肥皂盒注塑模具设计.docx
《肥皂盒注塑模具设计.docx》由会员分享,可在线阅读,更多相关《肥皂盒注塑模具设计.docx(30页珍藏版)》请在冰豆网上搜索。
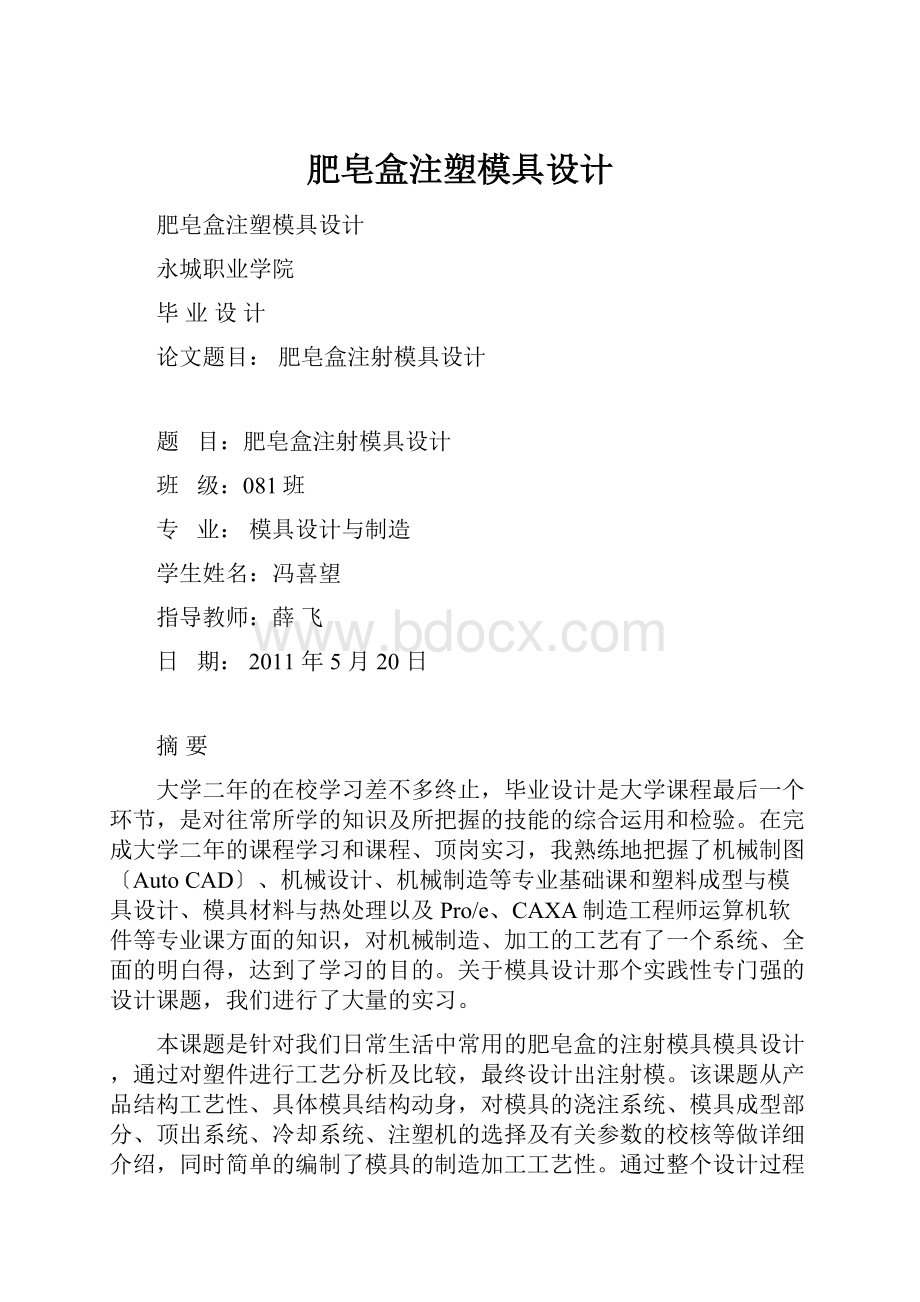
肥皂盒注塑模具设计
肥皂盒注塑模具设计
永城职业学院
毕业设计
论文题目:
肥皂盒注射模具设计
题目:
肥皂盒注射模具设计
班级:
081班
专业:
模具设计与制造
学生姓名:
冯喜望
指导教师:
薛飞
日期:
2011年5月20日
摘要
大学二年的在校学习差不多终止,毕业设计是大学课程最后一个环节,是对往常所学的知识及所把握的技能的综合运用和检验。
在完成大学二年的课程学习和课程、顶岗实习,我熟练地把握了机械制图〔AutoCAD〕、机械设计、机械制造等专业基础课和塑料成型与模具设计、模具材料与热处理以及Pro/e、CAXA制造工程师运算机软件等专业课方面的知识,对机械制造、加工的工艺有了一个系统、全面的明白得,达到了学习的目的。
关于模具设计那个实践性专门强的设计课题,我们进行了大量的实习。
本课题是针对我们日常生活中常用的肥皂盒的注射模具模具设计,通过对塑件进行工艺分析及比较,最终设计出注射模。
该课题从产品结构工艺性、具体模具结构动身,对模具的浇注系统、模具成型部分、顶出系统、冷却系统、注塑机的选择及有关参数的校核等做详细介绍,同时简单的编制了模具的制造加工工艺性。
通过整个设计过程说明该模具能够达到此塑件所要求的加工工艺。
依照题目设计的要紧任务是肥皂盒注塑模的设计。
设计出一套注射模来生产肥皂盒塑件产品,以实现自动化提高生产。
针对肥皂盒的具体结构,该模具是埋伏式浇口的〔单〕分型面注射模具。
通过模具设计说明模具能达到肥皂盒的质量和加工工艺要求。
在设计过程中,我通过在图书馆借阅相关手册和书籍,充分利用和查阅各种资料,并与同学进行充分讨论,尽最大努力搞好本次毕业设计。
在设计中难免会遇到一定的困难,但通过指导老师的尽心指导和自己的努力,相信会完满的完成毕业设计任务。
由于学生水平有限,而且缺乏体会,设计中不妥之处在所难免,肯请各位老师给予指正。
关键词:
注射模具肥皂盒设计
第一章塑件成型工艺分析
1.1肥皂盒的结构设计
依照塑件的结构分析,本设计塑件的三维尺寸为100×70×25〔㎜〕,壁厚为1㎜,外部圆角为R20㎜,底部与侧壁圆角为R5㎜。
其图形如1—1所示:
1—1
肥皂盒在我们生活中极为普遍,几乎每家都要用到。
其结构也各种各样。
本次设计以使用方便为原那么,设计出一套生产结构简单,使用方便,使用寿命长的肥皂盒注射模具。
1.2肥皂盒材料的选择及成型工艺分析
1.2.1依照塑件的结构及使用要求,我选择聚苯乙烯〔PS〕。
(1)、PS的概述
PS是一种无色、透亮、质坚、性脆,似玻璃状的非晶型塑料。
其密度为1.04~1.07g/cm3,吸水率为0.02%~0.05%,PS制品能在潮湿环境下保持其强度和尺寸稳固性。
在设计PS制品时应幸免尖角、缺口。
同时,壁厚差距不宜过大,应尽量平均、一致,以减小应力开裂现象,耐热性差。
PS的特点:
优点:
PS价格低廉,透亮性、刚性、着色性及模塑性好,吸湿性低。
缺点:
冲击强度差,耐化学试剂和耐融试剂性不行。
质硬而脆不耐沸水易燃烧。
〔2〕、PS的成型加工性能
①流淌性:
熔融状态下的表观黏度随温度和剪切应力的增高而降低,因此在成型加工时,要降低熔融黏度以提高流淌性。
同时,幸免树脂在高温下的热、氧降解。
②吸湿性:
PS的吸湿性小,约为0.02%~0.05%。
成型前可不干燥,为提高表面光泽,可先在70℃的温度下预热1~2h。
③收缩率及其变化范畴小,在0.4%~0.7%之间,有利于成型出尺寸精度较高,尺寸稳固性较好的制品。
一样型腔脱模斜度为35′~1°30′,型芯脱模斜度为30′~1°。
④宜采纳高料温〔108~215℃〕,高模温〔<70℃〕及低注射压力、延长注射时刻,有利于减小内应力,防止缩孔和变形。
第二章塑件工艺性分析
2.1分析塑件的结构工艺性
该塑件尺寸中等,整体结构较简单,精度要求相对较低,再结合其材料性能,我选择一样精度等级:
五级。
塑件工艺参数:
成型时刻:
注射时刻:
0s~3s模具温度:
20~60℃
保压时刻:
15s~40s喷嘴温度:
180~190℃
冷却时刻:
15s~30s保压压力:
30~40Mp
总周期:
40s~90s注射压力:
60~100Mpa选用70Mpa
结论:
由分析可确定为注射成型的模具。
2.2工艺性分析
为了满足制品表面光滑的要求与提高成型效率采纳埋伏式浇口。
该浇口的分流道位于模具的分型面上,而浇口却斜向开设在模具的隐藏处。
塑料熔体通过型腔的侧面或推杆的端部注入型腔,因而塑件别处不受损害,不致因浇口痕迹而阻碍塑件的表面质量与美观成效。
2.3注射机的选择
注射机的选择应考虑的因素专门多,除了模具的结构、类型和一些差不多参数和尺寸外,还有模具的型腔数、需用的注射量、塑件在分型面上的投影面积、成型时需要的合模力、注射压力、模具的厚度、安装固定尺寸以及开模行程等都与注射机的有关性能参数密节相关,假如两者不相匹配,那么模具无法使用,为此,必须对两者之间有关数据进行较核,并通过较核来设计模具与选择注射机型号。
按图1—1塑件所示尺寸近似计
塑件质量:
M≈26g
塑件体积:
M≈24.7㎝3
依照塑件的结构及尺寸,我初选的注射机为国产注射机XS-ZY-125卧式注射机。
该注射机参数为:
额定注射量:
125㎝3螺杆直径:
42㎜
注射压力:
120Mp锁模力:
900KN
注射时刻:
1.6s最大成型面积:
320㎝2
模具最大厚度:
300㎜模具最小厚度:
200㎜
注射方式:
螺杆式最大开合模行程:
300㎜
拉杆空间:
260×290㎜定位圈尺寸:
ø100㎜
中心距:
230㎜动、定模固定板:
428×458㎜
喷嘴球半径:
18㎜喷嘴口直径:
4㎜
顶出形式:
两侧设有顶杆
第三章塑件在模具中的位置与浇注系统的设计
3.1型腔数目的确定
与多型腔模具比较,单型腔模具具有塑件形状和尺寸一致性好、成型工艺条件易操纵、模具结构简单紧凑、模具制造成本低、制造周期时刻短等特点。
然而,在大批量生产的情形下,多型腔应为更适合的形式,它能够提高生产效率,降低塑件的整体成本。
依照注射机的额定锁模力来确定型腔的数目,
n≤(Fp-pA1)/pA
式中
Fp…………注射机的额定锁模力,N;900KN
P…………塑料熔体在型腔中的成型压力,MPa;70
A1…………浇注系统在分型面上的投影与型腔不重叠部分的面积,㎜2;164
A…………单个塑件在分型面上的投影,㎜2。
5706
n≤(900000-70×164)/70×5706
n≤2.21
依照以上运算,我确定选用一模两腔制。
3.2型腔的分布
关于多型腔模具由于型腔的排布与浇注系统紧密相关,因此在模具设计时应综合加以考虑。
型腔的排布应使每个型腔都能通过浇注系统从总压力中均等地分得所需的足够压力,以保证塑料熔体能同时平均地填充每个型腔,从而使各个型腔内的塑件质量均一稳固。
多型腔模具的型腔在模具分型面上的排布形式有两种,即平稳式排布和非平稳式排布。
本设计为一模两腔制。
因此,型腔的分布如以下图3—1:
3—1
3.3分型面的选择
分型面是决定模具结构形式的一个重要因素,它与模具的整体结构、浇注系统的设计塑件的脱模和模具的制造工艺等有关,因此分型面的选择是注射模具设计的一个关键步骤。
分型面位置选择的总体原那么,是能保证塑件的质量、便于塑件脱模及简化模具的结构,分型面受到塑件在模具中的成型位置、浇注系统设计、塑件的结构工艺性及精度、嵌件位置形状以及推出方法、模具的制造、排气、操作工艺等多种因素的阻碍,因此在选择分型面时应综合分析比较具体能够从以下方面进行选择。
分型面的选择原那么:
①分型面应选在塑件外形最大轮廓处。
分型面的选择应有利于塑件顺利脱模
分型面的选择应保证塑件的精度要求
分型面的选择应满足塑件的外观质量要求
分型面的选择应便于模具的加工制造
分型面的选择应便于排气
除了以上这些差不多因素外,分型面的选择还要考虑到型腔在分型面上投影面积的大小以幸免接近或超过所选用注射机的最大注射面积而可能产生溢流现象。
3—2
3.4浇注系统的设计
浇注系统可分为一般浇注系统和热流道浇注系统两大类。
浇注系统操纵着塑件成型过程中充模和补料两个重要时期,对塑件质量关系极大。
浇注系统是指从注塑机喷嘴进入模具开始,到型腔入口为止的那一段流道。
3.4.1浇注系统的组成及设计原那么
浇注系统由:
主流道、分流道、浇口、冷料穴组成。
浇注系统的设计原那么
了解塑料的成型性能
尽量幸免或减少产生熔接痕
有利于型腔气体的排出
防止型芯变形和嵌件位移
尽量采纳较短的流程充满型腔
流淌距离比和流淌面积比的校核
3.4.2主流道的设计
主流道是指浇注系统中从注射喷嘴与模具接触处道分流道为止的塑料熔体的流淌通道。
他的形状与尺寸对塑料熔体流淌速度和冲模时刻有较大阻碍,因此必须使熔体的温度降低和压力缺失最小。
主流道的设计要点:
主流道通常垂直于分型面设计在模具的浇口套中,呈圆锥形,锥角一样为2°~6°,以便于凝料从浇口套中拔出。
小端直径比注射机喷嘴直径大0.5~1㎜。
由于其小端前面是球面,其深度为3~5㎜。
主流道球面半径比喷嘴球面半径大1~2㎜。
流道面粗糙度为Ra≤0.8μm。
3—3
浇口套的制造:
浇口套一样采纳碳素工具钢〔T8A、T10A〕制造,热处理淬火硬度35~57HRC。
浇口套与模板之间的配合采纳H7/m6过渡配合,浇口套与定位圈采纳H9/f9配合。
定位圈外径比注射机模板上的定位孔直径小0.2㎜以下。
主流道凝料体积
V主=〔л/4〕d2L=(3.14/4)×[(7.1+4)/2]×2×30=259.05㎜3≈0.26㎝3
3.4.3分流道的设计
分流道是指主流道末端与浇口之间的一段塑料熔体的流淌通道。
其作用是改变熔体流向,使其以平稳的流态均衡地分配到各个型腔。
设计时应注意尽量减少流淌过程中的热量与压力的缺失。
分流道的形状与尺寸分流道开设在动定模分型面的两侧或任意一侧,其截面形状应尽量使其比表面积〔流道表面积与其体积之比〕小。
常用分流道截面形状有圆形、梯形、U形、半圆形及矩形。
分流道截面尺寸视塑料品种、塑件尺寸、成型工艺条件及流道长度等因素来确定。
分流道的长度依照型腔在分型面上的排布情形,分流道可分为一次分流道、二次分流道等。
分流道的长度要尽可能短,且少弯折,以减少热量与压力的缺失,节约塑料材料和降低耗能。
分流道的表面粗糙度由于分流道中与模具接触的外层塑料迅速冷却只有内部的熔体流淌状态比较理想,因此分流道表面粗糙度要求不能太低,一样Ra取1.6μm。
分流道在分型面上的布置形式分流道在分型面上的布置形式与型腔在分型面上的布置形式紧密相关。
其应遵循两个原那么:
一是排列尽量紧凑,以缩小模板尺寸;二是流程尽量短,对称分布使胀模力的中心与注射机锁模力的中心一致。
3—4
3.4.4浇口的设计
浇口亦称进料口,是连接分流道与型腔的熔体通道,其设计与位置的选择是否恰当,直径关系到塑件能否完好、高质量的注射成型。
本设计中,我选择矩形侧浇口浇口。
该浇口在国外被称为标准浇口,位于模具的分型面上。
塑料熔体从内侧或外侧注入型腔,其截面多为矩形。
改变浇口的宽度和厚度能够调剂熔体的剪切速率及浇口的冻结时刻。
该接口因加工和修整方便而被广泛应用,普遍应用于中小型塑件的多型腔模具中,且对各种塑料的成型适应性较强。
由于该浇口截面小,减少了浇注系统塑料的消耗量,同时去除浇口容易,且不留明显痕迹。
但这种浇口成型的塑件往往有熔接痕存在,且注射压力缺失大,对深型腔塑件排气不利。
1〕浇口位置的选择
浇口的形式专门多,但不管采纳哪种形式,其开设的位置对塑件的成型性能及成型质量阻碍都专门大。
因此,合理开设浇口位置是提高塑件成型质量的一个重要环节。
选择浇口位置时,需要依照塑件的结构与工艺特点、成型质量要求,并分析塑件原材料的工艺特性与塑料熔体在模具内的流淌状态、成型的工艺条件进行综合考虑。
浇口位置的设计原那么:
尽量缩短熔体的流淌距离
幸免熔体破裂现象引起的塑件缺陷
浇口应设在塑件的壁厚处
考虑分子定向阻碍
减少熔接痕提高熔接强度
此外,浇口位置的选择还应注意到实际塑件型腔的排气问题、塑件外观的质量问题等。
2〕浇口尺寸的运算
参考«塑料成型工艺与模具设计»5.2.4浇口的设计〔P119〕可知,关于中小型塑件侧向进料的侧浇口。
一样宽度b=1.5~5.0㎜,厚度t=0.5~2.0㎜.因此,我取b为3.0㎜,t为1.0㎜。
3.4.5冷料穴和拉料杆的设计
冷料穴的作用:
容纳浇注系统流道中料流的前锋冷料,以免这些冷料注入型腔。
这些冷料既阻碍熔体冲模速度,又阻碍成型塑件的质量。
冷料穴除以上作用外,还有便于在该处设置主流道拉杆的作用。
拉料杆的设计:
拉料杆的作用:
注射终止模具分型时,在拉料杆的作用下,主流道中的凝料从定模浇口套中被拉出。
最后推出机构开始工作,将塑件和浇注系统中的凝料一起推出模外。
主流道拉料杆有两种差不多形式,一种是推杆形式的拉料杆,其固定在推杆固定板上。
另一种是仅适用于推件板脱模的拉料杆。
因此,我选择推杆是球字形的拉料杆。
3—6
3.4.6排气系统的设计
排气槽的作用要紧有两点。
一是在注射熔融物料时,排除模腔内的空气;二是排除物料在加热过程中产生的各种气体。
越是薄壁制品,越是远离浇口的部位,排气槽的开设就显得尤为重要。
另外关于小型件或周密零件也要重视排气槽的开设,因为它除了能幸免制品表面灼伤和注射量不足外,还能够排除制品的各种缺陷,减少模具污染等。
那么,模腔的排气如何样才算充分呢?
一样来说,假设以最高的注射速率注射熔料,在制品上却未留下焦斑,就能够认为模腔内的排气是充分的。
适当地开设排气槽;能够大大降低注射压力、注射时刻。
保压时刻以及锁模压力,使塑件成型由困难变为容易,从而提高生产效率,降低生产成本,降低机器的能量消耗。
其设计往往要紧靠实践体会,通过试模与修模再加以完善,此模我们利用模具零部件的配合间隙及分型面自然排气。
第四章成型零部件的结构设计
模具中决定塑件几何形状和尺寸的零件称为成型零件,包括凹模、型芯、镶块、成型杆和成型环等。
成型零件工作时,直截了当与塑料接触,塑料熔体的高压、料流的冲刷,脱模时与塑件间还发生摩擦。
因此,成型零件要求有正确的几何形状,较高的尺寸精度和较低的表面粗糙度,此外,成型零件还要求结构合理,有较高的强度、刚度及较好的耐磨性能。
设计成型零件时,应依照塑料的特性和塑件的结构及使用要求,确定型腔的总体结构,选择分型面和浇口位置,确定脱模方式、排气部位等,然后依照成型零件的加工、热处理、装配等要求进行成型零件结构设计,运算成型零件的工作尺寸,对关键的成型零件进行强度和刚度校核。
4.1凹模的结构设计
凹模也确实是所谓的型腔,是成型塑件外表面的要紧零件,按结构不同可分为整体式和组合式。
依照此次设计的要求和加工特点来看,我选择整体式凹模,其优点为:
结构牢固,不易变形,可不能产生塑件拼接线痕迹。
缺点:
加工困难,热处理不方便。
因此其常用于形状简单的中小模具上。
4.2型芯结构的设计
成型塑件内表面的零件称为型芯或凸模,其类型有主型芯、小型芯、螺纹型芯、和螺纹型环等。
本设计塑件有小孔,因此需设计主型芯和小型芯。
4.2.1主型芯的设计
主型芯按结构形式可分为整体式和组合式两种。
整体式主型芯结构牢固,但不便加工,消耗的模具钢多,要紧用于工艺试验或小型模具上形状简单的型芯;组合式型芯往往用于形状复杂的型芯。
鉴于本设计塑件结构简单,我采纳整体式主型芯。
4.2.2小型芯的设计
小型芯是用来成型塑件上的小孔或槽。
小型芯单独制造后,再嵌入模板中。
本设计中,肥皂盒底部有十个长形漏水孔,由于塑件的精度要求较低。
因此,不再进行小型芯的设计。
而是直截了当设在主型芯上。
4.3成型零部件工作尺寸的运算
4.3.1运算成型零部件工作尺寸要考虑的因素
〔1〕塑件的平均收缩率
S=(Smin+Smax)/2
=(0.4%+0.7%)/2
=0.55%
〔2〕模具成型零件的制造误差
模具成型零件的制造精度是阻碍塑件尺寸精度的重要因素之一。
一样模具成型零件的制造精度取塑件公差值的1/3。
〔3〕成型零件的磨损
实践证明,关于一样的中小型塑件,最大磨损量可取塑件公差的1/6。
〔4〕模具安装配合误差
4.3.2成型零部件相关尺寸的运算
〔1〕型腔径向尺寸的运算
依照公式:
Lm=[LS〔1+S〕-3Δ/4]δz0
Lm1=[LS1〔1+S〕-3Δ/4]δz0
=[100×(1+0.55%)-3×0.015/4]0.3750
=100.5390.3750
Lm2=[LS2〔1+S〕-3Δ/4]δz0
=[104×(1+0.55%)-3×0.015/4]0.3750
=104.5610.3750
Lm3=[LS3〔1+S〕-3Δ/4]δz0
=[70×(1+0.55%)-3×0.015/4]0.3250
=70.3740.3250
Lm4=[LS4〔1+S〕-3Δ/4]δz0
=[74×(1+0.55%)-3×0.015/4]0.3250
=74.3960.3250
Lm5=[LS5〔1+S〕-3Δ/4]δz0
=[20×(1+0.55%)-3×0.015/4]0.3250
=20.0990.3250
〔2〕型芯径向尺寸的运算
依照公式lm=[lS〔1+S〕+3Δ/4]0-δz得
lm1=[lS1〔1+S〕+3Δ/4]0-δz
=[98×(1+0.55%)+3×0.015/4]0-0.375
=98.5500-0.375
lm2=[lS2〔1+S〕+3Δ/4]0-δz
=[68×(1+0.55%)+3×0.015/4]0-0.325
=68.3850-0.325
lm3=[lS3〔1+S〕+3Δ/4]0-δz
=[5×(1+0.55%)+3×0.015/4]0-0.325
=5.0380-0.325
〔3〕型腔深度尺寸的运算
〔Hm〕+0δz=[HS(1+S)-xΔ]0δz
=[25×(1+0.55%)-0.009×2/3]00.375
=25.13100.375
〔4〕型芯高度尺寸的运算
(hm)0_δz=[hS(1+S)+xΔ]_δ0z
=[25×(1+0.55%)+0.009×2/3]_0.3250
=25.143_0.3250
〔5〕中心距尺寸的运算
Cm=(1+S)Cs
=〔1+0.55%〕×68
=68.374
第五章结构零部件的设计
5.1模架的选择
模架设计、制造塑料注射模的基础部件。
我国已于1998年完成«塑料注射模中小型模架»、«塑料注射模大型模架»等国家标准,因此,为了简化设计步骤,缩短设计周期,便于模具的修理和结构零部件的更换,我选用标准模架。
标准模架的选择要点在模具设计时,应依照塑件图样及技术要求,分析、运算、确定塑件形状类型、尺寸范畴、壁厚、孔形及孔位,尺寸精度及表面性能要求以及材料性能等,以制定塑件成型工艺,确定进料口位置、塑件重量以及型腔数,并选定注射机的型号和规格等等。
选用标准模架的要点如下:
模架厚度H和注射机的闭合距离L关于不同型号及规格的注射机,不同结构形式的锁模机构具有不同的闭合距离。
模具厚度与闭合距离的关系为:
Lmax≤H≤Lmin
式中H…………模架厚度;
Lmax…………注射机最大闭合距离;
Lmin…………注射机最小闭合距离.
因此,由所选注射机得模架厚度的范畴为200~300㎜。
开模行程与定、动模分开的间距与推出塑件所需行程之间的尺寸关系设计时须运算确定,在取出塑件时的注射机开模行程应大于取出塑件所需的动、定模分开的距离,而模具推出塑件距离须小于顶出液压缸的额定顶出行程。
选用的模架在注射机上的安装安装时需注意:
模架外形尺寸不应受注射机拉杆间距的阻碍;定位孔径与定位环尺寸需配合良好;注射机推出杆孔的位置和顶出行程是否合适;喷嘴孔径和球面半径是否与模具的浇口套孔径和凹球面尺寸相配合;模架安装孔的位置和孔径与注射机的移动模板上的相应螺孔相配。
选用模架应符合塑件及其成型工艺的技术要求为保证塑件质量和模架的使用性能及可靠性,需对模架组合零件的力学性能,专门是它们的强度和刚度进行准确地运算和校核,以确定动、定模及支撑板的长、宽、高尺寸,从而正确地选定模架的规格。
5.2支撑零部件的设计
用于防止成型零部件及各部分机构在成型压力作用下发生变形超差现象的零部件称为支撑零部件。
支撑零部件要紧有支撑板、垫板、支撑块、支撑板支撑柱等。
5.2.1支撑板的设计
支撑板又称动模垫板是垫在动模型腔下面的一块平板,其作用是承担成型时塑料熔体对动模型腔或型芯的作用力,以防止型腔底部产生过大的变形和防止型芯脱出型芯固定板。
支撑板的设计要点:
支撑板应具有较高的平行度和必要的硬度和强度,应结合动模成型部分受力状况进行厚度运算。
因我选用标准模架,因此支撑零部件也选用标准件,不需再设计。
5.3合模导向机构的设计
合模导向机构是保证动、定模合模时,正确定位和导向的零件。
合模导向机构要紧有导柱导向和锥面定位两种形式。
本设计采纳导柱导向。
导向机构有以下作用:
定位作用模具闭合后,保证动、定模位置正确,保证型腔的形状和尺寸精度。
导向作用合模时,第一是导向零件接触,引导动、定模准确闭合,幸免型芯先进入型腔造成成型零件的损坏。
承担一定的侧向压力塑料熔体在充形过程中可能产生单向侧向压力,现在导柱将承担一定的侧向压力,以保证模具的正常工作。
5.3.1导向机构设计要点
小型模具一样只设置两根导柱,当其元合模方位要求,采纳等径且对称布置的方法,假设有合模方位要求时,那么应采取等径不对称布置,或不等径对称布置的形式。
大中型模具常设置三个或四个导柱,采取等径不对称布置,或不等径对称布置的形式。
直导套常应用于简单模具或模板较薄的模具;Ⅰ型带头导套要紧应用于复杂模具或大、中型模具的动定模导向中;Ⅱ型带头导套要紧应用于推出机构的导向中。
导向零件应合理分布在模具的周围或靠近边缘部位;导柱中心到模板边缘的距离δ一样取导柱固定端的直径的1~1.5倍;其设置位置可参见标准模架系列。
导柱常固定在方便脱模取件的模具部分;但针对某些专门的要求,如塑件在动模侧依靠推件板脱模,为了对推件板起到导向与支承作用,而在动模侧设置导柱。
为了确保合模的分型面良好贴合,导柱与导套在分型面处应设置承屑槽;一样差不多上削去一个面,或在导套的孔口倒角,
导柱工作部分的长度应比型芯端面的高度高出6~8mm,以确保其导向作用。
应确保各导柱、导套及导向孔的轴线平行,以及同轴度要求,否那么将阻碍合模的准确性,甚至损坏导向零件。
导柱工作部分的配合精度采纳H7/f7〔低精度时可采纳H8/f8或H9/f9〕;导柱固定部分的配合精度采纳H7/k6〔或H7/m6〕。
导套与安装之间一样用H7/m6的过渡配合,再用侧向螺钉防止其被拔出。
关于生产批量小、精度要求不高的模具,导柱可直截了当与模板上加工的导向孔配合。
通常导向孔应做志通孔;假如型腔板特厚,导向孔做成盲孔时,那么应在盲孔侧壁增设通气孔,或在导柱柱身、导向孔开口端磨出排气槽;导向孔导滑面的长度与表面粗糙