第二章注射模设计.docx
《第二章注射模设计.docx》由会员分享,可在线阅读,更多相关《第二章注射模设计.docx(36页珍藏版)》请在冰豆网上搜索。
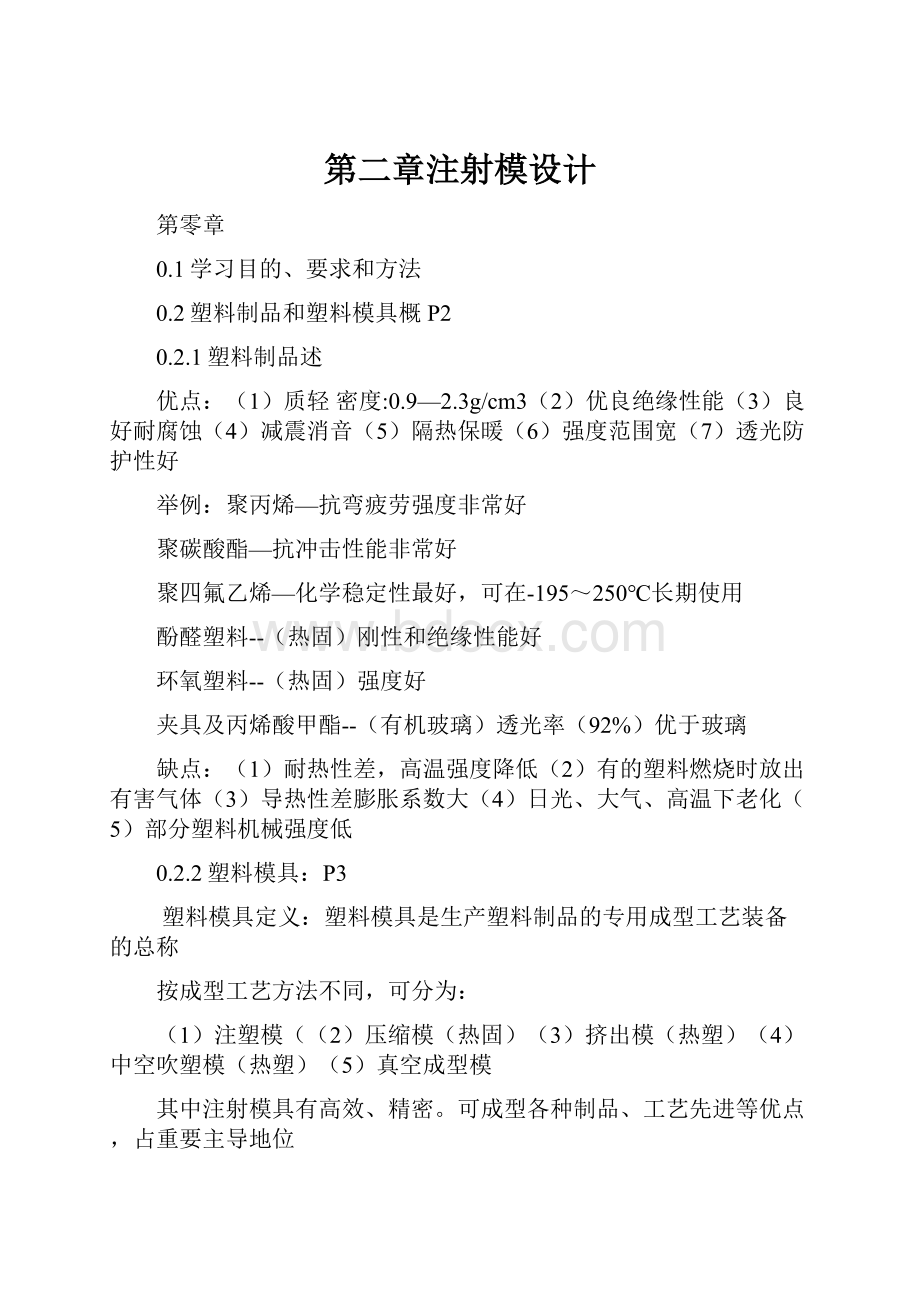
第二章注射模设计
第零章
0.1学习目的、要求和方法
0.2塑料制品和塑料模具概P2
0.2.1塑料制品述
优点:
(1)质轻密度:
0.9—2.3g/cm3
(2)优良绝缘性能(3)良好耐腐蚀(4)减震消音(5)隔热保暖(6)强度范围宽(7)透光防护性好
举例:
聚丙烯—抗弯疲劳强度非常好
聚碳酸酯—抗冲击性能非常好
聚四氟乙烯—化学稳定性最好,可在-195~250℃长期使用
酚醛塑料--(热固)刚性和绝缘性能好
环氧塑料--(热固)强度好
夹具及丙烯酸甲酯--(有机玻璃)透光率(92%)优于玻璃
缺点:
(1)耐热性差,高温强度降低
(2)有的塑料燃烧时放出有害气体(3)导热性差膨胀系数大(4)日光、大气、高温下老化(5)部分塑料机械强度低
0.2.2塑料模具:
P3
塑料模具定义:
塑料模具是生产塑料制品的专用成型工艺装备的总称
按成型工艺方法不同,可分为:
(1)注塑模(
(2)压缩模(热固)(3)挤出模(热塑)(4)中空吹塑模(热塑)(5)真空成型模
其中注射模具有高效、精密。
可成型各种制品、工艺先进等优点,占重要主导地位
0.3塑料基础知识P3
0.3.1树脂
天然树脂和人造树脂的总称
0.3.2高分子聚合物
①原子数多,几十万个②分子质量高③分子长度长
0.3.3聚合物分子结构P4
(1)线性
(2)支链线性(3)网状体
0.3.4不同温度的三种状态
(1)低温:
玻璃态
(2)中温:
高弹态(3)高温:
粘流态
0.3.5聚合物交联P4
聚合物在成型时,当温度达到成型固化温度时,其分子结构由线型或支链型二维结构转化为网状体行三维结构。
0.3.6塑料的组成P4
1.塑料的定义:
以高分子合成树脂为主要原料,加上旨在改善和提高性能的各种添加剂的合成材料。
在一定温度压力下可塑化成型。
2.塑料的组成
合成树脂+增塑剂、润滑剂、稳定剂、着色剂和固化剂
0.3.7塑料分类P5
1.按分子结构分
(1)热塑性塑料—可多次加压加温,反复成型
(2)热固性塑料—当温度达到固化剂产生化学反应,分子结构从线型或支链型转化为交联体型三维结构,在加热也不逆转。
2.按用途分
(1)通用塑料—聚乙烯、聚丙烯、聚苯乙烯、酚醛
(2)工程塑料—ABS、尼龙(聚酰胺PA)聚甲醛(POM)
(3)特种塑料—耐高低温、高冲击、高强度、导电、超导….
0.3.8塑料的性能和用途P5
1.使用性能
1)热塑
(1)聚乙烯PE高密—耐腐蚀、绝缘件
低密—薄膜
超高分子—减磨、耐磨件
(2)聚丙烯PP具有特别高的抗疲劳弯度,7×107机械零件、耐腐和绝缘件
(3)聚氯乙烯PVC硬PVC—管材、棒、焊条、板
软PVC—薄板、密封件、电线电缆外皮
(4)聚苯乙烯PS—透光率仅次于玻璃—绝缘透明件、装饰件
(5)苯乙烯-丙烯晴共聚物AS—耐热、耐油、耐腐蚀件
(6)ABS共聚物—机械零件,工程塑料
(7)聚酰胺PA(尼龙)--自润滑性好。
工程塑料
(8)聚甲醛POM—综合性能好。
工程塑料
(9)聚碳酸酯PC—具有非常好的韧性和刚性相结合的抗冲击性能
(10)聚砜PSF—具有突出的耐热耐氧化性能
(11)聚苯醚PPO
(12)氟塑料—聚四氟乙烯:
①化学稳定性最好,可在-195~250°C长期使用
②自润滑性能最好
(13)聚甲基丙烯酸甲酯PMMA(有机玻璃)--密度1.18g/㎝3,透光率92%优于硅玻璃
2)热固P7
(1)酚醛塑料—刚性好、变形小、绝缘性能好
(2)氨基塑料
(3)有机硅塑料
(4)硅酮塑料
(5)环氧塑料—强度高
2.成型工艺特性P8
1)热塑
(1)流动性—塑料熔体在一定温度和压力下流的的距离或注满型腔的能力
影响因素:
①温度—适中最好
②压力—越大越好
③模具结构—结构、尺寸、粗糙度、排气
流动性好的:
聚乙烯、聚丙烯、聚苯乙烯
中等:
ABS、有机玻璃、聚甲醛
差:
聚碳酸酯、硬聚氯乙烯、聚砜
(2)收缩性—塑料制品脱模冷去后尺寸变小,这种性质称为收缩性。
(3)相容性—两种或两种以上不同品种的塑料熔融后能结合在一起不产生分离、起层现象的性能。
(4)吸湿性—塑料对水的吸附性能。
强的:
ABS、碳酸酯(成型前预热烘干)
弱的:
聚乙烯、聚丙烯
(5)热敏性—某些热敏性差的塑料,遇高温或高温中时间较长时发生降解、变色、
聚甲醛,硬聚氯乙烯
(6)结晶性—某些熔融塑料在程序冷却过程中原子重新生成晶格的特性。
结晶:
聚乙烯、聚丙烯、聚甲醛、聚酰胺、聚四氟
非结晶:
聚苯乙烯、ABS、聚碳酸酯
2)热固P9
(1)流动性
(2)收缩性
(3)比容和压缩率—塑料体积与成型后制品体积之比、
(4)固化速度—熔融态热固性塑料进入型腔后分子从线型或支链型转化为网状体型交联固化所需要的时间。
(5)水分和挥发物含量—含量大流动性大:
易产生益边和内应力
含量小流动性小:
不易充型
塑料的优点:
密度低(0.9~2.3)g/c㎡、良好的绝缘性能、耐腐蚀、隔热保温、
化学稳定性强。
例如:
聚丙烯具有很高的抗弯疲劳强度、聚碳酸酯抗冲击性能好,酚醛塑料刚性好,有机玻璃的透光率达92%、聚四氟乙烯化学稳定性最好。
0.3.9常用塑料的成型工艺条件P9
0.4塑料注射成型工艺
0.4.1注射成型原理与成型过程
合模注射成型—保压预塑—冷去定型—开模取件
保压—当熔融态塑料充满型腔后,注射机喷嘴继续保持压力一段时间,以利于型腔内塑件的成型
0.4.2注射成型模具结构简介P22
单分型面,双型腔,侧浇口,推杆卸料,复位杆复位,弹簧测抽芯
模具由定模和动模两大部分组成
按功能结构分:
(1)成型部分—型腔、型芯
(2)侧面分型与抽芯部分
(3)浇注部分
(4)导向与定位部分
(5)推出与复位部分、推杆、复位杆
(6)固定模板与支承紧固部分
(7)冷却与加热部分
(8)排溢部分
图0.4
推杆—用以将冷却固化定型后的塑料制品在开模后平稳推出型腔
0.4.3塑料注射成型机结构简介P24
0.4.4模具与注塑机的配合要求P29
模具外形与拉杆—图0.13P31
模具的闭合高度与注射机最小闭合距离的关系图0.14
模具的闭合高度是合模后模具的厚度,应大于注射机两模板之间的最小间距。
模具的安装和固定图0.15图0.16
模具开模行程的要求:
单分型面Smas≥H1+H2+(5~10)
双分型面Smas≥H1+H2+(5~10)
直角式有侧向抽芯
1)注塑机最大注射量的确定
按重量:
KM机max≥Ms*n+m1
2)注射压力的确定
P机max≥Ps
3)锁模力的确定
锁模力是注射机动模板在注射时对模具的夹紧力,必须大于塑料充满型腔时注射压力在型腔内产生的涨力。
第一章注射成型模具结构P38
1.1注射模分类
1.按整体结构分类:
①单分型面注射模具
②双分型面注射模具
③多分型面注射模具
④垂直分型面注射模具
⑤有侧向分型和抽芯结构注射模具
⑥定模有定距推板结构注射模具
⑦直角注射机专用注射模具
⑧有活动镶件注射模具
2.按浇注系统结构分类:
①热流道注射模具
②绝热流道注射模具
③温流道注射模具
3.按塑料制品材料分类:
①热塑性塑料模具
②热固性塑料模具
1.2热塑性塑料注射模具的特点
1.3热塑性塑料注射模典型结构P39
1.3.1单分型面结构
模具结构、动作、零件号名称,件24、25的作用图1.1
1.3.2双分型面结构P41
第一分型面、第二分型面、点浇口、定距拉杆、定距压板图1.2
1.3.3垂直分型面结构P45
有两种结构:
1.斜滑块瓣合结构(哈夫块)
分型面、零件名称、推管、斜滑块瓣合结构图1.3
2.斜滑块斜导柱在动模的三瓣合结构
1.3.4注射成型模具点的其他常用典型结构P47
(1)潜伏浇口、推管推出结构
图1.5模具结构、动作、分型面位置、潜伏浇口、推管推出结构特点
(2)弹簧测抽芯结构
图0.4
(3)四爪形浇口、推杆推管联合脱模结构P48
分型面、复位结构图1.7
(4)导柱在动模、滑块在定模的斜向分型结构
(5)斜导柱、斜滑块均在定模的侧向抽芯结构P50
(6)斜导柱在定模、斜滑块在动模的内抽芯结构P51
图1.10模具结构、动作、分型面、结构特点
(7)斜滑块推杆顶出式内抽芯结构
1.3.5侧向分型抽芯结构P52
(1)用斜导柱抽芯
(2)用导滑板抽芯
(3)油缸或汽缸抽芯P54
(4)用齿轮齿条斜抽芯P55
(5)用弹簧抽侧型芯
(6)斜导柱二级顺序抽芯结构P56
1.3.6定模定距推板脱模结构P58
1.3.7直角注射成型机上用注射模结构P59
(1)一般结构
(2)自动脱螺纹结构
1.3.8有活动镶件的注射模结构P60
(1)有单面活动镶件的注射模
(2)有双面活动镶件的注射模
1.3.9多层型腔的简易注射模结构P62
1.4热流道注射模结构
热流道模具—浇注系统为热流道结构或隔热保温结构的注射模为热流道模具。
优点:
浇注系统内的塑料始终保持熔融状态,冷却定型后只需取出制件,而没有交到凝料,省料、自动化程度高。
缺点:
结构复杂、零件增加、能耗增多、只适用于大批量生产。
1.4.1热流道注射模的应用范围P63
并非所有热塑性塑料都适合于热流道模具
适合于热流道的塑料性能:
熔融温度范围宽
比热容小、导热性好聚乙烯、聚丙烯、聚苯乙烯
1.4.2无流道凝料注射模具分类
方法:
一是隔热保温法。
二是浇注系统加热法。
①井式喷嘴
②延伸喷嘴
③绝热流道
④半绝热流道
⑤热流道
1.4.3井式喷嘴隔热保温流道的注射模结构P64
1.4.4多形腔隔热保温流道和半隔热保温流道结构
1.4.5热流道结构P65
(1)外热式塑料层隔热保温延伸喷嘴结构
(2)全隔热外热式喷嘴结构
(3)用空气隔热保温的延伸式喷嘴结构
(4)内加热式多形腔热流道注射模结构
1.4.6热流道板的结构形式P67
I型:
4型腔Y型:
三型腔H型:
八型腔X型:
四型腔
第二章注射模设计
2.1注射模合理设计P69
2.2方法
2.3设计方案内容P70
(1)首先确定分型面,是否有侧抽芯
(2)确定型腔数、排列形式以及型腔、型芯结构
(3)浇口位置、脱浇道结构、排气结构
(4)冷却系统
(5)导向、定位结构
(6)推出、复位结构
(7)模架及标准件
(8)模具钢热处理
(9)注射机型号、规格选定
2.4分型面与型腔结构P70
2.4.1分型面确定的要点
分型面:
模具打开的面,制品从分型面被推出,双分型面模具有两个分型面,用于取出浇道凝料的分型面为第一分型面,推出塑件的分型面为第二分型面。
(1)应在制件最大外形之处,有利脱模。
(2)不影响外观
(3)便于进料,利于成型排气。
(4)利于型腔加工
(5)避免侧抽芯或有利于侧抽芯。
(6)利于嵌件、活动镶件的安装。
2.4.2分型面常见几种形状
(1)水平分型面
(2)斜分型面
(3)阶梯分型面
(4)垂直分型面
(5)曲面分型面
2.4.3排气和溢流P73
排气槽的作用—当熔融塑料进入模具型腔时,排气槽将空气导出而熔融塑料不溢出型腔。
排气槽的深度—视不同塑料而定,一般(0.01~0.03)mm
(1)模具合模后排气不良的后果
①增大阻力,难以充满型腔,造成凹陷、缺料
②造成气泡、熔接痕—熔融塑料在模具型腔内再次熔接而造成的接痕印记。
③降低连续注射的效率
(2)排气槽位置
①熔料流程最远端
②熔料汇合处
③型腔内空气易于储留之处
④型腔中盲孔的底部
(3)排气槽的排气方法P75
①利用分型面排气
②利用设有排气间隙的排气杆排气
③利用型芯和镶件的配合间隙排气
2.5成型件设计P79
2.5.1凸凹模结构设计
1.凹模—是成型件外表面的成型零件,是制品外表面形状、结构的复制。
凹模结构形式;
(1)整体结构凹模—小型模具采用
(2)整体镶入凹模—中小型模具采用
①台肩式
②吊装式
③有定位要求
(3)局部镶拼凹模—型腔内有易于磨损或复杂的部分
(4)四壁镶拼凹模—大型模具采用
(5)两瓣组合(哈夫块)--垂直分型面采用
(6)螺纹形环
2.凸模—是成型件内表面的成型零件,是制品内表面形状、结构的复制。
P86
凸模结构形式:
(1)整体结构
(2)整体镶入
(3)镶拼组合
(4)小型芯安装固定方式
(5)螺纹型芯装固定方式
(6)活动型芯装固定方式
①
②
③
④
⑤
(7)镶拼注意事项P90
表2.8
2.5.2(凸凹模)成型尺寸计算P91
收缩率—以制品收缩尺寸单位长度的百分比表示为收缩率
1.(凹模)型腔尺寸计算
(1)径向尺寸
①按平均尺寸计算
②按极限尺寸计算
(2)深度尺寸
①按平均尺寸计算
②按极限尺寸计算
2.(凸模)型芯尺寸计算
(1)径向尺寸
①按平均尺寸计算
②按极限尺寸计算
(2)深度尺寸
①按平均尺寸计算
②按极限尺寸计算
3.中心距的计算
4.螺纹型芯尺寸计算(了解)P94
5.螺纹形环的尺寸计算(了解)P95
6.螺距的计算(了解)
7.计算注意事项P97
(1)脱模斜度—为使塑件顺利从凸凹模取出而在型腔及型芯上设置的斜度,不同品种塑料脱模斜度不同,一般凹模脱模斜度略大于凸模。
表2.11P96
①凹模以大端尺寸为准,选好斜度后标注小端尺寸
②凸模以小端尺寸为准选好斜度后标注大端尺寸
(2)对于收缩率很小的塑料(聚苯乙烯、醋酸纤维等)薄壁制品不计算收缩率。
(3)收缩率个方向不同(收缩率取法)
①与主流道垂直方向(横向)取稍大于平均值
(纵向)取稍小于平均值
②制品中有金属镶件时取小值。
8.(凹模)型腔侧壁和底板厚度计算P98
1)(凹模)矩形型腔结构尺寸计算
(1)(开口)组合结构的矩形型腔
①型腔侧壁厚度计算
②底板厚度计算
(2)整体结构的矩形腔P100
①型腔侧壁厚度计算
②底板厚度计算
③矩形型腔支撑板厚度计算
刚度计算
强度计算
加支持板计算
2)圆形型腔结构尺寸计算P103
(1)开口:
①侧壁厚度计算
②底板厚度计算
(2)整体结构
①侧壁厚度计算
②底板厚度计算
2.6成型件(凸凹模)常用钢材及其热处理要求P108
成型件所用钢材均应进行调质处理,以满足性能要求并消除应力。
2.6.1成型零件(凸凹模)的钢材
2.6.2热处理要求P109
(1)调质处理—去应力
(2)有粗糙度要求的非亚光面—不低于HRC32一般达到HRC45
(3)有腐蚀气体产生的(聚氯乙烯PVC、聚碳酸酯PC)
38CrMoAl—调质(28~32)HRC氮化(60~65)HRC
PCR--空冷淬硬(42~53)HRC
(4)镜面
P20(3Cr2Mo)预先热处理(36~38)HRC
PMS(10Ni3CrCuAlVS)预先热处理(40~45)HRC
(5)大型注射模
含硫易切预硬化钢:
5NiSCa、SM1(55CrNiMnMoVS)
易切钢:
4Cr5MoSiVS
(6)精密、复杂、小型的型腔、型芯、镶件
65Nb、LD2、CG-2、012A1
2.7成型件配合尺寸的公差要求P110
(1)固定件:
凹模、凸模、型芯(侧型芯)H7/m6或H7/K6
(2)滑动件:
型芯-推板、推管—型芯杆、推杆H7/f7、H8/f7间隙小于益边值
2.8型芯与型腔的定位与导向结构设计P111
定位、导向结构的组成:
一般由导柱和导套组成,对于精密薄壁制品可在动模和定模之间增加二次精定位结构。
定位、导向结构的作用:
保证动、定模型腔、型芯合模的准确位置,也就保证了制品尺寸精度和形状要求。
2.8.1一般的定位与导向
导柱与导套:
固定部分—H7/k6活动部分—H7/f7
2.8.2二次精定位结构设计
①简易卧销精定位结构
②无间隙滚珠导套、导柱精定位结构
③圆锥定位件二次精定位结构
④锥面矩形精定位结构
⑤型芯与型腔的锥面、斜面精定位结构
⑥型芯与滑块的精定位
⑦滑块的精美导向结构
⑧型腔、型芯、滑块组合成型精定位结构
2.9型腔数的确定方法P116
2.9.1
2.9.2按注射剂的容量
n≧KmN-m
2.9.3
2.9.4按注射机的额定锁模力
2.9.5确定型腔数应考虑的问题
2.10浇注系统设计P117
浇注系统—熔融态塑料经注射机喷嘴在高温高压高速状态下进入模具型腔的通道
2.10.1设计要点
①力求与型腔距离近、一致,不直接冲击型芯,避免熔接痕、有利排气。
②力求在分型面上、利于加工、快速平稳充满型腔,主流道在中心位置。
③利于制品外观。
易于清除。
④对于大型模具力求用软件分析型腔填充过程。
⑤大批量制品应是浇道凝料与塑件自动分离。
⑥利于后工序加工、装配。
2.10.2浇注系统的组成和作用
浇注系统的组成:
主流道、分流道、进料浇口、冷料穴
2.10.3主流道设计P118
主流道—连接注射机喷嘴与分流道之间的通道
1.垂直式主流道结构参数
(1)主流道小端直径=(注射剂喷嘴孔径+1)mm
长度:
越短愈好(一般不超过60mm)
锥度:
粘度小2~4°粘度大3~6°
(2)浇口套(主流道钢材):
T8A、T10A(50~55)HRC
①小径=注射剂注射嘴直径+(0.5~1)mm
凹球面直径SR=SR1+2mm
配合H7/j7H7/h6
粗糙度0.4~0.8Ra
2.倾斜式主流道
2.10.4浇注系统的拉料与定出设计P124
冷料穴—用于储存注射熔料最前端降温冷料部分,防止进入型腔而造成制品缺陷
1.冷料穴的位置与作用
2.主流道的拉料和顶出结构的设计
图:
a、b、c、d、e、f
2.10.5分流道设计P125
分流道—连接主流道和浇口之间的通道
1.分流道设计要点:
①使熔料的温度压力损失小,长度要短,粗糙度要低。
②熔料固化时间稍慢与制品,有利于保压、补缩。
③使熔料快速均匀进入型腔,多形腔力求进料平衡
④便于加工,便于使用标准刀具。
2.分流道界面形状及面积设计P126
图:
a、b、c、d、e、f表2.30
3.分流道及型腔的布置和排列P127
①平衡排列
②非平衡排列
4.分流道的修正
5.按分型面设计分流道
6.辅助流道的设计
2.10.6浇口的设计P134
浇口—是熔融态塑料进入型腔的通道,位于浇注系统的末端
1.浇口截面尺寸的确定要点
①其截面形状和尺寸根据制品尺寸大小、壁的薄厚
②先取小值,后试模修正
2.浇口位置确定的要点
①在制品壁最厚处,至型腔各部分距离尽可能近,利于补缩。
②避免产生喷射,在成型中产生蛇流。
③应在制品成型时的主要受力之处
④应考虑收缩的方向性和可能引起的变形
3.各类浇口的结构、尺寸和计算
①直接浇口
②侧浇口
③搭接浇口
④薄片浇口
⑤扇形浇口
⑥环形浇口
⑦盘形浇口
⑧护耳浇口
⑨点浇口
⑩潜伏浇口
2.11.1热流道浇注系统设计P139
热流道的适用范围和优点
2.11.2分流板结构P140
多型腔用
2.11.3热喷嘴结构P141
2.11.4热流道其它零件P159
2.11.5热流道设计
1)主流道直径计算
2)分流道直径计算
3)进料口直径计算
4)体积流率计算
5)热流道板加功率计算P160
P=0.115t*W/860T*n
6)热流道板热损失的计算P162
(1)辐射、对流损失
(2)传导损失
2.12浇道凝料的脱模结构P161
2.12.1推杆
2.12.2推板
2.12.3剪切式P162
2.12.4差动式推杆
2.12.5顶出式
2.12.6斜窝式
2.12.7托板式
2.12.8斜面式
2.13侧向分型与抽芯结构设计P175
2.13.1斜销抽芯结构的设计要点与注意事项
d1=d+(0.5~1)mm其中:
d1—斜导柱孔d=导柱孔
α≤25°其中:
α—斜导柱的角度α1=α+(2°~3)其中:
α1—压板斜面角度
h≥2/3H其中h—压板斜面高度H–抽芯滑块厚度
定位制动装置—图2.135
2.13.1斜块抽芯结构的设计要点与注意事项
α≤25L1≥H其中:
L1—滑块留在滑块槽内的长度H—滑块长度
2.13.3抽芯力的估算P177
2.13.4斜销(斜导柱)直径计算
2.13.5弯销截面尺寸计算
2.13.6抽芯距的计算
2.13.7圆形线轴抽芯距计算P179
2.13.8矩形线轴抽芯距的计算
2.13.9圆形多瓣滑块抽芯距的计算P180
2.13.10斜销(斜导柱)长度计算
2.13.11弯销滑块方孔尺寸确定P181
2.13.12滑块倾斜时的角度和斜销工作段尺寸计算P182
2.14常用的侧向分型与抽芯结构特点分析P183
2.14.1斜滑块侧向抽芯结构特点分析
1.结构特点:
利用推出机构的推力,在推出制品的同时完成垂直分型面的分型、抽芯
2.适用范围:
抽芯距不大,但侧凹成型面积大,需要抽芯力大的制品,如线轴之类。
3.常用结构:
(1)斜滑外侧分型图2.149
(2)斜滑内侧抽芯图2.150
(3)斜滑块内侧抽芯的另一种结构图2.151
(4)弹簧顶销止动结构
4.斜滑块的组合结构
5.斜滑块的导滑结构
2.14.2滚轮式変角弯销抽芯结构的特点分析P185
2.14.3斜销抽芯、分型面斜面锁紧结构特点分析P186
2.14.4弯销二级抽芯结构特点分析P187
2.14.5斜推杆式瓣合抽芯结构特点分析
2.14.6斜推杆式内抽芯结构特点分析P188
2.14.7推杆平移式内抽芯结构特点分析
2.14.8连杆式顶出抽芯结构特点分析P189
2.14.9斜推杆的内抽芯、弹簧复位结构特点分析P190
2.14.10液压抽芯结构简介
2.14.11内部连杆式液压抽芯结构的特点
2.14.12斜向液压抽芯结构特点简介P191
2.14.13顶出式斜面内抽芯结构分析
2.14.14侧型芯与滑块的九种连接方法P192
2.14.15滑块的导滑结构(7种)
2.15螺纹制品的脱螺纹结构P193
(1)旋转脱模
(2)非旋转脱模
①利用制品的弹性(聚乙烯、聚丙烯)
②手动脱螺纹模架
③瓣合斜滑块
其它方式
2.16制品脱模的结构设计P196
脱模结构--将塑料制品在开模后从模芯上推出的机构
2.16.1脱模结构的设计原则
①分析计算制品包紧力大小、部位和阻力中心,推力尽量与脱模力重合。
②着力点力求靠近型芯
③着力点力求对称、平衡
④推出位置力求在制品内表面
⑤结构合理,便于制造和维修
⑥选材合理,热处理得当,寿命长
3.16.2脱模结构分类
(1)简单脱模结构
(2)两次推出脱模结构
(3)双脱模结构
(4)顺序脱模结构
(5)螺纹内旋转脱模结构
2.16.3简单的脱模结构P197
推杆推出结构特点:
结构简单、可利用推杆与孔的间隙排气、便于布置、与塑件接触面积小,数量不足时会损坏塑件。
图2.197
2.16.4推出结构的导向零件
图2.180P198
2.16.5推杆、推管及固定方法P198
1.推杆图2.181
2.推杆的固定方法图2.184
2.