原油储罐的腐蚀机理研究及防护技术现状.docx
《原油储罐的腐蚀机理研究及防护技术现状.docx》由会员分享,可在线阅读,更多相关《原油储罐的腐蚀机理研究及防护技术现状.docx(16页珍藏版)》请在冰豆网上搜索。
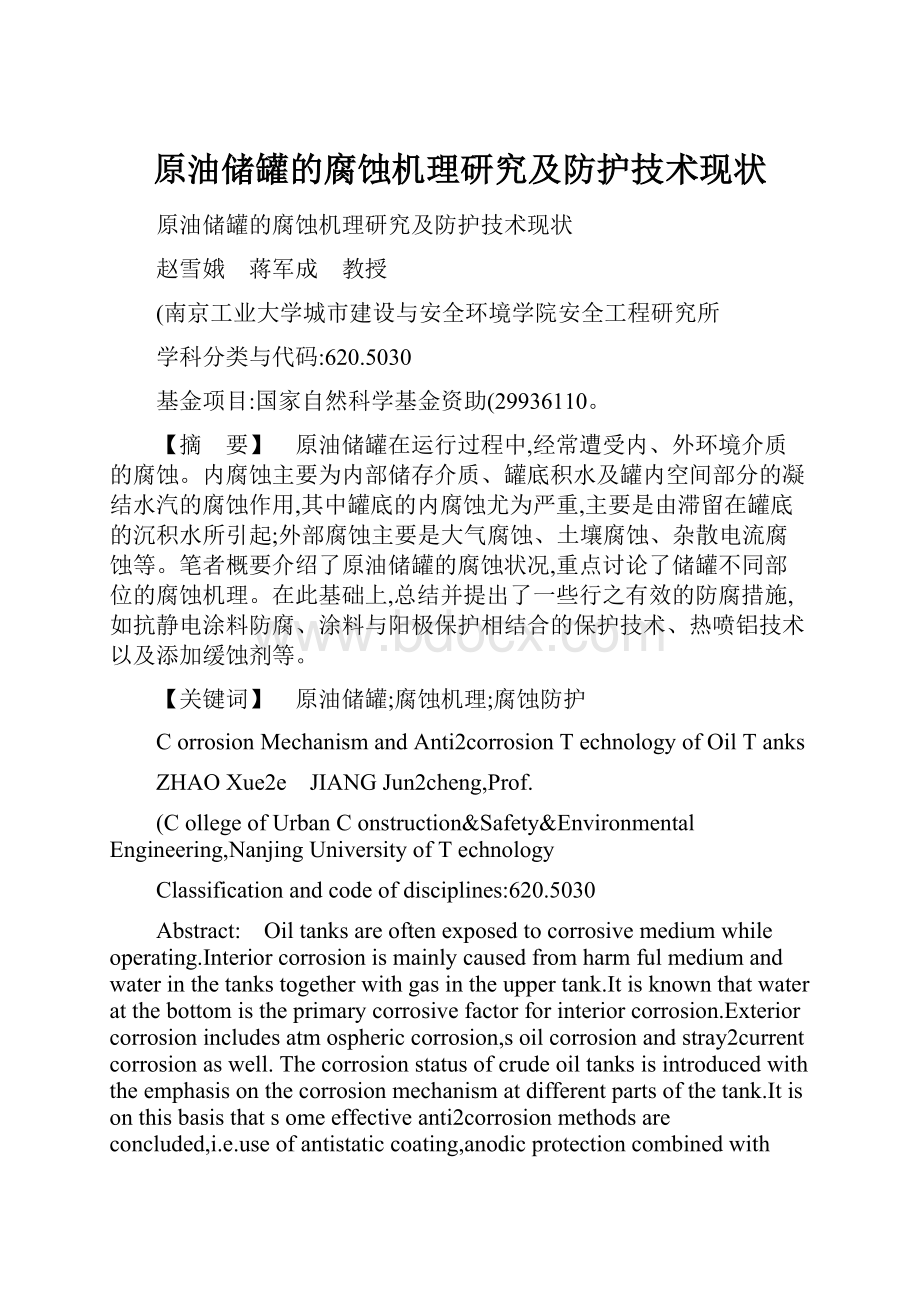
原油储罐的腐蚀机理研究及防护技术现状
原油储罐的腐蚀机理研究及防护技术现状
赵雪娥 蒋军成 教授
(南京工业大学城市建设与安全环境学院安全工程研究所
学科分类与代码:
620.5030
基金项目:
国家自然科学基金资助(29936110。
【摘 要】 原油储罐在运行过程中,经常遭受内、外环境介质的腐蚀。
内腐蚀主要为内部储存介质、罐底积水及罐内空间部分的凝结水汽的腐蚀作用,其中罐底的内腐蚀尤为严重,主要是由滞留在罐底的沉积水所引起;外部腐蚀主要是大气腐蚀、土壤腐蚀、杂散电流腐蚀等。
笔者概要介绍了原油储罐的腐蚀状况,重点讨论了储罐不同部位的腐蚀机理。
在此基础上,总结并提出了一些行之有效的防腐措施,如抗静电涂料防腐、涂料与阳极保护相结合的保护技术、热喷铝技术以及添加缓蚀剂等。
【关键词】 原油储罐;腐蚀机理;腐蚀防护
CorrosionMechanismandAnti2corrosionTechnologyofOilTanks
ZHAOXue2e JIANGJun2cheng,Prof.
(CollegeofUrbanConstruction&Safety&EnvironmentalEngineering,NanjingUniversityofTechnology
Classificationandcodeofdisciplines:
620.5030
Abstract:
Oiltanksareoftenexposedtocorrosivemediumwhileoperating.Interiorcorrosionismainlycausedfromharmfulmediumandwaterinthetankstogetherwithgasintheuppertank.Itisknownthatwateratthebottomistheprimarycorrosivefactorforinteriorcorrosion.Exteriorcorrosionincludesatmosphericcorrosion,soilcorrosionandstray2currentcorrosionaswell.Thecorrosionstatusofcrudeoiltanksisintroducedwiththeemphasisonthecorrosionmechanismatdifferentpartsofthetank.Itisonthisbasisthatsomeeffectiveanti2corrosionmethodsareconcluded,i.e.useofantistaticcoating,anodicprotectioncombinedwithcoating,aluminumthermalspraying,additionofcorrosioninhibitorandsoon.
Keywords:
Oiltanks Corrosionmechanism Corrosionprotection
1 引 言
腐蚀、磨损和断裂是材料和构件失效的三大主要形式。
就腐蚀来说,往往会造成重大经济损失、人员伤亡和环境污染等灾难性后果,1969年英国Hoar报告报道,英国每年因腐蚀造成的经济损失估计不少于13.65亿英磅[1]。
美国在1992年发表在ASM手册B卷的数字报道,美国每年腐蚀造成1700亿美元的经济损失[2]。
我国对腐蚀损失所做的统计表明,腐蚀造成的损失约占国民经济的3%,对于石油与化工行业尤其严重,约占6%左右。
近年来,石油工业发展速度不断加快,储罐的数量持续增加,因在服役过程中经常受到各种有害介质的腐蚀而导致的安全运行问题日益突出。
有关调查表明:
绝大多数储罐损坏是由腐蚀引起的,既有外腐蚀也有内腐蚀。
原油本身并不腐蚀金属材质,但原油中含有一些腐蚀性杂质,如无机盐、硫化物、氮化物、有机酸、氧、二氧化硫和水分等,这些杂质含量虽少,但危害性很大。
另一方面,随着原油消耗量的不断提高,国产原油已经不能满足国内市场的需要,许多企业开始进口国外原油。
但国外原油,尤其是中东的原油日益劣化,呈高酸、高硫、高含水量变化趋势,更加重了油罐内的腐蚀。
原油储罐的腐蚀不仅缩短了油罐正常的使用寿命,而且腐蚀产物进入油品后将造成炼油后续工序催化剂中毒,对成品油质量造成不良影响,且一旦油罐腐蚀穿孔造成原油外泄,不但造成环境污染,还有可能造成重大火灾及爆炸事故,影响生产的正常运行。
天津石化公司石化厂的一台30000m3原油储罐,于1996年投用,主体材质为Q235A,壁厚24mm,1998年7月,该罐侧部出现泄漏。
开罐后,发现罐体离水平高度15m以下,出现大面积蚀坑,点蚀深度大小不一,底板上有大面积疏松的片状腐蚀。
茂名石化公司2000年和2001年,在原油罐区,连续发生突发原油泄漏事故,经现场分析和相应测试,均为硫化物腐蚀开裂导致,造成油罐罐体焊缝损伤,导致泄漏。
某公司曾针对原油储罐的运行情况作过专门的统计,统
第15卷第3期2005年3月
中国安全科学学报
ChinaSafetyScienceJournal
Vol.15No.3
Mar.2005
计资料显示,原油储罐投用2~3年后,罐体均出现程度不同的腐蚀,并有38%的油罐出现过穿孔漏油,60%的油罐受到硫酸盐还原菌的严重污染。
腐蚀破坏形式及部位如图1所示。
储罐多在罐底部和顶部腐蚀最为严重,罐底板及底圈壁板腐蚀速度>0.15mm/年,并有大面积腐蚀麻坑,深度达1~3mm不等,严重点蚀处已有穿孔,孔径多数在5~10mm,有些孔径在20~
100mm[3]。
a—大面积麻坑;
b—局部点蚀;
c—点蚀穿孔;
d—轻微腐蚀
图1 储罐破坏形式及部位
因此,加强对原油储罐腐蚀机理的研究,找出造成腐蚀的关键所在,提出经济合理的防护方法,以减少泄漏事故的发生显得尤为重要,并且日益引起石化企业的关注。
2 原油储罐腐蚀类型及机理
2.1 油罐气相部位
21111 二氧化碳腐蚀
二氧化碳溶于水形成弱酸,基本化学反应式如下:
CO2+H2OH2CO3
H2CO3+Fe
FeCO3+H2↑
阳极反应:
FeFe2++2e-阴极反应:
H2CO3
H+
+HCO3
-
2H+
+2e
-H2↑
二氧化碳常常造成坑点腐蚀、片状腐蚀等局部腐蚀。
21112 硫腐蚀
硫腐蚀以元素硫和硫化氢为主[4]。
在无水的情况下,油品中的硫化氢对金属无腐蚀作用,湿硫化氢或与酸性介质共同存在时,腐蚀速度会成倍增加[5]
。
硫化氢在水中发生的电
离式如下:
H2SH++HS-HS-H++S2-在湿硫化氢的腐蚀环境中的氢离子,硫氢根离子,硫离子和硫化氢对金属腐蚀为氢去极化作用,其反应式如下:
阳极反应:
Fe
Fe
2+
+2e
-
Fe2++S2-FeS或Fe
2+
+HS
-
FeS+H+
+e
-
阴极反应:
2H++2e-
H2
硫化物腐蚀产物多以固态形式出现,在静态或流速不太大的环境和适当的pH下,硫化物能在罐壁内表面上形成膜,在适当的条件下,甚至会导致储罐自燃事故的发生[6,7]。
2.2 油罐的储油部位
该部位直接与原油接触,罐壁上粘结了一层相当于保护膜的原油,因而腐蚀速率较低,一般不会造成危险,但是由于油品内和油面上部气体空间中含氧量的不同,形成氧浓差电池而造成腐蚀。
当含氧量由0.02mg/l增加到0.065mg/l时,金属的腐蚀速度将增加5倍,含氧量增加1mg/l时,腐蚀速度将增加20倍。
罐液位的变化及搅拌作用,更加速了腐蚀。
2.3 油罐内底板
进储罐的原油中夹杂有大量的水分,这些水分经过长时间的沉积,在罐底逐渐形成沉积水。
虽然,原油储罐都设计有排水管,但由于排水管的中心线一般比罐底约高300mm,所以罐底至少始终有200~300mm的水;再加上受液体流动
的粘滞性及罐底板不平等因素的影响,罐底长期处于浸水状态;气相水蒸气的凝结水下沉也沉积在罐底部。
沉积水中含有大量的氯化物、硫化物、氧、酸类物质,成为较强的电解质溶液,产生了电化学腐蚀。
根据罐底沉积物、沉积水的化学成分分析,可推断罐底的腐蚀类型及过程如下:
(1硫酸盐还原菌的腐蚀。
微生物对原油的腐蚀研究
已经很充分,其中硫酸盐还原菌(SRB最具有代表性,硫酸盐还原菌腐蚀的典型特征是孔蚀[8],近年来对其腐蚀机理的研究得到进一步的发展[9,10],机理如下:
它在厌氧条件下能够利用附着于金属表面的有机物作为碳源,并利用细菌生物膜内产生的氢,将硫酸盐还原成硫化物:
SO42-+8H
S2-+4H2O
罐底水溶液中氢原子不断被硫酸盐还原菌代谢反应消耗,结果造成罐底防腐层部分脱落,钢板表面电化学腐蚀过程中的阴极反应不断进行下去:
Fe2++S2-FeS↓(黑色铁锈
Fe
Fe2++2e-
从而促进了罐底钢板表面的阳极离子化反应,加速了罐底板的腐蚀过程。
据国外资料报道,活性硫化氢的存在,使得平均腐蚀速率提高到0.5~1.5mm/年,使得罐龄降低3~5年[11]。
(2硫化物、氯化物对罐底的电化学腐蚀:
Fe2++S2-FeSFe2++2Cl-FeCl2Fe2++SO42-FeSO4
(3溶解氧对罐底产生的电化学腐蚀:
Fe2++Fe3++O2
FeO,Fe3O4・nH2O,Fe2O3等。
(4缝隙腐蚀。
原油罐立柱下的底板,在静止状态下主
要发生缝隙腐蚀,但原油罐在灌装、提取、液流运动等正常状
・
501・第三期 赵雪娥等:
原油储罐的腐蚀机理研究及防护技术现状
态下,都能造成立柱与底板的摩擦与振动,磨损就成为主要的破坏因素,缝隙腐蚀的又加剧了腐蚀磨损过程,在这种机械磨擦和腐蚀的联合作用下,导致了立柱底板的腐蚀穿孔。
2.4 储罐外壁
储罐外壁主要发生大气腐蚀。
原油储罐所处的大气环境中的氧、水蒸气、二氧化碳可导致原油储罐罐体的腐蚀,同时由于原油储罐的周边环境一般为石油化工企业,因此,罐体还可能受到工业大气中二氧化硫、硫化氢、二氧化氮等有害气体所引起的腐蚀。
大气中的水气会在金属设备表面冷凝而形成水膜,这种水膜溶解了大气中的气体及其他杂质,起到电解液的作用,使金属表面发生电化学腐蚀。
储罐外壁的腐蚀发生过程是:
阳极反应:
Fe
Fe2++2e-阴极反应:
O2+2H2O+4e-4OH-总反应:
2Fe+2H2O+O2
2Fe(OH2↓
氢氧化亚铁在大气环境下转变为三氧化二铁或四氧化三铁,形成疏松的氧化层。
在锈层表面,空气中的氧与水不断进行阴极反应,而在锈层与金属的结合面,则不断进行阳极反应,这种氧浓差电池引起的大阳极小阴极反应,又由于氯离子的存在,反应进行得相当快,从而形成局部腐蚀,最终导致穿孔。
在罐顶凹陷处、焊缝凹陷处和其他易积水的地方,大气腐蚀尤为严重
[12,13]
。
2.5 罐底下表面腐蚀
21511 土壤腐蚀
原油储罐的土壤腐蚀实际是电化学腐蚀,其阴极过程为还原反应:
有氧条件:
O2+2H2O+4e-OH-缺氧条件:
SO42-+4H2OS2-+8OH-
其阳极过程为氧化反应:
Fe
Fe2++2e-Fe2++2OH-Fe(OH2(绿色腐蚀产物
2Fe(OH2+H2O+1/2O2
Fe(OH3
Fe(OH3FeOOH+H2O(赤色腐蚀产物Fe(OH3Fe2O3・3H2O(黑色腐蚀产物
Fe2++CO32-FeCO3Fe2++S2-FeS
21512 杂散电流腐蚀
罐区是地中电流较为复杂的区域。
当站内管网有阴极保护而罐未受保护时,则可能形成杂散电流干扰影响。
位于电气化铁路、大型电气设备附近的油罐,其底板会因杂散电流而腐蚀。
21513 氧浓差电池腐蚀
在罐底,氧浓差主要表现在罐底板与砂基础接触不良,如满载和空载比较,空载时接触不良;再有罐周和罐中心部位的透气性差别,也会引起氧浓差电池,该中心部位成为阳
极而被腐蚀。
目前,国内外对于储罐大气腐蚀,土壤腐蚀以及内壁水相的腐蚀机理研究已经很充分,但对于储罐内气相部位以及气液交界部位的研究虽有报道,却仅停留在机理探讨阶段,缺乏相关试验测试,这将是今后该领域研究的重点。
3 防腐措施
在生产实践中用得最多的原油储罐防腐蚀技术大致可分为合理选材、抗静电涂料防腐、热喷铝技术等7个种类。
3.1 合理选材
宜选用含碳量小于0.2%和硫、磷含量低于0.5%的钢材,适当增加腐蚀严重部位如罐底和罐顶的厚度,但不应超过钢板总厚度的20%。
3.2 抗静电涂料防腐
油料在流动、过滤、搅拌、喷射和灌注等过程中可能产生静电荷,携带静电荷的流体进入储罐后发生电荷积聚,引起电位升高,如果油料中的静电荷不能迅速释放,则该电位上升到超过安全极限值,可能发生火灾或爆炸事故。
因此,所选涂料除应具有良好的耐油、耐水性、柔韧性,附着力强,抗冲击、抗老化等性能之外,还应满足抗静电的要求,即其电阻率在108Ω以下[14]。
3.3 涂料与阳极保护相结合的保护技术
单一的涂层可以对大面积基体金属起到保护作用,但对涂层缺陷处不但不能起到保护作用,还会形成大阴极小阳极而加速涂层破损处的腐蚀;涂层与牺牲阳极联合保护可以对涂层破损处达到有效保护,并且联合保护比单纯的阴极保护节省牺牲阳极用量,电流分散效率好,是行之有效的保护办法[15,16]。
3.4 热喷铝技术
针对罐内壁腐蚀较严重的情况,可采用金属火焰喷镀的方法对罐内壁进行喷铝。
喷铝涂层在大气中极易产生致密的氧化膜,提高了稳定性。
此项技术可以避免罐体与氧气和
H2S发生反应,阻止油罐的腐蚀。
3.5 添加缓蚀剂
缓蚀技术是减轻石油化工行业中各类油、气、水储罐内腐蚀的有效方法[17],油罐用缓蚀剂根据用途不同分为3类。
其一为防止油罐底部沉积水腐蚀用的水溶性缓蚀剂;其二为防止与油层接触的金属腐蚀的油溶性缓蚀剂;其三为油罐上部与空气接触的金属防腐蚀用气相缓蚀剂。
3.6 合理的结构防腐蚀设计以减轻或防止金属
腐蚀
储罐的设计除了满足工艺上的要求外,还应当考虑尽量
・
601・中国安全科学学报ChinaSafetyScienceJournal 第15卷
2005年
减少腐蚀条件的出现,避免出现死角及流动不畅,在进口处尽量减少冲蚀等。
对于新设计建造的油罐,建议采用外浮顶油罐储油技术,可以稀释、去除硫化氢气体和含硫水份,从而有效防治腐蚀的发生。
3.7 开发石油脱硫新技术
原油高含硫是事故发生的重要原因,为了预防事故的发生,尽量采用含硫量低的原油,对于高含硫原油要采取措施降低硫含量,在工艺上可采取“一脱四注”技术[18]。
目前世界上普遍采用的原油脱硫方法是加氢脱硫。
加氢脱硫投资大,操作费用高,为此人们不断研究新的脱硫方法,生物脱硫即是其中之一[19]。
生物脱硫属于高新技术,符合21世纪清洁生产发展方向,必将成为21世纪炼油工业发展的新方向。
4 结论及建议
(1原油储罐的内腐蚀主要是由滞留在罐底的沉积水
造成的,氯离子的存在加速了腐蚀。
罐底无氧条件很适合硫酸盐还原菌的生长,引起了细菌腐蚀。
采用涂料与阳极保护相结合的保护技术,可以达到长效防护。
油相腐蚀一般不严重,为了防止静电造成火灾及爆炸事故,罐壁油相区应采用导静电涂料。
由于原油罐罐顶的特殊性,罐顶不适宜使用玻璃钢内衬,而应采用涂料。
(2储罐外表面主要是大气腐蚀,可进行金属喷涂与涂
料的复合保护。
(3原油储罐长期受到各种类型腐蚀的威胁,为了减少
腐蚀及经济损失,实现安全、文明生产,建议实施在线监测,使防蚀工作更精致、有效。
(收稿:
2004年9月;作者地址:
江苏省南京市中山北路200号;南京工业大学城市建设与安全环境学院;邮编:
210009
参考文献
1 魏宝明主编.金属腐蚀理论及应用[M].北京:
化学工业出版社,19842 ASMHandbook[M],Vol.13:
Corrosion.USA:
ASMInternational,1992
3 王建新.玻璃钢防腐在钢储罐大修理中的研究与应用[A].腐蚀科学与防腐蚀工程技术新进展[M].北京:
化学工业出
版社.1999:
532~533
4 王宝辉.石油原油贮罐自燃的化学机理和控制技术[J].中国安全科学学报,2003,13(1:
23~255 梁仕普.含硫原油加工中的设备防腐[J].炼油设计,1998,28(4:
40~42
6 蒋军成,王三明等.含硫油品储罐自燃机理及事故原因分析[J].安全与环境学报,2001,1(2:
7~10
7 王志荣,蒋军成等.含硫油品储罐腐蚀自燃理论及实验研究[J].石油化工高等学校校报,2002,15(4:
65~69
8 G.H.Booth,A.K.Tiller.CathodicCharacteristicofMildSteelinSuspensionsofSulfateReducingBacteria[J].CorrosionScience.
1993,8:
583~600
9 V.L.Rainha,I.T.E.Fonseca.KineticStudiesontheSRBInfluencedCorrosionofSteel:
AFirstApproach[J].CorrosionScience,
1997,39(4:
807~813
10 刘宏方.硫酸盐还原菌生物膜下钢铁腐蚀研究[J].油田化学,2000.3(4:
13~16
11 阎永贵,吴建华,陈光章.原油储罐内底板的腐蚀防护现状与展望[J].腐蚀与防护,2002,23(5:
119~20112 姚杰,俞中华.电化学保护在某原油储罐中的应用[J].腐蚀与防护,2001,22(7:
307~30813 王敏.原油储罐内壁腐蚀防护[J].装置・设备,1998,15(2:
17~1814 张磊.原油储罐的腐蚀与防护[J].腐蚀与防护,2001,22(2:
72~77
15 吴迪,郭丽.原油储罐腐蚀与长效综合保护[J].石油化工设备,2003,32(1:
52~5316 刘玲莉.原油储罐底板的腐蚀与阴极保护防腐[J].石油工程建设,1994,4:
29~33
17 M.A.Khalifa,M.El2batoui,F.Mahgoub,A.BakrAknish.CorrosionInhibitionofSteelinCrudeOilStorageTanks[J].Material
andCorrosion,2003,54:
251~258
18 王志荣,蒋军成等.焦化汽油储罐腐蚀模拟试验研究[J].工业安全与环保,2002,28(5:
25~2819 杜长海,贺岩峰等.生物催化石油脱硫技术进展[J].化工进展,2002,21(8:
569~571,528
・
701・第三期 赵雪娥等:
原油储罐的腐蚀机理研究及防护技术现状
安全科学技术人才交流园地
本期
论文作者简
介
宋 瑞 北京交通大学交通运输
学院特聘教授,中国运筹学会会
员。
1971年2月出生,1997年获交
通运输规划与管理专业工学博士
学位,1999年于北京交通大学交通
运输工程博士后流动站出站后留
校并被评为副教授。
主要研究方向为城市公共交通规划与管理、智能运输系统(ITS、城市轨道交通、交通安全技术与管理等。
主持并参加国家自然科学基金、霍英东青年教师基金、国家教委博士点基金、科技部、铁道部及北京市等20余项科研项目的研究工作。
近几年在国内外刊物及会议上发表学术论文40余篇,主编《交通运输设备》、
《城市公共交通运营调度管理》、参编《智能运输系统》等论著。
赵雪娥 南京工业大学安全技术
与工程专业博士研究生,
中国腐蚀与防护协会会员。
山西翼城人,
1974年2月生。
1995年7月本科毕
业于南京化工大学腐蚀与防护专
业。
1995年7月~2001年7月在中
国(洛阳第一拖拉机股份有限公司从事中(小型拖拉机覆盖件及底盘件涂装工艺以及辅助材料定额管理工作,被聘为工程师。
2001年考取南京工业大学安全技术与工程专业硕士研究生,主要从事新建、改建、扩建项目的安全卫生预评价工作。
2003年开始攻读博士学位,主要研究方向为化工装置安全技术与可靠性分析过程。
参与了国家自然科学基金项目“典型化工过程灾害性事故预测与防治技术基础研究”和教育部骨干教师资助计划项目的研究工作。
ALIHessami 教授,阿特金斯
铁路公司控制与系统部门主任工
程师,欧洲系统安全协会主席,前
英国线路公司(Railtrackplc系统
审查委员会主席,现任IEEE系统、
人和控制论学会英国和爱尔兰地
区主席,英国电气工程师学会会士,伦敦大学客座教授,CEng英国注册工程师,FEANI2(法国欧洲工程师,英国CENELEC(欧盟电子技术标准化委员会TC9X“系统安全保障和整体观念”首席专家,CENELEC2EN50126标准的评估和建模负责人,系统安全理论和技术实践专家。
在关键型工业应用计算机控制系统的设计和开发领域颇有建树,在系统安全保证方面,享有极高的国际声誉,开发的七步风险评估框架理论已经成为英国铁路行业“黄皮书”———《工程安全管理》重要的内容之一,该书已作为铁路工业系统安全管理的指导用书。
在全世界范围内,发表了大量的论文专著。
叶洲元 湖南科技大学教师,中
南大学博士研究生,主要研究方向
为控制爆破、采矿工程技术研究。
湖北蕲春人,1977年生。
2000年毕
业于包头钢铁学院,2003年于武汉
科技大学获硕士学位。
先后参与
了大冶灵乡城市拆除控制爆破、水工爆破、湘潭电厂拆除控制爆破、武钢大冶铁矿尖林山矿体破碎带、粉矿带支护优化研究、乌龙泉矿西区爆破参数的优化与边坡稳定性研究、铁门坎井下安全回采的研究、武汉市九峰乡爆破震动监测工程、平顶山深井地压研究等多项工程及“973”国家重点课题。
发表论文10余篇,其中被EI检索一篇。