钢材轧制厚度计算机控制系统设计.docx
《钢材轧制厚度计算机控制系统设计.docx》由会员分享,可在线阅读,更多相关《钢材轧制厚度计算机控制系统设计.docx(58页珍藏版)》请在冰豆网上搜索。
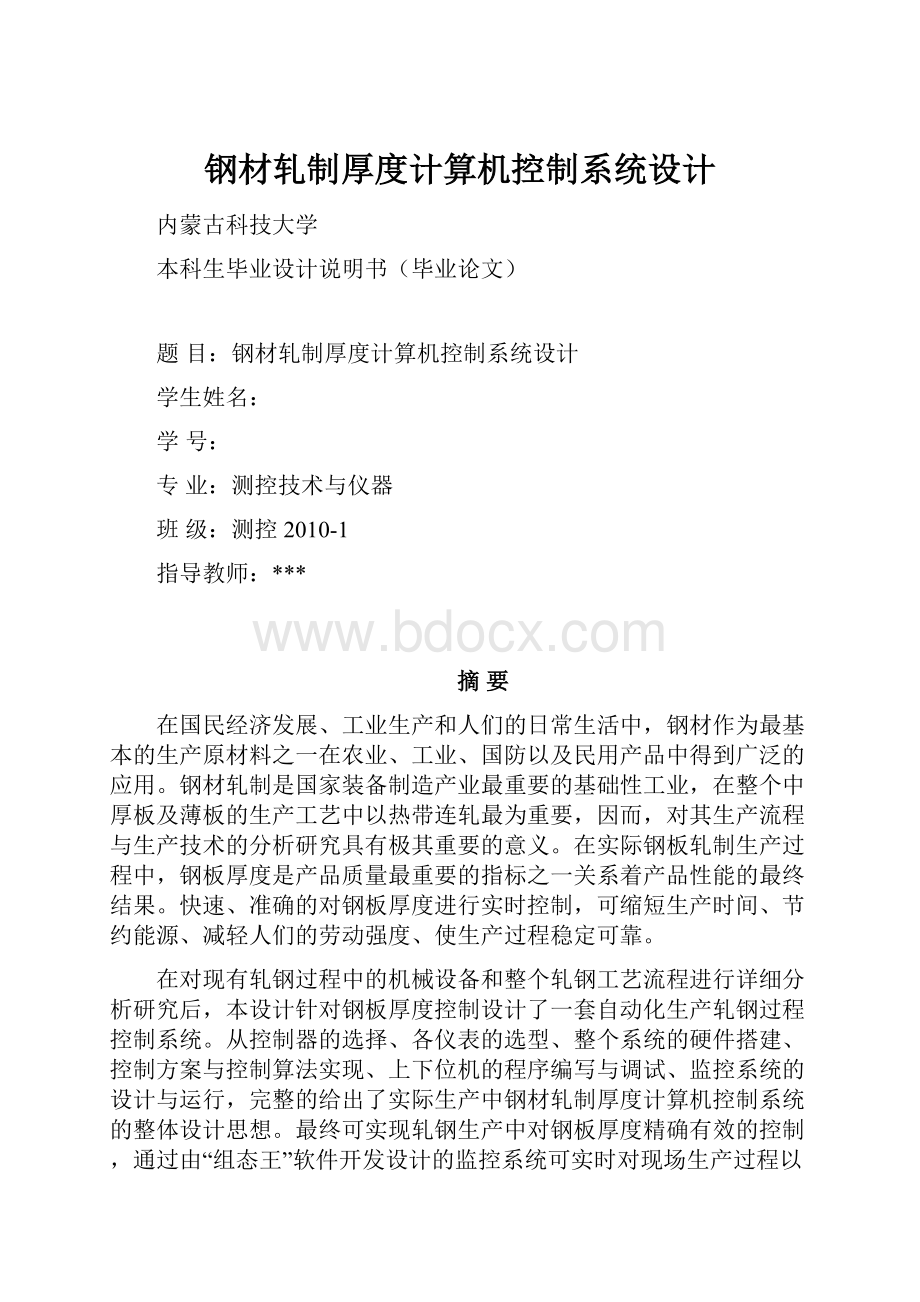
钢材轧制厚度计算机控制系统设计
内蒙古科技大学
本科生毕业设计说明书(毕业论文)
题目:
钢材轧制厚度计算机控制系统设计
学生姓名:
学号:
专业:
测控技术与仪器
班级:
测控2010-1
指导教师:
***
摘要
在国民经济发展、工业生产和人们的日常生活中,钢材作为最基本的生产原材料之一在农业、工业、国防以及民用产品中得到广泛的应用。
钢材轧制是国家装备制造产业最重要的基础性工业,在整个中厚板及薄板的生产工艺中以热带连轧最为重要,因而,对其生产流程与生产技术的分析研究具有极其重要的意义。
在实际钢板轧制生产过程中,钢板厚度是产品质量最重要的指标之一关系着产品性能的最终结果。
快速、准确的对钢板厚度进行实时控制,可缩短生产时间、节约能源、减轻人们的劳动强度、使生产过程稳定可靠。
在对现有轧钢过程中的机械设备和整个轧钢工艺流程进行详细分析研究后,本设计针对钢板厚度控制设计了一套自动化生产轧钢过程控制系统。
从控制器的选择、各仪表的选型、整个系统的硬件搭建、控制方案与控制算法实现、上下位机的程序编写与调试、监控系统的设计与运行,完整的给出了实际生产中钢材轧制厚度计算机控制系统的整体设计思想。
最终可实现轧钢生产中对钢板厚度精确有效的控制,通过由“组态王”软件开发设计的监控系统可实时对现场生产过程以及生产设备进行监控,达到了预期目标,为企业带来丰富的经济效益及社会效益。
关键词:
轧钢机;厚度控制;液压压下;过程控制
Abstract
In thedevelopmentofthenationaleconomy, industrialproductionand people'sdailylife, thesteel asthebasic rawmaterial isoneofthe widelyusedinagriculture, industry, nationaldefenceand civilproducts. Steelrolling isthemostimportantfoundation ofnational equipmentmanufacturing industry industry, intheproductionprocessof the plateand plate in hotcontinuousrolling isthemostimportant, therefore, hastheextremelyvitalsignificance tostudythe productionprocessand technology. Intheactual processofplaterolling, thethicknessofthesteelplate is oneof themostimportant resultof productquality index inrelationtothe propertiesoftheproduct. Fast, accuratereal-time controlof thethicknessofthesteelplate, canshortentheproduction time, saveenergy,reducelaborintensity, people maketheproduction processisstableandreliable.
Inthe existingmachinery inrollingprocess and the rollingprocess ofdetailedanalysis, thedesignforthe platethickness control designonesetofautomaticrollingmillproduction processcontrol system. From theselectionofcontroller,the instrumentselection, thesystem hardware, controlstrategy andcontrolalgorithm, theupperandlowercomputer programminganddebugging,monitoringsystemdesignand operation, complete the overalldesign ofcomputerintheactualproductionof steel rollingthicknesscontrol system. Finally canachievetocontrol thethicknessofthesteelplate accurate rollingproduction,"monitoringsystem by Kingview" software canreal-time monitorthe productionprocessand productionequipment, hasachievedtheanticipatedtarget, bringeconomicbenefitsfortheenterprise and society will benefit therich.
Keywords:
rollingmachine; gaugecontrol; hydraulicpressure; processcontrol
第一章引言
随着我国钢铁企业的飞速发展,钢材已成为经济快速发展和国家建设的重要物资之一。
据统计,近90%的钢材均是通过轧制方法生产的。
该方法具有生产率高、生产过程连续性强、品种多、易于实现机械化和自动化等优点。
目前,我国对轧制技术和轧钢机械设备的研究已具备了一定的基础,但与欧美等发达国家相比还存在一定的差距。
如何利用现有轧钢过程中的机械设备,通过深入研究分析整个轧钢工艺流程,综合考虑各种轧钢过程的影响因素并采取相应的补偿措施,实现最优控制以发挥轧机的最大生产效率使钢材的产量和质量进一步提高,是当今社会面临的现实问题,也是符合我国现阶段弘扬创新驱动发展的战略。
在钢板轧制过程中,钢板厚度的精确度大小直接关系着最终产品的性能,必须充分利用轧机设备、详细分析轧钢工艺后采用合理有效的控制方案实现对钢板厚度的准确控制。
本文通过对钢材轧制过程中钢板厚度控制的实现进行了相关的研究与设计,其目的是设计出一套安全、稳定、优质、高效的钢板厚度自动控制系统,提高生产效率及产品质量。
一.1轧钢机结构与工作原理
通常,轧钢机由一个或数个主机列构成。
主机列主要包括工作机座、传动装置与主电动机等部分组成。
轧辊、轧辊轴承、轧辊调节装置、上轧辊平衡装置及机架等组成工作机座;主联轴器、减速器、齿轮机座、万向或梅花接轴等组成传动装置。
主机列的类型和特征基本上决定了整个轧钢系统性能指标。
轧钢机各组成部分的工作过程:
由电动机通过齿轮和主轴驱动工作辊直接轧制钢板,调整机构调节压下装置和轧制线高度最终调整辊缝开度从而控制轧钢机钢板出口厚度,轧辊平衡装置以及液压弯辊装置用于平衡上下轧辊位置,支持辊用于支撑工作辊以减少其弯曲变形。
轧钢机是钢板轧制生产线的核心设备,产品质量和厚度的控制主要集中在连轧区。
因此在热带连轧区的扎钢机组一般有5~7个机架构成,由于科学技术的飞速发展,众多大型机械设备都需要不同规格钢板作为其零件加工材料,因此对生产工艺的要求越来越高,必须减少中间辊道的温降,同时加大钢板厚度,可通过在轧钢机组前放置F0机架或M机架作为轧钢生产线的粗轧区。
这样做不仅使钢板的厚度规格增加到50mm以上,并可以减少轧制的道次,同时使钢板的温降及头尾温度的降低减少,这样解决了特殊产品由于连轧能力不够而受到限制的缺点。
钢板在连轧中,终轧温度一般应控制在830~870℃,使终轧温度能高于相变点,在规定范围内轧出产品[1]。
一.2轧钢工业简介
轧钢工业生产中的过程控制是从生产现场实时检测控制对象的被控参数值与设定值的偏差运算,按预定的运算处理方式后自动输出控制量使其被控参数稳定在设定范围的控制过程。
从工程技术的角度上看,可把过程自动化控制具体理解为:
在不同的实际生产过程中,采用自动检测、电动执行等自动化装置和工业计算机,组成自动控制系统,使过程变量保持在预设定的给定值上,并通过人的合理控制协调全部生产过程,使生产过程稳定优质。
工业生产过程实现自动控制的目的是用有限资源生产出持久耐用的精美产品,提升工件产品质量;在人力所不能胜任的快速工作场合中实现自动操作;把人从繁杂的劳动中解放出来,生产过程不轻易受人的情绪和技术水平的影响,使生产作业稳定进行。
实现自动化控制,可以生产出性能稳定、质量高、价格合理的产品,从而提升企业的竞争力[2]。
钢材轧制生产过程的对象为机电、液压控制装置,因其对象惯性小、响应快,所以其控制周期通常为2~20ms[3]。
液压压下和轧辊系统的液压恒压力或位置控制系统的控制周期通常为2~3ms,工艺参数自动控制或机电设备控制也应小于20ms,这和以热工参数为主的化工、轻工、冶炼和炼油生产过程自动化控制相比,控制周期约快20~40倍。
轧钢生产过程自动化要求控制信息在各控制站之间能快速传递,特别是在连轧区域内,多个控制功能块联系密切且相互影响,并共享输入和输出模块,因此要求数据信息在各控制站之间以及和CPU之间能快速传递和更新。
因此,轧钢自动化控制系统要求具有高速通信能力和高速控制能力的技术特点。
采用快速分布式计算机控制系统,并以此系统为基础不断开发专业功能强大的软件,以适用于轧钢生产过程的计算机控制系统,钢材轧制自动控制系统是计算机为核心的自动化系统对轧制生产线进行实时监控。
以热带连轧轧钢机组为例,7个机架上集中了约10个机电设备的位置控制,20多个液压位置或恒压力控制,各种板形自动控制,主速度控制,厚度自动控制,活套张力控制或无活套控制,活套高度控制通常有6个以及轧钢机组终轧温度控制等,共有约55个控制回路。
因此系统就要求采用多个控制器、同时控制器内采用多处理器结构。
轧钢自动控制系统中由于多控制量的控制结果最终都将会影响集中到轧辊、轧件之间的变形区内,因此各功能间有明显的相互影响。
目前在HMI级和过程控制级,全部采用PC服务器或工作站,Windows操作系统和组态王监控软件应用于轧钢自动化控制系统。
在基础自动化级,虽以PC为基础的分布式控制系统逐渐增多,但是主流产品仍然是PLC和高性能控制器。
PLC和高性能控制器发展的一个方面是CPU和I/O的分离。
一.3轧钢工业国内外现状及发展历程
在全球范围内钢铁已被广泛的应用于各个领域,并成为主要生产原材料。
当今国内的轧钢机械和轧钢技术在不断创新中逐步的应用与发展,并且引进了世界上先进轧钢机械和轧制技术。
在钢材市场中,钢板的生产应用占得比重最大。
我国自1965年末研制成300mm五机架试验性窄钢板冷连轧机,80年代又引进了原西德生产的1700mm五机架带钢冷连轧机成套机组,自1981年我国在日本引进1700mm热连轧机的全套设备开始,随后迅速崛起了一大批拥有先进生产工艺的热连轧板带厂,90年代后又先后投入了六辊HC轧机、CVC轧机用作生产,截止2007年,我国的热轧宽板带材年生产能力已达到5500万吨。
热连轧机的发展主要包括以下几方面:
首先采用加速轧制,提升钢材产量,钢板热连轧机组的出口速度已经从20世纪50年代的10m/s~12m/s提升到现在的35m/s,并向着更高的速度发展;其次采用计算机控制,提高了自动化水平;还有产品规格的增加,提高精度等方面。
当今的钢板轧钢机正在向着高精度、大型化、高速化和自动化方向发展[4]。
轧钢工业自动化的发展可以分为三个阶段:
第一阶段为单机模拟系统自动化阶段,时期约在20世纪40年代至50年代;第二个阶段主要是数字电子计算机和单机自动控制系统共存阶段,时期约在60年代;第三个阶段逐步发展成为多层次计算机管理监控模式,时间是从20世纪70年代到现在,该模式将原来只靠一台计算机来实现数据采集、处理、输出的形式替换成为多层次分布式计算机控制系统[12]。
目前伺服调节和传动部分也全部采用计算机数字控制,形成多层次的数字化系统。
第二章板坯厚度自动控制系统总体方案设计
钢材的精度主要是指厚度(横向和纵向)的精确度。
钢板是在轧辊辊缝中轧制出来的,辊缝的大小及形状基本可以决定钢板纵向和横向厚度的变化,因此,要提高产品的厚度精确度,就必须清楚理解并分析出轧辊辊缝大小及形状变化规律。
厚度是板材产品最主要的质量指标。
轧件出口厚度产生波动主要受接触面摩擦、材料尺寸、温度和张力变化的影响。
可通过调节辊缝或轧制速度这两个变量来有效地控制轧机钢板的出口厚度,在实际轧制生产中通常需要联合调节这两个重要参数,找出两者相关的逻辑关系编写特定的算法程序以实现钢板厚度的最优控制。
二.1影响轧件厚度波动的主要因素
在钢材轧制生产过程中,有多种因素可以直接影响钢板的最终出口厚度,这些影响轧制厚度的因素主要取决于轧机和轧件两个方面。
其中轧机方面影响钢板厚度的因素主要是支撑辊的偏心影响,这个因素将直接使轧辊每旋转一周辊缝都会产生一次波动,同时轧机方面对于钢板厚度的影响因素还来自轧钢机工作机座的弹性形变和轧辊在轧制过程中发生的磨损以及热膨胀会造成辊缝发生不同的变化等;轧件方面对于钢板厚度的影响因素来自于变形抗力、材料厚度的不同和钢板张力的变化等。
首先对于钢材轧制生产过程中的研究可通过弹塑曲线进行理论分析计算,据轧钢机的弹跳方程可知,轧制过程中钢板的厚度主要由四个因素决定,包括空载辊缝、轧制压力、轴承油膜厚度以及轧机的纵向刚度系数。
因此,不论是讨论钢板厚度控制的原理,还是要分析轧件厚度波动影响因素,均需从这四个因素的分析研究开始入手[19]。
上述的影响因素都将造成钢板轧制过程中辊缝发生较大的变化,从而直接影响到轧钢机出口钢板厚度出现纵向厚度偏差。
而在实际的钢材轧制生产过程中,以上各种因素对实际出口扎件厚度的影响并不是孤立的,往往是相互联系共同影响轧制厚度。
因此,在对钢材轧制厚度控制系统设计时,需综合考虑各因素的相互影响。
二.2板材厚度控制方法
为在实际生产过程中能够精确控制钢板厚度,可采用厚度控制的方案有很多,其中调整压下以及调整轧制速度是比较经典的控制方法。
二.2.1调整压下(改变原始辊缝)
钢板厚度控制中应用最广泛、最有效、最主要、最直接的是调整压下控制方法。
它主要的工作原理即通过利用负反馈形成闭环控制改变辊缝的大小来消除各因素的变化对钢板出口厚度的影响。
二.2.2调整张力(调整轧制速度)
张力厚度控制与压下厚度控制相比具有响应快且稳定的优点,可提高钢板厚度的控制精度。
但张力厚度控制也有缺点即当对钢板进行热连轧时,轧制张力的变化过大会造成轧件被拉断或者被拉窄,因此,张力即轧制速度变化范围不能过大。
此种控制方法在热连轧中实际应用时,可放在最后一个机架上采用张力控制进行微调,也可以把张力厚度控制和压下厚度控制相互配合使用构成串级控制系统,此时由于串级控制系统只有一个执行器,可以将轧制速度作为系统的干扰,用副调节器对其进行快速校正,副调节器输出一个控制量给电液伺服阀,通过电液伺服阀最终改变轧辊的压下量,由于轧辊压下量的改变使轧辊与板材的摩擦力发生变化可以在较小范围改变轧制速度,使轧制速度稳定在设定值范围内,且保证板材的轧制厚度满足产品规定。
当轧制的钢板厚度与预期的板厚相差较大时,可采用压下厚度控制;当钢板厚度是由张力变化引起的,可在张力允许调节范围内即可通过张力控制进行微调。
张力厚度控制通常是通过细微调节轧制速度的大小来实现,而改变轧制速度不但影响到张力,还使温度以及摩擦系数等影响因素随之发生改变。
因此,调整轧制速度可以同时起到调节张力、轧制摩擦系数和温度的作用。
通过改变轧制速度进而改变轧制的张力,也就是当系统检测到轧制速度发生变化时,为使钢板厚度保持在设定的范围内,可以通过改变轧辊的压下量来改变钢板的轧制速度来消除张力变化对系统的影响。
根据实际现场轧制情况的不同,需采用不同的钢板厚度控制方案。
在本设计中为了使钢板厚控制更精确,因此,将两种厚度控制方案相互结合起来使用形成串级控制系统,把轧制速度作为整个系统的主要干扰量,在副回路中利用负反馈原理将其消除。
其中最基本、最主要的控制方法还是主回路中的调整压下的厚度控制,这样才能是钢板厚度更精确,达到更好的效果。
二.3板坯厚度与张力联合控制
二.3.1传统压下控制方式
传统压下控制方法多为直流电动机调节扎辊的压下量,即属于电动压下装置,用电机的转动量带动工作扎辊进行上下位置的移动。
电动压下的优点是压下速度快、辊缝调节范围大,能在制动控制系统、频繁的启停系统中可发挥优势。
但是因为用电机调节压下量的固有特性,具有传动装置部分反应慢、惯性大、精度低等缺点。
对于现代化的钢板轧制控制要求精度高、速度快的特点,如果继续在精轧机中使用电机压下控制方式将会降低其控制精度,所以电机压下控制方式已不满足现代化的高精度、高速度轧钢机。
为提高压下装置响应速度就必须减少其惯性,通常选用液压压下控制方案即可以达到精度准、速度快、稳定性能高的效果[4]。
二.3.2现代液压AGC系统及其控制方式
现代液压AGC系统正是针对传统控制方案的影响因素,采取相应的补偿措施或控制它们的影响范围,最终使出口板材厚度稳定在设定值范围内。
针对本文的研究对象和液压厚度控制方案的诸多优点,下面详细分析液压AGC系统。
现代化液压压下系统,通过电液伺服阀直接控制液压缸中液压油流量使其产生线性位移,现代液压压下系统执行器的液压控制元件(如伺服阀)以及液压缸是整个液压系统核心部件,其动态特性在很大程度上决定着整个液压压下系统性能。
和可控硅整流的直流电机压下控制系统相比,液压压下控制系统具有动态响应快,可以组成结构紧凑、重量轻、体积小、加速性好的伺服系统等最突出的优点。
在热带连轧液压压下这样的大、中功率伺服控制系统,这一优势尤为重要。
其一般特性是:
在液压压下控制系统中,动作最快的加速度可达到500mm/s2,减速和加速时间也仅有几十毫秒。
其滞后时间仅有10ms,从运动开始8ms后便达到最大速度4mm/s,过17ms后本来匀速运动便开始减速,再经过8ms后运动便会制动直到停止。
液压压下控制系统调节控制工作轧辊每移动100um一共只需花费43ms,如果调节的距离较小且以匀速移动,其调节时间将会更短。
液压压下控制系统组成的核心器件是电液伺服阀,系统中被加速的物质是液压缸中的液压油,通过控制液压油的流量可直接调节轧辊的压下量,压下位置也可在液压缸上直接进行测量,这样可以消除系统滞后现象,提高系统的整体响应速率。
钢板厚度自动控制系统称为AGC,通常一个完整的液压AGC除了位置闭环、压力补偿环,还应设有钢板出口厚度以及温度的自动检测控制系统。
通过液压AGC系统控制框图如图2.1所示,可以看出本设计采用的AGC系统控制方法及工作原理是通过按工艺要求设置钢坯厚度给定量可用SP表示,用测厚仪对实际钢坯厚度h进行测量并经变送器转换成标准信号输入到主调节器即位置控制器,与给定值SP作偏差运算后再在主调节器中进行的相应PID运算处理后,输出一个控制量传送给副调节器作为其设定值,在副调节器中速度变送器测量轧辊的转速n并将其变转换成标准传输信号与设定值作偏差运算后,经副调节器的相应PID运算后,把处理后的结果转换成电流信号△I输送给电液伺服阀。
伺服阀获得电流信号△I后输出一个控制量调节液压缸中液压油的流量△Q,油缸可直接带动轧辊也就调整了辊缝的大小,最终改变初始辊缝给定大小,使得钢板出口厚度控制在工艺规定的范围内。
通过测厚仪对轧制厚度的实际值进行测量转换,与给定信号进行比较,将所得偏差值送入调节器构成反馈系统,即实现辊缝闭环控制,提高控制精度,组成液压轧钢控制系统的主回路;而速度传感器对轧辊转速进行实时检测,并将检测到的信号反馈到副调节器,经副调节器处理运算后就可以补偿轧制过程中因张力即轧制速度的变化而使工作机座产生弹性跳变现象,从而致使辊缝大小发生改变,通过补偿辊缝的变化将会使钢板的厚度控制在很小的范围内改变甚至保持不变,即张力反馈闭环回路,组成液压轧钢控制系统的副回路。
图2.1AGC液压系统控制方框图
上述介绍的张力闭环反馈解决因轧辊磨损或轧辊热膨胀以及位置与速度检测元件本身的误差因素等使对于钢板厚度的控制造成的偏差。
而厚度闭环反馈则可消除设定值与钢板最终出口厚度形成的误差,即通过在轧钢机出口侧加入测厚仪装置形成闭环解决。
原理是通过测出轧机出口钢板厚度与产品规定的厚度进行比较,将得到的偏差值进行相应运算,得出精确的修正辊缝控制量,使钢板厚度控制的精度进一步提高。
通常完整的液压AGC系统,不是只有位置闭环、压力补偿闭环等,同时还需有轧机出口钢板板厚度和油膜厚度补偿以及材料板厚影响的预控的监控系统。
但系统中最重要的还是轧制张力闭环和测厚仪监控系统[4]。
文中提及的电液伺服阀根据其工作原理,将输入信号定为伺服阀线圈中的电流I或者阀芯位移
,输出的信号为滑阀上的负载流量
,通过推导计算则有
(2-1)
式中,
——供油压力
——执行器件负载误差
——流量系数
——油液密度
——功放级滑阀的面积增益
——阀芯位移
——伺服阀负载流量
在实际运用中,当电液伺服阀所带驱动或者负载的执行元件的固有频率较低,则这个系统的工作频率会受到上述原因的限制,此时电液伺服阀的传递函数则近似为
(2-2)
式中,
——伺服阀固有频率
由于在工业现场中多种因素造成测厚仪只能安装在轧机的入口前或者出口后的某一位置,结果使得轧机出口侧从测厚仪到压下的中心线位置其传递函数为一纯延迟环节,即:
(2-3)
其中
(2-4)
式中,
——轧机入口侧测厚仪测得的钢板厚度
——轧机入口侧的测厚仪到轧制中心线之间的距离
——轧机入口侧的钢板行进速度
本设计液压控制系统的控制策略采用PID调节器,其动态传递函数为
(2-5)
式中,
——PID调节器的比例系数
——PID调节器的积分时间常数
——PID调节器的微分时间常数
本设计液压动力部件经运算代入整理传递函数最终可得:
(2-6)
式中,
称总压力流量系数。
在大多数应用场合,液压动力部件所拖动的负载主要是惯性负载。
这时弹性负载甚
小,可以忽略,于是式子可写成[19]
(2-7)
式中,
——液压固有频率
——液压阻尼比
(2-8)
上述部分的分析推导,得到了液压压下控制系统各环节的控制模型,进一步确定了各个模型之间的传递函数。
其中包括了电液伺服阀、测厚仪、液压缸等设备的模型函数,为整个系统的搭建与研究进行了铺垫,能够更准确的分析出系统的固有特性和状态,使得对系统的内部结构特性有了更直观的、具体的、确切的了解,通过各对象模型分析研究便可得到传递函数,画出具体传递函数方框图分析出控制广义对象特点,找到控制广义对象的控制方法,利用PID调节器设置相应的参数最终找出使控制对象最佳运行的液压AGC控制系统。
第三章板坯厚度自动控制系统硬件设计
三.1板坯厚度控制系统