冲压件设计指导.docx
《冲压件设计指导.docx》由会员分享,可在线阅读,更多相关《冲压件设计指导.docx(32页珍藏版)》请在冰豆网上搜索。
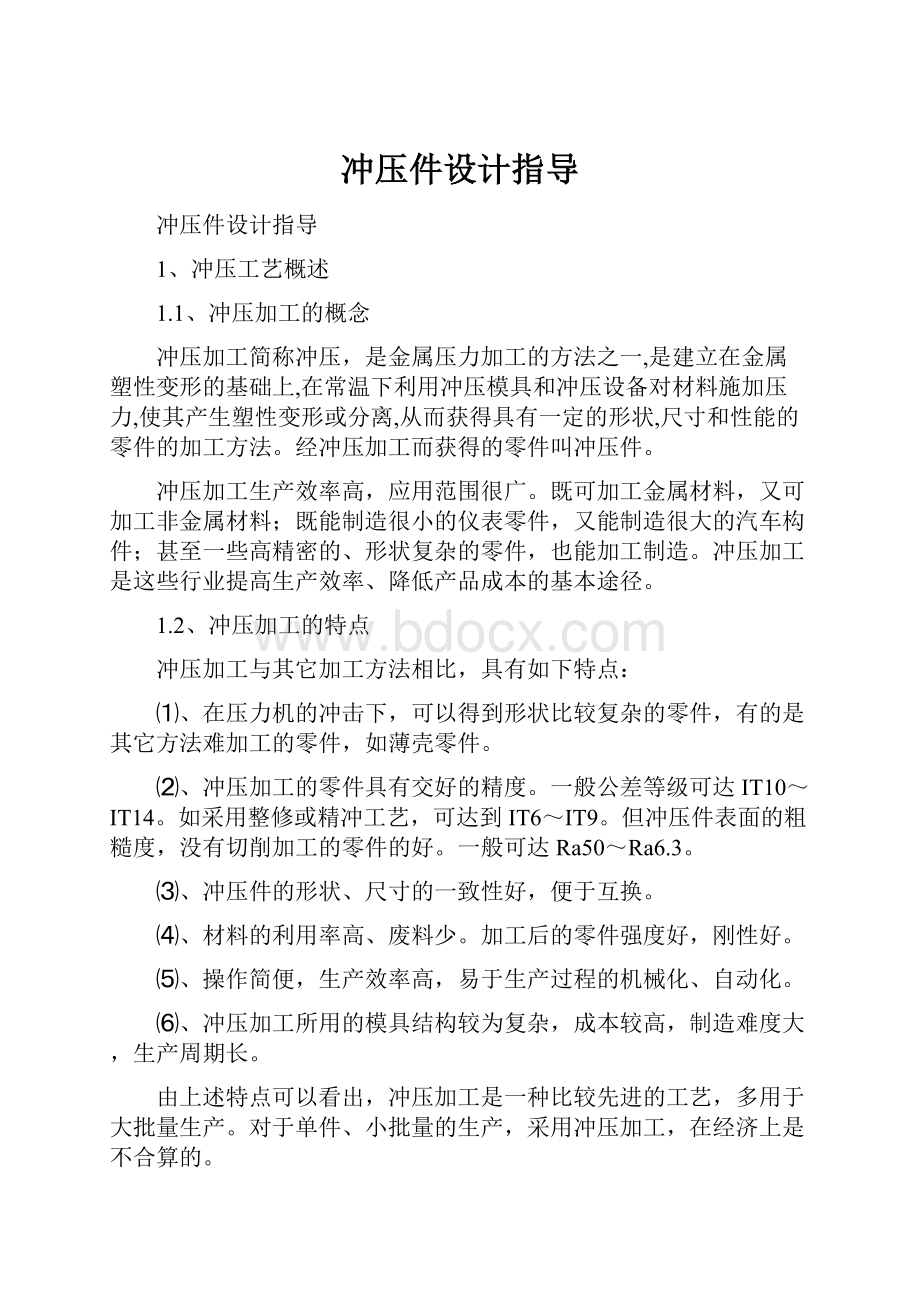
冲压件设计指导
冲压件设计指导
1、冲压工艺概述
1.1、冲压加工的概念
冲压加工简称冲压,是金属压力加工的方法之一,是建立在金属塑性变形的基础上,在常温下利用冲压模具和冲压设备对材料施加压力,使其产生塑性变形或分离,从而获得具有一定的形状,尺寸和性能的零件的加工方法。
经冲压加工而获得的零件叫冲压件。
冲压加工生产效率高,应用范围很广。
既可加工金属材料,又可加工非金属材料;既能制造很小的仪表零件,又能制造很大的汽车构件;甚至一些高精密的、形状复杂的零件,也能加工制造。
冲压加工是这些行业提高生产效率、降低产品成本的基本途径。
1.2、冲压加工的特点
冲压加工与其它加工方法相比,具有如下特点:
⑴、在压力机的冲击下,可以得到形状比较复杂的零件,有的是其它方法难加工的零件,如薄壳零件。
⑵、冲压加工的零件具有交好的精度。
一般公差等级可达IT10~IT14。
如采用整修或精冲工艺,可达到IT6~IT9。
但冲压件表面的粗糙度,没有切削加工的零件的好。
一般可达Ra50~Ra6.3。
⑶、冲压件的形状、尺寸的一致性好,便于互换。
⑷、材料的利用率高、废料少。
加工后的零件强度好,刚性好。
⑸、操作简便,生产效率高,易于生产过程的机械化、自动化。
⑹、冲压加工所用的模具结构较为复杂,成本较高,制造难度大,生产周期长。
由上述特点可以看出,冲压加工是一种比较先进的工艺,多用于大批量生产。
对于单件、小批量的生产,采用冲压加工,在经济上是不合算的。
应当指出,并不是所有的零件都可以采用冲压加工。
冲压件的加工,要满足冲压工艺性的要求,即零件对冲压加工的适应性。
1.3、冲压加工的种类
由于冲压加工零件的形状、尺寸、精度要求以及批量的大小,原材料性能等的不同,常采用的冲压加工方法多达二、三十种。
但根据板料在冲压过程中的受力和变形的情况,冷冲压工序基本上可以分为两大类型:
即分离工序和变形工序。
有时,为了进一步提高冲压加工的生产效率,常常将两个以上的基本工序合并为一个工序,称为复合工序。
⑴、分离工序
材料受力后,变形部分的应力超过材料的强度极限,材料中的一部分沿着一定轮廓与另一部分分离,称为分离工序。
也称冲裁工序。
常见的冲裁工序如下表所示。
名称
定义
裁剪
将板料用剪刀或冲模沿不封闭的切断线切断
落料
将板料沿封闭的曲线分离,冲落的部分为工件
冲孔
将板料沿封闭的曲线分离,冲落的部分为废料
切口
将板料沿不封闭的曲线切口,并且切口的部分弯曲
修整
将工件边缘预留的加工余量去除,从而获得高精度及光滑的表面
⑵、变形工序
材料受力后,变形部分的应力超过材料的屈服极限,但没有超过材料的强度极限,材料产生了塑性变形,改变其形状和尺寸,称为变形工序。
常见的变形工序如下表所示。
名称
定义
弯曲
将板料弯曲成一定的角度和形状
卷圆
将板料的端部卷圆
卷边
将空心件的边缘卷成一定的形状
扭曲
将制件扭转成一定的角度
拉延
将平板状毛坯制成空心、开口的筒形零件
起伏(压筋)
将板料局部成形,形成起伏不平的花纹
缩口/胀形
对空心件的内部或外部加压,使其壁部局部径向扩大或缩小。
翻孔
将制件上的孔翻出一定高度的直边
翻边
将制件的边缘翻出一定高度的圆弧或曲线形状的直边
校平
将毛坯或已成形工件的不平的面,在模具中压平
整形
将形状不太准确的制件校正成形
压印
在制件上压出文字或花纹,只在制件厚度的一个平面上有变形
⑶、复合工序
冲压工艺中,在一道工序、即在一副模具内,完成上述工序的一种,称为单工序。
如冲孔工序、落料工序等。
在一道工序内,同时完成上述工艺中的两种或两种以上的工艺,称为复合工序。
如冲孔—落料的复合工序、冲孔—落料—拉延的复合工序等。
1.4、一般原则
⑴、冲压件设计应合理,形状尽量简单、规则和对称,以节省原材料,减少制造工序,提高模具寿命,降低工件成本。
⑵、形状复杂的冲压件可考虑分成数个简单的冲压件再用连接方法制成。
⑶、以下给出的结构尺寸限制是根据工件质量和经济效益规定的。
2、冲压件材料的选用
冲压件所用的材料,不仅要适合零件的工作条件,而且要适合冲压过程中材料变形特点及变形程度所决定的制造工艺要求。
即应具有足够的强度和较高的可塑性。
选用的原则:
⑴、对于拉深及复杂的弯曲件应选用成型性好的材料。
⑵、对于弯曲件,应考虑材料的弯曲方向。
⑶、在保证产品质量的前提下,尽量降低所使用的材料的价格。
用薄料代替厚料;用钢铁代替非铁金属;能用碳钢的就不用合金钢,能用低合金钢的就不用高合金钢,能用普通钢的就不用不锈耐热钢,这对批量大的零件来说就显得更重要。
⑷、考虑后续工序的要求,如冲压后需要焊接、涂漆、镀膜处理的零件,应选用酸洗钢板。
⑸、在选用材料时,还应尽量立足于国内条件和国家资源,同时应尽量减少材料的品种、规格等,这些都直接影响到材料的经济性。
适合普通冲压的材料见表1,适合于精密冲压的材料见表2。
表1普通冲压的材料
冲压件类别
材料的力学性能
常用材料
抗拉强σb﹙MPa﹚
伸长率δ
﹙%﹚
硬度
﹙HRB﹚
平板冲裁件
﹤637
1~5
84~96
Q195、电工硅钢
冲裁件
弯曲件(以圆角半径R>2t作90°垂直于轧制方向的弯曲)
﹤490
4~14
76~85
Q195、Q275、40、45、65Mn
浅拉深件
成形件
弯曲件(以圆角半径R>0.5t作90°垂直于轧制方向的弯曲)
﹤412
13~27
64~74
Q215、Q235、15、20
深拉深件
弯曲件(以圆角半径R<0.5t作任意方向180°的弯曲﹚
﹤363
24~36
52~64
08F、08、10F、10
复杂拉延件
弯曲件﹙以圆角半径R<0.5t作任意方向180°的弯曲﹚
﹤324
33~45
38~52
08Al、08F
表中t为板料的厚度。
表2精密冲压的材料
钢铁﹙黑色金属﹚
非铁金属﹙有色金属﹚
普通碳素结构钢:
Q195、Q215、Q235、Q275
黄铜:
H62、H68、H70、H80、锡黄铜、铝黄铜、镍黄铜均可进行精冲。
青铜:
锡青铜、铝青铜、铍青铜都可精冲。
铜:
T1、T2、T3。
无氧铜:
TU1、TU2。
优质碳素结构钢:
°5、08、10~60
但含碳量超过0.4%的碳钢,需经球化退火后再精冲。
低合金钢和合金钢﹙经球化退火后σb<588MPa的均可精冲﹚
纯铝:
1070A~8A06。
防锈铝:
5A01~5A06,5B05等经淬火时效处理,在时效期内均可精冲。
不锈钢及经球化退火的合金工具钢也可精冲。
3、冲裁
3.1、冲裁的概念
冲裁是指利用冲模在冲压机上使材料分离的冲压工艺,是落料、切料、冲孔、切边、切口等分离工序的总称。
3.2、冲压件的工艺性的概念
冲压件的工艺性是指零件在冲切、弯曲、成形、拉伸加工中的难易程度。
良好的工艺应保证材料消耗少,工序数目少,模具结构简单、使用寿命高,产品质量稳定。
在一般情况下,对冲压件工艺性影响最大的是材料的性能、零件的几何形状、尺寸和精度要求。
3.3、冲裁件的结构要素
⑴、圆角半径
冲裁件的外形和内孔应避免的直角,宜有适当的圆角,以防止模具过度磨损。
一般圆角半径R应大于或等于板厚t的一半,既R≥0.5t(见下图)。
冲切缺口应尽量避免尖角。
尖角形式容易减短模具的使用寿命,且尖角处容易产生裂纹。
①、精冲件的最小圆角半径见下表。
料厚(毫米)
工件的轮廓角度α
30°
60°
90°
120°
1
0.4
0.2
0.1
0.05
2
0.9
0.45
0.23
0.15
3
1.5
0.75
0.35
0.25
4
2
1
0.5
0.35
5
2.6
1.3
0.7
0.5
6
3.2
1.6
0.85
0.65
8
4.6
2.5
1.3
1
10
7
4
2
1.5
12
10
6
3
2.2
14
15
9
4.5
3
15
18
11
6
4
注:
上表中的数值适用于抗拉强度低于441MPa的材料,强度高于此值时应按比例增加。
⑵、冲孔尺寸
优先选用圆形孔.冲孔的最小尺寸与孔的形状、材料机械性能和材料厚度有关,自由凸模冲孔的直径d或边宽a按下表的规定。
冲孔材料
孔的形状
2Cr13不锈钢板
钢δb>70×107帕(高碳钢)
钢δb(40—70)×107帕(中碳钢)
钢δb<40×107帕(低碳钢)
铜、黄铜
铝、锌
布质胶木层压板
d≥2.0t
d≥1.5t
d≥1.3t
d≥1.0t
d≥0.9t
d≥0.8t
d≥0.4t
a≥2.0t
a≥1.35t
a≥1.2t
a≥0.9t
a≥0.8t
a≥0.7t
a≥0.35t
a≥1.8t
a≥1.1t
a≥0.9t
a≥0.7t
a≥0.6t
a≥0.5t
a≥0.3t
a≥1.8t
a≥1.2t
a≥1.0t
a≥0.8t
a≥0.7t
a≥0.6t
a≥0.3t
⑶、凸出和凹入尺寸
冲裁件上应避免窄长的悬臂和凹槽。
一般凸出和凹入部分A应大于或等于板厚t的一倍半,即A≥1.5t。
对高碳钢、合金钢等较硬材料允许值应增加30%~50%,对黄铜、铝等软材料应减少20%~25%。
①、工件上不能有过长的悬臂和窄槽,以防止模具的强度和刚度不足,也要避免深度过浅的浅槽。
见下表。
对一般钢A≥1.5t
对合金钢A≥2t
对黄铜、铝A≥1.2t
t—材料厚度。
②、冲裁件的最小许可宽度与材料的关系见下表。
材料
最小值
B1
B2
B3
中等硬度钢
1.25t
0.8t
1.5t
高碳钢和合金钢
1.65t
1.1t
2t
有色金属
1.0t
0.6t
1.2t
③、精冲件的最小相对槽宽e/t见下表。
料厚t(㎜)
长度l(毫米)
2
4
6
8
10
15
20
40
60
80
100
150
200
1
0.69
0.78
0.82
0.84
0.88
0.94
0.97
1.5
0.62
0.72
0.75
0.78
0.82
0.87
0.90
2
0.58
0.67
0.70
0.73
0.77
0.83
0.86
1.0
3
0.62
0.65
0.68
0.71
0.76
0.79
0.92
0.98
4
0.60
0.63
0.65
0.68
0.74
0.76
0.88
0.94
0.79
1.0
5
0.62
0.64
0.67
0.73
0.75
0.86
0.92
0.95
0.97
8
0.63
0.66
0.71
0.73
0.85
0.9
0.93
0.95
1.0
10
0.68
0.71
0.80
0.85
0.87
0.88
0.93
0.96
12
0.70
0.79
0.84
0.86
0.87
0.92
0.95
15
0.69
0.78
0.83
0.85
0.86
0.90
0.93
⑷、孔边距和孔间距
孔边距A应大于或等于板厚t的二倍,即A≥2t(下图)。
孔间距B应大于或等于板厚t的二倍,即B≥2t(下图)。
①、孔距、孔边距(孔的位置)的要求见下表。
简图
最小距离
c>t
c>0.8t
c>1.3t
c>t
c>0.7t
简图
最小距离
c>1.2t
c>1.5t
k≥R+d/2
d<D1-2R;D>(D1+2t+2R+d1)
h>2d+t
⑸、端头圆弧尺寸
用调料冲制端头带圆弧的工件,其圆弧半径R应大于条料宽度B(含正偏差)的一半(下图),即R>B/2。
⑹、冲裁件的形状应尽量简单、对称。
⑺、冲裁件的尺寸精度不能要求太高。
①、平冲裁件(经平面冲裁工序加工而形成的冲压件)分为普通冲裁和精密冲裁,其尺寸公差等级分为ST1~ST11级。
按照《GB/T13914冲压件尺寸公差》标准执行。
②、冲裁件的冲裁角度(平冲压件或成型冲压件平面部分,经冲裁工序加工而成的角度)公差等级分为AT1~AT6级。
按照《GB/T13915冲压件角度公差》标准执行。
③、冲裁件(冲压件)的未注公差按照《GB/T15055冲压件未注公差尺寸极限偏差》标准执行。
④、冲裁件(冲压件)的形状和位置公差按照《GB/T13916冲压件形状和位置未注公差》标准执行。
⑤、、剪切面的表面粗糙度Ra为3.2~50微米。
⑥、、工件边缘的毛刺高度应小于0.05~0.15毫米。
⑻、冲裁件结构设计的注意事项
序号
图例
注意事项
改进前
改进后
落料件
节约金属
合理设计工件形状,以利于节料
避免尖角
工件如有细长尖角,易产生飞边或塌角
工件不宜过窄
工件太窄,冲模制造困难且寿命低
开口槽不宜过窄
B=2R
B<2R
圆弧边与过渡边不宜相切
节约金属和避免咬边
落料时必须注意:
刀口方向,必须是部件装配的正面落刀,在图纸上必须注明装配面。
切口件
切口处应有斜度
避免工件从凹模中退出时舌部与凹模内壁摩擦
4、弯曲
4.1、弯曲的概念
⑴、概念
弯曲是变形工序的一种,是将板料(杆料、管料)弯曲成所需的角度或形状的一种加工方法。
弯曲的方式很多,有手工弯曲成型(称为板金加工),有用折弯机、压弯机、滚弯机、拉弯机成型和在专用弯曲模上成型等数种。
本文讲述在冲床上利用模具进行弯曲的工艺。
4.2、弯曲件的结构要素
⑴、一般原则
②、弯曲件在弯曲变形区截面会产生变化,弯曲半径与板厚之比愈小,截面形状变化愈大。
②、弯曲件的弯曲线最好垂直于轧纹方向。
弯曲毛坯的光亮带最好作为弯曲件的外沿,以减少外层的拉裂。
③、弯曲成形时会产生回弹现象;弯曲半径与板厚之比愈大,回弹就愈大。
⑵、弯曲半径
弯曲件的弯曲半径r标注在内半径上。
a)、建议选取以下弯曲半径:
0.5;1;1.6;2;2.6;3;4;5;6;8;10;12;16;20;25;28;32;36;40;45;50;63;80;100mm。
b)、最小弯曲半径
①、最小弯曲半径的概念
在弯曲过程中,材料的外层纤维受拉,当材料的厚度一定时,弯曲半径r越小,则外层所受的拉力越大。
当弯曲半径r小到一定的程度时,弯曲件的外层会出现裂纹或破裂。
我们把材料弯曲变形时出现破坏与折断时的最小弯曲半径称为材料的最小弯曲半径。
常用材料允许的最小弯曲半径的数值见下表。
材料
弯曲线的位置
垂直于轧制方向
平行于轧制方向
08、10、Q195、Q215
0.3t
0.8t
15、20、Q235
0.5t
1.3t
30、40、Q235
0.8t
1.5t
45、50、Q275
1.2t
3.0t
25CrMnSi、30CrMnSi
1.5t
4.0t
60Mn、T8
1.2t
2.0t
紫铜
0.1t
0.35t
软黄铜和铜
0.3t
0.8t
黄铜(半硬)
0.5t
1.2t
铝
0.35t
1.0t
半硬铝
1.0t
1.5t
硬铝
2.0t
3.0t
注:
1)、当弯曲线与轧制方向成一定的角度时,按角度的大小,取表中两者之间的数值。
2)、表中的数值适用于冲件的毛刺在弯角内层的弯曲,毛刺在弯角外层时,应放大弯曲半径。
3)、t为材料的厚度(毫米)。
②、影响最小弯曲半径的因素
影响材料的最小弯曲半径的因素很多,主要有:
a、材料的机械性能:
塑性好的材料,允许的最小弯曲半径就小。
b、材料的几何形状及尺寸:
弯曲的板料越宽、越厚,则最小弯曲半径增大,弯曲程度减小。
板料越窄、越薄,则最小弯曲半径减小,弯曲程度增大。
c、工件弯曲角θ的大小:
当弯曲角θ大于90°时,对材料的最小弯曲半径的影响不明显,而当弯曲角θ小于90°时,最小弯曲半径随着弯曲角的减小而减小。
d、弯曲线的方向:
冷冲压所用的金属板料,存在着机械性能的异向性。
一般来说,钢板在纵向(轧制方向)的塑性比在横向(宽度方向)上要好。
所以弯曲线垂直于轧制方向时,允许有最小的弯曲半径,而弯曲线平行于轧制方向时,则允许的最小弯曲半径的数值要大。
⑶、弯曲件的工艺性审查
弯曲件的形状除了要满足使用的要求以外,还应该具有良好的结构工艺性,在设计弯曲件时,除了要考虑弯曲半径的大小、弯曲形状是否对称以外,还应考虑以下几个问题。
①、弯曲件直边的高度。
弯曲件直边的高度1H应大于2倍的料厚t,否则不易成型。
如果工件的直边高度小,常用在弯曲线处压工艺槽的方法来减少料厚(设计上的措施)。
或增加直边高度,弯曲后再将加高的部分去除(工艺上的措施)。
直角弯曲件的最小高度h应大于弯曲半径r加上板厚t的2倍(下图),即h>r+2t。
②、在弯曲变形区及其附近的斜面或孔。
在弯曲线附近如有斜面,如下图(b)中的A处,则使弯曲不易进行。
可将斜面改成该图B处的直边。
在弯曲变形区附近如有孔,则在弯曲过程中孔会产生变形。
应使孔边到弯曲区的距离大于(1~2)t,如下图(c)所示,或在弯曲区加工艺孔,使变形区产生在工艺孔内,如下图(d)所示。
③、增加必要的工艺孔或工艺槽。
弯曲件上某些不易成形或弯曲、且易开裂的部位,如图(a)、(b)中的A处,可在弯曲处增加一个工艺孔或给以槽如B处,从而使弯曲容易进行。
(a)(b)
在U形弯曲件上,两弯曲边最好等长,以免弯曲时产生向一边的移位。
如不允许,可设一工艺定位孔,如下图。
④、增加连接带(工艺上的措施)。
弯曲件弯曲变形区的侧面边缘如有缺口,会使缺口部分不易成形。
一般可在缺口处增加连接带,使整个弯曲区成为一个整体,弯曲成形后再将这个连接带冲掉,如下图。
⑤、弯曲件的的弯曲线不应位在尺寸突变的位置,离突变处的l应大于弯曲半径r,即即l>r(图a);或切槽或工艺孔,将变形区与不变形区分开(图b)。
ab
⑥、工艺切口:
直角弯曲件或板厚小圆角,为防止弯曲区宽度变化,推荐预先冲制切口(下图)。
⑷、弯曲件的尺寸精度
弯曲件(成形冲压件)(经弯曲、拉深及其他成形方法加工而成的冲压件)的尺寸公差分为10个等级,即FT1—FT10。
按照《GB/T13914-2002冲压件尺寸公差》标准执行。
弯曲件的角度公差分为5个等级,即BT1~BT5级,按照《GB/T13915-2002冲压件角度公差》标准执行。
弯曲件的未注公差按照《GB/T15055-2007冲压件未注公差尺寸极限偏差》标准执行。
弯曲件的形状和位置公差按照《GB/T13916-2002冲压件形状和位置未注公差》标准执行。
⑸、弯曲件结构设计的注意事项
序号
图例
注意事项
改进前
改进后
弯曲件
弯曲处切口
窄料小半径弯曲时,为防止弯曲处变宽,工件弯曲处应有切口
预冲月牙槽
弯曲带孔的工件时,如孔在弯曲线附近,可预冲出月牙槽或孔,以防止孔变形
预冲防裂槽
在局部弯曲时,预冲防裂槽或外移弯曲线,以免交界处撕裂
形状尽量对称
弯曲件形状尽量对称,否则工件受力不均,不易达到预定尺寸
弯曲部分压筋
可增加工件刚度,减小回弹
坯料形状简单
工件外形利于简化展开料形状
弯曲部分进行预切
防止弯曲部分起皱
5、拉延
5.1、拉延的概念
⑴、概念
拉延有称压延、拉伸或引伸,是变形工序中的一种,是以板料或筒形(或其它断面形状)件为毛坯,利用拉延模再制成筒形(或其他断面形状)零件的一种加工方法。
⑵、拉延件的种类
在冲压加工中,拉延件的种类很多,大致可分为以下几类:
①、圆筒形直壁旋转体件。
如直壁筒形件、带凸缘的圆形件和阶梯形件等。
②、曲面旋转体件。
如球形件和锥形件等。
③、直壁非旋转体盒形件。
如正方、长方盒形件及带凸缘的方盒件等。
④、非旋转体复杂曲面工件。
5.2、拉延件的工艺性
拉延件在满足使用要求的前提下,还应满足拉延的工艺要求。
⑴、拉延件的材料塑性要好,屈强比要小,厚度方向性系数要大。
这样拉延变形容易,也不至于破坏。
⑵、凸缘和底部圆角半径不能太小,否则拉延变形困难。
凸缘的大小要适当,凸缘过大,不容易产生变形。
凸缘过小,拉延时容易起皱。
凸缘的形状最好与筒体形状相似。
各部位的尺寸见下表。
R1、R2
材料
圆角半径
材料厚度t(毫米)
<0.5
>0.5~3
>3~5
软钢
R1
(5~7)t
(3~4)t
(2~3)t
R2
(5~10)t
(4~6)t
(2~4)t
黄铜
R1
(3~5)t
(2~3)t
(1.5~2)t
R2
(5~7)t
(3~5)t
(2~4)t
H/R0
当R0>0.14B
R1>1时
材料
比值
酸洗钢
4.0~4.5
当H/R0需大于左列数值时,则应采用多次拉延工序。
冷拉钢、铝、黄铜、铜
5.5~6.5
B
≤R2+(3~5)t
R3
≥R0+B
⑶、圆形拉延件的孔径和孔距应符合下表的要求。
底部孔径d1
d1≤d−2r1−t
孔距D1
D1≥d=3t+2r2+d2
壁上的冲孔中心与底部或凸缘边的距离h
h≥2d+t
⑷、拉延件的壁厚是由边缘向底部逐渐减薄的(大约从1.2t减到0.8t),因此对拉延件的尺寸标注,应仅标注外形尺寸或内形尺寸和毛坯的板料厚度,不能同时标注外形尺寸和内形尺寸及公差。
⑸、拉延件结构设计的注意事项
序号
图例
注意事项
改进前
改进后
拉深件
形状尽量简单并对称
圆筒形、锥形、球形、非回转体、空间曲面,成形难度依次增加
法兰边宽度应一致
拉伸困难,需增加工序,金属消耗大
法兰边直径过大
拉伸困难
5.3、拉延件的尺寸精度
拉延件的尺寸公差按照《GB/T13914-2002冲压件尺寸公差》标准执行。
拉延件的角度公差,按照《GB/T13915-2002冲压件角度公差》标准执行。
拉延件的未注公差按照《GB/T15055-2007冲压件未注公差尺寸极限偏差》标准执行。
拉延件的形状和位置公差按照《GB/T13916-2002冲压件形状和位置未注公差》标准执行。
6、成形
6.1、成形的概念
在冲压生产中,有些冲压件用冲裁、弯曲和拉延等工艺方法往往不能实现所需的最终形状,还需要配合翻边、起伏成形、缩口、胀形、校平、整形等工序。
这些冲压工序的共同特点是通过板料的局部变形来改变毛坯的形状,因此,统称为成形工序。
分别介绍如下:
⑴、翻边
翻边是在板料或筒形