年产40万吨氧化钙生产线工程项目初步设计文字修改.docx
《年产40万吨氧化钙生产线工程项目初步设计文字修改.docx》由会员分享,可在线阅读,更多相关《年产40万吨氧化钙生产线工程项目初步设计文字修改.docx(60页珍藏版)》请在冰豆网上搜索。
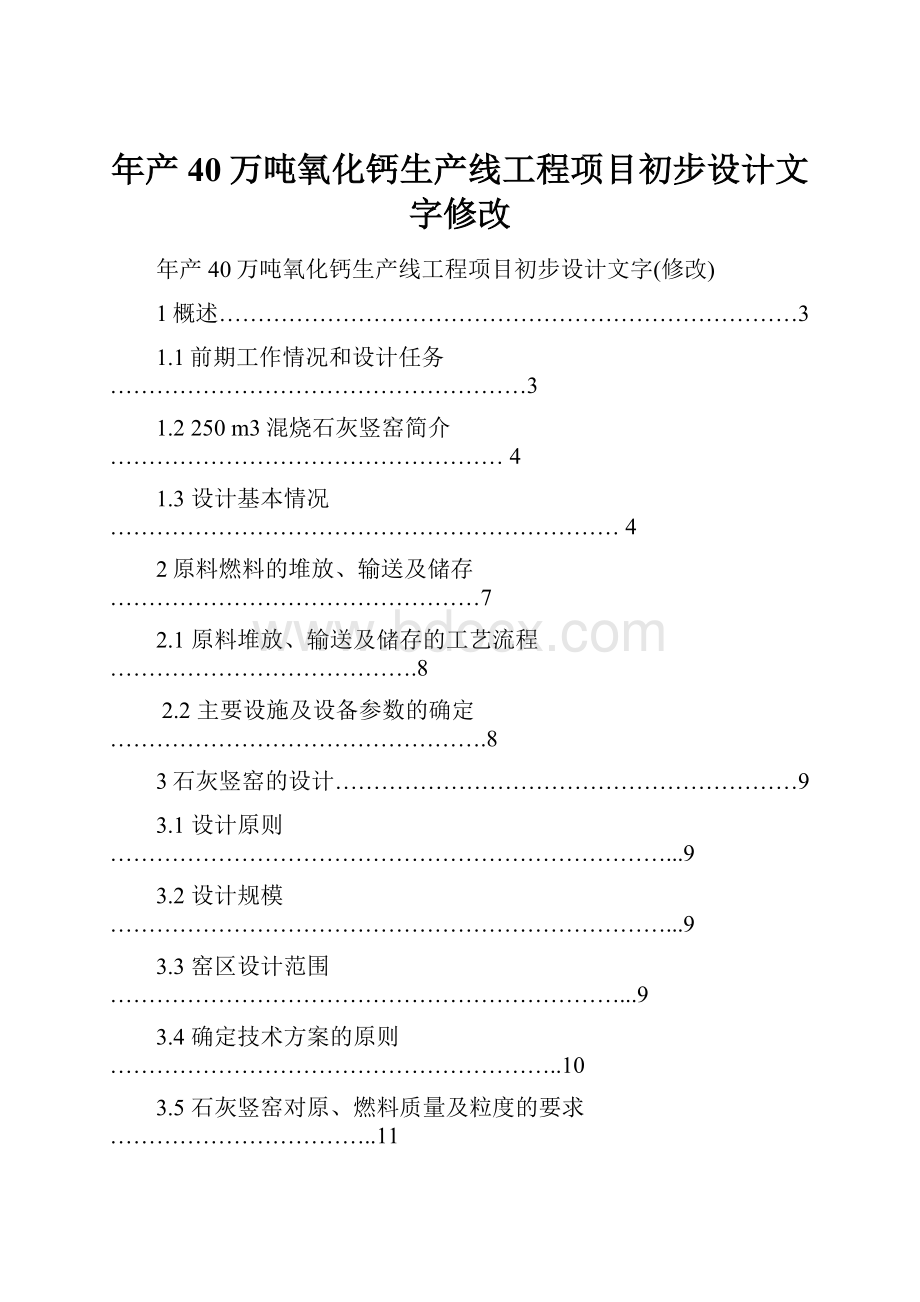
年产40万吨氧化钙生产线工程项目初步设计文字修改
年产40万吨氧化钙生产线工程项目初步设计文字(修改)
1概述…………………………………………………………………3
1.1前期工作情况和设计任务………………………………………………3
1.2250m3混烧石灰竖窑简介……………………………………………4
1.3设计基本情况…………………………………………………………4
2原料燃料的堆放、输送及储存…………………………………………7
2.1原料堆放、输送及储存的工艺流程………………………………….8
2.2主要设施及设备参数的确定………………………………………….8
3石灰竖窑的设计……………………………………………………9
3.1设计原则………………………………………………………………...9
3.2设计规模………………………………………………………………...9
3.3窑区设计范围…………………………………………………………...9
3.4确定技术方案的原则…………………………………………………..10
3.5石灰竖窑对原、燃料质量及粒度的要求……………………………..11
3.6石灰窑的原、燃料消耗量……………………………………………11
3.7设计范围内的工艺流程图……………………………………………..11
3.8竖窑工艺及本次设计所采取的技术措施和技术特点………………..12
4公用及辅助生产设施……………………………………………...18
4.1供配电及电气传动……………………………………………………18
4.2仪表检测和控制………………………………………………………23
4.3除尘及通风……………………………………………………………25
4.4热力设施……………………………………………………………....28
4.5给水排水………………………………………………………………28
5总图运输…………………………………………………………...29
5.1设计依据………………………………………………………………29
5.2厂区位置及四邻………………………………………………………29
5.3总平面布置……………………………………………………………29
5.4竖向布置………………………………………………………………29
5.5运输……………………………………………………………………30
6土建部分…………………………………………………………..30
6.1设计内容………………………………………………………………..30
6.2建材及施工条件………………………………………………………..31
6.3主要建筑物概述………………………………………………………31
7能源及环境保护…………………………………………………..32
7.1设计依据……………………………………………………………..32
7.2能源…………………………………………………………………...32
7.3环境保护……………………………………………………………...33
8消防、安全及工业卫生…………………………………………..34
8.1设计依据…………………………………………………………….34
8.2消防设计…………………………………………………………….34
8.3安全与工业卫生…………………………………………………….35
9施工条件、方法和进度
9.1工程概况……………………………………………………………..37
9.2施工场地条件………………………………………………………....37
9.3施工力量…………………………………………………....37
9.4主要工程项目的施工方法……………………………………………37
9.5施工现场总平面布置方案…………………………………………….38
9.6施工进度安排………………………………………………………….38
10劳动定员及岗位编制……………………………………………...38
10.1劳动定员……………………………………………………………….38
10.2岗位编制………………………………………………………………..38
11投资概算…………………………………………………………...39
11.1概况…………………………………………………………………......39
11.2编制依据及计算标准……………………………………………….....39
11.3氧化钙生产线投资构成…………………………………………….....39
12经济评价…………………………………………………………...50
12.1概述………………………………………………………………….....50
12.2技术经济评价结论……………………………………………………..52
附图13.7-1工艺流程简图
附图25.3工艺平面布置图
附图35.4工艺立面图
1概述
安徽XX矿业股份有限公司(以下简称公司或XX公司)坐落在安徽XX市,拟建厂区位于XX市XX区XX镇XX境内,地处长江XX水道XX南汊右岸XX一侧。
距XX石灰石矿约26公里,距XX水运距离234公里,距XX水运距离为672公里。
该公司生产的活性石灰主要供给XXXX炼铁厂烧结配矿使用。
该公司从XXXX的石灰需求量考虑,分两期共建250m3的活性石灰竖窑12座,一期工程建设两条生产线,一条3座,共6座,年产活性石灰40万吨。
技术采用XXXX石灰窑技术,设计由XXXX控制工程有限公司完成,详见《合同》(以下简称合同)。
1.1前期工作情况和设计任务
前期工作情况:
根据XX矿业股份有限公司对市场的调查和资金情况,我们前期与XX矿业股份有限公司进行了多次技术交流,共同商定了XX矿业股份有限公司氧化钙生产线工程的规模、主要技术经济指标以及工程的实施步骤。
并根据XX矿业股份有限公司的实际情况和投资情况,确定了本工程的设计范围以及设计依据,详见《合同》。
新建石灰竖窑的设计分工及设计范围:
根据双方协商确定设计合同如下:
XXXX控制工程有限公司负责设计的主要内容为:
原燃料的供配料;石灰窑煅烧出灰系统;石灰窑窑体低压配电设计及辅助设施的工程设计,并提供专有专利设备,及技术服务等。
1.2250m3混烧石灰竖窑简介
本设计选用XXXX公司250m3无烟煤混烧石灰竖窑。
该竖窑采用精密的补偿称量配料,保证原燃料配比稳定精确;窑顶采用旋转布料器,使入窑的原燃料分布均匀;采用四层温度检测,使冷却带、焙烧带、预热带相对稳定,使石灰分解完全;窑下出料采用圆盘出料机连续出料,并采用两段密封阀锁气,使竖窑能连续鼓风,窑内含尘气体不外溢,同时保证竖窑热工制度合理稳定。
从配料、上料、布料直到石灰烧成出窑全过程采用PLC计算机进行控制操作。
竖窑燃料要求烧无烟煤,无烟煤中固定炭≥85%,灰分≤14%,最大粒度不要超过50mm,最小粒度不要小于15mm,粒度20~40mm,>40mm和<20mm各量不要超过5%,S<0.5%。
入窑石灰石CaO含量≥53%,粒度40~80mm,最大粒度不要超过90mm,最小粒度不要低于30mm,在上述原燃料条件下,可生产出CaO≥90%,活性度300ml以上的活性石灰。
在一般原燃料条件情况下也可生产出活性度280ml左右的高等级石灰。
公称容积250m3竖窑砌砖内径4米,有效高度(从进风口到上料面)21.9米,设计利用系数0.8t/m3.d,每座窑每天可生产石灰200t,年工作日按333天计算,每窑每年可生产石灰6.67万t,六座窑年生产石灰能力40万t。
1.3设计基本情况
1.3.1原料破碎、储存及输送
本工程所用原料是XX公司在XX矿生产加工,最好运到本工程现场堆料场的的石灰石原料,原料粒径为30mm~60mm、60mm~90mm。
粒径规格不同的石料分别堆放使用,其中不符规格的碎石及灰土等杂质不大于5%。
合格干净石灰石由皮带机送到石灰竖窑混配仓。
石灰石堆场为露天堆场;无烟煤堆场全部为仓库堆场。
石灰石堆场考虑储料天数为10天;40万吨窑炉生产规模石灰石露天堆场拟建不小于4600m2。
无烟煤仓库堆场考虑可堆放无烟煤储料天数为15天;拟建无烟煤堆场面积不小于2700m2。
受料斗考虑铲车受料,受料斗内宽5m×4m。
上料皮带选择皮带机型号为TD75型B800。
混配仓按三座竖窑一组生产配置,一座窑对应一个石灰石仓、一个无烟煤仓。
石灰石仓容积储量按8小时的用量考虑,每班上料1次,3条窑每班上料3次,石灰石单仓有效容积为100m3。
无烟煤仓有效容积为:
50m3,每天上料一次,一次可储存无烟煤50吨。
1.3.2石灰竖窑
振动给料机从混配仓下口振动给料,经称量混匀后提升至窑顶,经布料器进入窑内煅烧,成品经圆盘卸灰机和两段阀卸出后由皮带机运至斗式提升机,进入统灰仓,再按要求进入后续石灰加工工序,磨粉筛分,最后装车、装船外运。
250m3石灰竖窑主要性能指标:
窑炉内径为φ4000mm;有效高度21.9m;煅烧温度<1200℃;废气出窑温度<200℃;产品出窑温度<70℃;窑炉利用系数为0.8t/m3.d;热耗为900×4.186kJ/kg石灰;单窑石灰日产200t;石灰年产6.67万t;石灰活性度>300ml;生过烧率5~7%。
单窑石灰石日消耗量:
340t,六条窑年消耗量:
68万t;无烟煤单窑日耗量:
26t,六条窑年消耗量:
5.2万t。
1.3.3公用及辅助生产设施
本设计主要内容有:
上料系统、竖窑本体、出灰系统的自动控制及与其配套的380V低压配电系统。
主厂房及设备的防雷、接地、窑体照明系统以及辅助的电气部分的传动、照明设计。
本设计在现场新建一个配电室(两层),一层内放置低压柜、变频器柜;二层放置PLC柜、计算机操作台等。
低压配电电压AC380V;控制电源、仪表电源、PLC电源:
AC220V;照明电压:
AC220V。
检修电源:
AC380V/AC220V。
总装机容量:
2000KW。
电力拖动:
所有电机采用三相交流异步电动机。
混料皮带、煤皮带、石灰石振动给料机、煤振动给料机、单斗提升机、布料器、圆盘出灰机、助燃风机采用交流变频拖动,其它部分采用常规拖动。
系统控制分为集中控制和机旁手动两种方式。
系统主要控制项目有:
原料上料;石灰石、煤的自动称量及两种物料的自动配料,自动混匀;单斗料车的自动上料;窑顶布料器九点布料;成品自动出灰等。
混配、料车、布料器、振动给料机、罗茨风机等需要调速的设备,采用交流变频调速器,并通过PLC给定速度值;在石灰竖窑窑顶、卷扬、混配处设置工业电视,监视器安装在主控室。
温度检测主要设有窑顶温度检测、上升管温度检测、窑体四层16点温度检测、出灰温度检测、窑顶压力检测、助燃风温度检测、风机压力检测、石灰石配料控制、煤配料控制、窑顶料位检测。
1.3.4总图运输
设计中考虑道路运输、原燃料和成品的运输,并考虑检修设备出入以及行车方便。
1.3.5土建
按6度进行抗震设计。
窑基础为钢筋混凝土基础,主控楼采用砖混结构,成品仓柱基础,混配仓柱基础以及一些支架基础。
1.3.6能源、环境保护
在设计中尽可能地考虑采用节能措施。
石灰生产过程中和辅助生产等系统中的各种能源消耗,按吨灰标准煤计算折合120Kg/t,远低于国内同类型石灰竖窑平均能耗160Kg/t。
在设计中考虑节能、安全、消防与工业卫生等,并充分考虑环境污染以及污染源进行达标排放。
2原燃、料的储存
根据250m3石灰窑生产要求,一座竖窑每天需要粒度合格的石灰石340吨,六座窑窑需石灰石2040吨;一座竖窑每天需要粒度合格的无烟煤约26吨,六座竖窑每天需要无烟煤156吨。
2.1原、燃料堆放、输送及储存的工艺流程
石灰竖窑生产所需合格原料堆放在石灰石、无烟煤料场,由铲车将石灰石和无烟煤分别装入石灰石受料斗和无烟煤受料斗内,经振动给料机将合格原料输送到上料皮带上,上料皮带将石灰石送至混配仓顶部,经卸料小车分别卸入不同窑窑对应的石灰石料仓和无烟煤料仓,从而完成原料的堆放、输送及储存。
2.2主要设施及设备参数的确定
1)原料堆场
原料堆场分为石灰石堆场及无烟煤堆场。
考虑当地气候及生产对原料的要求石灰石堆场分为露天堆场;无烟煤堆场全部为仓库堆场。
(1)石灰石露天堆场,根据现场地形,考虑车辆通行及料堆倒运等因素,石灰石堆场考虑储料天数为10天;石灰石露天堆场4600m2(一期40万吨工程)。
(2)无烟煤仓库堆场:
无烟煤仓库堆场考虑可堆放无烟煤储料天数为15天;一期建无烟煤仓库堆场面积2700m2。
2)受料斗
考虑铲车受料,受料斗接料口尺寸为5m×4m。
3)振动给料机
石灰石用振动给料机:
电机0.75KW×2输送量:
Q=100m3/h。
4)上料皮带
考虑到皮带的运输能力,选择上料皮带型号为TD75B800。
5)混配仓
一条生产线的混配仓按三座竖窑生产配置,每座窑对应一个石灰石仓和无烟煤仓。
混配仓楼体为钢结构。
石灰石仓容积的确定:
考虑生产及投资经济等因素,石灰石仓储量按1个班的用量考虑,则每天上料三次,共用3~4小时,即可满足生产要求。
单窑每班石灰石用量340÷3=113吨,石灰石堆比重按1.4t/m3计,单仓石灰石仓有效容积为:
113÷1.4=81m3。
无烟煤仓有效容积为:
50m3,无烟煤堆比重按1t/m3计,一次可储存无烟煤50吨。
而一座竖窑每天需要无烟煤26吨,因此无烟煤每两天上料一次,单仓用0.5小时三个仓用1.5~2小时,就能满足一座竖窑生产的需要。
3.石灰竖窑的设计
3.1设计原则
本设计主要依据前期双方达成的技术协议和有关原则进行,详细内容见《合同》。
3.2设计规模
根据《合同》设计250m3的石灰竖窑6座,考虑上二期石灰竖窑的场地和运输等因素以及预留石灰深加工场地。
一期石灰竖窑设计日产石灰1200吨/天·座,年产石灰40万吨。
3.3窑区设计范围
从原料和无烟煤的混配仓下口开始至成品灰料仓为止,主要包括原燃料混料系统、石灰窑、成品整粒系统的生产装置及配套辅助设施。
3.4确定技术方案的原则
(1)、工艺技术装备达到国内外当代先进水平,生产优质高活性化石灰产品。
(2)、提供部分关键设备和标准、非标准设备图。
(3)、技术设备本着实用、经济、先进、可靠的原则,但功能不过剩。
(4)、在获得最佳投资效益的前提下,节省工程投资,注重整体优势和技术的系统平衡及协调。
(5)、厂址由XX矿业股份有限公司提供的可建场地范围内进行总平面布置。
(6)、立足以节能、降耗、降低产品成本为指导思想的设计意识,为降低石灰生产成本创造条件。
(7)、产品质量
本工程窑窑由XXXX设计,其主要性能指标如下:
窑炉内径:
φ4000mm
窑炉外径:
φ6000mm
有效高度:
21.9m
产品:
活性石灰
原料:
石灰石
燃料:
无烟煤
煅烧温度:
<1200℃
废气出窑温度:
<200℃
产品出窑温度:
<70℃
窑炉利用系数:
0.8t/m3.d
热耗:
900×4.186kJ/kg石灰
石灰产量:
单窑日产200t;六座窑年产200t×6×333天=40万吨
3.5石灰竖窑对原、燃料质量及粒度的要求
3.5.1石灰竖窑对石灰石质量及粒度的要求:
石灰石最佳粒度:
40~80mm。
超上下限的各不大于5%,但上限不得超过90毫米,下限不得超过30毫米。
石灰石质量要求:
CaO含量>53%。
石灰石泥土含量:
<0.2%
3.5.2石灰竖窑对无烟煤的要求:
无烟煤最佳粒度:
20~40mm。
超上下限的各不大于5%,但上限不超过50毫米,下限不小于15毫米。
无烟煤质量要求:
C固≥85%,灰份≤14%,S<0.5%;
无烟煤低发热值≥6500×4.186kJ/kg无烟煤
3.6石灰窑的原、燃料消耗量
3.6.1合格石灰石消耗量:
日消耗量:
340t×6=2040t
年消耗量:
68万t
3.6.2无烟煤消耗量:
(折成标煤)
日耗量:
24t×6=144t
年消耗量:
47952t
3.7设计范围内的工艺流程图(见附图3.7-1)
3.8竖窑工艺及本次设计所采取的技术措施和技术特点:
根据双方多次讨论、协商及签署的合同精神,确定初步设计。
3.8.1工艺流程及相关数据的确定:
石灰石和无烟煤堆场,经前端式装载机装入受料仓,由上料皮带机进入混配仓,经称量混匀后提升至窑顶,经布料器进入窑内煅烧,成品经圆盘卸灰机和两段阀卸出后由皮带机运至成品斗式提升机,进入统灰仓,再按要求进入后续石灰加工工序,磨粉筛分,最后装车装船外运。
主要建筑物有受料斗、混配仓、窑体、配电及主控室、成品料仓和除尘器。
各种工艺参数的确定:
(1)、窑炉有效容积250m3,利用系数0.8t/m3·d。
(2)、石灰石粒度40~80mm,无烟煤粒度20~40mm。
(3)、受料仓按前端式装载机上料设计。
(4)、上料按一班考虑,分三次运行,每次1小时,上料皮带机输送能力按100吨/小时考虑。
(5)、混配仓容积的确定。
按储存一个班113吨考虑,混配仓有效容积为113÷1.4=81(m3)。
(6)、装料周期的计算;每次(铲)装料量定为5吨,每小时需用石料113÷8=14.1(吨),装料频次为14.1÷5≈3次,三座窑需3x3=9次,则装料周期为60÷9=6.67(6分40秒),我们设装载机每装一铲需两分钟,则60X(2÷6.67)≈18,即每小时装载机工作18分钟即可保持物料平衡。
(7)、卷扬机主要参数:
电动机:
22kW
最大提升线速度:
0.82m/s
(8)、混配、窑顶布置形式按XXXX现行模式。
(9)、窑炉本体工艺参数:
有效容积250m3,窑膛内径φ4000mm,窑炉有效高度21.9m.预热带高度约为5.4m,煅烧带高度约为10m,冷却带高度约为6.5m。
(10)、窑炉下部出灰部分由圆盘卸灰机和两段密封阀配置,最大出灰能力84吨/小时。
(11)、成品斗式提升机型号为TB400型。
(12)、岗位除尘考虑混配、出灰、提升等部位共计7个吸尘点。
(13)、压缩空气:
使用压力0.4MPa,瞬时最大用气量7m3/min(压力状态下)。
压缩机选用螺杆式空气压缩机(两条线六条窑配两台),容积流量9.8m3/min,排气压力0.7Mpa,功率55kw。
3.8.2设计主要工艺及技术特点:
本次设计为保证生产高质量的活性石灰,在设计中根据XXXX自身的石灰技术和多年的生产实践,用于本次设计的石灰工艺技术如下:
(1)、窑顶布料系统:
在窑内合理布料是生产优质活性石灰的重要技术之一。
窑内布料合理是指:
石灰石、无烟煤、在窑内“点、网”均匀分布,无不同物料的偏析;窑顶料面呈平缓连续的马鞍形。
XXXX开发的旋转布料器具有以上功能,可实现理想布料。
其布料方式分为两种:
环行布料(自动)和定点布料(手动)。
正常操作时,采用环行布料;煅烧出现异常情况时,采用定点布料和调整挡料反射板位置,靠窑顶料面形状调整窑炉状况。
布料器转速、启停由变频器调整并在模拟屏上显示旋转溜槽的位置。
(2)、计算机仿真风帽实现窑内供风均匀
采用结构独特,通过计算机仿真模拟计算并经实践检验的风帽,可使竖窑内部气流运动的流场和温度场达到最佳,保证供风在窑内断面上的均匀性。
(3)、窑炉卸灰系统
卸灰系统的设计要点是:
物料在窑内平稳下移。
XXXX开发的圆盘卸灰机能够很好地将竖窑窑膛内烧成的生石灰定时而均匀地卸下,供给两段出灰机。
它既可在窑外方便地控制正反转和下料速度,又能使窑内断面各处下料均匀,从而保证了窑内料柱均衡地下降和在料柱产生异常时能及时排除,利于窑断面的通风均匀。
(4)、窑炉出灰系统
与卸灰系统配套的出灰系统是影响窑炉利用系数和操作的关键部位。
我公司提供的专利设备两段出灰阀能够做到不停风出灰,同时又能避免窑气的外泄。
由此实现竖窑稳压恒量地供风和煤气流动的合理分布,保证煅烧质量和改善环境。
其工作特点是:
上段阀和下段阀同时开或同时闭,中间与其相应闭和开,二者交替动作进行出灰,保证出灰的同时窑气与外界隔绝。
(5)、窑炉绝热
窑炉的绝热性能一方面反映在节约煤比上,另一方面是窑炉顺行上。
因此,对窑炉采取合理的绝热和良好的窑衬结构,能够达到绝热节焦,延长窑衬寿命的目的。
在本次设计过程中,根据各种耐火材料的性能和使用条件,采取特殊的窑衬结构达到节省投资、绝热效果好、窑衬使用寿命长的目的。
窑衬主要使用耐材为高铝砖、轻质粘土砖、保温浇注料、硅酸铝耐火纤维等。
(6)、窑炉温度检测
在竖窑的顶盖和烟气上升管上设3个热电偶,监控窑顶温度,以及三个段带上分设4层热电偶,每层设4支热电偶用于检测窑内温度,实现快速、准确地探知煅烧带的位置,在窑下出灰处设一个测温热电阻,测量成品灰的温度,这些为竖窑的热工控制提供快速准确的参数和调整依据。
(7)、原燃料混配系统
由XXXX开发的原燃料混配系统可实现配料自动化,并能保证窑料称量精确、混配均匀,从而为窑炉的顺行操作提供可靠的保证。
(8)、石灰的加工
采用由XXXX提供为生石灰的磨粉、筛分、转运专业配套的ZYMX自控系统,控制将石灰窑生产出来的统灰首先输送到颚式破碎机进行初破,初破后的石灰上振动筛进行过筛分选,其中0~3mm粉灰过筛后经皮带机集中收集后由斗提机提升入粉灰仓,20~40mm粒子灰经皮带机集中收集后由斗提机提升入粒子灰仓,其余粒径的石灰则由皮带机收集后输送至反击式破碎机进行二次加工,加工出来的石灰由皮带机再次输送到原振动筛上,进行二次过筛分选,循环流动石灰完全加工成业主所要求的粒度并装仓,石灰加工区共配统灰仓两座、粒子仓一座、粉灰仓两座,仓容均为600m3,仓内石灰产品同时具备现场装车和装船外运两套方案,满足业主外销需求。
3.8.3竖窑生产工艺设备及其选型
竖窑生产部分主要分为混配部分、卷扬提升部分、窑顶部分和排灰部分。
(1)、混配部分。
混配部分指从混配仓下口开始到上料小车入口为止。
在这个范围内,工艺设备有振动给料机2台,石灰石及无烟煤计量秤各1台,混配皮带2条和一些非标制做件。
其中振动给料机的给料能力分别为100吨/小时和60吨/小时。
石灰石和无烟煤计量秤的称量范围分别为5吨和1吨,精度均为3‰,混配皮带机为通用TD75型。
(2)、卷扬部分
卷扬部分是指从上料小车开始至窑顶受料斗入口为止.这部分主要包括上料小车、斜桥及支撑、平衡重锤及卷扬机。
上料小车有效容积1.1m3,卷扬机各部分型号和工艺参数为:
电动机:
22kw最大提升速度:
0.82m/s
卷扬及斜桥部分为钢结构制作。
(3)、窑顶部分
窑顶部分主要有窑顶受料斗、支架平台、钢梯等钢结构。
工艺设备为振动给料机1台,旋转布料器1台。
其中振动给料机给料能力100吨/小时,旋转布料器为专利设备,布料器电机功率为3kw,旋转速度3—7转/分。
(4)、排灰部分
排灰部分在窑炉的底部。
主要由风帽、送风管道、钢结构锥形管、支撑架、卸灰筒、圆盘卸灰机、两段出灰阀及检修平台等组成。
工艺设备有圆盘卸灰机和两段出灰阀。
两段出灰阀动力源为压缩空气,使用压力为0.4Mpa,瞬时最大用气量1m3/min,干油润滑使用2#锂基脂,汽缸润滑油型号为30号气轮机油,最大出灰能力20吨/小时。
(5)、窑炉本体
窑炉本体部分主要包括窑炉钢结构、梯子、平台和窑内砌砖。
窑内砌砖主要采用高窑高铝砖、粘土砖、轻质粘土砖、耐火纤维和浇注料。
(6)、助燃风系统
助燃风系统主要包括