金属手柄冲裁工艺与模具设计.docx
《金属手柄冲裁工艺与模具设计.docx》由会员分享,可在线阅读,更多相关《金属手柄冲裁工艺与模具设计.docx(31页珍藏版)》请在冰豆网上搜索。
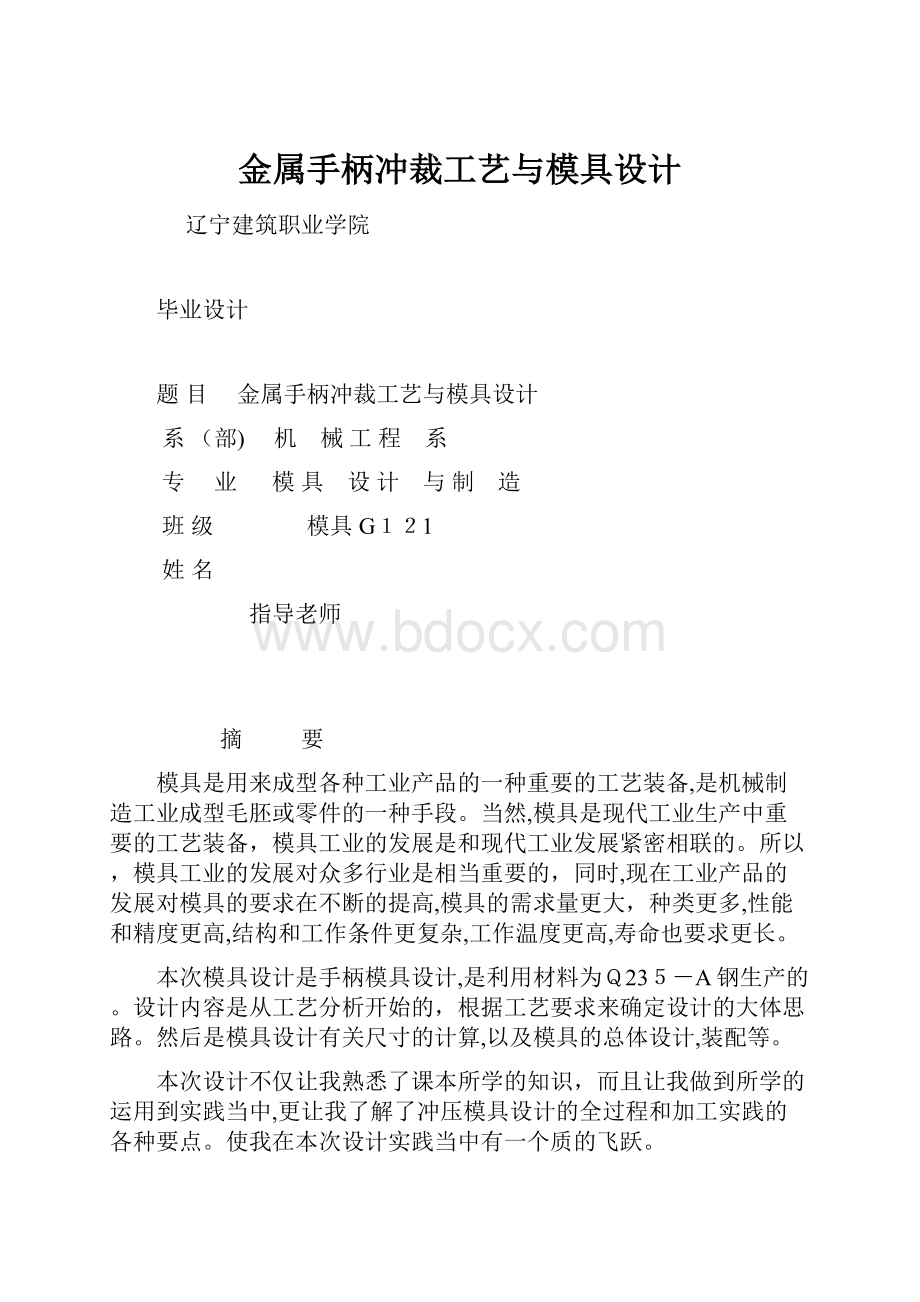
金属手柄冲裁工艺与模具设计
辽宁建筑职业学院
毕业设计
题目 金属手柄冲裁工艺与模具设计
系(部) 机 械工程 系
专 业 模具 设计 与制 造
班级 模具G121
姓名
指导老师
摘 要
模具是用来成型各种工业产品的一种重要的工艺装备,是机械制造工业成型毛胚或零件的一种手段。
当然,模具是现代工业生产中重要的工艺装备,模具工业的发展是和现代工业发展紧密相联的。
所以,模具工业的发展对众多行业是相当重要的,同时,现在工业产品的发展对模具的要求在不断的提高,模具的需求量更大,种类更多,性能和精度更高,结构和工作条件更复杂,工作温度更高,寿命也要求更长。
本次模具设计是手柄模具设计,是利用材料为Q235-A钢生产的。
设计内容是从工艺分析开始的,根据工艺要求来确定设计的大体思路。
然后是模具设计有关尺寸的计算,以及模具的总体设计,装配等。
本次设计不仅让我熟悉了课本所学的知识,而且让我做到所学的运用到实践当中,更让我了解了冲压模具设计的全过程和加工实践的各种要点。
使我在本次设计实践当中有一个质的飞跃。
关键词:
模具 冲压手柄
目 录
第一章.冲压成型与模具技术概述………………………………1
1.1冲压与冷冲模概念.………………………………………………1
1.2冲模设计与制造要求………………………………………… 1
1.3冲压现状与发展方向…………………………………………4
第二章.冲压变形理论……………………………………………7
2.1 塑性变形的概念……………………………………………… 7
2.2 塑性力学基础………………………………………………… 8
2.3冲压材料及其冲压成型性能…………………………………9
第三章.模具材料选用…………………………………………… 11
3.1 冲压对模具材料的要求………………………………………11
3.2冲模材料的选用原则………………………………………… 11
第四章.设计依据原始数据………………………………………12
4.1冲压件工艺性分析……………………………………………12
4.2冲压工艺方案确定…………………………………………… 12
4.3主要设计计算…………………………………………………12
4.3.1排样方式的确定及其计算………………………………12
4.4冲压力的计算………………………………………………… 13
4.5压力中心的确定及相关计算…………………………………13
4.6工作零件刃口尺寸计算………………………………………13
4.7卸料橡胶的设计………………………………………………16
4.8模具总体设计………………………………………………… 16
第五章.主要零部件设计………………………………………… 17
5.1工作零件的结构设计…………………………………………17
5.2定位零件的设计……………………………………………… 17
5.3导料板的设计…………………………………………………17
5.4卸料部件的设计……………………………………………… 18
5.5模架及其它零部件设计……………………………………… 19
第六章.模具总装图……………………………………………… 21
第七章.冲压设备的选定…………………………………………22
第八章. 模具加工工艺……………………………………………24
第九章.模具的装配………………………………………………24
总结………………………………………………………………… 28
参考文献……………………………………………………………… 29
致谢………………………………………………………………… 30
第一章 冲压成型与模具技术概述
1.1冲压与冷冲模概念
冲压是在温室下,利用安装在压力机上的模具对材料施加压力,使其产生分离或塑性变形,从而获得所需零件的一种压力加工方法。
在冲压加工中,将材料(金属或非金属)加工或零件(或半成品)的一种特殊工艺装备,称为冲压模具(俗称冲模)。
冲模是现实冲压加工中是必不可少的工艺装备,与冲压件是“一模一样”的关系,若没有符合要求的冲模,就不能生产出合格的冲压件;没有先进的冲模,先进的冲压成型工艺就无法实现。
在冲压零件的生产中,合理的冲压成型工艺,先进的模具,高效的冲压设备是必不可少的三要素。
冲模在种类繁多的模具中占有十分重要的地位,它占了模具总产量的30%以上,从产值上看,它占了模具总产值的50%左右。
冲压加工与其他加工方法相比,无论在技术方面,还是在经济方面,都具有许多独特的优点,生产的制件所表现出来的高精度,高复杂度,高一致性,高生产率和低消耗,是其他加工制造方法所不能比拟的。
但需要指出的是,犹豫进行冲压成型加工必须具备相应的模具,而模具是技术密集型产品,其制造属单件小批量生产,具有难加工,精度高,技术要求高,生产成本高(占产品成本的10%到30%)等特点。
所以,只有在冲压零件生产批量大的情况下,冲压成形加工的优点才能充分体现,从而获得好的经济效益。
由于冲压加工具有上述突出的优点,因此在批量生产中得到了广泛的应用,在现代工业生产中占有十分重要的地位,是国防工业及民用工业生产中必不可少的加工方法。
1.2 冲模设计与制造要求
通常冲压产品的生产流程如下图1所示。
冲压技术工作包括冲压工艺设计,模具设计及冲模制造三方面内容,尽管三者的内容不同,但三者之间都存在着相互关联,相互影响和相互依存的联系。
三者基本内容和基本要求见表1示
(冲压)产品设计
↓
冲压成型工艺设计
↓
冲压模具设计
↓
冲模制造
↓
冲压产品生产
图1
表1
项目名称
基本内容
基本要求
冲压成形工艺设计
针对给定的产品图样,根据其生产批量的大小,企业现有冲压设备的类型规格,模具制造能力及工人技术水平等具体生产条件;从对产品零件图的冲压工艺性分析入手,经过必要的工艺计算,制订出合理的工艺方案(包括工序性质,数量的确定,工序顺序的安排,工序组合方式及工序定位方式的确定等),最后
编写出冲压工艺卡
(1)冲压原材料利用率高,即材料消耗应尽可能少。
(2)根据工厂的具体生产条件,制定的工艺方案应技术上先进可行,经济上合理。
(3)工序组合方式和工序排列顺序应符合冲压变形规律,能确保冲压出合格的工件。
(4)工序数量应尽可能少,生产效率尽可能高。
(5)制订的工艺规程,应方便工厂的生产组织与管理。
续表
项目名称
基本内容
基本要求
冲压模具设计
依据制订的冲压工艺规程,在认真考虑毛坯的定位、出件、废料排除等问题以及模具的制造维修方便、操作安全可靠等因素后,设计计算并构思出于冲压设备相适应的模具总体结构,然后绘制出模具总装图和所有非标准零件图,要能保证冲压工艺的实施。
(1)模具结构及其尺寸参数应保证能冲压出形状、尺寸、精度均符合图样要求的零件。
(2)模具结构应尽可能简单,加工精度合理,制造维修方便,成本低廉。
(3)模具要坚固耐用,能满足批量生产的要求。
(4)模具要操作方便,工作安全可靠,工人劳动强度要低。
(5)生产准备周期要短。
模具制造
根据模具结构、模具材料、尺寸精度、行位精度、工作特性和使用寿命等要求,综合考虑各方面的特点,并充分发挥现有设备的一切特长,正确选择加工方法和装配方法,选出最佳加工放方案,制订出合理的冲模加工工艺规程
(1)为了生产合格的产品和发挥模具的效能,制造的模具必须具有较高的精度。
(2)一般要求模具应具有较长的使用寿命。
(3)较短的模具制造周期。
(4)较低的模具制造成本
应该指出,冲模设计与制造必须根据企业和产品生产批量的实际情况进行全面考虑,在保证质量的前提下,寻求最佳的技术经济性。
片面追求生产效率、模具精度和使用寿命必然导致成本的增加,只顾降低成本和缩短制造周期而忽视模具精度和使用寿命必然导致质量下降。
1.3冲压现状与发展方向
目前,我国冲压技术与工业发达国家相比还相当落后,主要原因是我国在冲压基础理论及成形工艺、,模具标准化、模具制造工艺及设备等方面与工业发达国家尚有相当大的差距,导致我国模具在寿命、效率、加工精度、生产周期等方面与工业发达国家的模具相比差距相当大。
随着工业产品质量的不断提高,冲压产品生产证呈现多品种、少批量,复杂、大型、精密,更新换代速度快等变化特点,冲压模具正向高效、精密、长寿命、大型化方向发展。
为适应市场变化,随着计算机技术和制造技术的迅速发展,冲压模具设计与制造技术正由手工设计、依靠人工经验和常规机械加工技术向以计算机辅助设计(CAD)、数控切削加工、数控电加工为核心的计算机辅设计与制造(CAD/CAM)技术转变。
1.冲压成形理论及冲压工艺
加强冲压变形基础理论的研究,以提供更加准确、适用、方便的计算方法,正确地确定冲压工艺参数和模具工作部分的几何形状,解决冲压变形中出现的各种实际问题,进一步提高冲压件的质量。
研究和推广采用新工艺,如精冲工艺、软模成形工艺,高能高速成形工艺、超塑性成形工艺以及其他高效率、经济成形工艺等,进一步提高冲压技术水平。
2,模具新材料及热处理、表面处理
随着产品质量的提高,对模具质量和寿命要求越来越高。
而提高模具质量和寿命最有效的方法就是开发和应用模具新材料及热处理、表面处理新工艺,不断提高使用性能,改善加工性能。
(1)模具新材料
冲压模具使用的材料术语冷作模具钢,是应用量大、使用面广、种类最多的模具钢。
主要性能要求为强度、韧性、耐磨性。
目前,冷作模具钢的发展趋势是在高合金钢D2(相当于我国Cr12MoV)性能基础上,分为两大分支:
一种是降低含碳量和合金元素量,提高钢中碳化物分布均匀度,突出提高模具的韧性,如美国钒合金钢公司的8CrMo2V2Si、日本大同特殊钢公司的DC53(Cr8Mo2SiV)等。
另一种是以提高耐磨性为主要目的,以适应高速、自动化、大批量生产而开发的粉末高速钢。
如德国的320CrVMo13,5等。
(2)热处理、表面处理新工艺
为了提高模具工作表面的耐磨性、硬度和耐蚀性,必须采用热处理、表面处理新技术,尤其是表面处理新技术。
除人们熟悉的镀硬铬,渗氮等表面硬化处理方法外,今年来模具表面性能强化技术发展很快,实际应用效果很好。
其中,化学气相沉积(CVD)、物理气相沉积(PVD)以及盐浴渗金属(TD)等方法是集中发展较快、应用最广的表面涂覆硬化处理的新技术。
它们对提高模具寿命和减少模具昂贵材料的消耗,有着十分重要的意义。
3.模具CAD/CAM技术
计算机技术、机械设计与制造技术的迅速发展和有机结合,形成了计算机辅助设计与计算机辅助制造(CAD/CAM)这一新技术。
CAD/CAM是改造传统模具生产方式的关键技术,是一项高科技、高效益的系统工程,它以计算机软件的形式为用户提供一种有效的辅助工具,使工程技术人员能借助计算机对产品、模具结构、成形工艺、数控加工以成本等进行设计和优化。
模具CAD/CAM能显著缩短模具设计及制造周期、降低生产成本、提高产品质量,以成为人们的共识。
随着功能强大的专业软件和高效继承制造设备的出现,以三维造型为基础、基于并行工程(CE)的模具CAD/CAM技术正成为发展方向,它能实现面向制造和装配的设计,实现成形过程的模拟和数控加工过程的仿真,使设计、制造一体化。
4.快速经济制模技术
为了适应工业生产中多品种、小批量长生的需要,加快模具的制造速度,降低模具生产成本,开发和应用快读经济制模技术越来越受到人们的重视。
目前,快速经济制模技术主要有低熔点合金制模技术、锌基合金制模技术、环氧树脂制模技术、喷涂成形制模技术、叠层钢板制模技术等。
应用快速经济制模技术制造模具,能简化模具制造工艺、制造周期、降低模具生产成本,在工业生产中取得了显著地经济效益。
对提高新产品的开发速度,促进生产的发展有着非常重要的作用。
5.模具标准化
模具标准化是缩短模具制造周期、降低模具开发成本、提高模具质量的有效方法,模具标准化程度的高低是体现一个国家整体技术水平的重要标志之一。
我国模具标准件技术水平低、模具标准化程度低,与先进工业国家相比有较大差距。
国外标准件应用覆盖率达到80%,我国仅40%左右。
学习借鉴国外先进模具标准,开发我国模具新标准,提高模具标准件精度和互换性以及模具标准化程度,是我国模具标准化工作努力的方向。
6.先进生产管理模式
随着需求的个性化和制造的全球化、信息化,企业内部和外部环境的变化,改变了模具业的传统生产观念和生产组织方式。
现代系统管理技术在模具企业正得到逐步应用,主要表现在:
①应用集成化思想,强调系统集成,实现了资源共享;②实现金字塔式的多层次生产管理结构向扁平的网络结构转变,由传统的顺序工作方式想并行工作方式的转变;③实现以技术为中心向以人为中心的转变,强调协同和团队精神。
先进生产管理模式的应用使得企业生产实现了低成本、高质量和高速度,提高了企业市场竞争能力。
第二章冲压变形理论基础
2.1塑性变形的概念
在金属材料中,原子之间作用着相当大的力,足以抵抗重力的作用,所以在没有其他外力作用的条件下,金属物体将保持自由的形状和尺寸。
当物体受到外力作用之后,它的形状和尺寸将发生变化即变形,变形的实质就是原子间的距离产生变化。
假如作用于物体的外力去除后,由外力引起的变形随之消失,物体能完全恢复自己的原始形状和尺寸,这样的变形称为塑性变形塑性变形和弹性变形都是在变形体不破坏的条件下进行的(即连续性不破坏)。
通常用塑性表示材料塑性变形能力。
所谓塑性,是指固体材料在外力作用下发生永久变形而不破坏其完整性能力。
金属的塑性不是古亭不变的,影响它的因素很多,除了金属本身的晶格类型、化学成分和金相组织等内在因素之外,其外部因素——变形方式(机械因素及应力状态与应变状态)、变形条件(物理因素及变形温度与变形速度)的影响也很大。
影响金属塑性的主要因素见下表。
影响因素
影响规律
材料组织结构
面心立方结构的金属塑性好于体心立方,密排六方最差。
组成金属的元素越少(如纯金属和固溶体),晶粒越细小,组织分布越均匀,则金属塑性越好
应力状态
压应力有利于封闭裂纹,阻止其继续扩展,减小或阻止晶间变形,增加晶间结合力,消除由于塑性变形引起的各种破坏;与此相反,拉应力则促使材料的裂纹扩展,加快材料的破坏。
所以,在应力状态中,压应力个数越多,数值越大,则金属的塑性越好。
反之,拉应力个数越多,数值越大,则金属的塑性越差。
变形温度
一般温度升高,塑性增加
变形
速度
变形速度对塑性的影响有正反两方面,对大多数金属来说民俗性随变形速度变化的一般趋势是先降低,后增加
2.2塑性力学基础
1.点的应力与应变状态
金属冲压成型时,外力通过模具作用在坯料上,使其内部产生应力,并且发生塑性变形。
一定的力的作用方式和大小都对应着一定的变形,受力不同,形变就不同。
由于坯料变形区内个点的手里和变形情况不同,为了全面、整地描述变形区内个点受力情况,引入点的应力状态的概念。
某点的应力状态,通常是围绕该点取出一个微小(正)六面体(即所谓的单元体),用该单元体上三个相互垂直面上的应力来表示。
一般可沿坐标方向将这些应力分解成9个应力分量,即3个正应力和6个切应力。
由于单元体处于静平衡状态,根据切应力互等定理,实际上只需要知道6个应力分量,即3个正应力和3个切应力,就可以确定该点的应力状态。
2.金属的屈服条件
众所周知,在材料单向拉伸中,由于质点处于单向应力状态,只要单向拉伸应力达到材料的屈服极限,该质点即行屈服,进入塑性状态。
在多向应力状态时,显然就不能仅仅用某一应力分量来判断质点是否进入塑性状态,必须同时考虑其他应力分量。
研究表明,只有当各应力分量之间符合一定的关系时,质点才进入塑性装填。
这种关系叫做屈服条件,或屈服准则,也称塑性条件或塑性方程。
满足屈服条件表明材料处于塑性状态。
材料要进行塑性变形,必须始终满足屈服条件。
对于应变硬化材料,材料要由弹性变形转为塑性变形,必须满足的屈服条件叫初始屈服条件;而塑性变形要继续发展,必须满足的屈服条件则叫后继屈服条件。
在一般应力状态下,塑性变形过程的发生、发展,实质上可以理解为一系列的弹性极限状态的突破——初始屈服和后继屈服。
材料是否屈服和进入塑性状态,主要取决于两个方面的因素:
(1)在一定的变形条件(变形温度和变形速度)下材料的物理力学性质——转变的根据;
(2)材料所处的应力状态——转变的条件。
2.3冲压材料及其冲压成形性能
1冲压成形性能的概念
冲压成形加工方法与其他加工方法一样,都是以自身性能作为加工依据,材料实施冲压成形加工必须有好的冲压成形性能。
材料对各种冲压加工方法的适应能力称为材料的冲压成形性能。
材料的冲压性能好,就是指其便于冲压加工,一次冲压工序的极限变形程度和总的极限变程度大,声场效率高,容易得到高质量的冲压件,模具寿命长等。
由此可见,冲压成形性能是一个综合性的概念,它涉及的因素很多,但就其主要内容来看,有两方面:
一是成形极限,二是成形质量。
(1)成形极限 在冲压成型过程中,材料能达到的最大变形程度成为成形极限。
对于不同的成形工艺,成形极限是采用不同的极限变形系数来表示的。
由于大多数冲压成形都是在板厚方向上的应力数值近似零的平面应力状态下进行的,因此不难分析:
在变形坯料的内部,凡是受到过大拉应力作用的区域,就会使坯料局部严重变薄,甚至拉裂而使冲件报废;凡是受到大压应力作用的区域,若超过了临界应力就会使坯料丧失稳定而起皱。
因此,从材料方面来看,为了提高成形极限,就必须提高材料的塑性指标和增强抗拉、抗压能力。
冲压时,当作用于坯料变形区内的拉应力的绝对值最大时,在这个方向上的变形一定是伸长变形,故称这种冲压变形为伸长类变形(如胀形、扩口、内孔翻边等)。
当作用于坯料变形区内的压应力的绝对值最大时,在这个方向上的变形一定是压缩变形,故称这种冲压变形为压缩类变形(如拉深、缩口等)伸长类变形的极限系数主要决定于材料的塑性;压缩类变形的极限变形系数通常是受坯料传力区的承载能力的限制,有时则受变形区或传力区的失稳起皱的限制。
(2)成形质量 冲压件的质量指标主要是尺寸精度、厚度变化、表面质量以及成形后材料的物理、力学性能等。
影响工件质量的因素很多,不同的冲压工序情况又各不相同。
材料在塑性变形的同时总伴随着弹性变形,当载荷卸除后,由于材料的弹性回复,造成制件的尺寸和形状偏离模具,影响制件的尺寸和形状精度。
因此掌握回弹规律,控制回弹量是非常重要的。
冲压形成后,板厚一般都要发生辩护啊,有的是变厚,有的是变薄。
厚度变薄直接影响冲压件的强度和使用,对强度有要求时,往往要限制其最大变薄量。
材料经过塑性变形后,除产生加工硬化现象外,还由于变形不均,造成残余应力,从而引起工件尺寸及形状的变化,严重时还会引起工件的自行开裂。
所有这些情况,在制定冲压工艺时都应予以考虑。
影响工件表面质量的主要因素是原材料的表面状态、晶粒大小、冲压时材料粘膜的情况以及模具对冲压件表面的擦伤等。
原材料的表面状态直接影响工件的表面质量;晶粒粗大的钢板拉伸时产生所谓“子皮”样的缺陷(表面粗糙);冲压易于粘膜的材料则会擦伤冲压件并降低磨具寿命。
此外,模具间隙不均,模具表面粗糙也会擦伤冲压件。
第三章模具材料选用
3.1冲压对模具材料的要求
不同冲压方法,其模具类型不同,模具工作条件有差异,对模具材料的要求也有所不同。
表1.4.1是不同模具工作条件及对模具工作零件材料的性能要求。
表1.4.1
模具类型
工作条件
模具工作零件材料的性能要求
冲裁模
主要用于各种板料的冲切成形,其刃口在工作过程中到手强烈的摩擦和冲击
具有高的耐磨性、冲击韧性以及耐疲劳断裂性能
弯曲模
主要用于板料的弯曲成形,工作负荷不大,但有一定的摩擦
具有高的耐磨性和断裂抗力
拉深模
主要用于板料的拉深成形,工作应力不大,但凹模入口处承受强烈的摩擦
具有高的硬度及耐磨性,凹模工作表面粗糙度值比较低
3.2冲模材料的选用原则
模具材料的选用,不仅关系到模具的使用寿命,而且也直接影响到模具的制造成本,因此事模具设计中的一项重要工作。
在冲压过程中,模具承受冲击负荷且连续工作,使凸、凹模受到强大压力和剧烈摩擦,工作条件及其恶劣。
因此,选择模具材料应遵循如下原则:
(1)根据模具种类及其工作条件,选用材料要满足使用要求,应具有较高的强度、硬度、耐磨性、耐冲度、耐疲劳性等;
(2)根据冲压材料和冲压件生产批量选用材料;
(3)满足加工要求,应具有良好的加工工艺性能,便于切削加工,淬透性好、热处理变形小;
(4)满足经济性要求。
第四章设计依据原始数据
工件名称:
手柄;生产批量:
中批量;材料:
Q235-A钢;材料厚度:
1.2mm
工件简图:
如下图所示。
设计步骤:
4.1冲压件工艺性分析
此工件只有落料和冲孔两个工序。
材料为Q235-A钢,具有良好的冲压性能,适合冲裁。
工件结构相对简单,有一个φ8mm的孔和5个φ5mm的孔;孔与孔、孔与边缘之间的距离也满足要求,最小壁厚为3.5mm(大端4个φ5mm的孔与φ8mm孔、φ5mm的孔与R16mm外圆之间的壁厚)。
工件的尺寸全部为自由公差,可看作IT14级,尺寸精度较低,普通冲裁完全能满足要求。
4.2冲压工艺方案的确定
该工件包括落料、冲孔两个基本工序,可有以下三种工艺方案:
方案一:
先落料,后冲孔。
采用单工序模生产。
方案二:
落料-冲孔复合冲压。
采用复合模生产。
ﻫ方案三:
冲孔-落料级进冲压。
采用级进模生产。
方案一模具结构简单,但需两道工序两副模具,成本高而生产效率低,难以满足中批量生产要求。
方案二只需一副模具,工件的精度及生产效率都较高,但工件最小壁厚3.5mm接近凸凹模许用最小壁厚3.2mm,模具强度较差,制造难度大,并且冲压后成品件留在模具上,在清理模具上的物料时会影响冲压速度,操作不方便。
方案三也只需一副模具,生产效率高,操作方便,工件精度也能满足要求。
通过对上述三种方案的分析比较,该件的冲压生产采用方案三为佳。
4.3主要设计计算
4.3.1排样方式的确定及其计算
设计级进模,首先要设计条料排样图。
手柄的形状具有一头大一头小的特点,直排时材料利用率低,应采用直对排,如图二所示的排样方法,设计成隔位冲压,可显著地减少废料。
隔位冲压就是将第一遍冲压以后的条料水平方向旋转180°,再冲第二遍,在第一次冲裁的间隔中冲裁出第二部分工件。
搭边值取2.5mm和3.5mm,条料宽度为135mm,步距离为53mm,一个