大型轴类锻件锻造工艺过程数值模拟.docx
《大型轴类锻件锻造工艺过程数值模拟.docx》由会员分享,可在线阅读,更多相关《大型轴类锻件锻造工艺过程数值模拟.docx(46页珍藏版)》请在冰豆网上搜索。
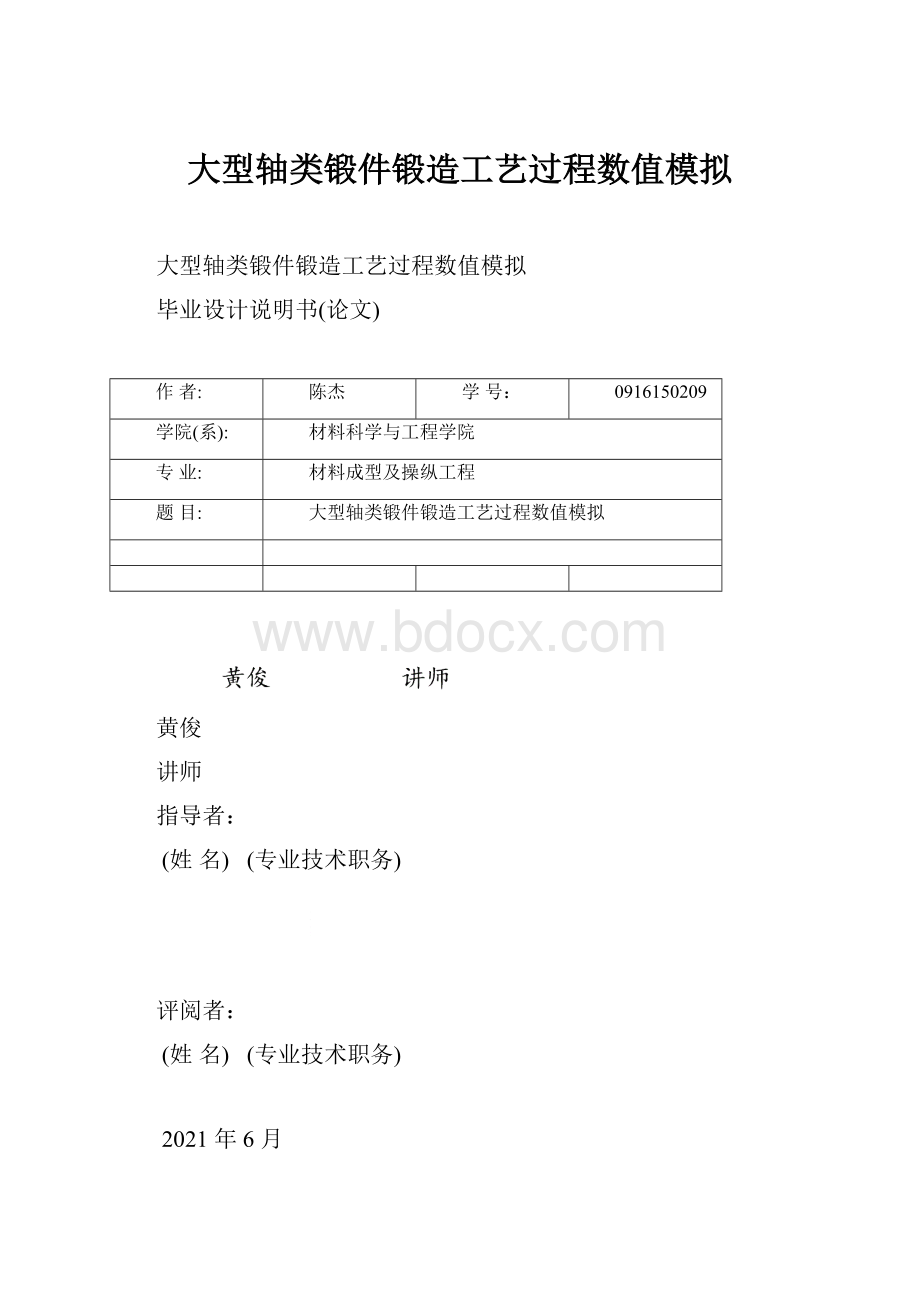
大型轴类锻件锻造工艺过程数值模拟
大型轴类锻件锻造工艺过程数值模拟
毕业设计说明书(论文)
作者:
陈杰
学号:
0916150209
学院(系):
材料科学与工程学院
专业:
材料成型及操纵工程
题目:
大型轴类锻件锻造工艺过程数值模拟
黄俊
讲师
指导者:
(姓名)(专业技术职务)
评阅者:
(姓名)(专业技术职务)
2021年6月
毕业设计说明书〔论文〕中文摘要
本文针对2MW风电主轴为研究对象,将其完整的锻造工艺分成了四大锻造步骤,并运用有限元软件DEFORM,重点对倒棱滚圆、镦粗、拔长、号印分料和模锻等步骤分别进行了数值模拟。
在模拟过程中分析了各个步骤的锻件内部应力应变和尺寸精度的阻碍。
具体的研究内容和所得结论如下:
(1)获得了大型风电主轴类锻件倒棱滚圆过程有限元模型,使用平砧滚圆,截面平均直径值与初始方形锻件边长相比增加2.8%,
(2)
(3)获得了大型风电主轴类锻件镦粗拔长过程有限元模型,,研究了拔长过程中接砧量对工件表面缺陷的阻碍。
应设定较小的接砧量60mm,保证锻件表面质量同时提高工作效率。
(4)
(5)获得了大型风电主轴类锻件模锻过程有限元模型,研究了模锻过程中锻件应力应变和温度的改变,以及最终锻件的精度。
最终锻件顶部平均直径1546mm,底部直径405mm,均符合工艺卡要求。
(6)
关键词风电主轴,数值模拟,锻造工艺,,
毕业设计说明书〔论文〕外文摘要
TitleSTUDYONFESIMULATIONOFFORGINGPROCESSOF
HEAVYAXIALFORGINGS
Abstract
Thecompleteforgingprocessof2MWwindpoweraxisisstudiedanddividedinto4mainforgingapproachesfirstly.Then,thefiniteelementcodeDEFORMisappliedtosimulatethedifferentforgingapproachsequentially.Andfinally,byanalyzingtheinfluenceofdifferentforgingparametersontheinternalqualityandsizeprecisionofthefinal-shapedforging.Themainresearchcontentsandconclusionsofthisarticlearesummarizedasfollows:
(1)Thechamferingandroundingprocessofwindpoweraxisaresimulated.Duringthesimulation,thestrain-stressdistribution,temperatureandthesizeprecisionofthefinalforgingarediscussed.Withaflatanvilrounded,thecross-sectionalaveragediameterofforgingincreasesby2.8%comparedtotheoriginal.
(2)
(3)Theheadingandstretchingprocessofwindpoweraxisaresimulated.Duringthesimulation,theimpactofreceived-anvil-distanceonsurfacedefectsthefinalforgingarediscussed.Settingthereceived-anvil-distanceof60mm,whichnotonlyimproveworkefficiency,butalsotoensurethesurfaceofthefinalforging.
(4)
(5)Thedieforgingprocessofwindpoweraxisissimulated.Duringthesimulation,thestrain-stressdistribution,temperatureofthefinalforgingandthesizeprecisionarediscussed.Theaveragediameterofthetopofthefinalforging1546mm,bottomdiameter405mm,areinlinewithprocesscardrequirements.
(6)
Keywordsheavyaxialforging,chamferingandrounding,headingandstretching,dieforging,numericalsimulation,forgingprocessoptimization
目次
1绪论
1.1选题背景及意义
大型锻件生产的要紧特点是:
体重形大,质量要求严格,工艺过程复杂,生产费用高,生产周期长。
其完整的生产流程为:
冶炼→铸锭→锻造→粗加工→热处理→精加工。
明显大锻件的质量是炼钢、锻造和热处理等专业综合技术水平的标志,其中锻造环节起着专门重要的作用。
大型锻件锻造的任务,不仅是为了得到一定形状和尺寸的锻件,更重要的是通过锻造破裂钢锭的铸态组织,排除钢锭内部的疏松、裂纹、气孔等缺陷,改善第二相化合物及非金属夹杂物在钢中的分布,以提高锻件性能。
可见,锻造是大型锻件生产的重要工序之一,锻造工艺的好坏以及锻造水平的高低往往会对最终成形产品的质量产生专门大的阻碍,甚至可能造成锻件报废的后果。
然而,目前我国大型锻件锻造工艺过程的制定要紧依据人为体会,缺乏对锻造具体工艺规律与实质的认识。
因此,要提高大型锻件的生产水平,就必须从具体的锻造过程入手,研究每一步锻造工艺及其参数对大锻件成形质量的阻碍,真正了解大锻件锻造的目的与实质,从而制定出有效且可行的锻造工艺[1-3]。
风电装备中采纳的大型轴类锻件重数十吨,前期投入大,一旦报废,缺失庞大,对锻造工艺设计的合理性提出了更高的要求,针对大型风电主轴锻件制造过程,采纳三维有限元方法进行温度场及应力场数值模拟与仿真,分析锻件成形过程中温度及应力应变的分布与变化规律,从而研究锻造温度、加热时刻、锻压力等工艺参数与锻件质量的关系,得出工艺参数对锻件质量的阻碍规律。
1.2国内外研究概况
大型锻件的锻造变形是复杂的大塑性变形,运用经典的金属塑性成形理论专门难求出精确解,对内部应力、应变场的分析更是无能为力。
因此,物理模拟和数值模拟便成为了求解锻造过程中应力应变场以及分析金属流淌规律的有效方法。
90年代前,塑性泥法[4-5]、密珊云纹法[6-7]等物理模拟方法得到了广泛的应用,为人们最初认识拔长和评判拔长方法提供了关心。
然而,由于大型锻件的尺寸过大,物理模拟方法只能采纳按比例缩小的近似模型,如此的近似使得模拟结果产生较大的误差,限制了其应用范畴。
近二十年来,随着运算机软硬件水平和数值分析方法理论的不断进展,有限元模拟技术在金属加工领域得到了大量的应用,目前差不多成为人们研究拔长技术和理论、优化并规范拔长工艺的最有效工具。
大型轴类锻件的锻造过程包括拔长、倒棱、滚圆等差不多工序。
其中拔长是改善锻件性能的要紧工序,目前国内外学者针对不同的拔长工艺和特点,差不多运用数值模拟技术进行了许多研究[8-12]。
倒棱和滚圆是大型轴类锻件的最后成形工序,对锻件最终的尺寸精度和成形质量同样有着专门大阻碍。
但一直以来,有关倒棱和滚圆的深入研究还专门少:
燕山大学的王雷刚选取大型锻件横截面建立二维模型,并运用ANSYS软件模拟平砧倒棱,研究了锻件在倒棱过程中的应力应变分布[13];ChoiSK等人针对不同的进给量和翻转角度,运用Deform软件模拟了锻件的滚圆过程[14]。
然而这些研究并未分析型砧形状对锻造成形精度的阻碍,也没有考虑倒棱与滚圆两道工序之间的相互作用。
上海交通大学付强,崔振山等人通过编写Fortran程序,反复调用Deform软件的前处理模块,实现了包括一次进给多次翻转的倒棱滚圆过程的自动模拟。
然后依照模拟结果,分析并比较了不同型砧下锻造工艺路线的拔长成效,以及在给定坯料初始尺寸的情形下成形锻件的尺寸大小、精度和内部应力应变状态[15]。
是否来自同一篇文献?
上海交通大学付强对圆截面坯料拔长至矩形截面的工艺过程进行数值模拟分析,该工艺过程是大型轴类锻件完整拔长工艺的第一步,为后续矩形截面锻件的拔长做好锻件形状及初始内部质量的预备,是大型轴类锻件拔长工艺中的关键步骤[15-16]。
1.3有限元软件DEFORM-3D简介加引用
1.4
DEFORM-3D是对在一个集成环境内综合建模、成形、热传导和成型设备特性,并基于工艺模拟系统的有限元仿真分析软件。
它专门用于各种金属成形工艺和热处理工艺的模拟仿真分析,可模拟自由锻、模锻、挤压、拉拔、轧制等多种塑性成形工艺过程,包括冷、温、热塑性成形问题、多工序塑性成形问题、模具应力和弹性变形及破旧的模拟分析。
可提供极有价值的工艺分析数据;如材料流淌、模具填充、锻造负荷、模具应力、晶粒流淌、金属微结构的缺陷产生进展情形等。
DEFORM-3D适用于刚性、塑性及弹性金属材料、粉末烧结体材料、玻璃及聚合物材料等的成形过程。
DEFORM-3D强大的模拟引擎能够分析金属成形过程中多个关联对象祸合作用的大变形和热特性,系统中集成了在必要时能够自行触发自动网格重划生成器,生成优化的网格系统。
在精度要求较高的区域,能够划分较细密的网格,从而降低问题的规模,并显著提高运算效率。
DEFORM-3D图形界面,既强大又灵活。
便于输入工艺参数、几何数据、材料性能、热性能、扩散和材料金相组织数据,并为用户观看结果数据提供了有效的工具。
1.3.1DEFORM软件的要紧功能
〔1〕成形分析:
①冷、温、热锻的成形和热传导偶合分析,提供材料流淌、模具充填、成形载荷、模具应力、纤维流向、缺陷形成和韧性破裂等信息;②丰富的材料数据库,包括各种钢、铝合金、钛合金等,用户还可自行输入材料数据;③刚性、弹性和热粘塑性材料模型,专门适用于大变形成形分析,弹塑性材料模型适用于分析残余应力和回弹问题,烧结体材料模型适用于分析粉末冶金成形;④完整的成形设备模型能够分析液压成形、锤上成形、螺旋压力成形和机械压力成形;⑤温度、应力、应变、损害及其他场变量等值线的绘制使后处理简单明了。
〔2〕热处理:
①模拟正火、退火、淬火、回火、渗碳等工艺过程;②推测硬度、晶粒组织成分、扭曲和含碳量;③能够输入顶端淬火数据来推测最终产品的硬度分布;④能够分析各种材料晶相,每种晶相都有自己的弹性、塑性、热和硬度属性。
混合材料的特性取决于热处理模拟中每步各种金属的百分比。
DEFORM-3D用来分析变形、传热、热处理、相变和扩散之间复杂的相互作用,各种现象之间相互耦合。
拥有相应的模块之后,这些耦合将包括:
由于塑性变形引起的升温、加热软化、相变操纵温度、相变内能、相变塑性、相变应变、应力对相变的阻碍以及含碳量对各种材料属性产生的阻碍等[21-23]。
1.5本课题研究内容
1.6
本课题以有限变形理论及传热学理论为基础,运用有限元分析软件DEFORM-3D对倒棱滚圆、平板镦粗、平板拔长、模锻等锻造过程进行模拟分析,并用DEFORM自带模块对数值模拟的数据进行采集,并做进一步的分析。
本文要紧研究内容如下:
(1)分析风电主轴锻造时每一步骤的特点,并依照不同步骤制定相应的研究方法;
(2)
(3)通过DEFORM-3D完成每一步的有限元建模;
(4)
(5)分析并讨论平砧倒棱滚圆过程的应力、应变、温度分布规律和锻件滚圆后的精度;
(6)
(7)分析平板镦粗及拔长过程的应力、应变、温度分布规律;
(8)
(9)通过设定不同的接砧量,分析拔长过程中接砧量对锻件表面的阻碍;
(10)
(11)模锻过程中锻件应力分析、温度分布及使用性能的推测。
(12)
2大型风电主轴锻件锻造过程有限元模型建立
3
3.1大型风电主轴锻件锻造过程模拟参数原2.2.1节内容
3.2
3.3大型风电主轴锻件锻造过程模拟过程原2.2.2节内容
3.4
3.5此节删除
(1)
(2)
采纳DEFORM软件对整个锻造过程的数值模拟,需要在每一工步模拟终止时,重新调用DEFORM的前处理模块来手动设置新的上下砧及锻件的位置、角度等工艺参数,然后再进行下一工步的模拟。
2.2.1锻造工艺模拟数据预备
本文选取2MW及以上风电主轴,如图2.1。
锻件材料为R34CrNiMo6A号钢〔德国牌号〕,对应中国牌号40CrNiMoA,对应美国牌号4340。
初始矩形截面坯料的尺寸为1200×1200mm,最终应锻成符合客户要求的大型轴类锻件。
上下砧由于变形量专门小,在DEFORM中设置为刚体,上砧板下压速度为5mm/s。
初始模型的材料参数如表2.1所示。
表2.1初始有限元模型的材料参数
锻件材料
AISI-4340
锻件初始温度〔℃〕
1200℃
上下砧初始温度
300℃
环境温度
剪切摩擦系数
锻件与上下砧间传热系数
20℃
0.3
5
锻件与环境间传热系数
0.02
(a)三维立体图
〔b〕锻件工艺图
图2.1工件实体图
2.2.2多工步锻造过程的模拟方案
2MW风电主轴典型的锻造过程包括倒棱滚圆、镦粗拔长、分料切除和模锻四个要紧工序。
本文将对所有步骤进行模拟分析,其中倒棱滚圆和模锻是两个要紧过程。
锻造数值模拟过程中各时期的锻件模型及形状变化。
先将初始矩形截面坯料〔图2.2a,截面边长为1200mm〕通过倒棱工序压成八方形截面坯料〔图2.2b〕,最后通过滚圆工序压成所需的圆轴类锻件〔图c,圆截面直径应操纵在1200~1250mm之间〕。
然后将圆柱镦粗〔图d〕,再通过拔长工序降低内部应力〔图e,截面直径1300mm〕。
用印刀砧在拔长后的圆柱上压出痕迹〔图f〕,对分料部分再次进行拔长〔图g,拔长部分的截面直径操纵在790~820mm〕,切除拔长部分尾部〔图h〕。
最后将锻件放入模具,锻压出最终零件〔图i〕。
如图2.2所示。
这段内容用自己的话写
〔a〕
〔b〕
〔c〕
〔d〕
〔e〕
(e)
(f)
(g)
(h)
(i)
图2.2风电主轴锻件锻造过程图示
依照上图所示的锻造工艺过程,将大型风电主轴锻件的数值模拟分析分为四大步骤,研究不同的锻造工序和锻造过程中的压下量、下压速度、接砧量等锻造参数,,对锻件的尺寸精度和成形质量的阻碍,风电主轴锻造的四个要紧步骤为:
〔1〕初始矩形截面锻件倒棱滚圆的数值模拟。
〔2〕大型圆柱的镦粗拔长的数值模拟。
〔3〕号印分料与切除过程的数值模拟。
〔4〕大型轴类锻件的模锻过程数值模拟。
大型风电主轴锻件锻造过程的数值模拟
3.6大型风电主轴锻件倒棱滚圆过程的数值模拟
3.7
3.1.1倒棱滚圆过程有限元模型建立
锻件材料为R34CrNiMo6A号钢〔德国牌号〕,对应中国牌号40CrNiMoA。
40CrNiMoA属于合金调制钢,它是在优质碳素钢的基础上,适当的加入合金元素。
具有高的强度,高的韧性和良好的淬透性。
材料性能如表3.1所示。
要紧用于高强度、高韧性、截面尺寸较大的锻件:
风力发电机锻件,锻压机曲轴等。
表3.1材料要紧性能参数参数顺序换一下
物理性能
参数值
抗拉强度σb(MPa)
≥980
屈服强度σs(MPa)
≥835
伸长率δ5(%)
≥12
断面收缩率ψ(%)
≥55
冲击功Akv(J)
≥78
实际生产中,在倒棱滚圆工艺前,需要将大型锻件放到加热炉中加热,保证合适的锻造温度。
依照生产过程中的实际条件,对模型做出以下处理:
(1)考虑矩形截面毛坯与砧板及周围环境的传热;
(2)
(3)考虑到倒棱滚圆的过程中平砧的变形比较小,将其处理成刚体。
(4)
依照以上条件对矩形截面锻件进行建模,截面尺寸为1200×1200mm。
锻件轴向长度为1700mm,初始有限元模型如图3.1所示。
采纳相对网格设置,网格单元数量设定为20000,网格比率为2。
图3.1初始矩形截面有限元建模
3.1.2平砧倒棱滚圆过程分析
为了提高模拟效率,在模拟过程中,滚圆过程中只模拟一次。
表3.2为本章平砧倒棱滚圆过程有限元模拟过程中所用到的参数符号。
表3.2物理参数对应符号表
参数物理意义
符号
初始方形截面对边中点距离
倒棱后上下砧间距
滚圆后上下砧间距
d0
m0m90m120
n0n90n120
2
1
6
5
4
3
砧板
图3.2平砧倒棱滚圆过程
图3.2为平砧倒棱滚圆工艺过程示意图,其中的单箭头表示上砧压下次序及方向。
平砧倒棱是压对角倒八方的过程,为了保证倒棱后锻件截面为正八边形,理想情形下上下砧压下后的距离应与初始方形截面两边中点的距离d0相等。
因此,在倒棱过程中操纵上下平砧压下后的间距:
m0=d0〔3-1〕
平砧滚圆是压正八方锻件八条棱边的过程,压下四趟后即能压遍所有棱边。
由于滚圆过程压下量较小,〝鼓肚〞现象不明显,因此在滚圆过程中同样操纵上下砧压下后间距:
n0=d0〔3-2〕
平砧倒棱滚圆具体工序如表3.3所示。
表3.3平砧倒棱滚圆工序表〔单位:
mm〕
工序
翻转角度
该方向压前尺寸
压后尺寸
压下量
1
0
1697
1200
497
2
90
1700
1200
500
3
22.5
1273
1200
73
4
45
1230
1200
30
5
45
1233
1200
33
6
45
1240
1200
40
3.1.3模拟结果分析
3.1.3.1倒棱过程尺寸精度分析
从上述分析可知,通过倒棱过程,平砧将锻件方形截面锻成正八边形。
图3.3为平砧倒棱后的锻件形状。
图3.3平砧倒棱后锻件形状
从图3.3能够看出,平砧倒棱后,工件表面局部有下凹缺陷,是因为一次下压量过大引起。
选取倒棱后锻件截面各边的中点,对各点到截面中心的距离进行分析和比较,以此来描述倒棱后锻件的形状精度和变形程度,分析结果如图3.4及表3.4所示。
图3.4倒棱后截面各边到中心距离
表3.4为倒棱后截面上各边上的点到中心的距离统计表。
表3.4倒棱后截面各边到中心距离分析表〔单位:
mm〕
砧型
距离均值
距离变化Δd
标准方差
平砧
620
3.3%
8.2
从表3.4能够看出,平砧倒棱后正八边形截面各边到中心距离平均为d=620mm,与初始方形截面相比d∆=+3.3%。
这是由于平砧倒棱时不管如何翻转均是锻压长方体锻件的两条对棱,且压下量较大,如此在锻件不受压的四个侧面上始终会显现〝鼓肚〞。
3.1.3.2滚圆过程尺寸精度分析
为了压遍八棱柱锻件的所有侧棱达到滚圆的成效,平砧需通过四趟翻转压下。
图3.5为平砧倒棱后锻件形状〔一次给进〕。
为了检查滚圆成效和成形锻件的尺寸精度,在锻件截面圆周平均选取12个点,对滚圆后每一点处的半径值进行分析和比较。
图3.5平砧滚圆后锻件形状〔一次给进〕
图3.6滚圆后截面个点半径
表3.5滚圆后截面各点半径分析(单位:
mm)
砧型
最大
最小
均值
标准方差
平砧
627
607
617
7.4
从表3.5能够看出,平砧倒棱滚圆后锻件截面平均直径值与初始方形锻件边长相比增加2.8%,且成形锻件截面各点半径值方差较大,尺寸精度不佳,需要增加工序进一步滚圆。
3.1.3.3倒棱滚圆后成型锻件内部温度变化
图3.7锻件内部温度变化
由图3.7可知,锻造过程中,心部温度下降缓慢,而公交表面温度下降较快。
因为表面不仅和环境有热交换,和上下砧板也存在热损耗。
3.1.3.4成形锻件内部应力应变分析
锻造过程中锻件心部的应力应变状况是决定锻件质量的重要指标。
在锻造过程中应保证锻件内部应变尽量大,且在心部不存在拉应力。
选取距锻件端面200mm的一截面,平砧压下过程中该截面中心点的应力应变状态进行分析。
〔a〕初始压下〔b〕旋转90°压下
图3.8截面中心一点横向应力比较
图3.8为倒棱过程中该端面中心点应力情形比较。
其中,〔a〕为锻件初次压下过程中的中心点横向应力,〔b〕为翻转90°压下过程中该点横向应力。
从图中能够看出,平砧倒棱时锻件心部始终存在横向拉应力,假如压下量过大有可能在锻件心部产生裂纹。
3.8大型轴类锻件镦粗与拔长的数值模拟
3.9
3.2.1大型轴类锻件镦粗与拔长过程有限元模型建立
镦粗开始前,需要再次将大型锻件放到加热炉中重新加热,以保证锻件的锻造温度不至于过低。
因此,在下一步数值模拟中,能够在保证之前倒棱滚圆得到的锻件形状尺寸的基础上,对锻件重新进行有限元建模。
有限元几何模型如图3.9〔a〕所示。
图中,坯料尺寸为φ1234×1234mm,采纳相对网格设置,只对初始坯料进行网格划分,网格单元数量设定为20000,网格比率为2。
坯料表面均为自由表面,无边界约束,与环境和砧板之间发生热交换
〔a〕初始几何模型〔b〕初始网格模型
图3.9初始有限元模型
3.2.2镦粗过程分析
镦粗坯料的高径比一样不超过2.5~3,最好在2~2.2。
图3.10为墩粗过程示意图,镦粗板直径φ1600,与工件接触面为R3600的圆弧面,压下量500mm,下压速度5mm/s。
墩粗漏盘直径φ1700,漏盘直径φ500,接触面为R5000的圆弧面。
上下砧板均为弧面,能够让工件受力平均,鼓型饱满。
图3.10墩粗过程示意图
3.2.3拔长过程分析
拔长工序紧跟镦粗之后,不需要重新建模,直截了当调用DEFORM-3D前处理模块连续对工件模拟。
将墩粗的毛坯圆柱拔长的过程包括两个步骤,第一将圆截面拔长至矩形截面,然后将矩形截面再次倒棱滚圆。
要紧分析在圆截面拔长至矩形截面的过程中,前后工序的接砧量对锻件表面下凹缺陷的阻碍,如图3.11。
接砧量的定义是:
上一工序压下时平砧右侧表面到下一工序压下时平砧左侧表面的水平距离。
如图3