工业硅生产常识问答.docx
《工业硅生产常识问答.docx》由会员分享,可在线阅读,更多相关《工业硅生产常识问答.docx(62页珍藏版)》请在冰豆网上搜索。
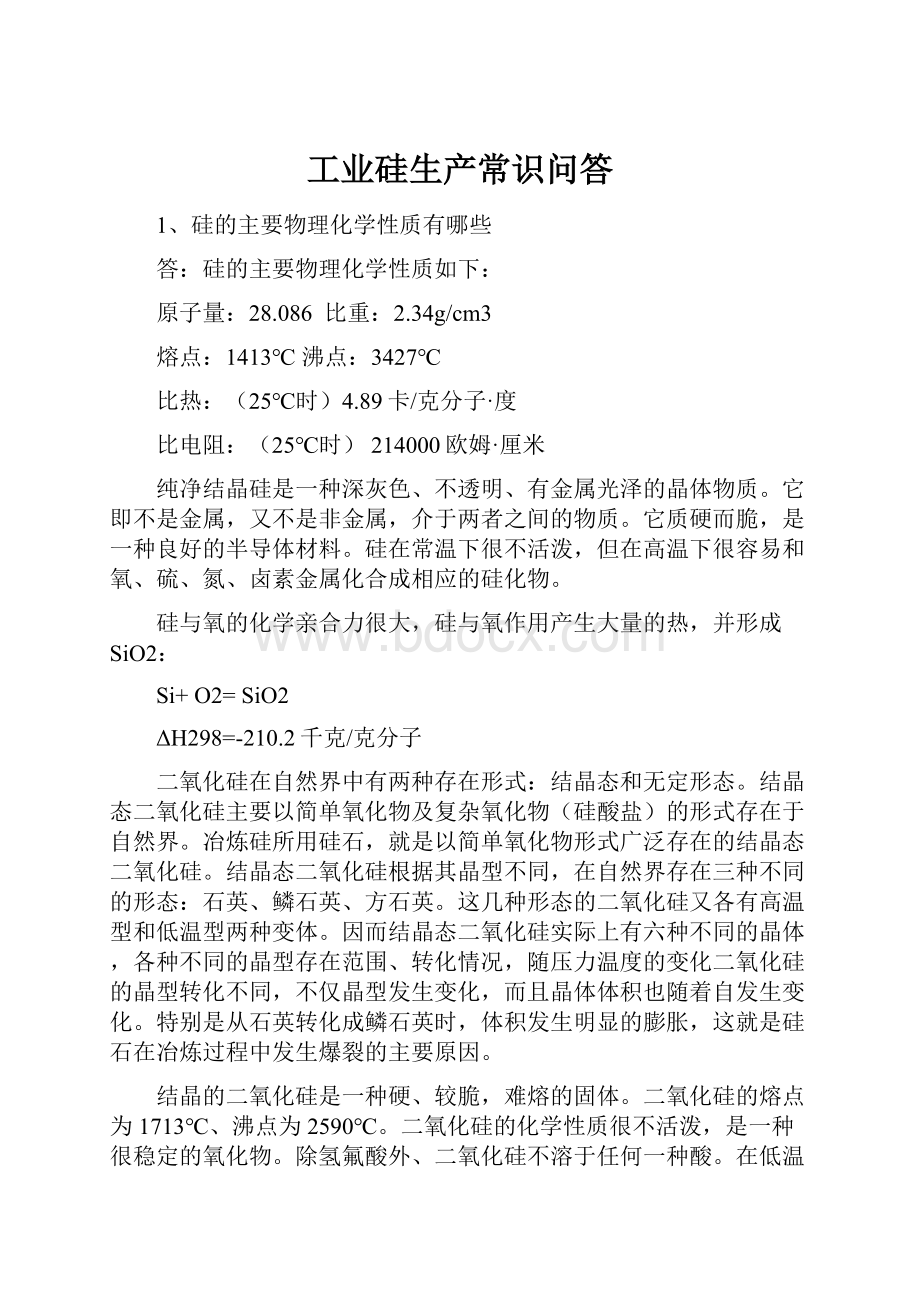
工业硅生产常识问答
1、硅的主要物理化学性质有哪些
答:
硅的主要物理化学性质如下:
原子量:
28.086比重:
2.34g/cm3
熔点:
1413℃沸点:
3427℃
比热:
(25℃时)4.89卡/克分子·度
比电阻:
(25℃时)214000欧姆·厘米
纯净结晶硅是一种深灰色、不透明、有金属光泽的晶体物质。
它即不是金属,又不是非金属,介于两者之间的物质。
它质硬而脆,是一种良好的半导体材料。
硅在常温下很不活泼,但在高温下很容易和氧、硫、氮、卤素金属化合成相应的硅化物。
硅与氧的化学亲合力很大,硅与氧作用产生大量的热,并形成SiO2:
Si+O2=SiO2
ΔH298=-210.2千克/克分子
二氧化硅在自然界中有两种存在形式:
结晶态和无定形态。
结晶态二氧化硅主要以简单氧化物及复杂氧化物(硅酸盐)的形式存在于自然界。
冶炼硅所用硅石,就是以简单氧化物形式广泛存在的结晶态二氧化硅。
结晶态二氧化硅根据其晶型不同,在自然界存在三种不同的形态:
石英、鳞石英、方石英。
这几种形态的二氧化硅又各有高温型和低温型两种变体。
因而结晶态二氧化硅实际上有六种不同的晶体,各种不同的晶型存在范围、转化情况,随压力温度的变化二氧化硅的晶型转化不同,不仅晶型发生变化,而且晶体体积也随着自发生变化。
特别是从石英转化成鳞石英时,体积发生明显的膨胀,这就是硅石在冶炼过程中发生爆裂的主要原因。
结晶的二氧化硅是一种硬、较脆,难熔的固体。
二氧化硅的熔点为1713℃、沸点为2590℃。
二氧化硅的化学性质很不活泼,是一种很稳定的氧化物。
除氢氟酸外、二氧化硅不溶于任何一种酸。
在低温下比电阻很高(1.0×103Ω·cm),但温度升高时,二氧化硅的比电阻急剧下降,当温度升至2000℃时,二氧化硅的比电阻只有(100Ω·cm)。
硅与氧在自然界中普片存在的形式是二氧化硅。
但是,在一定条件下,将硅和二氧化硅混合加热到1500℃以上时,或将炭各过量二氧化硅加热到2000℃左右时,可获得一种挥发性很强的气态物质-氧化硅。
气态氧化硅只有在高于1500℃时才能稳定存在。
低于1500℃时按下列反应分解:
2SiO<1500℃Si+SiO2
一氧化硅的挥发性很强,其蒸气压约在1890℃时,就达到一个大气压。
一氧化硅的高挥发性硅石还原过程中起着十分重要的作用。
硅与碳可以形成炭化硅(SiC)。
纯炭化硅是种无色透明、即硬的晶体物质。
工业硅生产中形成的碳化硅因含有硅、炭和二氧化硅等杂志,形成黑色或绿色两种颜色不同的晶体。
炭化硅化学活性很差,但在高温下,大于1500℃,炭化硅能与某些氧化物强的气体作用发生分解。
如在高温下遇到二氧化硅时,就能产生以下分解反应:
SiC+2SiO2>1500℃3SiO+CO
总的来说:
炭化硅的主要特性稳定、难分解、高温下比电阻小,不熔于合金。
在硅中只能熔解少量炭:
如1725℃时在液态硅中可熔解0.32%炭。
硅与铁形成硅铁,硅与钙可形成一系列的硅化钙。
硅是“工业之米,金属魔术”。
2、硅冶炼化学反应进程的影响因素
答:
在硅冶炼二氧化硅还原成硅的化学反应过程中如何平衡温度、压力、化学成分、气象成分。
从热力学角度看,所有的反应都要在体系达到平衡状态下向正反应方向进行。
当然在生产的实际过程中,受综合条件的影响,必然有不同程度的波动,甚至严重打乱和偏离平衡状态。
我们在这里以反应平衡状态为起点来对生产实际过程偏离原因进行分析,寻找影响有利反应的因素。
在冶炼炉中,用C还原SiO2的反应如下:
SiO2+C700-1200℃SiO+CO
SiO+2C1200-1500℃SiC+CO
2SiO2+SiO1500-1800℃2Si+CO
SiO+SiC1800-1980℃2Si+CO
在冶炼硅时,炉料从炉口加入,随着反应的进行,炉料逐渐预热下沉,温度渐渐升高,炉料在多层中的反应逐步展开,现分层分析如下:
a、SiO2-C层
这一层是出于炉膛上部物料预热散料层。
冶炼用炉料的配料比,每批料的C与SiO2的配比为2:
1,此层温度小于1200℃,该层中主要凝聚相是SiO2与C共存。
与其他梯阶层相比,最显著不同是有大量的C存在。
低温时的主要反应以SiO形态存在。
反应随着炉料下沉加热,温度升高大于1500℃生成SiC反应,反应随温度升高而加速。
这一层反应温度不是很高,在实际生产中都能满足,加上这一层里SiO2为过剩相。
所以只要在散料层有一定厚度其反应就可充分进行,直到炉料中的C全部反应。
b、SiO-SiC层
这一层处于SiO2-C以下,其温度大于1500℃,又在层界交汇处,反应物层界交汇处,反应物SiO2是上层中末消解完而沉落下来的。
其化学计量数为(C/SiO2=1/3)。
主要参与反应物是上层的产物SiC,随着温度的升高,相比强化。
在这一层中SiC是过剩相。
有SiC存在时在该温度区SiO2是非稳定相,直到将SiO2全部反应。
随温度和压力的逐渐升高,为下一步Si的生成反应创造条件。
由于此时反应是吸热,导致该层温度上升缓慢,因而这层不能满足Si生成的条件。
c、SiC-Si层
在本层紧连着SiO2-SiC层,由于上层反应产生的炉气同时充满着本层,这层离电弧区更近,故温度更高,有利于Si反应生成,温度越高反应越激烈,体系中生成的Si也越稳定。
生成的液态Si从SiC表面低落下来,离开反应区。
反应不断进行,直到把SiC消耗完。
以上分层断分析是一个基本单元反应进行的过程。
在实际的生产中,炉内在交错进行多层反应。
并不是说某批料生成的SiC就一定要由该批料所产生的SiO来反应完,只不过是在反应物和产物的量上,始终保持着动态平衡,以上分析模式是一个理想模式,假定SiO全部被吸收转化,而没有损失,那么Si的回收率100%。
显然这在实际生产中是不可能达到的。
但是对分层的反应分析,将有助于我们对实际生产过程中反应进程的理解和找出影响化学反应进程的因素。
通过对以上硅冶炼反应层带的分析,下面对影响反应进程的因素分别讨论如下:
a、温度和压力的而影响
大家知道满足化学正向反应的主要条件是温度和压力,根据压力、温度,结合Si-O-C绘制出平衡图。
依据热力学定律:
在体系中某时刻压力、温度平衡时,当体系某状态的分压比(Jp)小于平衡状态时的气相分压(Kp)时反应正向进行,当体系中某状态点的分压比(Jp)大于平衡状态时该气相的分压(Kp)时,反应向反向进行。
由此可见随着温度的增高而压力跟不上,反应只能反向进行,而不能生成SiC。
相反随着温度的升高,而压力平衡于温升增大的状态,反应都能顺利进行而生成SiC。
也就是说体系不适当的过热,阻碍了SiC送往生成,热损大效率低。
实践证明,若预热带温度高,压力小,则炉况恶化,这就是冶炼过程要求“冷料面”的原因。
只要保证在1980℃及高的平衡状态时的该气相分压值,有利于Si的生成。
这就是当炉眼大喷火时产量下降的原因。
b、配比的影响
我们知道理想的炉料比是SiO2:
C为1:
2,当偏离这一比值时,虽然不会改变温度压力的平衡,但反应产物与SiO2与SiC的相对量都发生了变化,进而影响反应的进程。
如当SiO2量低于理论配比时:
SiO2-SiC层,SiO量少于化学计量数1/3mol,反应达某一进度时就会终止。
这是因为反应的前提条件要有SiO2存在,由于SiO2的不足,在该层中消尽。
因而不能源源不断满足Si的生成条件。
若要达到生成条件反应,就必须提升体系的反应温度尽快下沉到大于1500℃以上的反应区域,达不到这个温度,SiC就积存在这一带。
在实际的生产中,这种情况就是料轻涨炉底导致。
当SiO2的配量多于理想配比时,在SiO2-SiC层,SiO2量大于1/3mol:
对于炭化平衡来说,在这一带过多的消耗了SiC,造成后续反应的SiC量不足,同时生成更多的SiO,造成SiO损失增大。
在实际生产中由于操作、硅石粒度大,将有一部分SiO2未完全反应,而成熔体渣相。
具体化表现料重、刺火、渣多渣粘,增大了副反应,降低电热效率。
若温高易排,温低积极垫涨炉底。
特别强调的是过量的SiO2是透气性变坏的最主要的原因之一。
过量的SiO2增加了副反应,限制了体系温度的提高。
在这里即使有Si,由于SiO2的存在,Si属不稳定相,它将再次与SiO2反应,生成SiO。
c、炉料透气性的影响
炉料的透气性反应了炉料对气体排出阻力的大小、透气性越差,则阻力越大。
冶炼过程中要排出大量的炉气,当排气受阻时,所排出的气体就要反过来对体系形成一个附加压力。
然而炉料的透气性越差,体系中承受的压力越大。
只要生成物与反应物之间体积存在差异,体系压力就会对反应产生影响。
由于反应的产物的体积较其反应物扩大约4倍左右,所以当有附加压力存在时,将使反应严重受阻,形成Si生成条件温度提高。
实际生产表明,当炉膛内压力过大时,炉况差,且难于控制,其原因就在于此。
因此在生产过程中十分注重炉料的透气性,千方百计加以改善。
d、炭质还原剂水分的影响
还原剂中的水份在SiO2-C层与SiO2-SiC层或蒸发或离解,大多以气体的形式存在和排出,因而易造成体系中分压发生变化。
当水份含量较大时分压值变化相当明显,特别是SiO2-C层和SiO2-SiC层,由于蒸发离解反应带走大量的热,给下步反应温度带来的不足,造成亏热现象,降低反应速度和产能。
据相关资料介绍,炉温每降低10℃,反应速度降低1%。
e坩埚大小的影响
“坩埚”系指炉料通过率高,容量大,透气性良好的反应区,从气体存纳的角度看,“坩埚”区即为体系气相有效地存贮库。
“坩埚”区大,气体的体积则大,体系压力就小,有利于反应正向进行,进而降低硅的生成温度,强化反应和冶炼容量。
相反,当“坩埚”区缩小后,无论配比怎样准确,操作如何到位,炉子总是烧不好,如刺火,电极变浅,产量低,电耗高,质量差,实践中同样的炉料,同样的配比,同样的操作,投入到不同的两座容量能力相同的炉子,其中一个“坩埚”大,一个“坩埚”小,其结果就是“坩埚”大小的差异,导致体系压力不同,造成反应能力强弱,形成差距极大结果。
f、铁的影响
在硅冶炼过程中铁参与使C还原SiO2的反应顺利进行。
而且实践表明硅铁生产中Fe含量越高,冶炼越易进行。
这是因为当液态Si和液态中的Si都以纯物质为标准时,反应平衡常数只是温度和函数关系:
Fe的熔点易提前生成Fe的化合液相,硅的生成温度随之下降,降低了Si冶炼的烧成温度,大大有利促进反应正向进行。
比如当硅铁含硅20%左右时,甚至用一般高炉可冶炼,根据这一现象,在硅铁生产中为了有效破坏炉底积存的SiC,采用变换生产含铁较高的品种,如生产75硅改产50硅铁。
Fe可降低烧成温度,有利于化学反应的顺利进行。
但Si产品中的Fe含量过高是不允许的。
总之,我们针对硅冶炼的化学反应进程的分析,讨论和了解,特别是对主要影响化学反应因素的讨论,可使我们进一步深入从源头弄清楚诸多不利影响炉况变化的实质,从而来指导我们的工艺,通过调整生产操作整体把握生产工艺全过程,达到稳产、高产、低消耗的目的。
3、硅产量、质量、消耗主要指标取决于什么?
答:
它取决于原材料的质量和稳定性、设备先进配置、工艺参数的先进性和冶炼工艺操作及参数的选用与其相互之间合理有效地紧密结合。
金属硅生产可分为三大要素:
要素一(硬件)是原料、供电质量、设备、工艺参数的合理使用。
要素二(软件)是必须具备较高的工艺、技术操作水平和维护保养检修水平。
要素三(保证)必须要有较高素质的管理人才和科学的管理水平。
“三要素、三水平”必须和谐统一。
也就是常说的“原料是基础,设备是保障,操作是关键”。
4、产一吨硅耗理论硅石是多少?
答:
在冶炼过程中,提供SiO2的主要来源于硅石碳质还原剂,灰分中提供的SiO2是忽略不计,则生产一吨硅需硅石的理论耗量为X:
X=1·(SiO2/Si)=1·(60/28)=2.14吨/吨-硅
5、配料提供烧损的炭量如何计算
答:
硅冶炼的过程中受热停炉、水份、操作技能、炉况变化的影响,当炉料要补炭量时可根据炉型的大小,功率高低,缺炭的现状而取不同的值范围13-15%(粉尘中带走的固定炭7-8%)。
6、生产一吨硅需要投入多少炭量
答:
设一吨硅所需配炭量为X,根据其反应方程式:
因为SiO2+2C=Si+2CO
24/x28/1
所以X=(24×1)/28=0.857吨
7、为什么常说两个炭原子还原一个硅原子
答:
因在硅冶炼的进程中,进入反应区的物料的配合分子比等于2。
才能保持化学反应的平衡,不出现过剩的SiC和SiO2,炭与SiO2的分子比大于2小于3会出现过多的碳化硅,小于2会出现过多的氧化熔渣,将造成炉底上涨,坩埚的收缩,炉况的恶化,周期变短。
8、碳质还原剂灰份对硅冶炼有什么影响
答:
碳质还原剂中的杂质主要来源于灰份和杂物,全部由氧化物组成。
在冶炼的同时,各氧化物也被还原,即消耗电能、热能、又要消耗碳素原料,而且还原后的杂物融入硅中,降低硅的纯度,影响产品质量。
据资料介绍,炉料中每增加1%灰份,要多耗电60KW·H左右。
9、碳质原料挥发份对硅冶炼的影响
答:
关于碳质原料中的挥发形态,是游离态,没有适当准确的分析方法,所以不能明确肯定。
单从挥发元素来看,可以推出是一些脂肪族饱和物。
如,甲烷、焦油气态物之内的物资。
在碳质原料中,一般含有20-30%的氧在炉内与温度极高的电极反应,使电极消耗增加,同时造成烟罩、水圈、铜瓦反应腐蚀变形。
有10-15被碳化,使碳质原料的效率降低,易造成刺火,热损增加,操作环境恶化,产能降低。
10、碳质原料粒度对硅冶炼的影响
答:
硅冶炼对碳质还原剂的电阻率要求要大碳质原料在各种不同的粒度下,其电阻相差很大,一般来说粒度小,电阻大,有利于电极的深埋,有利于电炉热工制度的稳定,有利于反应速度的加快。
反之粒度大,电阻小,炉内的支路电流增强,电极易上抬,对冶炼操作不利。
原则上要求原料的活性要高,电阻大气孔率高,保证炉气上升容易的碳质原料的粒度。
我司对碳质原料粒度要求:
木炭:
40×40mm石油焦:
8-14mm精煤:
8-14mmm
原煤:
14-18mm木块:
50×50×50mm
11、硅石粒度对硅冶炼的影响
答:
入炉硅石要有一定合理配比的粒度,粒度是冶炼中的一个重要因素,粒度过大接触面积变小,反应慢而不彻底,造成炉底氧化物过剩涨炉底。
粒度过小,炉料的透气性变坏,反应速度过快,炉料发粘,导电性增强,烧失量大,回收率低。
另外硅石的粒度对操作电阻有直接关系,炉料中电阻系数随硅石粒度的增大而下降。
生产中我司对硅石粒度及配合比是:
20-40mm<15%40-80mm>75%80-100mm<10%
12、硅石中杂质对硅冶炼的影响
答:
硅石中杂质对硅生产时十分有害的,造成硅石中的SiO2含量较低,其它有害氧化物Fe2O3、Al2O3、CaO、MgO、P2O5…..含量相应较高,他们在炭热反应中结成稳定的化合物(熔渣)时则需要更高的反应温度,由此电能、还原剂都会增加,炉况变差。
生产中要求硅石的杂质含量要低。
当炉料在炉内反应生成硅时,同时各种有害杂质也在进行如下反应:
SiO2+2C1500℃Si+2CO(吸热)1137千卡
Fe2O3+3C730℃2Fe+3CO(吸热)1108千卡
Al2O3+3C2160℃2Al+3CO(吸热)1291千卡
MgO+2C800℃Mg+CO(吸热)116千卡
CaO+2C850℃Ca+2CO(吸热)130千卡
因此在冶炼过程中多有消耗电能、热能、还原剂,所以对冶炼硅石要求杂质越低越好,清洁无杂质,硅石水洗、精选杂石入炉是金属硅冶炼、节能、降耗的重要措施。
13、精煤还原剂的理化性质及作用
精煤是洗煤厂根据生产厂家提供的相关经济技术指标,经机械富选、精洗配制的低灰分烟煤。
通过苏联恩科夫在硅冶炼运用实践成功后目前的我国广泛应用。
由于精煤的独特属性性质,一是发热量高(QDW>6000大卡/kg)有助于炉温的提高,经实验证明可降低电耗6.2%,硅石单耗减少500kg/T(煤用量0.45T/T-硅)。
二是重金属成份较多、溶剂元素多、矿化物大,有利于炉料的烧结,是炉料烧结性能的调整剂。
三是反应能力强,电阻大,有利于产量的提高。
但烟煤含氧化铁、氧化铝,几乎是油焦的5倍,木炭的10,对产品质量影响明显。
使精煤时炉料的下沉速度慢,这使还原剂的水份、挥发份更能充分地从料面逸出,可使加料工作时间减少25%左右,并提高炉料的透气性。
14、工业硅用木炭应满足哪些要求
答:
根据苏联TOCT7657-58标准:
要求工业硅用木炭应满足如下基本要求:
水份<10%,挥发份<20%,灰分<3%,杂质总和<2%,粒度<40mm,粒度小于25mm<5%
15、碳质还原剂最佳配合比的应用
答:
作为硅冶炼对还原剂使用的碳质材料,应满足:
反应能力强、机械强度高、孔隙率高、电阻大、灰分低、价格便宜等要求。
生产经验表明木炭、石油焦、低灰煤以及木块等都具有这些性质,但是没有一种能独立完全满足硅冶炼对还原剂的要求。
只有科学合理地把这些材料按各自不同的属性组合成最佳配合使用,才能创造出硅还原过程所需的最佳条件。
16、碳质还原剂在硅冶炼中的最佳配合比确定
答:
在长期的硅冶炼的实践和研究的基础上,选择和确定炉料的配合比,还原剂的最佳组成,其特点是最大限度的利用活性还原剂(木炭、低灰烟煤)限制石油焦数,以基本弄清,为了降低电耗,提高产量,必须的混合还原剂的使用中使各组炉料组分保持一定合理科学的比例关系,最佳炉料配比(按应用基的固定碳计算)。
原料名称
配料比
中性值
硅石
200kg
木炭
35-40%
38
精煤
40-45%
42
油焦
15-25%
20
17、硅石粒度与比电阻关系
答:
经实验结果证明,随硅石粒度从10mm增大到40mm,炉料的电阻极具下降。
而进一步在增大粒度从40mm-100mm电阻变化则较小。
同时SiO的生成速度与硅石粒度关系也具有类似的特性。
由于必须保证在熔炼过程中使SiO损失尽可能减少,所以硅石的粒度不小于40mm(下限),在确定配电制度时应考虑到使用大粒度硅石炉料电阻下降因素。
最佳粒度控制在40-100mm为宜。
但由于加工、破碎、购进小于40mm大于100mm硅石粒度的比例较大,从成本节约角度我司对硅石粒度作出如下要求:
20-40mm:
15%,40-80mm:
75%,80-10mm:
10%
18、木炭还原剂对硅冶炼作用及特性
答:
木炭是木材在350-450℃,经隔绝空气条件下,通过热分解制的产物。
木炭的质量取决于木材的种类、木材自身的质量,木炭反应能力强、孔隙率高、其纵横细孔可增大氧化硅与还原剂的接触面积,因而加速还原过程。
木炭的堆密度为0.22-0.24t/m3,孔隙率为79-83%,灰分含量0.5-3.5%,其导电系数低(电阻高)几乎是任何一种焦炭的1/10。
特别是木炭灰分中含有一定量的Na2O和K2O,经炭化作用后能形成流动性良好的熔渣,易同硅液排出,有利于坩埚壁的保持,弧柱的稳定,周期的延长。
19、石油焦在硅冶炼中的功能作用
答:
石油焦是用重热裂渣分解(在450-700℃下的石油精制之后)炼焦制得的副产品。
在垂直加热反应罐中延迟焦化方法的制取石油残留的渣。
油焦质量和性质取决于天然原料的质地,焦化速度和温度以及焦化条件。
在硅冶炼过程中由于木炭是一种可息资源,且价格高,为了降低还原剂的费用,提高产品质量,在生产中用部分石油焦代替部分木炭用量。
在操作中常把油焦作炭量的调整剂,且量大,波动大,可达50%,时至100%。
其使用数量取决于生产过程的动力参数,操作技能经验及炭质还原剂供应情况。
在所有还原剂中石油焦的灰分是最低的(<0.3%),有助于产品质量提高,但反应能力它次于木炭和煤,孔隙率仅次于木炭(46%)。
但是在有条件情况下,不宜全焦工艺或高焦工艺,因石油焦的导电性太强,而且反应能力差(不活泼)比电阻小,提前结晶,启用程序是:
木炭-精煤-石油焦。
20、怎样形象描述坩埚
答:
硅炉冶炼的坩埚好比浸泡在水里的毛笔头,电极好比毛笔杆,当笔杆适当下插时,毛笔头缩短而均匀散开,直径扩大了;当笔杆向上提升时,毛笔头将伸长头靠拢直径缩小了。
21、什么叫坩埚
答:
矿冶炼在正常生产情况,三相电极的下端与炉底之间形成的高温反应区空腔,形成圆屋顶,称为坩埚。
此区的温度最高,故其导电性强,外部各层的导电性则依次降低。
22、什么叫坩埚壁
答:
在熔炼过程中炉料每当塌料时,我们直接可见塌料的好坏?
沉料的多少?
所形成时大时小的空腔叫坩埚壁。
由于他的直观可见性我们通常以它的大小来判断坩埚的大小。
23、什么叫工作端
答:
硅炉输电的最终导体是电报,当表露在铜瓦以下的电报长度统称工作端。
但它可分为埋入部分称之为有效工作端,露出料面至铜瓦部分称之为无效工作端。
24、捣炉有几种方法
答:
硅冶炼的捣炉操作是一项十分重要的操作规程方法。
可称为:
1深捣,②浅捣,③彻底捣
25、捣炉的目的是什么?
答:
在冶炼的过程中,必然实施捣炉操作,其目的是:
1沉料,②扩大坩埚壁,③破坏炭化硅,④改善透气性
26、捣炉有什么具体要求
答:
捣炉时的捣炉要求有:
1适时捣炉,②准确捣炉,③快速捣炉,④有效捣炉,⑤彻底捣炉,⑥严禁压料
27、在硅冶炼过程中的水份转化
答:
在运行中的炉料中带入的水份,在高于100℃时被蒸发;200℃时的炉料中心的水份被全部蒸发掉;400℃左右化学水被排除。
同时分离出的水蒸气在热气中分解,生成氢和炭的氧化物或二氧化碳气体。
水蒸气的挥发消解要消耗一定的热量。
因此理论上要求入炉炉料的水份<10%,不准向炉内添加过湿的炉料,以及炉子的循环水冷系统都是不允许的。
28、硅炉运行时炉气、粉尘、成份比例
答:
在硅炉运行时对功率为10000KVA的数据,在24小时测出,排出的气体量1.0×105m3/H左右,炉气的平均组成是:
CO:
88.6%,CO2:
4.85%,CH4:
1.42%,H2O:
8%,N2:
2.6%,H2:
1.97%。
炉气中含有大量的粉尘中的SiO:
80%,Al2O3:
4%、Fe2O3:
1.6%,CaO:
1.6%,固定炭7-8%,在正常情况下炉气中粉尘的平均量为1.4-1.8g/m3,根据物料平衡算出,气体占全部熔炼产物65-70%,而硅产品25-28%。
熔渣2—3%。
29、硅冶炼过程的热收入、热支出
答:
经熔炼时的热平衡计算表明,电能形式的热收入约占69-72%,而炭被氢在物氧化放出的热约占所需全部热量的17%,其余的热是炉料热和熔炼中形成化合物时放出的。
热支出由以下各项构成:
还原氧化物消耗的热占69-72%,熔体硅带走的热4-6%,熔渣带走的热占0.2-0.3%,气体带走的热占4-6%,炉体的保温散热占2-4%,炉面上部炉口散热占9-12%,电热损占10%左右。
据有关资料介绍:
炉温每降低10℃,反应温度降低1%。
30、炉料的组成对硅生产有何影响
答:
在生产配方过程中,硅石与炭原料的组成,配炭量、冶炼炉料的配合比正确与稳定,对于电炉的大小,又取决它的粒度的大小。
碳质还原剂原料,除主要提供固定炭含量外,它的活性、粒度、反应结合性能、亲合力、电气性能都是决定碳质原料的主要指标。
反应能力强的还原剂在短时间内能充分利用和捕集矿石中的有用因素,确保回收率的提高。
反之炉况被动、产量下降、成本增高(一般情况下还原100kg硅石需40kg固定炭)。
31、硅冶炼时物料熔化过程
答:
当电炉运行时,电极通电,在电极周围的炉料层中形成坩埚。
电极所处的部位通常是高功率密度区域。
由于电炉中的电热功率分布是很不均匀的,且是动态曲线,因此温度分布也就很不均匀。
在生产中的电极应当是中埋,这时的工作电阻相对稳定,电热功率比较稳定,炉料的热转换平稳,各部都能加热。
熔炼中的炉料加热和电热转换同时在各产层中进行。
属内热源加热、热阻小、热效率高。
一般热效率在0.6-0.8范围内。
物料的熔化是电热转换和热传导,热效率的综合效果