中厚板TMCP生产技术现状及发展.docx
《中厚板TMCP生产技术现状及发展.docx》由会员分享,可在线阅读,更多相关《中厚板TMCP生产技术现状及发展.docx(9页珍藏版)》请在冰豆网上搜索。
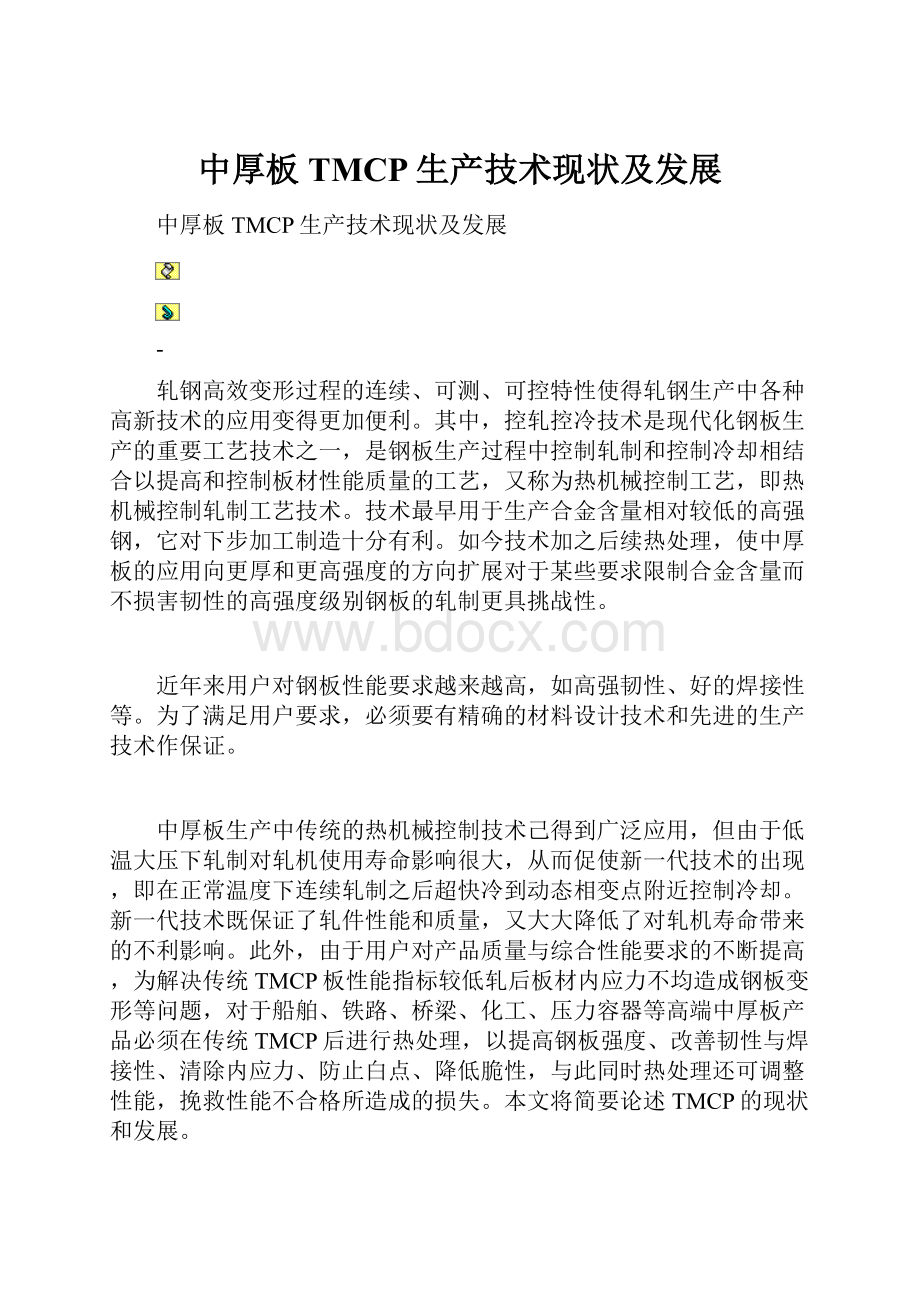
中厚板TMCP生产技术现状及发展
中厚板TMCP生产技术现状及发展
-
轧钢高效变形过程的连续、可测、可控特性使得轧钢生产中各种高新技术的应用变得更加便利。
其中,控轧控冷技术是现代化钢板生产的重要工艺技术之一,是钢板生产过程中控制轧制和控制冷却相结合以提高和控制板材性能质量的工艺,又称为热机械控制工艺,即热机械控制轧制工艺技术。
技术最早用于生产合金含量相对较低的高强钢,它对下步加工制造十分有利。
如今技术加之后续热处理,使中厚板的应用向更厚和更高强度的方向扩展对于某些要求限制合金含量而不损害韧性的高强度级别钢板的轧制更具挑战性。
近年来用户对钢板性能要求越来越高,如高强韧性、好的焊接性等。
为了满足用户要求,必须要有精确的材料设计技术和先进的生产技术作保证。
中厚板生产中传统的热机械控制技术己得到广泛应用,但由于低温大压下轧制对轧机使用寿命影响很大,从而促使新一代技术的出现,即在正常温度下连续轧制之后超快冷到动态相变点附近控制冷却。
新一代技术既保证了轧件性能和质量,又大大降低了对轧机寿命带来的不利影响。
此外,由于用户对产品质量与综合性能要求的不断提高,为解决传统TMCP板性能指标较低轧后板材内应力不均造成钢板变形等问题,对于船舶、铁路、桥梁、化工、压力容器等高端中厚板产品必须在传统TMCP后进行热处理,以提高钢板强度、改善韧性与焊接性、清除内应力、防止白点、降低脆性,与此同时热处理还可调整性能,挽救性能不合格所造成的损失。
本文将简要论述TMCP的现状和发展。
1.TMCP技术的现状及发展
应用TMCP技术可生产出综合机械性能和焊接性能均优良的高强度焊接结构钢板,该工艺技术已成为近几年来中厚板生产领域最为核心的工艺技术。
TMCP技术已被各国所普遍认可。
1.1TMCP技术现状
传统TMCP技术见图是将钢坯加热到1150-1050℃温度,在再结晶区或未再结晶区给予大压下进行轧制,然后再根据轧件的不同,进行不同温度区段的冷却。
通常根据不同钢种,控制钢板950℃-600℃温度范围的变形量,达到奥氏体状态的控制和进一步由这种受控态奥氏体发生相变的控制。
目的是改善钢板组织状态,细化奥氏体晶粒,使碳化物在冷却过程中于铁素体中弥散析出,提高钢板强度和综合机械性能。
传统TMCP技术利用添加微合金元素来扩大未再结晶区,采用低温大变形产生硬化奥氏体通过加速冷却控制硬化奥氏体相变。
但是传统TMCP技术的不足是低温大压下轧制,轧机受力过大,降低了轧机的使用寿命,因此发展出新一代TMCP技术。
1.1TMCP技术的发展
为了弥补传统TMCP技术的不足,根据TMCP技术特点创新出新一代TMCP技术见图。
新一代技术开始应用阶段主要用于生产高强度造船钢板和长距离输送石油、天然气用管线钢板,以及其它用途的高强度焊接结构钢板。
近年来,又开发出了应用于LPG储罐和运输船用钢板、高层建筑用厚壁钢板、海洋构造物等重要用途的钢板。
以造船板、管线用钢板、焊接结构钢板等产品为主的厚钢板,在钢铁发达国家采用新一代TMCP技术生产的约占30-50%新一代TMCP技术思路归纳为以下几点。
1.2.1减量化
新一代钢铁材料的开发,尽量少地添加合金元素或微合金化元素,以达到生产高性能钢材的目的。
高强度、高塑性及高吸能潜力的先进高强度钢(AHSS-AdvancedHighStrengthSteel),如双相钢(DP-DualPhase)和相变诱导塑性钢(TRIP-TransformationInducedPlasticity)在汽车工业中己得到广泛应用。
其中AHSS钢强化机理依赖相变及软硬相的复杂结合来达到所需的性能。
1.2.2连续大压下及超快冷
正常轧制温度下进行连续大压下轧制时,由于不断连续变形的大变形应变积累使奥氏体得到硬化随后进行冷速高达300-400℃/s的超快速冷却(UFC-UltraFastCooling),一方面保持硬化奥氏体不变,即“冻结”了硬化的奥氏体另一方面UFC还促进了20nm以下细小粒子的大量析出并且随着超快速冷却温度的不断降低,粒子分布更加弥散。
由于采用了超快速冷却,从而提高了形核率,细化了铁素体晶粒。
保持超快冷状态到相变点附近停止冷却,随后进行冷却路径控制,得到具有优良性能的不同组织钢板。
1.2.3控制冷却路径
轧件变形后瞬时进入冷却区,实施快速或超快速冷却,以及动态相变点附近冷却路径的控制是新一代TMCP技术的核心之一。
冷却过程的相变取决于温度、钢板运行速度、厚度、冷却水压、冷却速度和冷却时间等。
同时相变热的释放也会对其产生影响。
通过冷却对硬化奥氏体相变过程进行控制,实现细晶强化和相变强化。
对于热连轧,轧制阶段可改变因素较少,所以把轧后冷却的控制作为重点。
根据不同用户对钢板性能的不同要求,利用控制冷却路径来控制硬化奥氏体的相变,得到多相或双相同比例的不同组织,实现对钢的相变强化,缩短相变时间。
例如强度要求不是很高的钢,冷却到动态相变点附近时,采用一定的冷却速度得到铁素体钢(冷却路径见图2的a);当强韧性要求都较高时,可采用较大冷速进入贝氏体区,得到贝氏体组织(冷却路径见图2的b);如果对强度要求很高的钢采用更大冷却速度,得到马氏体钢(冷却路径见图2的c)
图1传统TMCP技术示意图
图2新一代TMCP技术示意图
1.3传统TMCP与新一代TMCP技术对比
1.3.1轧制区间不同
新一代TMCP技术采用再结晶区范围内的正常轧制温度轧制,传统TMCP技术在较低温度的未再结晶区轧制。
1.3.2轧后内部应力不同
新一代TMCP技术采用正常温度下连续轧制。
由于温度高,使积累的位错可以进行滑移和析出,高能状态应力得以释放而传统TMCP技术采用的是低温大压下轧制(见图3),位错聚集,造成内部应力集中,不能释放。
图3新旧TMCP工艺对比
1.3.3相变机理不同
新一代TMCP技术的相变是一种动态相变,相变发生在变形过程中和相变后短时内,它是形核控制相变,从界面形核开始,在连续热变形、连续应变能积累和释放过程中晶核在高时变区(应变带、滑移带、孪晶带、亚结构界面)不断反复形核,具有“形核位置不饱和”机制:
相变速率快,可产生等轴低位错密度的超细亚铁素体。
而传统TMCP技术的相变主要发生在变形后的连续冷却过程中。
1.3.4控制冷却能力的不同
传统TMCP技术是在相变电附近轧制,冷却途径只有一条,其冷却途径必能控制,而新一代TMCP技术可以根据用户对钢板组织与性能的要求,控制冷却路径和所需组织,可以设计多条冷却路径,而且比传统加速冷却速度快2-5倍,的到得钢板强度提高,焊接性改善,且处理后钢板表面的温度非常均匀。
2.结束语
我国中厚钢板TMCP生产技术已有了长足发展,还在不多开拓和完善,为满足高端中厚板产品高性能指标要求,必须对TMCP板进行后续热处理,得到均匀一致的组织利性能,随着工艺和设备的不断改进,中厚钢板的性能和质量奖会进一步提高。