塑胶原料手册.docx
《塑胶原料手册.docx》由会员分享,可在线阅读,更多相关《塑胶原料手册.docx(12页珍藏版)》请在冰豆网上搜索。
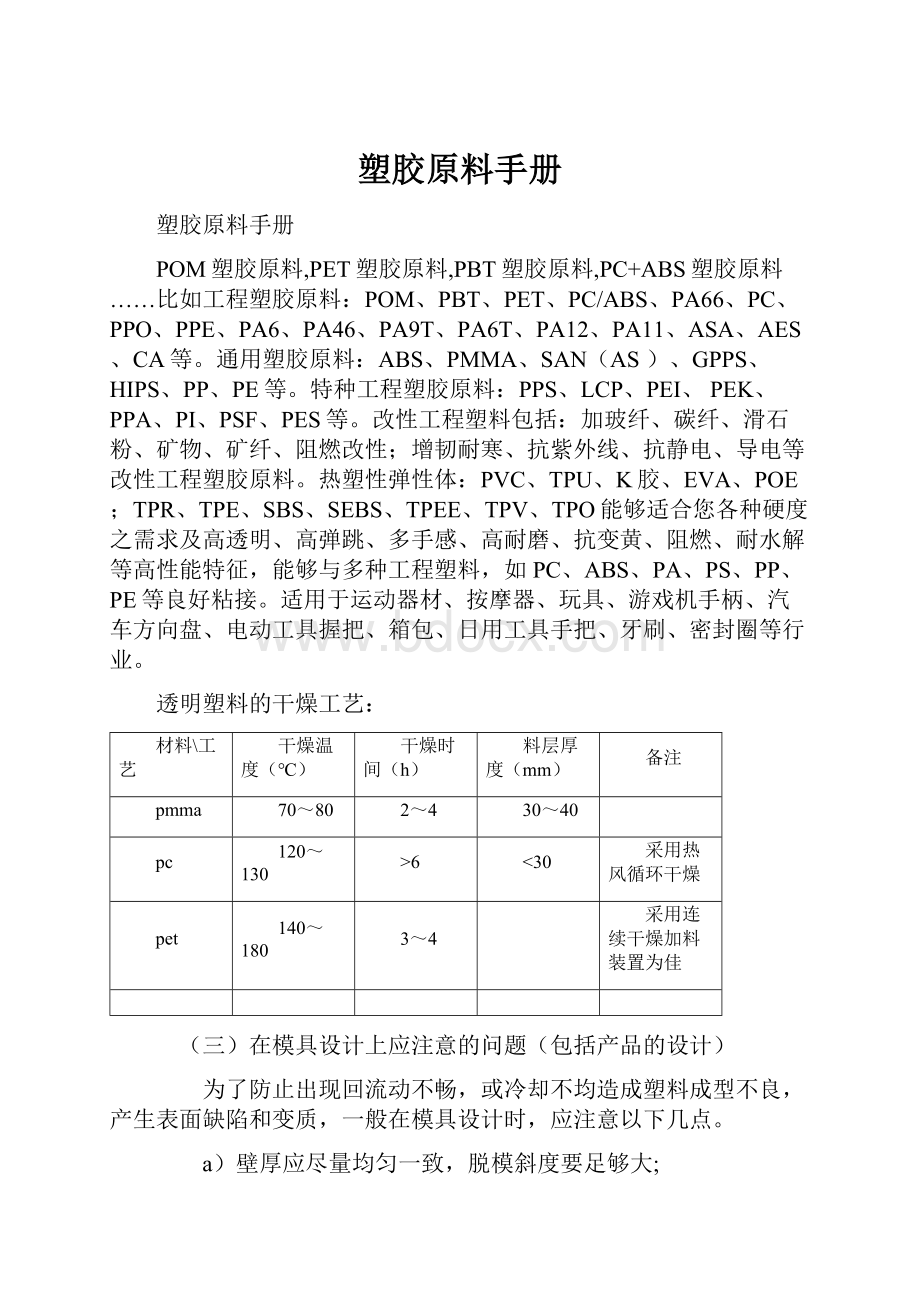
塑胶原料手册
塑胶原料手册
POM塑胶原料,PET塑胶原料,PBT塑胶原料,PC+ABS塑胶原料……比如工程塑胶原料:
POM、PBT、PET、PC/ABS、PA66、PC、PPO、PPE、PA6、PA46、PA9T、PA6T、PA12、PA11、ASA、AES、CA等。
通用塑胶原料:
ABS、PMMA、SAN(AS)、GPPS、HIPS、PP、PE等。
特种工程塑胶原料:
PPS、LCP、PEI、PEK、PPA、PI、PSF、PES等。
改性工程塑料包括:
加玻纤、碳纤、滑石粉、矿物、矿纤、阻燃改性;增韧耐寒、抗紫外线、抗静电、导电等改性工程塑胶原料。
热塑性弹性体:
PVC、TPU、K胶、EVA、POE;TPR、TPE、SBS、SEBS、TPEE、TPV、TPO能够适合您各种硬度之需求及高透明、高弹跳、多手感、高耐磨、抗变黄、阻燃、耐水解等高性能特征,能够与多种工程塑料,如PC、ABS、PA、PS、PP、PE等良好粘接。
适用于运动器材、按摩器、玩具、游戏机手柄、汽车方向盘、电动工具握把、箱包、日用工具手把、牙刷、密封圈等行业。
透明塑料的干燥工艺:
材料\工艺
干燥温度(℃)
干燥时间(h)
料层厚度(mm)
备注
pmma
70~80
2~4
30~40
pc
120~130
>6
<30
采用热风循环干燥
pet
140~180
3~4
采用连续干燥加料装置为佳
(三)在模具设计上应注意的问题(包括产品的设计)
为了防止出现回流动不畅,或冷却不均造成塑料成型不良,产生表面缺陷和变质,一般在模具设计时,应注意以下几点。
a)壁厚应尽量均匀一致,脱模斜度要足够大;
b)过渡部分应逐步。
圆滑过渡,防止有尖角。
锐边产生,特别是pc产品一定不要有缺口;
c)浇口。
流道尽可能宽大、粗短,且应根据收缩冷凝过程设置浇口位置,必要时应加冷料井;
d)模具表面应光洁,粗糙度低(最好低于0.8);
e)排气孔。
槽必须足够,以及时排出空气和熔体中的气体;
f)除pet外,壁厚不要太薄,一般不得小于lmm。
(四)注塑工艺方面应注意的问题(包括注塑机的要求)
为了减少内应力和表面质量缺陷,在注塑工艺方面应注意以下几方面的问题。
a)应选用专用螺杆、带单独温控射咀的注塑机;
b)注射温度在塑料树脂不分解的前提下,宜用较高注射湿度;
c)注射压力:
一般较高,以克服熔料粘度大的缺陷,但压力太高会产生内应力造成脱模因难和变形;
d)注射速度:
在满足充模的情况下,一般宜低,最好能采用慢一快一慢多级注射;
e)保压时间和成型周期:
在满足产品充模,不产生凹陷、气泡的情况下;宜尽量短,以尽量减低熔料在机筒停留时间;
f)螺杆转速和背压:
在满足塑化质量的前提下,应尽量低,防止产生解降的可能;
g)模具温度:
制品的冷却好坏,对质量影响极大,所以模温一定要能精确控制其过程,有可能的话,模温宜高一些好。
1)异色点:
与本身颜色不同的杂点或混入树脂中的杂点暴露在表面上。
2)气丝:
由于种种原因,气体在产品表面留下的痕迹与底面颜色不同并发亮,带有流动样。
3)塌坑:
由于材料收缩,使产品局部整体表面下陷。
4)熔接缝:
产品在成型过程中,二股以上的融熔料相汇合的接线,目视及手感都有感觉。
5)缺料:
产品某个部位不饱满。
6)白印:
由于内应力,在产品表面产生与本色不同的白色痕迹。
7)滋边:
(毛刺)由于种种原因,产品非结构部分产生多余的料
8)封堵:
应该通透的地方由于滋边造成不通。
9)断裂:
塑料理局部断开后的缺陷。
10)拉毛:
因摩擦而产生的细皮,附在塑料表面的现象。
11)油丝:
油痕,加种种原因,油污(包括脱模式剂)在产品表面留下的痕迹,使该部位发光并带有流动样。
12)漆点:
涂层厚度比周围涂层厚的部分。
13)垂流:
涂层后由于局部喷异色点:
与本身颜色不同的杂点或混入树脂中的杂点暴露在表面上。
14)气丝:
由于种种原因,气体在产品表面留下的痕迹与底面颜色不同并发亮,带有流动样。
15)塌坑:
由于材料收缩,使产品局部整体表面下陷。
16)熔接缝:
产品在成型过程中,二股以上的融熔料相汇合的接线,目视及手感都有感觉。
17)缺料:
产品某个部位不饱满。
18)白印:
由于内应力,在产品表面产生与本色不同的白色痕迹。
19)滋边:
(毛刺)由于种种原因,产品非结构部分产生多余的料
20)封堵:
应该通透的地方由于滋边造成不通。
21)断裂:
塑料理局部断开后的缺陷。
22)拉毛:
因摩擦而产生的细皮,附在塑料表面的现象。
23)油丝:
油痕,加种种原因,油污(包括脱模式剂)在产品表面留下的痕迹,使该部位发光并带有流动样。
24)漆点:
涂层厚度比周围涂层厚的部分。
25)垂流:
涂层后由于局部喷漆量过大,产生下垂形成条状物。
26)皱皮:
由于涂膜的流平性不良,涂层处产生的皱褶。
27)分界线不清:
一种或两种不同颜色的涂料边界线互相交错。
28)针孔:
由于喷涂产生的气泡破裂,产生的小孔。
29)露底:
该喷没喷的部位称露底。
30)虚喷:
涂膜厚度过薄,可看见基材底色的部位。
漆量过大,产生下垂形成条状物。
31)皱皮:
由于涂膜的流平性不良,涂层处产生的皱褶。
32)分界线不清:
一种或两种不同颜色的涂料边界线互相交错。
33)针孔:
由于喷涂产生的气泡破裂,产生的小孔。
34)露底:
该喷没喷的部位称露底。
虚喷:
涂膜厚度过薄,可看见基材底色的
塑料名称
干燥温度
干燥时间
初期水分
适合水分
热风
除湿
ABS
80℃~
2hr~
0.2~0.4%
0.07%
○
※
PS
70~80℃
1~2hr
0.1~0.2%
0.07%
※
PE
60~80℃
1~2hr
0.1~0.2%
0.07%
※
PP
60~80℃
1~2hr
0.1~0.2%
0.07%
※
PVC
60~70℃
1~2hr
0.1~0.2%
0.07%
※
PMMA
80~90℃
3hr~
0.2~0.4%
0.07%
○
※
PA
80℃~
4~6hr
0.5~2.0%
0.1%
×
※
PC
120~℃
2~4hr
0.1~0.2%
0.02%
○
※
POM
80~℃
2hr~
0.2~0.4%
0.02%
○
※
MPPO
80~100℃
2~4hr
0.1%~
0.02%
○
※
PBT
130℃~
3~42hr
0.2~0.4%
0.02%
○
※
R-PET
130~℃
4~5hr
0.2~0.4%
0.02%
□
※
PPS
130~180℃
1~3hr
0.1~0.2%
0.05%
※
PES
180℃
3hr~
0.4%~
0.05%
×
※
PEEK
150℃
3hr~
0.5%~
0.06%
×
※
注:
※最佳;○可接受;□尽量避免;×不好
料别
适当模温
料筒温度
成型收缩率
射出压力
PA
40~60℃
160~260℃
0.2~0.6%
500~1000kg/cm2
ABS
50~70℃
190~260℃
0.4~0.8%
500~1500kg/cm2
AS
50~70℃
170~290℃
0.2~0.6%
700~1500kg/cm2
PMMA
59~80℃
180~260℃
0.2~0.8%
700~1500kg/cm2
LDPE
35~65℃
140~300℃
1.5~5%
300~1000kg/cm2
HDPE
40~70℃
150~300℃
1.5~5%
300~1500kg/cm2
PP
20~80℃
180~300℃
0.8~2.5%
400~1500kg/cm2
软PVC
50~70℃
150~190℃
1~5%
600~1500kg/cm2
硬PVC
50~70℃
150~190℃
0.1~0.4%
900~1500kg/cm2
EVA
20~55℃
120~200℃
0.7~2%
600~1500kg/cm2
PC
80~120℃
260~320℃
0.6~0.8%
1000~1500kg/cm2
POM
80~120℃
190~240℃
0.6~2%
500~1500kg/cm2
改生PPO
60~100℃
260~280℃
0.7~0.8%
1200~1300kg/cm2
PA
20~90℃
220~285℃
0.6~2%
500~1400kg/cm2
CA
20~80℃
170~265℃
0.2~0.7%
700~900kg/cm2
PSF
90~165℃
330~420℃
0.7%
700~2000kg/cm2
PET
50~150℃
290~315℃
1~2%
700~1400kg/cm2
PBT
60~70℃
230~270℃
0.5~2%
300~1200kg/cm2
■由机床引起的原因及对策
原 因
对 策
1.射出能力不足
机台射出部能力确认
2.射出压力太低
提高压力
3.原料温度低,流动性差
确认加热缸温度及提高射出压力
4.原料供给量不足
增加料量
5.射出速度慢
提高射速
6.射出喷嘴部阻力大
确认孔径及电热能力
7.螺杆进料不良
手动进料
8.原料落下因难
确认清除原料团,降低入料口温度
9.螺杆射出逆流
更新checkring(逆止环)
■由模具引起的原因及对策
原 因
对 策
1.汤口设计不平均
重新计算与修正
2.汤口\流道\浇口设计过小
重新计算及加大尺寸
3.冷料储井阻塞
清除阻塞部位
4.排气不良
追加逃气设计
5.模温低
减少冷却水温、水量
6.成品肉厚太薄
检查排气性或增加肉厚设计
7.热料道阻塞未通
检查电路及温度并检修
8.模具冷却不当
确认水路系统并修改之
■由机床引起的原因及对策
原 因
对 策
1.射速太慢
提高射出速度
2.射压偏低
提高射出压力
3.保压时间不足
增加保压时间
4.原料供应量不足
增加原料供应量
5.原料温度偏高
降低原料加热温度
6.射出喷嘴太长或孔径太小
更换短喷嘴或增大喷嘴孔径
7.射出喷嘴与模具汤口未吻合
重新校正中心度及圆弧度
8.射出喷嘴部温度低
提高喷嘴温度
9.开模太早、冷却不足
增加冷却时间
10.热流道温度低
提高热流道之温度
11.射出时原料产生逆流
螺杆逆止环更换
■由模具引起的原因及对策
原 因
对 策
1.模具温度太高
增加冷却水路或降低水路
2.模具温度不一局部过高
确认水路循环系统或增减
3.汤口或流道细小
重新计算及修改汤口或流道
4.模穴有特别厚肉的部位
增加厚肉部位之流道
5.肉厚设计不均一或不适当
依肉厚比例修正
■由原料引起的原因及对策
原 因
对 策
1.原料流动性太好
修正成型条件配合或变更村质或规格级数
2.原料收缩率太高
4、流道痕(flowmark)
熔融的原料射入模穴后,以进料点为中心,呈现年轮状纹路的现象。
■由机床引起的原因及对策
原 因
对 策
1.原料温度低,流动性不够
提高原料加热温度
2.射出速度慢
提高射出速度
3.射出喷口太长、孔径太小
适当修正孔径、更换合适品
4.保压压力低
提高保压压力
5.保压时间不足
增加保压时间
6.原料供应略不足
略增加计量值
7.刚成型时冷料流入
可以松退来防止冷却出现
8.射出喷口部温度低
检修喷口部电热圈及能力
■由模具引起的原因及对策
原 因
对 策
1.模温偏低
确认后再适提高
2.模具冷却不当
确认整个水路系统再修正
3.冷料储陷设计太小
增大冷料储陷部位
4.脱气不良
增加逃气槽设计或追加pin
5.热浇道温度偏低
适当提高温度
■由原料引起的原因及对策
原 因
对 策
原料本身之流动性差
修正成型条件来配合变更规格级数或材质
5、银线(silverstreak):
成品表面出现随着原料流动方向的银白色线条之状况。
■由机床引起的原因及对策
原 因
对 策
1.射出能力不足
确认射出容量/可塑化能力
2.原料加热温度太高产生热分解
降低原料加热温度
3.射出速度太快产生热分解
降低射出速度
4.射压太高产生热分解
降低射出压力
5.背压不足卷入空气
提高背压
6.原料加热时间太长产生热分解
降低原料加热温度或时间
7.原料加热温度低熔不均
提高原料加热温度
8.螺杆转速太快产生热分解
降低螺杆回转r.p.m值
9.螺杆不洁残留他料所致
徹清除螺杆内异物异质
■由模具引起的原因及对策
原 因
对 策
1.模具温度低
可先行预热模具
2.排气不良不顺
追加顶出梢或逃气槽
3.汤口位置不适当
重新确认与修正
4.汤口、流道、浇口设计太小
重新确认与变大尺寸
5.冷料储陷设计太小
重新确认与变大尺寸
6.肉厚设计不良
重新确认与修正
7.模面残留水份或过多之润滑剂
徹底去除水份\适当润滑剂
■由原料引起的原因及对策
原 因
对 策
1.原料含水份及挥发物质多
以干燥设备预热干燥
2.材料受空气湿度影响混合一起
先预热干燥提高机台背压
6、表面雾状痕(cloudymappearance)、光泽不良(lusterless):
成品光泽面的部分,出现类似云雾状的白色现象。
■由机床引起的原因及对策
原 因
对 策
1.原料熔融程度不均匀、部分过热
增加原料加热时间使之均匀
2.射出喷嘴太冷
检修喷嘴部电热片及提高温度
3.射出喷嘴孔径太小
适当修改孔径或更换合适品
4.射出速度太快或太慢
适当调整射出速度
5.原料过热分解
降低原料加热温度或时间
■由模具引起的原因及对策
原 因
对 策
1.模温过高或过低或不均
检查水路、水温及水量并修正之
2.汤口、流道、浇口过小
重新确认与修改
3.冷料储陷设计过小
重新确认与修改
4.模面附着水份或油质
清洁及擦拭模面及顶出梢
5.排气不良
追加顶出梢或逃气槽
6.离型剂使用过多
减少离型剂之量
■由原料引起的原因及对策
原 因
对 策
1.原料本身含水份或挥发物
预备干燥
2.润滑剂中含挥发物所影响
适当地减少润滑剂使用量
3.不同材料混合造成
更新材料
7、融接线(weldline):
塑料射入模具中,流经流道,面后再会合而成的细线。
■由机床引起的原因及对策
原 因
对 策
1.原料温度偏低\流动性不足
提高原料加热温度
2.射出喷嘴温度太低
检修喷嘴部电热片及提高温度
3.射出压力低
提高射出压力
4.射出速度慢
提高射出速度
■由模具引起的原因及对策
原 因
对 策
1.原料流动距离太长
提高模具温度或增加流道数
2.模具温度太低
提高模具温度
3.汤口位置及数量不当
重新计算与修正
4.汤口、流道、浇口太小
重新计算与修正
5.冷却时间太长
缩短冷却时间
6.排气不良
追加顶出梢或逃气槽
7.离型剂使用太多
以少量多次来改善
■由原料引起的原因及对策
原 因
对 策
1.原料本身含水份或挥发物
预备干燥时间加长
2.原料流动性不良
提高原料温度
3.原料硬化速度快
提高模具温度
4.润滑剂不良或用量过多
适当修正