注塑过程中常见的问题.docx
《注塑过程中常见的问题.docx》由会员分享,可在线阅读,更多相关《注塑过程中常见的问题.docx(15页珍藏版)》请在冰豆网上搜索。
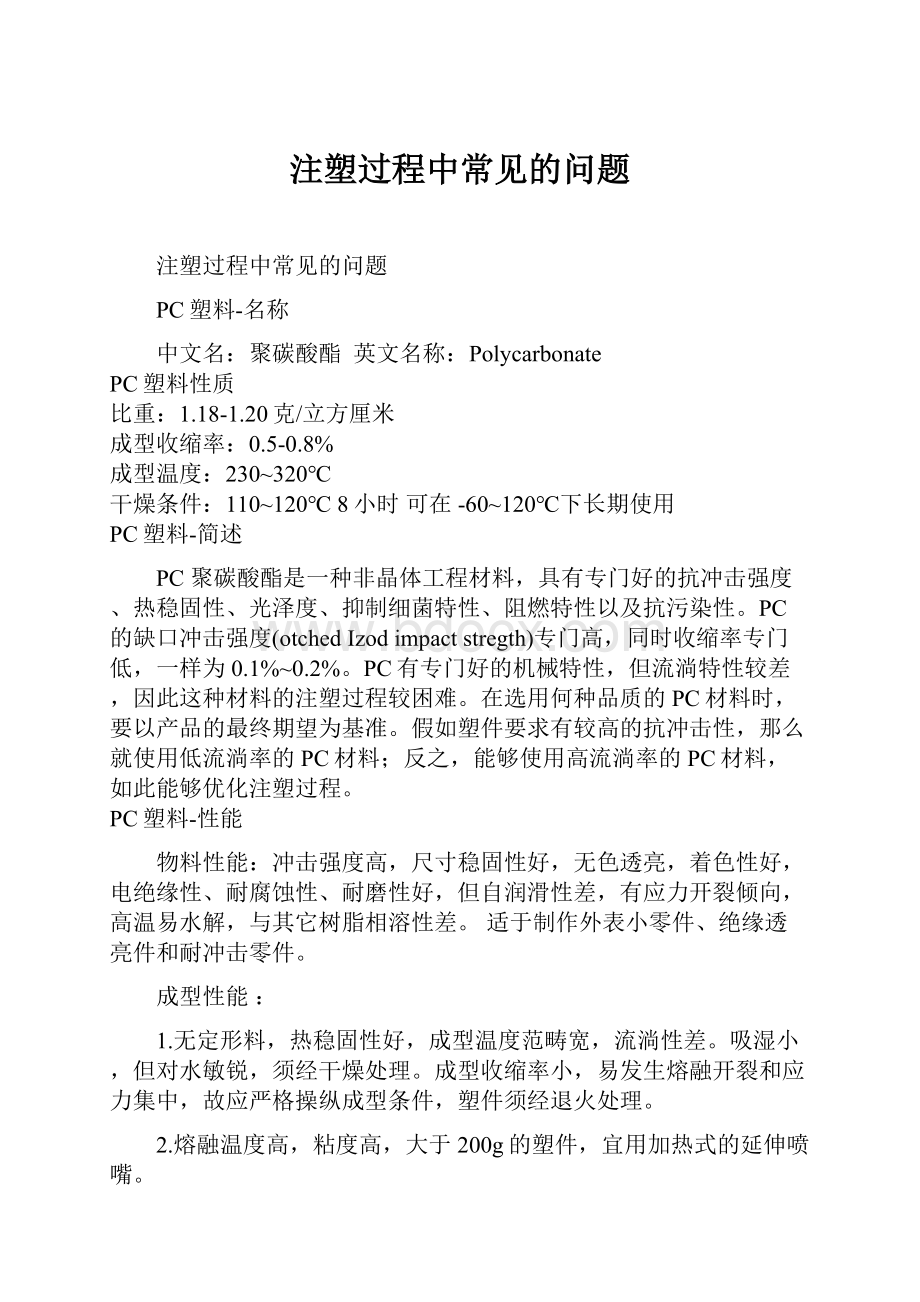
注塑过程中常见的问题
注塑过程中常见的问题
PC塑料-名称
中文名:
聚碳酸酯英文名称:
Polycarbonate
PC塑料性质
比重:
1.18-1.20克/立方厘米
成型收缩率:
0.5-0.8%
成型温度:
230~320℃
干燥条件:
110~120℃8小时可在-60~120℃下长期使用
PC塑料-简述
PC聚碳酸酯是一种非晶体工程材料,具有专门好的抗冲击强度、热稳固性、光泽度、抑制细菌特性、阻燃特性以及抗污染性。
PC的缺口冲击强度(otchedIzodimpactstregth)专门高,同时收缩率专门低,一样为0.1%~0.2%。
PC有专门好的机械特性,但流淌特性较差,因此这种材料的注塑过程较困难。
在选用何种品质的PC材料时,要以产品的最终期望为基准。
假如塑件要求有较高的抗冲击性,那么就使用低流淌率的PC材料;反之,能够使用高流淌率的PC材料,如此能够优化注塑过程。
PC塑料-性能
物料性能:
冲击强度高,尺寸稳固性好,无色透亮,着色性好,电绝缘性、耐腐蚀性、耐磨性好,但自润滑性差,有应力开裂倾向,高温易水解,与其它树脂相溶性差。
适于制作外表小零件、绝缘透亮件和耐冲击零件。
成型性能 :
1.无定形料,热稳固性好,成型温度范畴宽,流淌性差。
吸湿小,但对水敏锐,须经干燥处理。
成型收缩率小,易发生熔融开裂和应力集中,故应严格操纵成型条件,塑件须经退火处理。
2.熔融温度高,粘度高,大于200g的塑件,宜用加热式的延伸喷嘴。
3.冷却速度快,模具浇注系统以粗、短为原那么,宜设冷料井,浇口宜取大,模具宜加热。
4.料温过低会造成缺料,塑件无光泽,料温过高易溢边,塑件起泡。
模温低时收缩率、伸长率、抗冲击强度高,抗弯、抗压、抗张强度低。
模温超过120度时塑件冷却慢,易变形粘模
PC塑料用途
光学照明:
用于制造大型灯罩、防护玻璃、光学仪器的左右目镜筒等,还可广泛用于飞机上的透亮材料。
电子电器:
聚碳酸酯是优良的E(120℃)级绝缘材料,用于制造绝缘接插件、线圈框架、管座、绝缘套管、机壳体及零件、矿灯的电池壳等。
也可用于制作尺寸精度专门高的零件,如光盘、、电子运算机、视频录象机、交换器、信号继电器等通讯器材。
聚碳酸酯薄摸还被广泛用作电容器、绝缘皮包、录音带、彩色录象磁带等。
机械设备:
用于制造各种齿轮、齿条、蜗轮、蜗杆、轴承、凸轮、螺栓、杠杆、曲轴、棘轮,也可作一些机械设备壳体、罩盖和框架等零件。
医疗器材:
可作医疗用途的杯、筒、瓶以及牙科器械、药品容器和手术器械,甚至还可用作人工肾、人工肺等人工脏器。
其它方面:
建筑上用作中空筋双壁板、暖房玻璃等;在纺织行业用作纺织纱管、纺织机轴瓦等;日用方面作奶瓶、餐具、玩具和模型等。
一、注塑过程常见问题
1、龟裂
龟裂是塑料制品较常见的一种缺陷,产生的要紧缘故是由于应力变形所致。
要紧有残余应力、外部应力和外部环境所产生的应力变形。
1.1残余应力引起的龟裂
残余应力要紧由于以下三种情形,即充填过剩、脱模推出和金属镶嵌件造成的。
作为在充填过剩的情形下产生的龟裂,其解决方法要紧可在以下几方面入手:
(1)由于直浇口压力缺失最小,因此,假如龟裂最要紧产生在直浇口邻近,那么可考虑改用多点分布点浇口、侧浇口及柄形浇口方式。
(2)在保证树脂不分解、不劣化的前提下,适当提高树脂温度能够降低熔融粘度,提高流淌性,同时也能够降低注射压力,以减小应力。
(3)一样情形下,模温较低时容易产生应力,应适当提高温度。
但当注射速度较高时,即使模温低一些,也可减低应力的产生。
(4)注射和保压时刻过长也会产生应力,将其适当缩短或进行几次保压切换成效较好。
(5)非结晶性树脂,如AS树脂、ABS树脂、PMMA树脂等较结晶性树脂如聚乙烯、聚甲醛等容易产生残余应力,应予以注意。
脱模推出时,由于脱模斜度小、模具型胶及凸模粗糙,使推出力过大,产生应力,有时甚至在推出杆周围产生白化或破裂现象。
只要认真观看龟裂产生的位置,即可确定缘故。
在注射成型的同时嵌入金属件时,最容易产生应力,而且容易在通过一段时刻后才产生龟裂,危害极大。
这要紧是由于金属和树脂的热膨胀系数相差悬殊产生应力,而且随着时刻的推移,应力超过逐步劣化的树脂材料的强度而产生裂纹。
通用型聚苯乙烯差不多上不适于宜加镶嵌件,而镶嵌件对尼龙的阻碍最小。
由于玻璃纤维增强树脂材料的热膨胀系数较小,比较适合嵌入件。
另外,成型前对金属嵌件进行预热,也具有较好的成效。
1.2外部应力引起的龟裂
那个地点的外部应力,要紧是因设计不合理而造成应力集中,专门是在尖角处更需注意。
1.3外部环境引起的龟裂
化学药品、吸潮引起的水降解,以及再生料的过多使用都会使物性劣化,产生龟裂。
2、充填不足
2.1要紧缘故
有以下几个方面:
(1)树脂容量不足;
(2)型腔内加压不足;(3)树脂流淌性不足;(4)排气成效不行。
2.2改善措施
从以下几个方面入手:
(1)加长注射时刻,防止由于成型周期过短,造成浇口固化前树脂逆流而难于充满型腔。
(2)提高注射速度。
(3)提高模具温度。
(4)提高树脂温度。
(5)提高注射压力。
(6)扩大浇口尺寸。
一样浇口的高度应等于制品壁厚的1/2~l/3。
(7)浇口设置在制品壁厚最大处。
(8)设置排气槽(平均深度0.03mm、宽度3~5mm)或排气杆。
关于较小工件更为重要。
(9)在螺杆与注射喷嘴之间留有一定的(约5mm)缓冲距离。
(10)选用低粘度等级的材料。
(11)加入润滑剂。
3、皱招及麻面
产生这种缺陷的缘故在本质上与充填不足相同,只是程度不同。
因此,解决方法也与上述方法差不多相同。
专门是对流淌性较差的树脂(如聚甲醛、PMMA树脂、聚碳酸酯及PP树脂等)更需要注意适当增大浇口和适当的注射时刻。
4、缩坑
缩坑的缘故也与充填不足相同,原那么上可通过过剩充填加以解决,但却会有产生应力的危险,应在设计上注意壁厚平均,应尽可能地减少加强肋、凸柱等地点的壁厚。
5、溢边
关于溢边的处理重点应要紧放在模具的改善方面。
而在成型条件上,那么可在降低流淌性方面着手。
具体可采纳以下几种方法:
(1)降低注射压力;
(2)降低树脂温度;(4)选用高粘度等级的材料;(5)降低模具温度;(6)研磨溢边发生的模具面;(7)采纳较硬的模具钢材;(8)提高锁模力;(9)调整准确模具的结合面等部位;(10)增加模具支撑柱,以增加刚性;(11)依照不同材料确定不同排气槽的尺寸。
6、接痕
熔接痕是由于来自不同方向的熔融树脂前端部分被冷却、在结合处未能完全融合而产生的。
一样情形下,要紧阻碍外观,对涂装、电镀产生阻碍。
严峻时,对制品强度产生阻碍(专门是在纤维增强树脂时,尤为严峻)。
可参考以下几项予以改善:
(l)调整成型条件,提高流淌性,如提高树脂温度、提高模具温度、提高注射压力及速度等;
(2)增设排气槽,在熔接痕的产生处设置推出杆也有利于排气;(3)尽量减少脱模剂的使用;(4)设置工艺溢料并作为熔接痕的产生处,成型后再予以切断去除;(5)假设仅阻碍外观,那么可改变烧四位置,以改变熔接痕的位置。
或者将熔接痕产生的部位处理为暗光泽面等,予以修饰。
7、烧伤
依照由机械、模具或成型条件等不同的缘故引起的烧伤,采取的解决方法也不同。
(1)机械缘故,例如,由于专门条件造成料筒过热,使树脂高温分解、烧伤后注射到制品中,或者由于料简内的喷嘴和螺杆的螺纹、止回阀等部位造成树脂的滞流,分解变色后带入制品,在制品中带有黑褐色的烧伤痕。
这时,应清理喷嘴、螺杆及料筒。
(2)模具的缘故,要紧是因为排气不良所致。
这种烧伤一样发生在固定的地点,容易与第一种情形区别。
这时应注意采取加排气槽反排气杆等措施。
(3)在成型条件方面,背压在300MPa以上时,会使料筒部分过热,造成烧伤。
螺杆转速过高时,也会产生过热,一样在40~90r/min范畴内为好。
在没设排气槽或排气槽较小时,注射速度过高会引起过热气体烧伤。
8、银线
银线要紧是由于材料的吸湿性引起的。
因此,一样应在比树脂热变形温度低10~15℃的条件下烘干。
对要求较高的PMMA树腊系列,需要在75℃左右的条件下烘干4~6h。
专门是在使用自动烘干料斗时,需要依照成型周期(成型量)及干燥时刻选用合理的容量,还应在注射开始前数小时先行开机烘料。
另外,料简内材料滞流时刻过长也会产生银线。
不同种类的材料混合时,例如聚苯乙烯和ABS树脂、AS树脂,聚丙烯和聚苯乙烯等都不宜混合。
9、喷流纹
喷流纹是从浇口沿着流淌方向,弯曲如蛇行一样的痕迹。
它是由于树脂由浇口开始的注射速度过高所导致。
因此,扩大烧四横截面或调低注射速度差不多上可选择的措施。
另外,提高模具温度,也能减缓与型腔表面接触的树脂的冷却速率,这对防止在充填初期形成表面硬化皮,也具有良好的成效。
10、翘曲、变形
注射制品的翘曲、变形是专门棘手的问题。
要紧应从模具设计方面着手解决,而成型条件的调整成效那么是专门有限的。
翘曲、变形的缘故及解决方法可参照以下各项:
(1)由成型条件引起残余应力造成变形时,可通过降低注射压力、提高模具并使模具温度平均及提高树脂温度或采纳退火方法予以排除应力。
(2)脱模不良引起应力变形时,可通过增加推杆数量或面积、设置脱模斜度等方法加以解决。
(3)由于冷却方法不合适,使冷却不平均或冷却时刻不足时,可调整冷却方法及延长冷却时刻等。
例如,可尽可能地在贴近变形的地点设置冷却回路。
(4)关于成型收缩所引起的变形,就必须修正模具的设计了。
其中,最重要的是应注意使制品壁厚一致。
有时,在不得已的情形下,只好通过测量制品的变形,按相反的方向修整模具,加以校正。
收缩率较大的树脂,一样是结晶性树脂(如聚甲醛、尼龙、聚丙烯、聚乙烯及PET树脂等)比非结晶性树脂(如PMMA树脂、聚氯乙烯、聚苯乙烯、ABS树脂及AS树脂等)的变形大。
另外,由于玻璃纤维增强树脂具有纤维配向性,变形也大。
11、气泡
依照气泡的产生缘故,解决的计策有以下几个方面:
(1)在制品壁厚较大时,其外表面冷却速度比中心部的快,因此,随着冷却的进行,中心部的树脂边收缩边向表面扩张,使中心部产生充填不足。
这种情形被称为真空气泡。
解决方法要紧有:
(a)依照壁厚,确定合理的浇口,浇道尺寸。
一样浇口高度应为制品壁厚的50%~60%。
(b)至浇口封合为止,留有一定的补充注射料。
(c)注射时刻应较浇口封合时刻略长。
(d)降低注射速度,提高注射压力,
(e)采纳熔融粘度等级高的材料。
(2)由于挥发性气体的产生而造成的气泡,解决的方法要紧有:
(a)充分进行预干燥;(b)降低树脂温度,幸免产生分解气体。
(3)流淌性差造成的气泡,可通过提高树脂及模具的温度、提高注射速度予以解决。
12、白化
白化现象最要紧发生在ABS树脂制品的推出部分。
脱模成效不佳是其要紧缘故。
可采纳降低注射压力,加大脱模斜度,增加推杆的数量或面积,减小模具表面粗糙度值等方法改善,因此,喷脱模剂也是一种方法,但应注意不要对后续工序,如烫印、涂装等产生不良阻碍
找了一段,供参考:
注塑产品在生产过程中发生表面有麻坑现象有两个缘故:
1.模具不清洁;2.注塑温度,注塑压力及注塑速度未调试到最正确状态(依原料品种,产品大小的不同而不同)。
在描述注塑件的缺陷时将涉及许多技术术语。
其中包括流痕、银丝、烧伤、气孔等。
缺陷缘故
注塑件产生缺陷的某些典型的缘故是工艺参数不正确,材料干燥不佳,滞留时刻过长,熔料温度不适当,模具设计错误,模具或机床被磨损。
起初步判定属于某类缺陷之后,就需对缺陷进行详细的诊断。
这时对造成注塑件缺陷的前题来说,可能显现200种不同的状况。
一旦确定了具有最大可能性的有关前题时,即可开始纠正不良现象的行动。
往往可能直截了当从前题中得出结论,那么能够按照向用户举荐的行动方案采取行动。
缺陷和缘故之间的关系
注塑件的征兆和前题之间并不是始终具有确定的关系。
换句话说,不同的征兆可能有着相同的前题。
专家系统的用处不在于显示了征兆之间关系的首次判定,而是在进一步信息的关心下,在所有有关前题中确定可能性最大者。
至少达到80%的可能性时才认为这种前题具有充分的依据,当低于80%时,按照规那么仍不加以考虑。
在判定注塑件缺陷时,假如只有将显现缺陷的信息,那么关于判定缺陷是专门不够的。
只有在充分探究之后,由专家或专家系统明确地描述最大可能的前题。
在此过程中将涉及以下各种重要问题:
①材料种类;②产生缺陷的可能部位;③产生缺陷的可能时机;④缺陷的现象;⑤材料的预处理状况;⑥使用模具的状况及机床种类。
需依照征兆考虑不同的条件。
并应对每一种独立的征兆设置这些条件。
废疵品缘故分析:
注塑件废疵品大部分是在试模过程中产生的,因此,仅就试模时塑件易产生的缺陷进行缘故分析。
常见的注塑缺陷是:
飞边、缺料、缩坑、气泡、熔接痕、破裂、翘曲变形、白化、流痕、喷射流、颤纹、模糊、银条、烧焦、表面光泽不良、起层等。
在注塑成型过程中,制品缺陷产生的要紧缘故是:
(1)成型塑件设计不合理;
(2)模具设计、制造不合理;(3)塑料本身的性质;(4)成型工艺条件选择不当;(5)注塑机型号匹配不合理。
因此,解决塑料注射成型不良这一问题,可从注射机、成型条件与模具(包括制品设计)、塑料等方面入手。
然而,从塑料中寻求缺陷产生的缘故专门困难,因为成型件的缺陷常常是由前面所述几种缘故相互藕合作用而形成的,故缺陷的形成缘故有赖于宽敞工程技术人员的体会与判定。
二、计策
1、合理的塑件设计
设计塑件是要壁厚平均,这是因为成型周期中的冷却时刻是由塑件壁厚决定的,假设某一部分较厚,冷却时刻受厚的部分阻碍而延长成型周期,使成型效率降低;另外假如壁厚不均,那么造成收缩不均,产生缩坑或者内部应力,以至发生变形或者开裂。
塑件设计要具有一定的脱模斜度,保证塑件的顺利脱模。
因为内部应力往往集中在面与面的相交处,即集中在拐角,为了减少变形,在根部设计圆角可使应力分散,同时还能改善塑料的流淌性,也有利于脱模。
有时为了增强塑件或提高塑料的流淌性,需设置加强筋,要注意在脱模方向上应设有反向斜度。
2、改进模具设计
浇口设计是一个重要且复杂的问题,其形式有直截了当浇口、侧浇口、埋伏式浇口、点浇口等。
实际制造中如何选择浇道排列、浇口种类与位置,大多是由塑件的形状、尺寸精度和外观要求而决定的,同时其浇道的形式也是多种多样的。
为了使塑料填充的过程同时终止,浇口与浇道必须平稳。
在注塑过程中,注射到模具型腔内的熔融塑料温度为200~300℃左右,而塑件固化后从模具型腔中取出时其温度在60℃以下,温度降低是由于模具通入冷却水将热量带走,因此冷却系统的合理性直截了当阻碍塑件的尺寸精度和机械性能。
在实际注塑模时还必须考虑排气的问题,假如注塑模型腔内的气体不能顺利排出,将使制品产动气泡、疏松、充填不满、熔接不牢、制件表面发泡,或在注塑时由于气体被压缩所产生的高温使制件底部炭化烧焦。
常用的排气方法专门多,例如利用排气孔槽排气、配合间隙排气等。
在设置顶出系统时应综合考虑,以幸免变形、白化、卡滞现象发生。
3、调整注塑工艺
关于不同类型和牌号的塑料,其烘干与成型时的熔体温度差不多上有明确规定的,因此在制定成型工艺时,可依照制品所用塑料的具体要求,确定其烘干与加热料筒的温度。
压力也是成型工艺的重要参数,压力分为注射压力与保压压力两个时期。
注射压力是指推动螺杆将熔体注入模具型腔内所用的压力,保压压力是指在填充立即完成时,注入熔体来补足制品因冷却固化而引起体积收缩的补充过程所用的压力,在成型过程中,正确的选择注射压力和保压压力与注射速度,是成型工艺成败的关键。
目前,大多数注塑机采纳电脑操纵,采取分级注射的方法。
4、选用高效的设备
选用注塑机时应考虑与模具的匹配问题,锁模力既要满足要求又不能过大,每次注射量不小于塑件加浇道凝料的重量。
设备注意经常爱护,保证生产的正常运行。
5、终止语
由于注塑成型是一个复杂的过程,阻碍制品成型的因素专门多,往往在改善一个因成型因素所带来的制品缺陷,可能会使另一个往常无关紧要因素突出出来,使制品显现新的缺陷。
因此,在制定和调整成型工艺时,不仅要建立压力、速度、温度的正确组合,而且关于螺杆转速、螺杆各位置的注射压力、保压的正确选择。
背压以及冷却时刻等问题也应充分重视。
先进的模具、高效的设备以及合理的成型工艺是现代化注塑生产中的三大要素。
因此,作为模具设计者除研究模具结构和加工技术外,还应把握一定的注射成型工艺技术,专门对制品在成型过程中常见的缺陷及解决方法应有充分的认识。
可能为以下三种情形:
5.1浇口区域缺陷
(1)冷料斑:
冷料斑要紧是指制品近浇口处带有雾色或亮色的斑痕或从浇口发出的宛假设蚯蚓贴在上面的弯曲疤痕,它们由进入型腔的塑料前锋料或因过分的保压作用而后来挤进型腔的冷料造成。
前锋料因为喷嘴或流道的冷却作用传走热量,在进入模穴时,形成熔体破裂,紧接着又被后来的热熔料推拥,因此就成了冷料斑。
冷料斑在薄壁制品上将摊开而成烟云状斑痕,在自由流淌的厚壁制品上将留下一条蜿转走向的疤痕。
此现象常发生在ABS、PC等制品上。
至于由过度保压作用形成的冷料斑,是在保压时刻过长,保压压力过大的情形下将流道、浇口上的冷料连续挤进制品所致,这种冷料斑往往使靠近浇口的一片专门小范畴形成圆形的亮斑。
冷料斑不单破坏了制品的表观质量,阻碍喷涂或电镀成效,而且不同程度上降低制品机械强度。
依照上述分析有针对性地调高料筒和射嘴温度,减慢注射速度,增大注射压力,调好注射、保压时刻,提高模温来减小冷料的阻碍。
合理的模具浇口设计能够预先减小或幸免冷料斑的形成,传统而有效的方法是在流道末端开设冷料井,使前锋冷料陷入井内而不致进入模穴。
有些模具除设冷料井外,还需要考虑浇口的形式,大小和位置的合理性。
此外,气体的干扰作用也会使浇口处显现混浊性斑纹,应改善模具排气,减小或调换润滑剂,加强料的干燥,去除料中污染物。
(2)光芒线:
制品表面显现以浇口为中心的由不同颜色和光泽组成的辐射条纹。
它可能表现为:
①深色底暗色线;②暗色底深色线;③暗色线密集而发白。
如PS和改性PS混合经常有显现。
一样与以下因素有关:
(1)2种料流变性、着色性等方面有差异,浇注系统层流与紊流流速和受热状况有差异;
(2)塑料因热分解而生成烧焦丝;(3)塑料进模时气体物质的干扰(如空气)等。
5.2解决方法:
(1)调剂好松退位置,使之刚好不流延为止,以免抽进空气。
(2)混合好塑料,要充分将塑料和着色剂混合平均,可用机械搅拌除湿机并加入适当的扩散剂。
(3)塑化完全,可利用挤出机进行预塑或造粒,使塑料充分熔融混合。
(4)成型时采纳较合理的工艺条件。
如提高喷嘴温度,减少前炉温度,降低注射速度、压力,缩短注射和保压时刻,提高模温。
(5)改进浇口设计,如放大浇口直径,改变浇口位置,将浇口改成圆角过渡;在流道端添加冷料井。
(6)抛光螺杆和料筒前端的内表面。
(7)加强原料的干燥,清除料筒内高温死角。
6、气泡(真空泡)
透亮塑料制品内部存在着的气泡,有2种情形,一种是充满气体,形成的缘故是由于气体的干扰,这在银纹(气纹)部分差不多分析过;另一种是〝真空泡〞。
这在制品的凹陷(缩水)部分也已作过分析。
那个地点作补充说明。
一样来说,假如在开模瞬时已发觉存在气泡,是属于气体干扰问题,用克服气体干扰的方法解决。
假如在脱模冷却过程显现并变大,是属于真空泡的问题。
真空泡的形成是由于充模时塑料不足或压力较低。
在模具的急剧冷却作用下,与模壁接触的熔料表面第一固化,然后中心部分的熔料冷却收缩,造成体积缩小而形成泡。
解决方法:
(1)提高注射能量:
压力、速度、时刻和料量;
(2)调整料温:
当真空泡远离浇口位置时,提高料温使熔料流淌顺畅,压力能传到远浇口部位,当真空泡在浇口邻近时可降低料温使收缩减小;
(3)适当提高模温,专门是形成真空泡部位的局部模温;
(4)将浇口设在制品壁厚部位,改善喷嘴、流道和浇口的流淌状况;
(5)改善模具排气状况;
(6)缩短制品在模内冷却时刻,必要时将制品投入热水中缓慢冷却;
(7)用针点浇口成型的制品,可用慢速、低温成型解决真空泡问题,当流道上有真空泡时可加大流道尺寸。
7、鼓泡
有些塑料制品在脱模后,专门快在制品壁厚部位显现鼓泡现象,这是由于制品厚壁部位的气体膨胀造成。
解决方法:
(1)有效地冷却,延长冷却时刻;
(2)提高保压压力和时刻;(3)降低料的干燥温度及成型温度;(4)降低充模速度;(5)改善制品的壁厚平均度。
8、翘曲
翘曲变形是指注塑制品的形状偏离了模具型腔的形状,它是塑料制品常见的缺陷之一。
显现翘曲变形的缘故专门多,单靠工艺参数解决往往力不从心。
结合相关资料和实际工作体会,下面对阻碍注塑制品翘曲变形的因素作简要分析。
8.1模具的结构对注塑制品翘曲变形的阻碍。
在模具方面,阻碍塑件变形的因素要紧有浇注系统、冷却系统与顶出系统等。
8.1.1浇注系统
注塑模具浇口的位置、形式和浇口的数量将阻碍塑料在模具型腔内的填充状态,从而导致塑件产生变形。
流淌距离越长,由冻结层与中心流淌层之间流淌和补缩引起的内应力越大;反之,流淌距离越短,从浇口到制件流淌末端的流淌时刻越短,充模时冻结层厚度减薄,内应力降低,翘曲变形也会因此大为减少。
一些平板形塑件,假如只使用一个中心浇口,因直径方向上的收缩率大于圆周方向上的收缩率,成型后的塑件会产生扭曲变形;假设改用多个点浇口或薄膜型浇口,那么可有效地防止翘曲变形。
当采纳点浇口进行成型时,同样由于塑料收缩的异向性,浇口的位置、数量都对塑件的变形程度有专门大的阻碍。
另外,多浇口的使用还能使塑料的流淌比(L/t)缩短,从而使模腔内熔体密度更趋平均,收缩更平均。
同时,整个塑件能在较小的注塑压力下充满。
而较小的注射压力可减少塑料的分子取向倾向,降低其内应力,因而可减少塑件的变形。
8.2.2冷却系统
在注射过程中,塑件冷却速度的不平均也将形成塑件收缩的不平均,这种收缩差别导致弯曲力矩的产生而使塑件发生翘曲。
假如在注射成型平板形塑件(如手机电池壳)时所用的模具型腔、型芯的温度相差过大,由于贴近冷模腔面的熔体专门快冷却下来,而贴近热模腔面的料层那么会连续收缩,收缩的不平均将使塑件翘曲。
因此,注塑模的冷却应当注意型腔、型芯的温度趋于平稳,两者的温差不能太大(现在可考虑使用两个模温机)。
除了考虑塑件内外表的温度趋于平稳外,还应考虑塑件各侧的温度一致,即模具冷却时要尽量保持型腔、型芯各处温度平均一致,使塑件各处的冷却速度均衡,从而使各处的收缩更趋平均,有效地防止变形的产生。
因此,模具上冷却水孔的布置至关重要。
在管壁至型腔表面距离确定后,应尽可能使冷却水孔之间的距离小,才能保证型腔壁的温度平均一致。
同时,由于冷却介质的温度随冷却水道长度的增加而上升,使模具的型腔、型芯沿水道产生温差。
因此,要求每个冷却回路的水道长度小于2米。
在大型模具中应设置数条冷却回路,一条回路的进口位于另一条回路的出口邻近。
关于长条形塑件,应采纳直通型水道。
(而我们的模具大多是采纳S型回路----既不利于循环,又延长周期。
8.3.3顶出系统
顶出系统的设计也直截了当阻碍塑件的变形。
假如顶出系统布置不平稳,将造成顶出力的不平稳而使塑件变形。
因此,在设计顶出系统时应力求与脱模阻力相平稳。
另外,顶出杆的截面积不能太小,以防塑件单位面积受力过大(专门在脱模温度太高时)而使塑件产生变形。
顶杆的布置应尽量靠近脱模阻力大的部位。
在不阻碍塑件质量(包括使用要求、尺寸精度与外观等)的前提下,应尽可能多设顶杆以减少塑件的总体变形(换顶杆为顶块确实是那个道理)。
用软质塑料(如TPU)来生产深腔薄壁的塑件时,由于脱模阻力较大,而材料又较软,假如完全采纳单一的机械顶出方式,将使塑件产生变形,甚至顶穿或产生折叠而造成塑件报废,如改用多元件联合或气(液)压与机械式顶出相结合的方式成效会更好(以后会用到)。
8.2塑化时期对制品翘曲变形的阻碍
塑化时期即由玻璃态料粒转化为粘流态熔体的过程(培训时讲