝板粘边条有未剔除的多余胶条,如果操作检査不认真,未将多出的胶条剔除,边缘电力线作用将更强,可能造成边缘极化作用过强,影响整块板面的电流密度,影响电流效率。
4结论
(1)电流效率是湿法锌生产中的一项重要经济技术指标,对产品粗加工行业,由于产品价格与原料价格波动周期相同,因此提升电流效率对增加工厂利润具有重要意义;
(2)实际生产过程中电流效率下降的主要原因如下:
1电解液中锌、酸含量不合理。
在工厂中,由于电解槽、供液循环管道等设备体积已经确定,因此结合电解温度要求,最佳锌、酸含量也必将确定在一个很小的范围内。
如果盲目根据电流密度的高低,调整电解液中锌、酸含量,将会造成电解体积平衡和热平衡失调,最终降低电流效率。
2电解液杂质超标。
严把锌液质量关口,是提升电流效率的关键所在。
3电解液温度过高或过低,都可能造成电流效率下降。
经过实践证明,电解液温度控制在34〜39°C时,可有较高的电流效率。
4阴极电流密