整理973项目申报书CB724400超高速加工及其装备的基础研究.docx
《整理973项目申报书CB724400超高速加工及其装备的基础研究.docx》由会员分享,可在线阅读,更多相关《整理973项目申报书CB724400超高速加工及其装备的基础研究.docx(36页珍藏版)》请在冰豆网上搜索。
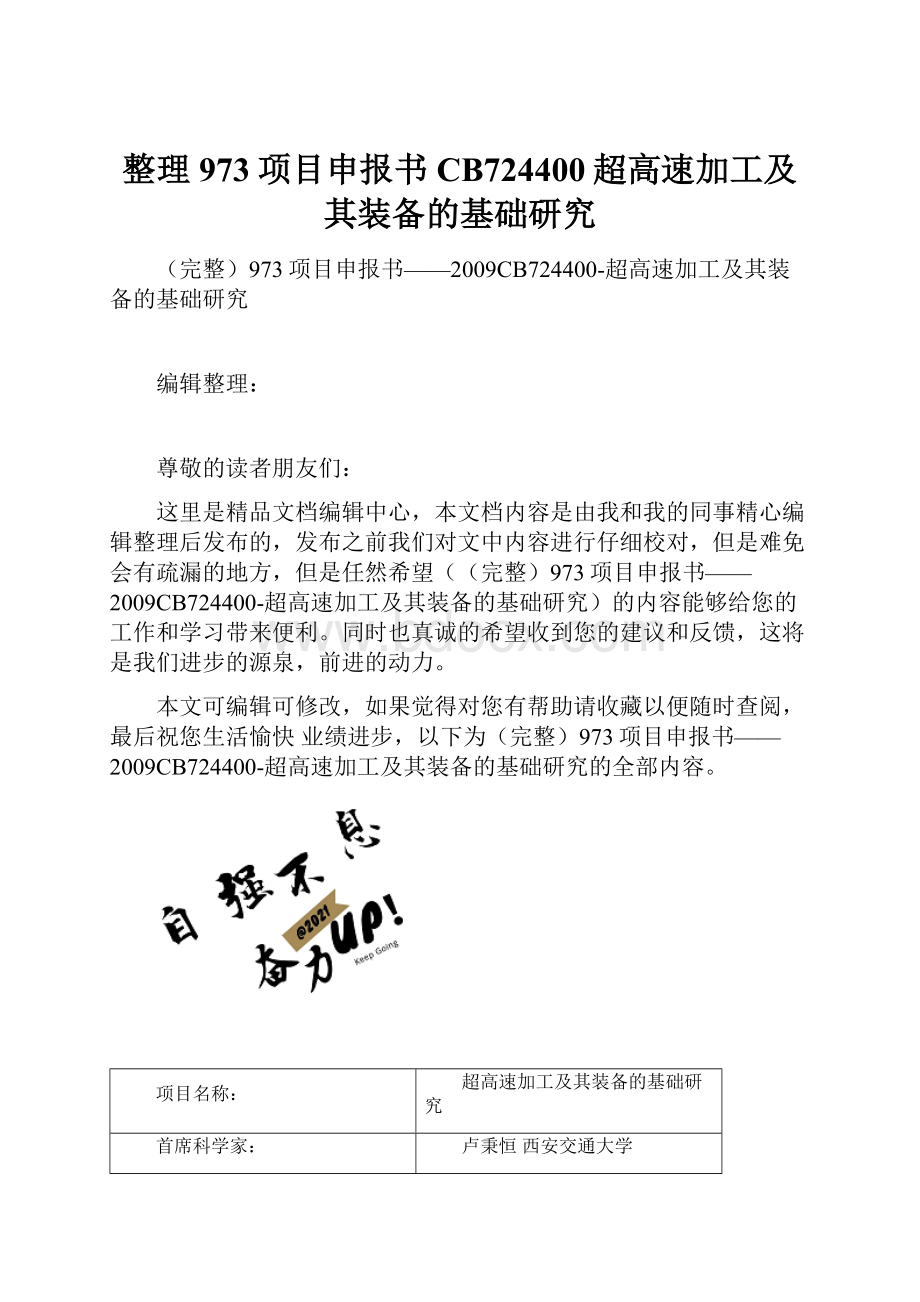
整理973项目申报书CB724400超高速加工及其装备的基础研究
(完整)973项目申报书——2009CB724400-超高速加工及其装备的基础研究
编辑整理:
尊敬的读者朋友们:
这里是精品文档编辑中心,本文档内容是由我和我的同事精心编辑整理后发布的,发布之前我们对文中内容进行仔细校对,但是难免会有疏漏的地方,但是任然希望((完整)973项目申报书——2009CB724400-超高速加工及其装备的基础研究)的内容能够给您的工作和学习带来便利。
同时也真诚的希望收到您的建议和反馈,这将是我们进步的源泉,前进的动力。
本文可编辑可修改,如果觉得对您有帮助请收藏以便随时查阅,最后祝您生活愉快业绩进步,以下为(完整)973项目申报书——2009CB724400-超高速加工及其装备的基础研究的全部内容。
项目名称:
超高速加工及其装备的基础研究
首席科学家:
卢秉恒西安交通大学
起止年限:
2009。
1至2013。
8
依托部门:
教育部
一、研究内容
超高速加工已经成为先进制造技术竞争的一个制高点。
超高速加工中,工件与刀具相互高速撞击,力的瞬态作用使剪切局限在一个微区域,能量在此微区的耗散使材料局部高温,可能达到熔化或接近熔化的状态。
正反馈效应使局部绝热剪切作用愈加增强.切削速度越高,这种绝热剪切作用也越强,接近音速的超高速切削走向极端条件,带来了诸多新机理研究和对传统切削机理的突破性挑战。
机床工作在数万转/分转速下承受冲击载荷,依然达到μ级的工作精度,要求实现机床主轴系统旋转的高精度高稳定性控制以及整机动静热特性的精确设计。
冲击载荷下,主轴的高刚度、高精度要求轴承工作间隙很小,在微间隙中轴承润滑介质受到强剪切与挤压,同样达到了一种极端的工况.机械装备大多工作在力热耦合状态下,现代CAE技术对连续的机械结构的特性预测已达到很高的精度.分析的困难发生在结构界面造成的不连续性。
因此,无论整机的结构设计,还是高速切削中,刀具与工件材料的强烈摩擦,以及高速轴承支承的工作表面与润滑介质的相互作用都存在界面强耦合作用问题。
本项目探索在多场耦合强作用条件下的材料剧变和去除的科学实质,阐明超高速加工工具的失效机理;揭示微约束空间、强剪切润滑介质支承系统的热、动力学行为规律,发现冲击载荷下,保证超高速主轴系统运行稳定性的条件;建立超高速机床结构界面的物理表征方法,实现高速机床整机系统耦合的精确建模与设计。
项目将形成我国自主的高速加工机床核心部件创新技术,建立高速加工技术及机床装备和工具设计制造的理论,实现加工速度向超高速阶段的跨越.
为此,本项目围绕下列三个重要科学问题开展研究工作:
科学问题一:
超高速加工多场强作用下的材料激变行为及其去除机理
Salomon高速切削(highspeedmachining,HSM或highspeedcutting,HSC)的理念提出以来,超越“热沟"、切削力和切削热同时下降的假设始终未得到验证.超高速加工过程中,被切材料与刀具以接近声速进行瞬间碰撞,材料的高速激烈应变和切屑的瞬间形成,工件材料的应变达到1—10,应变速率达到105-107/s,甚至更高,工件材料发生剧变,工件材料发生超强应变过程及工具-切屑-工件之间剧烈的摩擦学行为将导致在局部区域产生高温,工件材料接近或达到熔化状态,形成绝热剪切.在这些极端工作状态下,工件材料被软化剥离去除而形成高精度、高光洁表面。
工件材料有时发生塑脆或脆塑转变,传统金属切削加工的剪切滑移理论已很难适用超高速切削的研究。
揭示超高速切削的机理,探明其科学实质,不仅是对传统切削理论的突破,同时可实现切削速度的跨越,从而获得更高的制造效率和更高的加工质量,降低能耗,并为解决高速加工工具的设计、使用以及最佳工艺选择提供理论依据.
主要研究内容如下:
1)多场耦合强作用下超高速加工的切削学行为
建立超高速切削的实验平台,捕捉切削的瞬态过程,通过对超高速切削过程的实验分析,研究切屑形成的机理,探索所发生的力学、物理与化学行为的本质,揭示多场强作用超高速切削过程的科学实质,形成对超高速切削加工的切削学行为认识的突破,重点研究:
●超高速切削加工过程多场强作用的形成机制
●工件材料高应力、高应变、高应变率和高温动态行为变化规律
●多场强作用超高速加工过程的材料去除机理
●多场强作用超高速切削加工表面层材料学行为及其演变
●超高速切削摩擦学行为的非线性特征及其控制
2)超高速切削刀具的跨尺度设计理论
超高速切削过程中,刀具在热-力-化学等强场作用下是如何损伤失效的?
刀具材料的宏观性能与微观结构是如何跨尺度关联的?
如何设计可靠长寿命工作的超高速刀具材料与刀具结构?
如何根据工件材料及切削条件合理选择刀具材料?
通过研究高性能梯度功能陶瓷刀具材料、纳米复合陶瓷刀具材料、金属陶瓷刀具材料及其强韧化机理,自润滑刀具、新型涂层刀具及其润滑、减摩机理,揭示在超高速切削条件下,刀具材料微观结构与宏观性能的跨尺度关联关系,探索刀具材料失效机理与刀具可靠性,提供高可靠性和长寿命的超高速切削刀具设计原理及创新设计,重点研究:
●超高速切削刀具材料微观结构与宏观性能关系
●超高速刀具材料损伤行为演变过程和失效机理
●超高速刀具材料和工件材料性能的匹配性
●基于多场强作用和切削可靠性的刀具材料设计理论
●超高速多齿回转刀具的切削均匀性和可靠性
3)超高速磨削机理与磨粒有序排布砂轮
超高速磨削中,工件材料与负前角的磨粒之间剧烈摩擦,瞬间产生大量热,来不及扩散的磨削热局限在一个微区内,对工件表面的局部加热,可能造成材料去除抗力及磨削热的同时降低。
通过单磨粒及砂轮磨粒仿真分析、统计分析与实验,揭示磨削热的产生、耗散规律,揭示磨削应力及磨削热的空间分布特征;研究磨削力(或磨削力比)、磨削比能和材料的临界成屑厚度之间的关系,揭示力、热耦合对材料去除的影响机理,阐明超高速磨削的“热沟”机理;研究磨削热对工件及砂轮的效应,从而获取充分降低切削抗力的工艺参数,恰当利用磨削热对工件实施空冷淬火,指导砂轮的安全设计,重点研究:
●超高速磨削的材料激变行为及去除机理
●超高速磨削热生成及磨削弧区的强化传热
●脆硬材料的脆/延性演变机制
●有序排布砂轮设计及其高效磨削机理
●超高速磨削表面损伤及表面完整性控制
科学问题二:
微约束空间、强剪切润滑介质支承系统的热、动力学行为
高速旋转系统的稳定性是旋转装备的共性问题,对高速机床来说,是其核心技术。
超高速机床主轴工作过程中的快速启、停要求,使高速旋转的主轴必须尽量减小惯量,呈现出柔性轴特征,给实现精准的主轴动平衡提出了在线的要求。
动静压复合轴承可以提供高刚度、长寿命的有发展前景的新型支承结构,而其高精度、高刚度要求及冲击切削力的激振,使润滑轴承的间隙设计尽量小,介质处于微间隙、高剪切应力之中,其发热及动态行为显著地影响着主轴系统的稳定运行。
在超高速旋转强剪切与微间隙高压力工况下,润滑介质的状态异常复杂,现有的层流假设已不再适用,轴承润滑介质的类固化现象更加剧了系统的发热,由此显著地影响着支承系统运行的可靠性及其使用寿命。
需要通过实验和仿真研究,揭示微约束空间的强剪切率下润滑介质的性能以及高速旋转主轴精度演变规律,实现对轴承结构及参数的创新设计,并为实现主轴系统高速高精度稳定运行与控制提供理论指导。
主要研究内容:
1)超高速轴承微约束空间、强剪切润滑介质的热、动力学耦合行为
以超高速主轴轴承为代表的超高速旋转体的微约束空间中存在着十分复杂的多场强耦合作用现象,研究极端条件下超高速旋转体的支承界面的摩擦学、热力学及动力学行为特征,探索高速轴承材料以及润滑材料界面之间的耦合关系,从而揭示超高速动压润滑油膜的形成机理及其传热规律,阐明超高速、低粘度、紊流状态下稳定润滑状态形成的本质及实现条件,是开展对支承方式或者支承体的结构、形状、材料构成与匹配、表面改性及润滑方式等轴承技术开发的前提,是实现适应极端环境下支承功能与性能设计的理论基础,重点研究:
●超高速、低粘度、冲击切削力下动压润滑膜形成的本质及实现条件
●局限空间、瞬态参量测量的MEMS传感技术
●超高速、微空间润滑、切削条件下轴承表面材料摩擦学行为与特征描述
●超滑材料、超滑结构及低粘度润滑介质的超高速主轴支承原理
●适应极端环境的高可靠长寿命支承设计理论及结构创新
2)超高速柔性主轴系统高精度动平衡的数学力学原理
针对超高速机床主轴换刀频繁、切削过程不稳定、多结合面复杂系统、高速离心力的干扰等不稳定工况和其高刚度、高精度、高稳定性要求之间的矛盾,除了对其结构精心设计外,提出精准高效的高速主轴动平衡方法,实现高速主轴实时监测、在线状态辨识和不平衡控制,是一种必然的选择。
超高速机床主轴属柔性轴,其动态响应涉及高频段,因此,将本团队创新的动平衡全息谱理论发展到适用于高频段、多模态柔性转子系统的全息谱理论,探索超高速主轴系统的非线性动力学行为规律,开展高速主轴系统状态监测与高精度稳定控制的研究,具有重要意义,重点研究:
●考虑加工干扰的超高速主轴系统非线性动力学描述与分析
●超高速主轴和工具系统接触界面的力学演变规律
●超高速主轴系统热力物理参数的实时获取及数学处理方法
●超高速柔性主轴系统在线全息谱动平衡理论
●超高速主轴不平衡量的自动控制原理与实现方法
科学问题三:
机械结构界面的物理表征及系统耦合
机床是由主轴系统、床身系统、多维工作台及其驱动系统等组成的复杂机电系统。
这些系统通过系列结合面组成一个整体,处于随机动态切削力、高速进给机构的冲击力、旋转轴不平衡质量的离心力及热载荷的作用之下。
整机刚度的50%及阻尼的50-80%来自结合部的影响。
有限元对连续体机床构件的动静热特性,可以精确计算预测,现有的有限元的接触单元为结合面的计算也提供了一种方法,但刚度、阻尼、热阻等物理参数的确定对结合面来说是相当困难的,从而造成结合部的精确计算是整机设计和性能预测的瓶颈。
机床的固定结合面一般有较大的预紧力,而高速机床的移动结合面处于轻面压的强非线性状态,其动静热特性与位移、载荷及振动频率高度非线性,使其建模和分析的难度更大。
另外,高速机床结合部的接触问题计算数值精度要求要比一般机械结构要求高得多。
现有的有限元接触分析技术,很难满足高速高精度机床结合部问题的计算要求。
超高速机床这样一种多约束、多物理场交互作用的复杂工艺系统,结合面的高度非线性和设计计算的高精度要求之间的矛盾,使得对于结合面的物理表征及系统耦合的研究益发重要。
突破结合面建模在整机结构创新设计中的瓶颈约束,丰富机械设计理论,对装备设计制造具有普遍意义。
主要研究内容:
1)多场强作用下的结合面物理表征
通过实验与仿真研究,获取机床各种类型的结合面物理参数,探索建立复杂系统模态综合中的结合面耦合模型及其分析方法。
揭示高速制造装备的移动结合部非线性耦合规律,建立考虑结合面耦合关系的高速机床整机特性预测模型与解析方法,提高制造装备整机设计的准确性,实现高速加工设备开发的科学指导,重点研究:
●结合面物理参数研究
●结合部耦合关系的建模及其数值方法
●提高结合部阻尼特性的研究
●高速机床结合面结构创新设计方法
2)超高速加工机床整机集成及验证平台的构建
由高速主轴系统、刀具系统、床身系统、高速驱动系统、多维工作台等组成的超高速加工机床这一复杂系统,工作在驱动力和切削力的强烈对抗之中,处于切削热及环境变化构成的复杂温度场内。
为了获得超高速机床在复杂工况下高精度稳定的工作性能,本课题研究结合面的动静热特性参数的整机耦合机制,探索高速机床机电系统耦合行为规律与动态误差补偿途径,提出复杂结构系统集成的设计方法。
在此基础上,构建超高速加工机床验证平台,验证本项目研究的成果,提供超高速机床整机设计技术基础,重点研究:
●基于结合面特性耦合的整机模态综合理论
●高速高加速度进给系统动态误差成因与数控补偿
●动静热特性的整机结构的优化设计
●超高速加工机床验证平台的构建
二、预期目标
总体目标:
围绕超高速切削工具和装备的核心技术,探索超高速加工多场强作用下的材料激变与去除机理,揭示超高速切削的科学本质;研究在热力耦合强作用下工具与工件、机械结合面、轴承构件与润滑介质之间的界面互相作用的科学问题,发展高速工具新材料和设计理论、新型主轴高速轴承、高速柔性主轴在线动平衡理论与技术等,获得高速机床集成技术和自主设计能力。
通过对高速主轴系统和考虑机械结合面精确模型的整机设计理论两个方面的突破,大幅提升高速装备设计制造的技术水平,从而提高我国制造业生产效率及装备制造能力。
培养一批创新精神强的高速加工装备制造科技骨干力量,并与企业共同建我国高性能机床的研究基地。
五年预期目标:
深入研究多场、强作用下的材料激变行为,揭示高速加工的材料去除机理;研究微约束空间、强剪切润滑介质支承系统的热、动力学行为,发明新型超高速轴承和主轴动平衡技术;研究机械结构界面的数学描述及系统耦合特征,建立超高速切削机床的集成技术验证平台。
1、理论层面
●揭示多场耦合强作用下超高速加工过程的科学实质,突破目前对超高速加工切削学行为认识的局限,建立切削方程,揭示高速刀具材料的失效机理;揭示高速磨削热的产生、耗散规律与砂轮的失效规律。
●创建微空间、高剪切率下,低粘度混合介质润滑的稳定支承理论和高速柔性主轴的在线动平衡理论;
●系统建立超高速加工装备结合界面的动静热等物理特性的表征方法;奠定超高速加工装备整机设计基础。
2、技术层面
●铝等轻合金切削速度达8000m-10000m/min;钛合金150-300米/分
●2-3种超高速加工的长寿命刀具材料;
●用于高速磨削的有序排布砂轮设计技术;
●新型超高速动静压滑动轴承(可用于铣床、10000小时以上寿命、5万rpm)及其设计方法;
●超高速主轴系统在线动平衡的MEMS监测和全息谱分析技术;
●可用于机械装备创新设计的结合面通用性解析方法;
●设计制造一台高速加工装备作为验证平台;
●提出一套超高速机床整机设计方法。
拟在国内外重要刊物上发表论文260篇以上(其中SCI/EI论文130篇以上),撰写专著3部以上,申请专利30项左右。
组成一支富有拼搏精神、创新能力强的研究队伍,培养博士后、博士和硕士100名左右。
三、研究方案
1。
总体思路:
如图1所示,本项目以解决超高速加工及其装备的基础科学问题和拥有若干具有自主知识产权的关键核心技术为目标,重点围绕三个主要科学问题开展多学科交叉基础研究,在超高速加工的共性基础研究取得突破的基础上,提出超高速加工核心技术问题的解决方法,形成若干我国自主知识产权的原创性成果。
图1总体学术研究思路
2。
技术路线
在本项目研究中,拟通过如下几方面的思路和手段,实现研究目标:
1.构建采用新技术、新原理和新思路的高速加工实验方法和测试平台,实现对高速加工过程和高速相对运动部件及其关联机械系统的信息采集
2.通过基础实验和切削实验研究,发现高速加工过程中的物理与化学特征。
着重从相关的力学基本概念出发,通过适当的数学描述,建立多场强作用下的高速加工过程及其关联系统的数学、力学模型。
3.开发及利用专业的分析软件,实现对高速加工过程的仿真与分析。
4.系统深入地开展理论与实验的比较研究,采取正问题和反问题结合的方法,揭示超高速加工过程的动态演变规律及加工装备的服役特性,进而提出超高速加工的新原理新方法,建立超高速加工装备的设计、制造以及应用的理论体系。
具体技术路线如下:
1)超高速加工的切削学行为研究路线
(1)超高速切削过程的基础性实验
首先建立超高速切削过程的模拟平台,通过超高速弹射击模拟实验,观测高速断裂过程材料损伤裂纹发展机理,建立其物理模型,再与机床上进行的超高速切削实验比对,形成对超高速加工机理的认识,逐步揭示瞬态、强冲击、绝热剪切的材料去除过程的科学本质.
超高速切削过程的模拟平台拟采用冲击速度可达25—35m/sHopkinson压杆技术实现切削冲击过程。
如果基于轻气炮平板撞击技术可以获得102m/s量级更高的冲击速度。
采用切刀静止方案则可以方便地进行其温度和冲击力的测定。
高速切削过程的动态应力与变形测试系统由应变片或MEMS压力传感器、动态应变仪和示波器组成。
通过测试不动切刀上几个特定点的压力和变形,利用深梁原理确定切刀与工件间的冲击力;也可模拟工件静止不动情形,直接测试其上个别特定点的应变和冲击面上的冲击压力.利用动力学原理推算切削力;同样,对于工件与子弹为一体的情形,可以通过测试冲击速度和切削过程中切刀的速度-时间变化规律确定切削力。
瞬态温度测试系统用于测定切削工程中切刀和工件的瞬态温度场。
有热电耦技术、红外辐射技术和增强式CCD相机等方法。
基于高速冲击切削温度瞬变的特点,本研究拟采用热电偶测温和新型红外传感探头测温技术。
红外测温系统由红外探头、信号放大器和记录仪组成。
该方法可以实现被测物体表面单点和多点的温度测定,最快响应时间为微秒量级,适合高速切削.实验研究的环境温度可从常温到材料熔点的大跨度变化,适应对切削过程中材料剥离机理的探索,为研究切削过程中材料剥离和切削机理奠定科学基础。
模拟实验平台可以控制冲击的能量,进行损伤冻结实验.通过损伤冻结实验,观测高速断裂过程材料损伤裂纹发展的不同阶段,研究高速断裂过程材料损伤裂纹发展的历程和机理,深入研究切屑形成演变的过程及其形态转变的物理机制;系统深入探索工件材料绝热剪切敏感性及其对切屑形成演变的影响规律。
逐步建立其物理模型,再与高速切削机床的切削实验比对,形成超高速加工机理的认识,逐步揭示瞬态、强冲击、绝热剪切的材料去除过程的科学本质。
(2)超高速切削实验及其行为规律的描述
在开展上述高速冲击实验基础上,进一步开展高速切削行为的实验研究,以直接获取工件材料动态剪切应力与应变、温度等关系。
实验材料以航空航天工业应用广泛的铝合金、钛合金等为主.切削实验在50000rpm的超高速铣床上进行。
切削力的测量可采用压电晶体传感器,有足够的响应频率。
温度的测量可以采用MEMS温度传感器,其热容量极小,可以反映温度的瞬态变化。
温度场尤其切屑内的绝热剪切带的温度是难以获得的,拟以对切屑截面进行电镜观测,由晶格的变形观察到绝热剪切带的存在与走势,再与仿真分析相结合。
在充分获取高速切削过程的基本数据基础上,以切削理论、材料学、力学为指导,结合超高速实验发现的科学规律,研究超高速材料去除的多场强作用形成的科学机制,探索超高速切削过程所发生的力学、物理与化学行为的本质:
建立超高速切削过程切削方程、能量守恒方程,发现并阐释超高速加工过程的切削变形机理;建立高速切削加工过程刀—屑,刀—工摩擦系统的热物理方程,对超高速切削过程的摩擦学行为及其效应进行热力学分析;建立超高速切削过程参数(切削力、切削热、切削功率、刀具寿命等)预报方程,为超高速切削装备及工具提供设计基础,为制订超高速切削加工工艺提供理论依据;建立切削条件和表面变质层行为的关系描述模型,为提高超高速加工工件的表面质量和使役寿命提供理论基础。
在超高速切削实验研究和理论探索的基础上,开发超高速切削加工的数字模拟仿真系统,模拟超高速切削加工过程的切屑形成和预测超高速切削加工变形参数(应变、应变率、变形系数等)、过程参数(切削力、切削功率、温度场、速度场等)、表面变质层残余应力等.
在以上切削实验及模拟实验研究、理论探索和数字模拟仿真分析的基础上,以求建立起超高速加工切削学研究体系,并用于指导切削加工的工程实践。
(3)超高速切削刀具的跨尺度设计方法
在上述对超高速加工切削学研究基础上,拟从宏观与微观两方面开展超高速切削刀具的材料与结构设计。
在研究方法上,首先采用逆工程方法,即收集分析已破损刀具的损伤形态,以微观力学(代表体积单元(RVE)方法、平均场理论)、显微结构物理学与宏观连续介质力学相结合,实现刀具材料微观结构与宏观性能的关联;采用“统计损伤力学”方法,研究刀具材料由微观损伤到宏观失效的演变规律,揭示刀具的磨损、脆性断裂、塑性变形破坏等各种失效机制;采用最小耗能/最小熵原理,确定刀具宏观失效的“临界阈值",从而建立超高速切削刀具寿命及可靠性预报模型;研究过程中,采用SEM、TEM实验设备的微观结构观测与分析方法,实现刀具材料微观结构、物理性能的解析;通过实验分析与比较,以长寿命和高可靠性为目标,优化设计刀具材料的成份配比,优化刀具材料的颗粒分散、烧结制造工艺,实现超高速切削刀具的跨尺度设计。
通过建立多齿回转刀具结构参数、刀刃几何参数与切削均匀性及可靠性的关系模型,实现超高速切削多齿回转刀具结构设计.
(4)超高速磨削理论与技术的实现途径
●超高速磨削理论基础实验
在超高速磨削研究中,首先以单颗粒磨粒进行磨削仿真实验观测,测量其力、热及能量转换规律,从而为超高速加工砂轮的结构创新与应用提供理论依据。
采用单磨粒研究的优点是其观测的方便性。
实验研究的重点在确立关于单颗磨粒的切削力、比能和临界成屑厚度三个重要特征参数随砂轮线速度提高而呈规律下降特性的基础实验数据以及不同难加工材料相应的对比数据.通过研究磨削过程中的变形与摩擦问题、力、温度、热力耦合关系、砂轮磨损等规律,突破难加工材料超高速加工技术瓶颈,解决超高速磨削加工基础理论问题。
●磨粒有序排布及强化换热砂轮的的研究
为获取超高速磨削技术,首先通过实施对磨削过程的建模仿真研究,按照不同加工要求和用量条件优化设计砂轮地貌,磨削用量,并预估磨削过程,实现有效地控制和降低磨削比能;采用高温钎焊方法实现增加磨粒的结合强度,提高单层磨粒的有序排布砂轮的寿命。
利用热管超高效的强化换热能力,将其布置在磨粒有序排布的砂轮工具基体上(这在普通磨料工具上是无法实现的),同时在难加工材料超高速磨削时把冷却的重心转向砂轮一方,利用砂轮基体的良好导热性,将带翅环形热管内置于砂轮并贴近砂轮表面,可将磨削弧区产生大量的热有效地疏导出去。
拟从环形热管的结构设计开始,综合考虑热端尽量贴近工具表面且满足高速旋转条件下砂轮结构强度要求的热管布局的腔体尺寸,进而选择合适的液态工质和比例,通过传热学计算反复模拟仿真,最终确定环形热管砂轮的优化设计。
制作环形旋转热管强化冷却装置,对其换热效果进行实验考核验证与改进.
在上述仿真与实验基础上,进一步开展磨削实验验证.验证实验拟在南京航空航天大学的德国BLOHMPRFIMATMT408超高速数控平面/成形磨床上进行,其最高砂轮线速度170m/s;功率60KW;主轴精度:
径跳/端跳2m;进给系统精度1m。
2)超高速机床装备的关键部件创新研究的技术路线
(1)超高速动静压混合轴承的实现途径
目前高速机床采用的高速轴承基本是陶瓷球轴承,其保证寿命仅2000h,流体润滑轴承的理论寿命是无限长,是有应用前景的结构.抗切削力的冲击要求具有高刚度、高旋转精度的特点。
静压保证了其启停的安全性,动压具有转速越高,刚度越高的优点。
其发热是应用的主要障碍。
本研究拟采用提高轴承工作表面的加工精度、降低粗糙度等方法,保证润滑轴承的小间隙,以提高刚度,满足冲击切削下精度的要求。
拟采用超滑材料及超滑结构(如支承表面的微纳结构)来改变微间隙内润滑流体的速度分布,降低剪切率,采用低粘度的润滑介质(如水、水银)等措施来降低润滑介质的发热.
本项目初步仿真计算,轴承间隙在10μ以下时,能满足高速铣床主轴的刚度要求.
(2)超高速主轴系统在线动平衡的实现方法
在高速动平衡原理研究问题上,拟通过对2阶以上的幅频和相位的信息利用,通过信息融合技术,实现对屈梁生院士发明的转子动平衡全息谱理论的进一步发展,为高速主轴系统的不平衡质量与相位的计算提供精确的数学原理。
拟采用FPGA大规模可编程逻辑集成电路实现高速的数学处理,以解决动平衡过程中对高速信号测量与信息融合中的高速数据处理问题.
当主轴的