麻花钻加工切削热和温度研究.docx
《麻花钻加工切削热和温度研究.docx》由会员分享,可在线阅读,更多相关《麻花钻加工切削热和温度研究.docx(46页珍藏版)》请在冰豆网上搜索。
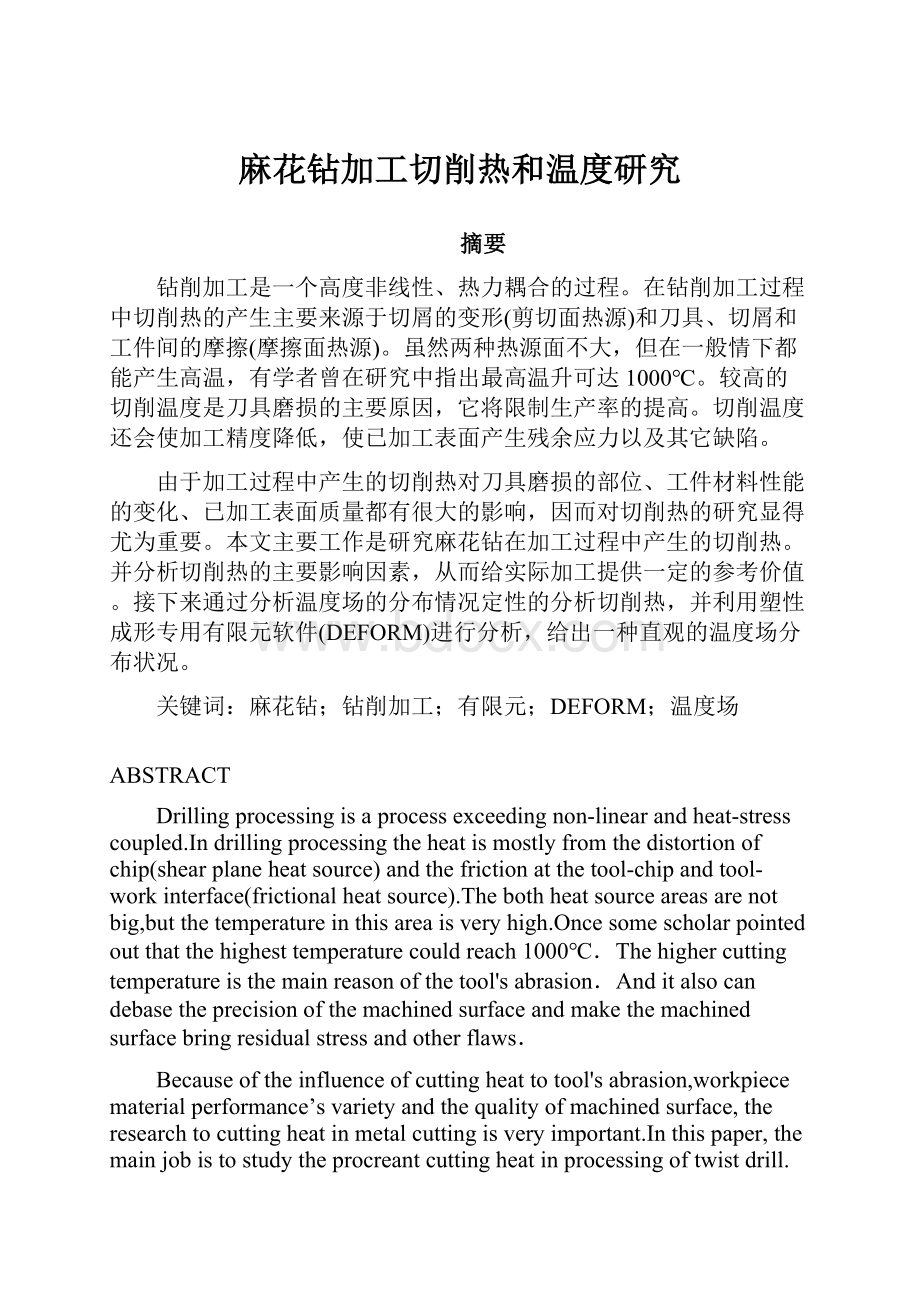
麻花钻加工切削热和温度研究
摘要
钻削加工是一个高度非线性、热力耦合的过程。
在钻削加工过程中切削热的产生主要来源于切屑的变形(剪切面热源)和刀具、切屑和工件间的摩擦(摩擦面热源)。
虽然两种热源面不大,但在一般情下都能产生高温,有学者曾在研究中指出最高温升可达1000℃。
较高的切削温度是刀具磨损的主要原因,它将限制生产率的提高。
切削温度还会使加工精度降低,使已加工表面产生残余应力以及其它缺陷。
由于加工过程中产生的切削热对刀具磨损的部位、工件材料性能的变化、已加工表面质量都有很大的影响,因而对切削热的研究显得尤为重要。
本文主要工作是研究麻花钻在加工过程中产生的切削热。
并分析切削热的主要影响因素,从而给实际加工提供一定的参考价值。
接下来通过分析温度场的分布情况定性的分析切削热,并利用塑性成形专用有限元软件(DEFORM)进行分析,给出一种直观的温度场分布状况。
关键词:
麻花钻;钻削加工;有限元;DEFORM;温度场
ABSTRACT
Drillingprocessingisaprocessexceedingnon-linearandheat-stresscoupled.Indrillingprocessingtheheatismostlyfromthedistortionofchip(shearplaneheatsource)andthefrictionatthetool-chipandtool-workinterface(frictionalheatsource).Thebothheatsourceareasarenotbig,butthetemperatureinthisareaisveryhigh.Oncesomescholarpointedoutthatthehighesttemperaturecouldreach1000℃.Thehighercuttingtemperatureisthemainreasonofthetool'sabrasion.Anditalsocandebasetheprecisionofthemachinedsurfaceandmakethemachinedsurfacebringresidualstressandotherflaws.
Becauseoftheinfluenceofcuttingheattotool'sabrasion,workpiecematerialperformance’svarietyandthequalityofmachinedsurface,theresearchtocuttingheatinmetalcuttingisveryimportant.Inthispaper,themainjobistostudytheprocreantcuttingheatinprocessingoftwistdrill.Andthemainfactorsofhot-cuttingareanalyzed,whichprovidessomereferencevaluefortheactualmachining.Thenthroughtheanalysisofthetemperaturefielddistributiontoanalysequalitativelythecuttingheat.Andplasticformingdedicatedfiniteelementsoftware(DEFORM)isusedforanalysis,anintuitivetemperaturefielddistributionisgiven.
Keyword:
twistdrill;drillingprocess;finiteelement;DEFORM;temperaturefield
图表目录
1绪论
钻削是最广泛最复杂的加工过程之一,因为它占整个加工的很大一部分。
随着钻削精度和生产率要求的提高,有必要更好的研究钻削过程。
孔加工是机械加工中的重要加工工艺之一,相关资料表明:
孔加工量占机械加工总量的30%左右。
随着机械科学的发展,高精度孔、深孔、难加工材料孔也变得越来越普遍,对孔的加工要求也越来越高,因此深入开展钻削机理、钻削方法与工艺以及对钻削过程中温度场的研究显得越来越重要。
由于传统的试验方法具有耗时、成本高、局限性强等缺点,其使用范围受到限制。
而作为试验方法的有效补充,有限元仿真技术以其高效便捷的特点越来越受到专家学者们的青睐。
自上世纪七十年代开始,国内外许多学者开展了钻削加工的有限元建模与仿真的研究,并在麻花钻的建模、有限元方法的应用方面取得了大量的成果。
1.1钻削切削热的提出及其影响
孔加工是在封闭或半封闭的状况下进行,因此不能直接观察刀具的切削情况。
切削热不易传散,而且排屑困难、工艺系统刚性差,切削效果不理想。
另外,在孔加工中产生的切削热远大于普通车削加工,并且又不能采用普通车削加工中通过提高切削速度而加快散热的方法(这会造成无法排屑及刀具急剧磨损)。
切削热是切削过程中的重要物理现象之一。
切削时所消耗的能量,除了1%~2%用以形成新表面和以晶格扭曲等形式形成潜藏能以外,有98%-99%转换为热能,因此可以近似地认为切削时所消耗的能量全部转换为热。
由于切削热而产生的温升,会对切削性能产生很大的的影响。
(1)切削机理和切削力的变化:
如果因切削热而使前刀面的温度上升,那么,就在前刀面处带来了减少摩擦应力、减小摩擦角、增大剪切角、减小切削力等一连串的结果。
同时,剪切角的增大也改变了切屑形态,使切屑向增加连续性的方向变动,即从崩碎形到挤裂形再到带状变动。
(2)刀具磨损的增大:
如刀具产生温升,通常刀具的强度(硬度)就降低了,刀具容易磨损。
(3)因热应力而发生崩刃:
由于刀具内部的温度梯度而产生的热应力致使刀具崩刃。
(4)因工件与刀具的热膨胀而降低加工尺寸精度:
因切屑加热了机床的某一部分而引起的机床热变形,也是精度降低的原因。
(5)产生加工变质层与参与应力:
由于通过刃口附近时的加热而使已加工表面层急剧加热;同时,也受到剧烈的塑性变形。
所以,加工表面层与母材具有不同的结晶组织,通常形成很硬的加工变质层。
同时,加工表面层也往往产生残余应力,使薄的工件产生变形。
(6)使切屑折断困难:
切屑温度上升,切屑的延展性就增加,使切屑不易折断。
综上所述,切削热在加工过程中,无论是对刀具耐用度,还是对工件加工精度和表面质量都有很大的影响,所以对切削热和切削温度的研究显得尤为重要。
1.2钻削切削温度的国内外发展现状
1.2.1国外研究现状
切削温度的研究可追溯到1907年泰勒的实验研究。
泰勒的实验结果表明提高切削速度会降低刀具寿命。
1931年德国学CarlJ.Salomon开创了高速切削理论研究先河,提出了切削温度与速度的关系曲线;Trigger和Chao首次对切削温度进行解析估算,通过研究金属切削过程热量产生机理计算出刀.屑接触区的平均温度;Ling和Saibeld得到金属切削刀具寿命和切削温度的关系,指出切削温度的重要性及影响;Usuiet和Tlustu等人先用能量法算出如切屑变形、切削力等大小,然后用有限元分法预报连续切削稳态温度分布,他们预报的温度比切削刃和切削终止点附近的温度低,他们将刀具的月牙洼磨损和刀具预报温度、应力联系起来。
M.V.Ramesh,K.N.Seetharamu用有限元法对各同性材料的热传导进行分析,建立了稳定的二维和三维有限元模型。
二维有限元分析中,在不同的切削速度下,对前刀面温度分布的有限元分析结果与Tay等人的实验结果进行比较,发现二者较好的吻合,验证了二维有限元模型的正确性。
随后得出不同导热系数对前刀面温度和切屑温度的影响曲线。
重点是建立三维有限元仿真模型,并将二维分析结果与三维结果进行比较,发现三维分析的温度值低一些,更接近实验值,切削深度对前刀面温度影响不大,而切削速度和进给良对切削温度影响较大。
A.Abdel.Hamid,A.S.Wifi等人用有限元法对断续切削过程进行热.机械耦合分析,建立三维切削模型。
在所建模型中,剪切热源和摩擦热源看成是均匀分布的平面热源,切削比是恒定的,不考虑切屑卷曲。
根据切削过程中损耗的能量计算剪切面温度和摩擦热。
由稳态切削过程平均温度公式求得剪切面的平均温度。
边界条件是前刀面和后刀面为对流边界,刀柄的温度为温室,并且施加全约束。
得出不同切削条件下前刀面温度分布曲线,发现最高温度出现在距刀尖不远处。
同时得出切削速度和切削宽度对刀具最高温度影响曲线,发现切削温度与切削速度的对数成线性关系,切削宽度与切削温度不成线性关系。
S.Led,YC.Shin等人用有限元法对正交切削过程进行仿真,建立热.机械耦合模型,建立能够反映切削实质的本构方程,考察了工件材料在变形时的应变、应变率和切削温度之间的关系。
研究结果表明刀尖的应变最大,剪切区各处的应变值差别很小。
应变率分布图表明最大应变率出现在刀尖附件处,离刀尖越远,应变率越小。
应力分布受应变、应变率和温度的影响,最大应力出现在剪切区中部。
最高切削温度在刀/屑接触面的切屑与刀具分离点附近。
1.2.2国内研究现状
我国于90年代初开始在国家基金委、国家计委和航空工业总公司的支持下对高速干式切削加工技术的各关键领域进行了卓有成效的研究。
在高速干式切削温度方面的研究也取得了一定的成果,主要有:
西北工业大学的杨巧风,张明贤等人对铝合金高速铣削温度进行了实验研究,实验采用红外热像法对铝合金高速铣削的工件表面温度进行了研究,得出的结论与CarlJ.Salomon的设想符合,他们还通过红外热像法对钛合金TC4铣削表面温度场分布进行
了研究。
重庆大学的周忆、梁锡昌通过对超高速铣削中切削区的动态热力学行为的计算分析,推导了切削区温度场的分布模型,模拟超高速铣削区的温度场,得出了超高速铣削加工的机理,并通过切屑材料的金相组织分析验证了机理模型。
山东大学的孟辉、赵军等人建立了正交切削的热传导分析模型,采用有限元法对高速切削条件下的温度场进行了数值模拟,得到切削速度对切削温度的影响规律,为研究刀具磨损机理、优化切削参数提供了有益的参考数据。
哈尔滨理工大学的刘献礼等人研究了硬态干式切削条件下PCBN刀具的切削温度场分布及其切削性能,得出切削与硬态切削的临界硬度和最佳切削用量对已加工表面完整性的影响规律及最佳的切削用量组合这一重要结论;还根据聚晶立方氮化硼(PCBN)刀具应用技术研究中,通过被磨损刀具的微观形貌电镜照片,分析干式切削条件下刀具磨损的原因,提出了减少和避免磨损、提高刀具寿命的方法等。
1.3钻削切削温度有限元模拟研究存在的主要问题
目前国内外关于机械加工中钻削切削温度的有限元模拟研究已经取得了一定的进展,但是通过大量的参考文献可以看出,钻削切削温度的有限元模拟研究还存在很多问题,主要体现在以下几个方面:
(1)由于很难确定各种切削条件下可靠的材料流动应力数值,影响了有限元模拟的准确性。
目前多数学者通过反求直角车削或铣削实验测量的部分数据来确定材料的流动应力数值,这种方法有很大的局限性;
(2)对钻削加工进行有限元分析时,其中最困难的是缺乏一个在大的塑性流动情况下可靠的材料失效标准。
例如由于所用的切屑分离准则不是特别准确,GUO的模型并不能描述某些没有盖帽毛刺材料的毛刺形成过程;
(3)由于钻削模拟中问题的复杂性,多数学者在研究中并没有考虑切屑的形成。
当前,有限元模拟切屑生成、卷曲及折断遇到很大的困难;
(4)应用有限元分析钻削加工,其研究的范围还比较窄,多数研究只是考虑理想工况下的钻削过程,如局限于未涂层刀具,未考虑各种复杂切削工况等。
(5)钻孔切削温度的研究还没有形成一套完整的理论,没有建立具体的钻削温度模型和推导钻孔切削温度的理论计算公式。
(6)由于钻孔加工的复杂性,切削温度受切削因素的影响又非常敏感,在实验方面还没有成熟、准确的切削温度测量方案和测试技术。
(7)钻孔的切削机理研究还只是处于初步的探讨阶段。
1.4本课题的研究意义、目标及主要工作
1.4.1本课题研究的意义及目标
切削热和切削温度是金属切削过程中的重要物理现象之一。
金属切削时所做的功大部分转化为热能,除切削时所产生的热能外,虽还有新生面的表面能,加工表面和切屑中的残留应变能等,但这部分的能量只不过占总能量的1%~3%。
在转化成的总热能中,除去极少量的以辐射形式发散以外,其余均用于加热切屑、工件以及刀具。
显然金属切削中的许多经济和技术问题大都直接或间接地由切削热所引起,它影响刀具的磨损及耐用度,影响工件的加工精度和已加工表面的质量。
同时在很大程度上决定金属切削的成本。
因此,了解刀具切削刃附近区域的温度分布、热流密度及其影响因素,无论对于进行金属切削加工机理的研究、刀具磨损机理的磨损规律的探讨,还是刀具的设计与制造、切削加工参数的选择以及已加工表面质量的控制等都是相当重要的。
但是要精确地测量和计算切削区的温度分布,在技术上还存在一定的困难。
本课题将用有限元分析软件(DEFORM)对钻削加工建立模型并对钻削加工温度场进行模拟仿真,得到切削过程中温度场变化情况。
在指定的条件下,为减小切削热选择合适的切削参数提出依据。
1.4.2本文的主要研究内容
钻削是一种应用广泛的精密加工方法。
在对钻削加工的研究中,由于对加工机理的认识有限,因此对钻削加工过程的实际调整多数是靠试凑法(即凭操作者所积累的大量经验知识)来进行,特别是有关钻削温度分析模型,多是通过单因素获得的。
随着计算机性能的日益提高,仿真技术在工业中的应用越来越广泛,给钻削理论的研究带来了新的思路,使我们有可能克服传统研究方法的局限性,深入研究钻削过程中钻削温度的变化,建立系统的钻削温度场理论模型。
从切削机理分析,钻削加工属于高速切削加工范畴,按目前国内外专家对高速切削机理的研究通常认为需要解决切削时的温度升高。
通常认为在切削加工过程中,刀具的磨损与机械摩擦、刀具与工件材料的粘结、合金元素的相互扩散以及金相组织的变化有关,同时在金属切削时工件受刀具的切削和推挤发生弹性变形,使切屑分离,产生大量热量。
因此控制切削时的温度升高,可以防止刀具的快速磨损。
针对上面的问题——解决切削时的温度升高问题,本文采取温度模拟的方式来分析钻削加工中产生的切削热,其主要研究内容如下:
1)了解钻削加工过程中钻削温度模拟的研究现状及存在问题;
2)有限元分析在钻削加工温度场的理论分析中的应用;
3)建立钻削温度场的数学模型;
4)采用仿真模型分析不同加工参数对钻削弧区温度的影响,从而发现钻削温度场的变化规律。
2钻削加工过程中切削温度的理论分析
钻削技术的发展和应用来源于钻削切削理论的研究和突破。
虽然钻削加工己经在界上很大范围内使用,并取得了巨大的经济技术效益。
但是钻削切削理论仍然处于研究之中,还远远没有成熟。
对切削温度进行理论分析,必将推动钻削切削机理的研究和完善,促进钻削技术的进一步发展和应用。
因此,对于切削温度机理的研究,无论于分析切削过程,还是优化切削参数、研究刀具磨损机理等方面都是极为重要的。
2.1切削热的产生与传出
被切削的金属在刀具的作用下,发生弹性和塑性变形而耗功,这是切削热的一个重要来源。
此外,切屑与前刀面、工件与后刀面之间的摩擦也要耗功,也产生出大量的热量。
因此,切削时共有三个发热区域,即剪切面、切屑与前刀面接触区、后刀面与过渡表面接触区,如图2.1所示。
所以,切削热的来源就是切屑变形功和前、后刀面的摩擦功。
图2-1钻削热的产生与传导
切削热主要通过切屑、工件、刀具传出,周围介质带走的热量很小(无切削液时约占1%)。
不同的加工方法切削热传导的比例不同:
车削加工,50%~86%由切屑带走,40%~10%由刀具传导出去,3%~9%传入工件,1%左右的热量辐射进入空气;钻削加工,28%切削热由切屑带走,14.5%传入刀具,52.5%传入工件,55%传入周围介质。
2.2钻削加工热模型建立
2.2.1基本假定
考虑钻削加工过程的复杂性,为简化计算及突出主要问题,在钻削加工切削热模型建模前作如下假定:
(1)工件和钻头材料的温度特性及密度是均匀的,传热系数不随温度的变化而变化;
(2)将变形区的热源看成是平面热源;
(3)在金属的切削过程中,塑性变形和摩擦功全部都转化为热量,忽略了用于改变金属晶格约l%~2%的能量损失。
2.2.2切削热模型建立
钻头主切削刃的几何参数在钻削过程中对切削力、排屑和切削刃强度等均起着相当重要的作用。
由切削理论可知,刀具的法向前角直接影响刀具的切削力,而刃倾角则影响切屑的流出方向。
钻削过程的轴向力、切向力来自主切削刃、副刃和横刃三部分。
由大量理论和实验研究得知,在轴向力总和中,来自两个主切削刃的共占40%,来自横刃的占57%,其余来自副刃;在扭矩的总和中,来自两个主切削刃的共占60%,来自横刃的占30%,其余来自副刃。
由于钻头的横刃部分的切削过程属于挤压塑性成型范畴,虽然人们对此进行了大量的研究,但由于其机理比较复杂,尚不能合理准确地预测它产生的切削力。
图2-2麻花钻切削过程示意图
2.3切削热的分析与计算
在钻削加工时,阿·奥·施密特(A.0.Schmidt)等人用热量计进行直接测定在钻削中产生的热量实验。
而且,把所测得的热量与作用于钻头的扭矩和轴向力所计算出来的动力消耗相比,得知97%~99%的动力消耗转换为热。
因此可以近似的认为全部切削功都转化为热。
一般被切削的金属在刀具的作用下,发生弹性和塑性变形而耗功,这是切削热的一个重要来源。
此外,切屑与前刀面、工件与后刀面之间的摩擦也要耗功,也产生大量的热量。
因此,切削热来自于三个方面:
切削层金属的剪切变形热、切屑底层金属的摩擦挤压变形热和己加工表面上的摩擦挤压变形热。
因此,可以将切削区的温度场划分出三部分:
剪切区(即第一变形区)温度场、刀具与切屑接触区(即第二变形区)温度场和刀具与工件接触区(即第三变形区)温度场。
剪切区(第一变形区)内:
被切金属层在切削力的作用下,受到挤压、摩擦和剪切变形,产生大量的切削热,形成剪切区温度场。
剪切变形的程度与工件材料的应力、应变特性有关。
当材料达到屈服极限时,切削层金属从工件基体材料上分离出来。
沿剪切面滑移,形成切屑,从刀具前刀面流出。
其中,大部分切削热由切屑带走,小部分切削热传入工件和刀具。
向周围介质直接传出的热量,在干切削(不用切削液时),所占比例在1%以下,故在分析和计算时可以忽略不计。
刀具与切屑接触区(第二变形区)。
当切屑沿刀具前刀面流出时,受到前刀面的挤压和摩擦,进一步加剧了变形,由摩擦而产生的热量使切屑与刀具接触面的温度升高,形成刀具与切屑接触区温度场。
当切削刃沿着工件材料高速切削时,由于刀具钝圆半径的作用和工件材料的反弹,在刀具的后刀面与工件接触部分产生第三变形区,后刀面与工件已加工表面摩擦,产生摩擦热。
对正常磨损的刀具,后刀面的摩擦较小,所以在计算切削功时,可将后刀面摩擦所产生的热量忽略不计。
如上所述,切削功主要消耗于两个区域:
(1)剪切区以及向以加工表面层的扩散;
(2)刀具前刀面以及与前刀面相接触的切屑内部。
综上所述,由切削功所转换的切削热可按如下公式进行计算:
(2.1)
(2.2)
(2.3)
其中,
为主切削力,v是切削速度,n是钻头的转速,d是钻头的直径,M为钻头的扭转力矩。
代入钻头的各个切削参数就可以计算得到钻头工作时产生的切削热。
同时根据热力学平衡原理,产生的热量和散出的热量相等,即
(2.4)
式中
——工件材料的弹、塑性变形所产生的热量;
——切屑与前面、加工面和后面摩擦所产生的热量;
——切屑带走的热量;
——刀具传散的热量;
——工件传散的热量;
——周围介质如空气等带走的热量;
2.4切削热对切削过程的影响
因切削热而产生的温升,由于切削条件的不同,而使温度在很广的范围内变化。
例如,在通常条件下切削钢时,在刀具前刀面上达到600℃以上,即使在剪切区也达到400~500℃。
由于这种切削热而产生的温升,在下述各点上对切削性能有重大的影响。
(1)切削机理和切削力的变化:
如果因切削热而使前刀面的温度上升,那么,就在前刀面处带来了减少摩擦应力、减小摩擦角、增大剪切角、减小切削力等一连串的结果。
同时,剪切角的增大也改变了切屑形态,使切屑向增加连续性的方向变动,即从崩碎形-挤裂形-带状变动。
可以说这些都是所希望的影响。
(2)刀具磨损的增大:
如刀具产生温升,通常刀具的强度(硬度)就降低了,刀具容易磨损。
(3)因热应力而发生崩刃:
由于刀具内部的温度梯度而产生的热应力致使刀具崩刃。
如铣削那样的重复切削,由于重复地周期性地改变热应力而产生热疲劳。
因工件与刀具的热膨胀而降低加工尺寸精度:
因切屑加热了机床的某一部分而引起的机床热变形,也是精度降低的原因。
(4)产生加工变质层与参与应力:
由于刀具刃口附近的温升导致已加工表面层急剧加热并产生剧烈的塑性变形。
所以,加工表面层与母材具有不同的结晶组织,通常形成很硬的加工变质层。
同时,加工表面层也往往产生残余应力,使薄的工件产生变形。
(5)使切屑折断困难:
切屑温度一上升,切屑的延展性就增加,使切屑不易折断。
这是高温切削存在的问题之一。
随着切削而产生的温度上升,它有利弊两个方面的影响。
所以,必须了解
温度上升是由于什么原因造成的,它又怎样来确定的,这对提高加工技术是非常
重要的。
2.5切削温度场
2.5.1切削温度场的定义
金属切削时的温度场是指刀具表面的温度分布状况和被加工材料内部的温度分布状况,即刀具、被切削材料、切屑的温度分布情况。
切削温度场分成三个部分:
剪切区温度及其分布;刀具与切屑接触区的温度及其分布;刀具后刀面与被切削材料的接触区的温度及其分布。
2.5.2切削温度场的研究方法
温度场求解方法有解析法(分离变量法、积分变换法、拉普拉斯变换法),数值法(有限差分法、有限元法、蒙特卡洛法),热源法等。
解析法是根据能量守恒定律和传热学的基础方程式,满足存在于现实切削中的各种条件来解方程式,就可以得到各点的温度。
其优点是可以得到表示温度分布的函数关系,而且可以分析影响因素。
但需要设定一些条件:
几何条件、传热条件、密度、比热和导热系数、在剪切区和二次滑移区中材料速度的分布、由于剪切变形和摩擦产生的热量的分布等。
由于这些条件的变化都很复杂,在求解考虑材料的加工硬化以及几何非线性等复杂切削模型时,解析法往往导致不可解。
而数值法对于处理非线性、复杂几何形状、复杂边界条件等问题或者处理藕合偏微分方程组都是有用的。
金属切削过程中,其导热问题的主要特点是热源有一定的形态和尺寸,有一定的动态状况,有一定的热量输出,但边界条件则多是未知值。
因此,很多加工过程中的导热问题用传统的解析法或数值法求解有很大困难,而热源法却有其独到之处,特别是对导热范围无限大,热源又集中于极小的微元容积内,热源可得出最简单形式的解答,计算结果和实际结果很接近。
热源法是利用导热微分方程的解,先求得简单热源(点热源)简单边界条(无限大物体)的解答,经过迭加计算,然后再推导到复杂的场合。
因此首先要建立导热微分方程,经过傅式变换,求得瞬时点热源在无限大物体内发出一定热量后的任何时刻的温度场的解,推导出无限长移动线热源在无限大物体内的温度场的解,对剪切热源