锅炉化学清洗原则.docx
《锅炉化学清洗原则.docx》由会员分享,可在线阅读,更多相关《锅炉化学清洗原则.docx(18页珍藏版)》请在冰豆网上搜索。
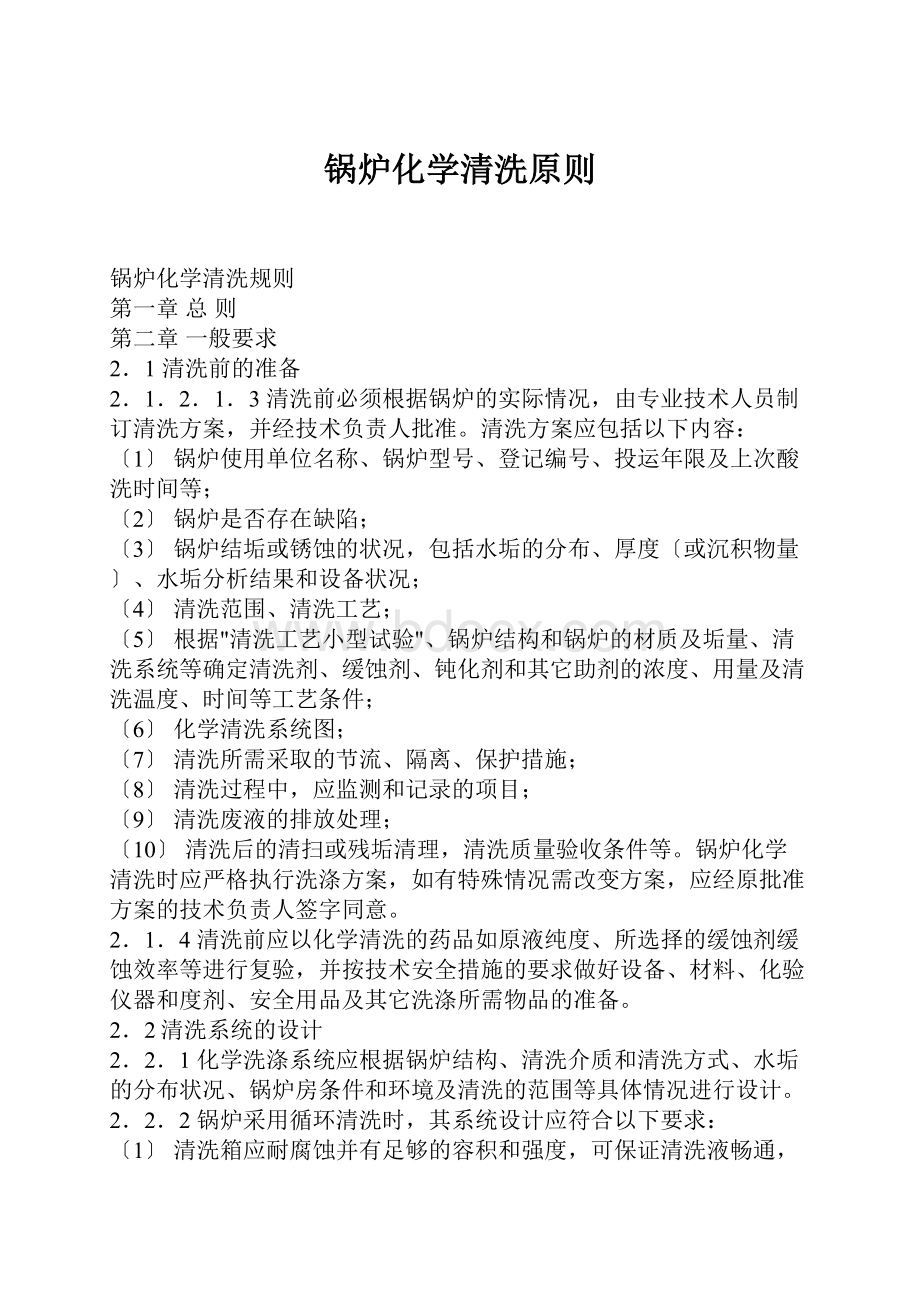
锅炉化学清洗原则
锅炉化学清洗规则
第一章总则
第二章一般要求
2.1清洗前的准备
2.1.2.1.3清洗前必须根据锅炉的实际情况,由专业技术人员制订清洗方案,并经技术负责人批准。
清洗方案应包括以下内容:
〔1〕锅炉使用单位名称、锅炉型号、登记编号、投运年限及上次酸洗时间等;
〔2〕锅炉是否存在缺陷;
〔3〕锅炉结垢或锈蚀的状况,包括水垢的分布、厚度〔或沉积物量〕、水垢分析结果和设备状况;
〔4〕清洗范围、清洗工艺;
〔5〕根据"清洗工艺小型试验"、锅炉结构和锅炉的材质及垢量、清洗系统等确定清洗剂、缓蚀剂、钝化剂和其它助剂的浓度、用量及清洗温度、时间等工艺条件;
〔6〕化学清洗系统图;
〔7〕清洗所需采取的节流、隔离、保护措施;
〔8〕清洗过程中,应监测和记录的项目;
〔9〕清洗废液的排放处理;
〔10〕清洗后的清扫或残垢清理,清洗质量验收条件等。
锅炉化学清洗时应严格执行洗涤方案,如有特殊情况需改变方案,应经原批准方案的技术负责人签字同意。
2.1.4清洗前应以化学清洗的药品如原液纯度、所选择的缓蚀剂缓蚀效率等进行复验,并按技术安全措施的要求做好设备、材料、化验仪器和度剂、安全用品及其它洗涤所需物品的准备。
2.2清洗系统的设计
2.2.1化学洗涤系统应根据锅炉结构、清洗介质和清洗方式、水垢的分布状况、锅炉房条件和环境及清洗的范围等具体情况进行设计。
2.2.2锅炉采用循环清洗时,其系统设计应符合以下要求:
〔1〕清洗箱应耐腐蚀并有足够的容积和强度,可保证清洗液畅通,并能顺利地排出沉渣;
〔2〕清洗泵应耐腐蚀,泵的出力应能保证清洗所需的清洗液流速和扬程,并保证清洗泵边疆可靠运行;
〔3〕清洗泵入口或清洗箱出口应装滤网,滤网孔径应小于5MM,且应有足够的通流截面;
〔4〕清洗液的进管和回管应有足够的截面积以保证清洗液的流量,且各回路的流速应均匀;
〔5〕锅炉顶部及封闭式清洗箱顶部应设排气管。
排气管应引至安全地点,且应有足够的流的流通面积;
〔6〕应标明监视管、采样点和挂片位置;
〔7〕清洗系统内的阀门应灵活、严密、耐腐蚀。
含有钢部件的阀门、仪表等应在酸洗前拆除、封堵或更换成涂有防腐涂料的管道附件。
过热器内应充满加有联氨N2H4100~300mg/或乙醛肟100~300mg/L,pH值为9.5~10.0〔用氨水调pH值〕的除盐水作保护。
所有不参与清洗的系统、管道等都庆严密隔离;
〔8〕必要时可装设喷射注酸装置、蒸汽加热装置和压缩空气装置;
〔9〕应防止将炉前系统的脏物带入锅炉本体和过热器。
一股应将锅炉分为炉前系统、炉本体和蒸汽系统三个系统进行清洗。
2.3清洗介质的要求
2.3.1清洗介质的先择,应根据垢的成分,锅炉设备的结构、材质,清洗效果,缓蚀效果,药剂的毒性和环保的要求等因素进行综合考虑。
一般应通过试验选用。
2.3.2一般情况下不得利用回收的酸洗废液清洗锅炉。
特殊情况下回收利用的酸液中铁离子总量不得超过250mg/L。
2.3.3清洗时必须根据清洗介质、温度、锅炉材质等因素选择合适的缓蚀剂。
缓蚀剂的缓蚀效率应到达98×10-⒉以上,并且不发生氢脆、点蚀及其它局部腐蚀,同时应尽量选择气味小、无毒害作用、性能稳定、水溶性及均匀性好的缓蚀剂。
2.3.3.1如清洗中需添加清洗助剂的,应预先对加助剂后的缓蚀剂进行缓蚀效率测定,以防有些助剂对缓蚀性能产生影响。
测定方法见附录取2《缓蚀剂缓蚀效率和酸洗剂腐蚀速率的测定方法》。
2.3.3.2清洗单位应对库存的缓蚀剂进行缓蚀效率复测,不得以锅炉清洗时腐蚀试片的测定来代替。
2.3.4酸洗剂:
对不同的水垢和金属材料,应选用合适的酸洗剂和助溶剂,一般选择如下:
〔1〕对碳酸盐水垢,一般采用盐酸清洗。
〔2〕对硅酸盐水垢,可在盐酸中添加氢氟酸或氟化物清洗。
〔3〕对硫酸盐水垢或硫酸盐与硅酸盐混合水垢,应预先碱煮转型,然后再用盐酸或盐酸添加氟化物清洗。
〔4〕对氧化铁垢,可在盐酸中添加氟化物或采用硝酸清洗。
〔5〕对于电站锅炉,当氧化伯垢中含铜量较高〔CμO>5×10ˉ⒉〕时,应采取防止金属外表产生镀铜的措施,一般可选用盐酸加氟化物及硫脲等清洗助剂。
〔6〕奥氏体钢的清洗,不可选用盐酸作清洗剂。
对于含铬材料的锅炉部件的清洗,一般可选用氢氟酸、EDTA、柠檬酸或甲酸、乙酸等有机混合酸作清洗剂。
2.3.5清洗剂用量:
锅炉清洗时,所需的盐酸〔硝酸〕、EDTA、柠檬酸、缓蚀剂的用量计算方法见附录3《清洗药品用量的计算方法》。
2.4清洗腐蚀的控制
2.4.1清洗时必须加入合适的缓蚀剂,其浓度和适用性应根据产品说明和试验结果确定。
酸洗时一般应先加缓蚀剂,并在系统中循环均匀后再加酸液。
缓蚀剂需和酸同时加入的,应配制均匀后才可进入锅炉内。
2.4.2酸洗时须防止因Fe3+浓度过高而引起的电化学腐蚀。
当酸法液中FE3+浓度≥100mg/L时,应在酸洗液中加入复原剂〔一般应加氯化亚锡〕进行复原,其添加量的计算可参考附录4《酸洗中复原剂加入量的计算方法》。
2.4.3酸洗液浓度的控制:
酸洗液的浓度不得过高,最高浓度一般控制为:
HC1、HNO3、EDTA;10×10ˉ2;HF:
3×10ˉ⒉。
不得向锅炉内直接注入浓酸。
2.4.4酸洗流速的控制:
酸洗时,锅炉炉管内酸液流速应维持在0。
2~0。
5m/s,但有得大于1m/s。
2.4.5酸液温度的控制:
〔1〕无机酸的清洗温度宜控制在55℃以下,最高不得超过65℃;
〔2〕有机酸的清洗温度控制为;柠檬酸90~98℃;EDTA110~145℃。
酸洗过程中〔除EDTA清洗外〕严禁采用炉膛点为方式加热酸液,以防爆炸和产生局部过热。
酸液的加热方法见附录5《酸液加热方法》,加热时应注意整个清洗系统的温度平衡,防止局部温度过高而产生腐蚀。
2.4.6酸洗时间的控制:
从酸液到达预定浓度起到开始排酸时的酸洗时间,一般应不超过12小时,对较厚和难容水垢,在严格监督下可适当处长酸洗时间,处长酸洗时间,处长酸洗时间的长短,可以腐蚀量测定的方法确定。
2.4.7腐蚀批示片的测定:
2.4.7.1酸洗开始时,必须在清洗系统中挂放腐蚀批示片〔一般应在清洗箱或循环管路及锅内分别挂放〕。
腐蚀批示片的材质应与锅炉被清洗部分的材质相同,其制作与腐蚀测定方法见附录6《腐蚀批示试片的制作与腐蚀测定方法》。
2.4.7.2金属腐蚀速度的计算方法如下:
式中:
▲m-----酸洗前与酸洗耳恭听后腐蚀试片的质量之差,g〔均用万分之一分析天平称重〕;
S-------腐蚀试片的总外表积,M2;
T-------酸洗时间,小时。
其计算方法为:
〔1〕循环清洗,从清洗系统进、出口酸度趋于一致超到开始排酸止的时间。
〔2〕开式清洗,从清洗系统开始加酸起到停止加酸止的时间。
2.4.7锅炉化学清洗后应尽快投入运行,假设不能很快投入运行,钝化后应采取保养措施,以防腐蚀。
第三章工业锅炉化学清洗工艺及验收要求
第四章电站锅炉化学清洗工艺及验收要求
4.1电站锅炉是指以发电和热、电联产为主要目的的锅炉,一般指额定工作压力≥3.8MPa的锅炉。
4.2电站锅炉化学清洗条件确实定:
4.2.1新建锅炉的化学清洗,应能除去新建锅炉在轧制、加工过程中形成的高温氧化物以及在存放、运输、安装过程中所产生的腐蚀产物、焊渣和泥沙污染物等。
其清洗范围为:
〔1〕直流炉和额定工作压力为9.8MPa及以上的锅筒式锅炉,在投产前必须进行酸洗;额定工作压力在9.8MPa以下的锅筒炉,除锈蚀严重者外,一般可不进行酸洗,但必须进行碱煮。
〔2〕再热器一般不进行化学清洗,但额定工作压力大于13.0MPa锅炉的再热器可根据情况进行化学清洗.清洗时必须保证管内流速大于0.15m/s,过热器进行化学清洗时,必须有防止立式管产生气塞和腐蚀产物在管内沉积的措施。
〔3〕容量为200MW及以上的机组,凝结水及高压给水系统必须进行学清洗〔不包括高压加热器〕;容量为200MW以下的机组,凝结水及高压给水管道的化学清洗,应根据管道内壁的腐蚀产物情况决定。
4.3清洗前应完成的准备工作:
4.3.1机组热力系统已安装或检修完毕,并经水压试验合格。
4.3.2临时系统安装完毕后,应通过1。
5倍清洗工作压力的热水水压试验。
清洗泵和各种计量泵及其它转动机械经试运转无异常。
4.3.3储、供水的质量和数量已能满足化学清洗和冲洗的用水需要。
清洗用水量可参照附录9《发电锅炉化学清洗用水》。
4.3.4废液处理的临时或正规设施应安装完毕,并能有效地处理排放废液。
4.3.5安装在临时系统中的温度、压力、流量表计及分析仪器应经计量校合格,并备齐全。
腐蚀指示片、监视管等制作完毕。
4.4清洗系统及其安装
4.4.1清洗方式应根据清洗介质和炉型来选择,一般盐酸、柠檬酸、EDTA等采用循环清洗,氢氟酸采用开式清洗。
4.4.2清洗系统的安装应符合以下要求:
4.4.2.1安装临时系统时,水平敷设的临时管道,朝排水方向的倾斜度不得小于1/200。
应保证临时管道的焊接质量。
焊接部位庆位于易观察之处,焊口不宜靠近重要设备。
4.4.2.2所有阀门在安装前,必须研磨,更换法兰填料,并进行水压试验。
阀门压力等级必须高于清洗时相应的压力等级。
阀门本身不得带有铜部件。
阀门及法兰填料应采用耐酸、碱的防腐材料。
EDTA清洗时,升温后应检查并紧固循环系统内所有的法兰螺栓。
4.4.2.3清洗箱的标高及液位应能满足清洗泵的吸人高度,以防泵抽空。
安装泵进、出口管道时,应考虑热膨胀补偿措施,不使水泵受到过大的推力。
4.4.2.4可在锅筒上设临时液位计及液位报警讯号。
根据循环流速的要求,在锅筒下降管口设节流装置,并将锅筒放水管加高。
4.4.2.5清洗系统中的监视管段应选择脏污程度比较严重,并带有焊口的水冷壁管,其长度为350~400mm,两端焊有法兰盘,监视管段一般安装于循环泵出口,必要时高压锅炉还应在水冷壁管处设置临视管装置。
4.4.3不参加化学清洗的设备、系统应与化学清洗系统可靠地隔离,要求:
〔1〕拆除锅筒内不宜清洗的装置;
〔2〕水位计及所有不耐腐蚀的仪表、取样、加药等管道均应与清洗液隔离;
〔3〕过热器假设不参加清洗,应采取充满除盐水等保护措施。
4.4.4为维持锅炉清洗液的温度,应严密封闭炉膛及尾部
4.4.5在锅筒水位监视点、加药点及清洗泵等处,应设通讯联络点。
4.4.6应将清洗系统图挂于清洗现场。
系统中的阀六应按图纸编号,并挂编号牌。
管道设备应标明清洗液流动方向,并经专人核对无误。
4.4.7系统安装完毕后应清理系统内的砂石、焊渣和其它杂物。
4.5电站锅炉化学清洗工艺
4.51系统水冲洗
新建锅炉,在化学清洗前必须进行水冲洗。
可用过滤后的澄清水或工业水进行分段冲洗,冲洗流速一般为0.5~1.5m/s。
冲洗终点以出水到达透明无杂物为准。
4.52碱洗或碱煮
4.52.1新建锅炉仅实施碱煮的,在煮炉过程中,需由底部排污2~3次.煮炉结束后进行大量换水,告诉百出水和正常锅水的浓度接近,且pH值降至9左右,水温降至70~80℃,即可将水全部排出。
煮炉后应对锅炉进行内部检查,要求金属外表无腐蚀产物和滔犭,且形成完整的印化保护腊。
同时应清除堆积于锅筒、集箱等处的污物。
4.5.2.2酸洗前的去没碱洗,一般应采用循环清洗或循环与浸饮相结合。
碱洗后用澄清水、软化水或除盐水冲洗,洗至出水pH值≤8.4,水质透明为止。
4.5.2.3假设水垢中硫酸盐、硅酸盐含量较高,为提高除垢效果,可在酸洗前按3.4.3的方法,先进行碱煮转型。
4.5.3酸洗及酸洗后的水垢
4.5.3.1监视管段应在清洗系统进酸至预定浓度后,投入循环系统,并控制监视管内流速与被清洗锅炉水冷壁管内流速相近。
4.5.3.2酸洗时必须按清洗方案严格监控酸洗液的温度、循环流速,锅筒和酸槽的液位等,并每小时记录一次。
按时巡回检查,如实记录出现的问题。
4.5.3.3当每一回路循环清洗到预定时间时,应加强酸液浓度和铁离子浓度铁离子浓度的测定。
当各回路酸洗液中酸液浓度和铁离子浓度趋于稳定和平衡,预计酸洗将结束时,可取下监视管检查清洗效果。
假设管段内仍有污垢,应再把监视管段装回系统继续酸洗。
至监视管段内清洗干净,应再循环1小时,方可停止酸洗。
4.5.3.4为防止活化的金属外表产生二次锈蚀,酸洗结束时,不得采用将酸直接排空再上水的方法进行冲洗,可用纯度大于97×10ˉ2的氨气连续顶出废酸液,也可用除盐水顶排出废酸液。
废液顶出后采用变流量水冲洗,冲洗时水流速应到达清洗流速的一倍以上,尽可能缩短冲洗时间。
水冲洗至排出液的pH什为4~4.5,含铁量小于50mg/L为止。
4.5.3.5对沉积物量或垢量较多的锅炉,酸洗后如有较多未深解的没渣堆积在清洗系统及设备的死角,可在水冲洗至出水pH值为4~4.5后,再排水用人工方法清除锅炉和酸箱内的沉渣。
用此法冲洗后,须经漂洗才能进行钝化。
4.5.4漂洗和钝化
4.5.4.1采氮气或水顶酸,即在锅内金属未接角空气的情况下可免漂洗,假设退酸水冲洗后有二次锈蚀产生的,则须进行漂洗。
4.5.4.2锅炉酸洗后必须进行钝化〔除EDTA清洗钝化一次完成外〕。
如漂洗后钝化的,漂洗液中的铁离子总量应小于300mg/L,假设超过该值,应用热的除氧水更换部分漂洗液至铁离子含量小于该值。
钝化过程中,应定时取样化验,如钝化液溶液浓度降至起始浓度的二分之一时,应及时适量补加钝化液。
4.6清洗后的内部检查和系统的恢复
4.6.1清洗后,应打开锅筒、集箱和直流炉的训动别离器等能打开的检查孔,彻底清除下的沉渣。
4.6.2一般应对水冷壁进行割管检查,判断清洗效果。
对于运行锅炉应在热负荷较高部位割管;对于新建锅炉应在清洗流速最低处,割取带焊口的管样。
对于新建锅炉,如能确定清洗效果良好的,也可视具体情况免作割管检查。
4.6.3清洗检查完毕后,应将锅筒内和系统中拆下的装置和部件全部复位,并撤掉所有的堵头、隔板、节流装置等,使系统恢复正常。
4.7循环清洗中注意事项
4.7.1酸洗时,应维持酸液位在正常水位线上,水冲洗时,应维持液位比酸洗时的液位略高一些,钝化时的液位应比水冲洗的液位更高。
4.7.2清洗液的循环方式与锅炉的结构和受热面结垢的程度等因素有关。
对结垢严重的回路应先进行循环清洗,其余回路静止浸泡,待该回路循环一定时间后,再依次倒换。
必要时可对结垢严重的回路重复进行循环清洗。
4.7.3为了提高清洗效果,每一回路最好能正反向各循环一次〔取决于炉管和锅筒连接的情况〕。
如通向锅筒的某些导汽管位置较高,只能进行单向循环时,酸液应由高位管进入,低位管排出。
4.8清洗后的保养
锅炉清洗后如在一个月内不能投入运行,应采取以下之一的防腐蚀方法进行保护。
4.8.1液相保护法:
氨液保护:
钝化液排尽后,用1×10-2的氨液冲洗至排出液不含钝化剂,再用〔03~05〕×10-2的氨液充满锅炉,进行保护。
氨一联氨溶液保护:
将浓度为500mg/L的NH3,300~500mg/L的N2H4,pH值为9.5~10的保护液充满锅炉,进行保护。
氨一乙醛肟〔C2H5ON〕溶液保护:
将浓度为300~500mg/L的C2H5ON,加氨水调pH值,pH值为9.5~10的保护液充满锅炉,进行保护。
4.8.2气相保护法:
在严冬季节,可采用充氮法保护或气相缓蚀剂保护。
使用的氮气统一计划应大于99.9×10-2锅炉充氮压力应维持在0.2~0.05Mpa。
4.9清洗过程的化学监测及留样分析项目
4.9.1清洗系统中应在有代表性的部位设置便于操作的监视取样点。
一般锅筒式锅炉的监视取样点布置在系统回路的入、出口处;直流锅炉应在以下各部们分别布置取样点:
①凝结水处理系统出口;②低压加热器出口;③除氧器水箱出口;④高压加热器出口;⑤水冷壁管出口;⑥启动别离器出口;⑦高温过热器出口;⑧再热器出口。
4.9.2清洗过程中应定时对清洗液进行取样化验,化验方法见附录7《清洗过程化学监测分析方法》,其监测的项目一般规定如下:
4.9.2.1煮炉和碱洗过程:
锅筒式锅炉取盐段和净段的水样,直流炉取锅炉出、入口水样,每2小时测定碱度和PO3-4一次;换水时每2小时测定碱度一次,直至水样碱度与正常锅水碱度相近为止。
4.9.2.2碱洗后的水冲洗:
每15分钟测定一次出口水的pH值,每隔30分钏收集一次冲洗出口水留样分析。
4.9.2.3循环本酸过程:
每10∽20分钟分别测定酸洗耳恭听回中出、入口酸浓度一次,直至浓度均匀,并到达指标要求为止。
4.9.2.4酸洗过程:
每30分钟分别测定酸洗箱出口、酸洗回路同、入口的酸浓度和Fe3+及Fe2+的含量。
用EDTA清洗时,每1小时〔酸洗后期每30分钟〕分别测定酸洗回路出、入口清洗液中EDTA的pH值和总铁含量。
开工酸洗系统在开始进酸时,每5分钟测定一次锅米出、入口酸液的浓度。
酸洗过程中,每10分钟测定一次锅炉出、入口酸液的酸浓度及含铁量。
为了计算出的铁渣量,在酸洗过程中还应定期取排出液混合样品,测定其悬滔物和总铁量的平均值。
4.9.2.5酸洗后的水冲洗:
每15分钟测定一次出口水的pH值、酸浓度冲洗接近终点时,每15分钟测定一次出口水的pH值、酸浓度。
冲洗接近终点是,每15分钟测定一次含铁量。
4.9.2.6漂洗过程:
每30分钟测定一次碱度、pH值和含铁量并在漂洗结束时留样分析。
4.9.2.7印化过程:
每1~2小时测定一次印化液浓度和pH值。
4.9.2.8过热器水冲洗过程:
分别从饱和蒸汽和过热蒸汽取样,主要测定测定悬滔总铁量;漂洗留样,主要测定沉积物含量。
4.9.2.9留样分析项目:
碱洗留样,主要测定碱度、硅酸化物和沉积物含量;酸少留样,主要测定悬滔总铁量;漂洗留样,主要测定喾物含量。
4.10清洗质量验收要求
4.10.1被清洗的金属外表应清洁,基本上无残留氧化物和焊渣,无明显示金属粗晶析出的过洗现象,不允许有镀铜现象。
4.10.2用腐蚀指示片测量的金属腐蚀速度的平均值应小于6g/〔m2·h〕,且腐蚀总量不大于60g/m2
4.10.3锅炉清洗外表应表成良好的钝化保护膜,金属外表不出现二次浮锈,无点蚀。
4.10.4固定设备上的阀门等不应受到损伤。
第五章清洗废液的处理
5.1锅炉清洗废液应经处理后才能排放。
废液处理和测定方法见附录11《清洗废液的处理和F-含量的测定方法》和附录10《电站锅炉化学清洗工艺综合表》。
严禁排放未经处理的酸、碱液及其它有毒刻液,也不得采用渗坑、渗井和漫流的方式排放刻液。
5.2锅炉化学清洗刻液的排放应依据当地受纳水哉功能的要求,按GB8978-1996《污水综合排放标准》的规定控制污染物排放浓度其中主要的有关指标和最高允许拜谢浓度如下:
第五章安全基本要求
6.1清洗单位须根据本单位具体情况制定切实可行的安全操作规程。
锅炉清洗前,工作人员必须学习并熟悉清洗折安全操作规程,了解所使用的各种药剂的特性及急救方法,并做好自身的防护。
6.2清洗现场应备有可靠的消防设备、安全灯、充足的照明、急救药品和劳保用品。
6.3清洗时,禁止在清洗系统上进行其它工作,酸洗时不准进行明火作业。
在加药场地及锅炉顶部严禁吸烟。
清洗过程中,应有专人值班,定时巡回检查,随时检修清洗设备的缺陷。
第七章附则
7.1本规则由国家质量技术监督避负责解释。
7.2本规则自2000年3月1日起施行。
附录1水垢类别的鉴别方法
附录2缓蚀剂缓蚀效率和酸洗剂腐蚀速率的测定方法
2.1仪器及药品
(1)腐蚀试片,制作和处理方法见附6《腐蚀指示试片的制作与腐蚀测定方法》;
(2)烧杯,500mL;
(3)水砂纸,320#;
(4)恒温水浴锅;
(5)量筒,100~200mL;
(6)游标卡尺;
(7)分析天平〔万分之一〕;
(8)温度计,0~100℃;
(9)盐酸分析〔分析纯〕;
(10)丙酮;
(11)无水乙醇;
(12)氢氧化钠〔分析纯〕;
(13)1×10-2的酚酞指示剂。
2.2缓蚀剂缓蚀效率的测定
先将度片用320#水砂纸在平面玻璃板上前后方向研磨,并仔细磨去棱边的小毛刺,然后用丙酮去掉油污〔注意擦洗试片挂也内污物〕,用纱布擦干后放入无水乙醇中泡1~2分钟,取出后擦干燥器中,1小时扣将试片称重备用。
取7×10-2的酸液〔HCI或HNO3,用NaOH标准溶液标定,其浓度误差不超过±0.1×10-2〕400mL,注入500mL烧杯中,加入一定量的缓蚀剂并搅均,在水浴锅上保持恒温55±1℃,将三个已知重量的腐蚀度片分别用耐酸碱的塑料线串过试征挂孔,等距离地悬挂于烧杯中,试片应全部浸入酸液中,并低于液面低于20~25mm。
在此恒温下保持3小时取出,立即用清水冲洗并擦干,放入无水乙醇中浸泡1~2分钟,取出用纱布擦干后放入干燥器中,1小时后称重。
另取同样浓度的酸液,除不加缓蚀剂外,其它条件相同的情况下,以另一组同样试片按上述步骤作空白试验。
2.3酸洗液的腐蚀速度测定
利用化工厂的生产废酸清洗锅炉,必须预先用该酸进行腐蚀速度测定,以免其中有些杂质不受级蚀剂抑制而腐蚀金属,造成危害。
测定方法基本同工同2.2,只是试片需在酸液浸泡下恒温保持10小时,酸少后除了计算腐蚀速度和缓蚀效率外,还应仔细观察试片外表是否有点蚀或其它腐蚀迹象。
2.4计算
附件5酸液加热方法
5.1工业锅炉可采用锅内加热法:
先将锅炉水位上到低水位处,在投酸前将锅水加热到60℃左右,然后彻底退灭炉火蔌撤去其它热源,封闭炉门及尾部烟道出口,以防热量散失。
在投加酸洗剂时,需根据加酸量先适当排放部分锅水,以便加酸后,清洗液的液位维持在锅筒中间水位。
5.2锅外加热法:
将蒸汽管或电加热器管置于清洗箱内,边循环边将清洗系统内的水加热到预定的温度,然后加入清洗剂。
附录6腐蚀指示试片的制作与腐蚀测定方法
6.1试片规格
6.1.1试片用材必须与所洗锅炉接角酸液的受压部件的材质相同,取材时应使钢材的压延面作为试片平面。
6.1.2试片尺寸:
市售统一规格大多为:
50mm×25mm×2mm,挂孔直径4mm;
发电锅炉如用水冷壁管制作试片,尺寸为:
35mm×12mm×2mm,挂孔直径4mm。
6.2试片外观要求
试片外表不能有划痕、凹坑、锈斑;棱角及挂孔不能有毛刺;试片六面加工的粗糙度均不得低于;挂孔内粗糙度不得代于。
6.3加工程序
由整块钢板上气割下坯料〔或将钢管用铣床铣成条状〕,然后用刨床刨去四周的热影响区并刨平,再经铣、钻、磨等工序将试片加工到规定尺寸和粗糙度,并打上钢印编号,再用细砂纸研磨除去棱角处、挂孔周围等的季节性刺。
试片在加工过程中,严禁敲打撞击。
6.4加工后处理
用卡尺是取试片外表尺后,用丙酮或无水乙醇洗去试征外表油污〔注意挂孔内污物〕,再置于洁交的无水乙醇中浸泡几分钟,取出后干,置于干燥器内,2小时后称后果待用。
苦试片暂时不用,可将试生干燥后,浸泡在机没