叶轮机设计与实验.docx
《叶轮机设计与实验.docx》由会员分享,可在线阅读,更多相关《叶轮机设计与实验.docx(15页珍藏版)》请在冰豆网上搜索。
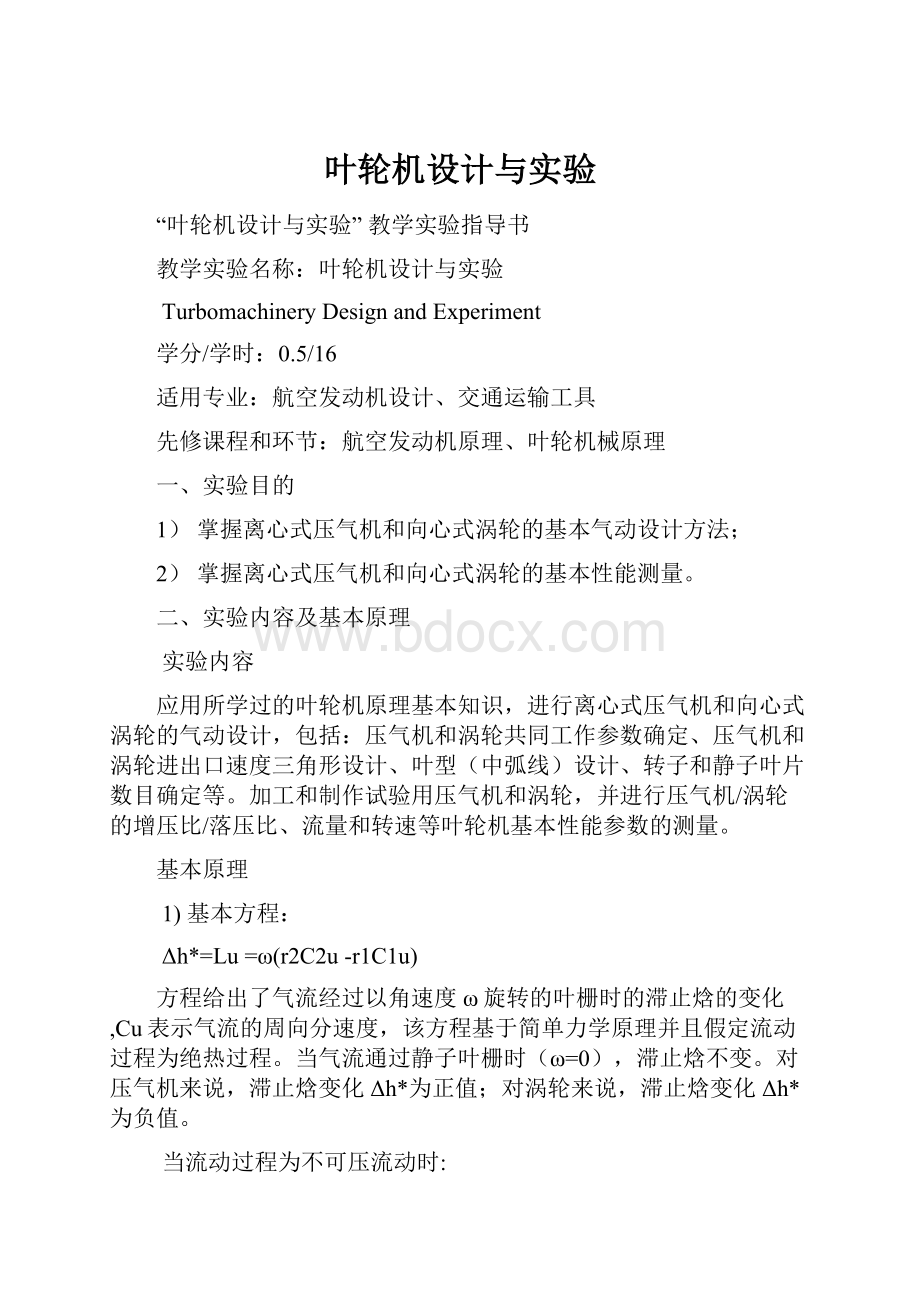
叶轮机设计与实验
“叶轮机设计与实验”教学实验指导书
教学实验名称:
叶轮机设计与实验
TurbomachineryDesignandExperiment
学分/学时:
0.5/16
适用专业:
航空发动机设计、交通运输工具
先修课程和环节:
航空发动机原理、叶轮机械原理
一、实验目的
1)掌握离心式压气机和向心式涡轮的基本气动设计方法;
2)掌握离心式压气机和向心式涡轮的基本性能测量。
二、实验内容及基本原理
实验内容
应用所学过的叶轮机原理基本知识,进行离心式压气机和向心式涡轮的气动设计,包括:
压气机和涡轮共同工作参数确定、压气机和涡轮进出口速度三角形设计、叶型(中弧线)设计、转子和静子叶片数目确定等。
加工和制作试验用压气机和涡轮,并进行压气机/涡轮的增压比/落压比、流量和转速等叶轮机基本性能参数的测量。
基本原理
1)基本方程:
Δh*=Lu=ω(r2C2u-r1C1u)
方程给出了气流经过以角速度ω旋转的叶栅时的滞止焓的变化,Cu表示气流的周向分速度,该方程基于简单力学原理并且假定流动过程为绝热过程。
当气流通过静子叶栅时(ω=0),滞止焓不变。
对压气机来说,滞止焓变化Δh*为正值;对涡轮来说,滞止焓变化Δh*为负值。
当流动过程为不可压流动时:
其中ΔP*c和ΔP*T分别表示气流流经压气机和涡轮时的总压变化。
当空气从静止的大气环境中被吸入压气机时,在进入压气机时没有周向分速度,即C1u=0。
当气体离开涡轮时,如果气流的周向分速度不为零,将会增加涡轮出口至真空泵进口管路中的流动摩擦损失。
因此,在设计状态下,涡轮转子出口气流的周向分速度应该为零(C4u=0)。
压气机和涡轮的转子或静子的进、出口径向分速度可通过连续方程得出:
Cr=m/(2πρrh)
其中m为流量,h为叶片的轴向宽度,ρ为空气密度。
知道径向和周向两个分速度后,可计算出相对静叶和动叶的气流方向。
动叶:
tan(αrel)=(Cu-ωr)/Cr
静叶:
tan(α)=Cu/Cr
α为绝对速度气流角,αrel为相对速度气流角,以气流的切线方向分速度Cu或Wu(Wu=Cu-ωr)与转子旋转方向相同为正值。
此外,叶型几何构造角以β表示。
2)压气机转子叶片
离心式压气机由动叶和静叶组成,动叶提高气体的动能和静压(静压升高约占总静压升的一半),静叶使气体的动能尽可能多地转换成静压升高。
假定流动过程是无粘的,气体通过静叶时的静压升高可以用伯努力方程计算。
实际的扩压过程远非等熵过程,实际扩压过程的压升小于等熵过程的压升,扩压效率通常为70%左右。
前弯径向后弯
转子叶片可以是如图所示的前弯、径向和后弯式,在转速一定的条件下,前弯角度越大,转子叶片出口的Cu越大,叶片对气体的加功量越大。
或者在加功量一定的条件下(受涡轮所能发出的功率限制),动叶的前弯角越大所需要的旋转速度越小,转速越低,压气机或涡轮的机械损失(轴承中摩擦损失)越小,但是这将增加气体离开动叶时的绝对速度,增加气体在静叶中的静压升,同时也将增加静叶中的流动损失。
因此,在设计转速较高时,转子叶片选择后弯叶型,可以在满足一定加功量的同时,获得较高的效率。
设计转速确定后,可以先选定动叶几何出口角β2,再根据加功量(涡轮输出功率)计算流量,这样做比预先选定转速和流量再算叶片几何出口角要容易些,最佳的β2值需经过较详细的计算才能确定,要从流动效率高和易于制造两个方面考虑来选择合适的值。
确定转速、转子叶片几何出口角β2和加功量后,可以求出压气机的流量和气流流入扩压器的速度。
由于气流离开转子不是完全以叶型的几何出气角流出,而总是有一点“滑移”,造成实际的C2u值小于理想值(气流以叶型的几何出气角流出转子时的C2u)。
通过引入滑移因子σ,可以计算实际的C2u。
Weisner定义滑移因子σ:
σ=1-(C2u,理想-C2u,实际)/u2
σ的值与许多因素有关,尤其是由叶片数目。
常用经验关系式如下:
σ=1-(cosβ2)0.5/N0.7
其中N是叶片数。
开始计算时,可初定σ=0.85,在初算时不改变σ的值,否则求解叶片数目的迭代计算可能会发散,在叶片数目确定以后,重新计算σ的值并代入计算。
理想的C2u计算很简单,
C2u,理想=(u2+C2rtanβ2),对于前弯叶片β2是正值,对于后弯叶片β2是负值。
C2u,实际=(σu2+C2rtanβ2)
将C2u,实际代入能量方程,得:
其中mc为压气机流量,NT为涡轮输出功率,C2r由连续方程求出:
其中h为转子叶片轴向宽度,将C2r代入能量方程,可得到求解流量的方程:
这是一个一元二次方程,mc取其合理解(较小值解)。
给定转子出口半径r2、转速和涡轮功率后,可以在前弯和后弯叶片范围内选择β2,并求出相应的流量,流量确定后可以计算出动叶进、出口气流的绝对速度和相对速度,当给定转子进口设计攻角为零攻角时,叶型几何进口角β1等于相对气流角α1rel。
要注意检查动叶出口相对速度与进口相对速度比值,这个比值不应太小,否则动叶的边界层可能分离,典型的W2/W1〉0.5,后弯角度越大,速度比值也越大,边界层分离的可能越小。
动叶数目是一个很重要的参数,若叶片数目太多,叶片表面与气流的摩擦损失大,若叶片数太少,气流从叶片表面分离也将引起大的损失,可以通过以下方法简单估算所需的叶片数目,由于叶片出口受到“滑移”的影响和叶片进口受到实际攻角的影响,以下方法只适用于叶片通道的平均半径rmid附近(rmid为几何平均半径)。
由动量矩方程可以得到:
Nb为叶片数,h为叶片的轴向宽度,ΔPb表示叶片压力面和吸力面压差。
假定相对气流角与叶片几何角相等,则:
Cu=u+Crtanβ
β为半径r处的叶型几何角,其它参数确定后,上述两个式子决定ΔPb的大小。
在相同半径处,叶片两面的滞止压力是相等的,即:
Ps+0.5ρWs2=Pp+0.5ρWp2
其中下标s,p表示吸力面和压力面,W为气流的相对速度。
可以假设从压力面的Wavg-ΔW到吸力面的Wavg+ΔW的相对速度是线性变化的,代入到上一个方程得:
ΔPb=Pp-Ps=2ρWavgΔW
当ΔW=Wavg时,压力面的速度为零,对应流动从叶片表面分离。
为防止分离发生,必须有ΔPb<2ρWavg2,将此不等式代入叶片数目表达式(动量矩方程),得:
上式表明Wavg值越大,所需要的叶片数目将越少,这可以理解为在较高的Wavg下,叶片的压力面和吸力面之间可以有较大的压力差,而流动仍然不分离。
Wavg的值可由平均半径rmid处径向速度和叶型几何角得到:
Wavgcosβ=Cr
叶片平均半径rmid处的叶型角βmid可由下式估算:
βmid=0.5×(β1+β2)
平均半径rmid处的Cr由连续方程确定。
d(rCu)/dr可以用rCu和半径r变化的平均值代替,即:
d(rCu)/dr≈Δ(rCu)/Δr=(r2C2u-r1C1u)/(r2-r1)
由于是在叶片平均半径rmid处估算叶片数目,为留有一定的余量,实际的叶片数目应略多于估算数目(大约多25%),若实际的叶片数目少于8或多于25,则需要修改设计,增加叶片后弯角度可以减少叶片数目。
采用上述方法在不同半径处估算出的叶片数目会不一样,在半径大处需要的叶片多,半径小处所需叶片少。
因此,许多离心压气机采用大小叶片结构,从平均半径处开始在大叶片之间增加小叶片,这样可以使用较少的大叶片,并且可以减少全部叶片与气体接触的总面积。
如果采用大小叶片设计,用1/3叶片高度处半径估算大叶片数目,从平均半径处开始在大叶片之间增加相同数量的小叶片。
叶片的型面最好是光滑的曲面,沿半径曲率的变化可以选择叶片载荷ΔPb沿半径r为一不变的常数。
由前面的方程:
可以看到,若ΔPb为常数,并将Cu=u+Crtanβ代入上式,得:
d(tanβ)/dr=const×r
此方程可以被积分,从而可得到叶片几何角β随半径r变化的函数,两个积分常数可由进出口边界条件(β1和β2)确定,可以通过作图法确定转子叶型。
转子叶片也可以采用简单的圆弧叶型,如图,在已知r1、r2、β1和β2条件下,可以求得叶型圆弧半径RC和其圆心半径RO:
RC=
R0=
3)扩压器叶片
在决定压气机效率方面,扩压器叶片起的作用可能比动叶大,扩压器叶片使气流减速并且尽可能地将动能转换为压力能。
只要流动减速就有可能出现附面层分离,这会使扩压器的性能受到限制。
扩压器的效率定义:
ηdiff=ΔP/ΔPis
ΔPis表示在相同的进口条件和相同的进出口面积比条件下,等熵流动过程的静压升,ΔP为实际过程静压升。
如果扩压器的长度不受限制,在均匀的进气条件下,扩压器的效率可以达到80%。
扩压器性能的另一种表示方法是其静压升系数:
ηeff=ΔP/(P*01-P1)
ηeff=ΔP/0.5ρC12(不可压流动)
C1为扩压器进口气流速度。
在转子出口和扩压器进口之间有一无叶片的径向间隙,气流流过此间隙时如果不考虑摩擦,则rCu保持不变,由连续方程还可知,Cr与半径是成反比例的,Cu和Cr两个速度分量在间隙中都是随半径增大而减小的,因此,在气流到达扩压器叶片之前在间隙内已经开始减速扩压,这一扩压过程在理论上可用伯努力方程算出。
然而,由于相对速度大时端壁摩擦力大,造成间隙流动的扩压效率低,因此无叶间隙不应太大,但是,也还必须有一定的尺寸,好让转子出口不均匀的气流在到达扩压器叶片之前变得均匀些,通常这种无叶片径向间隙的大小为当地半径的5%-10%,扩压器进口半径的大小也由此确定了。
扩压器叶片进口气流角是由离开转子的绝对气流角度α2,以及在间隙内流动时环量(rCu)和流量守恒决定的,进口气流角可以很容易算出,在设计扩压器叶片时应使其进口几何角近似等于算出的进口气流角。
有关扩压器叶片设计最重要的参数是喉道面积,即在两个邻近叶片间的最小通道面积。
在喉道处的速度由连续方程决定,并且在选择喉道处速度的大小时必须使扩压器总的压升中的一部分在喉道前完成,通常希望1/3的压升在喉道前完成,对应的喉道速度为扩压器进口速度的80%。
扩压器叶片的进口几何角确定后,可以通过改变叶片数和进口与喉道之间的叶片曲率来改变喉道面积,喉道面积对压气机性能来说是至关重要的,因为它是主要的控制流量的参数之一。
扩压器叶片的另一个重要参数是喉道以后的向外扩张的角度。
如果扩张角度太大,则附面层容易分离,扩张角度太小,流道面积沿流向增加偏小,会造成静压升偏小。
如果扩压器长度没有限制,较佳的扩张角约为6°。
通常情况下扩压器长度是受限制的,大的扩张角可以在有限空间里使流道出口与进口的面积比增大和静压升增大,但扩压器的效率会降低。
在扩压器长度受限制条件下,扩张角最大可以达到12°,其流动损失的大小仍然可以接受。
扩张角的大小由叶片数目和叶片曲率决定,对于简单的径向薄叶片来说,扩张角为360°/Nd,Nd为叶片数,因此,除非采用大量叶片,否则必须将叶片做成后弯形式来减少扩张角度。
设计扩压器应对扩张角和叶片数目进行优化,既要叶片数目合理,又要使静压升系数尽可能高。
通常扩压器叶片几何出口角β4可选择比几何进口角β3小12∽20度,几何进口角β3、几何出口角β4以及扩压器进口半径R3、出口半径R4选定后,试给出叶片数Nb,并计算叶栅稠度τ=l/t,其中l相当于叶片的长度,可用下式近似计算:
l≈
栅距t取扩压器进口叶片栅距,稠度τ范围为2.0∽3.0。
计算当量扩张角θeq,
h为叶片轴向宽度,最佳当量扩张角θeq约为5°。
可采用与转子叶片相同的方法,生成圆弧型扩压器叶片。
4)涡轮转子叶片
涡轮性能受涡轮叶片几何形状细节的影响小,这一点同压气机不一样,因为气流流经涡轮时是加速流动,边界层分离的可能性小,但是,应争取获得尽可能高的效率。
以下公式中,下标3表示的涡轮转子进口,下标4表示涡轮转子出口。
涡轮设计应使涡轮转子出口处气流的Cu接近与零,而压气机转子进口气流的Cu也为零,由能量守恒方程:
mCLK=mTLT
式中mC为压气机流量,mT为涡轮流量,可得:
mT(rCu)涡轮转子进口=mC(rCu)压气机转子出口
等式右边由压气机设计参数确定。
由涡轮转子进口速度三角形得:
tanα3,rel=(C3u-u3)/C3r
C3r由连续方程确定,转子进口设计攻角为零时,转子进口叶型几何角β3=α3,rel。
转子出口C4u=0,由转子出口速度三角形得:
tanα4,rel=-u4/C4r
C4r由连续方程确定,α4,rel为负值。
由于转子出口气流角和叶型几何角之间存在着落后角,目前尚无有关该落后角的准确估算方法,若转子叶片数目较多,并且气流在转子通道中的转角也比较小,可以认为落后角为零度,这样转子出口叶型几何角β4即为转子出口相对气流角α4,rel。
涡轮转子的喉道面积是另一个影响流量的重要参数,应该使得气体在喉道处的速度与在涡轮出口处的速度相同,即满足下列关系:
N叶片数×喉道宽度=2πr4cos(α4,rel)
这样就要求转子叶片在出口附近可能曲率比较大,准确的喉道面积比叶型角β4更为重要,但是两者都应尽可能地满足各自的设计要求。
涡轮转子叶片的数目可以用与压气机相同的方法在中径处(rmid)估算,由于前缘附近气流容易分离,建议按比估算出的叶片数目多25%进行设计。
如果采用大小叶片设计,则小叶片放置在涡轮转子进口部分。
转子叶型可以按与压气机相同的方法进行设计,即沿半径负荷ΔPb不变叶型或圆弧叶型,但是,所要求的喉道面积必须保证,喉道宽度可以从图上量出。
5)涡轮静子叶片
本实验的涡轮进口总压为大气压力,总温为大气温度,涡轮静子使气体加速,静子中流动分离的可能性很小,但也必须使摩擦损失尽可能小。
在静子出口和转子进口之间有一径向间隙,由于在间隙中气流相对于壁面速度大,会产生较大的摩擦损失,因此,径向间隙应尽量小。
然而间隙又不能过小,否则将导致转子叶片受到很强的非定常力的作用,引起叶片振动和疲劳断裂,通常该间隙的大小是当地半径的5%左右。
已知转子进口Cu,并且假定rCu在间隙中保持不变,通过连续方程可以知到静子出口的Cr,这样静子出口气流角度和气流速度便可以确定,另外,静子进口气流Cu=0。
涡轮静子叶栅最重要的参数是其喉道面积,喉道面积决定喉道处的速度大小,喉道处的速度应该与静子出口处的速度接近,这样在喉道和尾缘之间就没有减速扩压流动。
然而,由于在喉道和尾缘之间半径大小是变化的,这就要求气流角或叶型角从喉部至尾缘是逐渐减小的,即在喉道下游叶片曲率应稍微相反。
这个区域内的流动非常关键,因为该区域内气流速度最大,摩擦损失也最大,在喉部和尾缘之间叶片应该是光滑的而且不能有很大的曲率。
喉道面积由喉部的叶型角度和叶片数目二者决定,没有固定的公式来计算静子叶片数目,叶片数目过多会因为与气体接触面积过大而导致摩擦损失过大以及较大的尾迹损失,后者与尾缘堵塞成比例(即:
叶片厚度/喉道宽度)。
叶片数目过少会导致喉道位置不明显、喉道面积计算不准确和静叶出口气流沿周向不均匀。
可粗略地借用轴流式涡轮静子的设计准则,按栅距与弦长比大约为0.75来确定静子叶片数目,栅距取静子进口栅距,弦长取前缘到尾缘的距离。
试画出可能的静叶叶栅草图,判断并选择静叶叶型和叶片数目。
6)设计参数选择
本实验有些几何参数是固定的,如:
压气机转子进口半径r=50毫米,压气机转子出口半径r=120毫米,
压气机静子进口半径r=128毫米,压气机静子出口半径r=185毫米,
涡轮转子进口半径r=120毫米,涡轮转子出口半径r=50毫米,
涡轮静子进口半径r=185毫米,涡轮静子出口半径r=128毫米,
压气机和涡轮静叶的轴向宽度hs=18毫米,压气机和涡轮动叶的轴向宽度hr=16毫米。
另外,有些参数的选择是有一定范围的,如:
最大转速n=3000∽4000转/分,涡轮功率100∽150W。
压气机流量mK=0.15∽0.25kg/s左右,涡轮流量mT=0.10∽0.20kg/s左右,
压气机总压升ΔPC*=1000∽2000Pa,涡轮总压降ΔPT*=2000∽4000Pa。
无论是压气机还是涡轮,动叶叶片数最好与静叶的叶片数互质,以免产生共振。
三、实验使用的仪器设备及实验装置
1.转速测量仪,2.测压水排,3.涡轮出口总压,4.涡轮出口静压,5.软管,
6.连接段,7.整流格栅,8.真空泵。
四、具体实验步骤
叶片采用用0.5毫米厚的薄铝片按中弧线形状加工成型,叶片与盘用胶粘贴。
为了使联接处有足够的强度,联接处胶体应堆砌成三角形,并且涂抹要均匀。
试运转后检查所有转子和静子叶片与盘的粘贴情况,若胶体不再是半透明状,而是有些发白时,说明粘接不牢靠,应该将叶片拆下,重新粘贴。
实验时接通两台真空泵,用光电测速仪测量转速,当转速稳定后,开始记录数据。
由于涡轮出口总压沿半径是不均匀的,需要沿半径多点测量,取平均值。
五、实验准备及预习要求
尽管可以很容易用手工完成以上所有的计算,但是最好还是编制一个有关压气机和涡轮叶片设计的简单计算程序,这样既可以避免手工计算产生错误,同时又可以在较大范围内进行设计参数的快速优化调整。
实验报告
学号姓名时间成绩
1.设计值和实验测量结果
1.1离心压气机
转子
进口几何角
出口几何角
叶片数目
滑移因子σ
轮缘功Lu
静子
进口几何角
出口几何角
叶片数目
当量扩张角
稠度τ
总参数
转速(rpm)
流量(kg/s)
总压升Pa
设计值
实验值
1.2向心涡轮
转子
进口几何角
出口几何角
叶片数目
喉道宽度
轮缘功Lu
静子
进口几何角
出口几何角
叶片数目
喉道宽度
稠度τ
总参数
转速(rpm)
流量(kg/s)
总压降Pa
设计值
实验值
3.若总参数设计值与实验值存在较大差别,试说明可能的原因。