集成电路制造生产实习实习报告.docx
《集成电路制造生产实习实习报告.docx》由会员分享,可在线阅读,更多相关《集成电路制造生产实习实习报告.docx(13页珍藏版)》请在冰豆网上搜索。
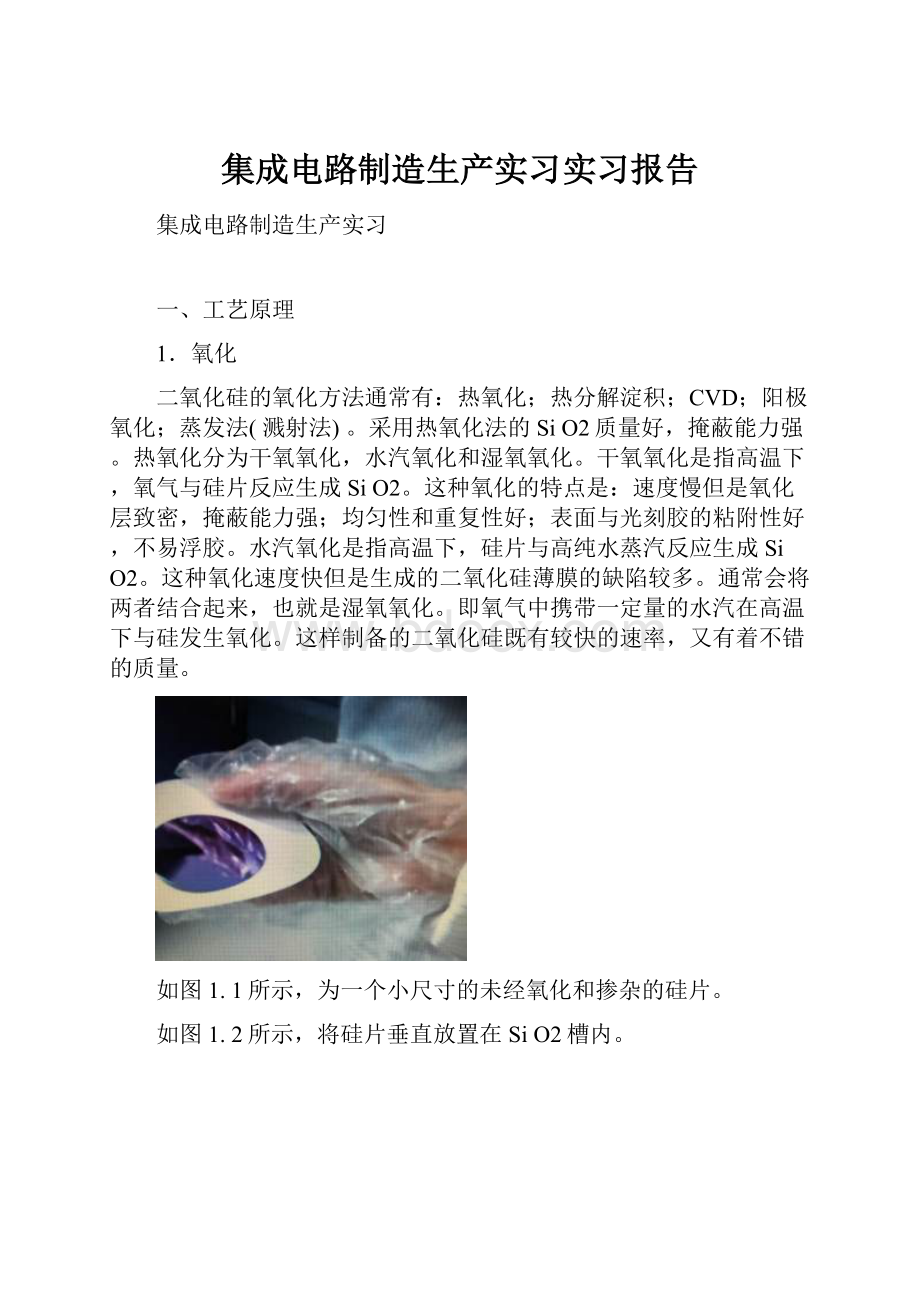
集成电路制造生产实习实习报告
集成电路制造生产实习
一、工艺原理
1.氧化
二氧化硅的氧化方法通常有:
热氧化;热分解淀积;CVD;阳极氧化;蒸发法(溅射法)。
采用热氧化法的SiO2质量好,掩蔽能力强。
热氧化分为干氧氧化,水汽氧化和湿氧氧化。
干氧氧化是指高温下,氧气与硅片反应生成SiO2。
这种氧化的特点是:
速度慢但是氧化层致密,掩蔽能力强;均匀性和重复性好;表面与光刻胶的粘附性好,不易浮胶。
水汽氧化是指高温下,硅片与高纯水蒸汽反应生成SiO2。
这种氧化速度快但是生成的二氧化硅薄膜的缺陷较多。
通常会将两者结合起来,也就是湿氧氧化。
即氧气中携带一定量的水汽在高温下与硅发生氧化。
这样制备的二氧化硅既有较快的速率,又有着不错的质量。
如图1.1所示,为一个小尺寸的未经氧化和掺杂的硅片。
如图1.2所示,将硅片垂直放置在SiO2槽内。
如图1.3所示,将放有硅片的SiO2槽用SiO2制成的硅棒将其缓慢推入氧化炉内。
2.扩散
扩散和离子注入是常用的两种掺杂方法。
按照表面掺杂源浓度分类,扩散分为恒定表面源扩散和有限表面源扩散。
恒定表面源扩散即指在扩散过程中,Si片表面的杂质浓度始终不变(等于杂
质在Si中的溶解度)。
恒定表面源扩散的主要特点如下:
(1)在一定扩散温度下,表面杂质浓度Ns为由扩散温度下的固溶度决定。
(2)扩散时间越长,扩散温度越高,扩散进硅片内的杂质数量越多。
(3)扩散时间越长,温度越高,扩散深度越大。
有限表面源是指在扩散过程中,杂质源限定于扩散前淀积在晶片表面极薄层内的杂质总量Q,硅片内的杂质总量保持不变,没有外来杂质补充,也不会减少。
有限源扩散的特点如下:
(1)扩散时间越长,杂质扩散越深,表面浓度越低;扩散温度越高,杂质扩散得也越深,表面浓度下降得越多;
(2)在整个扩散过程中,杂质总量Q保持不变。
(3)表面杂质浓度可控,
通常对硅片进行了氧化与光刻后,再采用扩散方式或者离子注入。
本次实习采用两级扩散进行p型掺杂,采用硼元素掺杂。
如图1.5(a)所示,将光刻后的硅片放入SiO2槽内,再放置进氧化炉内,高温下进行扩散。
在实际工艺中,通常会采用所谓的两部扩散工艺。
硅晶体管基区的硼扩散,一般就采用双步扩散的方法。
因为硼在硅中的固溶度随温度的变化较小(固溶度是指在一定温度下杂质所能溶入固体中的最大浓度),一般都在1020/cm3以上,而通常要求基区的表面浓度较低些约1018/cm3.所以只得借助于第二步的主扩散来实现对较低表面浓度的控制。
两部扩散工艺如下:
第一步:
在较低温度(800-900℃)下,短时间得浅结恒定源扩散,即预淀积(预扩散);
第二步:
将预淀积的晶片在较高温度下(1000-1200℃)进行深结扩散,最终达到所要求的表面浓度及结深,即再分布(主扩散)。
即预扩散确定了杂志总量,再分布确定了杂质分布情况与结深。
对硅片进行扩散的同时也进行了氧化。
并分别检测了预扩散和在分布后的方块电阻。
3.光刻
光刻是指通过光化学反应,将光刻版(mask)上的图形转移到光刻胶上。
在二氧化硅或者金属或者其他的薄膜上,我们需要在一些区域开窗口,这时就需
要在薄膜上涂上光刻胶来划定需要留下来的薄膜区域和需要刻蚀掉的薄膜区域。
通过光照来划定这些区域的过程就是光刻。
刻蚀是指在光刻后需要通过腐蚀,将光刻胶上图形完整地转移到Si片上。
经过光刻后,光刻胶所覆盖的区域已经被划分为了需要被刻蚀掉的和需要保留下来的区域,根据不同光刻胶的性质,利用相应的试剂去掉所需要刻蚀掉的薄膜或金属区域的光刻胶,然后进行腐蚀,将光刻胶上图形完整地转移到Si片上。
光
刻的步骤分别是涂胶,前烘,曝光,显影,坚模,刻蚀,去胶。
如图1.6所示,先将硅片涂上光刻胶,并在该机器上进行甩胶,使得光刻胶
均匀地附着在硅片表面上。
如图1.7所示,将涂了光刻胶的硅片放入该仪器内,进行前烘。
前烘可以促进胶膜内溶剂充分挥发,使胶膜干燥;增加胶膜与SiO2(Al膜等)的粘附性及耐磨性。
但是如果烘焙不足(温度太低或时间太短),显影时易浮胶,图形易变形。
若烘焙时间过长,则增感剂挥发,导致曝光时间增长,甚至显不出图形。
若烘焙温度过高,光刻胶黏附性降低,光刻胶中的感光剂发生反应(胶膜硬化),不易溶于显影液,导致显影不干净。
前烘之后要进行曝光。
如图1.8所示,对前烘后的硅片进行曝光。
利用电脑操作该仪器,对光刻胶进行光照,需要的部分光刻胶在光照后会固化。
曝光有很多种类:
光学曝光、X射线曝光、电子束曝光光学曝光通常采用紫外,深紫外光。
可以采用高压汞灯,产生紫外(UV)光,或是准分子激光器:
产生深紫外(DUV)光。
光学曝光的方式有三种:
a.接触式:
硅片与光刻版紧密接触。
b接近式:
硅片与光刻版保持550μm间距。
c.投影式:
利用光学系统,将光刻版的图形投影在硅片上。
电子束曝光的优点是分辨率高、不需光刻版(直写式)、缺点是产量低。
X射线曝光的特点是分辨率高,产量大。
对硅片进行曝光之后要用显影液去除掉不需要的光刻胶。
显影的作用是将未感光的负胶或感光的正胶溶解去除,从而显现出所需的图形。
正负胶的显影液是不同的,通常正胶显影液使用含水的碱性显影液,如KOH、TMAH(四甲基氢氧化胺水溶液),等。
负胶显影液使用有机溶剂,如丙酮、甲苯等。
对KPR(负胶)来说,显影液使用丁酮-最理想;甲苯-图形清晰度稍差;三氯乙烯-毒性大。
曝光时间、前烘的温度与时间、胶膜的厚度、显影液的浓度、温度、显影时间都会影响显影效果。
显影时间t太短,可能留下光刻胶薄层,阻挡腐蚀SiO2(金属),形成氧化层“小岛”。
如果t太长则会导致光刻胶软化、膨胀、钻溶、浮胶,从而导致图形边缘破坏。
显影后将硅片放入仪器内进行坚模。
坚膜可以使软化、膨胀的胶膜与硅片粘附更牢;从而增加胶膜的抗蚀能力。
具体的方法是将硅片放入恒温烘箱,在180-200℃下,烘培30min。
采用红外灯在距离6cm的地方照射10min。
若坚膜不足则腐蚀时易造成浮胶和侧蚀。
若坚膜过度则会导致胶膜热膨胀,从而导致光刻胶翘.若温度大于300℃则会导致光刻胶分解,失去抗蚀能力。
坚模后进行刻蚀。
如图1.11所示。
腐蚀(刻蚀)要求腐蚀液(气体)既能腐蚀掉裸露的SiO2(金属),又不损伤光刻胶。
腐蚀有两种方法:
湿法腐蚀的腐蚀剂是化学溶液,它是各向同性腐蚀。
干法腐蚀的腐蚀剂是活性气体,如等离子体;它的分辨率高;各向异性强。
去胶也有两种方法:
湿法去胶可以采用无机溶液去胶,如H2SO4(负胶);也可以采用有机溶液去胶,如丙酮(正胶);而干法去胶通常可以采用O2等离子体。
如图1.12所示,在刻蚀之后采用该仪器进行去胶。
去胶完成了,基本完成了光刻操作。
进行光刻操作时需注意光刻胶涂抹均匀,前烘和坚模的时间长短以及温度,曝光显影的时长等因素。
同时也需要光刻胶的选取,正胶显影时,感光部分溶解,未感光部分不溶解。
负胶显影时,感光部分不溶解,不感光部分溶解。
4.金属化
金属化是指金属及金属性材料在IC中的应用。
按功能可划分为:
①MOSFET栅电极材料-MOSFET器件的组成部分;
②互连材料-将各个独立的元件连接成为具有一定功能的电路模块。
③接触材料-直接与半导体材料接触的材料以及提供与外部相连的接触点。
常用金属材料有Al、Cu、Pt、Au、W、Mo等
制备铝膜的常用方法有真空蒸发法(电阻丝或电子束加热)和溅射法(目前的主流,质量好)。
如图1.13所示,使用该仪器在硅片上进行淀积一层金属。
金属化是在硅片表面形成一层金属互连线,之后还要进行光刻,将多余的
金属除去。
进行金属淀积后,采用探针法或其他设备来测量该金属层的厚度。
二、器件制作
1.工艺流程
N/N+型衬底――氧化生长――光刻窗口――P型扩散――光刻接触孔――金属淀积――Al反刻――合金――测试
本次生产实习工艺流程主要分为六个步骤。
①氧化
为了在n型衬底上进行p型掺杂,需要先制备一层二氧化硅薄膜。
②光刻一
在二氧化硅薄膜上进行光刻,刻蚀出需要进行p型掺杂的区域。
③扩散
在刻蚀出的区域内进行p型掺杂,这里采用B的两步扩散工艺进行掺杂,
第一步预淀积确定杂质总量,第二步再扩散确定扩散深度。
扩散的同时也形成了
新的二氧化硅薄膜。
④光刻二
对p型掺杂区上的二氧化硅薄膜进行光刻,刻蚀出需要淀积金属铝的区域。
⑤金属化
在硅片上淀积一层金属铝膜。
⑥光刻三
在金属铝膜上进行光刻,刻蚀掉不需要的金属,形成金属线。
2.工艺条件
①氧化
●温度T:
1145℃
●时间t:
干氧氧化5分钟
湿氧氧化40分钟
干氧氧化15分钟
●氧气流量:
100ml/min
测量氧化层厚度doc=400nm
②光刻一
●曝光时间:
3.5秒
●显影时间:
2分30秒
●SiO2腐蚀时间:
3分
●去胶时间:
10分钟
③扩散
第一步硼的预淀积:
●温度T:
930℃
●时间t:
20分钟
●N2流量:
100ml/min
测量方块电阻为750Ω/□
第二步再扩散:
●温度T:
1150℃
●时间t:
30分钟
干氧5分钟湿氧15分钟干氧10分钟
●O2流量:
100ml/min
测量方块电阻为243Ω/□
④光刻二
●曝光时间:
3.5秒
●显影时间:
2分30秒
●SiO2腐蚀时间:
3分30秒
●去胶时间:
10分钟
⑤金属化
●衬底温度T:
102℃
●真空度:
5E-3Pa
●溅射时间:
3分钟
测量金属铝膜厚度dAL=150nm。
⑥光刻三
●曝光时间:
3.5秒
●显影时间:
2分30秒
●Al腐蚀时间:
3分45秒
●去胶时间:
10分钟
3.测试结果
采用如图2.1(a)、(b)所示的设备进行击穿电压测量。
测试了pn结的反向击穿电压(15个测试点),结果如下:
V击穿=58、60、65、70、50、62、70、60、58、55、50、50、50、64、60V
4.结果分析
①本组测试氧化层厚度400nm。
采用干湿干的氧化方法,既拥有较高的氧化速率,同时也有较好的氧化质量。
②硼的预淀积和再分布的方块电阻分别为750Ω/□和243Ω/□。
采用两部扩散工艺使得杂质分布较均匀。
③金属层的厚度为150nm。
采用溅射法淀积了金属层。
④最终15个测试点的反向击穿电压相差不多,在正常范围内。
去掉一个相差极大的值70V,得到该pn结的反向击穿电压均值为60V,属于正常范围。
因此本次实习所制作的pn结符合要求。
三、实习收获与建议
本次生产实习,让我进一步学习和了解到了制作一个pn结的工艺设备、工艺条件、以及工艺流程。
老师们十分悉心地讲解了设备的工作原理,操作方法,并进行提问,还指导了我们亲自动手,有必要时指出问题所在。
这次实习让我切身体验到了科学工作人员的辛苦,闷热的防静电服,在实验时长达几个小时早已令人呼吸不畅。
这次实习也让我进一步深入理解了课本中的知识,从各种原理到工艺条件,工艺流程。
了解了各种设备是如何工作和操作的,看老师操作氧化炉,也亲身体验了涂抹光刻胶,拿着硅片的激动感,和同学一起合作,交流整个流程中的不懂的知识点。
并且第一次亲眼目睹了一个小的硅片从初始未掺杂的状态,经历了氧化、光刻、扩散到金属化等等操作直到最终的pn结形成。
这是一次伟大的体验和学习。
总而言之,这次实习对我来说意义重大,是我在学习专业知识,将理论与实践结合道路上的一个重要的拐点。