合成氨工艺作业.docx
《合成氨工艺作业.docx》由会员分享,可在线阅读,更多相关《合成氨工艺作业.docx(21页珍藏版)》请在冰豆网上搜索。
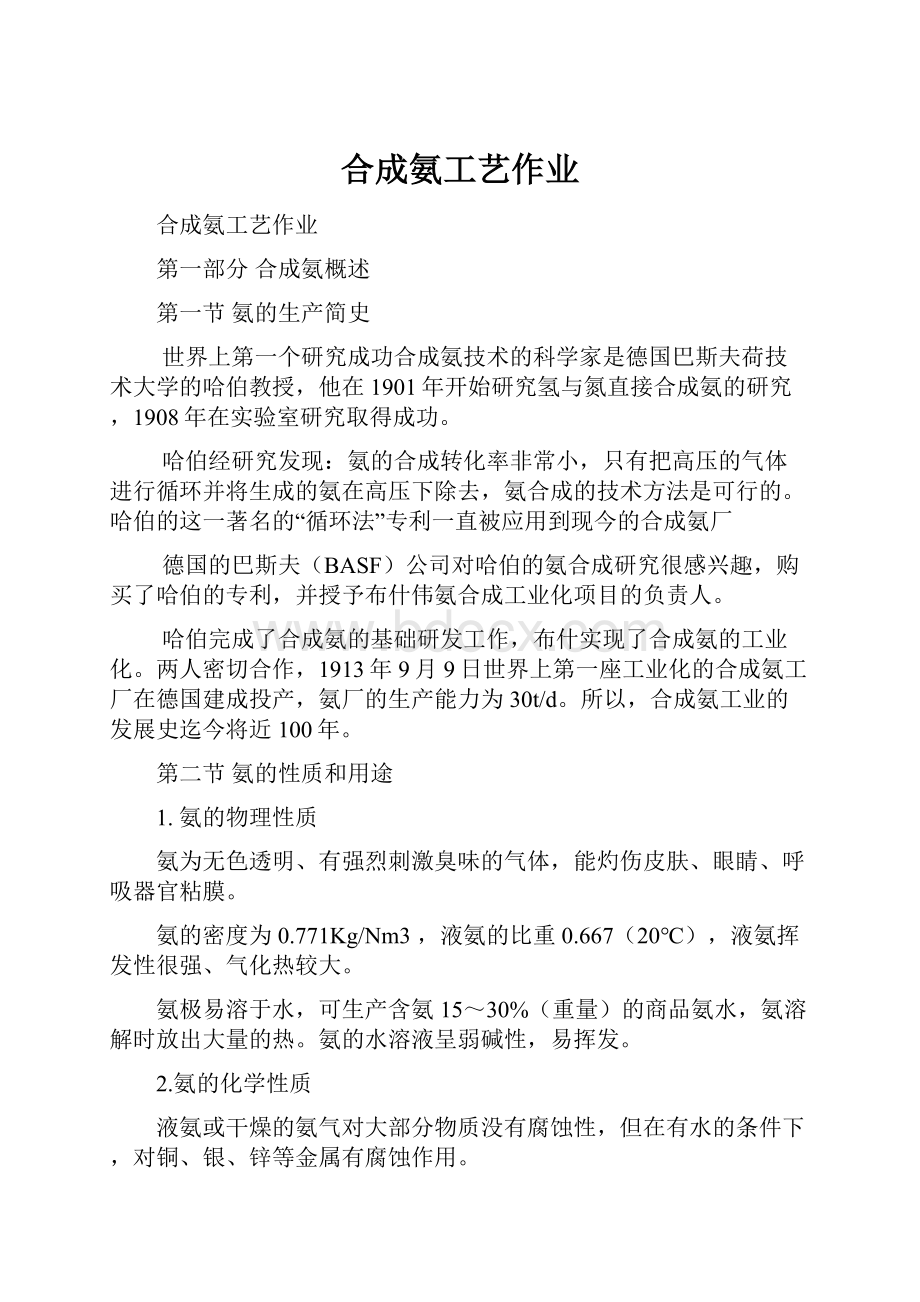
合成氨工艺作业
合成氨工艺作业
第一部分合成氨概述
第一节氨的生产简史
世界上第一个研究成功合成氨技术的科学家是德国巴斯夫荷技术大学的哈伯教授,他在1901年开始研究氢与氮直接合成氨的研究,1908年在实验室研究取得成功。
哈伯经研究发现:
氨的合成转化率非常小,只有把高压的气体进行循环并将生成的氨在高压下除去,氨合成的技术方法是可行的。
哈伯的这一著名的“循环法”专利一直被应用到现今的合成氨厂
德国的巴斯夫(BASF)公司对哈伯的氨合成研究很感兴趣,购买了哈伯的专利,并授予布什伟氨合成工业化项目的负责人。
哈伯完成了合成氨的基础研发工作,布什实现了合成氨的工业化。
两人密切合作,1913年9月9日世界上第一座工业化的合成氨工厂在德国建成投产,氨厂的生产能力为30t/d。
所以,合成氨工业的发展史迄今将近100年。
第二节氨的性质和用途
1.氨的物理性质
氨为无色透明、有强烈刺激臭味的气体,能灼伤皮肤、眼睛、呼吸器官粘膜。
氨的密度为0.771Kg/Nm3,液氨的比重0.667(20℃),液氨挥发性很强、气化热较大。
氨极易溶于水,可生产含氨15~30%(重量)的商品氨水,氨溶解时放出大量的热。
氨的水溶液呈弱碱性,易挥发。
2.氨的化学性质
液氨或干燥的氨气对大部分物质没有腐蚀性,但在有水的条件下,对铜、银、锌等金属有腐蚀作用。
氨的自燃点630℃,在空气中燃烧分解为氮和水。
氨与空气遇火能爆炸,在常压常温下氨的爆炸范围为15.5~28%,或13.5~82%(在氧气中)。
氨是活泼性化合物,与酸作用生成盐类。
例如,氨与硝酸作用生成硝酸铵,与二氧化碳作用生成氨基甲酸铵,然后脱水生成尿素。
3.氨的用途
(1)氨主要用于农业。
除氨本身就可作为化肥外,几乎所有的氮肥、复合肥料都离不开氨。
(2)氨不仅对发展农业有着重要的意义,而且也是重要的工业原料,广泛用于制药、炼油、合成纤维、合成树脂等工业部门。
(3)将氨硝化可制成硝酸。
硝酸用来制造氮肥,也是生产炸药、染料等产品的化工原料。
(4)液氨是常用的冷冻剂。
所以,氨是基本化工的产品之一,在国民经济中占有十分重要的地位。
第三节合成氨生产的基本过程
合成氨生产所用的原料,按物质状态可分为固体燃料、气体燃料和液体燃料。
虽然生产原料不同,工艺流程也不相同,但基本上由四个部分组成,即原料气的制备、原料气的净化、压缩和合成、氨的分离。
1.原料气的制备(简称造气)
生产合成氨,首先必须制备含有氮和氢的原料气。
它可以由分别制得的氢气和氮气混合而成,也可同时制得氢、氮混合气。
氮气可取之于空气。
将空气液化分离可制得氮气;或使空气通过燃料层燃烧,将生成的CO和CO2除去而制得氮气。
氢气来源于水或含有烃类的各种原料。
目前工业普遍采用以煤炭、天然气、重油等为原料,在高温下与水蒸气反应的方法来制取。
2.原料气的净化
除电解水外,不论采用何种原始原料和方法造气,原料气中都含有硫的化合物、一氧化碳、二氧化碳等对合成氨有害的各种杂质,必须采取适当的方法除去这些杂质,即对原料气进行净化,才能得到合格的氮氢原料气。
3.压缩和合成
将符合要求的氢、氮混合气压缩到一定压力,在高温和催化剂存在的条件下,合成为氨。
4.氨的分离
由于由氮气和氢气合成为氨的反应的转化率较低,故需在氨的合成工序之后通过氨的分离,以便将反应生成的氨分离出来,而未反应的原料气通过一个回路再循环返回合成系统。
第二部分合成氨工艺的危险特点
合成氨工艺是各安全生产监督管理局重点监管的危险化工工艺之一,其危险特点主要表现为以下几点:
1.高温、高压使可燃气体爆炸极限扩宽,气体物料一旦过氧,极易在设备和管道内发生爆炸;
2.高温、高压气体物料从设备管线泄漏时会迅速膨胀与空气混合形成爆炸性混合物,遇到明火,静电火花引起着火和空间爆炸。
3.气体压缩机等转动设备在高温下运行会使润滑油挥发裂解,在附近管道内造成积炭,可导致积炭燃烧或爆炸。
4.高温、高压可加速设备金属材料发生蠕变、改变金相组织,还会加剧氢气、氮气对钢材的氢蚀及渗氮,加剧设备的疲劳腐蚀,使其机械强度减弱,引发物理爆炸。
5.液氨大规模事故性泄漏会形成低温云团引起大范围人群中毒,遇明火还会发生空间爆炸。
第三部分合成氨工艺过程
第一节合成氨工艺设备安全技术
1.氨合成塔
氨合成塔是合成氨生产的重要设备之一,其作用是使合格的氢、氮气在高温、高压及催化剂存在的条件下合成氨。
高温、高压的合成条件,要求合成塔具有较高的机械强度、良好的耐热能力等。
另外,在高温、高压条件下,氢、氮气对碳钢有明显的腐蚀作用。
为了适应氨合成反应条件,又解决反应条件对合成塔材料带来的困难,合成塔设计成内件和外筒两部分。
外筒需保证气体能够处于高压下,因此必须坚固。
根据强度高,容积大,易加工等要求,外壳一般都制成长筒形。
由于采取降温措施,外壳温度一般不超过50-60℃。
所以,对外壳材料并不强调要耐氢、氮腐蚀,外壳通常是用高强度、低合金钢制成。
内件供气体进行预热、反应和冷却之用。
内芯由于处于高温、高压下,必须采用耐氮、氢腐蚀的特种合金钢,但内芯处于外壳内,压差很小,可以单薄一些,即使腐蚀损坏了,也可以更换。
由此可见,把合成塔分成外壳和内芯两部分是节省大量合金钢、降低投资的重要措施。
在工艺上对合成塔的要求主要包括:
(1)在正常操作条件下,反应能维持自热,塔的结构要有利于升温还原,保证催化剂有良好的活性;
(2)催化剂床层温度分布合理,充分利用催化剂的活性;
(3)气流在催化剂床层内分布均匀,压力减小;
(4)热交换器传热强度大、体积小,充分利用塔内空间,尽可能多装催化剂;
(5)生产稳定,调节灵活,具有较大的操作弹性。
合成塔内件应具备之条件:
(1)半塔生产能力高;
(2)操作便于调节、控制;
(3)能较好地回收利用反应热,作为系统的能源;
(4)结构坚固、可靠,操作维修方便
合成塔的分类:
按照降温方法不同,可以分为:
(1)连续换热式:
在催化剂床层中进行氨合成反应的同时,还与外界进行热量交换;
(2)多段间接换热式;
(3)多段冷激式
2.冰机
(1)概述
氨合成塔只能将一部分氢氮气合成为氨。
为使产品氨与未反应的气体分离,一般都采用降温冷凝的办法。
合成回路气体的温度越低,分离就越完全。
通常的冷却水是达不到这样的要求的,因而需要专门的制冷工序。
所谓冷冻,就是指获取低于一般冷却水温的冷源。
冷冻需要能量,具体体现在一台压缩机上,叫做冰机,即氨气压缩机。
(2)冷冻原理
液氨的蒸发温度与压力有关,如下表所示:
温度℃
压力Kg/cm2(A)
汽化热
Kcal/Kg
温度℃
压力Kg/cm2(A)
汽化热Kcal/Kg
-40
0.732
331.3
10
6.271
292.8
-30
1.219
324.5
20
8.741
283.5
-20
1.940
317.3
30
11.895
273.6
-10
2.966
309.7
40
15.850
262.9
0
4.379
301.5
50
20.727
251.3
从上表可知:
液氨的蒸发温度与压力有关。
温度越低,压力也越低。
因此可根据所求的冷冻温度确定液氨的蒸发压力。
整个冷冻回路如下图所示
(3)冷冻工序流程
(4)冰机系统常见事故的预防措施
1冰机出口压力过高
危害:
冰机出口压力过高,使电机超负荷运行,浪费动力,严重超压还会造成容器的损坏。
预防与处理:
a.排放惰性气体;
b.加大水量,清理列管结垢;
c.开大出口阀,降低液位;
d.增开冰机,检查用氨单位氨冷器列管是否泄漏;
e.定期煮油,清理过滤器,开大冷凝器出口阀等。
2冰机带氮
危害:
用氨单位氨冷器液位高,加氢过猛过多和本岗位中间冷却器及油冷器加氨过多。
冰机带氨的表现:
一般会出现进口管道和气缸外壳结霜;进口压力升高;少量带液氨时阀片有滴嗒声;严重时缸内有冲击声,机身震动;马达电流波动幅度大。
预防与处理
a.轻微带氨可关小一段进口阀,出口温度维持不小于40℃,联系有关岗位处理掉带液氨的源头;联系生产调度维持氨总管压力;打开进口气流分离器排液阀排液。
b.大量带液当出现机身震动,缸内严重液击等现象时要按紧急停车方法处理。
3.氨蒸发器
液氨蒸发器是一个换热设备。
它是利用液氨的汽化需要吸收大量热量,来冷却流经管内的被冷却的物料。
在生产上,往往要求被冷却物料的出口温度稳定,这样就构成了以被冷物料出口温度为被控变量,以液氨流量为操纵变量的控制方案。
第二节原料气的制备
合成氨的原料气是氢气和氮气,而且要求氢氮比约为3。
本节主要介绍以固体燃料(焦炭、无烟煤等)、烃类为原料生产原料气的基本原理和工艺。
以固体燃料为原料生产原料气
将固体燃料无烟煤或焦炭气化以制造合成氨原料气,简称造气。
造气常用的气化剂有空气、富氧空气、氧气和水蒸气等。
气化所得的气体统称为煤气。
用于造气的设备称为煤气发生炉。
以空气为气化剂制取的煤气称为空气煤气,以水蒸气为气化剂制取的煤气称为水煤气,以空气和适量水蒸气为气化剂制取的煤气,则为混合煤气。
半水煤气特指组成符合(CO+H2)与N2体积之比为3.1~3.2的混合煤气,即合成氨原料气。
1.固体燃料气化反应器
固体燃料气化,属于非催化气-固相反应,这类反应器有移动床、流化床、固定床等。
如图所示的间歇式固定层煤气发生炉属于移动床气-固相反应器。
无烟煤或焦炭从炉顶加
入,炉渣自炉底排出。
该煤气发生炉主要由三部分组成:
燃料进行气化反应的空间即炉体部分,气化剂分布及排渣部分和加料装置。
在稳定的操作条件下,燃料层自下而上移动发生一系列的物理和化学变化。
在燃料层的顶部,新加入的燃料与热的煤气接触,水分被蒸发,此区域称为干燥区。
燃料下移继续受热,释放出低分子烃类气体,燃料本身被焦炭化,这一区域称为干馏区。
再继续下移,燃料的温度更高,气化反应主要在这个区进行。
以空气为气化剂时,在气化区的下部,主要进行的是碳与氧的燃烧反应,称为氧化层,其上部主要进行碳与二氧化碳的反应,称为还原层。
若以水蒸气为气化剂时,在气化区主要发生高温碳分解水蒸气的反应,所以不再有氧化层和还原层只分。
燃料经过气化反应后形成的灰渣留有一层在炉篦上,称为灰渣区。
灰渣区可起到预热和均匀分布炉底进来的气化剂的作用,同时保护炉篦不因过热而变形。
2.间歇式气化法的工作循环
理论上采用间歇式气化法生产半水煤气时,只需交替地向煤气发生炉内通入空气和水蒸气。
从上一次通空气开始到下一次通空气,称为一个工作循环考虑到热量的充分利用,燃料层温度均衡及生产安全等因素,工业上采用五个阶段为以工作循环的间歇操作法。
(1)吹风阶段
空气从煤气发生炉底部吹入,所含的氧气与燃料层中的碳发生氧化反应,反应放出大量热能,使炉温升高(1100~1400℃)。
生成的吹风气(即空气煤气)主要含有氮气和二氧化碳,去余热回收系统而后放空。
(2)一次上吹制气阶段
吹风阶段结束后,燃料层温度升高,这时从煤气发生炉底部通入混有适量空气的水蒸气,与燃料层中炽热的碳发生反应,生成半水煤气从炉顶排出,之后经除尘、洗涤与冷却后送入气柜。
制气阶段加入的空气称为加氮空气,其主要目的是为了得到氮气,以使得半水煤气符合合成氨原料气的要求。
另外,加氮空气与碳反应也为水蒸气与碳的反应提供热量。
(3)下吹制气阶段
一次上吹制气后,由于水蒸气温度较低,且反应吸热,使燃料层气化区温度显著降低,然而燃料层上部却因煤气的通过,温度有所上升,气化区上移,煤气带走的热量损失增加,因此在上吹制气一段时间后改变气流方向,即水蒸气从煤气发生炉顶部进入,这样可充分利用燃料层上部的热量,使气化区恢复到正常位置。
生成的半水煤气从炉底导出,经过除尘、洗涤、冷却后也进入气柜。
(4)二次上吹制气阶段
经下吹制气后炉内燃料层温度大大降低,需再通入空气提高炉温。
但是下吹制气后,炉底部充满煤气,如果立即送入空气,在炉底部空气与煤气相遇就会发生爆炸。
因此,在下吹制气阶段结束后,再自炉底送入水蒸气,将炉底煤气排净,为下一个工作循环的吹风做好准备。
二次上吹时,虽然也可以制气,但因炉温偏低,制得的半水煤气质量不高,因此二次上吹时间尽可能短一些。
(5)空气吹净阶段
二次上吹制气后,煤气发生炉上部与管路中尚充满半水煤气。
在吹风时,如果把这部分半水煤气从烟囱排掉,不仅造成浪费,而且这部分半水煤气和带有火星的吹风气一起排至烟囱口与空气接触,可能发生爆炸。
因此,吹风阶段之前,从炉底吹入空气,使其与残留的半水煤气一并送入气柜,加以回收。
这一过程称为空气吹净。
空气吹净阶段结束后,重新转入吹风阶段,开始进行第二个工作循环,如此反复进行。
每一个工作循环所需的时间称为循环时间。
循环时间长,气化区温度波动大,从而煤气的产量、质量波动也大。
循环时间短,有利于气化区温度的稳定,生产的煤气产量、质量也较稳定。
但循环时间太短,阀门开关过于频繁,容易损坏。
生产中循环时间一般为2.5~3.5min。
确定造气工序工艺条件的目的是在保证煤气成分合格的前提下,尽可能提高煤气的产量和减少燃料的消耗。
第三节原料气的净化
由原料制成的原料气中含有能导致催化剂中毒的组分,主要是含硫化合物和碳的氧化物。
它们需经历脱硫和脱碳的净化过程。
1.脱硫
各种硫化物中,H2S和有机硫是最有害的杂质。
硫的脱除根据原料的种类及其含硫量的多少,安排在适当的地方进行。
天然气含硫极少,而且是气体,一般安排在转化前,成为氨生产的第一道工序。
以煤为原料时,由于煤的脱硫比较困难,目前都在气化后进行。
如果含硫量较高,通常是先脱硫后变换;如果含硫量较少,则放在变换后脱硫。
变换后根据净化方法可以单独进行,也可以与脱除CO2同时进行。
工业上脱硫的方法很多,按照脱硫剂的状态可分为干法和湿法两种。
改良ADA法脱硫:
它是一种化学吸收法。
吸收液的主要成分是蒽醌二磺酸(ADA)钠盐,还含有起催化作用的偏钒酸钠、碱、三氧化二铁以及起稳定作用的酒石酸钠和EDTA等。
在吸收塔中,半水煤气中的H2S与吸收液中的碱发生吸收反应:
NaOH+H2S=NaHS+H2O
再生反应:
2NaHS+4NaVO3+H2O=Na2V4O9+4NaOH+2S
2(NaSO3)2C14H6O2+Na2V4O9+2NaOH+H2O=4NaVO3+2(NaSO3)2C14H6(OH)2
2(NaSO3)2C14H6(OH)2+O2=2(NaSO3)2C14H6O2+2H2O
脱硫全过程的计量方程式:
2H2S+O2=2H2O+2S
在实际运行过程中因半水煤气中含有少量CO2,发生了下列反应:
2NaOH+CO2=Na2CO3+H2O
所以在脱硫过程中尚需补充碱液。
2.变换
无论用固体、液体或气体为原料,所制得的合成氨粗原料气中均含有一氧化碳。
粗原料气中一氧化碳的含量因原料及方法的不同有较大的差别,范围为12%~40%。
固体燃料气化时制得的半水煤气中,一氧化碳的含量通常为28%~30%。
一氧化碳不是合成氨的直接原料,而且对氨合成催化剂还有毒害,必须除去。
利用一氧化碳与水蒸气的变换反应,既可以使一氧化碳变为易于除净的二氧化碳,又可制得等体积的氢气。
因此,对于合成氨来讲,变换过程既是原料气的净化,又是原料气制作的继续。
变换后的气体称为变换气。
温度、反应物的组成、催化剂的性能都是影响平衡转化率的因素。
变换的工艺条件:
(1)催化剂
目前广泛应用的变换催化剂有铜催化剂和铁铬催化剂
铜催化剂的活性组分为铜,活性温度范围为180~250℃,反应气体中所含的硫和氯容易使催化剂中毒,因此要求反应气体的含毒量必须很低。
铁铬催化剂的活性组分是氧化铁,以氧化铬为助催剂,活性温度范围为350~450℃,并具有良好的耐硫性能。
生产实践中,根据催化剂活性温度的高低,称铜催化剂为低变催化剂,称铁铬催化剂为中变催化剂。
中变催化剂的反应温度高,反应速率大,有较强的耐硫性,价廉而寿命较长。
低变催化剂则相反。
为了取长补短,生产上采取中变与低变相串联的流程。
这样中变可以在较高的温度下承担绝大部分任务,然后通过低变以获得较高的转化率。
中变和低变催化剂及操作条件
型号
组成
活性温度
H2O/CO
空速
转化率
℃
mol/mol
h-1
%
104
Fe2O3、MgO、Cr2O3、k2O
380~550
3~5
300~400
80~90
201
CuO、ZnO、Cr2O3
180~252
6~10
1000~2000
96~99
(2)原料气的组成
在变换反应过程中,CO的转化率即使在催化剂最低的活性温度条件下也不够高。
生产上采取提高转化率的方法是使水蒸气过量。
(3)反应温度
对于可逆放热反应,最大反应速率时的反应温度是随转化率的提高而降低的。
所以反应的前阶段应使用中温变换催化剂,反应过程称作中温变换;反应的后阶段应使用低温变换催化剂,反应过程称作低温变换。
反应温度的控制,采用水蒸气分阶段冷激的办法。
既可使反应温度接近最优反应温度,又可只在后期提高n(H2O)和n(CO)的比例,既获得更高的转化率,又不致使反应器的容积过大。
(4)反应压力
CO变换是体积不变的反应,压强与平衡转化率无关。
但加压可以增加催化反应器的生产能力,更重要的是加压可降低能耗。
这是因为水蒸气来自锅炉,不需压缩功,所以压强越大,能耗越少。
但加压变换时,二氧化碳的分压增大,加剧了对设备的腐蚀,因而对设备材质要求提高,设备投资增加。
一般中型合成氨厂采用1.2~1.8MPa,小型合成氨厂采用0.7~1.2MPa。
(5)空间速度
变换过程采用一次通过流程,空间速度不宜太大,一般为400~600h-1。
变换工艺流程
变换是气固催化可逆放热反应。
反应热不大,可以采用绝热反应器。
由于可逆放热反应的最优反应温度是先高温后低温,所以如果混合气体中CO的浓度超过15%时,为了使反应温度接近于最优温度,中变反应分成二段或三段进行,并在段间用蒸汽或软水冷激。
低变时,CO很低,放热量很少,可以一次完成。
中变、低变串联流程
1-中变反应器;2-废热锅炉;3,5-换热器;4-低变反应器
3.脱碳
脱碳是除去气体中的CO2。
由于气体中CO2的浓度较高,数量多,CO2的脱除一般使用溶液吸收法。
为了重复使用吸收液,所采用的生产流程是吸收--解吸--吸收液循环流程。
(1)低温甲醇洗涤——物理吸收
在低温的条件下,甲醇是的CO2很好的溶剂。
在3MPa,-30~-70℃的温度下,气体中的CO2可以从33%下降到10ppm,显然甲醇脱碳是十分彻底的。
此法可作为低温净化法的配套部分。
(2)改良热钾碱法——化学吸收
此法以K2CO3水溶液为吸收液,并添加少量活化剂如乙二醇胺或氨基乙酸,缓蚀剂如V2O5等。
吸收—解吸反应为
当吸收液中添加氨基乙酸,吸收压强为2~3MPa,温度为85~100℃气体中的CO2可以从20~28%降低到0.2~0.4%。
解吸时压强为10~30KPa,温度为105~110℃。
用热碱脱除CO2时,同时也脱除了微量的H2S。
化学吸收法具有选择性好、脱碳干净和回收二氧化碳纯度高等优点。
4.原料气的精制
甲烷化反应
经净化的气体还含有一氧化碳和二氧化碳。
为了防止它们对氨合成催化剂的毒害,在原料气送往合成工段前,还需进一步净化,即原料气的精制。
精制后气体中一氧化碳、二氧化碳总含量,大型合成氨厂控制在10cm3/m3以下,小型合成氨厂控制在25以下。
由于CO既不是酸性气体,又不是碱性气体,且在各种无机、有机液体中的溶解度很小,所以脱除少量的CO并非易事。
目前常用的方法是把它们转化成对氨合成催化剂无毒害的CH4,这就是甲烷化反应。
CO+3H2=CH4+H2O+206kJ/mol
CO2+4H2=CH4+2H2O+165kJ/mol
甲烷化反应是在以镍为主的催化剂的作用下,在280~380℃,以及原有的压强(0.6~3MPa)下进行的。
反应后气体含CO、CO2总量在10ppm以下,比铜洗法低得多(100ppm)。
它们对氨合成催化剂仍有毒害。
残余CO的去除也可以低温液化法除去。
此法将甲醇去除CO2后的气体进一步降温,使CO以及其它杂质气体如CH4、Ar、O2等液化而分离。
也可用液氮洗涤,达到同样的目的。
低温净化法得到的气体非常纯净。
例如含CO仅5ppm,O2<10ppm,CH4<1ppm,Ar<60ppm。
完全不含水、硫化物、氧化物等。
液氮洗涤法是基于混合气体中各组分在不同的气体分压下冷凝的温度不同,混合气体中各组分在相同的溶液中溶解度不同,使混合气体中需分离的某种气体冷凝和溶解在所选择的溶液中,实现从混合气体中分离。
液氮洗涤法是一种物理吸收法,属深冷技术。
洗涤液仅为液体氮,洗涤吸收、分离的影响因素少,而且氮气也是氨合成的有效成分,故工艺流程简单、工艺过程容易控制。
该工艺除能很干净地脱除CO,还可同时脱除原料气中的CH4、Ar等惰性气体,得到惰性气体含量100×10-6以下的高质量氢氮混合气体,这对降低原料气的消耗,增加氨合成生产能力特别有利。
由于此法需要液体氮,选用该技术时必须考虑液体氮的来源。
由于低温会使H2O和CO2凝结成固体,影响传热及堵塞管道和设备,因此进入液氮洗涤系统的原料气体必须预先完全脱除H2O和CO2。
第四节氨的合成
氨的合成是合成氨厂的核心。
其任务是将经脱硫、变换等净化工序所得的合格氢、氮混合气,在高温、高压及催化剂存在的条件下直接合成氨。
1.工艺条件
氨合成工序的工艺条件主要包括压力、温度、空间速率、气体组成等。
(1)压力
生产上选择压力的主要依据是能源消耗,以及包括能源、原料费用、设备投资、技术投资在内的综合费用。
目前普遍采用10~15MPa左右的压力。
(2)温度
氨合成反应是催化反应,催化剂只有在一定温度条件下才具有较高的活性,所以氨合成反应温度必须在催化剂活性温度范围内。
氨合成反应温度控制在470~520℃为宜。
(3)空间速率
对于同一反应器,空间速率的大小意味着处理气量的大小。
在一定的温度、压力和进塔气组成的条件下,增大空间速率,就加快了气体通过催化剂床层的速度,缩短了气体与催化剂的接触时间,从而使进塔气体中氨含量降低。
增大空间速率时,虽然出塔气体中的氨含量有所降低,但氨含量的降低对氨产量的减少量比气量增加对氨产量的增加量要小得多,又因为合成氨的原料气是循环使用的,故可不追求单程转化率而通过适当加大空间速率以提高合成氨生产能力。
对于压力为30MPa左右的中小型氨合成系统,空间速率选择20000~30000h-1较适宜;对于压力为15MPa左右的大型氨合成系统,空间速率选择10000~20000h-1较适宜。
(4)进塔气体的组成
氨合成进塔气体的组成包括氢氮比、惰性气体含量和进塔氨含量。
氢氮比
实际生产中控制进合成塔气体的氢氮比为2.7~2.9,但生成氨时,氢和氮是按3:
1消耗的。
惰性气体含量
新鲜原料气中惰性气体含量一般仅为0.5%~0.7%。
由于惰性气体不参与反应,在循环过程中逐渐积累增多,这对化学平衡和反应速率都不利。
为了使循环气中惰性气体含量不致过高,需要将一部分循环气放空,以降低进氨合成塔气体中惰性气体的含量。
循环气体中惰性气体含量应根据操作压力、催化剂活性等条件而定。
若以增产为主要目标,惰性气体含量可控制低一些,为10%~14%;