印刷包装工艺 重点.docx
《印刷包装工艺 重点.docx》由会员分享,可在线阅读,更多相关《印刷包装工艺 重点.docx(31页珍藏版)》请在冰豆网上搜索。
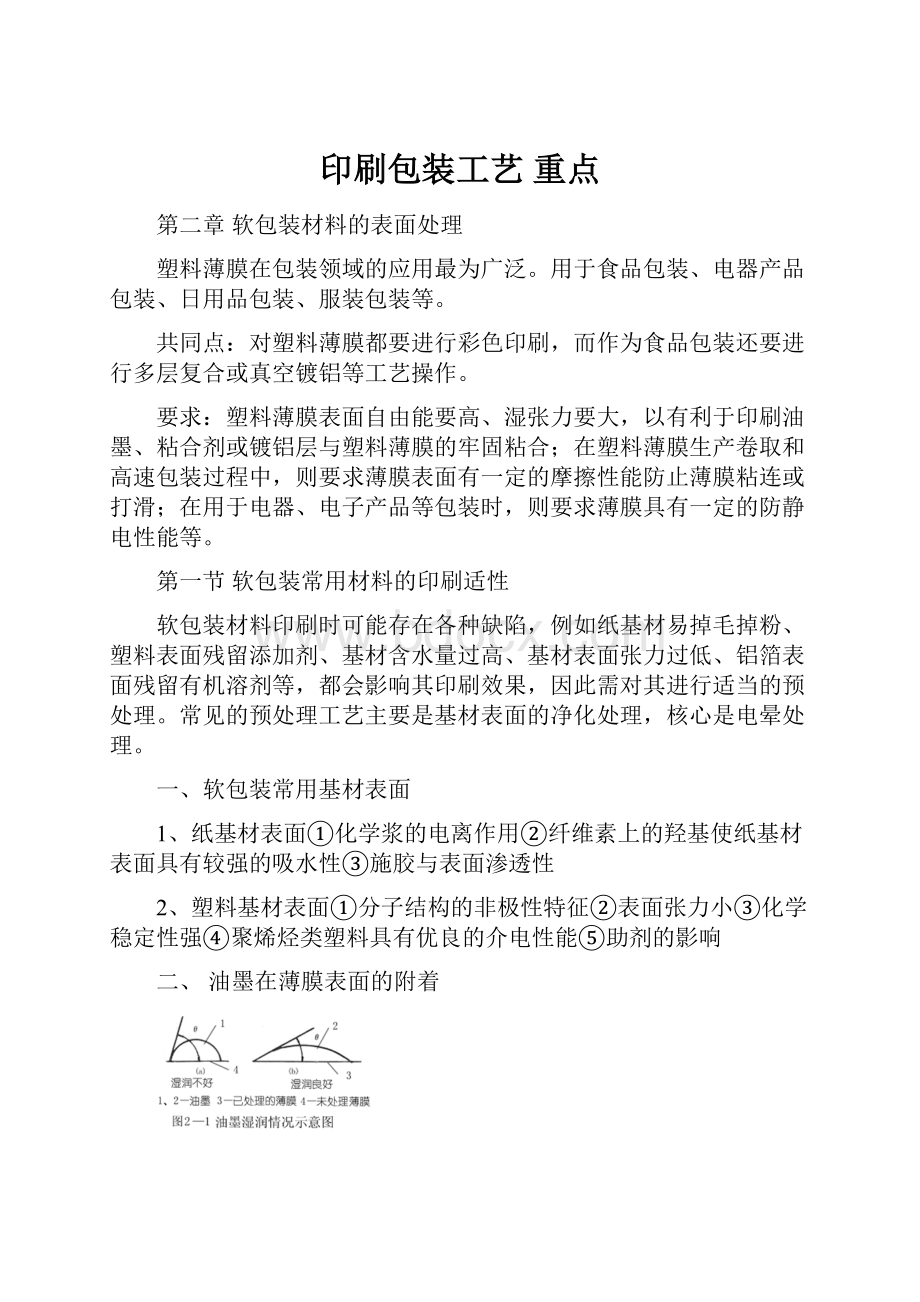
印刷包装工艺重点
第二章软包装材料的表面处理
塑料薄膜在包装领域的应用最为广泛。
用于食品包装、电器产品包装、日用品包装、服装包装等。
共同点:
对塑料薄膜都要进行彩色印刷,而作为食品包装还要进行多层复合或真空镀铝等工艺操作。
要求:
塑料薄膜表面自由能要高、湿张力要大,以有利于印刷油墨、粘合剂或镀铝层与塑料薄膜的牢固粘合;在塑料薄膜生产卷取和高速包装过程中,则要求薄膜表面有一定的摩擦性能防止薄膜粘连或打滑;在用于电器、电子产品等包装时,则要求薄膜具有一定的防静电性能等。
第一节软包装常用材料的印刷适性
软包装材料印刷时可能存在各种缺陷,例如纸基材易掉毛掉粉、塑料表面残留添加剂、基材含水量过高、基材表面张力过低、铝箔表面残留有机溶剂等,都会影响其印刷效果,因此需对其进行适当的预处理。
常见的预处理工艺主要是基材表面的净化处理,核心是电晕处理。
一、软包装常用基材表面
1、纸基材表面①化学浆的电离作用②纤维素上的羟基使纸基材表面具有较强的吸水性③施胶与表面渗透性
2、塑料基材表面①分子结构的非极性特征②表面张力小③化学稳定性强④聚烯烃类塑料具有优良的介电性能⑤助剂的影响
二、油墨在薄膜表面的附着
油墨要在薄膜表面附着(润湿),油墨的表面张力必须小于薄膜的表面张力。
如图2–1所示。
同一种油墨在表面经过处理和未经过处理的同一种薄膜材料上的润湿情况。
图中θ为接触角。
三、油墨与薄膜的适应性
油墨的附着牢固度,取决于油墨润湿薄膜表面的程度,即油墨本身的表面张力和塑料薄膜材料的表面张力。
①不同油墨对薄膜的表面张力有不同的要求,通常薄膜材料的表面张力要大于油墨的表面张力10mN∕m,这样才能保证油墨在薄膜表面牢固吸附。
②对薄膜类材料,印刷时要注意油墨与薄膜特性相匹配。
③为保证印刷效果,印刷一种薄膜最好使用同一厂家同一批号的油墨,不要同时混合使用其它厂家生产的同类油墨。
四、软包装常用材料的印刷适性
1.常用塑料薄膜的印刷特性:
(1)塑料薄膜对油墨的粘附能力很差,印刷前需对塑料薄膜进行表面活化处理。
(2)薄膜在强度允许范围内,印刷时伸长率随张力的加大而升高,给彩色印刷套印的准确性带来困难。
(3)表面光滑,无毛细孔存在,油墨层不易固着、不易干燥,使图案及文字不完整,造成缺陷。
(4)表面油层渗出。
掺入添加剂制成的薄膜,在印刷过程中添加剂部分极易渗出,在薄膜表面形成一层油质层,油墨层、涂料或其它黏合剂不易在这类薄膜表面牢固地粘结。
2.玻璃纸的印刷特性:
(1)透明度高、光泽度强,印刷图文后色泽格外鲜艳,这是塑料薄膜所不能达到的;
(2)印刷适性好,印刷前不需经过任何处理;
(3)玻璃纸还具有抗静电处理性能,不易吸附灰尘,避免了图文粘尘等印刷故障的发生;
(4)防潮性差,薄膜受温、湿度的影响易变形,导致印刷时图文不易套准。
3.铝箔的印刷特性:
(1)质轻,具有金属光泽,避光性好,金属光泽和反射能力可以提高印刷色彩的亮度。
(2)形状稳定性好,不受湿度变化的影响。
易于加工,可对铝箔进行印刷、压花、表面涂布、上胶上漆等;
(3)不能受力,无封缄性,有针孔和易起皱等现象,一般情况下不单独使用,通常与纸、塑料薄膜加工成复合材料。
注意:
铝箔在食品和医药等包装领域中应用很广,铝箔与塑料薄膜复合,有效地利用了耐高温蒸煮和完全遮光的特性,制成蒸煮袋,可包装烹调过的食品,多层复合薄膜也用于饼干、点心、饮料等小食品包装。
4.真空镀铝薄膜的印刷特性:
(1)作用是代替铝箔复合,使软塑包装同样具有银白色的美丽光泽,提高软包装膜袋的阻隔性、遮光性,降低成本。
(2)真空镀铝的被镀基材膜是熔点比较高的聚丙烯膜,包括CPP、IPP、BOPP。
PET膜、NY膜,纸在采用预处理或调湿处理后也可直接真空镀铝。
(3)印刷方法有两种,①在薄膜的面膜上进行反向印刷(里印),然后真空镀铝,再同底膜复合。
②在面膜上反向印刷,再同已真空镀铝的底膜进行干式复合。
后者的底膜必须是耐热性较好且可以热封的CPP或IPP。
注意:
(1)里印时不必使用里印油墨,只需是耐热性优良的油墨即可。
如果真空镀铝后印品发暗,是因为油墨的耐热性差。
在印刷面上进行真空镀铝,由于油墨中的粘结性树脂是一个良好的底涂层,镀铝的牢度比较好,尤其是印刷满版实地时,镀铝层的牢度更好。
(2)真空镀铝与铝箔相比,节约了用铝量,(仅为后者的1/100~1/200),但具有金属的光泽性及隔绝性。
(3)真空镀铝层的厚度比较薄(0.4~0.6微米),不能用于代替需要高阻隔性的铝箔复合膜,例如抽真空包装和高温蒸煮袋。
5.复合薄膜的印刷特性:
(1)复合薄膜具有防潮、防气、防光、耐油、耐高温、热封性好等优良性能,同时还具有良好的印刷适性和装饰艺术效果,性能和要求是单一薄膜难以达到的。
(2)复合种类很多,常见的有玻璃纸与塑膜复合,塑膜与塑膜复合,铝箔与塑膜复合,铝箔、玻璃纸与塑膜复合,各种纸张及其印刷品与各种塑膜复合等,复合层数一般为2~5层不等。
(3)各种复合薄膜的基本结构是以PT、BOPP、NY、PET等非热塑性或高熔点薄膜为外层,以PP、PE为内层进行综合应用。
第二节软包装材料的表面处理
一、表面处理的必要性
(1)最常用的聚烯烃薄膜材料(如PE、PP、改性聚烯烃等)属非极性的聚合物,表面张力仅29~31mN∕m。
从理论上来说,若某种物体的表面张力低于33mN∕m,就几乎无法附着于目前已知的任何一种黏合剂,故而要使油墨在聚烯烃表面获得一定的印刷牢度,就必须提高其表面张力,根据工艺要求,应达到38mN∕m以上才行。
(2)塑料薄膜表面处理的方法有:
电晕处理法、化学处理法、机械打毛法、涂层法等。
(2)国内外普遍采用的塑膜有效表面处理方法是电晕处理法,经电晕处理使塑膜表面发生一系列的物理、化学变化,大大提高薄膜的表面张力,改善油墨、黏合剂在薄膜表面的润湿性,增加塑膜表面与油墨及黏合剂的结合力。
二、表面处理的方法
1.电晕放电处理装置
电晕放电处理装置是把电解质材料包覆在接触被处理薄膜的辊筒上,使用棒状电极进行放电处理的一种方法。
1)辊筒上包覆电解质,避免了电晕放电变成电弧放电。
2)电解质材料必须使用具有耐高电压和在臭氧下不至于很快老化的材料,而且具有介电常数大、且介电损耗小等性质,目的是避免由于电晕放电的集中所造成的处理不均匀问题。
2.电晕放电处理的作用
①化学作用:
电晕放电处理时,空气中的O2变成O3,O3又分解O2和新生态的氧原子,新生态的氧原子有极强氧化性,能对软包装基材表面进行氧化,生成各种含氧集团,如—CHO、—NH2、—ON2等,这些集团极大地提高了薄膜表面极性和表面张力,对油墨具有很大的亲和力,且提高了薄膜表面的交联度,使得软包装塑料基材表面在几十纳米范围内发生了氧化,表面性能发生变化。
②物理作用:
电晕放电处理能改变软包装基材薄膜的表面微观结构,影响印刷性能。
电晕放电会使薄膜表面生成微小的斑点,使薄膜表面粗化,提高机械黏合作用。
注意:
(1)电晕处理过度:
不利于塑料基材表面的黏附与润湿,原因是过热而烧毁;
(2)表面微观结构随处理时间和温度的变化而变化:
长时间处理,黏合强度下降。
3.影响电晕处理效果的因素
(1)设备选择处理装置有三种类型:
固态式、火花间隙式、电子管式。
电压8~60kV,频率10~50kHz。
固态式:
质量稳定、能耗低、效率高,是电晕处理的首选装置。
根据被加工的材料、环境条件确定适当的电频率或处理功率。
如对各种塑膜基材,当幅宽400mm,处理速度25m/min时,其施加功率见表2-1。
对于纸张来讲,其含水率远大于塑膜,且同时还需进行尘埃物质清除、晶化冲击、油墨干燥等,其功率一般控制在1000~1500W范围内。
(2)电极的间隙一般对塑料薄膜类,间隙控制在1~2mm为宜,单张平板纸间隙应在5~12mm范围内调整。
改变电极间隙会产生两种互为相反的作用,一方面间距增大,电晕辉光区宽度扩大,薄膜在辉光区内停留时间变长;另一方面,间隙变大时,能量分布到较大空气体积上,作用于薄膜表面的有效能量比例降低。
注意:
对于同种基材,在固定电晕放电处理时间、电极电压时,调节不同的电极间隙,可得到不同净化程度、不同表面张力的基材。
(3)电极电压:
表面张力值随电压升高而升高。
(4)输出电流对处理效果的影响当输出电流过低时,电晕处理效果差,当输出电流达到某临界值后,电晕处理的效果反而增加缓慢,即对某种塑料薄膜进行电晕处理时有一最佳输出电流。
(5)处理温度的影响当处理温度高时,化学反应速度加快,反应程度也大,处理效果好。
但温度不宜太高,否则会形成新的薄弱界面层,反而使强度下降。
注意:
不同的材料,处理温度不同。
(6)薄膜厚度的影响薄膜的厚度影响处理强度,较厚的膜需增加处理能量,但在处理较薄的膜时由于牵引速度快,摩擦也较剧烈,膜温下降得少些,相对处理电流也可小些。
(7)湿度的影响湿度大时处理效果变差,这是由于空气中的水分子吸收了部分由电晕而产生的离子。
生产车间应增加排风量,把电极附近的湿气及时排出。
(8)薄膜本身的影响①薄膜种类的影响:
在相同的处理条件下,不同薄膜的处理效果也不相同,如聚丙烯薄膜比聚乙烯薄膜就需要更高的能量才能达到相同的处理效果。
②薄膜密度的影响:
密度过高,电晕处理效果变差。
(9)机器速度的影响薄膜表面的电晕处理时间越长,处理强度增加,效果愈好。
要处理时间长,机器的速度就要慢一点,但若机器的速度太慢,处理时间太长,会使材料老化,产生异味,发生粘边,光泽变差。
三、电晕处理的效果
(1)聚烯烃表面由非极性变为极性表面。
也可以说,经电晕放电处理后的聚烯烃表面大约零点几纳米的厚度已变成了与原聚烯烃结构完全不同的极性物质,表面张力提高,可达38~44mN∕m。
(2)高压高频电火花将薄膜材料表面冲击打毛,提高了油墨的浸润性和接触面积,在化学和物理两方面的作用下提高了油墨在其表面的附着牢度。
四、薄膜处理后表面张力的时效性问题
(1)刚处理好的薄膜,能达到40mN/m或42mN/m,几天后会下降到39mN/m左右,一两个星期,又会下降一些,因此,加工好的薄膜最好在7天以内用完,保存期超过1个月时表面张力会下降到38mN/m以下,在粘接、印刷方面就不太理想。
(2)同一卷膜中表面张力不均匀,粘接牢度和印刷牢度都非常差。
这是由于电压不稳定或临时停电,无电火花发生,停止了处理的故障造成的。
(3)若发现纵向方向有一条一条张力较低,或者半边高、半边低。
这是由于电火花发生器与被处理的薄膜不平行,或者发生器的局部被灰尘污染,造成集中放电,局部特别强,别的地方就偏弱,从纵向看就有条状不均匀现象。
(4)一般情况下,表面张力高,印刷和复合粘接的牢度都好,但也不是越高越好,太高反而不利。
据资料报道,对聚烯烃类来说,表面张力提高到48mN/m以前,粘接牢度是与表面张力的高低成正比的,但超过48mN/m后,粘接牢度反而下降。
从实际经验与条件的许可情况来看,聚乙烯和聚丙烯的表面张力维持在40~44mN/m就足够了,要求低一点的话,38~40mN/m也可以。
第三章第一节电眼光标的设计
在制袋或复合卷材的自动包装过程中常常要进行定位热合和定位裁切,一般应在适当位置印制光标(eyemark),这样自动包装机才能正确认读光标,从而控制机器的间歇节奏和切断位置
具体包括:
(1)光标位置:
设计时一般可以将电眼光标置于袋的底部。
电眼光标在卷材可以单边有,也可以双边有,一般建议双边有。
(2)光标与背景的颜色:
一般把印图中与背景颜色反差最大的颜色作为光标颜色,同时还须考虑认读光标的光电管的颜色。
①光标一般选用与底色有较大反差的深色,最好用黑色;②在透明复合包装产品上,光标在制版雕刻时尽量刻深点;
③一般不用红色和黄色作光标,也不能用与光电眼光同一颜色的色标为光标颜色;
④如果底色是较深的颜色(如黑色、深蓝色、深紫色等),光标应设计成镂空露白的浅色光标。
注意:
对于制袋机,一般有微电脑控制带定长的电眼跟踪系统,可以选择在一定位置范围内的光电眼信号(一般定长±3mm内的信号有效),而在这一范围之处的文字和图案可“视而不见”,因而可以不设计光标。
但应注意不能用太小太短的文字图案作跟踪点,也不能用圆弧状或斜线形的图案作跟踪点,如果没有合适的跟踪点,就必须设计光标。
(3)光标的尺寸:
①光标的开头为矩形,与包装机运行一致的方向偏短、与之垂直的方向偏长。
②一般光标的宽度在2~10mm内。
光标的宽度太小(小于2mm)可能会由于信号弱,影响设备的正常跟踪,若光标太宽(大于10mm),既不美观,又会引起跟踪定位精度降低。
③光标的长度大于5mm,因为在包装过程中由于卷膜会抖动走偏,光标太短可能会使光标偏离光电眼的位置而造成无法跟踪。
取15×5mm的居多。
注意:
当考虑光标的宽度时,应知道包装机光电管的有效宽度,并考虑包装膜在包装机上运行时的横向晃动。
当包装机光电管的有效宽为9mm,光标的尺寸可定为15mm。
(4)光标背景的图案:
从包装膜的运行方向来说,在光标的宽度(纵向)范围中,以光标的前沿或后沿(视认读的设置而定)为中心,在前后各15mm的范围内不应有妨碍认读的图案出现(图3–1),以防止引起识别错误。
(5)光标之间的间距:
光标之间的间距是用来定长的,一般只允许有±0.5mm的误差。
注意:
(1)对于许多自动包装设备来说,负偏差要比正偏差的跟踪效果好。
对于有些自动包装机只有光标之间为负偏差的间距时才能正常工作,有极个别自动包装机不但光标之间的间距要求负偏差,而且其精度要求很高,如德国Siebler公司的真空吸附跟踪控制的自动包装机,其要求每个光标之间的误差不超过-0.02mm
(2)镀铝或纯铝具有较强的镜面反射,会影响电眼的识别,建议在复合膜光标印上白色底;对于透明复合膜,由于会受与它相接触的物品的颜色的影响,也建议光标印上白色底,以减少其它底色的干扰。
(3)对于一些多列的包装机(在药品、洗剂的自动小包装中应用较多),原则只要有一组电眼即可。
一、凹版印刷的种类
1、照相凹版:
采用晒版、腐蚀等方法制作完成。
但包括电子雕刻凹版。
(印刷厂俗称“影写版”)
画面阶调层次表现方式:
网点面积相同,版面凹下深浅不同(如普通照相凹版)
网点面积不同,版面凹下深浅相同(如普通照相加网凹版)网点面积不同,版面凹下深浅不同(如电子雕刻凹版)
2、雕刻凹版:
采用手工或机械雕刻方法制作完成。
主要印刷有价证券。
二、凹版印刷的网穴特点
照相凹版的网穴特点
网点形状:
方形、砖形、菱形、不规则形
网墙宽度∶网穴宽度=1∶3~1∶2.5
比值小:
网墙窄,网穴大,图像再现性好,但网墙易被刮刀损坏,印版耐印率低。
比值大:
网墙宽,网穴小,网墙耐磨,印版耐印率高,但亮调和中间调图像再现性差。
网穴腐蚀深度:
一般为2~40μm,特殊的可达60μm过深,暗调层次无法表现
电雕凹版的网穴特征
共同点:
图文部分凹下而低于印版表面
凹下的网穴可容纳的油墨量不同,用来复制不同深浅的图文
差异点:
网穴深度和网穴面积率双调制型
网穴深度调制型
网穴面积率调制型
三、凹版印刷的网穴形状
五、凹版印刷的网墙
网墙的作用主要是支撑刮墨刀
防止油墨在网穴之间流动
无软片电雕机的特点:
①提高产品质量计算机直接控制将分色数据送人电雕机,不用分色软片,减少了工艺环节以及出软片和电雕机再扫描造成的信息损失,使雕刻质量提高。
②提高制版效率使用计算机替代的人工修拼版工作,并省去了旧工艺的照排、剪贴、翻晒、显影等手工劳动,制版周期大大缩短。
③降低成本和费用由于无需分色软片,故胶片、显影、冲洗、照相等材料已不再需要。
对一台电雕机而言,每年可节约几十万元的相关材料与设备费用。
④减少了设备投资由于不用分色软片,用户可以使用一台价格低廉的高档扫描仪来替代价格昂贵的电分机,这对原先无电分机的厂家来说尤为重要。
⑤提高了设计制作能力计算机整页拼版系统突破了手工制作和修版的局限性,它可充分发挥创作人员的想象力与创造力,做各种复杂的美术创意。
同时,无软片雕刻使雕刻方式更加灵活多样,可实现传统雕刻难以完成的工作。
⑥易于操作和掌握计算机操作进行图像修拼版,所见即所得,特别是整个操作采用菜单方式,中文提示,直观易学。
计算机系统的使用,使得操作人员需要掌握的重点是技术,柔性版印刷在印前处理时若按照胶印或凹印的方法制作柔性版,印出的样张会出现什么样的质量问题1.从加网线数上来讲,柔印比胶印和凹印的要低;2.柔印高光、暗调处达不到凹印和胶印的层次水平;3.从质量上来讲,柔印属于中低档层次,其套准精度不如凹印和胶印。
柔性版印刷的特点:
柔性版兼有凸、胶、凹印三者之特性
(1)柔性版印刷机采用网纹辊传墨的印刷部件,与其他印机相比,省去了复杂的输墨辊组,使印刷机大大简化,输墨控制反应更为迅速,操作更为方便。
(2)光敏柔性版是一种光敏橡胶型的印版,具有柔软、可弯曲、富于弹性的特点,耐印力高。
同时印版对印墨的传递性能好,特别适合醇类溶剂油墨的印刷。
(3)采用轻印刷压力进行印刷,其印刷压力约为1kg/m,仅仅是凸版印刷压力的1/30柔性版印刷由于具有很大的弹性,能适应极为广泛的承印材料,包括表面较为粗糙、较厚的纸张和纸板、瓦楞纸、丝织品以及吸收性差的不干胶纸、塑料、铝箔等的印刷。
(凸印压力:
50kg/平方厘米;凹印压力:
40kg/平方厘米;平印压力:
4~10kg/平方厘米;而柔印压力:
1~3kg/平方厘米)
(4)柔性版印刷机结构简单,成本低,价格仅为胶印机或凹版印刷机的二分之(5)印刷过程中印版装卸容易、材料损耗少,适合于大批量印刷品的印刷。
(6)柔性版不仅可以使用小幅面印刷,而且还可用于卷筒纸大幅面的印刷。
最近几年,有很多国家柔性版已经用于新闻报纸等大型印刷品的印刷,据统计,其印刷报纸的废品率只是胶印的一半。
网纹传墨辊:
又称为网纹辊、网线辊、格子辊、精细辊等
作用:
是保证短墨路传墨、匀墨质量的最为关键的部件。
是向印版上图文部分定量、均匀传递其所需要的油墨。
由于网纹辊的表面是由无数大小一致、分布均匀的凹孔所组成的,油墨通过这些凹孔再被传递到印版上,因此,严格来讲艺传递到印版上的油墨不像常规印刷墨辊那样是呈面状的,而是呈点状的。
(1)网纹传墨辊的功能:
A、利用其表面的凹孔载体来传递和控制油墨,因而具有储墨、匀墨、传墨的作用。
B、由于网纹传墨辊加工精度很高,即使在轻压状态下,也能侵好地传递油墨,从而减少和避免了墨杠和重影的产生。
C、由于网纹传墨辊表面的凹孔分布特性,其传递的墨膜具有均匀、一致的厚度。
如果加装适当的刮墨刀,油墨更能均匀而薄地被传递,从而可进行彩色网点印刷。
D、由于采用网纹传墨辊,克服了“飞墨”现象,对提高印刷机的速度起到了至关重要的作用。
(2)网纹传墨辊的类型与加工金属网纹辊、陶瓷网纹辊、新型的网纹辊
A、金属网纹辊由钢质辊芯、镀镍层、镀铜层和镀铬层等组成,其加工的方法有化学腐蚀法、机械雕刻、电子雕刻法和激光雕刻法等。
化学腐蚀法:
与凹版滚筒的制作基本相似机械雕刻法:
辊基装配一→镀镍一→精加工一→镀铜一→雕刻一→镀铬激光雕刻法:
激光束,激光雕刻的凹孔具有大小均匀、边缘光洁、深浅一致等优点。
B、陶瓷网纹辊使用寿命——很重要的参数
是将雕刻加工的着墨孔与陶瓷材料涂层结合在一起,因而既具有雕刻网纹辊的传墨性能,又具有极好的耐磨强度。
其制作的基本过程是:
在雕刻加工出表面的着墨孔后,先要进行喷砂处理,使网纹辊着墨孔表面质地变得粗糙些,以便增加陶瓷的附着力。
陶瓷材料是极细颗粒的氧化铝。
C、新型的网纹辊
由石墨碳纤维辊芯制成的网纹辊。
这种网纹辊质硬而轻,质量仅仅是钢辊的1/10,便于换辊,减轻了劳动强度。
而它的强度是普通钢辊的2倍,因此比较耐磨,不易损坏、对刮墨刀摩擦也更小。
同时,印刷中石墨碳纤维辊即使在高速运转也不易产生跳动,从而极大地提高柔性版质量。
(3)网纹传墨辊的结构采用雕刻方法加工制作的网纹传墨辊,其表面着墨孔的几何形状和尺寸是相同的。
A、四棱锥形着墨孔最普遍使用的一种着墨孔形式,由于雕刻刀刃尖圆角所决定,着墨孔有个小的底面,一般适用于橡胶墨斗辊使用,其规格有13~118线/cm。
B、四棱台形着墨孔底部是一平面,着墨孔的侧面比棱锥形更垂直,着墨孔间的隔墙更宽。
因此,网纹辊的释墨性能好,更具有通用性,既可用于橡胶墨斗辊也可配合刮墨刀使用。
其规格有4~217线/cm。
C、六棱台形着墨孔
开口角度较大,因而着墨孔释墨性能比前两种形式更好,墨孔间的隔墙具有更高的强度,可减缓刮墨刀造成的磨损。
D、斜线形着墨孔
斜线形着墨孔是与网纹传墨辊轴线呈45°螺旋雕刻斜槽而形成的,如图⒉8d所示。
这种着墨孔可保证油墨的流动性,适用于粘度较大的油墨,具有良好的传墨性能,其规格有4~80线/cm。
E、附加通道的着墨孔
这种结构的着墨孔是对四棱台形着墨孔的改进,它是沿垂直网纹辊轴线方向,在相邻着墨孔之间雕刻出通道,以增加油墨在着墨孔内的流动性,提高网纹辊的传墨性能。
这种着墨孔特别适用于半色调和彩色印刷要求的高线数网纹传墨辊。
以上结构的着墨孔如果采用激光雕刻加工工艺,还可加工出半球形着墨孔及其他异形着墨孔的网纹传墨辊。
(4)网纹传墨辊的传墨性能
A、网纹辊的网线数是指网纹辊表面直线方向上单位长度内着墨孔的数量,以线/cm表示。
网纹辊的网线数决定了网纹辊传墨的均匀性,网线数愈高,着墨孔愈小,传出去的墨点愈细,形成的墨层就越接近“连续”状态。
B、网纹辊的油墨涂布量
是指网纹辊表面上单位面积内着墨孔储存油墨的能力,其单位是g/m2.它的大小取决于着墨孔容积的大小及其分布密度。
由于网纹辊着墨孔大小均匀一致,所以根据着墨孔的形状便可计算出单个着墨孔的容积。
假如以四棱台形着墨孔为例,从剖面看它是一个梯形,现设梯形的顶部边长为况,底部边长为乙,着墨孔的深度,即高为乃,单位均为cm,则单个着墨孔的容积V为:
V=1/3h(a2+ab+b2)
网纹传墨辊的网线数愈高,其单个的着墨孔的容积愈小,网纹孔的油墨涂布量则愈少,着墨孔的释墨性能差,所以,网纹传墨辊的网线数并非愈高愈好。
但是,网纹传墨辊的网线数相对高些,着墨孔的开日面积小,传出去的墨点要细,适用于半色调或彩色印刷。
C、网纹传墨辊的传墨系数
是衡量网纹传墨辊传墨能力的大小的参数,它是指网纹传墨辊表面转移出去的墨量与剩余墨量的比值。
设网纹辊表面施加的墨量为X,转移后网纹辊上的剩余墨量为Y,则网纹传墨辊的传墨系数f为:
f=(X-Y)/Y
从理论上讲,网纹辊的传墨系数愈高,印刷效果愈好,印刷品的实地密度愈大,墨层愈饱满、厚实。
但是,一般网纹辊上的油墨都不太可能百分之百的转移,它受到网纹辊的结构形状、线数和印刷压力等因素的影响而有差别。
D、网纹传墨辊的使用寿命
网纹传墨辊在长期使用过程中,与墨斗辊、印版等的接触摩擦,尤其是在带有刮刀系统的刮墨刀的作用下,网纹辊表面将会出现不同程度的磨损,使着墨孔的开口变小,深度变浅,造成网纹传墨辊传墨单元面积减小,从而使总传墨量也相应降低。
网纹辊的磨损量与着墨孔深度变化有关,网纹辊的储墨量随磨损量的增加而急剧减小。
在相同印刷条件下,棱锥形网纹辊的寿命要比棱台形网纹辊短,即使两者的磨损量相同,棱锥形网纹辊的储墨量的下降要快得多,因此,棱锥形网纹传墨辊不适用于刮刀式印刷系统。
(5)网纹辊的选择
A、根据输墨方式的类型选择
在一般情况下,双辊式输墨的传墨量最大,反向刮刀式输墨的传墨量最小,因此为了满足一定传墨量及耐磨性